Top 31 Coater Interview Questions and Answers [Updated 2025]
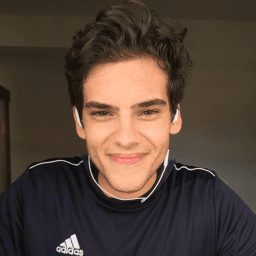
Andre Mendes
•
March 30, 2025
Preparing for a Coater interview can be daunting, but we've got you covered with this comprehensive guide to the most common interview questions for the role. In this post, you'll find example answers and expert tips on how to respond effectively, ensuring you're well-equipped to impress your future employer. Dive in and discover how to articulate your skills and experience with confidence and clarity.
Download Coater Interview Questions in PDF
To make your preparation even more convenient, we've compiled all these top Coaterinterview questions and answers into a handy PDF.
Click the button below to download the PDF and have easy access to these essential questions anytime, anywhere:
List of Coater Interview Questions
Situational Interview Questions
How would you prioritize tasks if you were faced with multiple coating deadlines?
How to Answer
- 1
Assess the urgency and importance of each deadline
- 2
Communicate with your team to understand dependencies
- 3
Break tasks into manageable steps and timelines
- 4
Use a task management tool to visualize deadlines
- 5
Be prepared to adapt as priorities may shift
Example Answers
I would first evaluate which tasks have the earliest deadlines and are critical for operations. Then, I'd communicate with my team to ensure we're aligned on priorities and dependencies. I would create a timeline to break down each task and manage my workload effectively.
If a coating batch fails quality control measures, what steps would you take to resolve the issue?
How to Answer
- 1
Identify the specific quality control measures that were failed
- 2
Review batch records and processes to find potential causes
- 3
Conduct a root cause analysis to determine the underlying issue
- 4
Implement corrective actions based on findings
- 5
Re-test the batch after adjustments to ensure compliance
Example Answers
First, I would identify which quality control measures were not met, then I'd review the batch record for any deviations. Next, I would perform a root cause analysis to find the issue, implement corrective actions, and finally re-test the batch to ensure quality standards are met.
Don't Just Read Coater Questions - Practice Answering Them!
Reading helps, but actual practice is what gets you hired. Our AI feedback system helps you improve your Coater interview answers in real-time.
Personalized feedback
Unlimited practice
Used by hundreds of successful candidates
If team members disagree on the best coating method, how would you facilitate a resolution?
How to Answer
- 1
Encourage open communication to express differing opinions.
- 2
Focus on data and past results to assess coating methods objectively.
- 3
Facilitate a discussion that allows each team member to present their case.
- 4
Seek a compromise that incorporates the best elements of each suggestion.
- 5
Document the decision-making process to avoid future conflicts.
Example Answers
I would start by creating an environment where everyone feels comfortable sharing their views. Then, I would ask each member to present their arguments, focusing on data and past experiences to guide the discussion. Finally, I'd aim to find a solution that combines the best aspects of their suggestions.
You notice a safety hazard in the coating area. What actions would you take to address it?
How to Answer
- 1
Immediately report the hazard to a supervisor or safety manager.
- 2
Assess the risk associated with the hazard to determine urgency.
- 3
Use appropriate personal protective equipment if necessary.
- 4
If safe, take temporary measures to mitigate the hazard.
- 5
Document the hazard and your actions taken for future reference.
Example Answers
I would report the hazard to my supervisor right away, as safety is a priority. I would also assess if there is an immediate risk to anyone in the area. If necessary, I would put on protective equipment and, if safe, take steps to secure the area until the issue is resolved.
A client is unhappy with the coating finish. How would you handle their complaint?
How to Answer
- 1
Acknowledge the client's feelings and thank them for their feedback.
- 2
Ask specific questions to understand the details of their concern.
- 3
Explain how you will address the issue, providing reassurance.
- 4
Offer to inspect the coating and propose a solution together.
- 5
Follow up to ensure that they are satisfied with the resolution.
Example Answers
I would start by acknowledging the client's dissatisfaction and thanking them for bringing it to my attention. I would then ask them specific questions about what aspects of the coating finish they are unhappy with, ensuring I understand their concerns fully. I would let them know I will personally inspect the coating and work on a solution to rectify the issue.
