Top 30 Filter Changer Interview Questions and Answers [Updated 2025]
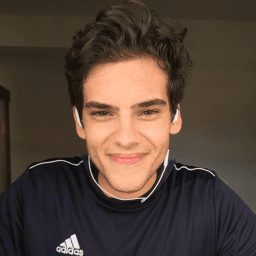
Andre Mendes
•
March 30, 2025
Preparing for a Filter Changer interview? This post is your go-to resource for mastering the most common questions asked in the field. We provide example answers and expert tips to help you confidently tackle each question and demonstrate your expertise. Whether you're a seasoned professional or new to the role, our insights will help you make a lasting impression and secure the position.
Download Filter Changer Interview Questions in PDF
To make your preparation even more convenient, we've compiled all these top Filter Changerinterview questions and answers into a handy PDF.
Click the button below to download the PDF and have easy access to these essential questions anytime, anywhere:
List of Filter Changer Interview Questions
Behavioral Interview Questions
Can you describe a time when you identified a filter issue before it caused a significant problem?
How to Answer
- 1
Focus on a specific example from your past experiences
- 2
Describe the actions you took to identify the issue
- 3
Explain the potential problem that was avoided
- 4
Highlight any tools or methods used in your identification process
- 5
Conclude with the positive outcome or lesson learned
Example Answers
In my previous job, I noticed a drop in airflow readings while monitoring the HVAC system. I investigated and found that the air filters were clogged. I changed them immediately, which prevented the system from overheating and breaking down during peak usage.
Tell me about a project where you collaborated with others to improve filter maintenance processes.
How to Answer
- 1
Choose a specific project with clear outcomes.
- 2
Highlight your role and contributions in the collaboration.
- 3
Include metrics or results that show improvement.
- 4
Discuss the teamwork and communication strategies used.
- 5
Describe any challenges faced and how they were overcome.
Example Answers
In my last role, I worked on a project aimed at reducing filter change downtime. I collaborated with the maintenance team, and we implemented a shared schedule for filter replacements. This reduced our maintenance time by 30%, as we could plan better and avoid overlap with production schedules.
Don't Just Read Filter Changer Questions - Practice Answering Them!
Reading helps, but actual practice is what gets you hired. Our AI feedback system helps you improve your Filter Changer interview answers in real-time.
Personalized feedback
Unlimited practice
Used by hundreds of successful candidates
Have you ever missed a critical maintenance step? What did you learn from that experience?
How to Answer
- 1
Acknowledge the mistake honestly without dwelling on it.
- 2
Explain the specific step you missed and its impact.
- 3
Discuss how you handled the situation afterward.
- 4
Share what system or change you implemented to avoid future mistakes.
- 5
Conclude with a positive note about continuous improvement.
Example Answers
Yes, I once forgot to replace a filter during a routine check. This led to reduced efficiency for a short time. I quickly informed my supervisor, corrected the mistake, and since then, I've used a checklist to ensure I never miss critical steps.
Describe a situation where you had multiple filters to change in a short timeframe. How did you prioritize?
How to Answer
- 1
Assess the urgency of each filter change based on their impact.
- 2
Communicate with the team if needed to clarify priorities.
- 3
Break down tasks into manageable steps and tackle the most critical filters first.
- 4
Consider the sequence in which filters need to be changed to streamline the process.
- 5
Document the process for future reference to improve efficiency.
Example Answers
In a previous job, I was tasked with changing air filters in several buildings during a maintenance rush. I prioritized the buildings with the oldest filters first since they had the highest risk of causing performance issues. I then communicated with my team about my plan, ensuring we tackled one building at a time efficiently, keeping track of which filters we had completed.
How do you communicate filter change requirements to a team member who is unaware of the standards?
How to Answer
- 1
Start with a clear overview of the filter change standards.
- 2
Use simple language and avoid technical jargon.
- 3
Provide visual aids or reference materials if possible.
- 4
Encourage questions to ensure understanding.
- 5
Offer to demonstrate the process if needed.
