Top 31 Bag Liner Interview Questions and Answers [Updated 2025]
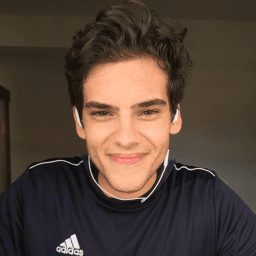
Andre Mendes
•
March 30, 2025
Preparing for a Bag Liner interview can be daunting, but we're here to help you succeed. In this post, we've compiled the most common interview questions for the Bag Liner role, complete with example answers and insightful tips to help you respond effectively. Whether you're a seasoned professional or new to the field, this guide is designed to boost your confidence and enhance your interview performance.
Download Bag Liner Interview Questions in PDF
To make your preparation even more convenient, we've compiled all these top Bag Linerinterview questions and answers into a handy PDF.
Click the button below to download the PDF and have easy access to these essential questions anytime, anywhere:
List of Bag Liner Interview Questions
Behavioral Interview Questions
Can you describe a time when you had to meet a tight deadline in your work as a Bag Liner and how you handled it?
How to Answer
- 1
Choose a specific project or task with a clear deadline.
- 2
Explain the steps you took to ensure timely completion.
- 3
Highlight any challenges faced and how you overcame them.
- 4
Emphasize teamwork if applicable, and your role in it.
- 5
Conclude with the outcome and any positive feedback received.
Example Answers
In one instance, we had a large order to fulfill in just two days due to a client's sudden request. I coordinated with the team to prioritize the most critical tasks, ensuring everyone knew their role. We worked overtime and communicated regularly to stay on track. Ultimately, we completed the order on time, and the client praised our efficiency.
Tell me about a time when you collaborated with a team to improve the quality of the bag lining process.
How to Answer
- 1
Choose a specific project or task.
- 2
Highlight your role in the collaboration.
- 3
Explain the steps your team took to identify quality issues.
- 4
Describe the solutions implemented and the results achieved.
- 5
Use metrics or feedback to showcase the improvement.
Example Answers
In my previous job, our team noticed inconsistencies in bag lining quality. I organized a meeting to discuss these issues and we collectively decided to streamline the lining procedure. We introduced a checklist for quality control, leading to a 20% reduction in defects over the next month.
Don't Just Read Bag Liner Questions - Practice Answering Them!
Reading helps, but actual practice is what gets you hired. Our AI feedback system helps you improve your Bag Liner interview answers in real-time.
Personalized feedback
Unlimited practice
Used by hundreds of successful candidates
What has been your biggest challenge as a Bag Liner and how did you overcome it?
How to Answer
- 1
Identify a specific challenge you faced.
- 2
Explain the context and why it was a challenge.
- 3
Describe the actions you took to address it.
- 4
Highlight the outcome and what you learned.
- 5
Keep it relevant to the Bag Liner position.
Example Answers
My biggest challenge was dealing with a sudden shortage of materials. I quickly coordinated with suppliers and adjusted our production schedule to ensure continuity. In the end, we met our deadlines and improved our supplier relationships.
Describe a situation where you identified a potential safety hazard in the bag lining process and what you did about it.
How to Answer
- 1
Think of a specific instance where a hazard was present.
- 2
Describe how you noticed the risk during the bag lining process.
- 3
Explain the steps you took to address the hazard effectively.
- 4
Include any collaboration with teammates or supervisors.
- 5
Highlight the outcome or lesson learned from the experience.
Example Answers
In my previous role, I noticed that the conveyor belt used for transporting bags had a loose panel that could pinch fingers. I immediately stopped the line and reported it to my supervisor, who arranged for a maintenance check, preventing any injuries.
Give an example of how you adapted to changes in project requirements or specifications in your previous bag lining projects.
How to Answer
- 1
Choose a specific project where requirements changed.
- 2
Briefly describe the initial requirements and the changes made.
- 3
Explain your thought process in adapting to these changes.
- 4
Highlight the positive outcomes of your adaptation.
- 5
Mention any tools or methods you used to achieve these results.
Example Answers
In my last project on bag lining for a retail client, the original specifications changed from a simple fabric lining to a waterproof lining due to customer feedback. I quickly researched waterproof materials and presented alternatives to the team, which led to a successful redesign. This adaptation not only met the new requirements but also increased customer satisfaction, resulting in a 20% increase in sales.
Describe a time when you took initiative to improve the bag lining process without being asked.
