Top 31 Tire Vulcanizer Interview Questions and Answers [Updated 2025]
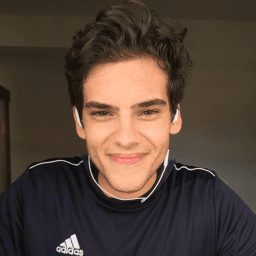
Andre Mendes
•
March 30, 2025
Preparing for a tire vulcanizer interview can be challenging, but with the right guidance, you can confidently tackle any question that comes your way. In this post, we cover the most common interview questions for the tire vulcanizer role, providing example answers and effective tips to help you impress potential employers. Dive in to enhance your interview skills and secure your next opportunity in the field!
Download Tire Vulcanizer Interview Questions in PDF
To make your preparation even more convenient, we've compiled all these top Tire Vulcanizerinterview questions and answers into a handy PDF.
Click the button below to download the PDF and have easy access to these essential questions anytime, anywhere:
List of Tire Vulcanizer Interview Questions
Behavioral Interview Questions
Can you describe a time when you worked as part of a team to accomplish a tire repair project?
How to Answer
- 1
Identify a specific project where teamwork was essential.
- 2
Highlight your role and contributions within the team.
- 3
Describe any challenges the team faced and how you worked together to overcome them.
- 4
Emphasize the end result and how it benefited the project or customer.
- 5
Use concrete examples to demonstrate effective communication and collaboration.
Example Answers
During a busy season, our team was tasked with repairing a large batch of truck tires. I took the lead on organizing the workflow and ensured everyone had clear tasks. We faced delays due to a shortage of materials, but I coordinated with the suppliers for quick delivery. We completed the repairs on time, which helped our client stay on schedule.
Tell me about a challenging tire vulcanization job you faced and how you overcame it.
How to Answer
- 1
Identify a specific job that was technically challenging.
- 2
Explain the problems you encountered during the vulcanization process.
- 3
Describe the solution you implemented to overcome these challenges.
- 4
Highlight any skills or tools you used that were pivotal in resolving the issue.
- 5
Share the outcome and what you learned from the experience.
Example Answers
I once had to vulcanize a tire that had a complex puncture. The issue was that the damage was near the sidewall, which made repairing it tricky. I first assessed the extent of the damage and decided to use a specialized patch and high-temperature vulcanizing adhesive. I carefully prepared the surface, applied the patch, and ensured it cured properly. The tire has been in use for over a year now without any issues, and I learned the importance of proper assessment.
Don't Just Read Tire Vulcanizer Questions - Practice Answering Them!
Reading helps, but actual practice is what gets you hired. Our AI feedback system helps you improve your Tire Vulcanizer interview answers in real-time.
Personalized feedback
Unlimited practice
Used by hundreds of successful candidates
Describe a situation where you had to adapt to new equipment or technology in your tire vulcanizing work.
How to Answer
- 1
Start by briefly explaining the new equipment or technology you encountered.
- 2
Describe the challenges you faced in adapting to it.
- 3
Explain the steps you took to learn and integrate the new technology.
- 4
Highlight any positive outcomes or improvements as a result of your adaptation.
- 5
Conclude with what you learned from the experience that can help in future adjustments.
Example Answers
In my previous job, we upgraded to a new high-speed tire curing machine. I faced a short learning curve as the control panel was different from what I was used to. I spent extra hours studying the manual and practiced under the supervision of a colleague. Within a week, I became proficient and was able to increase our production rate by 20%. This taught me the importance of flexibility and proactive learning.
How have you handled communication with customers regarding tire repairs and their expectations?
How to Answer
- 1
Listen carefully to customers' concerns and questions about their tire issues.
- 2
Clearly explain the repair process and what it entails to set accurate expectations.
- 3
Use layman's terms to ensure understanding, avoiding technical jargon.
- 4
Provide honest estimates of time and costs, and communicate any changes promptly.
- 5
Follow up with customers after the service to ensure satisfaction and address any further questions.
Example Answers
I always start by listening to the customer’s concerns, making sure I understand what issue they’re experiencing. Then, I explain the repair process in simple terms, so they know what to expect. I provide a clear estimate for time and cost, and I keep them updated if anything changes during the repair.
Give an example of a time when your attention to detail prevented a potential issue in tire maintenance.
How to Answer
- 1
Think of a specific incident that shows your attention to detail.
- 2
Describe the context briefly to set the scene.
- 3
Explain the specific action you took to address the detail.
- 4
Highlight the positive outcome due to your attention.
