Top 28 Color Strainer Interview Questions and Answers [Updated 2025]
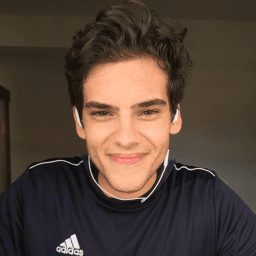
Andre Mendes
•
March 30, 2025
Preparing for a Color Strainer interview? You've come to the right place! This blog post compiles the most common interview questions for the Color Strainer role, complete with example answers and expert tips on how to respond effectively. Whether you're a seasoned professional or new to the field, this guide will help you navigate your interview with confidence and clarity. Dive in and get ready to impress!
Download Color Strainer Interview Questions in PDF
To make your preparation even more convenient, we've compiled all these top Color Strainerinterview questions and answers into a handy PDF.
Click the button below to download the PDF and have easy access to these essential questions anytime, anywhere:
List of Color Strainer Interview Questions
Technical Interview Questions
How do you choose the right materials for effective color straining?
How to Answer
- 1
Understand the type of colors you are working with.
- 2
Consider the viscosity and particle size of the materials.
- 3
Match the straining material with the intended color strength.
- 4
Test different materials to see which yields the best results.
- 5
Stay updated on new materials and technologies in color straining.
Example Answers
I choose materials based on the color type and desired intensity. For example, finer mesh nets work well for pigments with small particle sizes.
What types of color straining equipment are you familiar with, and how do you maintain them?
How to Answer
- 1
List specific types of color straining equipment you have used.
- 2
Explain the maintenance routine you follow for each type.
- 3
Include any relevant experience with troubleshooting equipment.
- 4
Mention any safety protocols you adhere to during maintenance.
- 5
Be prepared to discuss why maintenance is important for efficiency.
Example Answers
I am familiar with mesh strainers, basket strainers, and filter presses. For instance, I clean the mesh strainers after each use to prevent blockages and inspect basket strainers for wear. I also follow the manufacturer's instructions for any deep cleaning and servicing.
Don't Just Read Color Strainer Questions - Practice Answering Them!
Reading helps, but actual practice is what gets you hired. Our AI feedback system helps you improve your Color Strainer interview answers in real-time.
Personalized feedback
Unlimited practice
Used by hundreds of successful candidates
Can you explain the process of filtering or straining colors in a production environment?
How to Answer
- 1
Start by defining what color straining means in a production context
- 2
Outline the equipment typically used, such as filters and strainers
- 3
Describe the steps involved in the process, from material input to filtered output
- 4
Mention quality control measures to ensure the straining process is effective
- 5
Wrap up with the importance of this process in maintaining product quality and consistency
Example Answers
In a production environment, color straining involves using filters to remove impurities from pigments. First, the raw material is introduced into the filtering system, where it's passed through various mesh sizes to trap larger particles. After filtration, quality checks are done to ensure only clean colors are used in products. This step helps maintain consistency and quality in our final products.
What do you know about color theory, and how does it apply to your role as a color strainer?
How to Answer
- 1
Explain the basics of color theory, including primary, secondary, and tertiary colors.
- 2
Discuss complementary colors and their importance in color straining.
- 3
Connect color harmony to the products you'll be working with.
- 4
Mention any relevant color mixing techniques specific to your role.
- 5
Show enthusiasm for applying color theory to achieve desired results.
Example Answers
I understand that color theory includes primary, secondary, and tertiary colors, where combinations can create distinct shades. In my role as a color strainer, applying this knowledge helps me ensure the colors we use are vibrant and accurate by recognizing complementary pairs for balance.
What methods do you use to test the effectiveness of straining during the color preparation process?
How to Answer
- 1
Describe specific tests you implement to evaluate the strain quality
- 2
Mention any tools or equipment you use for testing
- 3
Highlight how you monitor consistency and color clarity post-straining
- 4
Talk about any adjustments you make based on test results
- 5
Give examples of problems you've solved with your testing methods
Example Answers
I use a simple filtration test to examine the clarity of the strained color. After straining, I check for any particles under a microscope and compare it to our quality standards.
Explain the safety procedures you follow when working with color straining materials.
How to Answer
- 1
Always wear appropriate personal protective equipment, such as gloves, goggles, and masks.
- 2
Ensure proper ventilation in the workspace to avoid inhaling fumes.
- 3
Store color straining materials in clearly labeled containers and follow MSDS instructions.
- 4
Be familiar with the emergency procedures for spills and exposure.
- 5
Regularly inspect all equipment for leaks or damage before use.
Example Answers
I always wear gloves and goggles while handling color straining materials to protect my skin and eyes. I also make sure my area is well-ventilated to prevent any harmful fumes from accumulating.
