Top 29 Rubber Liner Interview Questions and Answers [Updated 2025]
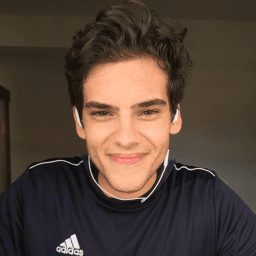
Andre Mendes
•
March 30, 2025
Preparing for a Rubber Liner interview? Look no further! This blog post compiles the most common interview questions for the Rubber Liner role, providing you with insightful example answers and practical tips to help you respond effectively. Whether you're a seasoned professional or new to the field, this guide will equip you with the knowledge and confidence needed to impress your interviewers. Dive in and start preparing today!
Download Rubber Liner Interview Questions in PDF
To make your preparation even more convenient, we've compiled all these top Rubber Linerinterview questions and answers into a handy PDF.
Click the button below to download the PDF and have easy access to these essential questions anytime, anywhere:
List of Rubber Liner Interview Questions
Behavioral Interview Questions
Can you describe a time when you worked with a team to complete a rubber lining project? What was your role?
How to Answer
- 1
Identify a specific project you worked on
- 2
Briefly explain the goal of the project
- 3
Describe your role and how you contributed
- 4
Mention teamwork and collaboration aspects
- 5
Outline the outcome and any challenges overcome
Example Answers
In my previous role, we had a project where we needed to apply rubber lining to a large tank. My role was to assist in the preparation and application process, ensuring the surfaces were clean and ready. I coordinated with other team members to manage our tasks efficiently and we completed the project ahead of schedule with positive feedback from the client.
Tell me about a challenge you faced during a rubber lining installation and how you overcame it.
How to Answer
- 1
Identify a specific challenge related to the installation process.
- 2
Mention the steps you took to address the issue.
- 3
Highlight any teamwork or communication involved in the solution.
- 4
Conclude with the positive outcome and what you learned from the experience.
- 5
Keep it relevant to the rubber lining industry.
Example Answers
During a rubber lining installation, we encountered a misalignment of the rubber sheets which could have led to water leakage. I quickly gathered the team to re-evaluate the installation and we adjusted the positioning using laser alignment tools. This improved accuracy, and we completed the job with no issues, reinforcing the importance of teamwork and precise planning.
Don't Just Read Rubber Liner Questions - Practice Answering Them!
Reading helps, but actual practice is what gets you hired. Our AI feedback system helps you improve your Rubber Liner interview answers in real-time.
Personalized feedback
Unlimited practice
Used by hundreds of successful candidates
Provide an example of a safety issue you encountered in your previous rubber lining work. How did you handle it?
How to Answer
- 1
Identify a specific safety issue you faced related to rubber lining.
- 2
Explain the steps you took to address the issue professionally.
- 3
Highlight any protocols or safety measures you followed.
- 4
Mention the outcome of your actions for future safety.
- 5
Keep your answer focused and relevant to the role.
Example Answers
During a lining installation, I noticed some workers not wearing proper safety gear. I addressed the issue by halting work and reminding everyone about the importance of PPE. I then ensured we had enough gear for everyone, which improved our safety record on site.
Describe a situation where you took the initiative to improve a process in rubber lining application.
How to Answer
- 1
Identify a specific challenge in the rubber lining process you observed.
- 2
Explain the steps you took to analyze the problem.
- 3
Describe the improvement you proposed and how you implemented it.
- 4
Mention the impact of your improvement on efficiency or quality.
- 5
Highlight any feedback or recognition you received from your team or management.
Example Answers
In my previous role, I noticed that we often faced delays due to the curing time of rubber linings. I researched faster curing agents and proposed a switch. After testing, we adopted a new mixture that cut curing time by 20% and increased our output without sacrificing quality. My manager recognized this as a significant efficiency gain.
How have you managed tight deadlines in your previous rubber lining projects?
