Top 32 Strainer Interview Questions and Answers [Updated 2025]
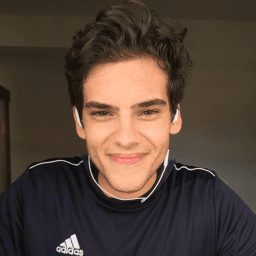
Andre Mendes
•
March 30, 2025
Navigating a job interview can be daunting, especially for specialized roles like a Strainer. In this updated guide for 2025, we delve into the most common interview questions candidates face. Discover example answers and insightful tips that will help you respond effectively and confidently. Whether you're a seasoned professional or new to the field, prepare to impress and secure your next opportunity.
Download Strainer Interview Questions in PDF
To make your preparation even more convenient, we've compiled all these top Strainerinterview questions and answers into a handy PDF.
Click the button below to download the PDF and have easy access to these essential questions anytime, anywhere:
List of Strainer Interview Questions
Situational Interview Questions
What would you do if you were faced with multiple straining tasks with tight deadlines?
How to Answer
- 1
Prioritize tasks based on urgency and importance.
- 2
Break down tasks into smaller, manageable steps.
- 3
Communicate with your team or supervisor about deadlines.
- 4
Set clear timelines for each smaller task.
- 5
Stay organized with a task management tool or list.
Example Answers
I would assess the tasks, prioritize them by deadline, and focus on the most urgent ones first. Then, I would break down each task into smaller steps to tackle them efficiently.
If you encounter a blockage in the strainer, how would you troubleshoot the issue?
How to Answer
- 1
Immediately stop the flow to avoid damage.
- 2
Inspect the strainer visually to identify the blockage.
- 3
Clean or replace the strainer as needed based on condition.
- 4
Check upstream and downstream for additional blockages.
- 5
Document the issue and solutions for future reference.
Example Answers
I would first stop the flow to prevent any further damage, then visually inspect the strainer to see what is causing the blockage. Depending on what I find, I would either clean it or replace it. I would also check both upstream and downstream systems to ensure there are no further blockages.
Don't Just Read Strainer Questions - Practice Answering Them!
Reading helps, but actual practice is what gets you hired. Our AI feedback system helps you improve your Strainer interview answers in real-time.
Personalized feedback
Unlimited practice
Used by hundreds of successful candidates
How would you handle a situation where a coworker disagrees with your method of straining?
How to Answer
- 1
Listen to your coworker's concerns fully
- 2
Ask questions to understand their perspective
- 3
Explain your reasoning and the benefits of your method
- 4
Suggest a trial of both methods if feasible
- 5
Keep the conversation respectful and collaborative
Example Answers
I would first listen carefully to my coworker's perspective and understand their concerns. Then, I would explain my straining method and its advantages. If they still disagreed, I would suggest we try both methods on a small scale to see which one yields better results.
If you notice a repeated issue with a particular batch during straining, what steps would you take to address it?
How to Answer
- 1
Identify the specific issue with the batch during straining
- 2
Review the straining process and equipment used
- 3
Consult with team members or supervisors for insights
- 4
Implement a temporary adjustment or fix to mitigate the issue
- 5
Document the findings and any changes made for future reference
Example Answers
I would first pinpoint what the repeating issue is, then I would examine the equipment and procedures used for that batch. If needed, I would involve more experienced colleagues to brainstorm solutions. Next, I would try a temporary fix and keep track of any adjustments made for future batches.
How would you approach training a new team member on straining techniques?
How to Answer
- 1
Start with a thorough introduction to the different straining techniques.
- 2
Demonstrate each technique step-by-step, allowing time for questions.
- 3
Provide hands-on practice with real scenarios to build confidence.
- 4
Use feedback sessions to address any difficulties they encounter.
- 5
Encourage continuous learning by sharing additional resources.
Example Answers
I would begin by introducing the various straining techniques and ensure that the new member understands the purpose behind each one. Then, I would demonstrate them, explaining each step, and encourage questions to clarify any doubts.
How would you manage your time if you were required to handle multiple types of strainers simultaneously?
How to Answer
- 1
Prioritize tasks based on urgency and importance.
