Top 29 Sterilizer Interview Questions and Answers [Updated 2025]
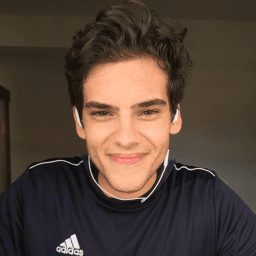
Andre Mendes
•
March 30, 2025
Preparing for a sterilizer role interview can be daunting, but we're here to help! This blog post covers the most common interview questions for the position, offering insightful example answers and practical tips on how to respond effectively. Whether you're a seasoned professional or new to the field, our comprehensive guide will equip you with the confidence to ace your interview and secure the job.
Download Sterilizer Interview Questions in PDF
To make your preparation even more convenient, we've compiled all these top Sterilizerinterview questions and answers into a handy PDF.
Click the button below to download the PDF and have easy access to these essential questions anytime, anywhere:
List of Sterilizer Interview Questions
Technical Interview Questions
What sterilization standards and regulations do you follow in your work?
How to Answer
- 1
Mention specific standards such as ISO, ANSI, or AAMI.
- 2
Explain how you stay updated on regulations.
- 3
Highlight any certifications you hold related to sterilization.
- 4
Discuss your experience with validating sterilization processes.
- 5
Emphasize the importance of compliance for safety and efficacy.
Example Answers
I follow AAMI and ISO 11135 standards for ethylene oxide sterilization. I regularly attend workshops to stay updated on the latest regulations and hold a certification in sterilization techniques.
What types of sterilization equipment are you familiar with, and how do you ensure they are maintained properly?
How to Answer
- 1
Identify and list specific types of sterilization equipment you have used.
- 2
Explain the maintenance procedures you follow for each type.
- 3
Mention any relevant experiences or training related to sterilization.
- 4
Highlight your attention to detail in maintenance activities.
- 5
Discuss the importance of following protocols and guidelines.
Example Answers
I am familiar with autoclaves, ethylene oxide sterilizers, and dry heat sterilizers. I ensure they are maintained by conducting routine checks, following the manufacturer’s guidelines for calibration, and keeping detailed logs of maintenance tasks.
Don't Just Read Sterilizer Questions - Practice Answering Them!
Reading helps, but actual practice is what gets you hired. Our AI feedback system helps you improve your Sterilizer interview answers in real-time.
Personalized feedback
Unlimited practice
Used by hundreds of successful candidates
Can you explain the difference between steam sterilization and ethylene oxide sterilization?
How to Answer
- 1
Define both steam sterilization and ethylene oxide sterilization clearly.
- 2
Highlight the types of materials each method is suitable for.
- 3
Mention the conditions under which each method is most effective.
- 4
Discuss the safety and environmental factors associated with each method.
- 5
Use concise examples to illustrate the differences.
Example Answers
Steam sterilization uses high-pressure steam at 121-134°C, ideal for heat-resistant items like surgical instruments, while ethylene oxide sterilization is a gas process effective for heat-sensitive items, performed at lower temperatures with longer cycles.
What are the key indicators that a sterilization cycle was successful?
How to Answer
- 1
Mention biological indicators to confirm sterilization.
- 2
Discuss physical indicators like temperature and pressure records.
- 3
Refer to chemical indicators and their color change.
- 4
Emphasize the importance of monitoring cycle time.
- 5
Talk about the verification of load placement for effective sterilization.
Example Answers
A successful sterilization cycle is confirmed by biological indicators showing no growth, proper temperature and pressure records, and color change in chemical indicators. You should also monitor the cycle time closely.
How do you validate the effectiveness of sterilization processes?
How to Answer
- 1
Explain the use of biological indicators to test sterilization efficacy
- 2
Mention routine monitoring and verification procedures
- 3
Discuss record-keeping for sterilization cycles
- 4
Highlight the importance of complying with industry standards
- 5
Emphasize training and competency assessments for staff
Example Answers
I validate sterilization processes by using biological indicators, where we place spore strips in the sterilizer. After the cycle, we incubate them to ensure no growth occurs. We also keep detailed records of all sterilization cycles and regularly review them.