How to Answer
- 1
Prioritize tasks based on urgency and importance
- 2
Communicate regularly with team members about progress
- 3
Use efficient installation techniques to save time
- 4
Stay organized and keep track of materials and schedules
- 5
Be flexible and ready to adapt to changes quickly
Example Answers
In my last project, we had a tight deadline due to a client's urgent requirements. I prioritized the most critical tasks and coordinated closely with my team to ensure everyone was aligned. We implemented faster curing methods to expedite the lining process, which helped us finish on time.
Can you describe a time when you learned a new skill related to rubber lining? How did you apply it?
How to Answer
- 1
Think of a specific skill related to rubber lining that you learned recently
- 2
Describe the learning process, including any training or resources you used
- 3
Explain how you applied this skill in a real-world scenario
- 4
Highlight the impact of your new skill on your work or your team
- 5
Be concise and focus on results or improvements made due to this skill
Example Answers
I learned how to effectively prepare substrates for rubber lining through a workshop. After the training, I applied this skill by leading a project where I ensured the surfaces were properly cleaned and treated, resulting in a significant reduction in adhesion issues.
Give an example of how you maintained a good relationship with a client during a challenging project.
How to Answer
- 1
Acknowledge the challenge you faced with the client.
- 2
Describe specific communication methods you used to keep the client informed.
- 3
Explain how you actively listened to the client's concerns.
- 4
Share a concrete outcome or resolution that resulted from your efforts.
- 5
Highlight any follow-up actions you took to ensure continued satisfaction.
Example Answers
During a tough installation project, I frequently updated the client via weekly check-ins, addressing any concerns they had directly. This communication helped us adjust our approach, and the project was completed on time, leading to a happy client who appreciated our transparency.
Describe how you have used feedback from previous projects to improve your rubber lining skills.
How to Answer
- 1
Reflect on specific projects where you received constructive feedback
- 2
Identify particular skills or techniques that were highlighted for improvement
- 3
Explain how you implemented changes in your approach based on the feedback
- 4
Include measurable results or outcomes from applying the feedback
- 5
Show willingness to learn and adapt based on previous experiences
Example Answers
In my last project, I received feedback regarding the consistency of my rubber lining thickness. I took this seriously and started using a more precise measuring tool, which improved my accuracy. The client noted a significant decrease in material waste in subsequent projects.
How have you collaborated with engineers or other professionals in rubber lining projects?
How to Answer
- 1
Describe specific projects where teamwork was key
- 2
Mention your role and contributions in the collaboration
- 3
Highlight effective communication methods used
- 4
Discuss challenges overcome through collaboration
- 5
Emphasize the results achieved as a team
Example Answers
In a recent project, I worked closely with engineers to design a new rubber lining system for a large tank. I coordinated the schedules, shared technical specifications, and ensured materials were compatible, which led to a successful installation ahead of schedule.
Don't Just Read Rubber Liner Questions - Practice Answering Them!
Reading helps, but actual practice is what gets you hired. Our AI feedback system helps you improve your Rubber Liner interview answers in real-time.
Personalized feedback
Unlimited practice
Used by hundreds of successful candidates
Technical Interview Questions
What types of rubber materials have you worked with, and what are their specific applications?
How to Answer
- 1
Identify specific types of rubber you have experience with, such as natural rubber or neoprene.
- 2
Discuss the properties of each rubber type that make them suitable for certain applications.
- 3
Mention any industries or projects where you have applied these materials.
- 4
Include examples of specific products or components made from these rubber types.
- 5
Be prepared to explain how you have ensured quality and performance using these materials.
Example Answers
I have worked primarily with EPDM and silicone rubber. EPDM is great for automotive applications due to its excellent weather resistance. Silicone is used in high-temperature environments like cooking appliances because of its stability and flexibility.
Can you explain the process of applying rubber lining for industrial tanks?
How to Answer
- 1
Start by describing surface preparation to ensure proper adhesion
- 2
Mention the type of rubber lining material used
- 3
Explain the application technique, such as spraying or hand application
- 4
Discuss the curing process and its importance
- 5
Finish by highlighting inspection and quality control steps
Example Answers
The process begins with preparing the tank surface, which involves cleaning and potentially sandblasting to remove any contaminants. I typically use EPDM rubber for its durability. The rubber is then applied using a spray technique for an even coat. After application, it is crucial to allow the lining to cure properly for optimal adhesion. Finally, I conduct thorough inspections to ensure the lining quality meets the standards.