- 5
Keep it concise and focus on the impact of your actions.
Example Answers
During a routine tire inspection, I noticed irregular wear patterns on a customer's tire. I measured the tread depth and discovered it was uneven, potentially indicating a misalignment issue. I informed the customer and recommended an alignment check, which avoided a dangerous blowout later.
Can you discuss a time when you had to manage multiple tire repair projects at once? How did you prioritize?
How to Answer
- 1
Identify the key projects and their urgency
- 2
Evaluate the resources available like tools and time
- 3
Communicate with team members to understand their timelines
- 4
Focus on high-impact repairs first for customer satisfaction
- 5
Document your process to refine future prioritization
Example Answers
In my previous job, I handled three tire repairs at once. I assessed which cars were due for pickup and prioritized the repairs that would allow for quicker turnaround. I communicated with my team to ensure we were all aligned on the priorities, allowing us to complete the work efficiently without compromising quality.
Describe your experience leading a team of tire vulcanizers. What challenges did you face?
How to Answer
- 1
Start with a brief overview of your role and responsibilities.
- 2
Highlight specific challenges you encountered and how you addressed them.
- 3
Mention any successful outcomes from your leadership.
- 4
Use numbers or metrics to quantify improvements if possible.
- 5
Focus on teamwork and collaboration to achieve results.
Example Answers
In my previous position, I led a team of 5 tire vulcanizers. One major challenge was managing a high workload during peak seasons. I implemented a rotating schedule to ensure consistent output and kept morale high. As a result, we improved our turnaround time by 20%.
Can you provide an example of how you keep up with advancements in tire technology?
How to Answer
- 1
Mention specific sources of information like trade publications or online forums
- 2
Highlight any courses or certifications you've completed in tire technology
- 3
Discuss attendance at industry conferences or workshops
- 4
Share experiences collaborating with manufacturers or suppliers
- 5
Stay updated on new tools and equipment related to tire maintenance
Example Answers
I subscribe to Tire Review magazine and regularly read articles about new tire technologies and materials. I've also completed an online course on advanced tire maintenance.
What motivates you to maintain high standards in your tire vulcanizing work?
How to Answer
- 1
Reflect on your personal values related to quality and safety.
- 2
Consider the impact of your work on customer satisfaction.
- 3
Think about the technical challenges and how mastering them is rewarding.
- 4
Mention how high standards contribute to your professional reputation.
- 5
Discuss the importance of teamwork and supporting colleagues by setting an example.
Example Answers
I strive for high standards because I believe that quality work ensures the safety of the drivers. Every tire I vulcanize represents a commitment to safety and reliability, and I want customers to trust their vehicles.
Technical Interview Questions
What safety precautions do you take while working with vulcanizing equipment?
How to Answer
- 1
Always wear appropriate personal protective equipment, such as gloves and goggles.
- 2
Ensure that the workspace is clean and free from obstructions to prevent accidents.
- 3
Follow the operating manual and safety guidelines specific to the vulcanizing equipment being used.
- 4
Regularly inspect equipment for any signs of damage or wear before beginning work.
- 5
Be aware of emergency procedures and have an first aid kit accessible nearby.
Example Answers
I always wear gloves and safety goggles when using the vulcanizing equipment to protect against heat and chemical exposure. I also make sure my workspace is clean and organized to avoid tripping hazards.
What are the critical steps in the tire vulcanization process, and why is each step important?
How to Answer
- 1
Know the main steps: ingredient mixing, shaping, curing, and cooling.
- 2
Emphasize the purpose of each step in improving tire durability and performance.
- 3
Be clear about the materials involved and how they react during vulcanization.
- 4
Use terms specific to the process, like sulfur, heat, and pressure.
- 5
Also mention safety and quality control during the process.
Example Answers
The critical steps in the tire vulcanization process include mixing the raw materials, shaping the tire, curing it with heat and pressure, and then cooling it down. Each step is crucial: mixing ensures proper chemical reactions, shaping defines the tire's form, curing solidifies its structure with sulfur, and cooling helps retain that structure after vulcanization.
Don't Just Read Tire Vulcanizer Questions - Practice Answering Them!
Reading helps, but actual practice is what gets you hired. Our AI feedback system helps you improve your Tire Vulcanizer interview answers in real-time.
Personalized feedback
Unlimited practice
Used by hundreds of successful candidates
What tools and equipment are essential for tire vulcanizing, and how do you use them?
How to Answer
- 1
Start by listing common tools like tire levers and patches.
- 2
Explain the function of each tool in the vulcanizing process.
