Top 30 Drawer Liner Interview Questions and Answers [Updated 2025]
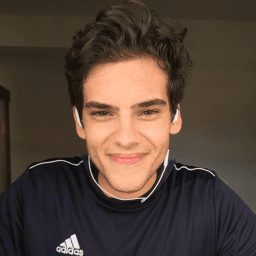
Andre Mendes
•
March 30, 2025
Preparing for a Drawer Liner interview? This blog post compiles the most common questions you might encounter, complete with example answers and expert tips to help you respond confidently and effectively. Whether you're aiming to perfect your technique or showcase your experience, this guide is designed to equip you with the insights needed to make a great impression and secure the job.
Download Drawer Liner Interview Questions in PDF
To make your preparation even more convenient, we've compiled all these top Drawer Linerinterview questions and answers into a handy PDF.
Click the button below to download the PDF and have easy access to these essential questions anytime, anywhere:
List of Drawer Liner Interview Questions
Behavioral Interview Questions
Can you describe a time when you had to ensure the quality of drawer liners you produced?
How to Answer
- 1
Select a specific instance where you checked quality.
- 2
Mention the standards or criteria you used.
- 3
Explain the steps you took to ensure quality control.
- 4
State the outcome or what you learned from the experience.
- 5
Keep it focused on your role and contributions.
Example Answers
In my previous job, I oversaw a batch of drawer liners that had to meet specific thickness standards. I measured each liner using calipers and removed those that did not meet the criteria. As a result, we maintained a 98% approval rate in our quality checks.
Tell me about a time you collaborated with a team to accomplish a project related to drawer liners.
How to Answer
- 1
Think of a specific project involving drawer liners.
- 2
Describe your role and contributions clearly.
- 3
Highlight the teamwork aspect and collaboration methods.
- 4
Mention any challenges faced and how the team overcame them.
- 5
Conclude with the positive outcome of the project.
Example Answers
In my previous job, I worked on a project to redesign our drawer liners for enhanced usability. I collaborated with the design team to brainstorm materials and styles. We faced a challenge in balancing aesthetics with durability, but by sharing ideas in our meetings and gathering feedback, we created a product that satisfied both criteria. The new liners increased customer satisfaction by 30%.
Don't Just Read Drawer Liner Questions - Practice Answering Them!
Reading helps, but actual practice is what gets you hired. Our AI feedback system helps you improve your Drawer Liner interview answers in real-time.
Personalized feedback
Unlimited practice
Used by hundreds of successful candidates
Describe a situation where you faced a challenge in the production of drawer liners and how you resolved it.
How to Answer
- 1
Identify a specific challenge related to drawer liner production.
- 2
Explain the steps you took to analyze and address the issue.
- 3
Highlight any teamwork or communication involved in resolving the challenge.
- 4
Discuss the outcome and any improvements made as a result.
- 5
Keep your response focused on your actions and the positive results.
Example Answers
In a recent production run, we discovered that the adhesive used for the drawer liners was not adhering properly. I initiated a meeting with the production team to gather input. We tested a different adhesive and retrained staff on the application process. As a result, we improved adhesion rates by 30%.
Give an example of how you prioritize tasks when working on multiple orders of drawer liners.
How to Answer
- 1
Identify urgent orders that need immediate attention based on deadlines.
- 2
Assess the complexity of each order, prioritizing simpler tasks first if time permits.
- 3
Group similar tasks together to increase efficiency during production.
- 4
Communicate with team members about workload to balance tasks effectively.
- 5
Review inventory levels to ensure necessary materials are available before starting.
Example Answers
When working on multiple orders of drawer liners, I prioritize based on deadlines, starting with the orders that are due soonest. For example, if I have three orders and one is due tomorrow, I'll focus on that one first.
Describe a time when you had to lead a project related to drawer liners.
How to Answer
- 1
Choose a specific project that involved drawer liners.
- 2
Highlight your leadership role and contributions.
- 3
Discuss the goals of the project and how you achieved them.
- 4
Mention any challenges faced and how you overcame them.
