Top 27 Magnet Maker Interview Questions and Answers [Updated 2025]
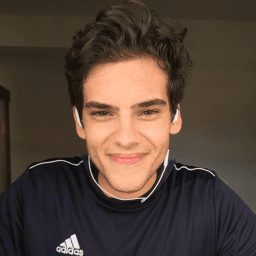
Andre Mendes
•
March 30, 2025
Are you preparing for a Magnet Maker interview and want to stand out? This blog post compiles the most common interview questions for this unique role, offering comprehensive example answers and expert tips to help you respond effectively. Whether you're a seasoned professional or just starting, these insights will equip you with the confidence to impress your interviewers and secure your dream position.
Download Magnet Maker Interview Questions in PDF
To make your preparation even more convenient, we've compiled all these top Magnet Makerinterview questions and answers into a handy PDF.
Click the button below to download the PDF and have easy access to these essential questions anytime, anywhere:
List of Magnet Maker Interview Questions
Behavioral Interview Questions
Can you describe a time when you worked in a team to create a prototype for a new magnet?
How to Answer
- 1
Identify a specific project where teamwork was essential.
- 2
Outline your role and responsibilities in the team.
- 3
Highlight collaboration and any challenges faced.
- 4
Mention the outcome of the prototype development.
- 5
Reflect on what you learned from the experience.
Example Answers
In my last internship, I was part of a team tasked with developing a new prototype for a magnet used in electric motors. My role was to design the layout and select materials. We faced challenges with material availability, but we brainstormed solutions together and adjusted our design accordingly. The prototype was successful, and we received positive feedback from our professor. I learned the importance of flexibility and communication in teamwork.
Tell me about a situation where you encountered a significant issue during the magnet production process. How did you resolve it?
How to Answer
- 1
Define the specific issue you faced in the production process.
- 2
Explain the impact this issue had on production or product quality.
- 3
Describe the steps you took to investigate and understand the problem.
- 4
Highlight the solution you implemented and the outcome of your actions.
- 5
Conclude with what you learned from the experience.
Example Answers
During a batch of magnet production, I noticed that the strength of the magnets was below our standards. I traced the issue to a malfunctioning machine that was not properly mixing the materials. I collaborated with the maintenance team to repair the machine and adjusted the mixing parameters. This resolved the inconsistency, and we were able to meet our quality targets again. I learned the importance of routine checks and maintenance to prevent equipment issues.
Don't Just Read Magnet Maker Questions - Practice Answering Them!
Reading helps, but actual practice is what gets you hired. Our AI feedback system helps you improve your Magnet Maker interview answers in real-time.
Personalized feedback
Unlimited practice
Used by hundreds of successful candidates
Describe an experience where you had to manage multiple projects at once as a magnet maker. How did you prioritize your tasks?
How to Answer
- 1
Identify the projects you managed and their deadlines
- 2
Describe the criteria you used to prioritize tasks, such as urgency or impact
- 3
Give a clear example of a challenge you faced in juggling the projects
- 4
Explain the outcomes of your prioritization and how it benefited the workflow
- 5
Conclude with what you learned from the experience about managing multiple projects
Example Answers
In my last role, I managed three different magnet production orders, each with tight deadlines. I prioritized them based on delivery dates and customer importance, completing the urgent orders first. One challenge was a machine breakdown, which I resolved by adjusting the schedule and reallocating resources. As a result, I delivered all orders on time and learned the importance of adaptability.
Have you ever had to learn a new technique or technology quickly in your role as a magnet maker? What was the outcome?
How to Answer
- 1
Identify a specific technique or technology you learned quickly.
- 2
Briefly explain the context or reason for learning it.
- 3
Describe the steps you took to learn it rapidly.
- 4
Mention the positive outcomes or results from learning it.
- 5
Highlight any recognition or feedback you received afterward.
Example Answers
When we transitioned to a new 3D printing technology for magnets, I had to learn it quickly to keep up with production. I dedicated a week to online tutorials and hands-on practice. As a result, I was able to help reduce our turnaround time by 20%, which impressed my supervisor.
Describe a time when effective communication with your team led to a successful magnet project.
How to Answer
- 1
Select a specific project where communication was key.
- 2
Use the STAR method: Situation, Task, Action, Result.
- 3
Highlight the communication tools or methods used.
- 4
Emphasize the team's collaboration and feedback.
- 5
Conclude with the positive outcome of the project.
Example Answers
In a recent project to create a new type of neodymium magnet, our team faced challenges with the design. We held daily briefings using a messaging app to share updates and ideas. This open communication allowed us to quickly address issues, and we completed the project two weeks ahead of schedule, increasing our output by 15%.
Have you ever mentored a new employee in magnet making? What approach did you take?