- 2
Create a schedule for each type of strainer to allocate specific time slots.
- 3
Use a checklist to ensure all tasks are completed on time.
- 4
Communicate proactively with team members about your progress.
- 5
Adjust your plan as necessary based on workload and deadlines.
Example Answers
I would assess which strainers need immediate attention and prioritize them. Then, I’d allocate specific time to work on each type of strainer throughout my day while using a checklist to keep track of my progress.
If a colleague insists on using a substandard process for straining, how would you handle that?
How to Answer
- 1
Address the situation calmly and privately.
- 2
Ask questions to understand their reasoning and perspective.
- 3
Share data or examples that support a better process.
- 4
Suggest a trial of both methods to assess the results.
- 5
Be collaborative and open to reaching a compromise.
Example Answers
I would first speak to my colleague privately to understand why they prefer the substandard process. I would share my concerns and suggest we compare the outcomes of both processes to see which performs better.
What would you do in the event of an accident while operating the strainer?
How to Answer
- 1
Stay calm and assess the situation quickly
- 2
Shut down the equipment to prevent further harm
- 3
Administer first aid if anyone is injured
- 4
Report the incident to your supervisor immediately
- 5
Follow the safety protocols outlined in the training
Example Answers
In the event of an accident, I would stay calm, shut down the strainer to prevent any further issues, and ensure that anyone injured receives first aid. Then, I would report the incident to my supervisor right away.
How would you adapt to new straining technologies or methods introduced in the workplace?
How to Answer
- 1
Stay informed about industry trends and new technologies.
- 2
Participate in training sessions or workshops offered by the employer.
- 3
Experiment with new methods in a controlled environment before full implementation.
- 4
Seek feedback from colleagues who are experienced with the new technology.
- 5
Document your learning process to share insights with the team.
Example Answers
I would keep up with the latest straining technologies through industry publications and webinars. When new methods are introduced, I would take part in any training sessions to fully understand their applications.
If your performance as a strainer is evaluated regularly, how would you prepare for such assessments?
How to Answer
- 1
Review past performance feedback and identify improvement areas
- 2
Set specific, measurable goals for your performance
- 3
Regularly practice straining techniques to enhance skill
- 4
Seek feedback from colleagues or supervisors proactively
- 5
Stay updated with industry best practices for straining
Example Answers
To prepare for performance assessments, I regularly review feedback to identify areas for improvement. I then set clear goals for myself, such as reducing error rates in straining processes by a certain percentage. I also practice my techniques regularly to ensure I maintain high standards.
Don't Just Read Strainer Questions - Practice Answering Them!
Reading helps, but actual practice is what gets you hired. Our AI feedback system helps you improve your Strainer interview answers in real-time.
Personalized feedback
Unlimited practice
Used by hundreds of successful candidates
How would you handle a situation where a customer is unhappy with a product processed through your straining?
How to Answer
- 1
Listen to the customer's concerns without interrupting.
- 2
Acknowledge the issue and empathize with their disappointment.
- 3
Ask clarifying questions to understand the specific problem.
- 4
Offer a solution, whether it's a replacement, refund, or additional service.
- 5
Follow up to ensure the customer is satisfied with the resolution.
Example Answers
I would first listen carefully to the customer's feedback and let them express their concerns. I would acknowledge their feelings and apologize for the inconvenience. Then, I would ask specific questions about what went wrong and offer to replace the product or provide a refund if necessary. Lastly, I would follow up to ensure they are happy with the resolution.
If you were short on materials necessary for a straining job, how would you address the issue?
How to Answer
- 1
Assess the situation and identify the specific materials lacking
- 2
Explore alternative materials that can serve the same purpose
- 3
Communicate with team members or suppliers for quick solutions
- 4
Prioritize the most critical tasks to ensure work continues
- 5
Document the issue to prevent future shortages.
Example Answers
I would first identify exactly what materials are missing and evaluate if there are any substitutes available. Then, I would reach out to my colleagues or suppliers to see if they can provide what we need quickly. Meanwhile, I would focus on any other tasks that could be completed without those materials.
Behavioral Interview Questions
Can you describe a time when you had to solve a difficult problem while straining materials?
