Top 30 Filtration Operator Interview Questions and Answers [Updated 2025]
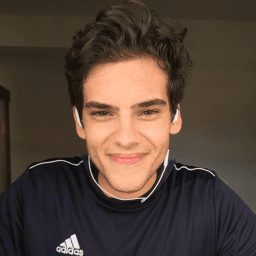
Andre Mendes
•
March 30, 2025
Preparing for a Filtration Operator interview can be daunting, but we're here to help streamline your preparation process. This post compiles the most common interview questions for the Filtration Operator role, complete with example answers and insightful tips to help you respond effectively. Whether you're a seasoned professional or new to the field, this guide will equip you with the confidence to tackle any question that comes your way.
Download Filtration Operator Interview Questions in PDF
To make your preparation even more convenient, we've compiled all these top Filtration Operatorinterview questions and answers into a handy PDF.
Click the button below to download the PDF and have easy access to these essential questions anytime, anywhere:
List of Filtration Operator Interview Questions
Behavioral Interview Questions
Can you describe a time when you identified a problem with the filtration system and how you resolved it?
How to Answer
- 1
Choose a specific incident where you spotted an issue with the filtration system.
- 2
Clearly explain how you recognized the problem, such as through monitoring or testing.
- 3
Discuss the steps you took to investigate and diagnose the issue.
- 4
Describe the solution you implemented and how it improved the system.
- 5
Mention any lessons learned or improvements made post-resolution.
Example Answers
In my previous role, I noticed a drop in filtration efficiency during routine checks. I analyzed the pressure readings and discovered a clog in the filter media. I replaced the filter and adjusted the system settings, which restored normal operation and improved output quality.
Tell me about a time you had to work closely with a team to complete a filtration operation. What was your role?
How to Answer
- 1
Describe the team and the filtration process clearly.
- 2
Explain your specific role and contributions to the operation.
- 3
Highlight any challenges the team faced and how they were overcome.
- 4
Mention the outcome of the operation and your team's success.
- 5
Use clear, simple language to convey your experience.
Example Answers
In my previous job, our team was tasked with replacing a filtration system at a water treatment facility. I was responsible for coordinating the equipment installation alongside technicians. We faced delays due to damaged parts, but I organized a quick sourcing of replacements. Ultimately, we completed the project ahead of schedule, improving water quality significantly.
Don't Just Read Filtration Operator Questions - Practice Answering Them!
Reading helps, but actual practice is what gets you hired. Our AI feedback system helps you improve your Filtration Operator interview answers in real-time.
Personalized feedback
Unlimited practice
Used by hundreds of successful candidates
Describe a situation where you had to prioritize safety in your operations. What steps did you take?
How to Answer
- 1
Identify a specific situation related to filtration operations.
- 2
Discuss the potential safety hazards involved in that situation.
- 3
Explain the safety measures you implemented to mitigate risks.
- 4
Highlight the outcome and how it improved safety or processes.
- 5
Reflect on any learnings and how they influenced future operations.
Example Answers
In my previous role, we faced a situation where a filtration unit was leaking hazardous materials. I immediately shut down the unit to prevent any accidents and notified my supervisor. We implemented a containment plan and used personal protective equipment (PPE) for ourselves. The quick response ensured no one was harmed, and we enhanced our maintenance schedules to prevent future leaks.
Have you ever had to lead a team during a challenging filtration operation? What challenges did you face?
How to Answer
- 1
Describe a specific situation with concrete details
- 2
Highlight your role and responsibilities
- 3
Mention the specific challenges faced
- 4
Explain how you and your team overcame the challenges
- 5
Reflect on the outcomes and what you learned
Example Answers
In a previous role as a filtration operator, I led a team during an unplanned shutdown caused by equipment failure. The challenge was to maintain production while ensuring safety. I organized a brainstorming session to troubleshoot and implement a temporary fix, and we successfully resumed operations quickly. This experience taught me the importance of teamwork and quick decision-making.
Tell us about a time you went above and beyond to ensure quality in your work as a filtration operator.
How to Answer
- 1
Choose a specific situation where you noticed a potential quality issue.
- 2
Explain the steps you took to address the issue proactively.
- 3
Highlight any tools or methods you used to improve the process.
- 4
Mention any positive outcomes from your actions, such as improved product quality.