If you were low on a critical coating material, how would you handle production to meet timeline requirements?
How to Answer
- 1
Assess the current inventory and identify critical needs.
- 2
Communicate with suppliers to expedite material delivery.
- 3
Prioritize production schedules based on availability of materials.
- 4
Explore alternatives or substitutes for the coating material.
- 5
Collaborate with the team to adjust workflows and timelines.
Example Answers
First, I would check our inventory levels and confirm the exact shortage. Then, I would quickly reach out to our suppliers to request an expedited delivery of the material. While waiting for the shipment, I would adjust our production schedule to prioritize jobs that can be completed with available materials.
You are responsible for training new team members on coating procedures. What approach would you take?
How to Answer
- 1
Assess the skill level of new members before training
- 2
Break down coating procedures into clear, manageable steps
- 3
Use hands-on demonstrations to enhance learning
- 4
Encourage questions and interactive participation
- 5
Provide written materials as reference for after training
Example Answers
I would start by evaluating the new members' existing skills to tailor the training accordingly. Then, I would introduce the coating procedures in small, digestible steps, allowing them to observe a hands-on demonstration before they try it themselves. Throughout the training, I would encourage them to ask questions to ensure they fully grasp the processes.
What would you do if you encountered unexpected technical issues during a critical coating operation?
How to Answer
- 1
Assess the situation quickly to understand the problem
- 2
Communicate with your team and supervisor about the issue
- 3
Determine if a temporary workaround is possible to minimize delays
- 4
Refer to troubleshooting manuals or standard operating procedures
- 5
Document the issue and the steps taken to resolve it
Example Answers
I would first assess the situation to pinpoint the issue and then inform my team and supervisor. If possible, I'd implement a temporary workaround to keep operations moving while we solve the problem. I'd also refer to the troubleshooting manuals for guidance and ensure everything is documented for future reference.
How would you approach a situation where a colleague is not following proper coating protocols?
How to Answer
- 1
Assess the situation calmly before taking action
- 2
Gather specific examples of the protocol violations
- 3
Approach the colleague privately to discuss your concerns
- 4
Use 'I' statements to express how the behavior affects the team
- 5
Suggest solutions or offer help in understanding the protocols
Example Answers
I would first observe and note specific instances where the protocols were not followed. Then, I would approach my colleague privately and share my concerns using 'I' statements, such as 'I noticed some deviations from our coating protocols that could affect our results. Can we discuss it?'
How would you handle a situation where customer coating specifications change last minute?
How to Answer
- 1
Stay calm and assess the changes quickly
- 2
Communicate with the customer to clarify their new needs
- 3
Evaluate the impact on production time and resources
- 4
Propose feasible solutions or alternatives to meet the new specs
- 5
Ensure all team members understand the changes before proceeding
Example Answers
I would first take a deep breath and analyze the changes. Then, I'd reach out to the customer immediately to confirm their new specifications. After that, I'd assess my team’s workload and determine how we can adjust our process to meet their needs, possibly offering alternatives if time is tight.
Don't Just Read Coater Questions - Practice Answering Them!
Reading helps, but actual practice is what gets you hired. Our AI feedback system helps you improve your Coater interview answers in real-time.
Personalized feedback
Unlimited practice
Used by hundreds of successful candidates
Behavioral Interview Questions
Can you describe a time when you worked on a team to complete a coating project? What was your role?
How to Answer
- 1
Select a specific project where teamwork was crucial
- 2
Clearly define your role in the team and contributions
- 3
Mention any challenges faced and how the team overcame them
- 4
Highlight the outcome of the project and the impact of your role
- 5
Use the STAR method: Situation, Task, Action, Result
Example Answers
In my previous role, we had a project to coat metal parts for a large client. I was the team lead responsible for coordinating tasks. We faced timeline challenges, but through effective scheduling and communication, we finished ahead of time, leading to a successful delivery and happy client.
Tell me about a challenging issue you faced during a coating process. How did you handle it?
How to Answer
- 1
Identify a specific challenge related to the coating process.
- 2
Describe the steps you took to analyze the issue.
- 3
Explain the solution you implemented and why it was effective.
- 4
Mention any outcomes or lessons learned.
- 5
Keep the answer concise and focused on your role.
