Top 32 Gold Stamper Interview Questions and Answers [Updated 2025]
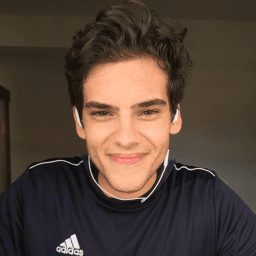
Andre Mendes
•
March 30, 2025
Looking to ace your Gold Stamper interview? This post equips you with the most common questions you'll encounter in this specialized role, offering insightful example answers and practical tips to help you respond confidently. Whether you're a seasoned professional or new to the field, our updated guide for 2025 ensures you're well-prepared to impress and succeed in your interview.
Download Gold Stamper Interview Questions in PDF
To make your preparation even more convenient, we've compiled all these top Gold Stamperinterview questions and answers into a handy PDF.
Click the button below to download the PDF and have easy access to these essential questions anytime, anywhere:
List of Gold Stamper Interview Questions
Behavioral Interview Questions
Can you describe a time when you successfully stamped gold with precision? What techniques did you use?
How to Answer
- 1
Think of a specific project or experience where you stamped gold.
- 2
Mention the tools or techniques you used during the process.
- 3
Explain how you ensured precision and quality in your work.
- 4
Include any challenges faced and how you overcame them.
- 5
Reflect on the outcome and any skills you gained from the experience.
Example Answers
In my previous role, I worked on a batch of custom gold pieces. I used a hydraulic press for even pressure and temperature control to ensure precision. I double-checked measurements and conducted a test run before the full batch. The result was high-quality gold stamps that met all specifications.
Tell me about a time you worked as part of a team to complete a gold stamping project. What was your role?
How to Answer
- 1
Identify a specific team project
- 2
Describe your role and contributions
- 3
Highlight teamwork and collaboration
- 4
Mention any challenges faced and how you overcame them
- 5
Conclude with the outcome and what you learned
Example Answers
In a recent gold stamping project, I was the lead designer. I collaborated closely with the stamping technicians to ensure the design was feasible and produced high-quality results. We faced a challenge with material compatibility, but by communicating effectively, we found a suitable alternative. The project was a success, resulting in increased client satisfaction and repeat business.
Don't Just Read Gold Stamper Questions - Practice Answering Them!
Reading helps, but actual practice is what gets you hired. Our AI feedback system helps you improve your Gold Stamper interview answers in real-time.
Personalized feedback
Unlimited practice
Used by hundreds of successful candidates
Describe a situation where you had a disagreement with a colleague about a gold stamping technique. How did you resolve it?
How to Answer
- 1
Identify the specific disagreement and its impact on your work.
- 2
Explain your approach to listening actively to your colleague's perspective.
- 3
Share how you discussed your viewpoints constructively.
- 4
Suggest how you reached a consensus or compromise.
- 5
Highlight any positive outcomes from resolving the disagreement.
Example Answers
In a project, my colleague and I disagreed on the temperature settings for gold stamping. I listened to her method and explained my concerns about durability. We tested both techniques and found a middle ground that improved our results, leading to a successful final product.
Can you give an example of when you had to quickly adapt to a new gold stamping machine or technique?
How to Answer
- 1
Begin with the context of the situation to set the stage.
- 2
Describe the new machine or technique and why it was necessary to adapt quickly.
- 3
Focus on your specific actions taken to adapt and learn the new system.
- 4
Mention any challenges faced and how you overcame them.
- 5
Conclude with the positive outcome or learning from the experience.
Example Answers
At my previous job, we received a new gold stamping machine that required us to update our production process. I quickly familiarized myself with the machine by reviewing the manual and watching training videos provided by the manufacturer. Within a week, I was able to operate it efficiently, resulting in a 20% increase in output while maintaining quality standards.
Have you ever trained someone in gold stamping techniques? How did you approach the training?
How to Answer
- 1
Explain your experience with gold stamping first.
- 2
Describe the training methods you used, such as demonstrations or hands-on practice.
- 3
Highlight the importance of patience and feedback during training.
- 4
Share an example of a challenge faced during training and how you resolved it.
