Top 30 Belt Maker Interview Questions and Answers [Updated 2025]
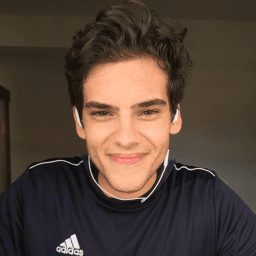
Andre Mendes
•
March 30, 2025
Preparing for a Belt Maker interview? Our updated guide delivers the most common questions you might face, complete with example answers and expert tips to help you respond effectively. Whether you're new to the field or an experienced artisan, this resource is designed to enhance your confidence and readiness. Dive in to refine your interview skills and stand out as the ideal candidate for the role.
Download Belt Maker Interview Questions in PDF
To make your preparation even more convenient, we've compiled all these top Belt Makerinterview questions and answers into a handy PDF.
Click the button below to download the PDF and have easy access to these essential questions anytime, anywhere:
List of Belt Maker Interview Questions
Situational Interview Questions
You notice that a batch of belts does not meet quality standards. What steps would you take to address the issue?
How to Answer
- 1
Identify the specific quality issues with the batch.
- 2
Stop production if necessary to prevent further defects.
- 3
Communicate the issue to your supervisor and team.
- 4
Assess the root cause of the quality issue.
- 5
Implement corrective measures and document the process.
Example Answers
I would first identify the specific defects in the belts, such as stitching problems or material flaws. Then, I would stop production to prevent any more faulty belts. I would inform my supervisor about the findings, and we would work together to determine the root cause and implement corrective actions.
If a customer is unhappy with a belt order, how would you handle the situation to ensure their satisfaction?
How to Answer
- 1
Listen actively to the customer's concerns to understand the issue fully
- 2
Apologize sincerely for the inconvenience caused
- 3
Offer a solution, such as a replacement or refund
- 4
Communicate clearly the steps you will take to resolve the issue
- 5
Follow up with the customer after the resolution to ensure satisfaction
Example Answers
I would start by listening to the customer to understand what went wrong. Then, I would apologize for the inconvenience and offer to replace the belt or issue a refund. I would make sure to communicate the resolution steps clearly and follow up to ensure they are satisfied with the outcome.
Don't Just Read Belt Maker Questions - Practice Answering Them!
Reading helps, but actual practice is what gets you hired. Our AI feedback system helps you improve your Belt Maker interview answers in real-time.
Personalized feedback
Unlimited practice
Used by hundreds of successful candidates
You are faced with an urgent order for a large quantity of belts with a tight deadline. How would you prioritize your tasks?
How to Answer
- 1
Assess the order details and quantity needed
- 2
Identify materials and tools required for production
- 3
Break down the production process into manageable tasks
- 4
Assign tasks based on team strengths and availability
- 5
Establish a timeline and monitor progress regularly
Example Answers
First, I would review the order to understand the specifications and quantities required. Then, I would gather my team to list all materials needed and quickly source them. I would break down the production steps and assign tasks to my team based on their skills to maximize efficiency. Finally, I would set up checkpoints to ensure we are on track to meet the deadline.
A client asks for a bespoke belt design that is outside your usual style. How do you approach this request?
How to Answer
- 1
Listen carefully to the client's vision and preferences
- 2
Ask questions to clarify specific elements they want
- 3
Research styles and materials you are unfamiliar with
- 4
Sketch out ideas to visualize the design together
- 5
Ensure the design meets both the client's desires and your craftsmanship standards
Example Answers
I would start by listening to the client's ideas and asking detailed questions about what they envision. Then, I would research the style they want and gather inspiration to explore materials. I would sketch a few concepts to ensure we are on the same page before finalizing the design.
If you are using a new machine for the first time in the belt-making process, what steps would you take to ensure safety?
How to Answer
- 1
Read the machine's operational manual thoroughly before use
- 2
Perform a safety inspection on the machine to check for any issues
- 3
Wear appropriate personal protective equipment (PPE) such as gloves and safety goggles
- 4
Get familiar with the emergency stop functions and safety features of the machine
- 5
Ask a supervisor or experienced operator for a walkthrough on the machine's operation
Example Answers
I would start by reading the operational manual to understand how the machine works. Then, I would do a safety inspection to ensure everything is in proper order. Wearing my PPE, I would familiarize myself with the emergency stop features and, if possible, seek advice from a more experienced operator.