Don't Just Read Rubber Liner Questions - Practice Answering Them!
Reading helps, but actual practice is what gets you hired. Our AI feedback system helps you improve your Rubber Liner interview answers in real-time.
Personalized feedback
Unlimited practice
Used by hundreds of successful candidates
What tools and equipment do you consider essential for a rubber lining job, and why?
How to Answer
- 1
Identify specific tools commonly used in rubber lining such as spray guns, rollers, and adhesives.
- 2
Explain the purpose of each tool and how it contributes to the quality of the work.
- 3
Mention safety equipment essential for worker protection.
- 4
Consider the need for surface preparation tools to ensure proper adhesion.
- 5
Conclude with a brief note on the importance of using high-quality materials.
Example Answers
In a rubber lining job, essential tools include spray guns for even application, rollers for smoothing out surfaces, and high-strength adhesives for bonding. We also need safety gear like gloves and masks for protection against fumes. Surface preparation tools like sanders ensure a clean base for proper adhesion.
What methods do you use to ensure proper adhesion of rubber lining to surfaces?
How to Answer
- 1
Start with surface preparation, ensuring all surfaces are clean and free of contaminants
- 2
Use appropriate primers or adhesives designed for rubber lining materials
- 3
Control the application temperature and humidity to optimize adhesion
- 4
Allow adequate curing time as per manufacturer's instructions
- 5
Inspect the finished lining for uniformity and adhesion quality
Example Answers
I ensure proper adhesion by first cleaning the surfaces thoroughly to remove any dust or oil. Then, I apply a suitable primer that promotes bonding with the rubber. I also monitor environmental conditions like temperature and humidity to ensure they are within recommended ranges for optimal adhesion.
How do you inspect and evaluate the quality of rubber lining after installation?
How to Answer
- 1
Check for uniform thickness using a calibrated gauge
- 2
Inspect for bubbles or wrinkles on the surface
- 3
Perform a pull test to ensure proper adhesion to the substrate
- 4
Look for any visible defects like cracks or tears
- 5
Ensure that the rubber lining is properly cured and meets specified standards
Example Answers
I inspect the rubber lining by measuring its thickness with a gauge to ensure it's uniform. Then, I check for surface defects like bubbles or wrinkles, and I perform a pull test to confirm good adhesion to the substrate.
What tests do you conduct to ensure the rubber lining is performing as required?
How to Answer
- 1
Discuss visual inspections during installation and routine maintenance
- 2
Mention adhesion testing methods to check bond strength
- 3
Include non-destructive testing techniques for quality assessment
- 4
Talk about monitoring abrasion resistance and impact testing
- 5
Explain the importance of regular environmental condition assessments
Example Answers
I conduct visual inspections after installation to check for any obvious defects and perform routine checks to ensure the integrity of the lining. Additionally, adhesion tests allow us to confirm that the bond strength meets our standards.
How do environmental factors influence your choice of rubber lining materials?
How to Answer
- 1
Identify specific environmental factors such as temperature, chemicals, and abrasion.
- 2
Discuss how these factors affect material degradation and performance.
- 3
Mention relevant standards or testing methods for material selection.
- 4
Explain the importance of durability and longevity in different environments.
- 5
Provide examples from past experiences or projects related to material choices.
Example Answers
In high-temperature environments, I choose heat-resistant rubber linings to ensure durability and prevent breakdown. For example, in a petrochemical context, I would select FKM rubber due to its resistance to aggressive chemicals.
What different application methods have you used for rubber lining and their effectiveness?
How to Answer
- 1
List specific application methods such as spray lining or hand application.
- 2
Discuss the conditions or scenarios where each method is most effective.
- 3
Include any personal experience or results from using each method.
- 4
Mention any challenges faced during application and how they were overcome.