Example Answers
I would explain the filter change standards in simple terms, making sure to outline why they are important. I'd provide a quick reference guide and invite them to ask any questions.
Describe a time when you took the initiative to improve a filter maintenance procedure.
How to Answer
- 1
Think of a specific instance where you identified an issue or inefficiency.
- 2
Explain the steps you took to address the problem.
- 3
Highlight the positive outcome or results of your initiative.
- 4
Use metrics or data if possible to demonstrate success.
- 5
Show how your action benefited the team or organization.
Example Answers
In my previous role, I noticed that our filter change intervals were causing us to over-maintain some filters while under-maintaining others. I proposed a new tracking system to assess filter performance based on usage metrics. This reduced our filter costs by 20% and improved air quality in the facility.
Can you recount an instance where you had to quickly adapt to a new filter type or technology?
How to Answer
- 1
Choose a specific example from your past experience.
- 2
Describe the context and what prompted the change.
- 3
Explain the steps you took to learn about the new filter.
- 4
Highlight any challenges you faced and how you overcame them.
- 5
Conclude with the positive outcome or what you learned from the experience.
Example Answers
In my previous job, we switched to a new HEPA filter system due to new regulations. I researched the new technology, attended a training session, and collaborated with my team to update our maintenance procedures. Despite initial confusion, we successfully implemented the filters, improving air quality significantly.
What was the most valuable lesson you learned from a previous job related to filter changes?
How to Answer
- 1
Reflect on specific filter change experiences
- 2
Identify a key lesson that improves efficiency or safety
- 3
Use examples that highlight your ability to adapt
- 4
Be concise and focus on the lesson's impact on your work
- 5
Connect the lesson to how it can benefit the new role
Example Answers
In my last role, I learned the importance of adhering strictly to the maintenance schedule. It taught me that timely filter changes prevent system failures and enhance equipment lifespan. This habit improved our entire team's efficiency.
Have you ever had to train a new employee on filter changes? How did you approach it?
How to Answer
- 1
Start with a clear explanation of the importance of filter changes.
- 2
Demonstrate the step-by-step process using visual aids or hands-on practice.
- 3
Encourage questions and provide immediate feedback during training.
- 4
Assign a simple task for the new employee to perform under your supervision.
- 5
Follow up to ensure they understand and can perform the task independently.
Example Answers
Yes, I have trained a new employee on filter changes. I began by explaining why regular filter changes are crucial for equipment efficiency. Then, I demonstrated the process step-by-step, using hands-on training to reinforce learning. I encouraged them to ask questions and provided feedback as they practiced. Finally, I assigned them to perform a filter change while I supervised, ensuring they felt confident to do it on their own later.
Don't Just Read Filter Changer Questions - Practice Answering Them!
Reading helps, but actual practice is what gets you hired. Our AI feedback system helps you improve your Filter Changer interview answers in real-time.
Personalized feedback
Unlimited practice
Used by hundreds of successful candidates
Situational Interview Questions
If you notice that a newly installed filter is not functioning as expected, how would you proceed?
How to Answer
- 1
Check the installation instructions to confirm proper setup
- 2
Inspect the filter for any visible damage or obstructions
- 3
Verify that the system is compatible with the filter type
- 4
Test the flow rate to see if it meets expected standards
- 5
Document any findings and communicate with your supervisor or supplier
Example Answers
I would first review the installation instructions to ensure everything was done correctly. Then, I would check the filter for visible damage and confirm that it's the right type for the system.
You have a tight deadline for changing several filters in different locations. How would you decide which to tackle first?
How to Answer
- 1
Assess the urgency of each location based on operational needs.
- 2
Consider the accessibility of the filters; tackle harder to reach locations first.
- 3
Prioritize locations with higher demand or risk of failure.
- 4
Evaluate the time each filter change typically takes.
- 5
Communicate with team members for insights on any specific issues.
Example Answers
I would first assess which location has the most immediate need based on operational output. Then, I would prioritize the harder-to-reach filters to ensure efficiency.
Don't Just Read Filter Changer Questions - Practice Answering Them!
Reading helps, but actual practice is what gets you hired. Our AI feedback system helps you improve your Filter Changer interview answers in real-time.