If you and a colleague disagree on the approach to making a belt, how would you resolve it?
How to Answer
- 1
Listen actively to your colleague's perspective and understand their reasoning
- 2
Present your own approach clearly, focusing on the benefits it brings
- 3
Suggest a compromise or a trial of both methods to see which works better
- 4
Seek input from a third party if needed to provide an unbiased opinion
- 5
Stay professional and focus on finding a solution rather than winning the argument
Example Answers
I would start by listening to my colleague’s ideas and understanding their reasoning. Then I would explain my approach and emphasize why I believe it is effective. If we still differ, I would suggest we try both methods on a small scale to determine which yields better results.
After a product launch, you receive mixed feedback on a new belt style. What actions would you take next?
How to Answer
- 1
Analyze the feedback for common themes and specific issues
- 2
Engage with customers to gain detailed insights about their experience
- 3
Collaborate with the design team to address any design flaws
- 4
Develop a plan for improvements or adjustments based on findings
- 5
Communicate updates to stakeholders to ensure transparency
Example Answers
I would first analyze the feedback to identify any common issues. Then, I would reach out to customers for more detailed insights. After that, I would work with the design team to address any noted flaws and draft a plan for product improvements.
You find that the materials you need to make specific belts are running low. How would you handle procurement?
How to Answer
- 1
Assess current inventory levels to identify exact shortages
- 2
Contact suppliers promptly to check availability and lead times
- 3
Consider alternative materials if the main components are delayed
- 4
Communicate with your team about potential production delays
- 5
Establish a reorder point to prevent future shortages
Example Answers
I would first check our inventory to see which materials are low. Then, I would reach out to our suppliers to see if they can deliver more stock in time for our production schedule.
If you observe unsafe practices in the workshop while making belts, what would you do?
How to Answer
- 1
Identify the unsafe practice immediately
- 2
Ensure your own safety first
- 3
Communicate your observations to a supervisor or manager
- 4
Encourage team members to follow safety protocols
- 5
Suggest a safety meeting to discuss improvements
Example Answers
I would first assess the situation to ensure I'm safe, then report the unsafe practice to my supervisor so they can address it properly.
How would you respond if your supervisor asked for suggestions to improve the belt production process?
How to Answer
- 1
Analyze the current process to identify any bottlenecks.
- 2
Consider the materials used and suggest alternatives that could reduce costs.
- 3
Think about the technology in use and whether automation could improve efficiency.
- 4
Gather feedback from coworkers to understand their challenges.
- 5
Be ready to present your suggestions clearly and with evidence of potential benefits.
Example Answers
I would first analyze the current belt production workflow and identify areas where we see delays or inefficiencies. For example, if we notice that certain materials frequently cause holdups, I would suggest exploring alternative materials that could speed up production.
Don't Just Read Belt Maker Questions - Practice Answering Them!
Reading helps, but actual practice is what gets you hired. Our AI feedback system helps you improve your Belt Maker interview answers in real-time.
Personalized feedback
Unlimited practice
Used by hundreds of successful candidates
Behavioral Interview Questions
Can you describe a time when you had to work closely with a team to complete a belt-making project? What was your role?
How to Answer
- 1
Choose a specific project you worked on with a team.
- 2
Mention your specific role and contributions.
- 3
Highlight collaboration with team members.
- 4
Discuss any challenges faced and how you overcame them.
- 5
Conclude with the successful outcome of the project.
Example Answers
In a recent belt-making project, I was part of a four-person team tasked with creating a custom belt for a client. My role was to design the belt layout and coordinate material selection. We communicated daily about our progress and offered feedback to each other. We encountered a delay in material delivery, but I suggested alternate suppliers, which helped us complete the project on time. The client was thrilled with the final product, which boosted our team's reputation.
Tell me about a time you encountered an issue with the quality of a belt you were making. How did you resolve it?
How to Answer
- 1
Identify a specific quality issue you faced.
- 2
Explain the steps you took to assess the problem.