- 5
Conclude with the results and impact of the project.
Example Answers
In my previous role at Home Goods, I led a project to redesign our drawer liners. I coordinated with the design team to create a more appealing pattern and material. We aimed to increase sales by 15%. We faced production delays but I organized daily meetings to adapt quickly. We ultimately exceeded our sales goal by 20%.
Can you give an example of when you had to adapt your approach in the production of drawer liners?
How to Answer
- 1
Think of a specific situation where you faced a challenge.
- 2
Describe what the original plan was and what went wrong.
- 3
Explain how you assessed the situation and what changes you made.
- 4
Focus on the outcome and what you learned from the experience.
- 5
Be concise and ensure your example is relevant to drawer liner production.
Example Answers
In a previous role, we had a sudden increase in demand for a specific pattern. Initially, we planned to produce a standard quantity. I quickly assessed our materials and adjusted the production schedule to increase output by 30%. This helped us meet the demand without compromising quality.
Tell me about a time you built a lasting relationship with a client regarding drawer liners.
How to Answer
- 1
Choose a specific client interaction that highlights your communication skills.
- 2
Explain how you understood the client's needs regarding drawer liners.
- 3
Discuss the solution you offered and how it met or exceeded their expectations.
- 4
Mention any follow-up actions that strengthened the relationship.
- 5
Conclude with the positive outcome for both you and the client.
Example Answers
I once worked with a home organizer who needed drawer liners that matched various kitchen styles. I spent time understanding her design needs and provided samples that complemented her projects. After she used my liners and received great feedback from her clients, I followed up to see how they were performing. She appreciated the personal touch, and we’ve collaborated on multiple projects since.
How do you handle constructive criticism regarding your work with drawer liners?
How to Answer
- 1
Listen carefully and stay open-minded when receiving feedback.
- 2
Ask clarifying questions to understand the criticism fully.
- 3
Reflect on the feedback and identify areas for improvement in your drawer liner designs.
- 4
Implement changes based on constructive criticism in future projects.
- 5
Thank the person giving feedback for their insights to show appreciation.
Example Answers
I listen attentively to the feedback and take notes to understand what can be improved in my drawer liner designs. I then reflect on this and make adjustments in my next projects.
Don't Just Read Drawer Liner Questions - Practice Answering Them!
Reading helps, but actual practice is what gets you hired. Our AI feedback system helps you improve your Drawer Liner interview answers in real-time.
Personalized feedback
Unlimited practice
Used by hundreds of successful candidates
Describe a situation where you had a conflict with a coworker regarding drawer liner production and how you resolved it.
How to Answer
- 1
Identify the conflict clearly and specifically
- 2
Explain the different perspectives involved
- 3
Describe the steps you took to address the conflict
- 4
Highlight the resolution and outcome
- 5
Emphasize what you learned from the experience.
Example Answers
I had a disagreement with a coworker about the type of materials to use for drawer liners. They preferred a more expensive option for durability while I advocated for a cost-effective choice. We agreed to test both materials in a small batch, which helped us assess performance and choose what worked best without escalating tensions. The outcome was successful, and we ended up using a blend that satisfied both durability and cost-efficiency.
Technical Interview Questions
What materials are commonly used for drawer liners and what are their benefits?
How to Answer
- 1
List popular materials like paper, vinyl, felt, and rubber
- 2
Explain benefits such as protection, cushioning, easy cleaning
- 3
Mention aesthetic appeal of certain materials
- 4
Consider mentioning moisture resistance
- 5
Summarize durability and grip properties of various options
Example Answers
Common materials for drawer liners include paper, vinyl, felt, and rubber. Paper liners are inexpensive and offer decorative options, while vinyl is easy to clean and protects surfaces from spills. Felt provides cushioning for delicate items, and rubber is durable and provides excellent grip to prevent items from sliding.
What tools or machines have you used in the production of drawer liners?
How to Answer
- 1
List specific tools or machines you have experience with.
- 2
Mention the purpose of each tool in the production process.