Example Answers
During a production run, we noticed that the coating was not adhering properly. I quickly analyzed the temperature and humidity levels, which were out of specification. I adjusted the environmental controls and re-ran the coating. This improved adhesion significantly, and we met our quality standards.
Don't Just Read Coater Questions - Practice Answering Them!
Reading helps, but actual practice is what gets you hired. Our AI feedback system helps you improve your Coater interview answers in real-time.
Personalized feedback
Unlimited practice
Used by hundreds of successful candidates
Have you ever led a coating project? Describe your approach to managing the team and resources.
How to Answer
- 1
Start with a brief overview of the project goal.
- 2
Highlight your leadership style and how you communicated with the team.
- 3
Discuss how you allocated resources effectively.
- 4
Mention any challenges you faced and how you addressed them.
- 5
Conclude with the project's outcome and what you learned.
Example Answers
In my previous role, I led a coating project aimed at improving the durability of our products. I adopted a collaborative leadership style, holding regular meetings to ensure everyone was on the same page. I allocated tasks based on each team member's strengths, and when we encountered a supply chain issue, I quickly identified an alternate supplier to keep us on schedule. The project was completed on time and resulted in a 20% increase in product lifespan.
Describe a situation where your attention to detail made a significant difference in your work.
How to Answer
- 1
Think of a specific project where your detailed work impacted the outcome.
- 2
Focus on the task you were doing and why detail was crucial.
- 3
Explain how your attention to detail helped prevent errors or achieved a better result.
- 4
Use the STAR method: Situation, Task, Action, Result to structure your answer.
- 5
Be concise and clear about the impact of your detail-oriented approach.
Example Answers
In a previous role, I was responsible for coating quality checks. During one project, I noticed a slight variation in the coating thickness specified by the client. I double-checked the settings and made adjustments, which resulted in a perfect match to the specifications and ultimately led to a successful delivery without reworks.
Tell me about a time when you had to adapt to new technology or methods while coating. How did you manage?
How to Answer
- 1
Identify a specific technology or method you adapted to.
- 2
Explain the challenges you faced with the new technology.
- 3
Describe the steps you took to learn and implement the changes.
- 4
Highlight any positive outcomes from your adaptability.
- 5
Reflect on what you learned from the experience.
Example Answers
In my previous role, we upgraded to a new automated coating machine. I found it challenging at first to understand the software settings but took the initiative to attend a training session offered by the supplier. I practiced with a mentor and within a week I was proficient, resulting in a 20% increase in production speed.
Describe a situation where effective communication led to a successful coating project outcome.
How to Answer
- 1
Identify a specific project where communication was key
- 2
Explain the roles of team members involved
- 3
Describe the communication methods used (meetings, emails)
- 4
Highlight the positive outcome resulting from effective communication
- 5
Keep it concise and focused on results.
Example Answers
In a recent project, our team faced a challenge with a new coating application. We scheduled daily stand-up meetings to discuss progress and address issues. By keeping everyone informed, we were able to quickly adjust our process and meet our deadline successfully.
Can you give an example of when you took the initiative to improve a coating process?
How to Answer
- 1
Start with a brief description of the coating process you improved
- 2
Explain the issue or inefficiency you identified
- 3
Describe the specific action you took to address it
- 4
Highlight the positive outcome or results of your initiative
- 5
Keep the example relevant to the role of a Coater
Example Answers
In my previous job, I noticed that our curing time for coatings was too long, which delayed production. I researched faster curing agents and proposed a new formulation. After testing, we implemented the change and reduced our curing time by 20%, boosting our productivity.
Describe a time when you received critical feedback on your coating work. How did you respond?
How to Answer
- 1
Choose a specific example that highlights your work and feedback.
- 2
Explain the feedback clearly and how you processed it.
- 3
Describe the steps you took to address the feedback.
- 4
Share any positive outcomes or lessons learned from the situation.
- 5
Emphasize your willingness to improve and adapt.
Example Answers
In my previous job, I received feedback that my spray technique resulted in uneven coating. I took it seriously, practiced my technique with a mentor, and adjusted my approach. The next batch turned out much smoother, and I received positive comments from my supervisor.
What is the most valuable lesson you've learned in your experience as a coater?
How to Answer
- 1
Reflect on a specific challenge you faced that taught you something important.
