Top 31 Filler Spreader Interview Questions and Answers [Updated 2025]
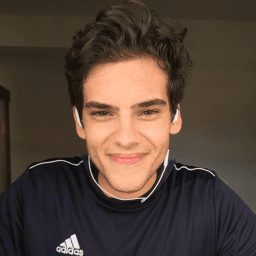
Andre Mendes
•
March 30, 2025
Preparing for a Filler Spreader interview? You're in the right place! This blog post compiles the most common interview questions for this specialized role, complete with example answers and insightful tips to help you respond effectively. Whether you're new to the field or seeking a refresher, our guide offers valuable advice to boost your confidence and help you ace your interview.
Download Filler Spreader Interview Questions in PDF
To make your preparation even more convenient, we've compiled all these top Filler Spreaderinterview questions and answers into a handy PDF.
Click the button below to download the PDF and have easy access to these essential questions anytime, anywhere:
List of Filler Spreader Interview Questions
Behavioral Interview Questions
Can you describe a time when you had to work closely with a team to complete a project successfully?
How to Answer
- 1
Choose a specific project that had clear objectives.
- 2
Explain your role and how you collaborated with team members.
- 3
Highlight any challenges faced and how they were overcome together.
- 4
Emphasize the outcomes and what you learned from the experience.
- 5
Keep it concise and relevant to teamwork and collaboration.
Example Answers
In my last job, we had to launch a new product within a tight deadline. I coordinated with the marketing and production teams to ensure alignment. We faced a major setback with supplier delays, but we held daily stand-up meetings to address issues promptly. As a result, we launched on time and my teamwork skills improved significantly.
Tell me about a time when you encountered a conflict with a coworker. How did you handle it?
How to Answer
- 1
Be specific about the conflict and the coworkers involved
- 2
Focus on your actions and the resolution process
- 3
Emphasize communication and understanding
- 4
Highlight the positive outcome or lesson learned
- 5
Keep it professional and avoid speaking negatively about the coworker
Example Answers
In a previous job, I disagreed with a coworker about the best approach to a project. I invited them to discuss our viewpoints over lunch. We shared our ideas openly, and by the end, we combined our approaches, which led to a successful project outcome.
Don't Just Read Filler Spreader Questions - Practice Answering Them!
Reading helps, but actual practice is what gets you hired. Our AI feedback system helps you improve your Filler Spreader interview answers in real-time.
Personalized feedback
Unlimited practice
Used by hundreds of successful candidates
Discuss a challenging situation where you had to think quickly. What was the outcome?
How to Answer
- 1
Identify a specific situation you faced in a previous role.
- 2
Clearly describe the challenge and the constraints you were under.
- 3
Explain the quick decision you made and your thought process.
- 4
Highlight the positive outcome and what you learned from it.
- 5
Keep it concise and relevant to the Filler Spreader position.
Example Answers
During a busy shift, I noticed that the filler machine was malfunctioning and backups were forming. I quickly assessed the situation, recalibrated the machine settings, and informed my team to handle the overflow. As a result, we minimized downtime and met our production targets.
Describe an instance where your attention to detail made a significant impact on the quality of work.
How to Answer
- 1
Choose a specific example from your experience as a filler spreader or in a related role
- 2
Emphasize the problem you identified due to attention to detail
- 3
Explain the actions you took and the meticulous steps you employed
- 4
Highlight the positive outcome that resulted from your attention to detail
- 5
Keep it concise and relevant to the position you are applying for
Example Answers
In my previous role, I noticed that the filler consistency was slightly off during a batch. I reviewed the mixing process and discovered that the measurements were not precise. I corrected the amount of filler being used, which improved the batch quality and reduced waste significantly.
Can you provide an example of a time when you had to adapt to a significant change at work?
How to Answer
- 1
Think of a specific change you experienced at work
- 2
Describe your initial reaction to the change
- 3
Explain the steps you took to adapt
- 4
Highlight the outcome of your adaptation
- 5
Focus on skills gained or lessons learned
Example Answers
In my previous role, our team was moved to a new project management software. Initially, I found it challenging to learn the new system. I dedicated extra hours each day to practice and attended training sessions. This allowed me to not only adapt quickly but also help my colleagues, leading to a smooth transition for the whole team.
Give me an example of how you prioritize safety in your work environment.
How to Answer
- 1
Discuss specific safety protocols you follow.
- 2
Mention any safety training you have undertaken.
- 3
Provide an example of a safety issue you identified and resolved.
- 4
Highlight how you communicate safety practices to your team.
- 5
Explain how you stay updated on safety regulations.
Example Answers
In my previous role, I always conducted a safety checklist before starting work. I attended safety training every year and implemented a buddy system to ensure we look out for each other.
What motivates you to perform well in your job as a filler spreader?