- 3
Mention safety equipment necessary for the job.
- 4
Discuss the importance of having quality vulcanizing compounds.
- 5
Highlight the need for a tire press or vulcanizing machine.
Example Answers
Essential tools for tire vulcanizing include tire levers for removing the tire, patches to cover punctures, and a vulcanizing machine to bond the materials. I use tire levers to safely detach the tire from the rim, apply patches with vulcanizing compound for a strong seal, and use the machine to ensure proper curing.
What industry standards do you follow in tire vulcanization, and how do you keep track of changes?
How to Answer
- 1
Mention specific industry standards, such as ASTM or ISO.
- 2
Discuss the importance of following safety regulations.
- 3
Explain how you stay updated through training and certifications.
- 4
Include methods for tracking industry changes like subscriptions to journals.
- 5
Highlight any professional networks you are part of for sharing best practices.
Example Answers
I follow ASTM D412 and ISO 37 standards for tire vulcanization to ensure quality and safety. I stay updated on changes through annual training sessions and by subscribing to industry publications.
Can you explain the different types of tire materials and how they affect the vulcanization process?
How to Answer
- 1
Identify common tire materials: natural rubber, synthetic rubber, fabric, and steel.
- 2
Explain how each material contributes to tire performance and durability.
- 3
Discuss the role of sulfur in vulcanization and how it interacts with different materials.
- 4
Mention the temperature and pressure required for effective vulcanization.
- 5
Relate the impact of material choice on the tire's handling, wear resistance, and environmental factors.
Example Answers
Common tire materials include natural rubber, synthetic rubber, and fabrics. Natural rubber enhances flexibility and grip, while synthetic rubber offers better wear resistance. During vulcanization, sulfur reacts with these materials at high temperatures to form cross-links, enhancing durability.
How would you troubleshoot a tire that is failing to hold pressure after vulcanization?
How to Answer
- 1
Inspect the tire for visible damage or punctures.
- 2
Check the bead area for proper sealing against the rim.
- 3
Examine the valve stem for leaks or damage.
- 4
Fill the tire with air and submerge in water to spot bubbles.
- 5
Verify that the correct vulcanization temperature and time were followed.
Example Answers
I would start by inspecting the tire for any visible punctures or cuts. Then, I'd check the bead area to ensure it is properly sealed to the rim. If necessary, I'd examine the valve stem for any leaks.
What repair techniques do you use for different types of tire damage?
How to Answer
- 1
Identify common types of tire damage such as punctures, sidewall damage, and tread separation.
- 2
Explain specific repair techniques like patching, plugging, or re-treading.
- 3
Emphasize safety and adherence to industry standards when making repairs.
- 4
Mention the importance of assessing the damage's severity before choosing a repair method.
- 5
Provide examples of scenarios where you successfully repaired tires using these techniques.
Example Answers
For punctures, I typically use a combination of plugging and patching, ensuring the puncture is no larger than a quarter inch. I always check the tire's inner surface for damage before proceeding.
What role does temperature play in the tire vulcanization process, and how do you monitor it?
How to Answer
- 1
Explain that temperature initiates and controls the chemical reactions necessary for vulcanization.
- 2
Mention the optimal temperature range for vulcanization and the consequences of too high or too low temperatures.
- 3
Discuss how you use thermocouples or temperature sensors to measure and monitor temperature during the process.
- 4
Emphasize the importance of maintaining consistent temperature for quality and safety.
- 5
Provide an example of a past experience where you successfully managed temperature during vulcanization.
Example Answers
Temperature is crucial in vulcanization as it activates the curing agents in the rubber. The optimal range is typically between 140°C to 160°C. I monitor this using thermocouples placed in the mold, ensuring consistent heat application to avoid under-curing or over-curing the tires.
What types of adhesives do you typically use in tire repairs, and how do you select the right one?
How to Answer
- 1
Mention specific types of adhesives like vulcanizing cement or rubber adhesive.
- 2
Explain criteria for selection such as temperature resistance and tire type.
- 3
Discuss safety considerations when handling adhesives.
- 4
Include a personal example of how you choose an adhesive for a specific job.
- 5
Highlight the importance of manufacturer recommendations for the adhesives.
Example Answers
I typically use vulcanizing cement for most tire repairs because it provides a strong bond that can withstand the heat and pressure of driving. When selecting an adhesive, I also consider the tire's condition and the environmental factors it will face.
What methods do you use to test the performance of vulcanized tires?