- 5
Keep your example relevant to filtration operations.
Example Answers
In my previous role, I noticed that the filtration process was not meeting our quality standards consistently. I initiated a thorough review of the filtration system and identified some clogging issues. I implemented a more frequent maintenance schedule and introduced a new cleaning procedure that reduced downtime. As a result, our product quality improved, leading to fewer complaints from clients.
Describe a time when you had to manage multiple filtration processes simultaneously. How did you prioritize your tasks?
How to Answer
- 1
Identify the situation clearly and briefly.
- 2
Explain the filtration processes involved.
- 3
Describe how you prioritized based on urgency and impact.
- 4
Include any tools or methods you used to stay organized.
- 5
Mention the outcome and what you learned.
Example Answers
In my previous role, I managed three filtration systems for different production lines. I prioritized tasks by assessing which line had the highest demand and urgency for shipment. I used a checklist to monitor progress and communicate with my team to ensure we stayed on track. This helped us meet all deadlines successfully, and I learned the importance of clear communication.
Can you provide an example of when you took the initiative to improve a filtration process?
How to Answer
- 1
Identify a specific filtration process you improved
- 2
Explain the problem you noticed with the existing process
- 3
Describe the initiative you took to solve the problem
- 4
Share the outcome or results of your actions
- 5
Emphasize teamwork if applicable
Example Answers
In my previous role, I noticed that the filtration system was frequently clogged, causing downtime. I initiated a review of the filter specifications and suggested switching to a more efficient filter type. After implementing the change, we reduced downtime by 30%.
Tell me about a time you received constructive criticism in your role and how you responded to it.
How to Answer
- 1
Choose a specific example that highlights the criticism received.
- 2
Explain the situation clearly and succinctly.
- 3
Describe your emotions and initial reaction to the criticism.
- 4
Detail the steps you took to improve based on the feedback.
- 5
Conclude with the positive outcomes resulting from your response.
Example Answers
In my previous role as a filtration technician, my supervisor pointed out that my documentation was sometimes unclear. Initially, I felt defensive, but then I recognized the importance of precise records. I took a course on effective documentation and implemented a checklist for my reports. As a result, my documentation improved significantly, and my supervisor praised the clarity and accuracy of my work.
Technical Interview Questions
What types of filtration techniques are you familiar with, and how have you applied them in your past roles?
How to Answer
- 1
Identify specific filtration techniques you've used such as membrane filtration, gravity filtration, or multimedia filtration.
- 2
Describe a situation in which you applied each technique, including the context and goals.
- 3
Mention any relevant equipment or systems you have operated related to those techniques.
- 4
Highlight the outcomes or improvements achieved from your filtration processes.
- 5
Be concise yet detailed enough to demonstrate your expertise and experience.
Example Answers
I am familiar with membrane filtration and gravity filtration. In my last role, I used membrane filtration to purify water for a production process, helping to reduce contaminants by 95%. I operated a reverse osmosis system and monitored the performance to ensure efficiency.
Can you explain how to properly maintain and calibrate filtration equipment?
How to Answer
- 1
Regularly inspect filtration equipment for wear and tear.
- 2
Clean filters and replace them according to manufacturer specifications.
- 3
Check calibration settings frequently to ensure accurate operation.
- 4
Document maintenance procedures and findings for compliance.
- 5
Train staff on proper usage and maintenance protocols.
Example Answers
To maintain filtration equipment, I regularly inspect all components for any signs of damage or wear. I clean the filters as per the manufacturer's instructions and replace them when necessary. Additionally, I check the calibration settings at least once a month to ensure everything is functioning correctly.
Don't Just Read Filtration Operator Questions - Practice Answering Them!
Reading helps, but actual practice is what gets you hired. Our AI feedback system helps you improve your Filtration Operator interview answers in real-time.
Personalized feedback
Unlimited practice
Used by hundreds of successful candidates
What safety and quality standards do you follow as a filtration operator?
How to Answer
- 1
Mention specific safety protocols relevant to filtration operations.
- 2
Discuss adherence to industry standards like ISO or OSHA.
- 3
Include examples of how you ensure quality in filtration processes.
- 4
Talk about your experience with equipment calibration and maintenance.