How to Answer
- 1
Identify specific aspects of the job that you enjoy, like working with your hands or seeing a tangible product.
- 2
Mention the importance of quality in your work and how that drives you.
- 3
Discuss goals and achievements that inspire you to do your best.
- 4
Relate personal pride in contributing to team success or the company’s goals.
- 5
Highlight the satisfaction of learning and improving your skills in the role.
Example Answers
I am motivated by the satisfaction of knowing that my work directly contributes to the quality of the final product. Seeing the smooth operation of the fillers and how they impact production inspires me to perform at my best.
Describe a situation where you took the initiative to improve a process at work.
How to Answer
- 1
Choose a specific example from your work history.
- 2
Clearly state the problem you identified.
- 3
Explain the steps you took to improve the process.
- 4
Highlight the positive outcome and any measurable results.
- 5
Keep it concise and focused on your initiative.
Example Answers
In my last job as a warehouse assistant, I noticed that the inventory management system was causing delays in order fulfillment. I proposed a new labeling system that improved tracking and implemented it with my team. As a result, our order processing time was reduced by 20%.
What specific experiences do you believe have best prepared you for the role of a filler spreader?
How to Answer
- 1
Identify relevant past roles where you operated machinery or worked in manufacturing.
- 2
Highlight experiences that involved attention to detail and quality control.
- 3
Mention any specific training or certifications related to equipment operation.
- 4
Share examples of teamwork and communication in fast-paced environments.
- 5
Quantify your experiences with metrics where possible, such as production rates if applicable.
Example Answers
In my previous role as a machine operator, I operated various filling machines for over three years, ensuring quality control and reducing waste by 15%.
Don't Just Read Filler Spreader Questions - Practice Answering Them!
Reading helps, but actual practice is what gets you hired. Our AI feedback system helps you improve your Filler Spreader interview answers in real-time.
Personalized feedback
Unlimited practice
Used by hundreds of successful candidates
Technical Interview Questions
What methods do you use to ensure even application of fillers during the spreading process?
How to Answer
- 1
Use consistent speed and pressure during spreading
- 2
Start from the edges and work towards the center
- 3
Regularly check the thickness as you spread
- 4
Use appropriate tools for the type of filler
- 5
Practice on a sample surface to adjust technique
Example Answers
I ensure even application by maintaining a consistent speed and pressure as I spread the filler. I start from the edges and work my way to the center, checking for any uneven spots.
What experience do you have with using filling machines or spreaders?
How to Answer
- 1
Start with your most relevant experience with filling machines.
- 2
Mention specific types of machines you have operated or worked with.
- 3
Include any training or certifications related to filling equipment.
- 4
Discuss the scale of projects you’ve worked on, like large production runs.
- 5
Highlight any troubleshooting or maintenance tasks you’ve performed.
Example Answers
I have 3 years of experience operating automatic filling machines in a food packaging company, where I handled liquid and powder fillers. I am also trained in basic maintenance, which helped minimize downtime.
Don't Just Read Filler Spreader Questions - Practice Answering Them!
Reading helps, but actual practice is what gets you hired. Our AI feedback system helps you improve your Filler Spreader interview answers in real-time.
Personalized feedback
Unlimited practice
Used by hundreds of successful candidates
What quality control checks do you perform when spreading fillers?
How to Answer
- 1
Ensure consistency in filler application by using calibrated equipment
- 2
Regularly inspect the filler for texture and compatibility with the substrate
- 3
Monitor environmental conditions such as temperature and humidity during application
- 4
Perform a visual check after application to identify any unevenness or defects
- 5
Document and report any discrepancies to maintain quality standards
Example Answers
I always use calibrated spreaders to ensure even application, and I visually check the filler for consistency before and after spreading. I also take note of the weather conditions, as they can affect the results.
Can you explain the standard operation procedures for filler spreading?
How to Answer
- 1
Start with the preparation of the filler material and machinery.
- 2
Explain the steps to set the desired spreading width and thickness.
- 3
Include safety checks and equipment maintenance protocols.
- 4
Describe the monitoring process during spreading operations.
- 5
Finish with the post-operation cleanup and equipment handling.
Example Answers
First, I prepare the filler material by ensuring it meets the required specifications and check the spreading equipment for proper functionality. Next, I set the spreader to achieve the desired width and thickness of the filler. I always conduct safety checks before starting, ensuring all guards are in place. During operation, I monitor the material flow and adjust settings as needed. After completing the job, I clean the equipment and storage area to maintain efficiency.
What types of fillers have you worked with, and what are their properties?
How to Answer
- 1
List specific fillers you have experience with.
- 2
Describe key properties of each filler briefly.
- 3
Mention any relevant applications or industries.
- 4
Highlight your familiarity with handling and processing these fillers.
- 5
Connect your experience to the requirements of the job.