What software tools do you utilize in color straining, and what tasks do they assist you with?
How to Answer
- 1
Identify the specific tools you have experience with.
- 2
Explain the primary tasks each tool assists with.
- 3
Mention any relevant experience or projects using these tools.
- 4
Keep your answer focused on color straining-related tasks.
- 5
Be prepared to discuss why you prefer these tools.
Example Answers
I primarily use Adobe Photoshop for color straining. It helps me adjust the hue, saturation, and brightness of images to achieve the desired color balance. I also use Pantone Color Manager to ensure accurate color matching in printing.
What quality metrics do you consider essential when assessing whether a color strain is acceptable?
How to Answer
- 1
Identify specific color metrics like hue, saturation, brightness.
- 2
Discuss the importance of consistency across batches.
- 3
Mention the need for compliance with industry standards.
- 4
Highlight any visual assessment techniques you employ.
- 5
Talk about documenting metrics for quality control.
Example Answers
I consider hue accuracy, saturation levels, and brightness consistency as essential metrics. It's crucial that the color strainer produces consistent results across different batches to meet industry standards.
What troubleshooting steps would you take if the color strainer machine fails during production?
How to Answer
- 1
Check the machine's display for error codes or alerts
- 2
Inspect for any obvious signs of mechanical failure or jams
- 3
Review the operational logs for any recent anomalies
- 4
Ensure all connections and settings are correct and secure
- 5
Consult the maintenance manual for specific troubleshooting procedures
Example Answers
First, I would check the machine's display for any error codes that could indicate the problem. Then, I would inspect the area for mechanical issues or any jams that might be affecting operation. Finally, I'd review the operational logs for any mistakes leading up to the failure.
What improvements would you recommend for the color straining process based on your experience?
How to Answer
- 1
Analyze current workflow and identify bottlenecks in the straining process
- 2
Suggest enhancements in equipment or materials for better filtration
- 3
Recommend regular maintenance schedules to ensure optimal equipment performance
- 4
Propose staff training programs to improve skills in color straining
- 5
Consider implementing a feedback loop to continuously evaluate and improve the process
Example Answers
I think we could analyze our workflow for any bottlenecks, especially in the filtering stages. Upgrading to more efficient filters could significantly reduce strain time.
Don't Just Read Color Strainer Questions - Practice Answering Them!
Reading helps, but actual practice is what gets you hired. Our AI feedback system helps you improve your Color Strainer interview answers in real-time.
Personalized feedback
Unlimited practice
Used by hundreds of successful candidates
Behavioral Interview Questions
Can you describe a time when you had to work closely with a team to meet a deadline for a project involving color straining?
How to Answer
- 1
Identify a specific project with a tight deadline.
- 2
Highlight your role in collaboration with the team.
- 3
Discuss the techniques used for effective color straining.
- 4
Mention any challenges faced and how they were overcome.
- 5
Conclude with the successful outcome and what you learned.
Example Answers
In my previous job, we had a project where we needed to strain colors for a large batch of fabric. I worked closely with the dyeing team, ensuring we communicated clearly about the color specifications. We faced a challenge with one color not being vibrant enough, so I suggested adjusting the straining process. We successfully met the deadline and delivered high-quality fabric.
Tell me about a challenging issue you faced with color consistency and how you resolved it.
How to Answer
- 1
Identify a specific instance where color inconsistency was a problem.
- 2
Explain the steps you took to analyze the issue.
- 3
Describe the solution you implemented to achieve consistency.
- 4
Highlight the outcome and any improvements that resulted.
- 5
Reflect on what you learned from that experience.
Example Answers
In my previous job, we faced a challenge with our color matching during a production run. The colors in our prints were varying widely. I investigated and discovered that the ink supplier had changed their formulation. I collaborated with our production team to adjust the color mixing ratios and performed several test prints to ensure accuracy. This resolved the issue, and we were able to maintain consistent colors, which improved our customer satisfaction ratings.
Don't Just Read Color Strainer Questions - Practice Answering Them!
Reading helps, but actual practice is what gets you hired. Our AI feedback system helps you improve your Color Strainer interview answers in real-time.
Personalized feedback
Unlimited practice
Used by hundreds of successful candidates
Describe a situation where you had to explain a technical process to someone without a technical background. How did you ensure they understood?
How to Answer
- 1
Choose a specific technical process you explained.
- 2
Use simple language and avoid jargon.
- 3
Relate the technical process to everyday experiences.
- 4
Encourage questions to clarify understanding.
- 5
Verify comprehension by summarizing or asking for their perspective.
Example Answers
In my last job, I needed to explain the process of color mixing for paint to a sales representative. I used everyday examples like mixing primary colors to create new shades. I asked them questions to engage and clarify complex points, and checked their understanding by asking them to explain it back to me.
