Top 31 Hand Tapper Interview Questions and Answers [Updated 2025]
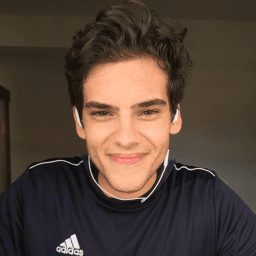
Andre Mendes
•
March 30, 2025
Preparing for a Hand Tapper interview can be daunting, but with the right guidance, you can approach it with confidence. In this blog post, we’ve compiled the most common interview questions for the Hand Tapper role. You'll find example answers and valuable tips to help you respond effectively and impress your potential employer. Dive in to equip yourself with insights that will set you apart in your interview!
Download Hand Tapper Interview Questions in PDF
To make your preparation even more convenient, we've compiled all these top Hand Tapperinterview questions and answers into a handy PDF.
Click the button below to download the PDF and have easy access to these essential questions anytime, anywhere:
List of Hand Tapper Interview Questions
Behavioral Interview Questions
Can you provide an example of how you handled pressure when meeting a tight deadline?
How to Answer
- 1
Choose a specific situation where you faced a tight deadline.
- 2
Explain the steps you took to organize your tasks and manage your time.
- 3
Highlight any teamwork or communication you relied on for support.
- 4
Describe the outcome and how you ensured success despite the pressure.
- 5
Reflect on what you learned from the experience and how you would apply it again.
Example Answers
In my last job, I was tasked with completing a project in just two days. I broke down the tasks into manageable pieces and prioritized them. I communicated with my team, and we collaborated to divide the workload. In the end, we met the deadline and delivered quality work, which taught me the importance of teamwork under pressure.
Describe an experience where you had to adapt your work techniques. What prompted the change?
How to Answer
- 1
Think of a specific situation that required you to change your methods.
- 2
Explain what the original technique was and why it was insufficient.
- 3
Describe the new technique and how you implemented it.
- 4
Mention the results of implementing the new method.
- 5
Keep your answer focused on your role and contributions.
Example Answers
In my last job, we faced a high error rate in product assembly. I was using a standard tapping technique, but it was inefficient. I researched and adopted a new method using a more precise tool that improved accuracy. This change reduced errors by 30% and increased production speed.
Don't Just Read Hand Tapper Questions - Practice Answering Them!
Reading helps, but actual practice is what gets you hired. Our AI feedback system helps you improve your Hand Tapper interview answers in real-time.
Personalized feedback
Unlimited practice
Used by hundreds of successful candidates
Can you give an example of a time you had to communicate a technical issue to someone without a technical background?
How to Answer
- 1
Identify a specific technical issue you faced.
- 2
Explain the issue in simple terms without jargon.
- 3
Describe the impact of the issue on the non-technical person.
- 4
Detail how you communicated the solution clearly.
- 5
Emphasize the importance of effective communication.
Example Answers
In my previous job, we had a server down that affected user access. I explained to the customer that the server was like a library and that some books were temporarily unavailable. I reassured them we were working to fix it and provided updates until the library was back open.
Have you ever had to resolve a conflict with a teammate regarding a tapping project? How did you handle it?
How to Answer
- 1
Identify the specific conflict and the parties involved
- 2
Explain how you communicated with your teammate to understand their perspective
- 3
Discuss the resolution steps you took and the outcome
- 4
Emphasize teamwork and collaboration in your approach
- 5
Reflect on what you learned from the experience
Example Answers
During a tapping project, my teammate and I disagreed on the technique for achieving a uniform finish. I scheduled a meeting to discuss our approaches, and we shared our reasoning. Together, we decided to test both methods and ended up using a combination that worked best. This compromise strengthened our teamwork and improved the project outcome.
What has been your most significant learning experience in your tapping career?
How to Answer
- 1
Reflect on a specific challenge you faced as a hand tapper.
- 2
Describe how you overcame this challenge and what you learned.
- 3
Emphasize the skills or techniques you improved from this experience.
- 4
Connect your learning experience to your growth as a hand tapper.
- 5
Keep your answer concise and focused on the key takeaways.
Example Answers
My most significant learning experience was when I struggled with consistent threading on small parts. I researched and practiced different tapping techniques, and I learned the importance of tool sharpening and proper speed. This challenge improved my precision and efficiency, which I now apply to all my work.
