Top 30 Base Filler Interview Questions and Answers [Updated 2025]
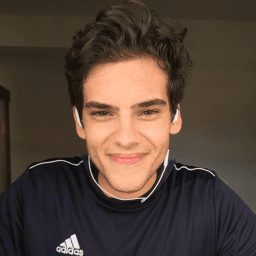
Andre Mendes
•
March 30, 2025
Are you preparing for a Base Filler interview and want to stand out? Our comprehensive guide provides the most common interview questions for this role, complete with example answers and insightful tips to help you respond effectively. Whether you're a seasoned professional or new to the field, this post will equip you with the confidence and knowledge needed to make a lasting impression.
Download Base Filler Interview Questions in PDF
To make your preparation even more convenient, we've compiled all these top Base Fillerinterview questions and answers into a handy PDF.
Click the button below to download the PDF and have easy access to these essential questions anytime, anywhere:
List of Base Filler Interview Questions
Behavioral Interview Questions
Can you describe a time when you worked effectively with a team to achieve a common goal?
How to Answer
- 1
Choose a specific project or task that required teamwork.
- 2
Highlight your role and contributions clearly.
- 3
Explain how the team collaborated and communicated.
- 4
Mention the outcome and its impact.
- 5
Use 'I' statements to showcase your personal contributions.
Example Answers
In my previous job, our team was tasked with launching a new product. I took the lead on market research and shared findings in weekly meetings. We collaborated closely, dividing tasks based on our strengths. The product launched on time and exceeded initial sales goals by 30%.
Tell me about a conflict you had with a colleague and how you resolved it.
How to Answer
- 1
Choose a specific conflict that is work-related.
- 2
Explain the perspective of both you and your colleague.
- 3
Describe the steps you took to address the conflict.
- 4
Focus on collaboration and compromise in your resolution.
- 5
Conclude with the positive outcome or lesson learned.
Example Answers
In my last project, I disagreed with a colleague about the approach to a task. I felt that we should follow a data-driven method, while he preferred a more experimental approach. I scheduled a meeting where we could both present our views. We listened to each other and eventually combined our methods to create a hybrid approach. This led to the project’s success and strengthened our teamwork.
Don't Just Read Base Filler Questions - Practice Answering Them!
Reading helps, but actual practice is what gets you hired. Our AI feedback system helps you improve your Base Filler interview answers in real-time.
Personalized feedback
Unlimited practice
Used by hundreds of successful candidates
Describe a situation where you had to manage your time effectively to meet a tight deadline.
How to Answer
- 1
Identify a specific project or situation with a deadline.
- 2
Explain the steps you took to prioritize tasks.
- 3
Mention any tools or methods you used for time management.
- 4
Highlight the outcome and what you learned.
- 5
Keep it brief and focused on your actions.
Example Answers
In my last job, I had to prepare a report in just two days. I prioritized the most critical sections first, breaking them into manageable tasks. I used a checklist to track my progress and spent extra time in the morning before work to stay focused. The report was completed on time and praised for its quality.
Can you give an example of a time when you had to adapt to a significant change at work?
How to Answer
- 1
Focus on a specific change that was significant to you.
- 2
Explain how you assessed the situation and determined your response.
- 3
Highlight the steps you took to adapt and overcome challenges.
- 4
Mention the outcome and what you learned from the experience.
- 5
Connect the experience to skills relevant for a Base Filler position.
Example Answers
In my previous job, our team had to switch from in-person meetings to a fully remote setup due to unforeseen circumstances. I quickly set up a virtual meeting schedule, organized our work into digital task boards, and ensured clear communication through chat apps. This led to a smooth transition and our team continued to meet deadlines effectively.
Describe a time you noticed a quality issue in your work. How did you handle it?
How to Answer
- 1
Think of a specific example where you identified a quality issue.
- 2
Explain the steps you took to address the issue promptly.
- 3
Highlight how you communicated this to your supervisor or team.
- 4
Discuss the outcome and what you learned from the situation.