How to Answer
- 1
Think of a specific project where you identified a problem.
- 2
Explain the steps you took to address the issue.
- 3
Mention the outcome or improvement resulted from your actions.
- 4
Use quantifiable results if possible.
- 5
Highlight your proactive attitude and teamwork.
Example Answers
In my previous position, I noticed that our bag lining process often led to fabric wastage. I proposed a new method of cutting the fabric to fit more efficiently. I created a new template and shared it with my colleagues. After implementing this, we reduced waste by 30% and saved costs significantly.
Can you provide an example where your attention to detail made a significant difference in the quality of the final product?
How to Answer
- 1
Think of a specific project where you caught an error others missed
- 2
Describe how your action improved the outcome or quality
- 3
Use metrics or feedback to highlight the positive impact
- 4
Be concise and focus on your role in the situation
- 5
End with a reflection on the importance of attention to detail
Example Answers
In my previous role, I reviewed a batch of product liners before shipment and discovered a misalignment that could have affected installation. I brought this to the team and we corrected it before it went out, avoiding potential customer complaints. The client later praised our quality control.
Describe a time when you successfully managed multiple projects at once. How did you ensure timely completion?
How to Answer
- 1
Identify specific projects you managed simultaneously.
- 2
Explain your prioritization method for tasks.
- 3
Describe any tools or methodologies you used to track progress.
- 4
Discuss communication strategies with team members or stakeholders.
- 5
Highlight the results and how deadlines were met.
Example Answers
In my previous role, I managed three projects at once: a product launch, a marketing campaign, and a customer feedback initiative. I prioritized tasks using a Gantt chart to visualize timelines. I held weekly check-ins with the teams to ensure alignment and used project management software to track progress. All projects were completed on time, resulting in a successful product launch and positive customer feedback.
Can you tell me about a time when you resolved a disagreement within your team regarding the bag lining procedures?
How to Answer
- 1
Identify a specific disagreement that occurred.
- 2
Explain your approach to facilitate discussion between team members.
- 3
Show how you listened to different viewpoints before proposing a solution.
- 4
Discuss the outcome and how the team benefited from the resolution.
- 5
Emphasize the importance of teamwork and communication in your response.
Example Answers
In my previous role, there was a disagreement on whether to use a thicker liner or a standard liner for our bags. I organized a meeting where both sides could present their reasons. After listening, we agreed to test both types for a week and then review the results together. This approach helped everyone feel heard and led to a solution based on real data rather than opinions.
Don't Just Read Bag Liner Questions - Practice Answering Them!
Reading helps, but actual practice is what gets you hired. Our AI feedback system helps you improve your Bag Liner interview answers in real-time.
Personalized feedback
Unlimited practice
Used by hundreds of successful candidates
Technical Interview Questions
How do you troubleshoot issues that arise during the bag lining process?
How to Answer
- 1
Identify the specific issue by inspecting the bag lining process carefully.
- 2
Use data from previous runs to understand patterns in the issues.
- 3
Involve team members to gather insights and possible solutions collaboratively.
- 4
Test solutions on a small scale before full implementation.
- 5
Document the troubleshooting process for future reference.
Example Answers
When issues arise, I first inspect the lining to identify the source of the problem. I also check previous production records to see if similar issues occurred before.
What types of materials do you have experience working with when creating bag liners?
How to Answer
- 1
Identify specific materials you have worked with, like polyester or nylon.
- 2
Mention the properties of these materials relevant to bag liners, such as durability or water resistance.
- 3
Provide examples of projects or products where you used these materials.
- 4
Highlight any technical skills related to working with these materials, such as sewing or laminating.
- 5
Express willingness to learn about new materials if needed.
Example Answers
I have experience working with nylon and polyester for bag liners, as they are lightweight yet durable. For instance, I used waterproof nylon in a series of outdoor bags, ensuring they are suitable for various weather conditions.
Don't Just Read Bag Liner Questions - Practice Answering Them!
Reading helps, but actual practice is what gets you hired. Our AI feedback system helps you improve your Bag Liner interview answers in real-time.
Personalized feedback
Unlimited practice
Used by hundreds of successful candidates
Explain the types of machinery or equipment you have used in bag lining and your proficiency level with them.
How to Answer
- 1
List specific machines used for bag lining such as filling machines or sealers.
- 2
Provide your proficiency level with each machine, such as beginner, intermediate or advanced.