What cleaning and disinfection procedures do you follow for sterilization equipment?
How to Answer
- 1
Start with the initial cleaning of equipment to remove organic matter
- 2
Detail the appropriate disinfectants used and their contact times
- 3
Mention any specific procedures for different types of sterilizers
- 4
Highlight the importance of following manufacturer's instructions
- 5
Discuss routine checks and maintenance of sterilization equipment
Example Answers
I begin by thoroughly cleaning the sterilization equipment to remove any debris, using an enzymatic cleaner. I then apply a hospital-grade disinfectant, ensuring it remains wet for the specified contact time. For steam sterilizers, I check the water quality regularly and perform routine calibration to ensure effectiveness.
What monitoring systems do you use to ensure the sterilization process is effective?
How to Answer
- 1
Identify the specific monitoring systems used, such as biological indicators and chemical indicators.
- 2
Explain the importance of regular validation and calibration of the sterilization equipment.
- 3
Discuss how data from monitoring systems is used to enhance processes and maintain compliance.
- 4
Mention any standards or regulations you adhere to in monitoring sterilization.
- 5
Highlight your experience with troubleshooting and responding to monitoring results.
Example Answers
I typically use biological indicators like spore tests and chemical indicators for monitoring. Regular calibration of the sterilizer is crucial, and I ensure compliance with industry standards like AAMI.
What safety precautions do you take when handling sterilization chemicals?
How to Answer
- 1
Always wear appropriate personal protective equipment (PPE) such as gloves, goggles, and masks.
- 2
Ensure proper ventilation in the area where chemicals are being used to avoid inhalation of fumes.
- 3
Follow the manufacturer's instructions regarding the dilution and mixing of sterilization chemicals.
- 4
Keep safety data sheets (SDS) accessible and familiarize yourself with the hazards of each chemical used.
- 5
Use compatible containers and tools when handling and storing sterilization chemicals to prevent reactions.
Example Answers
I always wear gloves, goggles, and a mask to protect myself when handling sterilization chemicals. I also ensure that the area has proper ventilation by keeping windows open or using exhaust fans.
What is the importance of packaging in the sterilization process?
How to Answer
- 1
Explain how packaging protects sterile items from contamination
- 2
Describe how it aids in the proper sterilization method selection
- 3
Mention the role of packaging in ensuring product integrity
- 4
Highlight the significance of packaging for storage and transport
- 5
Discuss the impact of packaging materials on the sterilization outcome
Example Answers
Packaging is essential as it protects sterile items from contamination during handling and storage. It ensures that the right sterilization method is applied, and helps maintain the integrity of the items until they are used.
What cycle parameters do you monitor during the sterilization process?
How to Answer
- 1
Focus on key parameters like temperature, pressure, and time required for sterilization.
- 2
Mention any specific standards or guidelines you adhere to.
- 3
Emphasize importance of monitoring for ensuring efficacy and safety.
- 4
Include examples of tools or equipment you use for monitoring.
- 5
Be ready to discuss how you respond to deviations in parameters.
Example Answers
During the sterilization process, I closely monitor temperature, pressure, and the sterilization time to ensure that all items are effectively sterilized according to protocol.
Don't Just Read Sterilizer Questions - Practice Answering Them!
Reading helps, but actual practice is what gets you hired. Our AI feedback system helps you improve your Sterilizer interview answers in real-time.
Personalized feedback
Unlimited practice
Used by hundreds of successful candidates
Behavioral Interview Questions
Describe a time when you worked as part of a team to improve sterilization processes. What role did you play?
How to Answer
- 1
Select a specific example from your past experience.
- 2
Focus on your specific role and contributions to the team's efforts.
- 3
Explain the outcome or improvements achieved by the team.
- 4
Use metrics or specific achievements to highlight success.
- 5
Practice articulating your answer clearly and confidently.