- 5
Emphasize your commitment to quality and problem-solving.
Example Answers
In my previous job, I noticed that a batch of products had a defect. I immediately informed my supervisor and halted the production for that batch. We conducted a review, identified the error in the machinery, and corrected it. This action prevented further defects and reinforced my attention to quality.
Tell me about a time you received feedback from a client. How did you respond?
How to Answer
- 1
Choose a specific example that highlights your ability to handle feedback.
- 2
Explain the feedback you received and its context clearly.
- 3
Describe your immediate response and how you implemented the feedback.
- 4
Share the outcome of the changes you made based on the feedback.
- 5
Emphasize the importance of client communication and continuous improvement.
Example Answers
In my previous role, a client mentioned that the reports we provided were too technical. I acknowledged their feedback, clarified their expectations, and adjusted the reports to be more user-friendly. As a result, the client was much happier and said they felt more engaged with the information.
Give an example of a time when you took initiative on a project or task.
How to Answer
- 1
Choose a specific project where you saw a need for change or improvement.
- 2
Explain the action you took and why you decided to take it.
- 3
Highlight the positive outcome or results from your initiative.
- 4
Use the STAR method: Situation, Task, Action, Result.
- 5
Keep your example relevant to the skills needed for the Base Filler position.
Example Answers
In my last job as a warehouse assistant, I noticed that our packing process was slow. I took the initiative to redesign the packing station layout to minimize movement. As a result, we improved our packing time by 20%, which helped meet tight deadlines.
Tell me about a time you identified an area for improvement in a process. What did you do?
How to Answer
- 1
Choose a specific process from your past experience
- 2
Explain how you noticed the inefficiency or issue
- 3
Describe the steps you took to address the problem
- 4
Mention any positive results or outcomes
- 5
Use the STAR method: Situation, Task, Action, Result
Example Answers
In my previous role, I noticed that our inventory checks took too long. I tracked the process and found that manual entries were causing delays. I proposed implementing a digital tracking system, which we rolled out after testing. As a result, we cut check times by 50%.
Can you describe an occasion where you went above and beyond to ensure a project was completed on time?
How to Answer
- 1
Think of a specific project where deadlines were tight.
- 2
Highlight your personal contributions and efforts.
- 3
Include any challenges you faced and how you overcame them.
- 4
Emphasize teamwork or communication that helped you succeed.
- 5
Conclude with the positive outcome of the project.
Example Answers
In my last job, we had a major product launch that was falling behind schedule due to supplier delays. I organized daily check-ins with the team, worked late to finalize our marketing materials, and coordinated with the suppliers to expedite shipments. This effort allowed us to launch on time, and the product exceeded sales expectations.
Don't Just Read Base Filler Questions - Practice Answering Them!
Reading helps, but actual practice is what gets you hired. Our AI feedback system helps you improve your Base Filler interview answers in real-time.
Personalized feedback
Unlimited practice
Used by hundreds of successful candidates
Situational Interview Questions
How would you respond if a client complained about the quality of the filler they received?
How to Answer
- 1
Listen carefully to the client's complaint without interrupting.
- 2
Acknowledge their feelings and validate their concerns.
- 3
Ask clarifying questions to understand the specific issue.
- 4
Offer a solution, such as a follow-up appointment or a redo if necessary.
- 5
Ensure to follow up after the solution to confirm their satisfaction.
Example Answers
I would listen to the client and acknowledge their concerns, then ask them to explain what specific quality issue they experienced. I would propose a follow-up appointment to resolve the matter and ensure they leave satisfied.
If you noticed that the filling process was not meeting quality standards, what steps would you take?
How to Answer
- 1
Immediately document the observed issue and any relevant data
- 2
Notify the supervisor or quality control team about the problem
- 3
Conduct a quick assessment to identify the root cause of the issue
- 4
Implement corrective actions based on the findings
- 5
Monitor the filling process closely to ensure standards are met going forward
Example Answers
I would first document any discrepancies I noticed and gather data to support what I've seen. Then, I would notify my supervisor to ensure they are aware of the issue. After that, I would look into possible causes, like checking equipment settings, and then implement the necessary adjustments. Lastly, I would continue to monitor the process to confirm that we return to quality standards.