How to Answer
- 1
Share a specific example of mentoring a new employee in magnet making
- 2
Explain the methods you used to teach them the process and techniques
- 3
Highlight the importance of hands-on experience and safety procedures
- 4
Mention how you provided feedback and supported their learning
- 5
Conclude with the outcome of your mentoring efforts
Example Answers
Yes, I mentored a new technician last summer. I started by walking them through the entire magnet making process, focusing on hands-on training with supervision. I emphasized the critical safety procedures and ensured they practiced under my guidance. I provided constructive feedback after each session. They became skilled in making various magnets and even helped optimize a process.
Can you give an example of a disagreement you had with a colleague regarding magnet specifications and how you resolved it?
How to Answer
- 1
Describe the specific disagreement clearly and briefly
- 2
Explain the reasons behind your perspective and your colleague's
- 3
Detail the approach you took to resolve the disagreement
- 4
Highlight any successful outcomes or learnings from the resolution
- 5
Keep your tone professional and focused on collaboration
Example Answers
In a recent project, I disagreed with a colleague on the required magnetic strength for a prototype. They wanted a lower specification to reduce costs. I presented data showing that a stronger magnet was necessary for the prototype's performance. We discussed our points and decided to conduct a small experiment to test both specifications. The experiment confirmed my suggestion, and we ended up using the stronger magnet, improving the prototype significantly.
Can you tell me about a particularly creative solution you devised in the field of magnet making?
How to Answer
- 1
Choose a specific project or problem you tackled.
- 2
Explain the challenge you faced in magnet making.
- 3
Describe the creative solution you implemented.
- 4
Highlight the results and impact of your solution.
- 5
Use clear and concise language to convey your story.
Example Answers
In my previous job, we faced an issue with low adhesion in our magnetic stickers. I devised a solution by experimenting with a new type of adhesive that increased the bonding strength. This not only improved customer satisfaction but also reduced returns by 20%.
Technical Interview Questions
What types of materials do you consider essential in the magnet-making process? Why?
How to Answer
- 1
Identify key materials used in magnet production such as iron, nickel, cobalt, and rare earth elements.
- 2
Explain the properties of these materials that make them suitable for magnet making.
- 3
Discuss the role of adhesives or coatings that may enhance the performance of magnets.
- 4
Relate material choice to the type of magnet being produced (e.g., permanent vs. temporary).
- 5
Be prepared to give examples of specific applications of the materials in real-world magnet use.
Example Answers
Essential materials in magnet-making include iron and neodymium. Iron provides the core magnetic properties, while neodymium significantly enhances the strength of permanent magnets due to its high energy product.
Explain the key steps involved in the manufacturing process of permanent magnets.
How to Answer
- 1
Start with material selection like neodymium or ferrite.
- 2
Explain the process of powdering, if applicable.
- 3
Include the steps of pressing and sintering the materials.
- 4
Discuss the magnetization process and its importance.
- 5
Conclude with quality control measures to ensure magnet specifications are met.
Example Answers
Permanent magnets are typically made from materials such as neodymium or ferrite. The process begins with selecting the right materials, after which they are powdered. These powders are then pressed into shape and sintered at high temperatures to create a solid structure. Afterward, the pressed magnets are magnetized using strong magnetic fields, and finally, quality control checks ensure they meet the required specifications.
Don't Just Read Magnet Maker Questions - Practice Answering Them!
Reading helps, but actual practice is what gets you hired. Our AI feedback system helps you improve your Magnet Maker interview answers in real-time.
Personalized feedback
Unlimited practice
Used by hundreds of successful candidates
How do you determine the specific magnetic requirements for a particular application?
How to Answer
- 1
Start by understanding the application and its operational environment.
- 2
Identify the required magnetic strength and direction based on use case.
- 3
Consider factors like size constraints and weight limitations.
- 4
Evaluate the magnetic material's properties suitable for the application.
- 5
Consult with cross-functional teams to align on requirements.
Example Answers
I begin by analyzing the application to identify its specific requirements, such as the magnetic strength needed and the environment it operates in. Then, I assess size and weight constraints before selecting suitable magnetic materials.
Discuss the different methods you use to test the strength and quality of magnets.
How to Answer
- 1
Mention common testing methods like pull strength tests and Gauss meter measurements.
- 2
Include the importance of verifying magnetic orientation and consistency across a batch.
- 3
Discuss any specific equipment or setups you use for testing.
- 4
Emphasize safety protocols when handling strong magnets during tests.
- 5
Relate previous experience or specific examples to showcase your expertise.
Example Answers
I typically use pull strength tests, where I measure the force required to pull a magnet away from a steel surface. This gives me a good idea of its holding power. Additionally, I utilize a Gauss meter to check the surface magnetic field strength of the magnets, ensuring they meet quality specifications.
What safety precautions do you take while working with magnet manufacturing equipment?
How to Answer
- 1
Always wear appropriate personal protective equipment like gloves and goggles.