- 2
Think about the importance of attention to detail and consistency in the coating process.
- 3
Consider how teamwork and communication contribute to successful coating operations.
- 4
Identify a lesson that aligns with the company's values or goals, if possible.
- 5
Be concise and share personal insights or anecdotes to make your answer memorable.
Example Answers
One of the most valuable lessons I've learned is the importance of precision. Early in my career, I had a batch that didn't meet quality standards due to a minor measurement error. It taught me to double-check everything before proceeding.
Don't Just Read Coater Questions - Practice Answering Them!
Reading helps, but actual practice is what gets you hired. Our AI feedback system helps you improve your Coater interview answers in real-time.
Personalized feedback
Unlimited practice
Used by hundreds of successful candidates
Technical Interview Questions
What types of coating processes are you familiar with, and which do you prefer to work with?
How to Answer
- 1
List specific coating processes you know, such as spray coating or powder coating.
- 2
Briefly explain your experience with each mentioned process.
- 3
Reflect on why you prefer one process over the others.
- 4
Mention any relevant projects where you applied these coating methods.
- 5
Be honest and concise, focusing on your strengths and interests.
Example Answers
I am familiar with spray coating, powder coating, and electrostatic coating. I prefer powder coating because it provides a durable finish and my experience with it includes several automotive parts projects.
Can you explain the differences between various coating materials and their applications?
How to Answer
- 1
Identify common types of coating materials like paints, varnishes, and powder coatings.
- 2
Discuss their properties, such as durability, appearance, and resistance to elements.
- 3
Mention specific applications for each type, like industrial, automotive, or decorative uses.
- 4
Highlight any environmental factors affecting coating choice, like VOC emissions.
- 5
Use clear examples to illustrate differences and applications effectively.
Example Answers
There are several types of coating materials, such as acrylic paints which are water-based and used for interior surfaces due to their low odor and quick drying time. Enamel paints, being more durable, are often used for outdoor furniture because they provide a tough finish. Lastly, powder coatings are popular in manufacturing for metal surfaces due to their excellent durability and resistance to corrosion.
Don't Just Read Coater Questions - Practice Answering Them!
Reading helps, but actual practice is what gets you hired. Our AI feedback system helps you improve your Coater interview answers in real-time.
Personalized feedback
Unlimited practice
Used by hundreds of successful candidates
What coating equipment are you experienced with, and how do you ensure it is maintained properly?
How to Answer
- 1
List specific coating equipment you have worked with
- 2
Mention your experience level with each type of equipment
- 3
Discuss maintenance routines or checks you perform
- 4
Explain how you document maintenance activities
- 5
Share an example of resolving an equipment issue
Example Answers
I have experience with spray coating equipment, specifically the Wagner Pro X series. To maintain it, I perform daily checks on the fluid delivery and clean the nozzles to prevent clogs. Additionally, I keep a maintenance log to track any repairs or part replacements.
What industry standards do you follow for quality assurance in the coating process?
How to Answer
- 1
Identify relevant industry standards such as ISO, ASTM, or NACE.
- 2
Discuss specific testing methods like adhesion tests or thickness measurements.
- 3
Mention any certifications you hold or relevant training.
- 4
Explain how you integrate quality checks into the coating process.
- 5
Highlight the importance of documentation and traceability.
Example Answers
I follow ISO 9001 standards and ASTM testing methods, specifically adhesion tests and thickness measurements, to ensure quality in the coating process.
How do you measure the thickness and consistency of a coating? What tools do you use?
How to Answer
- 1
Start by mentioning the specific tools you use like a wet film gauge or a dry film thickness meter.
- 2
Explain the process of measuring, including how often you take measurements during application.
- 3
Describe why consistency is important and how to ensure it, such as using multiple measurements and averaging them.
- 4
Mention any standards or specifications you follow for coating thickness.
- 5
Discuss any corrective actions you take if the measurements are outside acceptable limits.
Example Answers
I use a digital dry film thickness gauge to measure the thickness of the coating after it dries. I take readings at multiple points on the surface to ensure consistency and average the results. I ensure the thickness meets industry standards for optimal performance.
What steps do you take when troubleshooting a coating defect?
