Top 29 Filler Interview Questions and Answers [Updated 2025]
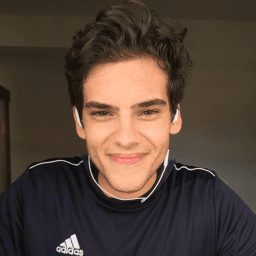
Andre Mendes
•
March 30, 2025
Navigating an interview for a 'Filler' role can be daunting, but preparation is key to success. In this post, we delve into the most common interview questions you'll encounter, complete with example answers and expert tips to help you respond confidently and effectively. Whether you're a seasoned professional or new to the field, these insights will equip you to make a lasting impression.
Download Filler Interview Questions in PDF
To make your preparation even more convenient, we've compiled all these top Fillerinterview questions and answers into a handy PDF.
Click the button below to download the PDF and have easy access to these essential questions anytime, anywhere:
List of Filler Interview Questions
Behavioral Interview Questions
Can you describe a time when you worked within a team to complete a project as a Filler? What was your role and contribution?
How to Answer
- 1
Choose a clear example from your experience as a Filler.
- 2
Focus on your specific role and tasks within the team.
- 3
Highlight how your contributions directly impacted the project's success.
- 4
Mention any challenges faced and how the team overcame them.
- 5
Conclude with what you learned from the experience.
Example Answers
In my previous job, our team had to meet a major deadline for a large order. I was responsible for efficiently filling orders based on priority. By organizing the workflow and communicating with team members, we completed the project ahead of schedule, resulting in positive feedback from our supervisor.
Describe an experience where you identified a quality issue during the filling process. What steps did you take?
How to Answer
- 1
Mention the specific quality issue you found.
- 2
Describe how you detected the issue during the filling process.
- 3
Explain the immediate actions you took to address the issue.
- 4
Discuss any preventive measures you implemented to avoid future issues.
- 5
Highlight the positive outcome from your actions on product quality.
Example Answers
During the filling process, I noticed that the fill levels of the containers were inconsistent. I checked the calibration of the filling machine and discovered it was off by a few milliliters. I recalibrated the machine immediately and completed a trial run to ensure accuracy. As a result, fill levels became consistent, and we maintained quality standards.
Don't Just Read Filler Questions - Practice Answering Them!
Reading helps, but actual practice is what gets you hired. Our AI feedback system helps you improve your Filler interview answers in real-time.
Personalized feedback
Unlimited practice
Used by hundreds of successful candidates
Have you ever trained a new employee in filling operations? What approach did you take?
How to Answer
- 1
Share specific experiences you had while training new hires
- 2
Highlight the training methods you used, such as hands-on demonstrations or shadowing
- 3
Mention the importance of clear communication throughout the process
- 4
Discuss how you tracked the new employee's progress and provided feedback
- 5
Include any adjustments you made based on the new employee's learning style
Example Answers
Yes, I trained several new employees in filling operations using a hands-on approach. I started with a detailed demonstration of the filling machines, followed by allowing them to shadow me. I encouraged them to ask questions and I provided feedback on their techniques as they practiced.
Describe a time when you took the initiative to improve the filling process. What was the outcome?
How to Answer
- 1
Identify a specific example where you made a change in the filling process.
- 2
Explain the problem you observed before your initiative.
- 3
Describe the action you took to improve the process.
- 4
Mention the results or outcomes of your action, using metrics if possible.
- 5
Reflect on what you learned from the experience.
Example Answers
In my previous role, I noticed that our filling process often led to overfills. I analyzed the filling data and proposed a re-calibration of the machines. After implementing new settings, we reduced overfills by 30%, which saved costs and minimized waste.
Tell me about a situation where you encountered a disagreement with a colleague during filling operations. How did you handle it?
How to Answer
- 1
Focus on a specific incident for clarity
- 2
Describe the nature of the disagreement, keeping it professional
- 3
Explain your approach to resolve the issue
- 4
Highlight the outcome and what you learned
- 5
Emphasize teamwork and communication skills
Example Answers
In one instance, my colleague and I disagreed on the best method for filling a batch. I suggested we take a few minutes to discuss our approaches. We compared our methods, leading to a compromise that improved efficiency. This experience taught me the value of open communication.
Give an example of how you have managed multiple tasks in a filling process under tight deadlines.
How to Answer
- 1
Identify a specific situation where you had to manage multiple filling tasks.
- 2
Describe the tasks you were juggling and their deadlines.
- 3
Explain the strategies you used to prioritize and organize your work.
- 4
Mention any tools or methods you utilized to track progress.
- 5
Conclude with the outcome and what you learned from the experience.
Example Answers
In my previous role at XYZ Corp, I had to fill 500 orders within a 2-day deadline. I listed all orders by priority, started with the high-volume ones, and used a checklist to ensure each was filled accurately. I often communicated with my team to delegate tasks effectively, and we completed all orders on time with zero errors.