Example Answers
In my last role, our team noticed that our sterilization cycle times were longer than industry standards. I took the initiative to analyze the data and led discussions to identify bottlenecks. As a result, we implemented changes that reduced cycle times by 15% and increased efficiency.
Can you give an example of a challenging situation you faced while operating sterilization equipment? How did you resolve it?
How to Answer
- 1
Describe the specific sterilization equipment involved.
- 2
Explain the challenge clearly and concisely.
- 3
Outline the steps you took to resolve the issue.
- 4
Highlight any teamwork or communication that was involved.
- 5
Share what you learned from the experience and how it improved your skills.
Example Answers
While operating an autoclave, I noticed a temperature discrepancy during a cycle. I promptly stopped the machine, checked the sensors, and found a faulty reading. I communicated with my supervisor, replaced the sensor, and recalibrated the equipment. This experience taught me the importance of regular equipment checks.
Don't Just Read Sterilizer Questions - Practice Answering Them!
Reading helps, but actual practice is what gets you hired. Our AI feedback system helps you improve your Sterilizer interview answers in real-time.
Personalized feedback
Unlimited practice
Used by hundreds of successful candidates
Tell me about a time when your attention to detail significantly impacted the outcome of a sterilization procedure.
How to Answer
- 1
Choose a specific incident that showcases your attention to detail.
- 2
Describe the context and your role in the sterilization process.
- 3
Highlight the specific detail you noticed and why it was important.
- 4
Explain the positive outcome that resulted from your attention to that detail.
- 5
Use measurable results if possible to illustrate the impact.
Example Answers
In my previous role, I noticed that the sterilization indicators were not changing color during a batch. After investigating, I found that the temperature settings were incorrect. Correcting this ensured all equipment was properly sterilized, maintaining our compliance with safety standards.
Explain an instance where you identified a problem with the sterilization process. What steps did you take to address it?
How to Answer
- 1
Identify a specific instance that clearly shows your problem-solving skills.
- 2
Describe the nature of the problem and its potential impact on sterilization.
- 3
Outline the steps you took to investigate and resolve the issue.
- 4
Emphasize teamwork and communication if relevant.
- 5
Conclude with the outcome and any improvements made.
Example Answers
During a routine check, I noticed that the sterilization cycle was not reaching the required temperature. I investigated by reviewing the equipment calibration and discovered a faulty sensor. I coordinated with the maintenance team to replace the sensor and recalibrated the machine. After testing, the cycle performed correctly, and we implemented daily checks to prevent recurrences.
Discuss a situation where you had to prioritize safety in your work as a sterilizer. What measures did you take?
How to Answer
- 1
Identify a specific incident from your experience.
- 2
Explain the potential safety risks and their impact.
- 3
Detail the safety measures you implemented.
- 4
Highlight the outcome and any improvements.
- 5
Emphasize your commitment to a safe working environment.
Example Answers
In a previous role, I noticed that some sterilization equipment was not functioning properly, risking contamination. I immediately reported the issue to my supervisor, temporarily suspended use, and ensured all staff were informed. After the equipment was serviced, I helped develop a regular maintenance schedule, greatly reducing future risks.
Have you ever trained a new hire in sterilization procedures? What was your approach?
How to Answer
- 1
Start with a brief overview of the training experience.
- 2
Highlight your training methods, such as hands-on demonstrations.
- 3
Emphasize the importance of compliance with safety standards.
- 4
Mention how you assessed the new hire's understanding.
- 5
Include a positive outcome from the training process.
Example Answers
Yes, I trained a new hire in sterilization procedures by first providing a hands-on demonstration of the equipment. I emphasized safety protocols throughout the training and used checklists to ensure compliance. I regularly assessed their understanding through quizzes, and the new hire was certified within two weeks.
Describe a time when you had to adapt quickly to changes in protocols or procedures.