How to Answer
- 1
Discuss visual inspections for signs of damage or defects
- 2
Mention standardized tests like tire tread depth measurement
- 3
Include reference to performance tests such as braking and handling
- 4
Talk about environmental tests for heat and cold performance
- 5
Highlight the importance of customer feedback on tire performance
Example Answers
I begin with visual inspections to check for any visible damage or irregularities in the vulcanized tire. After that, I perform standardized tests like measuring tread depth to ensure it meets specifications. Additionally, I conduct performance tests such as braking distance and handling to assess the overall quality.
Don't Just Read Tire Vulcanizer Questions - Practice Answering Them!
Reading helps, but actual practice is what gets you hired. Our AI feedback system helps you improve your Tire Vulcanizer interview answers in real-time.
Personalized feedback
Unlimited practice
Used by hundreds of successful candidates
What routine maintenance practices do you follow for the vulcanizing machines?
How to Answer
- 1
Check daily for any leaks or wear on hoses and seals
- 2
Ensure the temperature and pressure gauges are calibrated regularly
- 3
Grease and lubricate moving parts at scheduled intervals
- 4
Clean the machine surfaces and components to prevent buildup
- 5
Follow the manufacturer’s maintenance schedule for inspections
Example Answers
I perform daily checks for leaks and ensure all hoses and seals are in good condition. I also calibrate the temperature and pressure gauges weekly.
How do you feel about using emerging technologies in tire vulcanization?
How to Answer
- 1
Highlight your openness to innovation and change
- 2
Mention specific technologies you are familiar with or interested in
- 3
Discuss the benefits of emerging technologies for efficiency and safety
- 4
Acknowledge the importance of training and adaptation
- 5
Express a willingness to learn and grow with new tools
Example Answers
I believe that emerging technologies can greatly enhance the efficiency of tire vulcanization. For example, automated curing systems can reduce time and improve consistency. I am excited to learn and adapt to these advancements.
Situational Interview Questions
If a customer is dissatisfied with a tire repair you completed, how would you handle the situation?
How to Answer
- 1
Listen to the customer's concerns without interrupting
- 2
Acknowledge their feelings and validate their dissatisfaction
- 3
Offer to inspect the tire again to identify any issues
- 4
Provide a solution, whether it’s a fix, replacement, or refund
- 5
Follow up with the customer after resolving the issue to ensure satisfaction
Example Answers
I would first listen to what the customer has to say without interrupting them. Acknowledging their frustration is important, then I would inspect the tire to see if there’s an issue and offer a proper solution, possibly a fix or even a refund if necessary.
What would you do if you discovered a defect in a tire that was about to be sold to a customer?
How to Answer
- 1
Immediately remove the defective tire from the sales area
- 2
Document the defect and communicate it to your supervisor
- 3
Assess the severity of the defect and determine if it can be fixed
- 4
Notify the customer about the issue if they have already been informed
- 5
Ensure proper disposal or return of the defective tire according to company policy.
Example Answers
I would take immediate action by removing the defective tire from sales, documenting the issue, and informing my supervisor to prevent it from reaching a customer.
Don't Just Read Tire Vulcanizer Questions - Practice Answering Them!
Reading helps, but actual practice is what gets you hired. Our AI feedback system helps you improve your Tire Vulcanizer interview answers in real-time.
Personalized feedback
Unlimited practice
Used by hundreds of successful candidates
Imagine a scenario where multiple tires arrive needing urgent repairs. How would you organize your workflow?
How to Answer
- 1
Assess the condition and priority of each tire based on urgency.
- 2
Group similar repairs together to streamline the process.
- 3
Allocate resources and tools needed for the most urgent tasks first.
- 4
Communicate with the team about progress and any adjustments needed.
- 5
Keep track of completed repairs to ensure nothing is overlooked.
Example Answers
I would first inspect all the tires to identify which ones are the most urgent, prioritizing those that are dangerous or critical. Then, I would group similar types of repairs together to work efficiently and communicate with my team to ensure everyone is aware of the priorities. After that, I would start with the highest priority repairs and track each completed job to maintain organization.
How would you address a situation where a teammate repeatedly produces subpar vulcanized tires?
How to Answer
- 1
Identify the specific issues with the vulcanized tires.
- 2
Have a private conversation with the teammate to discuss your concerns.
- 3
Offer to help them improve their skills or knowledge.
- 4
Suggest training or resources they could use.
- 5
Follow up to see if there has been improvement after discussing the issues.
Example Answers
I would first analyze the faults in the vulcanized tires and then talk to my teammate one-on-one to express my concerns. I would offer my assistance and suggest we review the vulcanizing process together.