Example Answers
I have worked with silica gel and calcium carbonate. Silica gel is porous and used for moisture control, while calcium carbonate is a common filler in plastics for added stiffness. I used them in the packaging industry to enhance product durability.
How would you troubleshoot a malfunction in a filler spreading machine?
How to Answer
- 1
Inspect the machine for obvious mechanical issues like loose parts or blockages
- 2
Check electrical connections and settings to ensure they are correct
- 3
Run diagnostic tests if available to identify error codes or faults
- 4
Consult the machine's manual for troubleshooting steps specific to the issue
- 5
Document findings and adjustments made for future reference
Example Answers
First, I would inspect the machine closely for any loose parts or material blockages that might cause the malfunction. If everything looks fine, I would then check the control panel for any error messages before running a diagnostic test.
How do you perform routine maintenance on the spreading equipment?
How to Answer
- 1
Inspect the equipment daily for any visible wear or damage.
- 2
Lubricate moving parts according to the manufacturer's specifications.
- 3
Clean the spreading mechanism and remove any material build-up.
- 4
Check and adjust calibration settings for accurate spreading.
- 5
Schedule periodic deep maintenance checks based on usage frequency.
Example Answers
I perform daily inspections to check for wear, lubricate moving parts, and ensure everything is clean. I also make sure the calibration is accurate before every major use.
How do you determine if a filling material is adequate for a specific application?
How to Answer
- 1
Identify the application requirements such as strength, durability, and thermal stability
- 2
Check the material's properties like viscosity, curing time, and compatibility
- 3
Consider regulatory standards and safety data for the material
- 4
Review past usage data or case studies for similar applications
- 5
Test the material in a controlled environment before full-scale application
Example Answers
To determine if a filling material is adequate, I first assess the application requirements, like the need for strength and thermal stability. Then I check the material specifications for viscosity and curing time, ensuring it aligns with the project’s needs. Finally, I look for similar case studies to confirm its past performance.
How do environmental conditions affect your work as a filler spreader?
How to Answer
- 1
Discuss specific environmental factors like temperature and humidity.
- 2
Explain how these factors influence material application and spreader performance.
- 3
Mention the importance of adjusting techniques based on conditions.
- 4
Highlight awareness of safety concerns related to weather.
- 5
Provide examples of how you’ve adapted to conditions in past work.
Example Answers
Environmental conditions like humidity can affect the viscosity of the filler material, making it either too runny or too thick. I always check the weather before starting and adjust my spreader settings accordingly to ensure an even application.
What specific safety checks do you perform before starting work with filler materials?
How to Answer
- 1
Review Material Safety Data Sheets for each filler material
- 2
Inspect personal protective equipment to ensure it is in good condition
- 3
Check the work area for hazards such as spills or blocked exits
- 4
Ensure all machinery is operational and equipped with the necessary safety features
- 5
Confirm ventilation is adequate for handling fumes and dust
Example Answers
Before starting, I always check the Material Safety Data Sheets for the fillers to identify any hazards. I also inspect my PPE to make sure it’s in good shape. Lastly, I look around the work area for any obstructions or spills to ensure a safe environment.
Don't Just Read Filler Spreader Questions - Practice Answering Them!
Reading helps, but actual practice is what gets you hired. Our AI feedback system helps you improve your Filler Spreader interview answers in real-time.
Personalized feedback
Unlimited practice
Used by hundreds of successful candidates
What testing techniques do you utilize to ensure filler application quality?
How to Answer
- 1
Describe specific techniques you use for quality control
- 2
Mention tools or equipment you rely on for testing
- 3
Explain how you gather and analyze data from tests
- 4
Talk about collaboration with team members for quality assurance
- 5
Share a relevant example from your past experience
Example Answers
I regularly use visual inspections and consistency tests to assess filler application quality, along with data logging for moisture content and thickness measurements. This helps ensure we meet the project specifications.
Situational Interview Questions
If you were in the middle of a filler spreading job and realized you were running out of material, what would you do?
How to Answer
- 1
Assess the remaining filler material quickly.
- 2
Check the specific area you are covering.
- 3
Communicate with your supervisor or team about the shortage.
- 4
Plan for either replenishing the material or adjusting the spread.
- 5
Prioritize completing the task safely and efficiently.
Example Answers
I would quickly assess how much filler is left and determine if I can complete the current section. If I'm running low, I'd inform my supervisor immediately so they can arrange for more material.
Imagine you have two projects to complete by the end of the day but only enough time for one. How would you decide which to prioritize?
How to Answer
- 1
Evaluate the deadlines of both projects to see which is more urgent
- 2
Consider the impact of each project on the team or business
- 3
Assess how much progress you've already made on each project
- 4
Think about who is relying on the completion of each project
- 5
Communicate with stakeholders to gather input on priorities
Example Answers
I would evaluate both projects based on their deadlines and urgency. If one project has a stricter deadline, I would prioritize that one. I would also consider who is depending on each project and communicate with my team to ensure alignment.