- 5
Highlight the importance of personal protective equipment (PPE) in your role.
Example Answers
I follow OSHA guidelines to ensure a safe working environment, use PPE consistently, and regularly calibrate equipment to maintain high filtration quality.
How do you verify that a filtration system is operating within its normal parameters?
How to Answer
- 1
Check pressure readings at the inlet and outlet regularly.
- 2
Monitor flow rates to ensure they are within specified limits.
- 3
Inspect filter media for signs of clogging or wear.
- 4
Review control system alarms and alerts for any anomalies.
- 5
Perform routine maintenance according to the manufacturer's guidelines.
Example Answers
I verify the filtration system's operation by regularly checking the pressure readings and flow rates. If I notice any deviations, I inspect the filter media for clogs and perform maintenance as needed.
What types of chemicals are often used in the filtration process, and what precautions must be taken when handling them?
How to Answer
- 1
Identify common chemicals used in filtration such as chlorine and coagulants.
- 2
Mention the importance of wearing appropriate PPE like gloves and goggles.
- 3
Discuss the need for proper storage of chemicals, away from incompatible substances.
- 4
Highlight the significance of following Material Safety Data Sheets (MSDS) for each chemical.
- 5
Explain the importance of training in safe handling procedures.
Example Answers
Common chemicals used in filtration include chlorine for disinfection and coagulants like aluminum sulfate. It's crucial to wear gloves and goggles when handling these substances to prevent skin and eye contact.
What are the common troubleshooting steps you would take if sediment buildup is affecting filtration efficiency?
How to Answer
- 1
Identify the type and source of the sediment buildup
- 2
Check the pre-filtration systems for effectiveness
- 3
Inspect the filter for any damage or clogging
- 4
Perform backwashing or cleaning of the filter if applicable
- 5
Monitor the filtration parameters after adjustments
Example Answers
First, I would identify what type of sediment is causing the issue and where it's coming from. Next, I would check our pre-filtration systems to see if they're functioning properly. I would then inspect the filter itself for any signs of clogging or damage. If needed, I would perform a backwash to clear the filter. Finally, I would monitor the filtration parameters to ensure efficiency has returned.
Can you discuss the key parameters that affect filtration performance and how to monitor them?
How to Answer
- 1
Identify the main parameters like flow rate, pressure drop, and particle size.
- 2
Explain how these parameters influence filtration efficiency.
- 3
Discuss methods for monitoring these parameters, such as gauges and flow meters.
- 4
Provide examples of how adjustments can improve performance.
- 5
Mention the importance of regular calibration and maintenance.
Example Answers
Key parameters affecting filtration performance include flow rate, pressure drop, and particle size. Monitoring these can be done using pressure gauges and flow meters, allowing us to adjust conditions for optimal filtration. For instance, if pressure drops significantly, it may indicate clogging, prompting cleaning or replacement.
How do you ensure that the flow rates in the filtration process are optimized?
How to Answer
- 1
Regularly monitor and record flow rates to identify any fluctuations.
- 2
Adjust valve settings and pump speeds based on collected data to maintain desired flow.
- 3
Perform routine maintenance on filters and equipment to prevent blockages.
- 4
Analyze the filtration process to identify bottlenecks and areas for improvement.
- 5
Consult with the team for feedback on operational efficiency and practical adjustments.
Example Answers
I monitor flow rates daily and adjust the valves and pumps as needed to keep them within optimal ranges. Regular maintenance on filters helps prevent clogs that can reduce flow.
What steps do you take when you suspect that a filter is failing?
How to Answer
- 1
Observe indicators such as pressure drops or flow rate changes
- 2
Check the filter for visible signs of damage or wear
- 3
Review maintenance logs for the filter's performance history
- 4
Conduct a performance test if possible to confirm the suspicion
- 5
Replace the filter if diagnostics indicate a failure or if it's overdue for replacement
Example Answers
I first check for any abnormal pressure readings or flow rate variations. If I see discrepancies, I inspect the filter for physical damage, and if everything looks fine, I refer to the maintenance logs to see if there have been any recent issues. If needed, I would perform a test to check its efficiency and replace it if necessary.
What methods do you use for documenting and reporting filtration processes and results?