Personalized feedback
Unlimited practice
Used by hundreds of successful candidates
What would you do if a coworker disagrees with your approach to changing a filter?
How to Answer
- 1
Stay calm and listen to their perspective
- 2
Ask for specific reasons behind their disagreement
- 3
Explain your approach and reasoning clearly
- 4
Seek a compromise if possible to ensure safety and efficiency
- 5
Focus on the shared goal of effective filter changing
Example Answers
I would first listen to my coworker's concerns to understand their point of view. After that, I would share my reasoning and the benefits of my approach. If we still disagreed, I would propose we test both methods to see which works best, ensuring team collaboration.
If you find out that the filter you need is out of stock, how would you handle the situation?
How to Answer
- 1
Check for alternative filters that can be used temporarily.
- 2
Contact your supplier to find out when the stock will be replenished.
- 3
Notify your supervisor or team about the shortage.
- 4
Consider adjusting your schedule to accommodate the delay.
- 5
Explore other suppliers for immediate purchase options.
Example Answers
If I find the filter is out of stock, I would first look for any alternative filters that can work in the meantime. Then, I would reach out to our supplier to check when they expect to have it back in stock and inform my supervisor about the situation.
You are faced with a malfunctioning filter system that your training didn't cover. What steps would you take to resolve the issue?
How to Answer
- 1
Assess the symptoms of the malfunction.
- 2
Check for any visible issues like leaks or blockages.
- 3
Refer to the system's manual or troubleshooting guide if available.
- 4
Consult with a colleague or supervisor for assistance.
- 5
Document your findings and steps taken for future reference.
Example Answers
I would start by observing the filter system to identify any obvious issues. Then, I would check the manual to see if there are troubleshooting steps. If I'm still unsure, I would ask a colleague for help and document our findings.
If a customer reports a persistent problem after a filter change, how would you address their concerns?
How to Answer
- 1
Listen actively to the customer's concerns without interrupting.
- 2
Ask specific questions to understand the issue more clearly.
- 3
Reassure the customer that you take their concerns seriously.
- 4
Explain potential reasons for the persistent problem and possible solutions.
- 5
Follow up with a plan to resolve the issue and keep the customer informed.
Example Answers
I would first listen to the customer's concerns carefully to understand the issue. Then I'd ask them about the symptoms they're experiencing and reassure them that I will help find a solution. I would explain that there could be several reasons for the problem, such as installation issues or other factors, and would suggest steps to troubleshoot further.
If you were asked to perform a filter change in an environment with hazardous materials, what precautions would you take?
How to Answer
- 1
Wear appropriate personal protective equipment (PPE) including gloves, goggles, and masks.
- 2
Ensure proper ventilation in the area where the filter change will be performed.
- 3
Follow established safety protocols and emergency procedures for hazardous materials.
- 4
Label all materials and containers clearly to avoid contamination.
- 5
Dispose of used filters and PPE according to hazardous waste disposal guidelines.
Example Answers
I would wear the necessary PPE such as gloves and respirators, ensure the area is well-ventilated, and follow safety protocols for handling hazardous materials.
If a filter change is delayed due to unexpected circumstances, how would you update relevant stakeholders?
How to Answer
- 1
Immediately notify stakeholders of the delay.
- 2
Be clear about the reasons for the delay.
- 3
Provide a new estimated timeline for the filter change.
- 4
Offer solutions or alternatives if possible.
- 5
Maintain open communication until the situation is resolved.
Example Answers
I would inform all relevant parties as soon as I am aware of the delay, explaining why it's happening and providing a new expected completion date. I would also suggest temporary alternatives if they are available.
In the event of an emergency leak due to a faulty filter, what would be your immediate steps?
How to Answer
- 1
Assess the situation quickly to identify the source of the leak.
- 2
Shut off any relevant valves or equipment to stop the leak if it's safe to do so.
- 3
Put on appropriate personal protective equipment (PPE) to ensure safety.
- 4
Contain the leak to minimize damage and prevent hazards.