How to Answer
- 1
Use the STAR method: Situation, Task, Action, Result
- 2
Choose a specific and relevant example
- 3
Highlight your ability to remain calm and focused
- 4
Emphasize how you effectively communicated changes
- 5
Mention any positive outcomes from the adaptation
Example Answers
In my previous role, we had a sudden change in sterilization protocols due to new regulations. I quickly reviewed the updated guidelines and organized a team meeting to ensure everyone was informed. We adapted our processes within a week, ensuring compliance and maintaining safety standards, which resulted in zero incidents during inspections.
Have you ever had to explain sterilization results to a non-technical audience? How did you approach that?
How to Answer
- 1
Use simple language and avoid jargon
- 2
Break down complex concepts into basic ideas
- 3
Use analogies or examples familiar to the audience
- 4
Be clear about the importance of sterilization
- 5
Encourage questions to ensure understanding
Example Answers
I once explained sterilization results to a group of nurses. I used simple terms and compared the process to cleaning dishes at home, emphasizing that just like we ensure dishes are clean to prevent illness, sterilization ensures we eliminate harmful microbes from instruments.
Situational Interview Questions
If a sterilization batch has failed, what immediate actions would you take to rectify the situation?
How to Answer
- 1
Assess and document the failure thoroughly to understand the root cause.
- 2
Communicate immediately with the team and relevant supervision about the failure.
- 3
Initiate a quarantine of the affected batch to prevent further use.
- 4
Review and recalibrate equipment as necessary to ensure proper function.
- 5
Determine the next steps for re-sterilization or disposal in compliance with protocols.
Example Answers
I would first assess the batch failure and document any anomalies. Next, I’d inform my supervisor and the team. I would quarantine the batch to prevent accidental use while we investigate the cause. Then, I would check the sterilization equipment for any issues that could have led to the failure.
If you notice an inconsistency in the sterilization log, how would you handle that situation?
How to Answer
- 1
Stay calm and assess the inconsistency objectively.
- 2
Check related documentation and logs for errors or explanations.
- 3
Report the inconsistency to your supervisor immediately.
- 4
Follow up with corrective actions if needed.
- 5
Document your findings and actions taken for future reference.
Example Answers
I would first review the sterilization log to confirm the inconsistency, then check related documents. Once verified, I would report it to my supervisor and follow the necessary procedures to correct the issue and document everything for accountability.
Don't Just Read Sterilizer Questions - Practice Answering Them!
Reading helps, but actual practice is what gets you hired. Our AI feedback system helps you improve your Sterilizer interview answers in real-time.
Personalized feedback
Unlimited practice
Used by hundreds of successful candidates
How would you prioritize your workload if multiple sterilization requests come in at the same time?
How to Answer
- 1
Assess the urgency of each request based on patient needs
- 2
Consider the type of items being sterilized and their impact on workflow
- 3
Communicate with your team about the workload and timeline
- 4
Use a triage system to categorize requests by priority
- 5
Document all requests to ensure none are overlooked
Example Answers
I would first assess the urgency of each request, focusing on items needed for surgeries or critical procedures. Then, I would communicate with my team to ensure we're aligned on priorities and quickly organize the workflow for efficiency.
How would you communicate a failure in equipment to your supervisor and the team?
How to Answer
- 1
Be clear and specific about the failure details
- 2
Notify immediately to ensure prompt action
- 3
Use a calm and professional tone
- 4
Provide any relevant data or documentation
- 5
Suggest potential next steps or solutions
Example Answers
I would immediately inform my supervisor about the equipment failure, clearly stating what the issue is and the impact it has on operations. I would provide any relevant data I have collected, and suggest we gather the team to discuss next steps for repairs or workarounds.
If there’s a disagreement between team members on sterilization protocols, how would you facilitate a resolution?
How to Answer
- 1
Listen to all perspectives of the team members involved.
- 2
Encourage a collaborative discussion to find common ground.
- 3
Refer to established protocols and guidelines for clarity.
- 4
Facilitate a decision-making process that involves everyone.
- 5
Summarize the agreed-upon resolution to ensure understanding.