- 3
Mention any training or certification you have received related to these machines.
- 4
Include relevant work experience where you operated this machinery.
- 5
Be concise and focus on relevant details without being overly technical.
Example Answers
I have experience with automatic filling machines and heat sealers. I would rate my proficiency with filling machines as advanced, as I operated them daily for two years, ensuring proper bag weights and processes.
What are the essential steps in the bag lining process that ensure quality and durability?
How to Answer
- 1
Start by explaining the importance of material selection for durability.
- 2
Discuss the preparation of the bag including cleaning and inspecting.
- 3
Explain the lining application technique, ensuring even coverage and strong adhesion.
- 4
Highlight the curing or drying process, which is crucial for strength.
- 5
Mention quality checks and testing for leaks and tears before final approval.
Example Answers
The bag lining process begins with selecting high-quality materials that are resistant to wear. Next, the bag is thoroughly cleaned and inspected for any damages. The lining is then applied using a method that guarantees an even and strong bond. It's important to allow the adhesive to cure properly to ensure durability. Finally, we conduct quality checks for leaks and tear resistances to ensure the bag meets all standards.
What industry standards do you follow when production lining bags and ensuring compliance?
How to Answer
- 1
Always refer to the ISO standards applicable to your production processes.
- 2
Keep up-to-date with any regulatory requirements in packaging and manufacturing.
- 3
Utilize checklists for quality control at each stage of production.
- 4
Train your team on compliance standards and safety procedures regularly.
- 5
Document all processes and quality checks to ensure traceability.
Example Answers
I follow ISO 9001 standards for quality management and ensure all our processes comply with the latest packaging regulations. We conduct regular training sessions to keep the team informed.
What testing methods do you use to ensure the bag liners meet required specifications?
How to Answer
- 1
Mention specific testing methods like tensile strength testing or leak testing.
- 2
Describe how you ensure compliance with material specifications.
- 3
Include examples of quality control measures you implement.
- 4
Discuss any industry standards you follow during testing.
- 5
Emphasize the importance of documentation and traceability in testing.
Example Answers
I use tensile strength testing and leak testing to ensure our bag liners meet specifications. We also perform regular inspections during the production phase to maintain quality standards.
How do you approach the design of bag liners to ensure they meet both aesthetic and functional requirements?
How to Answer
- 1
Understand the target audience and their preferences for aesthetics.
- 2
Select materials that balance durability and visual appeal.
- 3
Consider the functionality aspects like usability, storage solutions, and ease of maintenance.
- 4
Collaborate with cross-functional teams to gather diverse insights.
- 5
Prototype designs and gather feedback to refine both appearance and functionality.
Example Answers
I start by researching the target audience to understand their color and style preferences. Then, I choose durable materials that also look good, like high-quality nylon with a trendy finish. I ensure that the liner has features for easy organization and cleaning. Collaborating with the marketing team helps to align the design with customer expectations. Finally, I create prototypes and test them with users to make necessary adjustments.
What regulations and compliance practices do you follow in the bag liner manufacturing process?
How to Answer
- 1
Identify key regulations relevant to bag liner manufacturing such as ISO standards and environmental regulations.
- 2
Highlight your knowledge of safety practices and worker safety compliance.
- 3
Discuss quality control processes and how they align with industry standards.
- 4
Mention any certifications or audits that your organization undergoes.
- 5
Emphasize continuous improvement practices to meet or exceed compliance standards.
Example Answers
In our bag liner manufacturing, we follow ISO 9001 standards to ensure quality management. We also adhere to local environmental regulations regarding waste disposal and material sourcing. Regular audits are conducted to maintain compliance and ensure worker safety practices are strictly enforced.
What new technologies or innovations in bag lining are you most excited about and why?
How to Answer
- 1
Research recent innovations in bag lining materials and techniques.
- 2
Identify specific technologies that improve functionality or sustainability.
- 3
Consider how these innovations align with industry trends and consumer needs.
- 4
Explain the benefits of the technologies you mention.
- 5
Show enthusiasm about how these innovations can transform the market.
Example Answers
I'm particularly excited about the development of biodegradable lining materials. These can significantly reduce environmental impact while maintaining quality and durability.
What routine maintenance practices do you perform on the machinery used for bag lining?
How to Answer
- 1
Discuss regular cleaning schedules for machinery.
- 2
Mention lubrication of moving parts to prevent wear.
- 3
Highlight the importance of checking and replacing filters regularly.