- 3
Include any safety protocols you followed while using the tools.
- 4
Highlight any relevant training you received on these machines.
- 5
Emphasize how your experience can benefit the company.
Example Answers
In my previous job, I operated rotary cutting machines to cut the liner material accurately. I also used edge banding machines to finish the edges, following strict safety protocols.
Don't Just Read Drawer Liner Questions - Practice Answering Them!
Reading helps, but actual practice is what gets you hired. Our AI feedback system helps you improve your Drawer Liner interview answers in real-time.
Personalized feedback
Unlimited practice
Used by hundreds of successful candidates
Explain your understanding of quality control measures in the production of drawer liners.
How to Answer
- 1
Identify specific quality control measures relevant to drawer liners.
- 2
Discuss the importance of material quality in production.
- 3
Mention testing methods used to ensure product durability.
- 4
Explain the role of inspection during and after production.
- 5
Highlight the importance of feedback in continuous improvement.
Example Answers
Quality control measures for drawer liners include inspecting raw materials for defects and conducting tests like tear resistance and color fastness. This ensures that the liners are durable and meet customer expectations.
How do you approach the design aspect of drawer liners to meet customer specifications?
How to Answer
- 1
Research the target market to understand common preferences.
- 2
Gather specific customer specifications such as size, material, and design.
- 3
Prototype different designs based on gathered specifications.
- 4
Solicit feedback from potential users on prototypes.
- 5
Iterate designs based on feedback to optimize aesthetics and functionality.
Example Answers
I begin by researching popular trends in drawer liner designs and materials that resonate with my target demographic. I then collect detailed specifications from customers regarding size and desired patterns, create prototypes, and gather user feedback for improvements.
What safety precautions do you think are important when working with drawer liner materials and production equipment?
How to Answer
- 1
Identify specific materials used and their associated hazards.
- 2
Mention the importance of personal protective equipment (PPE) like gloves and masks.
- 3
Discuss safe handling procedures for sharp tools and machinery.
- 4
Emphasize maintaining a clean and organized workspace to prevent accidents.
- 5
Talk about the need for proper training on equipment and emergency procedures.
Example Answers
I think it's important to wear gloves and masks while working with drawer liner materials to protect against any dust or chemical exposure. Using the correct tools safely and keeping a tidy workspace will reduce the risk of accidents.
What regulations or standards do you think are important for the production of drawer liners?
How to Answer
- 1
Research relevant industry regulations such as ASTM or ISO standards for materials.
- 2
Mention safety standards related to toxicity and flammability of materials used.
- 3
Consider environmental regulations for sourcing and waste management.
- 4
Highlight quality control standards to ensure product consistency.
- 5
Discuss consumer product safety regulations that apply to household goods.
Example Answers
I believe that adhering to ASTM standards for material safety is crucial, as it ensures the drawer liners are non-toxic and suitable for use in homes. Additionally, following ISO quality standards helps maintain consistent product quality, which is vital for customer satisfaction.
How do you approach customization requests for drawer liners from clients?
How to Answer
- 1
Listen carefully to the client's needs and preferences
- 2
Ask clarifying questions to understand specific requirements
- 3
Propose suitable materials and designs based on client input
- 4
Provide a few customized options for the client to choose from
- 5
Ensure clear communication about the customization process and timeline
Example Answers
I start by understanding exactly what the client is looking for during the initial consultation. Then, I ask follow-up questions to clarify their preferences and suggest a few materials and designs that could work for them.
What finishing techniques do you apply to ensure that drawer liners meet high-quality standards?
How to Answer
- 1
Start by discussing surface preparation methods.
- 2
Include specific finishing techniques like sanding or coating.
- 3
Mention quality control measures during and after finishing.
- 4
Highlight the importance of using high-quality materials.
- 5
Explain how you achieve consistency and durability in the finish.
Example Answers
I always begin with thorough surface preparation, ensuring all surfaces are clean and smooth. I utilize sanding to remove any imperfections, followed by applying a high-quality finish like a polyurethane coating for durability. Regular quality checks allow me to maintain consistent standards throughout the process.