- 5
Emphasize the results or improvements in the trainee's skills.
Example Answers
Yes, I trained a new hire in gold stamping techniques by starting with a demonstration of the basic processes. I provided hands-on practice and encouraged them to ask questions. I noticed they struggled with the heat settings, so I guided them through adjustments and gave constructive feedback. By the end, their skills improved significantly, and they were able to produce high-quality samples.
Tell me about a time you contributed to improving a gold stamping process. What did you do?
How to Answer
- 1
Identify a specific improvement you implemented.
- 2
Explain the problem the process had before your intervention.
- 3
Describe the actions you took in detail.
- 4
Quantify the impact of your improvement if possible.
- 5
Conclude with how this experience shaped your approach to processes.
Example Answers
At my last position, I noticed the gold stamping process was slow due to frequent machine jams. I analyzed the situation and replaced an outdated part that was causing the jams. After the upgrade, production time improved by 20% and downtime decreased significantly.
Can you provide an example of a project where your attention to detail in gold stamping made a significant difference?
How to Answer
- 1
Choose a specific project or task to discuss
- 2
Describe the initial challenges or requirements
- 3
Highlight the specific details you focused on
- 4
Explain the impact of your attention to detail
- 5
Conclude with the outcome and any positive feedback received
Example Answers
In a recent project for a luxury brand, I was tasked with gold stamping their logo on limited edition packaging. I noticed that the alignment of the stamp was slightly off in initial samples. By meticulously adjusting the positioning, the final product achieved perfect alignment, which enhanced the overall look and received positive comments from the client and customers.
Describe a time when you had to lead a project in gold stamping. What challenges did you face?
How to Answer
- 1
Think of a specific project where you were the lead.
- 2
Identify the main challenges you encountered during the project.
- 3
Focus on how you addressed these challenges.
- 4
Highlight the outcome and what you learned.
- 5
Use the STAR method: Situation, Task, Action, Result.
Example Answers
In my last project, I led the gold stamping of a new product line. A major challenge was ensuring the precision of the stamp on curved surfaces. I coordinated with the design team to adjust the tooling and conducted several rounds of testing. This resulted in a successful launch with 100% compliance to quality standards.
What drives you to excel in gold stamping, and how do you stay motivated during repetitive tasks?
How to Answer
- 1
Identify a personal passion or interest in craftsmanship.
- 2
Mention the pride of producing high-quality work.
- 3
Discuss setting personal goals for improvement.
- 4
Explain how you maintain focus and energy during repetitive tasks.
- 5
Share any techniques for making routines more engaging.
Example Answers
I excel in gold stamping because I have a deep passion for craftsmanship. Knowing that my work contributes to beautiful products motivates me greatly. During repetitive tasks, I set small goals for myself, like improving speed or precision, which helps keep my focus.
Don't Just Read Gold Stamper Questions - Practice Answering Them!
Reading helps, but actual practice is what gets you hired. Our AI feedback system helps you improve your Gold Stamper interview answers in real-time.
Personalized feedback
Unlimited practice
Used by hundreds of successful candidates
Technical Interview Questions
What types of tools and equipment do you find most effective for gold stamping, and why?
How to Answer
- 1
Identify specific tools used in gold stamping processes.
- 2
Explain the function of each tool and its importance.
- 3
Mention any personal experiences with these tools.
- 4
Include how certain equipment affects the quality of the final product.
- 5
Highlight any innovations or techniques you've adopted.
Example Answers
I find using a heated stamping die and a quality gold foil the most effective. The heated die ensures that the gold adheres well to the material, providing a crisp finish. My experience shows that precision dies can significantly enhance detail and reduce waste.
Explain the step-by-step process you follow in gold stamping from design to final product.
How to Answer
- 1
Start with design layout and mockup creation.
- 2
Select appropriate materials for the stamping process.
- 3
Prepare the stamping die and set up the machine.
- 4
Conduct a test stamp for quality assurance.
- 5
Finish with packaging and quality control before delivery.
Example Answers
First, I create a design layout and mockup using software to visualize the final product. Next, I select high-quality materials such as leather or cardstock suited for gold stamping. I then prepare the stamping die and set up the machine, ensuring everything is calibrated correctly. I always conduct a test stamp to check for quality and adjust as needed. Finally, I package the product carefully and perform a quality check before delivering to the client.