- 5
Highlight the overall benefits of each method in terms of durability and performance.
Example Answers
I have primarily used spray lining for large surface areas due to its efficiency and even coverage. In one project, it significantly reduced application time and provided a strong bond. I found hand application to be more effective for complex shapes and areas requiring precision, despite being more labor-intensive.
What industry standards do you follow in rubber lining applications?
How to Answer
- 1
Identify specific industry standards you are familiar with.
- 2
Mention certifications relevant to rubber linings, such as ASTM or ISO.
- 3
Discuss safety protocols and guidelines you adhere to.
- 4
Reference testing and quality assurance practices you implement.
- 5
Highlight your experience with industry-specific applications or materials.
Example Answers
I follow ASTM D2000 for rubber material specifications and ensure compliance with ISO 9001 for quality management in our installations.
What troubleshooting steps do you take when you encounter issues with rubber lining performance?
How to Answer
- 1
Identify the specific performance issue, such as leaks or adhesion failure.
- 2
Review the installation process and materials used for any compliance issues.
- 3
Check for environmental factors like temperature or chemical exposure that could affect performance.
- 4
Conduct visual inspections and tests to pinpoint failure locations.
- 5
Implement corrective actions and monitor the performance after adjustments.
Example Answers
First, I would identify the specific issue, whether it's a leak or adhesion problem. Then, I would review the installation process to ensure it followed guidelines. After that, I would check environmental conditions that might be affecting the rubber. Finally, I would perform inspections and make necessary corrections.
Don't Just Read Rubber Liner Questions - Practice Answering Them!
Reading helps, but actual practice is what gets you hired. Our AI feedback system helps you improve your Rubber Liner interview answers in real-time.
Personalized feedback
Unlimited practice
Used by hundreds of successful candidates
Situational Interview Questions
If you observe a leak in a rubber-lined tank shortly after installation, what steps would you take?
How to Answer
- 1
Immediately shut down the tank to prevent further leakage.
- 2
Identify the source and extent of the leak through visual inspection.
- 3
Document the leak conditions, including time, location, and potential causes.
- 4
Contact the installation team or manufacturer for advice on repairs.
- 5
Evaluate the need for replacement of the rubber lining if damage is severe.
Example Answers
First, I would shut down the tank to stop any further leakage. Then, I would inspect the area around the leak to determine its source, taking notes on the conditions observed. I would contact the installation team for guidance on the best repair method.
What would you do if a team member disagrees with your method of applying rubber lining?
How to Answer
- 1
Listen to their concerns and understand their perspective
- 2
Explain your method clearly and its benefits
- 3
Find common ground or compromises in the approach
- 4
Suggest a test or trial of both methods to compare results
- 5
Maintain a collaborative attitude to foster teamwork
Example Answers
I would first listen to my team member's concerns thoroughly to understand their viewpoint. Then, I would explain the benefits of my method. If we still disagree, I would propose that we test both approaches to see which works better in practice.
Don't Just Read Rubber Liner Questions - Practice Answering Them!
Reading helps, but actual practice is what gets you hired. Our AI feedback system helps you improve your Rubber Liner interview answers in real-time.
Personalized feedback
Unlimited practice
Used by hundreds of successful candidates
Imagine a client is unhappy with the rubber lining work. How would you address their concerns?
How to Answer
- 1
Listen carefully to the client's concerns without interrupting.
- 2
Acknowledge the issue and show empathy towards their feelings.
- 3
Ask clarifying questions to understand the specific problems they are facing.
- 4
Provide a solution or action plan to resolve the issue promptly.
- 5
Follow up with the client after addressing their concerns to ensure satisfaction.
Example Answers
I would first listen to the client to fully understand their concerns. I would acknowledge their feelings and express empathy. Then, I would ask specific questions to clarify the issues they have noted. After that, I would present a solution to fix the problem and ensure I follow up to check if they are satisfied.
How would you handle unexpected changes in project specifications when rubber lining?