How to Answer
- 1
Identify the type and cause of the defect by inspecting the coated surface.
- 2
Use process control data to correlate defect occurrence with manufacturing parameters.
- 3
Test potential solutions by adjusting parameters such as temperature, pressure, or coating composition.
- 4
Conduct small-scale trials to validate the effectiveness of the changes before full implementation.
- 5
Document findings and steps taken for future reference and training purposes.
Example Answers
First, I inspect the coating to determine the specific defect and its probable cause. Then, I review our process data to see if any parameters changed around the time the defect started appearing. After identifying possible adjustments, I run tests to see if altering those parameters resolves the issue.
How do you ensure compliance with environmental regulations in the coating process?
How to Answer
- 1
Familiarize yourself with relevant environmental regulations.
- 2
Implement proper waste disposal methods for coating materials.
- 3
Use low-VOC or eco-friendly coatings whenever possible.
- 4
Conduct regular maintenance and inspections of coating equipment.
- 5
Provide training for staff on compliance and best practices.
Example Answers
I ensure compliance by staying updated on environmental regulations and using low-VOC materials in the coating process. I also oversee proper waste disposal and conduct regular equipment inspections.
What process optimization techniques have you applied in your coating work?
How to Answer
- 1
Identify specific techniques you have used in your previous role.
- 2
Mention any tools or software that aided your optimization process.
- 3
Include measurable outcomes or results from your optimizations.
- 4
Discuss how you collaborated with team members or other departments.
- 5
Be prepared to explain the impact on efficiency, quality, or cost.
Example Answers
In my last role, I implemented a new spray pattern technique that reduced material waste by 15%. I used software to simulate coating processes before physical application, which helped identify optimal settings for each batch.
What considerations do you take into account when designing a coating for a specific application?
How to Answer
- 1
Identify the application environment and performance requirements
- 2
Consider substrate material and compatibility with the coating
- 3
Account for longevity and durability demands in the design
- 4
Evaluate the coating process and equipment capabilities
- 5
Think about cost-effectiveness and scalability of production
Example Answers
When designing a coating, I first assess the application environment, like exposure to chemicals or temperature extremes. Then, I choose materials that are compatible with the substrate and meet the required durability for the application.
How do you validate a new coating process or material before full-scale production?
How to Answer
- 1
Begin with small-scale testing to gauge the initial performance of the coating.
- 2
Evaluate adhesion, durability, and resistance through controlled experiments.
- 3
Conduct accelerated aging tests to predict long-term performance.
- 4
Gather data and feedback from quality control to refine the process.
- 5
Document all results and adjustments for traceability and future reference.
Example Answers
I start by running small-scale tests of the coating to evaluate its adhesion and durability. Then I conduct tests to assess how it performs under accelerated aging conditions. This gives insight into its long-term viability. I make adjustments based on quality control feedback and carefully document the entire process for future reference.
Don't Just Read Coater Questions - Practice Answering Them!
Reading helps, but actual practice is what gets you hired. Our AI feedback system helps you improve your Coater interview answers in real-time.
Personalized feedback
Unlimited practice
Used by hundreds of successful candidates
What finishing techniques are you familiar with, and how do they impact the final product?
How to Answer
- 1
List specific finishing techniques you have experience with
- 2
Explain the purpose of each technique in the context of coating
- 3
Discuss how each technique affects the appearance and durability of the product
- 4
Relate any relevant personal experience or outcomes from using these techniques
- 5
Be concise and avoid jargon unless it’s industry standard
Example Answers
I am familiar with techniques such as electrostatic coating, powder coating, and clear coating. Electrostatic coating improves adhesion and even coverage, while powder coating results in a durable finish that resists chipping. Clear coating enhances both the aesthetics and protection of the underlying coating.
Coater Position Details
Related Positions
- Stainer
- Coil Binder
- Filler Spreader
- Coil Wrapper
- Adhesive Primer
- Mold Sprayer
- Wire Roller
- Cross Roller
- Edge Roller
- Color Strainer
Similar positions you might be interested in.
Ace Your Next Interview!
Practice with AI feedback & get hired faster
Personalized feedback
Used by hundreds of successful candidates
Ace Your Next Interview!
Practice with AI feedback & get hired faster
Personalized feedback
Used by hundreds of successful candidates