Can you describe a time when you received constructive criticism about your filling work? How did you respond?
How to Answer
- 1
Choose a specific instance that clearly illustrates the criticism
- 2
Explain the context and what the criticism was about
- 3
Detail how you reacted emotionally and practically to the feedback
- 4
Describe the steps you took to improve your work
- 5
Conclude with the positive outcome or lesson learned from the experience
Example Answers
In my last job, my supervisor pointed out that I was not following the filing protocol correctly, which led to misplaced documents. I felt a bit embarrassed but appreciated the feedback. I asked for a refresher on the filing procedures and I also took notes to ensure I followed them properly from then on. As a result, my filing accuracy improved significantly and my supervisor noticed the change.
How do you evaluate your own performance in filling tasks? Can you share an example?
How to Answer
- 1
Reflect on specific metrics or criteria you use to assess your task completion.
- 2
Provide a concrete example of a task you filled and how you measured your success.
- 3
Discuss any feedback you seek from others to support your self-evaluation.
- 4
Mention any tools or methods you use for tracking your performance.
- 5
Highlight a lesson learned from your evaluation process that improved your performance.
Example Answers
I evaluate my performance by tracking the time it takes me to complete tasks and the quality of the outcomes. For instance, while filling out reports, I check for accuracy and make sure I meet deadlines. Recently, I completed a report 2 days early and received positive feedback from my manager, which confirmed my efficient approach.
Describe a situation where customer feedback influenced the way you approached filling tasks.
How to Answer
- 1
Choose a specific instance where customer feedback impacted your work.
- 2
Explain the feedback you received and its context clearly.
- 3
Describe the changes you made to your filling process based on that feedback.
- 4
Highlight the positive outcomes from those changes.
- 5
Keep your response focused and relevant to the filler position.
Example Answers
In my previous job, a customer noted that their orders often had missing items. I reviewed the filling process and found that we were missing key checks. I implemented a checklist system, which reduced errors and improved customer satisfaction significantly.
Don't Just Read Filler Questions - Practice Answering Them!
Reading helps, but actual practice is what gets you hired. Our AI feedback system helps you improve your Filler interview answers in real-time.
Personalized feedback
Unlimited practice
Used by hundreds of successful candidates
Technical Interview Questions
What types of filling machinery are you familiar with, and how have you operated or maintained them?
How to Answer
- 1
List specific filling machinery you have experience with.
- 2
Briefly describe your role in operating each type of machinery.
- 3
Mention any maintenance tasks you regularly performed.
- 4
Highlight any training you received on these machines.
- 5
Emphasize your adherence to safety and quality standards.
Example Answers
I have operated piston fillers and gravity fillers. In my last job, I was responsible for setting up and adjusting the piston filler for various products. I performed daily maintenance by cleaning and lubricating the machinery to ensure smooth operation.
What safety standards and regulations are important for filling operations, and how do you ensure compliance?
How to Answer
- 1
Identify relevant safety standards like OSHA regulations and industry-specific guidelines.
- 2
Discuss how to implement a safety training program for staff.
- 3
Explain the importance of regular safety audits and inspections.
- 4
Mention the use of personal protective equipment (PPE) and its compliance.
- 5
Include the significance of documentation and record-keeping for safety procedures.
Example Answers
In filling operations, key standards include OSHA regulations and FDA guidelines. To ensure compliance, I conduct safety training sessions for all staff, emphasizing the use of PPE and regular safety audits to identify potential hazards.
Don't Just Read Filler Questions - Practice Answering Them!
Reading helps, but actual practice is what gets you hired. Our AI feedback system helps you improve your Filler interview answers in real-time.
Personalized feedback
Unlimited practice
Used by hundreds of successful candidates
Can you explain different filling techniques and when each would be appropriate to use?
How to Answer
- 1
Briefly define at least three filling techniques.
- 2
Explain the advantages of each technique.
- 3
Provide real-world examples of when to use each technique.
- 4
Consider mentioning any specific materials associated with each technique.
- 5
Keep your explanations straightforward and focused.
Example Answers
There are several filling techniques like manual filling, vacuum filling, and pressure filling. Manual filling is cost-effective for small batches, vacuum filling prevents air from entering, making it ideal for sensitive liquids. Pressure filling is great for high-speed production lines but requires specialized equipment.
What methods do you use to ensure that the filled products meet quality specifications?
How to Answer
- 1
Describe specific quality control checks you perform during filling.
- 2
Mention any equipment or tools you use to measure quality.
- 3
Include steps for training staff on quality standards.
- 4
Talk about how you document and track quality data.
- 5
Discuss how you respond to any quality issues found.