- 4
Talk about inspecting belts, hoses, and electrical connections.
- 5
Include tracking maintenance logs to record issues and repairs.
Example Answers
I perform routine cleaning of the bag lining machinery weekly to remove dust and debris. I also ensure that all moving parts are lubricated according to schedule, and I regularly check and replace any filters as needed.
Don't Just Read Bag Liner Questions - Practice Answering Them!
Reading helps, but actual practice is what gets you hired. Our AI feedback system helps you improve your Bag Liner interview answers in real-time.
Personalized feedback
Unlimited practice
Used by hundreds of successful candidates
How do you adjust the bag lining process to accommodate changes in production volume?
How to Answer
- 1
Assess current production capacity and limit
- 2
Implement flexible scheduling for bag lining tasks
- 3
Train staff to operate multiple machines for increased efficiency
- 4
Monitor and adjust raw material supply based on demand
- 5
Regularly review and optimize the lining workflow for scalability
Example Answers
To adjust the bag lining process, I first evaluate our current capacity and identify bottlenecks. Then, I create flexible schedules that allow us to ramp up when needed. Additionally, I train team members to handle different machines, which helps us adapt quickly to changes in volume.
Situational Interview Questions
If you notice that the bag liners are consistently failing quality checks, what steps would you take to investigate and rectify the issue?
How to Answer
- 1
Review the quality check data to identify specific failure points.
- 2
Conduct a root cause analysis to understand why failures are occurring.
- 3
Engage with team members involved in the production process for insights.
- 4
Implement corrective actions based on findings and monitor improvements.
- 5
Document the process and results for future reference.
Example Answers
I would first analyze the quality check data to see the reasons for failure. Then, I would hold discussions with the production team to gather insights and perform a root cause analysis. Once I identify the issues, I would implement targeted corrective actions and monitor the outcomes closely.
Imagine you are assigned to a new project with limited resources. How would you prioritize tasks to meet project milestones?
How to Answer
- 1
Identify key project milestones and deadlines.
- 2
Assess available resources and team strengths.
- 3
List all tasks and their impact on milestones.
- 4
Use a priority matrix to categorize tasks: high, medium, low.
- 5
Communicate priorities clearly to the team to ensure alignment.
Example Answers
I would start by mapping out the project milestones and understanding the deadlines. Then, I would evaluate my team’s strengths and the resources at hand. After listing the tasks, I would use a priority matrix to focus on tasks that impact milestones the most and address high-priority tasks first while communicating clearly with the team.
Don't Just Read Bag Liner Questions - Practice Answering Them!
Reading helps, but actual practice is what gets you hired. Our AI feedback system helps you improve your Bag Liner interview answers in real-time.
Personalized feedback
Unlimited practice
Used by hundreds of successful candidates
If you were leading a team of Bag Liners and two members had a conflict, how would you resolve it?
How to Answer
- 1
Listen to both parties separately to understand their perspectives
- 2
Encourage open communication between the conflicting members
- 3
Focus on the issue, not personal attacks
- 4
Help them find common ground and a compromise
- 5
Follow up to ensure the resolution is effective and the team is cohesive
Example Answers
I would first meet with each member to hear their side of the conflict. Then, I'd bring them together and encourage a constructive conversation. My focus would be on the issue at hand, ensuring they address their concerns respectfully, and help them agree on a solution that works for both. Finally, I would check in after a few days to see how things are going.
What would you do if you realized a project was going to be delayed? How would you communicate this to your supervisor?
How to Answer
- 1
Assess the reasons for the delay clearly before communicating.
- 2
Prepare a solution or plan to mitigate the delay.
- 3
Communicate the delay as soon as possible to your supervisor.
- 4
Be honest and take responsibility while explaining the situation.
- 5
Suggest a follow-up meeting to discuss next steps.
Example Answers
If I realized a project was going to be delayed, I would first investigate the reasons for the delay and gather all relevant facts. I'd prepare a brief plan outlining how we could minimize the impact and present this to my supervisor promptly, taking responsibility for the situation and seeking their guidance on how to proceed.
If a client is unhappy with the bag liners produced, how would you handle the feedback?
How to Answer
- 1
Acknowledge the client's concerns sincerely.
- 2
Ask specific questions to understand the issues better.
- 3
Provide reassurance that you value their feedback.
- 4
Discuss potential solutions or adjustments directly.
- 5
Follow up after addressing the issue to ensure satisfaction.