Give an example of a time you had to quickly adapt to a new tool or technique for color straining. What was the outcome?
How to Answer
- 1
Describe the specific tool or technique you had to learn.
- 2
Explain the reason for the change and the urgency involved.
- 3
Share the method you used to learn and adapt quickly.
- 4
Discuss the positive outcome and any measures taken to ensure success.
- 5
Conclude with what you learned from the experience.
Example Answers
In my previous position, we switched to a new automated color straining machine. The change was urgent due to increased production demands. I took the initiative to stay late and familiarize myself with the machine's manual and watched tutorial videos. As a result, I was able to operate the machine efficiently within a week, which led to a 15% increase in productivity and less wastage.
Can you provide an example of when you took initiative to improve the color straining process at your previous job?
How to Answer
- 1
Describe the problem you identified in the color straining process
- 2
Explain the initiative you took to address this issue
- 3
Share the specific actions you implemented
- 4
Discuss the outcome and improvements resulting from your initiative
- 5
Highlight any skills or teamwork involved in your approach
Example Answers
At my previous job, I noticed that our color straining process was taking too long, which delayed production. I proposed a new filtration system that I researched. I worked with our maintenance team to implement it and reduced the straining time by 30%. This improvement helped meet our production targets more consistently.
Describe a time when you received constructive criticism about your work in color straining. How did you handle it?
How to Answer
- 1
Select a specific instance that showcases your growth.
- 2
Explain the criticism clearly without getting defensive.
- 3
Describe the actions you took to improve based on the feedback.
- 4
Highlight the positive outcome that resulted from the change.
- 5
Convey your appreciation for feedback as part of professional development.
Example Answers
During a project, a supervisor noted that my color mixing process led to inconsistency. I listened carefully and decided to implement a more systematic approach to measuring colors. After applying this method, I noticed a significant improvement in the quality of our final products, which the team praised.
Discuss an experience when a project involving color straining did not go as planned. How did you recover?
How to Answer
- 1
Describe the project and its initial goals briefly
- 2
Explain the specific issue that caused the project to go off track
- 3
Detail the steps you took to address the problem
- 4
Highlight what you learned and how it improved future projects
- 5
Demonstrate your ability to remain calm and solution-focused under pressure
Example Answers
In a project to develop a new color palette for a client, we miscalculated the color ratios, resulting in an undesirable shade. Once I realized the mistake, I quickly gathered the team to brainstorm alternative mixtures. We tested several combinations and presented the best options to the client, who appreciated our quick recovery and final choices.
Can you give an example of when you had to manage multiple color straining projects simultaneously? How did you ensure each got the attention it needed?
How to Answer
- 1
Identify a specific time when you managed multiple projects.
- 2
Explain how you prioritized tasks based on deadlines and importance.
- 3
Describe the tools or methods you used for tracking progress.
- 4
Include how you communicated with team members or stakeholders.
- 5
Mention the outcome or success from managing these projects.
Example Answers
In my previous role, I managed three color straining projects at once. I created a priority list based on client deadlines, and I used project management software to track each project's progress. I held daily check-ins with my team to address challenges quickly. As a result, we completed all projects on time and maintained high quality.
Situational Interview Questions
If you notice a discrepancy in the color strain results, how would you approach investigating the issue?
How to Answer
- 1
Review the data thoroughly to confirm the discrepancy.
- 2
Check for any errors in the color strain setup or procedure.
- 3
Consult with team members to gather additional insights.
- 4
Run a controlled test to replicate the results.
- 5
Document findings and suggest potential corrections.
Example Answers
First, I would double-check the data for accuracy and confirm the discrepancy. Then, I would review the testing setup to make sure there were no mistakes in procedure. After that, I’d involve colleagues to see if they have noticed similar issues. If necessary, I would run a repeat test to verify the results.
Imagine you have to choose between two different straining techniques for a specific color. How would you make your decision?
How to Answer
- 1
Analyze the properties of the color being strained
- 2
Evaluate the advantages of each straining technique
- 3
Consider the impact on the final product
- 4
Take into account consistency and quality requirements
- 5
Assess the efficiency and time needed for each technique
Example Answers
I would first examine the characteristics of the color, such as viscosity. Then, I'd compare the benefits of each technique, focusing on which one maintains vibrancy. Finally, I’d choose the one that produces consistent results while minimizing time and waste.
Don't Just Read Color Strainer Questions - Practice Answering Them!
Reading helps, but actual practice is what gets you hired. Our AI feedback system helps you improve your Color Strainer interview answers in real-time.
Personalized feedback
Unlimited practice
Used by hundreds of successful candidates
You are tasked with straining colors for multiple projects with tight deadlines. How would you prioritize your tasks?