Don't Just Read Filler Spreader Questions - Practice Answering Them!
Reading helps, but actual practice is what gets you hired. Our AI feedback system helps you improve your Filler Spreader interview answers in real-time.
Personalized feedback
Unlimited practice
Used by hundreds of successful candidates
If you notice a team member struggling with their job, how would you handle the situation?
How to Answer
- 1
Observe the team member's specific struggles without interrupting their work.
- 2
Approach them privately to offer help and ask if they need support.
- 3
Listen to their concerns and provide constructive feedback or guidance.
- 4
Suggest resources or training that could assist them in their role.
- 5
Follow up to see how they are progressing after offering your support.
Example Answers
I would first notice what specific areas they are struggling with, then I would approach them privately and ask if they would like some support. Listening to their concerns allows me to offer specific guidance or resources that might help them.
What steps would you take if you noticed a safety hazard in the work area?
How to Answer
- 1
Immediately assess the hazard and determine its severity.
- 2
Inform your supervisor or appropriate personnel about the hazard.
- 3
If safe to do so, take action to mitigate the hazard or isolate the area.
- 4
Document the hazard and any steps taken to resolve it.
- 5
Follow up to ensure that corrective measures are implemented.
Example Answers
If I noticed a safety hazard, I would first assess how serious it is. Then, I would report it to my supervisor as soon as possible. If it's safe, I would try to block off the area to keep others away until it’s fixed.
You are nearing the deadline for a filler project but are behind schedule. What actions would you take to ensure completion?
How to Answer
- 1
Assess the current status of the project and identify the key tasks that are pending.
- 2
Prioritize tasks based on their impact on project completion.
- 3
Communicate with the team to delegate tasks and ensure everyone is aligned.
- 4
Consider extending work hours or bringing in additional resources if necessary.
- 5
Regularly check progress and adjust the plan as needed to stay on track.
Example Answers
First, I would assess which tasks are most critical and prioritize them. Then, I would hold a quick meeting with the team to delegate those tasks efficiently. Finally, I would check in regularly to monitor our progress and make adjustments if necessary.
If you accidentally overshot a filler area, what corrective measures would you implement?
How to Answer
- 1
Assess the extent of the overshoot immediately to understand the impact.
- 2
Stop the filling process to prevent further excess material from being added.
- 3
Use appropriate tools to remove or redistribute the excess material.
- 4
Communicate with the team about the issue to ensure everyone is informed.
- 5
Document the incident to analyze the cause and prevent future occurrences.
Example Answers
If I overshot a filler area, I would first stop the filling process and assess how much overshot occurred. Then, I would use the necessary tools to remove the excess material and carefully redistribute it if possible. I would also inform my team about the incident to ensure everyone understands the situation and learn from it.
How would you handle a situation where a team member challenges your technique while spreading filler?
How to Answer
- 1
Stay calm and listen to their concerns without interrupting.
- 2
Ask for specific examples of the issues they see with your technique.
- 3
Share your reasoning behind your technique and any successful outcomes.
- 4
Suggest a collaborative approach to test both techniques for best results.
- 5
Remain open-minded and willing to adapt based on new findings.
Example Answers
I would first listen carefully to their concerns and ask for specific examples. Then, I would explain why I use my technique and how it has worked in the past. I would suggest we try a small test to compare both methods and see which one yields the best results.
How would you encourage and uplift team morale during a tough project?
How to Answer
- 1
Recognize individual and team achievements regularly.
- 2
Encourage open communication to share concerns and ideas.
- 3
Organize team-building activities or breaks to relieve stress.
- 4
Provide positive feedback and support during challenges.
- 5
Set small, attainable goals to create a sense of progress.
Example Answers
I would hold weekly check-ins to recognize both individual and team successes, even small ones, to keep spirits high.
How do you handle pressure when working to meet tight deadlines?
How to Answer
- 1
Prioritize tasks by urgency and importance
- 2
Break down projects into smaller, manageable steps
- 3
Stay organized with a clear plan and timeline
- 4
Maintain open communication with team members
- 5
Practice stress-relief techniques when needed
Example Answers
I prioritize tasks by urgency. When facing tight deadlines, I break the project into smaller, manageable steps to stay focused and organized. Keeping open communication with my team ensures we are all aligned.
Filler Spreader Position Details
Related Positions
Similar positions you might be interested in.
Ace Your Next Interview!
Practice with AI feedback & get hired faster
Personalized feedback
Used by hundreds of successful candidates
Ace Your Next Interview!
Practice with AI feedback & get hired faster
Personalized feedback
Used by hundreds of successful candidates