Don't Just Read Base Filler Questions - Practice Answering Them!
Reading helps, but actual practice is what gets you hired. Our AI feedback system helps you improve your Base Filler interview answers in real-time.
Personalized feedback
Unlimited practice
Used by hundreds of successful candidates
What would you do if you experienced a safety incident during a filling operation?
How to Answer
- 1
Stay calm and assess the situation quickly.
- 2
Ensure immediate safety of yourself and others first.
- 3
Follow established safety protocols and procedures for such incidents.
- 4
Report the incident to a supervisor or safety officer promptly.
- 5
Document the incident for further investigation and improvement.
Example Answers
In the event of a safety incident, I would first make sure everyone is safe and remove any hazards. Then I would follow our protocols to report the incident to my supervisor, ensuring that all necessary documentation is completed afterwards.
How would you handle a situation where a team member was not contributing effectively to the filling process?
How to Answer
- 1
Observe the team member's workflow and identify specific issues.
- 2
Communicate directly and empathetically with the team member.
- 3
Offer assistance and suggest ways to improve their contribution.
- 4
Involve the team in discussing best practices and solutions.
- 5
If necessary, escalate the issue to a supervisor with documented examples.
Example Answers
I would first observe the team member to identify what might be hindering their performance. Then I would have a private conversation with them to discuss their challenges and see how I could help. If needed, I could share some best practices that could enhance their efficiency.
If given multiple filling tasks with overlapping deadlines, how would you prioritize your work?
How to Answer
- 1
Assess the urgency of each task based on deadlines
- 2
Determine the importance of each task regarding quality and output
- 3
Break tasks into smaller steps to estimate completion time
- 4
Communicate with your supervisor if unsure about priority
- 5
Focus on completing one task at a time to maintain quality
Example Answers
I would first assess the deadlines and urgency of each task. Then, I would prioritize the one that has the closest deadline but also requires high quality. If I need clarification, I would communicate with my supervisor to ensure I am aligned with team goals.
If management requested a change in the filling process to increase efficiency, how would you approach this?
How to Answer
- 1
Analyze the current filling process to identify bottlenecks.
- 2
Gather data on filling times and error rates for informed decisions.
- 3
Propose specific changes based on findings, such as equipment upgrades or new techniques.
- 4
Involve team members in discussions to leverage their insights and experience.
- 5
Prepare to test changes on a small scale before full implementation.
Example Answers
First, I would analyze the current filling process to pinpoint inefficiencies. Then, I would gather data on our filling times and error rates. Based on this data, I might suggest new equipment or training for the team. Collaborating with my colleagues would help refine the proposal and ensure buy-in. Finally, I would recommend testing the changes in a pilot program before rolling them out fully.
If you were assigned to train a new employee on filling techniques, what key points would you cover?
How to Answer
- 1
Start with an overview of the filling process and its importance.
- 2
Explain the different types of fillers used and their specific applications.
- 3
Demonstrate proper techniques with hands-on practice and visual aids.
- 4
Emphasize safety protocols and quality control measures.
- 5
Encourage questions and provide ongoing support as they learn.
Example Answers
I would begin by explaining the filling process and its role in production. Then, I would introduce the various types of fillers we use, such as liquid and powder, and their uses. I'd provide a hands-on demonstration of the filling techniques, ensuring they understand each step. I'd also stress the importance of following safety guidelines and maintaining product quality. Finally, I would encourage them to ask questions during their training.
How would you handle a situation where you had too much work and not enough help?
How to Answer
- 1
Prioritize tasks based on urgency and importance.
- 2
Communicate with your supervisor about workload challenges.
- 3
Explore whether some tasks can be delegated or postponed.
- 4
Consider resources available, such as reaching out to colleagues for temporary assistance.
- 5
Stay organized and maintain a calm approach to manage stress.