- 2
Ensure all equipment is properly grounded to prevent electrical hazards.
- 3
Follow proper lockout/tagout procedures during maintenance and setup.
- 4
Be aware of magnetic field strength and keep sensitive electronics at a safe distance.
- 5
Regularly inspect equipment for any signs of wear or malfunction before use.
Example Answers
I always wear gloves and goggles while working with magnet manufacturing equipment to protect my hands and eyes. I also ensure that the equipment is grounded to reduce electrical hazards.
What software or tools do you use to design and model magnets?
How to Answer
- 1
Mention specific software you are familiar with
- 2
Explain how you use it in your design process
- 3
Highlight any collaborative tools used for team projects
- 4
Discuss any recent tools you've learned or want to explore
- 5
Emphasize the importance of precision and simulation.
Example Answers
I primarily use SolidWorks for designing magnets as it allows me to create detailed 3D models and run simulations on magnetic properties.
Explain how the type of magnet affects its applications in different industries.
How to Answer
- 1
Identify the main types of magnets: permanent, electromagnets, and temporary magnets.
- 2
Discuss specific industries and the types of magnets they use, such as electronics for permanent magnets.
- 3
Explain the advantages of each type of magnet in context, like strength or energy efficiency.
- 4
Use examples to illustrate your points, such as MRI machines using superconducting magnets.
- 5
Keep your explanation concise and focused on practical applications.
Example Answers
Permanent magnets are commonly used in electronics for applications like speakers and hard drives due to their reliability and efficiency.
What are the common methods used in the fabrication of industrial magnets?
How to Answer
- 1
Identify different types of magnets: permanent, temporary, and electromagnets.
- 2
Mention key fabrication methods: sintering, casting, and machining.
- 3
Discuss materials commonly used: neodymium, ferrite, and alnico.
- 4
Explain the importance of the magnetic field in the fabrication process.
- 5
Highlight quality control measures used in manufacturing.
Example Answers
Common methods of fabricating industrial magnets include sintering, which is popular for neodymium magnets, and casting used for ferrite magnets. I have experience with both processes, ensuring the materials are chosen based on the desired magnetic strength.
Describe how you would troubleshoot a machine that is malfunctioning during the magnet production process.
How to Answer
- 1
Start by identifying the symptoms of the malfunction.
- 2
Check machine settings and configurations for any discrepancies.
- 3
Inspect the machine components for wear and damage.
- 4
Consult the machine's error logs or indicators for specific issues.
- 5
Test the machine after making adjustments to ensure it's working properly.
Example Answers
First, I would observe the machine to identify the symptoms, such as unusual noises or failure to produce magnets. Then, I would check the settings to ensure they are correct. If everything seems set, I would look for any physical wear on the components, and check the error logs for any fault codes. Finally, I would make necessary repairs and run a test cycle to confirm it’s working again.
What is your understanding of the theories behind magnetic field generation and its applications?
How to Answer
- 1
Explain the basic principles of magnetism such as electromagnetism and permanent magnets.
- 2
Mention the key factors that influence magnetic fields, like current, coils, and materials.
- 3
Discuss practical applications such as motors, generators, and magnetic storage devices.
- 4
Use clear examples to illustrate your understanding of theory and practical use.
- 5
Be prepared to relate your knowledge to the specific requirements of the Magnet Maker role.
Example Answers
Magnetic fields are generated through electromagnetism, where electric current creates a magnetic field around a conductor. For example, in motors, this principle enables movement through magnetic forces. Additionally, permanent magnets, made from materials like neodymium, retain their magnetic properties and are used in speakers and sensors.
Don't Just Read Magnet Maker Questions - Practice Answering Them!
Reading helps, but actual practice is what gets you hired. Our AI feedback system helps you improve your Magnet Maker interview answers in real-time.
Personalized feedback
Unlimited practice
Used by hundreds of successful candidates
Situational Interview Questions
If you noticed that a batch of magnets did not meet quality standards, what steps would you take to address the issue?
How to Answer
- 1
Immediately stop the production line to prevent further defective magnets.
- 2
Conduct an investigation to determine the root cause of the quality issue.
- 3
Document the findings and communicate the issue to your supervisor.
- 4
Implement corrective actions based on the investigation results.
- 5
Monitor the next batches closely to ensure that quality standards are met.
Example Answers
If I noticed that a batch of magnets did not meet quality standards, I would stop the production line to prevent more defects. Then, I'd investigate the issue to find out what went wrong, document everything, and inform my supervisor. After that, I'd implement corrective measures and meticulously monitor the next batches for quality control.
Imagine a client demands a modification in the magnet specifications at the last minute. How would you handle this situation?