How to Answer
- 1
Explain the importance of accurate documentation in filtration processes
- 2
Mention specific tools or software you use for recording data
- 3
Describe the format you use for reporting results to stakeholders
- 4
Highlight your routine for reviewing and updating documentation
- 5
Emphasize how you ensure compliance with safety regulations in your documentation
Example Answers
I use an electronic logging system to record filtration parameters like flow rate and pressure, ensuring data accuracy. For reporting, I create monthly performance reports in standard format to present to management and ensure compliance with safety standards.
Don't Just Read Filtration Operator Questions - Practice Answering Them!
Reading helps, but actual practice is what gets you hired. Our AI feedback system helps you improve your Filtration Operator interview answers in real-time.
Personalized feedback
Unlimited practice
Used by hundreds of successful candidates
How do you analyze data from filtration processes to inform future decisions?
How to Answer
- 1
Identify key performance indicators relevant to filtration efficiency.
- 2
Utilize software tools for data collection and analysis to track trends.
- 3
Conduct root cause analysis on any deviations in performance metrics.
- 4
Engage with team members to gather insights on operational challenges.
- 5
Make data-driven recommendations for process improvements.
Example Answers
I analyze filtration data by first focusing on key metrics like flow rates and particle sizes. I use specialized software to track this data over time. If I see any fluctuations, I perform a root cause analysis to pinpoint issues. I also consult with the team for their observations to enrich my analysis and suggest improvements accordingly.
Have you been involved in any system upgrades? What was your role in the process?
How to Answer
- 1
Describe your specific involvement in the upgrade process
- 2
Mention any tools or technologies you used
- 3
Highlight your contributions or any challenges you overcame
- 4
Include the outcome of the upgrade
- 5
Keep it concise and relevant to the position
Example Answers
In my last role, I was part of a team that upgraded our filtration control system. I helped to calibrate the new sensors and conducted tests to ensure accuracy. This led to a 15% increase in operational efficiency.
Situational Interview Questions
If you notice a significant drop in output from the filtration system, what steps would you take to diagnose the issue?
How to Answer
- 1
Check system parameters like pressure and flow rates for abnormalities.
- 2
Inspect filters for clogs or blockages that may hinder flow.
- 3
Review maintenance logs to see if recent work could have affected output.
- 4
Test input water quality to ensure it meets filtration requirements.
- 5
Consult with team members to gather observations on changes in operation.
Example Answers
First, I would check the pressure gauges and flow meters to identify any irregularities. Next, I would examine the filters for clogs or issues. I would also look at the maintenance records to see if any recent changes might have caused the drop. Lastly, I would test the input water quality to ensure it's within limits.
Imagine your team is under a tight deadline to filter material. How would you ensure effective collaboration under pressure?
How to Answer
- 1
Communicate clearly and frequently with your team about tasks and deadlines.
- 2
Delegate responsibilities based on team members' strengths and expertise.
- 3
Encourage team members to share ideas and concerns to foster collaboration.
- 4
Maintain a positive attitude to help reduce stress among the team.
- 5
Prioritize tasks and focus on the most critical aspects of the project.
Example Answers
I would start by holding a quick meeting to clarify everyone's roles and deadlines. By understanding each person's strengths, I could assign tasks effectively, ensuring that we stay focused on our priorities under pressure.
Don't Just Read Filtration Operator Questions - Practice Answering Them!
Reading helps, but actual practice is what gets you hired. Our AI feedback system helps you improve your Filtration Operator interview answers in real-time.
Personalized feedback
Unlimited practice
Used by hundreds of successful candidates
In the event of a filtration system failure during a critical operation, what would be your immediate response?
How to Answer
- 1
Assess the situation quickly to understand the failure's impact.
- 2
Follow emergency protocols as per company procedures.
- 3
Notify the supervisor and relevant team members immediately.
- 4
Isolate the problematic system to prevent further issues.
- 5
Implement any backup systems or alternative filtration methods promptly.
Example Answers
I would first assess the situation to determine the extent of the failure. Then, I'd immediately notify my supervisor while following our emergency protocols. If needed, I would isolate the affected system and engage any backup filtration systems to maintain operation.
If you observed a coworker not following safety protocols while operating filtration equipment, how would you handle the situation?
How to Answer
- 1
Assess the situation to understand the severity of the safety violation.