How to Answer
- 1
Identify a specific challenging situation you faced with straining.
- 2
Explain the techniques or tools you used to address the problem.
- 3
Discuss the outcomes of your approach and what you learned.
- 4
Use the STAR method: situation, task, action, result.
- 5
Keep your answer focused on your role in solving the issue.
Example Answers
In my previous job, we had an issue with the mesh size during material straining which caused product inconsistency. I analyzed the strain method and noticed that the mesh was clogged. I switched to a coarser mesh and monitored the flow rates, which improved the output quality by 30%. This taught me the importance of regularly checking equipment to avoid processing delays.
Tell me about a time you worked closely with a team to improve the straining process.
How to Answer
- 1
Start with a specific example and set the context.
- 2
Describe your role and the team dynamics.
- 3
Explain the issue with the previous straining process.
- 4
Share the steps your team took to improve it.
- 5
Conclude with the results and what you learned.
Example Answers
In my last role, our team noticed that the straining process was slow and often resulted in product loss. I was assigned as the lead on a project to address this. We analyzed the issues, identified bottlenecks, and collaborated to redesign the workflow. We implemented a new strainer with a more efficient design, which reduced time by 30% and minimized waste. This experience taught me the importance of teamwork and effective communication.
Don't Just Read Strainer Questions - Practice Answering Them!
Reading helps, but actual practice is what gets you hired. Our AI feedback system helps you improve your Strainer interview answers in real-time.
Personalized feedback
Unlimited practice
Used by hundreds of successful candidates
Describe an instance where you had to adapt to a significant change in your work environment as a strainer.
How to Answer
- 1
Identify a specific change you experienced
- 2
Explain the reasons for the change
- 3
Describe your initial reaction and challenges faced
- 4
Discuss the steps you took to adapt
- 5
Highlight the positive outcome or lesson learned
Example Answers
In my previous position, our team switched from manual straining processes to an automated system. At first, I was hesitant due to the learning curve. I took the initiative to attend training sessions, practiced on the new machines after hours, and sought help from experienced colleagues. Eventually, I became proficient and helped train others, leading to increased efficiency in our operations.
Give an example of how your attention to detail made a difference in your work as a strainer.
How to Answer
- 1
Think of a specific situation where detail was critical.
- 2
Describe the problem you faced due to oversight or lack of detail.
- 3
Explain how your attention to detail resolved the issue.
- 4
Highlight the positive outcome resulting from your actions.
- 5
Keep the explanation concise and focused on your role.
Example Answers
In my previous position, I noticed that some import materials had minor inconsistencies. By double-checking each batch before processing, I prevented potential contamination issues, which led to an increase in the quality of our final product.
Can you provide an example of how you effectively communicated with your team regarding straining procedures?
How to Answer
- 1
Describe a specific situation where communication was key.
- 2
Mention the tools or methods you used (meetings, emails, etc.).
- 3
Highlight any challenges faced and how you overcame them.
- 4
Emphasize the outcome and its impact on the team or process.
- 5
Keep your response focused on clarity and teamwork.
Example Answers
In my last position, I led a team meeting where we discussed new straining procedures. I prepared a visual presentation to illustrate the steps clearly. After the meeting, I sent out a follow-up email summarizing the key points and invited team members to ask questions. This helped ensure everyone was on the same page, and we successfully implemented the new procedures without issue.
Describe a time when you took the initiative to improve a straining process.
How to Answer
- 1
Think of a specific situation where you noticed a problem.
- 2
Explain what steps you took to address the issue.
- 3
Emphasize the positive outcomes of your actions.
- 4
Use metrics or data to illustrate the improvements if available.
- 5
Make it clear how your initiative benefited the team or project.
Example Answers
In my previous job, I saw that our straining process was taking too long during production. I researched alternative methods and proposed implementing a new strainer design that reduced processing time by 30%. After testing, we adopted this new system, which improved efficiency and cut costs.
How have you handled constructive criticism regarding your straining methods in the past?
How to Answer
- 1
Acknowledge the criticism and show you appreciated the feedback.
- 2
Explain the specific criticism you received and how it was communicated.
- 3
Describe the actions you took to improve your straining methods.
