Top 31 Vulcanizer Interview Questions and Answers [Updated 2025]
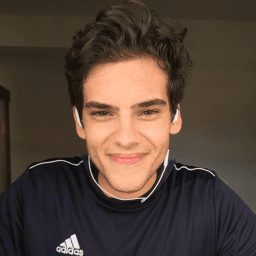
Andre Mendes
•
March 30, 2025
Preparing for a Vulcanizer job interview? This blog post is your ultimate guide to acing it! We've compiled the most common interview questions for the Vulcanizer role, complete with example answers and insightful tips to help you respond effectively. Dive in to boost your confidence and present yourself as the ideal candidate for this specialized position.
Download Vulcanizer Interview Questions in PDF
To make your preparation even more convenient, we've compiled all these top Vulcanizerinterview questions and answers into a handy PDF.
Click the button below to download the PDF and have easy access to these essential questions anytime, anywhere:
List of Vulcanizer Interview Questions
Behavioral Interview Questions
Can you describe a time when you had to troubleshoot a vulcanizing issue? What steps did you take?
How to Answer
- 1
Think of a specific instance where you faced a problem while vulcanizing.
- 2
Outline the issue clearly and mention how it impacted the process.
- 3
Describe the exact steps you took to analyze and solve the problem.
- 4
Highlight any tools or techniques you used during troubleshooting.
- 5
Conclude with the results or how the solution improved the outcome.
Example Answers
In my last job, I noticed that some vulcanized joints were not holding. I checked the temperature settings on the press and found they were too low. I adjusted the settings and retested the joints. After raising the temperature, the joints held firmly, and we had zero rejections that week.
Give an example of how you worked with a team to improve the vulcanization process.
How to Answer
- 1
Identify a specific issue in the vulcanization process.
- 2
Describe how you gathered team input to address the issue.
- 3
Explain the solution the team implemented together.
- 4
Highlight the impact of the changes on efficiency or quality.
- 5
Mention any collaboration tools or methods used.
Example Answers
In my previous role, our team noticed that the vulcanization process was taking too long due to inconsistent heating. We held a meeting where everyone shared their observations, and together we decided to optimize the oven settings. After implementing those changes, we reduced the time by 20% while also improving the consistency of the end product.
Don't Just Read Vulcanizer Questions - Practice Answering Them!
Reading helps, but actual practice is what gets you hired. Our AI feedback system helps you improve your Vulcanizer interview answers in real-time.
Personalized feedback
Unlimited practice
Used by hundreds of successful candidates
Describe a situation where you identified a safety risk in the vulcanization process. How did you handle it?
How to Answer
- 1
Think of a specific incident related to safety in vulcanization
- 2
Explain how you recognized the risk during the process
- 3
Detail the steps you took to address the risk
- 4
Include any collaboration with team members for safety
- 5
Mention the outcome or what you learned from the experience
Example Answers
In my previous job, I noticed that some vulcanizing machines were not properly calibrated, leading to uneven temperatures. I reported this to my supervisor and we immediately recalibrated the machines, reducing the risk of faulty products and ensuring safety in the workspace.
Tell me about a time when you had to adjust to a sudden change in production demands.
How to Answer
- 1
Describe the specific change in production demands.
- 2
Explain the immediate actions you took to adapt to the situation.
- 3
Highlight any teamwork or communication involved in handling the change.
- 4
Discuss the outcome of your actions and what you learned from the experience.
- 5
Keep it concise and focused on your role in the adjustment.
Example Answers
In my previous job, we suddenly received a large order that doubled our production target. I immediately organized a team meeting to assess our current workflow. We redistributed tasks and worked overtime to meet the demand. This collaboration allowed us to fulfill the order on time. I learned the importance of flexibility and teamwork in high-pressure situations.
Have you ever taken the initiative to suggest improvements in a vulcanization process? What was the outcome?
How to Answer
- 1
Think of a specific instance where you noticed an inefficiency in the vulcanization process.
- 2
Explain the improvement you suggested clearly and how you communicated it to your team or supervisor.
- 3
Describe the outcome of your suggestion, including any metrics or feedback if possible.
- 4
Emphasize teamwork and how collaboration contributed to the successful implementation of your suggestion.
- 5
Be honest if you haven't had such an experience, and discuss your willingness to learn and improve processes.
Example Answers
In my previous role, I noticed that the cooling time of the vulcanized rubber was longer than necessary. I suggested reducing the cooling period by calibrating the temperature settings on our machines. This led to a 15% reduction in the overall vulcanization cycle time, and management was pleased with the increased productivity.