- 5
Report the incident to a supervisor and follow emergency protocols.
Example Answers
First, I would identify the source of the leak and quickly assess the situation. Then, I would turn off any valves that could prevent further leakage, ensuring my safety with proper PPE. Next, I would contain the leak using absorbent materials or containers before informing my supervisor about the incident.
How would you handle a situation where the filters you received appear to be defective?
How to Answer
- 1
Inspect the filters thoroughly for any visible defects.
- 2
Document the issues with photographs and notes.
- 3
Notify the supplier immediately with clear details of the defects.
- 4
Check if there are alternative filters available to avoid downtime.
- 5
Follow up on the resolution to ensure timely replacement or credit.
Example Answers
I would first inspect the filters to confirm the defects and take notes and photos of the issues. Then, I would contact the supplier right away to report the problem and request replacements. Meanwhile, I would look into whether there are alternative filters we can use in the short term.
Don't Just Read Filter Changer Questions - Practice Answering Them!
Reading helps, but actual practice is what gets you hired. Our AI feedback system helps you improve your Filter Changer interview answers in real-time.
Personalized feedback
Unlimited practice
Used by hundreds of successful candidates
Technical Interview Questions
What tools do you typically use to perform filter changes, and how do you ensure they are in good condition?
How to Answer
- 1
Identify specific tools like wrenches, screwdrivers, and oil filter wrenches relevant to filter changes.
- 2
Mention any safety equipment used, such as gloves and goggles.
- 3
Describe how you inspect filters for wear, leaks, or blockages before installation.
- 4
Explain routine maintenance checks on tools to ensure they are in good working condition.
- 5
Discuss how you keep a checklist or documentation for tool condition and maintenance.
Example Answers
I typically use a wrench and an oil filter wrench to remove filters. Before changing, I check the condition of the filters for any leaks or damage and also ensure my tools are clean and well-maintained by performing routine checks.
Explain how you would identify the type of filter needed for a specific system.
How to Answer
- 1
Assess the system's requirements and specifications.
- 2
Check the manufacturer's documentation for filter recommendations.
- 3
Determine the type of contaminants the filter needs to remove.
- 4
Identify the size and fitting compatibility of the filter.
- 5
Consider the environment where the filter will be used.
Example Answers
To identify the needed filter, I start by checking the system's specifications to understand its requirements. Then, I refer to the manufacturer's documentation for recommended filters based on those specifications. I also consider what contaminants need to be filtered out and ensure the filter size and fittings match the system.
Don't Just Read Filter Changer Questions - Practice Answering Them!
Reading helps, but actual practice is what gets you hired. Our AI feedback system helps you improve your Filter Changer interview answers in real-time.
Personalized feedback
Unlimited practice
Used by hundreds of successful candidates
What safety precautions do you take when changing filters?
How to Answer
- 1
Always wear personal protective equipment such as gloves and safety goggles.
- 2
Ensure the system is turned off and properly locked out before starting work.
- 3
Check for any residual chemical exposure on the filter surface and clean if necessary.
- 4
Be aware of any sharp edges or parts and handle them carefully.
- 5
Dispose of used filters according to safety regulations and wear appropriate gear.
Example Answers
I always wear gloves and goggles when changing filters. I also make sure to turn off and lock out the equipment to prevent any accidents. I inspect the filter for chemical residues and handle it with care to avoid any sharp edges.
Can you walk us through the step-by-step process of changing a filter in a mechanical system?
How to Answer
- 1
Identify the type of filter and system involved.
- 2
Gather all necessary tools and safety equipment before starting.
- 3
Shut down the system and ensure it is safe to work on.
- 4
Remove the old filter carefully to avoid spills or damage.
- 5
Install the new filter, ensuring it is sealed properly.
Example Answers
To change a filter, I first identify the filter type and gather my tools, including gloves and wrenches. Then, I shut down the system to ensure safety. After that, I carefully remove the old filter, checking for any leaks. Finally, I install the new filter and ensure it's secured tightly.
How do you ensure compliance with filter change schedules and regulations?