Don't Just Read Gold Stamper Questions - Practice Answering Them!
Reading helps, but actual practice is what gets you hired. Our AI feedback system helps you improve your Gold Stamper interview answers in real-time.
Personalized feedback
Unlimited practice
Used by hundreds of successful candidates
What are the key properties of gold that you must consider when stamping?
How to Answer
- 1
Discuss gold's malleability and ductility for shaping.
- 2
Mention gold's corrosion resistance for durability.
- 3
Consider its weight and density for handling.
- 4
Talk about the importance of purity in quality stamping.
- 5
Highlight the thermal conductivity for processing temperatures.
Example Answers
When stamping gold, it's essential to consider its malleability and ductility, which allow it to be shaped without breaking. Additionally, gold's corrosion resistance ensures that the stamped items will last over time. Purity is critical as well; higher purity leads to better quality products.
What safety precautions do you take when working with gold stamping machinery?
How to Answer
- 1
Always wear appropriate personal protective equipment such as gloves and safety goggles.
- 2
Ensure that the machinery is well-maintained and regularly inspected for safety issues.
- 3
Keep the work area clean and free of hazards to prevent accidents.
- 4
Follow all manufacturer guidelines and operational procedures for the machinery.
- 5
Be aware of emergency shut-off procedures and how to respond to accidents.
Example Answers
I always wear gloves and safety goggles to protect myself from flying debris and sharp edges. I also ensure the machinery is well-maintained.
How do you ensure the accuracy of measurements in your gold stamping work?
How to Answer
- 1
Always use calibrated tools for measurement.
- 2
Double-check measurements before proceeding with stamping.
- 3
Take measurements in a controlled environment to avoid errors.
- 4
Regularly maintain and verify the accuracy of equipment.
- 5
Document measurement processes for consistency and review.
Example Answers
I ensure accuracy by using calibrated calipers and checking each measurement twice before stamping.
What finishing techniques do you use after gold stamping to enhance the product's appearance?
How to Answer
- 1
Mention the importance of achieving a professional finish.
- 2
Discuss techniques like embossing or debossing for added texture.
- 3
Include options for coatings or laminations to improve durability.
- 4
Talk about using color contrast to highlight the gold stamping.
- 5
Explain the significance of quality control in the finishing process.
Example Answers
After gold stamping, I often use embossing to create a raised texture that enhances the visual appeal. Additionally, I apply a protective laminate to ensure longevity.
How do you approach designing patterns for gold stamping?
How to Answer
- 1
Understand the purpose and functionality of the design.
- 2
Research current trends and materials used in gold stamping.
- 3
Sketch multiple ideas and explore variations before finalizing.
- 4
Consider the surface texture and finish for the best effect.
- 5
Test your designs with samples to see how they translate in practice.
Example Answers
I start by understanding the client's needs and the product's purpose. Then I research trends in gold stamping to inspire my ideas. I sketch several variations and consider how the texture will affect the final look.
What troubleshooting steps do you take when a gold stamping machine malfunctions?
How to Answer
- 1
Check the machine's power supply to ensure it is receiving electricity.
- 2
Inspect the settings and parameters to make sure they are correct for operation.
- 3
Examine the machine for any visible issues such as jams or misalignments.
- 4
Refer to the machine's manual for troubleshooting guidelines specific to the model.
- 5
Test the machine after making adjustments to see if the issue is resolved.
Example Answers
First, I ensure that the power supply is functioning properly. Then I check the machine settings for any discrepancies. If everything seems correct, I inspect for jams or mechanical issues and consult the manual if necessary.
How do you maintain and care for the gold stamping equipment you use?
How to Answer
- 1
Regularly clean the stamping plates to remove any residue.
- 2
Lubricate moving parts as recommended in the equipment manual.
- 3
Check and tighten screws and bolts to ensure stability before each use.
- 4
Store equipment in a dry, dust-free environment to prevent corrosion.
- 5
Perform routine inspections to identify any wear or damage early.