Example Answers
I would first acknowledge the client's concerns and ask them to elaborate on what specifically made them unhappy. It's important to ensure they feel heard. Then, I'd discuss possible adjustments and follow up later to make sure they're satisfied with the changes.
You have a short supply of a critical material needed for bag liners. What steps would you take to ensure production continues?
How to Answer
- 1
Identify alternative materials that can be used temporarily.
- 2
Assess current inventory and production schedules.
- 3
Communicate with suppliers for expedited deliveries or substitutes.
- 4
Engage the production team to adjust workflows.
- 5
Consider customer needs and prioritize essential orders.
Example Answers
I would first analyze our current inventory to understand how long we can sustain production. Then, I would contact our suppliers to find out the earliest they can deliver more of the critical material. If they cannot meet our needs quickly, I’d explore alternative materials that could be used in the meantime, ensuring they meet quality standards. Lastly, I would communicate with the production team to adjust operations accordingly and keep our customers informed about any delays.
If you were to encounter a major equipment failure mid-production, what steps would you take to minimize downtime?
How to Answer
- 1
Quickly assess the situation to identify the cause of failure.
- 2
Notify the supervisor and relevant team members immediately.
- 3
Isolate the equipment to ensure safety and prevent further damage.
- 4
Initiate the troubleshooting process or refer to equipment manuals.
- 5
Prepare a backup plan or alternative solutions to maintain production flow.
Example Answers
First, I would assess the equipment to determine the cause of the failure. Then, I would inform my supervisor and the team. After isolating the faulty equipment, I would follow the troubleshooting steps outlined in the manual. In parallel, I would check if we have backup equipment ready to minimize downtime.
How would you handle a situation where a customer demands a last-minute change to a bag liner order?
How to Answer
- 1
Stay calm and listen carefully to the customer's request.
- 2
Assess the feasibility of the change and check for immediate possibilities.
- 3
Communicate any potential impacts on delivery time and costs transparently.
- 4
Offer alternatives if the change cannot be accommodated exactly as requested.
- 5
Document the changes and confirm them with the customer to avoid misunderstandings.
Example Answers
I would first listen to the customer's request and understand what they need. Next, I would check our production capabilities to see if we can accommodate the change. If it's feasible, I'd inform them about any adjustments in delivery time and costs. If not, I’d suggest similar options that meet their requirements.
If you were to assess risks associated with a new bag liner material, what factors would you consider?
How to Answer
- 1
Identify potential hazards related to the material's chemical properties
- 2
Consider the performance characteristics under operational conditions
- 3
Evaluate environmental impacts and regulatory compliance
- 4
Assess the durability and lifecycle performance of the material
- 5
Include feedback from industry standards and previous material successes
Example Answers
I would analyze the chemical composition for toxicity and environmental risks, evaluate how the material performs under varying temperatures and pressures, and ensure it meets all regulatory guidelines.
Imagine you are tasked with training a new hire on bag lining. What key points would you emphasize?
How to Answer
- 1
Explain the importance of clean and organized workspace before starting.
- 2
Demonstrate the proper technique for aligning the bags.
- 3
Discuss the materials used and their specific purposes.
- 4
Emphasize safety protocols to prevent injury during the lining process.
- 5
Encourage questions and provide hands-on practice for better understanding.
Example Answers
I would start by stressing the importance of having a clean and organized workspace. Then, I would demonstrate the correct technique for aligning the bags. I would also explain the different materials we use and their roles in the process. Safety is a key factor, so I would cover all relevant protocols. Finally, I would ensure the new hire has time for hands-on practice and encourage them to ask any questions.
Don't Just Read Bag Liner Questions - Practice Answering Them!
Reading helps, but actual practice is what gets you hired. Our AI feedback system helps you improve your Bag Liner interview answers in real-time.
Personalized feedback
Unlimited practice
Used by hundreds of successful candidates
Bag Liner Position Details
Related Positions
- Drawer Liner
- Luggage Liner
- Carton Liner
- Rubber Liner
- Garment Folder
- Basket Filler
- Bottle Carrier
- Paper Bundler
- Paper Sorter
- Paperer
Similar positions you might be interested in.
Ace Your Next Interview!
Practice with AI feedback & get hired faster
Personalized feedback
Used by hundreds of successful candidates
Ace Your Next Interview!
Practice with AI feedback & get hired faster
Personalized feedback
Used by hundreds of successful candidates