Example Answers
I would first listen to each team member's concerns regarding the sterilization protocols. Then, I would lead a discussion where we could explore these concerns together and refer to our standard operating procedures to find a solution that aligns with best practices.
If you made a mistake in a sterilization protocol, how would you address it after the fact?
How to Answer
- 1
Acknowledge the mistake immediately without hesitation
- 2
Assess and document the impact of the mistake on patient safety and equipment
- 3
Communicate transparently with your supervisor and the team
- 4
Propose corrective actions to prevent future mistakes
- 5
Reflect on the situation and learn from it for professional growth
Example Answers
If I made a mistake in a sterilization protocol, I would first acknowledge the mistake and assess if any items were affected. Then, I would document everything and report to my supervisor immediately. I would suggest a review of the protocol with the team to understand what went wrong and implement measures to avoid it in the future.
If you had the opportunity to suggest improvements in the sterilization workflow, what would you propose?
How to Answer
- 1
Identify specific steps in the workflow that can be optimized.
- 2
Consider current compliance and safety standards.
- 3
Incorporate new technologies or methods that enhance efficiency.
- 4
Focus on training staff to reduce errors and improve consistency.
- 5
Suggest ways to monitor and evaluate the effectiveness of improvements.
Example Answers
I would suggest implementing a more automated tracking system for sterilized items to minimize human errors and improve accountability.
What would you do if you noticed that the sterilizer's temperature gauge was malfunctioning?
How to Answer
- 1
Immediately check the sterilizer's manual for troubleshooting steps.
- 2
Verify the temperature with a reliable external thermometer.
- 3
Report the malfunction to your supervisor and indicate urgency.
- 4
Document the incident in the maintenance log for future reference.
- 5
Avoid using the sterilizer until it is assessed and repaired.
Example Answers
If I noticed the temperature gauge was malfunctioning, I would first consult the sterilizer's manual for any troubleshooting information. Then, I would use an external thermometer to verify the temperature. After that, I would report the issue to my supervisor, emphasizing the need for immediate attention. I'd also document everything in the maintenance log and ensure the sterilizer was not used until it was fixed.
If you find discrepancies in the sterilization documentation, how would you resolve it?
How to Answer
- 1
Stay calm and assess the discrepancies logically
- 2
Verify documents against the relevant standard operating procedures
- 3
Consult with team members who may have insight on the discrepancy
- 4
Document your findings and actions taken for transparency
- 5
Report the issue to a supervisor if needed, following protocols
Example Answers
I would first verify the discrepancies against the operating procedures and confirm with my team to get their input. Then, I would document everything and escalate to my supervisor if necessary.
How would you analyze a sterilization cycle that repeatedly fails?
How to Answer
- 1
Review historical data for the sterilization cycles to identify patterns.
- 2
Check and calibrate the sterilizer equipment to ensure they are functioning correctly.
- 3
Inspect the sterilization protocol for compliance with recommended procedures.
- 4
Conduct a failure mode analysis to determine possible causes of failure.
- 5
Consult with team members and subject matter experts for additional insights.
Example Answers
I would start by reviewing the historical data to identify any trends or common failures. Next, I would ensure that all equipment is calibrated correctly and that we are following the established sterilization protocols. If issues persist, I would perform a failure mode analysis to pinpoint possible causes.
Don't Just Read Sterilizer Questions - Practice Answering Them!
Reading helps, but actual practice is what gets you hired. Our AI feedback system helps you improve your Sterilizer interview answers in real-time.
Personalized feedback
Unlimited practice
Used by hundreds of successful candidates
Sterilizer Position Details
Related Positions
- Garment Steamer
- Furniture Cleaner
- Meat Washer
- Pipe Cleaner
- Pillow Cleaner
- Brush Washer
- Washer
- Strainer
- Swabber
- Ventilator
Similar positions you might be interested in.
Ace Your Next Interview!
Practice with AI feedback & get hired faster
Personalized feedback
Used by hundreds of successful candidates
Ace Your Next Interview!
Practice with AI feedback & get hired faster
Personalized feedback
Used by hundreds of successful candidates