What printing techniques have you used for custom drawer liners and how do they impact the final product?
How to Answer
- 1
Identify specific printing techniques like digital printing or flexography.
- 2
Discuss the benefits of each technique, such as color vibrancy and durability.
- 3
Mention how the choice of technique affects materials and textures.
- 4
Consider the environmental impact of the printing methods you’ve used.
- 5
Explain how these choices enhance the customer's experience.
Example Answers
I have primarily used digital printing for custom drawer liners. This method allows for vibrant colors and intricate designs, which enhance the aesthetic appeal of the product. It also enables quick turnaround times for custom orders, making it efficient for meeting client demands.
Situational Interview Questions
If you noticed a defect in a batch of drawer liners after production, what steps would you take?
How to Answer
- 1
Identify the type and extent of the defect immediately.
- 2
Document the defect with photos and descriptions for records.
- 3
Notify the production supervisor and quality control team right away.
- 4
Determine if the defect affects the entire batch or only a portion.
- 5
Plan corrective actions and communicate them to relevant teams.
Example Answers
First, I would identify what kind of defect is present and how many drawer liners are affected. Then I would document it with photos and notes. Next, I would inform the production supervisor and work with the quality control team to assess the situation fully.
How would you handle a situation where you were given a last-minute order for drawer liners with a tight deadline?
How to Answer
- 1
Stay calm and assess the situation quickly.
- 2
Prioritize the order and allocate resources efficiently.
- 3
Communicate with your team to ensure everyone is aware.
- 4
Consider any potential obstacles and plan for them.
- 5
Keep the customer updated on the progress.
Example Answers
I would first assess how many drawer liners are needed and the time we have. I would prioritize this order and assign tasks to my team, making sure to keep communication clear. If there are any potential delays, I'd reach out to the customer to keep them informed.
Don't Just Read Drawer Liner Questions - Practice Answering Them!
Reading helps, but actual practice is what gets you hired. Our AI feedback system helps you improve your Drawer Liner interview answers in real-time.
Personalized feedback
Unlimited practice
Used by hundreds of successful candidates
If a customer is unhappy with the drawer liners you produced, how would you address their concerns?
How to Answer
- 1
Acknowledge the customer's feelings and validate their concerns
- 2
Ask specific questions to fully understand the issue
- 3
Offer a solution, whether it be a replacement, refund, or modification
- 4
Follow up to ensure their satisfaction with the resolution
- 5
Document feedback for future improvements and quality control
Example Answers
I would first listen to the customer's complaints carefully and acknowledge their feelings. Then, I would ask questions to clarify the specific issues they have with the drawer liners. After understanding their concerns, I would offer to replace the product or provide a refund if the situation warrants it. Finally, I would follow up with them to ensure they are satisfied with the solution.
Imagine you identified a more efficient method for producing drawer liners; how would you propose this change?
How to Answer
- 1
Start by clearly explaining the identified efficiency.
- 2
Use data or examples to support your proposal.
- 3
Outline the benefits for both production and company.
- 4
Suggest a pilot program or trial to test the new method.
- 5
Be open to feedback and willing to collaborate with teams.
Example Answers
I discovered that by optimizing the cutting technique, we could reduce waste by 20%. I would present this with before and after data, highlighting cost savings and increased productivity. I'd propose a trial run with one production line to evaluate its effectiveness.
If you were running low on materials for drawer liners, how would you manage the situation to ensure production continues?
How to Answer
- 1
Assess current inventory and forecast remaining production needs
- 2
Communicate with suppliers for expedited orders or alternatives
- 3
Prioritize production schedules to focus on high-demand products
- 4
Explore using substitute materials if compatible with product standards
- 5
Implement a temporary halt on less critical production until materials arrive
Example Answers
I would first check our inventory levels to determine exactly how much material is left and how long it will last. Then, I would reach out to our suppliers to see if we can expedite an order or find alternative materials that meet our standards. I'd prioritize production on our most popular drawer liners while temporarily slowing down production on lower-demand items.