Describe a time when you took the initiative to improve the quality of your work.
How to Answer
- 1
Think of a specific example where you noticed a problem in your process.
- 2
Explain the steps you took to address that problem.
- 3
Highlight the results of your actions and any positive feedback received.
- 4
Focus on your personal growth and what you learned from the experience.
- 5
Make sure to connect how this effort contributes to overall quality.
Example Answers
In my previous job, I noticed that our hand tapper machines were frequently underperforming. I took the initiative to research maintenance protocols and implemented a regular check-up schedule. As a result, we reduced downtime by 20% and received positive feedback from my supervisor on the improved efficiency.
Can you describe a time when your attention to detail made a significant difference in your work?
How to Answer
- 1
Choose a specific example from your past work experience
- 2
Highlight the context and the task at hand
- 3
Explain the detail you focused on and why it mattered
- 4
Describe the outcome and its significance to the project
- 5
Reflect on what you learned and how it applies to the Hand Tapper role
Example Answers
In my previous job as a quality control inspector, I noticed a small defect in a batch of parts that would have led to a significant failure in assembly. By addressing this defect early, we saved the company thousands in rework costs and ensured a high-quality product for our customer.
Tell me about a time when you worked collaboratively with a team on a project. What was your role?
How to Answer
- 1
Identify a specific team project you've worked on.
- 2
Clearly describe your role and contributions.
- 3
Highlight how you supported teamwork and collaboration.
- 4
Mention any positive outcomes from the project.
- 5
Keep it concise and focus on teamwork skills.
Example Answers
In my previous job, our team was tasked with improving production efficiency. I took the lead in coordinating our efforts by organizing regular meetings, gathering input from each member, and ensuring everyone’s ideas were heard. This collaborative approach led to a 15% increase in efficiency within three months.
Describe a difficult tapping project you managed. What challenges did you face and how did you overcome them?
How to Answer
- 1
Identify a specific project with clear challenges and outcomes.
- 2
Explain the steps you took to manage the project effectively.
- 3
Highlight your problem-solving skills in overcoming obstacles.
- 4
Discuss the tools and techniques you used for tapping.
- 5
Conclude with the results and what you learned from the experience.
Example Answers
I once managed a tapping project where we had to tap multiple metal sheets with varying thicknesses. The challenge was to ensure precision despite the differences. I organized the team to use calibrated taps for each thickness and implemented a double-check system for quality control. As a result, we completed the project ahead of schedule with zero defects.
Have you ever suggested a change in the tapping process that improved efficiency or quality? What was it?
How to Answer
- 1
Think of a specific instance where you identified a problem in the tapping process.
- 2
Explain the change you suggested clearly and how it was implemented.
- 3
Include measurable results achieved from your suggestion, such as time saved or quality improved.
- 4
Use action verbs to describe your involvement and initiative.
- 5
Keep it concise and relevant to the role of a Hand Tapper.
Example Answers
In my previous role, I noticed that our tapping process was taking too long due to frequent tool changes. I suggested a scheduled maintenance plan for our taps to prolong their life, which resulted in a 20% decrease in downtime.
Don't Just Read Hand Tapper Questions - Practice Answering Them!
Reading helps, but actual practice is what gets you hired. Our AI feedback system helps you improve your Hand Tapper interview answers in real-time.
Personalized feedback
Unlimited practice
Used by hundreds of successful candidates
Technical Interview Questions
What types of hand tap techniques are you familiar with, and which do you prefer to use?
How to Answer
- 1
Identify specific hand tap techniques you've used.
- 2
Explain how each technique suits different tasks.
- 3
Discuss your personal preference and why it works for you.
- 4
Mention any relevant experience or training.
- 5
Keep your answer clear and focused on both techniques and preference.
Example Answers
I'm familiar with both the straight tap and the spiral tap techniques. I primarily use the straight tap for precision jobs as it offers better control, especially in smaller components.
What hand tapping tools do you have experience with, and how do you select the appropriate tool for a job?
How to Answer
- 1
List specific hand tapping tools you have used like taps, tappers, or tap wrenches.
- 2
Explain your selection process based on material type, thread size, and precision requirements.
- 3
Mention any safety or quality standards you follow.
- 4
Provide examples of past experiences where tool selection was crucial to the outcome.