Example Answers
I would first prioritize my tasks to focus on the most critical ones. Then, I would communicate with my supervisor about the situation and see if more help can be provided or if some tasks can be pushed back.
How would you deal with a sudden shortage of a key base filler material during production?
How to Answer
- 1
Assess the current inventory levels immediately to understand the extent of the shortage
- 2
Communicate with suppliers to check availability and expedite delivery of the material
- 3
Evaluate the production schedule and consider adjusting it to accommodate the delay
- 4
Identify alternative materials that could be used temporarily and their impact on the final product
- 5
Keep the production team informed about developments and next steps to maintain morale and focus
Example Answers
I would first check our inventory to see how much of the key filler we have left. Then, I would reach out to our suppliers for quick delivery options. If the shortage would affect our schedule significantly, I would consider adjusting our production timeline accordingly. I'd also explore any alternative materials that might serve as substitutes, ensuring they meet quality standards. Throughout, I would keep the team updated to make sure everyone is aligned and focused.
How would you collaborate with the quality assurance team when addressing a filling issue?
How to Answer
- 1
Communicate clearly about the issue and its impact on production.
- 2
Gather detailed observations and data to support the QA team.
- 3
Participate in joint problem-solving sessions with QA.
- 4
Implement agreed-upon changes and monitor results closely.
- 5
Follow up to ensure the issue is resolved and document the process.
Example Answers
I would first communicate the specific filling issue to the QA team, including data on how it affects production. Next, I'd gather evidence from our side to help them understand the problem. We could then set up a meeting to brainstorm potential solutions together and decide on the best course of action. I would implement the agreed changes and monitor the results to ensure they work as intended.
Don't Just Read Base Filler Questions - Practice Answering Them!
Reading helps, but actual practice is what gets you hired. Our AI feedback system helps you improve your Base Filler interview answers in real-time.
Personalized feedback
Unlimited practice
Used by hundreds of successful candidates
What would you do if the filling machine you were operating suddenly stopped working?
How to Answer
- 1
Stay calm and assess the situation quickly
- 2
Check for visible issues like jammed products or error messages
- 3
Follow company procedures for machine troubleshooting
- 4
Inform your supervisor or maintenance team as necessary
- 5
Document the issue and your actions for future reference
Example Answers
I would first remain calm and check the machine for any visible jams or error indicators. After assessing the situation, I would follow the troubleshooting steps outlined in our training and reach out to my supervisor if I couldn't resolve it quickly.
Technical Interview Questions
What filling techniques are you familiar with and which do you prefer?
How to Answer
- 1
List specific filling techniques you have experience with.
- 2
Explain the advantages of each technique briefly.
- 3
Share your preferred technique and why you like it.
- 4
Mention any relevant experiences or results from using these techniques.
- 5
Keep your answer concise and focused on practical applications.
Example Answers
I am familiar with the gravity filling technique and the pressure filling technique. I prefer pressure filling because it allows for faster production rates and better control of the fill level, which I've successfully used in my last job, reducing product waste by 15%.
Can you explain the different types of base fillers and their specific applications?
How to Answer
- 1
Identify the main types of base fillers used in the industry
- 2
Explain the properties that make each type suitable for its application
- 3
Use specific examples to illustrate how each filler is used
- 4
Keep your answer organized by categorizing fillers
- 5
Be prepared to discuss advantages and disadvantages of each type
Example Answers
There are several types of base fillers such as chalk, talc, and calcium carbonate. Chalk is good for improving the texture and opacity of products. Talc adds softness and smoothness, especially in cosmetics. Calcium carbonate is often used in paints for its durability and cost-effectiveness.
Don't Just Read Base Filler Questions - Practice Answering Them!
Reading helps, but actual practice is what gets you hired. Our AI feedback system helps you improve your Base Filler interview answers in real-time.
Personalized feedback
Unlimited practice
Used by hundreds of successful candidates
What machinery or equipment have you operated in past roles related to base filling?