How to Answer
- 1
Stay flexible and open to changes as they arise
- 2
Communicate promptly with the team and stakeholders about the changes
- 3
Assess the impact of the changes on the project timeline and resources
- 4
Propose solutions or alternatives to address the changes
- 5
Document all changes for future reference and project tracking
Example Answers
I would first assess the changes in specifications and communicate with the team to understand the implications. Then, I would evaluate our timeline and resources and suggest alternatives if needed, ensuring we stay on track. Lastly, I would document these changes for clarity moving forward.
If your project is falling behind schedule, what strategies would you implement to catch up?
How to Answer
- 1
Assess the current project status and identify key areas causing delays
- 2
Prioritize tasks based on urgency and impact on the overall project
- 3
Communicate with the team to gather input and possibly reallocate resources
- 4
Set realistic short-term goals to achieve quick wins and boost morale
- 5
Consider implementing overtime or additional shifts if necessary
Example Answers
I would first assess why the project is delayed and prioritize tasks that are critical to the project's success. Then, I would talk to the team to see if we can reallocate resources to these high-impact areas and set achievable short-term goals to get back on track.
What would you do if you discover a defect in the rubber lining after installation has begun?
How to Answer
- 1
Immediately assess the extent of the defect and its implications.
- 2
Communicate the issue to your supervisor and the team clearly.
- 3
Determine if the defect affects safety or functionality.
- 4
Develop a plan for correction, including repairing or replacing the defective area.
- 5
Document the findings and actions taken for future reference.
Example Answers
I would first assess how serious the defect is and whether it poses a risk. Then, I would inform my supervisor and the team about the situation. Depending on the severity, I would either repair the affected area or discuss reinstallation if necessary, and ensure everything is documented.
How would you motivate your team to ensure high-quality work in rubber lining?
How to Answer
- 1
Set clear quality standards and expectations for the team
- 2
Encourage open communication and feedback to share concerns
- 3
Recognize and reward quality workmanship and achievements
- 4
Provide training and development opportunities for skill enhancement
- 5
Foster a team-oriented environment with shared goals and support
Example Answers
I believe in setting clear quality standards that everyone understands. I make sure the team knows what is expected and regularly check in to provide support and encouragement. Recognizing team members for their hard work also keeps morale high and motivates them to strive for the best quality.
If you were to run out of rubber material halfway through a job, how would you manage the situation?
How to Answer
- 1
Assess the remaining project requirements and urgency
- 2
Communicate immediately with your supervisor or team
- 3
Check inventory for any available materials
- 4
Explore alternative suppliers for quick delivery
- 5
Document the situation and your resolution plan
Example Answers
First, I would evaluate how much rubber is left and what the project timeline looks like. Then, I would inform my supervisor right away to discuss options. If we have any rubber in stock, I would use that, or else I would contact our suppliers to see if they can deliver more quickly.
If you receive last-minute changes that affect the project timeline, how would you respond?
How to Answer
- 1
Stay calm and assess the changes objectively
- 2
Communicate promptly with stakeholders about the impact
- 3
Prioritize tasks to accommodate the new timeline
- 4
Develop a contingency plan to manage risks
- 5
Be flexible and open to collaboration for solutions
Example Answers
I would first take a moment to understand the changes and their implications. Then, I would quickly inform my team and stakeholders about the potential impact. After that, I'd reevaluate the project tasks, prioritize them, and propose a revised timeline or alternative strategies to ensure we meet our goals.
Rubber Liner Position Details
Recommended Job Boards
ZipRecruiter
www.ziprecruiter.com/Jobs/Rubber-LiningThese job boards are ranked by relevance for this position.
Related Positions
- Bag Liner
- Drawer Liner
- Carton Liner
- Tire Vulcanizer
- Plastic Roller
- Luggage Liner
- Edge Roller
- Tire Builder
- Tire Recapper
- Wire Roller
Similar positions you might be interested in.
Ace Your Next Interview!
Practice with AI feedback & get hired faster
Personalized feedback
Used by hundreds of successful candidates
Ace Your Next Interview!
Practice with AI feedback & get hired faster
Personalized feedback
Used by hundreds of successful candidates