- 5
Be concise and confident in your delivery when discussing your expertise.
Example Answers
I have experience with various taps, including spiral point taps and hand taps. I choose the tool based on the material being tapped; for softer metals, I might use a spiral tap, while for harder materials, a tapered tap works better. I always ensure to follow safety guidelines and double-check the thread specifications before starting.
Don't Just Read Hand Tapper Questions - Practice Answering Them!
Reading helps, but actual practice is what gets you hired. Our AI feedback system helps you improve your Hand Tapper interview answers in real-time.
Personalized feedback
Unlimited practice
Used by hundreds of successful candidates
How do different materials affect your hand tapping strategies?
How to Answer
- 1
Identify the characteristics of the materials you work with
- 2
Discuss how hard materials require different tapping techniques
- 3
Emphasize the importance of tool selection based on material type
- 4
Mention adjusting tapping speed based on material hardness
- 5
Include examples from your experience with various materials
Example Answers
When working with harder metals, I find that a slower tapping speed is essential to avoid damaging my tools. I also switch to a more robust tool that can handle the increased resistance.
What methods do you use to ensure quality during the hand tapping process?
How to Answer
- 1
Inspect tools and equipment for signs of wear or damage before starting work
- 2
Maintain a consistent tapping speed to prevent variations in the final product
- 3
Perform regular checks on the dimensions of the tapped holes during the process
- 4
Use calibrated measuring tools to verify completed work meets specifications
- 5
Document any issues or deviations and address them immediately.
Example Answers
I always check my tapping tools for wear and ensure they're properly calibrated before starting a job. I also take measurements every few cycles to ensure accuracy.
What safety measures do you always follow while performing hand tapping?
How to Answer
- 1
Always wear appropriate personal protective equipment, such as gloves and eye protection.
- 2
Ensure the workplace is clean and free of obstructions.
- 3
Check the hand tap and tools for any damage before use.
- 4
Use the correct tapping techniques to avoid slips and injuries.
- 5
Maintain awareness of your surroundings and communicate with coworkers.
Example Answers
I always wear gloves and safety glasses when performing hand tapping to protect myself from any metal shavings. I also keep my workspace organized to prevent accidents.
How do you calculate the proper depth for a tap in a given project?
How to Answer
- 1
Understand the tap size and thread pitch you are using
- 2
Consider the material thickness you are tapping into
- 3
Account for the minimum thread engagement required for strength
- 4
Use a tap depth calculator or refer to tapping standards
- 5
Ensure you leave enough material at the bottom to prevent breakage
Example Answers
To calculate the proper depth for a tap, I first determine the tap size and thread pitch. Then, I measure the thickness of the material I'm tapping into and make sure to follow the guidelines for minimum thread engagement. Finally, I use a tap depth calculator to confirm the depth needed before starting the process.
What steps do you take to troubleshoot common issues encountered during hand tapping?
How to Answer
- 1
Identify the specific issue by asking questions or observing the process.
- 2
Check the tools for wear and damage that may affect performance.
- 3
Ensure proper alignment and positioning of the workpiece and tapping tool.
- 4
Review the tapping speed and feed rate to see if they are appropriate.
- 5
Document the issue and any steps taken to resolve it for future reference.
Example Answers
When troubleshooting hand tapping issues, I first identify the problem by observing the process and asking questions. Then, I check the tools for any wear that could affect tapping. If the tool is aligned properly and the speed is correct, I also document my findings.
What processes do you follow to ensure precision and accuracy in your hand tapping work?
How to Answer
- 1
Use a consistent tapping technique across all workpieces
- 2
Regularly check and calibrate tools before starting work
- 3
Implement a system for measuring depth and angles as you tap
- 4
Keep your work environment clean and organized to avoid distractions
- 5
Perform quality checks after each tapping session
Example Answers
I ensure precision by using a consistent tapping technique and regularly checking my tools for accuracy. I also measure the depth of each tap to guarantee it meets specifications.
What are the common tolerance standards you adhere to in hand tapping?
How to Answer
- 1
Familiarize yourself with industry standard tolerances such as those outlined in ISO or ANSI.
- 2
Mention specific tolerances relevant to the materials you work with, like +/-0.005 inches.
- 3
Discuss how you ensure precision through measurement tools like calipers and gauges.