How to Answer
- 1
List specific machinery you have experience with
- 2
Mention the context of their use for base filling
- 3
Highlight any relevant certifications or training
- 4
Emphasize your familiarity with safety procedures
- 5
Share results or accomplishments from your operation of this machinery
Example Answers
In my previous job at XYZ Company, I operated a Bobcat skid steer for base filling in construction projects. I ensured optimal material placement and adhered to safety standards.
What safety practices do you follow when working with base fillers?
How to Answer
- 1
Always wear appropriate personal protective equipment (PPE) such as gloves and masks.
- 2
Ensure proper ventilation in the work area to avoid inhalation of fumes.
- 3
Read and understand the material safety data sheets (MSDS) for base fillers before use.
- 4
Dispose of any waste materials according to hazardous waste regulations.
- 5
Keep a clean workspace to prevent spills and accidents with the fillers.
Example Answers
I always wear gloves and a mask when working with base fillers to protect myself from any harmful substances.
How do you troubleshoot problems that arise during the filling process?
How to Answer
- 1
Identify the specific issue by observing the filling machine and product.
- 2
Check for any error codes or alerts the machine may display.
- 3
Review the fill specifications to ensure they are being met.
- 4
Adjust the machine settings as needed based on the observed problem.
- 5
Consult with team members for additional insights or previous solutions.
Example Answers
When problems arise during filling, I first check the machine for any error codes and observe if the fill is inconsistent. I then refer to the fill specifications to make sure we are within the required limits. If adjustments are needed, I update the settings accordingly and monitor the results closely.
What regulations do you consider vital while performing the filling tasks?
How to Answer
- 1
Identify key regulations related to safety and quality control.
- 2
Mention industry standards relevant to filling processes.
- 3
Discuss the importance of cleanliness and contamination prevention.
- 4
Highlight the need for equipment calibration and maintenance regulations.
- 5
Emphasize adherence to documentation and traceability requirements.
Example Answers
I consider safety regulations such as OSHA guidelines essential for ensuring a safe working environment. I also follow ISO standards, which are critical in maintaining quality control during the filling process.
How do you ensure the quality of the base filler products?
How to Answer
- 1
Conduct regular quality checks during production.
- 2
Use high-quality raw materials from reliable suppliers.
- 3
Implement strict adherence to mixing and processing protocols.
- 4
Train staff on quality standards and procedures.
- 5
Document all quality control processes and results.
Example Answers
I ensure quality by conducting regular checks at different production stages, using top-grade raw materials, and following strict mixing protocols.
What specific properties do you consider important when selecting a base filler for a project?
How to Answer
- 1
Identify the key application of the filler and its purpose.
- 2
Consider the physical properties such as particle size, shape, and surface area.
- 3
Evaluate the chemical compatibility with other materials in the project.
- 4
Assess the filler’s performance characteristics like strength and durability.
- 5
Think about cost-effectiveness and availability for the project.
Example Answers
When selecting a base filler, I focus on its particle size and shape to ensure proper dispersion and bonding in the mixture, along with its compatibility with the other materials being used in the project.
How do you use data to track the performance of the filling process?
How to Answer
- 1
Identify key performance indicators like fill volume and cycle time
- 2
Use data logs to monitor consistency and deviations during the filling process
- 3
Analyze data trends to identify potential bottlenecks or inefficiencies
- 4
Implement regular reporting to keep stakeholders updated on performance metrics
- 5
Utilize software tools for real-time data tracking and alerts
Example Answers
I track KPIs such as fill volume and cycle time using data logging. This helps me monitor consistency and make adjustments as needed.
Base Filler Position Details
Related Positions
- Basket Filler
- Filler
- Board Filler
- Filler Spreader
- Hole Filler
- Bag Liner
- Core Finisher
- Part Maker
- Bed Setter
- Converter
Similar positions you might be interested in.
Ace Your Next Interview!
Practice with AI feedback & get hired faster
Personalized feedback
Used by hundreds of successful candidates
Ace Your Next Interview!
Practice with AI feedback & get hired faster
Personalized feedback
Used by hundreds of successful candidates