- 3
Describe the solution you implemented and the outcome.
- 4
Highlight any skills or teamwork used to resolve the issue.
- 5
Conclude with what you learned from the experience.
Example Answers
In one project, I noticed that the stitching on a batch of belts was uneven. To resolve this, I carefully inspected each belt and identified the faulty machine setup. I recalibrated the stitching machine and conducted a second quality check. This ensured the remaining belts met our standards, and we were able to deliver them on time. I learned the importance of regular machine maintenance.
Don't Just Read Belt Maker Questions - Practice Answering Them!
Reading helps, but actual practice is what gets you hired. Our AI feedback system helps you improve your Belt Maker interview answers in real-time.
Personalized feedback
Unlimited practice
Used by hundreds of successful candidates
Describe a situation where attention to detail was crucial in your belt-making process. What did you do?
How to Answer
- 1
Select a specific project where detail was important
- 2
Explain the exact detail you focused on
- 3
Describe the steps you took to ensure high quality
- 4
Mention the outcome or feedback you received
- 5
Keep it concise and focused on your actions
Example Answers
In a project where I made custom leather belts, I noticed the stitching was uneven. I took the time to re-measure the spacing and used a consistent distance for each stitch. This ensured the belt was both functional and visually appealing. The client praised the quality and attention to detail.
Give an example of how you managed your time effectively during a busy production period while making belts.
How to Answer
- 1
Identify a specific busy period and describe your role.
- 2
Explain the planning steps you took before production started.
- 3
Mention prioritization of tasks and how you delegated work if possible.
- 4
Highlight any tools or methods you used for tracking progress.
- 5
Conclude with the outcome and what you learned from the experience.
Example Answers
During the holiday season, I led a team that was overwhelmed with belt orders. I started by mapping out our production schedule and breaking it into daily tasks. I prioritized high-demand styles and delegated responsibilities, ensuring everyone had clear goals. We used a shared spreadsheet to track our progress, which kept us on target and improved communication. As a result, we met our deadlines and even had extra inventory.
Describe a time when you had to learn a new skill for belt making. How did you go about it?
How to Answer
- 1
Identify a specific skill relevant to belt making.
- 2
Explain why this skill was important for your work.
- 3
Describe your learning process in detail.
- 4
Mention any resources or training you utilized.
- 5
Conclude with how this skill improved your work or contributed to the team.
Example Answers
I needed to learn how to use a new stitching machine for belt making. I realized this skill was crucial for improving stitching efficiency. I watched online tutorials and then practiced on a sample belt over a weekend. I also consulted with a team member who was experienced in using the machine. This skill allowed us to increase our production speed, which benefited the whole team.
Can you give an example of how you provided excellent customer service in your previous belt-making roles?
How to Answer
- 1
Think of a specific instance where you directly helped a customer.
- 2
Describe the situation, the action you took, and the result.
- 3
Focus on how your actions improved customer satisfaction.
- 4
Use clear and concise language to convey your story.
- 5
Highlight any feedback or follow-up from the customer that indicates success.
Example Answers
In my last position, a customer was unhappy with a belt color mismatch. I listened to their concerns, offered to redo the belt in their preferred color at no extra cost, and expedited the order. The customer appreciated the quick turnaround and left a positive review.
Tell me about a time when you had to adapt your methods or techniques to meet a challenge in belt making.
How to Answer
- 1
Identify a specific challenge you faced in belt making.
- 2
Describe the original method you used and why it was not sufficient.
- 3
Explain how you adapted your methods or techniques in detail.
- 4
Highlight the outcome of your new approach and any lessons learned.
- 5
Keep your answer focused on your personal contribution and impact.
Example Answers
In a project to produce a custom belt design, we faced a material shortage that impacted our timeline. Initially, I used a standard leather, but when that ran out, I quickly sourced a different, compatible material. I adjusted my cutting and stitching techniques to accommodate the new material's properties. This change allowed us to meet the deadline and successfully deliver a quality product.
Have you ever had to lead a project or team in belt making? What challenges did you face?
How to Answer
- 1
Start with a brief overview of the project and your role.
- 2
Clearly explain the specific challenges you encountered.
- 3
Describe the steps you took to address those challenges.