Can you provide an example of how you effectively communicated with team members about a change in the vulcanization process?
How to Answer
- 1
Describe the change clearly and why it was necessary
- 2
Highlight how you informed the team, such as meetings or emails
- 3
Mention any tools or visuals you used to aid understanding
- 4
Explain how you encouraged feedback and questions
- 5
Share a successful outcome that resulted from the communication
Example Answers
I recently communicated a change to the vulcanization temperature. I organized a brief team meeting where I explained the reasons behind the change and shared a chart showing the new temperature settings. I also provided time for questions and addressed any concerns, which led to a smooth transition and improved product quality.
Describe a time when you mentored a newcomer in the vulcanization process. How did you ensure their understanding?
How to Answer
- 1
Start with a specific scenario where you mentored someone.
- 2
Explain the steps you took to teach them about vulcanization.
- 3
Mention how you checked their understanding throughout the process.
- 4
Highlight any specific techniques or tools you used to aid their learning.
- 5
Conclude with the outcome and how they improved under your guidance.
Example Answers
In my last job, I mentored a new employee in the vulcanization process by first demonstrating the entire procedure while explaining each step clearly. I then had them shadow me while asking questions. To ensure they understood, I quizzed them on the key steps and observed them as they practiced. By the end of the week, they were able to execute the process independently and even helped train others.
Can you give an example of how you responded to feedback from a supervisor on your vulcanizing work?
How to Answer
- 1
Think of a specific feedback instance you received.
- 2
Describe the feedback clearly and how you understood it.
- 3
Explain the steps you took to address the feedback.
- 4
Share the outcome of implementing the feedback.
- 5
Highlight what you learned from the experience.
Example Answers
I once received feedback that my vulcanizing temperatures were not consistently within the recommended range. I studied the temperature logs and adjusted my settings accordingly. After making these changes, my quality ratings improved significantly. I learned the importance of precision in our processes.
How do you set and achieve your professional goals in the field of vulcanization?
How to Answer
- 1
Identify specific and measurable goals related to your skills in vulcanization.
- 2
Develop a timeline for achieving each goal, such as completing a certification or mastering a technique.
- 3
Seek feedback from experienced vulcanizers to improve your skills and adjust your goals accordingly.
- 4
Stay updated with industry trends and technologies to refine your goals based on market demand.
- 5
Regularly review your progress and adjust your goals to ensure they remain relevant.
Example Answers
I set specific goals like obtaining a certification in tire vulcanization within six months. I break it down into weekly study sessions and practice on real tires. I also have a mentor who provides guidance.
Don't Just Read Vulcanizer Questions - Practice Answering Them!
Reading helps, but actual practice is what gets you hired. Our AI feedback system helps you improve your Vulcanizer interview answers in real-time.
Personalized feedback
Unlimited practice
Used by hundreds of successful candidates
What do you consider your biggest success in your vulcanization career so far?
How to Answer
- 1
Identify a specific achievement related to vulcanization.
- 2
Quantify the result if possible, such as percentage improvements or time saved.
- 3
Explain the impact of your success on the team or company.
- 4
Relate the success to your skills or qualities that helped you achieve it.
- 5
Keep it concise and focused on your role in the success.
Example Answers
My biggest success was reducing the vulcanization cycle time by 20%, which improved our production efficiency. I achieved this by streamlining the heating process and training my team on the new techniques, resulting in faster turnaround on orders.
Technical Interview Questions
What are the main chemical processes involved in vulcanization?
How to Answer
- 1
Focus on the role of sulfur in cross-linking rubber molecules.
- 2
Mention the heat and pressure involved in the process.
- 3
Explain the chemical reactions that improve elasticity and durability.
- 4
Discuss the types of vulcanization such as hot vs. cold vulcanization.
- 5
Use clear examples of the benefits of vulcanization in products.
Example Answers
The main chemical process in vulcanization involves the addition of sulfur to rubber, which creates cross-links between polymer chains. This process typically requires heat and pressure, leading to improved elasticity, strength, and overall durability of the rubber product.
What types of rubber compounds have you worked with and how do their properties affect the vulcanizing process?
How to Answer
- 1
Identify specific rubber compounds you have worked with, such as natural rubber, SBR, EPDM, or nitrile rubber.
- 2
Explain the unique properties of each compound, such as elasticity, resistance to heat, or chemical stability.
- 3
Discuss how these properties influence the vulcanizing temperature and time required.