What would you do if there was a disagreement among team members about the design of a new drawer liner?
How to Answer
- 1
Encourage open communication among team members to express their ideas.
- 2
Facilitate a meeting to discuss each perspective and the reasons behind them.
- 3
Seek to identify common goals and the criteria for the design.
- 4
Consider using design mockups or prototypes to visualize differing ideas.
- 5
If necessary, involve a neutral third party to mediate the discussion.
Example Answers
I would start by setting up a meeting for the team to openly discuss their ideas and concerns about the drawer liner design. It's essential everyone feels heard. Then, I'd help guide the conversation to focus on our shared goals and what features are most important to our users.
How would you respond if your inventory tracking showed an unexpected surplus of drawer liner materials?
How to Answer
- 1
Analyze the root cause of the surplus to understand if it’s a data error or a supply issue.
- 2
Communicate with the procurement team to check on any recent orders that may have caused the surplus.
- 3
Consider options for utilizing the excess material, such as promotional offers or bundling with other products.
- 4
Adjust future order forecasts based on the current inventory levels to prevent similar situations.
- 5
Document the findings and create a report for management to improve inventory tracking in the future.
Example Answers
I would first analyze the data to determine if the surplus is due to an error or unexpected orders. Then, I'd discuss with procurement to understand recent supply changes and explore ways to use the extra material, like special sales.
How would you incorporate new technology into the production of drawer liners?
How to Answer
- 1
Research current technologies in manufacturing and apply them to production processes.
- 2
Consider automation options to improve efficiency and reduce labor costs.
- 3
Explore innovative materials that are environmentally friendly and cost-effective.
- 4
Implement software for better inventory management and production tracking.
- 5
Stay updated with industry trends and be open to experimentation with new methods.
Example Answers
I would first research advanced manufacturing technologies, such as automated cutting machines, to increase precision and reduce waste in drawer liner production.
If a supplier failed to deliver materials on time, how would you manage production schedules for drawer liners?
How to Answer
- 1
Assess the impact on current production timelines
- 2
Communicate promptly with the supplier for updates
- 3
Explore alternative suppliers or materials if necessary
- 4
Adjust production schedules by prioritizing available resources
- 5
Implement a contingency plan to mitigate future delays
Example Answers
I would first evaluate how the delay affects our current production schedule. Then, I would contact the supplier to understand the cause of the delay and get an updated timeline. If the delay is significant, I would consider sourcing from an alternative supplier while adjusting our production priorities accordingly.
How would you redesign a workflow process if you found it to be inefficient in producing drawer liners?
How to Answer
- 1
Identify the key inefficiencies in the current process using data
- 2
Engage with team members to gather input on the workflow issues
- 3
Propose specific changes that streamline steps or reduce waste
- 4
Incorporate technology or tools that can automate repetitive tasks
- 5
Pilot the new process on a small scale before full implementation
Example Answers
First, I would analyze production data to pinpoint delays. Then, I'd consult with my team for feedback on bottlenecks. From there, I’d simplify the material handling steps and see if a machine could automate cutting. Finally, I’d run a trial of these changes to measure improvements.
Don't Just Read Drawer Liner Questions - Practice Answering Them!
Reading helps, but actual practice is what gets you hired. Our AI feedback system helps you improve your Drawer Liner interview answers in real-time.
Personalized feedback
Unlimited practice
Used by hundreds of successful candidates
Drawer Liner Position Details
Related Positions
- Bag Liner
- Carton Liner
- Rubber Liner
- Luggage Liner
- Leather Dresser
- Garment Folder
- Wire Drawer
- Paperhanger
- Basket Filler
- Cupboard Builder
Similar positions you might be interested in.
Ace Your Next Interview!
Practice with AI feedback & get hired faster
Personalized feedback
Used by hundreds of successful candidates
Ace Your Next Interview!
Practice with AI feedback & get hired faster
Personalized feedback
Used by hundreds of successful candidates