- 4
Highlight the outcome of the project and any skills you developed.
- 5
Reflect on what you learned from the experience.
Example Answers
In my last role, I led a team to develop a new line of belts. One major challenge was sourcing high-quality materials on a tight deadline. I coordinated with suppliers and negotiated faster delivery, which helped us meet our launch date. As a result, the new line was successful and increased our sales by 20%.
Tell me about a difficult situation in your belt-making career and how you overcame it.
How to Answer
- 1
Choose a specific situation that highlights a challenge in your belt-making process.
- 2
Explain the issue clearly, including the context and what made it difficult.
- 3
Outline the steps you took to address the problem and resolve it.
- 4
Include the outcome and what you learned from the experience.
- 5
Make sure to relate how this experience makes you a better candidate for the position.
Example Answers
While working on a custom belt order, I realized I had miscalculated the measurements, resulting in the wrong size. I immediately contacted the client to explain the situation and offered a free replacement. I adjusted the patterns, used my spare materials, and completed the new belt within two days. The client appreciated my honesty and promptness, leading to repeat business.
Don't Just Read Belt Maker Questions - Practice Answering Them!
Reading helps, but actual practice is what gets you hired. Our AI feedback system helps you improve your Belt Maker interview answers in real-time.
Personalized feedback
Unlimited practice
Used by hundreds of successful candidates
Technical Interview Questions
What types of materials do you prefer to use when making belts, and why are they suitable?
How to Answer
- 1
Identify 2 or 3 materials you prefer for belts.
- 2
Explain the properties of each material.
- 3
Discuss the suitability for specific uses or styles.
- 4
Mention durability, aesthetics, and comfort in your reasoning.
- 5
Align your response with the company's brand or product line.
Example Answers
I prefer using high-quality leather because it is durable and ages well, making it ideal for formal belts. Additionally, leather provides a classic look that aligns with the brand's style.
What types of machinery and tools have you worked with in the belt-making process?
How to Answer
- 1
List specific machines used, like sewing machines or cutting tools.
- 2
Mention any specialized tools unique to belt making.
- 3
Highlight your experience level with each type of machinery.
- 4
Discuss safety measures you follow when using machinery.
- 5
Speak about any maintenance experience you have with the tools.
Example Answers
I have worked with industrial sewing machines for stitching leather belts, a hydraulic cutting machine for precision cutting, and hand tools like awls and riveters. I'm very familiar with safety protocols, ensuring that all tools are properly maintained.
Don't Just Read Belt Maker Questions - Practice Answering Them!
Reading helps, but actual practice is what gets you hired. Our AI feedback system helps you improve your Belt Maker interview answers in real-time.
Personalized feedback
Unlimited practice
Used by hundreds of successful candidates
Can you explain the process you follow when cutting and stitching leather for belts?
How to Answer
- 1
Start by describing the type of leather selected based on the belt design.
- 2
Explain the measurement process to ensure accurate cutting.
- 3
Outline the cutting technique you use, emphasizing precision.
- 4
Discuss the stitching method, including thread choice and stitch type.
- 5
Mention finishing touches that enhance durability and appearance.
Example Answers
I start by choosing high-quality leather that's appropriate for the belt design. I carefully measure the length and width needed, marking it precisely. I then use a sharp knife or a leather cutter to ensure clean edges. For stitching, I prefer using a strong polyester thread and a saddle stitch for added strength. Finally, I finish the edges and add a sealant for durability.
What finishing techniques do you use to ensure the quality and durability of the belts you make?
How to Answer
- 1
Mention specific finishing techniques you use, like edge sealing or dyeing.
- 2
Emphasize the importance of material selection for durability.
- 3
Discuss any tools or machines that enhance finishing quality.
- 4
Include examples of quality checks you implement during the finishing process.
- 5
Talk about how finishing affects the overall aesthetics and function of the belt.
Example Answers
To ensure quality, I use edge sealing to prevent fraying and apply a high-quality dye that enhances color and durability. I also inspect each belt after finishing for consistency and overall appearance.
How do you approach the design process when creating a new belt? What considerations do you take into account?