- 4
Mention any positive outcomes or results from implementing changes.
- 5
Highlight your openness to continuous improvement and learning.
Example Answers
In my previous role, I received feedback about my straining technique being inefficient. I appreciated the input as it helped me recognize areas for improvement. After discussing with my supervisor, I adopted a new technique that reduced the time taken. As a result, the quality of the strained products improved significantly.
What keeps you motivated in a role that requires repetitive tasks like straining?
How to Answer
- 1
Focus on the importance of consistency and reliability in the role.
- 2
Mention setting personal goals to stay engaged with the task.
- 3
Discuss finding satisfaction in the quality of work produced.
- 4
Highlight the role's contribution to the bigger picture of the team's success.
- 5
Talk about routines that help maintain a positive mindset during repetitive work.
Example Answers
I stay motivated by focusing on the importance of getting the task done accurately. Setting daily goals helps me see progress and keeps me engaged.
Can you talk about a particularly challenging straining project and how you managed it?
How to Answer
- 1
Identify a specific challenging project you faced.
- 2
Explain the nature of the challenge clearly.
- 3
Describe the steps you took to overcome the challenge.
- 4
Highlight the results or what you learned from the experience.
- 5
Keep your answer focused and concise, using the STAR method (Situation, Task, Action, Result).
Example Answers
In my last position, I worked on a project where we had to strain a new type of material that was much denser than we had previously dealt with. The main challenge was adjusting our equipment settings to effectively handle the increased load. I collaborated with our engineering team to recalibrate the strainers, and after several trials, we found the right balance. The final product met all quality standards ahead of schedule.
Don't Just Read Strainer Questions - Practice Answering Them!
Reading helps, but actual practice is what gets you hired. Our AI feedback system helps you improve your Strainer interview answers in real-time.
Personalized feedback
Unlimited practice
Used by hundreds of successful candidates
Technical Interview Questions
What types of materials do you have experience straining, and what methods do you use?
How to Answer
- 1
Identify specific materials you've strained, like liquids, solids, or specific food items.
- 2
Mention the straining techniques you're familiar with, for example using filters, sieves, or strainers.
- 3
Highlight any equipment or tools you commonly use for straining.
- 4
Discuss the context in which you performed straining, like in cooking, laboratory work, or manufacturing.
- 5
Be clear and concise, providing relevant details to demonstrate your experience.
Example Answers
I have experience straining liquids like stocks and sauces using a fine mesh strainer. I also strain solids like pasta using a colander. In my previous job, I frequently used a cheesecloth to strain yogurt.
What straining equipment are you most familiar with, and how do you maintain it?
How to Answer
- 1
Identify specific types of straining equipment you have used.
- 2
Explain your regular maintenance routine for each type.
- 3
Mention any troubleshooting experience you have with the equipment.
- 4
Highlight the importance of cleanliness and proper storage.
- 5
Be prepared to discuss any safety protocols you follow.
Example Answers
I am most familiar with vibrating screen separators. I maintain them by regularly checking the tension on the screens, cleaning them to prevent clogging, and lubricating moving parts to ensure smooth operation.
Don't Just Read Strainer Questions - Practice Answering Them!
Reading helps, but actual practice is what gets you hired. Our AI feedback system helps you improve your Strainer interview answers in real-time.
Personalized feedback
Unlimited practice
Used by hundreds of successful candidates
How do you ensure the quality and consistency of the strained products?
How to Answer
- 1
Follow strict standard operating procedures for straining.
- 2
Regularly calibrate and maintain straining equipment.
- 3
Conduct quality checks at various stages of the straining process.
- 4
Implement a tasting panel to evaluate product consistency.
- 5
Document all processes and quality control measures for review.
Example Answers
I ensure quality and consistency by following established SOPs for straining, regularly calibrating the equipment, and performing quality checks during the process to catch any inconsistencies early.
What safety protocols do you follow while operating straining equipment?
How to Answer
- 1
Always wear personal protective equipment (PPE) such as gloves and goggles.
- 2
Ensure equipment is properly maintained and inspected before use.
- 3
Follow operational guidelines for straining equipment to avoid accidents.