If you run out of a key material needed for vulcanization, what steps would you take to continue operations?
How to Answer
- 1
Identify the specific material that is missing.
- 2
Check inventory for alternatives that can be used.
- 3
Contact suppliers to expedite delivery of the needed material.
- 4
Inform your supervisor about the situation and possible delays.
- 5
Plan workflow adjustments to minimize downtime during the interruption.
Example Answers
First, I would determine which specific material is out of stock. Then, I would check our inventory for any suitable alternatives that could be used in the vulcanization process. Simultaneously, I would contact our suppliers to see if they can deliver the required material urgently. I would keep my supervisor informed about the situation and adjust the workflow to limit operational disruptions.
What steps would you take immediately after a safety incident involving tire equipment?
How to Answer
- 1
Ensure safety first by checking for hazards and securing the area.
- 2
Administer first aid if anyone is injured and call emergency services if necessary.
- 3
Notify your supervisor and follow company protocols for reporting incidents.
- 4
Document the incident carefully, including what happened and conditions at the time.
- 5
Participate in a debrief to discuss what went wrong and identify preventive measures.
Example Answers
First, I would secure the area to ensure no one is in danger. Then, I would check if anyone needs medical help and call for assistance. After that, I would notify my supervisor and follow the reporting procedures. Finally, I would document everything and engage in a debrief with the team to prevent future incidents.
If you notice a co-worker struggling with a vulcanizing task, how would you assist them?
How to Answer
- 1
Approach the co-worker with a friendly attitude
- 2
Ask if they would like help before jumping in
- 3
Observe their technique to identify specific issues
- 4
Share your own tips or techniques that work for you
- 5
Encourage them with positive feedback as they improve
Example Answers
I would first ask my co-worker if they need help and listen to their concern. Then, I would observe their technique and suggest a few adjustments to improve the process. I would also share some of my own methods that have worked well for me.
How would you handle a situation where your workplace is not complying with safety regulations in tire handling?
How to Answer
- 1
Identify the specific safety regulations being ignored
- 2
Document the unsafe practices with notes or photos
- 3
Discuss the issue with your supervisor or safety officer
- 4
Suggest implementing a safety training session for staff
- 5
Prioritize employee safety and the importance of compliance
Example Answers
I would first identify which safety regulations are not being followed and document the specific practices. Then, I'd report the issue to my supervisor to ensure they are aware and can take appropriate action.
How would you diagnose why a customer’s tire keeps losing air after repair?
How to Answer
- 1
Ask the customer details about when the tire loses air.
- 2
Inspect the tire for visible signs of damage or debris.
- 3
Check the valve stem for leaks or damage.
- 4
Re-evaluate the patch or plug to ensure it's secure.
- 5
Test for air leaks using soapy water on the tire.
Example Answers
I would start by asking the customer when they notice the air loss and if it happens suddenly or gradually. Then, I would inspect the tire for obvious damages or any foreign objects penetrated the tire.
During busy periods, how do you ensure quality is not compromised in tire repairs?
How to Answer
- 1
Prioritize tasks to focus on essential quality checks
- 2
Utilize a checklist to maintain consistency in procedures
- 3
Communicate with team members to delegate effectively
- 4
Take brief breaks to maintain focus and avoid fatigue
- 5
Continuously review repairs to catch any potential issues early
Example Answers
During busy times, I prioritize the critical quality checks after each repair and ensure I follow my checklist to maintain standards. This helps prevent any errors despite the pressure.
Don't Just Read Tire Vulcanizer Questions - Practice Answering Them!
Reading helps, but actual practice is what gets you hired. Our AI feedback system helps you improve your Tire Vulcanizer interview answers in real-time.
Personalized feedback
Unlimited practice
Used by hundreds of successful candidates
Tire Vulcanizer Position Details
Recommended Job Boards
CareerBuilder
www.careerbuilder.com/jobs?keywords=Tire+VulcanizerZipRecruiter
www.ziprecruiter.com/Jobs/Tire-VulcanizerThese job boards are ranked by relevance for this position.
Related Positions
- Vulcanizer
- Tire Builder
- Tire Mounter
- Tire Groover
- Tire Recapper
- Rubber Liner
- Plastics Fabricator
- Fiberglass Laminator
- Sterilizer
- Wire Insulator
Similar positions you might be interested in.
Ace Your Next Interview!
Practice with AI feedback & get hired faster
Personalized feedback
Used by hundreds of successful candidates
Ace Your Next Interview!
Practice with AI feedback & get hired faster
Personalized feedback
Used by hundreds of successful candidates