- 4
Share examples of when you've correctly adhered to these standards in past projects.
- 5
Be prepared to explain why tolerance is critical in ensuring the quality of the final product.
Example Answers
In my experience, I adhere to a standard tolerance of +/-0.005 inches for most metal tapping operations. This ensures a good fit for threaded components.
How do you maintain your hand tapping tools to ensure optimal performance?
How to Answer
- 1
Regularly clean tools after each use to remove debris and residue
- 2
Inspect tools for wear and damage before each shift
- 3
Lubricate moving parts with appropriate grease to prevent friction
- 4
Store tools in a designated area to protect from environmental factors
- 5
Keep a maintenance log to track tool performance and repairs
Example Answers
I clean my tools thoroughly after every use to prevent buildup that can affect tapping precision. I also inspect them for any signs of wear, replacing parts as necessary. Lubricating the mechanisms ensures they operate smoothly.
Don't Just Read Hand Tapper Questions - Practice Answering Them!
Reading helps, but actual practice is what gets you hired. Our AI feedback system helps you improve your Hand Tapper interview answers in real-time.
Personalized feedback
Unlimited practice
Used by hundreds of successful candidates
Describe the step-by-step process you follow when setting up for tapping.
How to Answer
- 1
Begin by selecting the appropriate tap size for the hole.
- 2
Secure the workpiece firmly to prevent movement during tapping.
- 3
Use cutting fluid to ensure smooth operation and prolong tap life.
- 4
Align the tap with the hole carefully to avoid cross-threading.
- 5
Turn the tap at a steady pace, backing off periodically to clear chips.
Example Answers
I first choose the correct tap size for the material. Then I secure the workpiece in a vise. After that, I apply some cutting fluid for lubrication. Next, I carefully align the tap with the hole before starting to turn it slowly, and I back off occasionally to remove debris.
Situational Interview Questions
If you discover a defect in a tapped hole after completing your work, how would you address it?
How to Answer
- 1
Assess the severity of the defect before taking action
- 2
Report the defect to your supervisor promptly
- 3
Involve quality control if necessary to document the issue
- 4
If possible, determine the cause of the defect to prevent recurrence
- 5
Follow company procedures for rework or correction of defects
Example Answers
I would first check how serious the defect is. If it's significant, I would inform my supervisor immediately and document the issue. I'd also look into how the defect happened to make sure it doesn't occur again.
You have multiple tapping tasks to complete before the end of the day. How do you prioritize them?
How to Answer
- 1
List all tasks and their deadlines
- 2
Identify which tasks are the most urgent
- 3
Consider the complexity of each task and time needed
- 4
Allocate more time for high-priority tasks
- 5
Communicate with team if needed to adjust priorities
Example Answers
I first list all my tapping tasks and check their deadlines. Then, I prioritize tasks that are due soonest and those that are more complex, making sure I allocate enough time for them. If necessary, I’ll discuss with my supervisor to ensure I’m focusing on the right tasks.
Don't Just Read Hand Tapper Questions - Practice Answering Them!
Reading helps, but actual practice is what gets you hired. Our AI feedback system helps you improve your Hand Tapper interview answers in real-time.
Personalized feedback
Unlimited practice
Used by hundreds of successful candidates
What would you do if your tapping tool breaks mid-task? How would you handle the unfinished work?
How to Answer
- 1
Stay calm and assess the situation quickly.
- 2
Check if you have a spare tapping tool available.
- 3
If no spare is available, inform your supervisor immediately.
- 4
Document the unfinished work and tool failure for records.
- 5
Reprioritize tasks and focus on what can be done while waiting.
Example Answers
If my tapping tool breaks, I would first remain calm and check if I have a spare tool. If not, I would inform my supervisor about the issue. I would document the unfinished work to keep track of progress and then focus on completing other tasks while waiting for the tool to be replaced.
If a client complains about the quality of the tapping work you provided, how would you respond?
How to Answer
- 1
Listen carefully to the client's concerns
- 2
Acknowledge their feelings and express understanding
- 3
Ask specific questions to clarify the issue
- 4
Offer to rectify the issue or improve the work
- 5
Follow up after the resolution to ensure satisfaction
Example Answers
I appreciate you bringing this to my attention. Can you tell me specifically what part of the tapping work didn't meet your expectations? I'm committed to making it right for you.