- 4
Keep work areas clean and free of hazards to prevent slips or falls.
- 5
Be aware of emergency shutdown procedures and first aid protocols.
Example Answers
I always wear my PPE, including gloves and safety goggles, to protect against any spills or splashes while straining.
How do you identify when a straining process is not performing as expected?
How to Answer
- 1
Monitor key performance metrics consistently during operation
- 2
Look for deviations from baseline performance data
- 3
Check for unusual noise, pressure drops, or flow inconsistencies
- 4
Regularly inspect equipment for wear and malfunctions
- 5
Conduct periodic reviews and analyze output quality
Example Answers
I identify issues by tracking key performance metrics such as throughput and pressure. If I notice any deviation from our established norms, I investigate further.
What strategies have you employed to optimize the straining process?
How to Answer
- 1
Analyze the current straining methods and identify bottlenecks
- 2
Implement equipment upgrades based on material characteristics
- 3
Train staff on best practices and standard operating procedures
- 4
Regularly monitor and adjust parameters for optimal performance
- 5
Document and review each straining cycle to identify areas for improvement
Example Answers
I analyzed our straining process and identified that our mesh size was too fine, causing clogging. I upgraded to a coarser mesh and reduced downtime.
What steps would you take to troubleshoot a malfunction with your strainer?
How to Answer
- 1
Identify the specific issue with the strainer
- 2
Check for clogs or obstructions in the mesh
- 3
Inspect the strainer's fittings and connections
- 4
Test the flow rate to determine pressure drops
- 5
Replace or clean components as necessary
Example Answers
First, I would identify the symptoms of the malfunction, such as reduced flow or unusual noise. Then, I would check for any clogs in the mesh by inspecting it visually or backflushing it. If everything seems clear, I would check the fittings to ensure they are secure and not leaking. Finally, I would measure the flow rate to see if there's a significant drop, indicating a potential internal issue.
What do you know about the properties of materials that affect the straining process?
How to Answer
- 1
Focus on key properties like tensile strength and ductility
- 2
Mention the effects of temperature on material behavior
- 3
Discuss the impact of grain structure on straining
- 4
Include examples of different materials and their straining characteristics
- 5
Conclude with how understanding these properties aids in manufacturing processes
Example Answers
Materials like steel have high tensile strength and moderate ductility, making them ideal for straining processes. Ductility allows them to deform without breaking. Higher temperatures can improve ductility, enabling more effective straining.
Describe your experience with routine maintenance of straining equipment.
How to Answer
- 1
Highlight specific straining equipment you have worked with.
- 2
Mention any preventative maintenance schedules you followed.
- 3
Discuss troubleshooting techniques you used for maintenance issues.
- 4
Include examples of improvements you made to maintenance processes.
- 5
Emphasize your attention to detail and safety practices.
Example Answers
I have experience with various straining equipment, including drum strainers and wedge wire screens. In my previous role, I followed a weekly maintenance schedule to clean and inspect the strainers, ensuring they operated efficiently. I also developed a checklist that reduced equipment downtime by 20%.
How do you document and report your straining processes and outcomes?
How to Answer
- 1
Explain the tools you use for documentation like logs or software.
- 2
Mention how you ensure accuracy and consistency in your records.
- 3
Describe how you summarize key outcomes for reporting.
- 4
Talk about how you share these reports with relevant stakeholders.
- 5
Highlight the importance of regular updates and reviews of documentation.
Example Answers
I use a digital log to document the straining processes step by step, ensuring every detail is recorded accurately. I summarize the outcomes in a weekly report shared with my supervisor and team.
Don't Just Read Strainer Questions - Practice Answering Them!
Reading helps, but actual practice is what gets you hired. Our AI feedback system helps you improve your Strainer interview answers in real-time.
Personalized feedback
Unlimited practice
Used by hundreds of successful candidates
Strainer Position Details
Related Positions
Similar positions you might be interested in.
Ace Your Next Interview!
Practice with AI feedback & get hired faster
Personalized feedback
Used by hundreds of successful candidates
Ace Your Next Interview!
Practice with AI feedback & get hired faster
Personalized feedback
Used by hundreds of successful candidates