Example Answers
I ensure that the stamping plates are cleaned after each use to avoid any build-up of residue. I also lubricate the moving parts according to the manufacturer's recommendations to keep everything running smoothly.
Don't Just Read Gold Stamper Questions - Practice Answering Them!
Reading helps, but actual practice is what gets you hired. Our AI feedback system helps you improve your Gold Stamper interview answers in real-time.
Personalized feedback
Unlimited practice
Used by hundreds of successful candidates
How do you ensure color consistency when stamping gold with mixed materials?
How to Answer
- 1
Use high-quality, consistent materials for stamping
- 2
Regularly calibrate stamping equipment to maintain precision
- 3
Conduct test stamps to check color results before full production
- 4
Monitor environmental factors like temperature and humidity that may affect color
- 5
Document procedures for mixing materials to replicate successful outcomes
Example Answers
I ensure color consistency by using high-quality stamping materials and regularly calibrating our stamping press. Before starting production, I conduct test stamps to check the color alignment and make adjustments if necessary.
What challenges do you face when customizing stamps for unique gold designs?
How to Answer
- 1
Identify specific technical challenges such as material hardness or design intricacy.
- 2
Discuss the importance of precision and attention to detail in gold stamping.
- 3
Mention the need for creativity when adapting designs to customer requests.
- 4
Explain how customer expectations can sometimes lead to conflicts with production limitations.
- 5
Highlight the necessity of ongoing communication with clients to refine designs.
Example Answers
One challenge I face is the hardness of gold, which requires precise tooling to achieve clean impressions. I also need to balance the client's unique design with what is feasible to produce.
Situational Interview Questions
If a gold stamping project is falling behind schedule, what steps would you take to ensure timely completion?
How to Answer
- 1
Assess the current progress and identify specific bottlenecks.
- 2
Communicate with the team to gather input on obstacles.
- 3
Reprioritize tasks and adjust deadlines where feasible.
- 4
Implement additional resources or overtime if necessary.
- 5
Monitor progress closely and adjust the plan as needed.
Example Answers
First, I would assess the project timeline and identify the specific areas that are causing delays. Next, I would communicate with my team to hear their insights on any obstacles. Based on this, I would reprioritize tasks and adjust deadlines if possible. If needed, I would allocate additional resources to keep us on track, and I would closely monitor progress day by day.
Imagine you notice that the stamped gold items have a defect. What would be your immediate actions?
How to Answer
- 1
Assess the severity of the defect immediately.
- 2
Isolate the defective items to prevent further errors.
- 3
Notify your supervisor about the defect right away.
- 4
Document the defect details and any potential causes.
- 5
Analyze the processes that led to the defect for future prevention.
Example Answers
I would first assess how serious the defect is. Then I would set aside the affected items to ensure they don't get mixed up with non-defective ones. Next, I'd inform my supervisor of the issue immediately. After that, I'd document the defect and any observations I made during the process to help with analysis.
Don't Just Read Gold Stamper Questions - Practice Answering Them!
Reading helps, but actual practice is what gets you hired. Our AI feedback system helps you improve your Gold Stamper interview answers in real-time.
Personalized feedback
Unlimited practice
Used by hundreds of successful candidates
If a client requests changes to the gold stamping design after production has started, how would you handle it?
How to Answer
- 1
Acknowledge and validate the client's request first.
- 2
Assess the feasibility of the changes within the current production timeline.
- 3
Communicate any potential impacts on cost and delivery time.
- 4
Propose alternative solutions if the changes are not immediately feasible.
- 5
Document the conversation and any agreed changes for future reference.
Example Answers
I would first acknowledge the client's request and express understanding of their need for changes. Then, I would assess how these changes would impact our current schedule and costs. If the changes are feasible, I'd outline the new timeline and costs. If not, I'd offer alternatives that meet their needs while keeping production on track.
You are given two different stamping techniques that could be applied to the gold. How would you choose which one to use?
How to Answer
- 1
Evaluate the desired end result and quality of the stamped gold.
- 2
Consider the properties of each stamping technique, such as durability and design detail.
- 3
Assess the cost and time implications of each technique.