- 2
Approach the coworker calmly and privately to discuss your observations.
- 3
Emphasize the importance of safety protocols for everyone's well-being.
- 4
If the coworker does not respond positively, report the issue to a supervisor.
- 5
Follow up to ensure that the situation is addressed appropriately.
Example Answers
I would first assess how serious the violation is and then approach my coworker privately, pointing out the safety issue I noticed. I would explain why following safety protocols is crucial. If they dismiss my concerns, I would inform my supervisor to take further action.
How would you handle a disagreement with a fellow operator about the best approach to a filtration problem?
How to Answer
- 1
Listen actively to your colleague’s perspective and concerns.
- 2
Discuss the pros and cons of each approach without being confrontational.
- 3
Suggest a trial run of both methods to evaluate effectiveness.
- 4
Involve a supervisor if you cannot reach a consensus.
- 5
Stay professional and focused on finding the best solution.
Example Answers
I would first listen to my colleague's viewpoint, as understanding their reasoning is important. Then, I’d discuss the benefits and drawbacks of our approaches and suggest we try both methods on a small scale to see which one works better. If we still disagree, we could involve a supervisor for their input.
If you were given limited resources for filtration materials, how would you adjust your operations?
How to Answer
- 1
Assess current filtration processes for efficiency and waste reduction.
- 2
Prioritize the most critical filtration needs based on output quality.
- 3
Consider alternative materials or methods that may be less resource-intensive.
- 4
Implement a schedule for regular maintenance to extend the life of existing materials.
- 5
Train the team on optimizing existing resources to maximize effectiveness.
Example Answers
I would first evaluate our current filtration operations to identify any inefficiencies. This would help me reduce waste and prioritize our most critical filtration requirements to ensure we still meet quality standards.
How would you approach the situation if you realized you are running low on essential filtration supplies?
How to Answer
- 1
Assess current inventory to confirm low supply levels.
- 2
Communicate immediately with your supervisor or team about the situation.
- 3
Check if there are alternative supplies or workarounds available.
- 4
Prioritize critical operations while awaiting new supplies.
- 5
Document the incident and suggest improvements to avoid future shortages.
Example Answers
I would first check our inventory records to confirm we are low on supplies. Then, I would alert my supervisor to discuss potential orders. Meanwhile, I would look for alternative supplies that could be used temporarily, ensuring operations continue smoothly.
If you had to train a new operator on filtration systems, what key topics would you cover?
How to Answer
- 1
Start with basic principles of filtration and its importance in the process.
- 2
Discuss different types of filtration methods and their applications.
- 3
Explain maintenance procedures for filtration equipment.
- 4
Highlight safety protocols and the importance of personal protective equipment.
- 5
Include troubleshooting common issues with filtration systems.
Example Answers
I would start by explaining the basics of how filtration works and why it's vital for our processes. Then, I'd cover the different types of filters we use, like membrane and sand filters. After that, I'd go through regular maintenance tasks, such as cleaning and replacing filters, and emphasize the safety protocols we follow while operating these systems.
If a batch of filtered material did not meet quality standards, how would you approach investigating the cause?
How to Answer
- 1
Review the filtration process and equipment used.
- 2
Check the input materials for any inconsistencies.
- 3
Analyze the parameters during the filtration run.
- 4
Inspect the filter media for defects or saturation.
- 5
Conduct tests on the output and compare to standards.
Example Answers
First, I would review the filtration process to identify any deviations. Then, I would check the raw materials for quality issues. After that, I would analyze the operating parameters to see if they were within spec.
Filtration Operator Position Details
Recommended Job Boards
CareerBuilder
www.careerbuilder.com/jobs/filtration-operatorZipRecruiter
www.ziprecruiter.com/Jobs/Filtration-OperatorThese job boards are ranked by relevance for this position.
Related Positions
- Filterer
- Water Filterer
- Water Operator
- Relief Operator
- Water Treatment Operator
- Filter Changer
- Sifter
- Projector Operator
- Utilities Operator
- Process Operator
Similar positions you might be interested in.
Ace Your Next Interview!
Practice with AI feedback & get hired faster
Personalized feedback
Used by hundreds of successful candidates
Ace Your Next Interview!
Practice with AI feedback & get hired faster
Personalized feedback
Used by hundreds of successful candidates