How to Answer
- 1
Create a detailed schedule for filter changes based on manufacturer guidelines and operational needs.
- 2
Utilize reminders and tracking systems to monitor when filters need to be replaced.
- 3
Regularly review compliance regulations to ensure all practices meet industry standards.
- 4
Document each filter change to maintain a clear record for audits and evaluations.
- 5
Train team members on the importance of compliance and proper filter changing procedures.
Example Answers
I ensure compliance by creating a filter change schedule based on manufacturer recommendations and operational needs. I also use reminders to track when filters need changing and document every change for clear records.
What maintenance checks do you perform on the equipment associated with filters?
How to Answer
- 1
Identify the specific filters you work with and their maintenance requirements.
- 2
Mention routine checks like visual inspections for damage or wear.
- 3
Discuss assessing the operational performance and efficiency of filters.
- 4
Include cleaning, replacement schedules, and proper documentation.
- 5
Highlight the importance of safety protocols during maintenance.
Example Answers
I perform visual inspections on the filters for any signs of wear, check the performance to ensure they're operating efficiently, and follow the manufacturer's cleaning and replacement schedule.
How do you evaluate the performance of a filter post-installation?
How to Answer
- 1
Check for any leaks immediately after installation.
- 2
Monitor pressure drop across the filter to ensure it is functioning.
- 3
Inspect the quality of the output air or fluid for clarity and cleanliness.
- 4
Use testing equipment like manometers to measure performance metrics.
- 5
Conduct regular maintenance checks to assess long-term efficiency.
Example Answers
After installing a filter, I first check for any leaks to ensure a tight seal. Then, I monitor the pressure drop to verify it's within spec. I also inspect the output to confirm the air quality meets our standards.
How do you keep track of filter inventory and ensure you have the correct types available?
How to Answer
- 1
Utilize inventory management software to track stock levels and types.
- 2
Regularly conduct physical inventory checks to ensure accuracy.
- 3
Create a reorder schedule based on usage rates to avoid shortages.
- 4
Maintain a log for filter types and their specifications for easy reference.
- 5
Communicate with suppliers to ensure timely restocking of popular filter types.
Example Answers
I use inventory management software to keep an up-to-date log of all filter types and quantities. This software sends notifications when stocks are low, and I conduct physical checks monthly to confirm accuracy.
What considerations do you make regarding the environmental impact of disposing of old filters?
How to Answer
- 1
Research local regulations on waste disposal and recycling for filters
- 2
Consider the materials used in the filters and their impact on the environment
- 3
Look for recycling programs specifically for used filters
- 4
Educate yourself on the proper disposal methods to minimize pollution
- 5
Advocate for the use of eco-friendly filter options
Example Answers
I always check local guidelines for disposing of filters, ensuring they are recycled properly. I also prefer filters that are made from recyclable materials to lower environmental impact.
What types of filters are you familiar with, and how do you determine their maintenance needs?
How to Answer
- 1
List specific types of filters you have experience with such as HVAC, oil, air, or water filters.
- 2
Explain the importance of following manufacturer guidelines for maintenance.
- 3
Discuss frequency of checks and replacements based on usage and environment.
- 4
Mention any tools or indicators you use to assess the condition of filters.
- 5
Provide examples of common maintenance schedules or visual inspection methods you employ.
Example Answers
I am familiar with HVAC filters and air filters. I follow the manufacturer's recommended maintenance schedule and check the filters monthly for dirt or blockage. If they're visibly dirty or haven't been changed in three months, I replace them.
Don't Just Read Filter Changer Questions - Practice Answering Them!
Reading helps, but actual practice is what gets you hired. Our AI feedback system helps you improve your Filter Changer interview answers in real-time.
Personalized feedback
Unlimited practice
Used by hundreds of successful candidates
Filter Changer Position Details
Related Positions
Similar positions you might be interested in.
Ace Your Next Interview!
Practice with AI feedback & get hired faster
Personalized feedback
Used by hundreds of successful candidates
Ace Your Next Interview!
Practice with AI feedback & get hired faster
Personalized feedback
Used by hundreds of successful candidates