How to Answer
- 1
Understand the target market and customer needs
- 2
Choose appropriate materials for durability and style
- 3
Consider functionality such as width and buckle type
- 4
Incorporate current fashion trends and colors
- 5
Prototype and test for comfort and practicality
Example Answers
I start by researching the target audience to understand their preferences. Then, I select high-quality materials that balance durability and aesthetics. I also take into account the latest fashion trends when deciding on colors and styles, followed by creating prototypes to ensure comfort and functionality.
What sustainable practices do you incorporate into your belt-making process?
How to Answer
- 1
Discuss the materials you use and their sources.
- 2
Mention any waste reduction techniques in production.
- 3
Highlight energy-efficient equipment or practices.
- 4
Share how you encourage recycling or upcycling in your process.
- 5
Include any partnerships with eco-friendly suppliers.
Example Answers
I use organic leather sourced from local farms that practice sustainable grazing, reducing transportation emissions.
What types of stitches do you use in belt making, and what situations would call for different types?
How to Answer
- 1
Identify common stitch types used in belt making such as saddle stitch and machine stitch.
- 2
Explain the strength and aesthetic differences between stitches.
- 3
Discuss specific situations for each stitch type, like durability for heavy belts or decoration for fashion belts.
- 4
Mention any special techniques or tools used for each stitch type.
- 5
Keep your answer concise but informative to show your expertise.
Example Answers
I typically use saddle stitch for its strength and durability, especially for heavy-duty belts. For fashion belts, I opt for a decorative machine stitch that adds visual appeal while being quicker to produce.
How do you handle customizations requested by clients when making belts?
How to Answer
- 1
Listen carefully to the client's needs and specifications.
- 2
Clarify any details or requirements to ensure understanding.
- 3
Provide options based on their requests while suggesting your expertise.
- 4
Communicate a timeline and any costs associated with customizations.
- 5
Follow up with the client during the process to ensure satisfaction.
Example Answers
I start by listening to the client's specific customization requests, asking clarifying questions to fully understand their vision. I then present them with options based on their requests and my experience, along with timelines and costs, ensuring transparency throughout the process.
What is your experience with creating patterns for belts, and what tools do you use?
How to Answer
- 1
Describe your previous experience with belt pattern making.
- 2
Mention specific tools you use, such as CAD software or drafting tools.
- 3
Provide an example of a belt pattern you designed and its purpose.
- 4
Highlight any special techniques you employ or challenges you've overcome.
- 5
Discuss how you ensure accuracy and quality in your patterns.
Example Answers
I have been designing belt patterns for five years, primarily using Adobe Illustrator for precise designs. One notable project was a line of customizable belts for a retail client, where I created unique patterns that catered to their branding needs while ensuring durability.
Can you explain how you approach adding decorative elements to belts, such as patchwork or embossing?
How to Answer
- 1
Start by discussing your design process and inspiration sources.
- 2
Mention the materials you prefer for durability and aesthetics.
- 3
Explain the techniques you use, such as hand tooling for embossing.
- 4
Highlight your attention to detail in selecting patterns and colors.
- 5
Talk about how you ensure the decorative elements complement the overall belt design.
Example Answers
I begin by gathering inspiration from fashion trends and nature. I prefer using high-quality leather for both patchwork and embossing to ensure durability. For embossing, I use hand tooling techniques to create intricate designs. I pay close attention to how colors and patterns work together, ensuring they enhance the overall design rather than overwhelm it.
Don't Just Read Belt Maker Questions - Practice Answering Them!
Reading helps, but actual practice is what gets you hired. Our AI feedback system helps you improve your Belt Maker interview answers in real-time.
Personalized feedback
Unlimited practice
Used by hundreds of successful candidates
Belt Maker Position Details
Related Positions
- Leather Belt Maker
- Belt Tender
- Cord Maker
- Part Maker
- Leather Tooler
- Basket Maker
- Leather Worker
- Tire Builder
- Tube Maker
- Cap Maker
Similar positions you might be interested in.
Ace Your Next Interview!
Practice with AI feedback & get hired faster
Personalized feedback
Used by hundreds of successful candidates
Ace Your Next Interview!
Practice with AI feedback & get hired faster
Personalized feedback
Used by hundreds of successful candidates