- 4
Take into account the specific requirements of the gold piece being created.
- 5
Look at any industry standards or customer preferences relevant to the project.
Example Answers
I would compare the strength and finish of both techniques to ensure the final product meets quality standards.
If there’s a delay in receiving materials required for a gold stamping order, how do you adjust the workflow?
How to Answer
- 1
Assess the impact of the delay on current orders
- 2
Communicate with suppliers to get an estimated delivery time
- 3
Prioritize existing orders based on deadlines
- 4
Review stock levels for alternative materials that can be used
- 5
Adjust team assignments to focus on tasks that can proceed without the delayed materials
Example Answers
First, I would assess how the delay impacts our current orders. I’d communicate with the supplier for updates on their delivery timeline. Based on urgency, I would prioritize the most critical orders and see if any alternative materials can be utilized in the meantime. Lastly, I would reassign tasks within the team to ensure we keep progressing on other projects.
You are faced with a technical challenge during stamping that you have not encountered before. What steps do you take to resolve it?
How to Answer
- 1
Assess the situation by gathering all relevant information about the issue.
- 2
Consult the equipment manuals or technical documentation for guidance.
- 3
Reach out to colleagues or experts who may have experience with similar challenges.
- 4
Implement a potential solution on a small scale to test its effectiveness.
- 5
Document the problem and the steps taken for future reference.
Example Answers
First, I would gather all the details about the issue at hand. Then, I would check the equipment manuals to see if there are any known solutions. If I'm still unsure, I would consult with a more experienced colleague for their insights. After that, I would apply a potential fix on a smaller scale to see if it resolves the issue before implementing it fully. Finally, I would document what I did for future reference.
If resources are limited, how would you ensure quality in your gold stamping process?
How to Answer
- 1
Prioritize essential processes that directly impact quality.
- 2
Implement standardized procedures to maintain consistency.
- 3
Train the team on best practices for resource management.
- 4
Regularly assess and refine your quality checks.
- 5
Use available technology to optimize the stamping process.
Example Answers
In a resource-limited situation, I would focus on the critical steps of the gold stamping process, ensuring that the team follows standardized procedures that guarantee consistency. Training would be vital to maintain quality, and I would introduce regular assessments of our quality checks to catch any issues early.
If a customer is not satisfied with the stamped gold quality, how would you address their concerns?
How to Answer
- 1
Listen carefully to the customer's concerns without interrupting
- 2
Acknowledge the customer's feelings and express empathy
- 3
Ask specific questions to understand the exact issue
- 4
Offer a solution or alternative, such as re-stamping or a refund
- 5
Follow up to ensure the customer is satisfied with the resolution
Example Answers
I would first listen to the customer's concerns to understand what specific issues they have with the gold quality. It's important to show empathy and acknowledge their feelings. Then, I would ask clarifying questions to pinpoint the exact problems. Based on their feedback, I would propose a solution such as re-stamping the product or offering a refund if they prefer that. Finally, I would follow up with them after the resolution to ensure they are happy.
You receive mixed feedback on your last gold stamping project. How do you analyze and act on that feedback?
How to Answer
- 1
Identify common themes in the feedback.
- 2
Categorize feedback into positive and negative.
- 3
Seek clarification on any ambiguous comments.
- 4
Develop an action plan to address the negative aspects.
- 5
Follow up with stakeholders after implementing changes.
Example Answers
I first reviewed the feedback to find common issues, then categorized it into positive aspects and areas for improvement. I reached out for further clarification on specific points before creating a plan to address the concerns. After making adjustments, I followed up to confirm if the changes met expectations.
Gold Stamper Position Details
Related Positions
- Hand Stamper
- Machine Stamper
- Gold Layer
- Stamping Machine Operator
- Stamp Pad Maker
- Pin Sticker
- Carbon Printer
- Sticker
- Emblem Maker
- Machine Stapler
Similar positions you might be interested in.
Ace Your Next Interview!
Practice with AI feedback & get hired faster
Personalized feedback
Used by hundreds of successful candidates
Ace Your Next Interview!
Practice with AI feedback & get hired faster
Personalized feedback
Used by hundreds of successful candidates