Example Answers
I ensure filled products meet quality specifications by conducting visual inspections at each stage of the filling process and using calibrated equipment to measure fill levels.
How would you troubleshoot a malfunctioning filling machine? Can you describe the steps you would take?
How to Answer
- 1
Start by checking for error messages or alarms on the machine.
- 2
Inspect the machine's components, such as hoses and valves, for visible issues.
- 3
Ensure that all settings are correct and follow the machine's operational guidelines.
- 4
Test the machine with a small batch to identify the specific malfunction.
- 5
Document any changes made and observations noted during the troubleshooting.
Example Answers
First, I would check the control panel for any error messages. Then, I'd visually inspect the hoses and valves to see if there are any leaks or blockages. Next, I would confirm that the settings are as per the standard operating procedure before testing the machine with a small batch to identify the issue.
What procedures do you follow for the handling and storage of materials used in the filling process?
How to Answer
- 1
Start by discussing the importance of material integrity
- 2
Mention specific storage conditions like temperature and humidity controls
- 3
Explain how you categorize materials for ease of access and safety
- 4
Include any protocols for checking material quality before use
- 5
Highlight communication with team members about storage and handling procedures
Example Answers
I ensure that all materials are stored in a clean, dry area with proper temperature control. I regularly check the materials for damage and communicate with our team about any changes to storage conditions to maintain quality.
How do you keep track of filling operations and what documentation do you maintain?
How to Answer
- 1
Use checklists to track daily filling tasks and ensure consistency.
- 2
Document every batch with details such as date, time, and parameters of the filling process.
- 3
Utilize digital logs or filling software to maintain real-time records.
- 4
Regularly review documentation for accuracy and compliance with quality standards.
- 5
Create a centralized filing system for easy access to historical filling records.
Example Answers
I keep track of filling operations using checklists for each batch that list necessary parameters such as fill volume and speed. I also maintain a digital log that records the date and any issues encountered during the process.
What key performance indicators do you think are essential in filler operations, and how do you monitor them?
How to Answer
- 1
Identify critical KPIs such as production efficiency, downtime, and quality metrics.
- 2
Explain how you track these KPIs daily or weekly.
- 3
Mention any specific tools or software you use for monitoring.
- 4
Discuss the importance of using these indicators for continuous improvement.
- 5
Provide examples of how you've used KPIs to make operational decisions.
Example Answers
In filler operations, I believe that production efficiency, downtime, and product quality are essential KPIs. I monitor these indicators using a combination of daily production reports and real-time dashboards. We utilize software like MES to track performance, allowing for quick identification of trends and issues, which helps in optimizing our processes.
How do you coordinate with logistics to ensure timely supply of filling materials?
How to Answer
- 1
Establish clear communication channels with the logistics team.
- 2
Use inventory management tools to monitor supply levels.
- 3
Schedule regular meetings to discuss upcoming needs and any potential delays.
- 4
Prioritize critical materials and plan ahead for peak production times.
- 5
Implement a contingency plan for unexpected shortages.
Example Answers
I maintain open communication with logistics through weekly meetings to ensure we are aligned on upcoming supply needs. I also utilize an inventory management system to keep track of material levels and identify potential shortfalls early.
Situational Interview Questions
If you notice that the filling level is consistently below specifications, what steps would you take to address this issue?
How to Answer
- 1
Check the filling machine settings and calibration to ensure accuracy.
- 2
Investigate raw material quality; ensure the product is not inconsistent.
- 3
Review maintenance logs for the filling equipment and perform necessary repairs.
- 4
Conduct training sessions for operators on proper filling techniques.
- 5
Implement regular checks and monitoring to maintain consistent filling levels.
Example Answers
I would first check the calibration of the filling machine to ensure it's set correctly. Then, I would examine the quality of the filling material to make sure there are no inconsistencies affecting the fill levels.
Imagine you're faced with two orders that need immediate filling. How would you prioritize your work?
How to Answer
- 1
Assess the deadlines of both orders.
- 2
Consider the value or impact of each order on the client or business.
- 3
Evaluate the resources available to address each order.
- 4
Communicate with team members if needed for clarity.
- 5
Stay organized and document the priorities for better workflow.
Example Answers
I would first check the deadlines for both orders. If one has a tighter deadline, I would prioritize that one. Next, I'd consider which order impacts the customer relationship more and make my decision based on that.
Don't Just Read Filler Questions - Practice Answering Them!
Reading helps, but actual practice is what gets you hired. Our AI feedback system helps you improve your Filler interview answers in real-time.
Personalized feedback
Unlimited practice
Used by hundreds of successful candidates
If a team member was not following the filling procedure properly, how would you handle the situation?
How to Answer
- 1
Address the issue promptly and directly with the team member.
- 2
Use a calm and non-confrontational tone to discuss the observed behavior.