If you needed technical support while tapping a difficult material, who would you approach and why?
How to Answer
- 1
Identify team members with specific expertise related to the material.
- 2
Consider resources like technical manuals or guides before asking for help.
- 3
Approach someone who has experience with similar challenges.
- 4
Explain the situation clearly and what kind of help you need.
- 5
Be open to suggestions and collaboration to find a solution.
Example Answers
I would approach our lead engineer who has extensive experience working with this material. They have dealt with similar challenges before and can provide insights on the best practices for tapping it effectively.
How would you handle a situation where you are low on tapping supplies, but have a high workload?
How to Answer
- 1
Assess the available tapping supplies immediately
- 2
Prioritize tasks based on deadlines and importance
- 3
Communicate with your supervisor about the supply shortage
- 4
Look for alternative solutions or substitutes for the tapping process
- 5
Optimize your workflow to manage the workload efficiently
Example Answers
I would quickly evaluate the supplies I have on hand and prioritize my tasks based on urgency. If needed, I would inform my supervisor about the shortage and see if we can restock or if there are alternatives we can use.
How would you react if you received constructive criticism on your hand tapping methods?
How to Answer
- 1
Acknowledge the feedback positively
- 2
Ask for specific examples to clarify the criticism
- 3
Express willingness to improve and adapt
- 4
Share past experiences where you learned from feedback
- 5
Maintain a professional demeanor regardless of the criticism
Example Answers
I appreciate constructive criticism as it helps me improve my hand tapping skills. If someone suggested a better technique, I would ask for examples and be open to trying new methods.
If you were assigned to a project using a new tapping technique you are unfamiliar with, how would you proceed?
How to Answer
- 1
Research the new tapping technique thoroughly to understand its principles and applications.
- 2
Consult with experienced colleagues or supervisors who are familiar with the technique.
- 3
Practice the new technique in a low-stakes environment to build confidence.
- 4
Document your learning process and any challenges you encounter along the way.
- 5
Be open to feedback and continuously improve your skills as you use the technique.
Example Answers
I would start by researching the new tapping technique online and reviewing any technical manuals. Then, I would seek advice from coworkers who have experience with it. I would practice the technique on scrap materials to get a feel for it before using it on the actual project.
If you were told to switch between different tapping jobs frequently, how would you manage the workflow?
How to Answer
- 1
Prioritize tasks based on deadlines and complexity
- 2
Use a checklist to keep track of each job's requirements
- 3
Set specific time blocks to focus on each tapping task
- 4
Maintain clear communication with supervisors about any challenges
- 5
Stay organized and adaptable to switch quickly between tasks
Example Answers
I would start by prioritizing each tapping job based on when it's due and how complex it is. I would then create a checklist to ensure I meet each job's requirements. By setting time blocks for each task, I can stay focused and efficiently switch between jobs as needed.
How would you handle a sudden change in production specifications for a tapping job you are already working on?
How to Answer
- 1
Stay calm and assess the new specifications carefully
- 2
Communicate with your supervisor about the changes
- 3
Check the tools and materials to ensure they meet the new requirements
- 4
Adjust your workflow to accommodate the new specifications
- 5
Document any changes for future reference
Example Answers
I would first review the new specifications to understand exactly what has changed. Then, I would inform my supervisor about the updates and ensure I have the correct tools to meet the new requirements. Finally, I would adapt my workflow accordingly to ensure production continues smoothly.
Don't Just Read Hand Tapper Questions - Practice Answering Them!
Reading helps, but actual practice is what gets you hired. Our AI feedback system helps you improve your Hand Tapper interview answers in real-time.
Personalized feedback
Unlimited practice
Used by hundreds of successful candidates
Hand Tapper Position Details
Related Positions
- Hand Stamper
- Hand Stapler
- Punch Hand
- Hand Nailer
- Job Hand
- Hand Paster
- Hand Riveter
- Smash Hand
- Drum Handler
- Hand Driller
Similar positions you might be interested in.
Ace Your Next Interview!
Practice with AI feedback & get hired faster
Personalized feedback
Used by hundreds of successful candidates
Ace Your Next Interview!
Practice with AI feedback & get hired faster
Personalized feedback
Used by hundreds of successful candidates