How to Answer
- 1
List all projects and their deadlines.
- 2
Assess the complexity and time requirement for each project.
- 3
Identify any dependencies between projects.
- 4
Communicate with team members for input on priorities.
- 5
Focus on high-impact projects first while managing deadlines.
Example Answers
I would start by listing all projects along with their deadlines. Then, I would evaluate which projects are more complex and require more time, prioritizing those with the tightest deadlines and highest impact.
If you are collaborating with another team that has different color standards, how would you approach harmonizing these differences?
How to Answer
- 1
Identify key stakeholders from both teams
- 2
Organize a meeting to discuss each team's standards
- 3
Use visual aids to compare color samples
- 4
Suggest a compromise or middle ground color palette
- 5
Document agreed standards for future reference
Example Answers
I would first bring together key stakeholders from both teams to understand their color standards in detail. I would then set up a meeting where we can visually compare our colors side by side and discuss which ones can be harmonized. After that, I would propose a compromise that represents both teams' preferences and document this agreement for the future.
What would you do if you identified that a batch of colors did not meet quality standards during the straining process?
How to Answer
- 1
Immediately stop the straining process to prevent further waste of materials.
- 2
Document the issue clearly, noting specifics of the batch and quality standards not met.
- 3
Investigate the cause of the quality issue to determine if it was procedural or equipment-related.
- 4
Communicate with the team and relevant supervisors about the quality issue promptly.
- 5
Propose corrective actions to prevent reoccurrence and ensure quality standards are upheld.
Example Answers
If I found that a batch did not meet quality standards during the straining process, I would first stop the process to avoid wasting more materials. I would then document the issue, including details about the batch and the specific standards that were not met. Next, I would investigate to understand why the quality was off, whether it was due to a process error or equipment malfunction. I would inform my team and supervisors immediately so we can address it. Finally, I would suggest corrective actions to ensure it doesn’t happen again.
How would you approach a situation where a client is not satisfied with the color outcomes? What steps would you take?
How to Answer
- 1
Listen actively to the client's concerns about the color outcomes
- 2
Ask specific questions to understand what they are dissatisfied with
- 3
Show empathy and assure them you will work on a solution
- 4
Propose corrective actions such as re-evaluating the color mix or offering a redo
- 5
Follow up with the client after making adjustments to ensure satisfaction
Example Answers
I would first listen to the client's feedback to clearly identify their concerns. Then, I would ask questions about what specifically they don't like, showing that I care. I would assure them that I will find a solution, such as adjusting the color mix. After making changes, I would follow up to make sure they are happy with the new results.
If you were tasked with training a new hire in color straining techniques, what key points would you emphasize?
How to Answer
- 1
Explain the importance of using the right mesh size for different materials.
- 2
Demonstrate the proper cleaning process to maintain equipment.
- 3
Highlight safety precautions when handling materials.
- 4
Show the correct technique for pouring and filtering to avoid clogs.
- 5
Discuss color matching and the adjustment of strainers for various applications.
Example Answers
I would emphasize the importance of using an appropriate mesh size for the material being strained, as this affects the quality of the final product. Next, I would demonstrate how to properly clean the equipment after each use to prevent contamination. Safety is crucial, so I would ensure they are aware of all necessary precautions.
If you were leading a team of color strainers, how would you encourage collaboration and communication?
How to Answer
- 1
Establish regular team meetings to discuss progress and challenges.
- 2
Use collaborative tools for sharing ideas and updates.
- 3
Encourage open feedback within the team to improve processes.
- 4
Create a team culture that values each member's input and creativity.
- 5
Recognize and celebrate team achievements to boost morale.
Example Answers
I would hold weekly meetings where everyone shares their thoughts on ongoing projects, ensuring everyone feels heard and involved.
You find that one of your primary straining materials is in short supply. How would you handle the situation?
How to Answer
- 1
Assess current inventory levels to confirm the shortage
- 2
Identify alternative materials that could be used temporarily
- 3
Communicate with suppliers about restocking timelines
- 4
Prioritize production processes that can use available materials
- 5
Develop a long-term strategy to diversify supply sources
Example Answers
First, I would check our current inventory to confirm that we indeed have a shortage. Then, I would look for alternative straining materials that can be used instead. I would contact suppliers to understand when we can expect a new shipment. In the interim, I would adjust our production schedule to focus on processes that don’t rely on the short supply. Finally, I would consider finding additional suppliers to avoid similar shortages in the future.
Color Strainer Position Details
Related Positions
Similar positions you might be interested in.
Ace Your Next Interview!
Practice with AI feedback & get hired faster
Personalized feedback
Used by hundreds of successful candidates
Ace Your Next Interview!
Practice with AI feedback & get hired faster
Personalized feedback
Used by hundreds of successful candidates