How to Answer
- 1
Stay calm and listen carefully to the client's request
- 2
Assess the feasibility of the modification with your team
- 3
Communicate any implications of the changes on time and cost
- 4
Propose a realistic timeline for implementing the changes
- 5
Reconfirm the client's needs and ensure mutual understanding
Example Answers
I would first listen to the client's modification request and confirm my understanding. Then, I would quickly consult with my team to see if we can accommodate the changes in the existing timeline. I would inform the client about any impacts on cost or delivery time and suggest a revised plan that meets their needs.
Don't Just Read Magnet Maker Questions - Practice Answering Them!
Reading helps, but actual practice is what gets you hired. Our AI feedback system helps you improve your Magnet Maker interview answers in real-time.
Personalized feedback
Unlimited practice
Used by hundreds of successful candidates
If you were given a limited budget for a project involving the creation of high-efficiency magnets, what strategies would you employ?
How to Answer
- 1
Identify cost-effective materials that optimize magnet efficiency.
- 2
Leverage existing technology and methods to minimize research costs.
- 3
Focus on prototyping with low-cost solutions before scaling up.
- 4
Collaborate with universities or institutions for shared resources.
- 5
Implement a phased approach to spread costs over time.
Example Answers
I would start by researching low-cost material alternatives like ferrites that still provide good efficiency. Leveraging existing methods will help avoid high initial R&D costs. I'd also create a prototype using these materials to test effectiveness before committing larger budget allocations.
What would you do if you identified a potential improvement in the magnet-making process that could save time and resources?
How to Answer
- 1
Assess the potential improvement thoroughly
- 2
Consider how the change impacts current processes
- 3
Communicate your findings to your team
- 4
Suggest a trial implementation for feedback
- 5
Document the results and refine the approach
Example Answers
I would carefully evaluate the improvement to ensure it is viable. Then, I would share my insights with my team and propose a small-scale trial to assess its effectiveness.
If your team was divided on the approach to take for a new magnet design, how would you facilitate a resolution?
How to Answer
- 1
Listen to each team member's perspective to understand their viewpoints
- 2
Encourage an open discussion where everyone can share their ideas
- 3
Identify common goals and objectives to align the team's focus
- 4
Propose methods to test or prototype different approaches
- 5
Facilitate a consensus-building session to agree on a way forward
Example Answers
I would start by listening to everyone's opinions and ensuring that all ideas are shared openly. Then, I would try to identify our shared goals and build a discussion around how best to achieve them.
What would your response be if a magnet developed a serious defect after it had been shipped to a client?
How to Answer
- 1
Acknowledge the issue promptly and take responsibility.
- 2
Communicate clearly with the client about the defect and steps taken.
- 3
Propose a corrective action, such as repair or replacement.
- 4
Ensure to follow up with the client to confirm satisfaction post-resolution.
- 5
Document the defect and investigate the cause to prevent future issues.
Example Answers
I would first reach out to the client immediately to acknowledge the defect and express my concern. I would explain that we take such matters seriously and offer to replace the defective magnet or arrange for a repair. I'd follow up after the resolution to ensure they are satisfied and gather feedback to improve our processes.
How would you manage a situation where you faced a shortage of key materials needed for magnet production?
How to Answer
- 1
Assess the impact of the shortage on production schedules
- 2
Identify alternative materials or suppliers that could be used
- 3
Communicate proactively with the team and stakeholders about the issue
- 4
Develop a contingency plan to minimize disruption
- 5
Monitor inventory levels more closely to prevent future shortages
Example Answers
If faced with a shortage of key materials for magnet production, I would first evaluate how this impacts our overall production timeline. I would then look for alternative suppliers or materials that could substitute until we resolve the shortage. Communication with my team and management is crucial so we can all adjust our strategies accordingly. Lastly, I would implement tighter inventory controls to better forecast our material needs in the future.
How would you prioritize your workload if you had to meet tight deadlines on multiple magnet projects?
How to Answer
- 1
Identify the urgency and impact of each project.
- 2
Break down projects into smaller tasks and set milestones.
- 3
Communicate with team members to align on priorities.
- 4
Use a prioritization matrix to assess and rank tasks.
- 5
Stay flexible to adjust priorities as necessary.
Example Answers
I would first assess the deadlines and requirements for each project. Then, I would break them down into smaller tasks and rank them based on urgency and impact. By communicating with my team, we can ensure we are focused on the most critical tasks, and I would use a prioritization matrix to help visualize our workload.
Magnet Maker Position Details
Related Positions
- Magnetizer
- Part Maker
- Chemical Maker
- Cord Maker
- Cap Maker
- Belt Maker
- Heading Maker
- Rack Maker
- Tube Maker
- Puppet Maker
Similar positions you might be interested in.
Ace Your Next Interview!
Practice with AI feedback & get hired faster
Personalized feedback
Used by hundreds of successful candidates
Ace Your Next Interview!
Practice with AI feedback & get hired faster
Personalized feedback
Used by hundreds of successful candidates