- 3
Ask questions to understand their perspective and any challenges they face.
- 4
Reiterate the importance of following procedures for safety and quality.
- 5
Suggest additional training or resources if necessary.
Example Answers
I would approach the team member privately and say, 'I noticed that there are some inconsistencies in the filling procedure you’re following. Can we talk about what might be causing that?' This way, I can understand their perspective and help them correct it while emphasizing the importance of our procedures.
You are running a filling line and the system shows an error. What will you do first?
How to Answer
- 1
Stay calm and assess the situation methodically
- 2
Check the error message on the control panel for details
- 3
Inspect if any safety protocols need to be followed
- 4
Determine if you can reset the system or if it requires technical support
- 5
Document the error for future reference and troubleshooting
Example Answers
First, I will remain calm and check the control panel for the specific error message. Then, I will see if it’s safe to temporarily stop the line and attempt a reset if needed. If the error persists, I will follow our protocol to contact maintenance.
Suppose you have identified an inefficiency in the filling process. What actions would you take to improve it?
How to Answer
- 1
Analyze the current filling process to identify specific bottlenecks
- 2
Gather data on the filling times and error rates to support your findings
- 3
Propose specific changes, such as adjusting equipment settings or training staff
- 4
Request feedback from team members involved in the process for additional insights
- 5
Implement changes on a trial basis and measure the results to ensure improvement
Example Answers
I would first analyze the data from our filling process to see where the delays occur. After identifying specific bottlenecks, I would suggest adjusting the machine settings to optimize speed.
If you find that a batch of filled products is incorrectly labeled, what steps would you take to rectify the matter?
How to Answer
- 1
Immediately stop distribution of the affected products.
- 2
Identify the extent of the labeling issue and which products are affected.
- 3
Notify your supervisor and relevant quality control personnel.
- 4
Develop a plan to relabel the products correctly.
- 5
Implement a review process to prevent future labeling errors.
Example Answers
First, I would halt any further distribution of the incorrectly labeled products. Then, I would identify all affected batches and inform my supervisor about the situation. After that, I would create a plan for relabeling the products accurately and ensure that we review our labeling procedure to avoid this issue in the future.
What would you do if you run out of filling supplies while processing an urgent order?
How to Answer
- 1
Quickly assess the situation to understand the extent of the supply shortage
- 2
Communicate promptly with your supervisor about the issue
- 3
Look for alternative supplies or substitutes that can be used
- 4
Explore if other team members can assist with sourcing the supplies
- 5
Implement an order adjustment if necessary to fulfill the urgent request
Example Answers
I would first check the inventory to confirm what supplies are missing and how critical they are for the order. Then, I would inform my supervisor about the situation immediately. If possible, I would look for any substitutes that we could use to keep the order moving.
If you were in charge of the filling department and encountered low morale, what steps would you take to improve it?
How to Answer
- 1
Conduct a one-on-one meeting with team members to understand their concerns and feedback.
- 2
Organize team-building activities to foster relationships and enhance teamwork.
- 3
Recognize and celebrate small wins to boost positivity and motivation.
- 4
Implement an open-door policy to encourage communication and suggestions.
- 5
Provide opportunities for skill development and career growth within the team.
Example Answers
I would start by talking to each team member to understand their issues. Then, I would plan team-building events to strengthen our camaraderie. Additionally, I would celebrate our successes, no matter how small, to improve the workplace atmosphere.
If a filling line is behind schedule, how would you motivate your team to meet the deadline?
How to Answer
- 1
Assess the reasons for the delay and communicate transparently with your team.
- 2
Set short, achievable goals to create a sense of urgency and accomplishment.
- 3
Incentivize the team with rewards for meeting targets, such as recognition or small bonuses.
- 4
Provide support and resources to help them overcome obstacles quickly.
- 5
Foster teamwork by encouraging collaboration and open communication.
Example Answers
First, I would gather the team to discuss the reasons for the delay and listen to their input. Then, I would set clear, short-term goals to keep everyone on track. I might also implement a small reward system for achieving those goals to boost morale.
Filler Position Details
Salary Information
Recommended Job Boards
CareerBuilder
www.careerbuilder.com/jobs/fillerZipRecruiter
www.ziprecruiter.com/Jobs/FillerThese job boards are ranked by relevance for this position.
Related Positions
- Filler Spreader
- Base Filler
- Hole Filler
- Board Filler
- Basket Filler
- Core Finisher
- Finisher
- Heading Maker
- Masker
- Color Worker
Similar positions you might be interested in.
Ace Your Next Interview!
Practice with AI feedback & get hired faster
Personalized feedback
Used by hundreds of successful candidates
Ace Your Next Interview!
Practice with AI feedback & get hired faster
Personalized feedback
Used by hundreds of successful candidates