- 4
Mention any challenges faced with specific compounds during the vulcanizing process.
- 5
Use examples to illustrate your experience and expertise.
Example Answers
I have worked primarily with SBR and EPDM. SBR has excellent wear resistance and allows for faster vulcanization times due to its balance of elasticity and heat stability. In contrast, EPDM requires higher temperatures for vulcanization due to its chemical structure but is great for outdoor applications because of its resistance to UV and ozone.
Don't Just Read Vulcanizer Questions - Practice Answering Them!
Reading helps, but actual practice is what gets you hired. Our AI feedback system helps you improve your Vulcanizer interview answers in real-time.
Personalized feedback
Unlimited practice
Used by hundreds of successful candidates
What types of vulcanizing equipment are you familiar with? Can you explain how they work?
How to Answer
- 1
List specific types of vulcanizing equipment you know.
- 2
Briefly describe the function and operation of each type.
- 3
Mention any brands or models you have used, if applicable.
- 4
Highlight any relevant experience with maintenance or troubleshooting.
- 5
Keep your explanations clear and concise, focusing on key aspects.
Example Answers
I am familiar with hydraulic vulcanizing presses which apply heat and pressure to rubber to cure it. They operate by using hydraulic fluid to exert force evenly across the rubber mold.
How does temperature affect the vulcanization process and what precautions should be taken?
How to Answer
- 1
Discuss the temperature range optimal for vulcanization of rubber.
- 2
Explain how too high or too low temperatures can affect properties of the material.
- 3
Mention the importance of using thermocouples or sensors during the process.
- 4
Highlight precautions such as avoiding thermal degradation and controlling the heating process.
- 5
Emphasize the need for proper equipment calibration to ensure uniform heating.
Example Answers
Temperature is crucial in vulcanization because it needs to be within a specific range, typically between 140 and 180 degrees Celsius. Too high can cause the rubber to degrade, while too low will result in incomplete curing. Precautions include using temperature sensors to monitor levels and ensuring consistent heating throughout the material.
What methods do you use to inspect the quality of vulcanized products?
How to Answer
- 1
Explain visual inspections for surface defects
- 2
Discuss the use of hardness testers for evaluation
- 3
Mention the importance of dimensional checks against specifications
- 4
Include testing for adhesion strength between layers
- 5
Describe any use of non-destructive testing methods
Example Answers
I use visual inspections to check for any surface defects, then I employ a hardness tester to ensure the vulcanized product meets the required hardness specifications. I also perform dimensional checks to confirm they adhere to the design specifications.
What tests do you perform to evaluate the hardness and durability of vulcanized rubber?
How to Answer
- 1
Mention standard tests like Shore hardness tests and tensile strength tests
- 2
Include methods for evaluating abrasion resistance
- 3
Discuss how heat aging tests indicate long-term durability
- 4
Refer to flexibility tests to check performance under stress
- 5
Emphasize that each test provides insights into specific properties of the rubber
Example Answers
I typically use Shore hardness tests to measure the rubber's hardness. For durability, I conduct tensile strength tests and abrasion resistance tests to evaluate wear over time. Additionally, I perform heat aging tests to see how the rubber performs under prolonged heat exposure.
Have you ever implemented new technology or methods in vulcanization? What was the effect?
How to Answer
- 1
Think of specific examples where you adopted new technology or methods.
- 2
Explain the technology or method clearly and why you chose it.
- 3
Describe the outcome and its impact on efficiency or product quality.
- 4
Use metrics or observations if possible to illustrate the effect.
- 5
Keep your answer focused and relevant to vulcanization.
Example Answers
At my last job, I introduced a new digital monitoring system that tracked temperature and pressure in the vulcanization process. This led to a 15% reduction in defects, as we could quickly adjust parameters in real-time.
What common problems can arise during the vulcanization process and how would you troubleshoot them?
How to Answer
- 1
Identify common vulcanization issues like incomplete curing, blistering, or discoloration.
- 2
Explain the root cause for each problem clearly.
- 3
Suggest specific troubleshooting steps for each issue.
- 4
Mention the importance of temperature and pressure control.
- 5
Highlight the need for regular equipment maintenance and calibration.
Example Answers
Incomplete curing can occur if the temperature is too low; I would check the temperature settings and increase it if necessary.
What industry standards do you follow in the vulcanization process?
How to Answer
- 1
Mention specific standards such as ASTM or ISO relevant to vulcanization.
- 2
Discuss the importance of temperature and pressure control during the process.
- 3
Highlight safety protocols you adhere to while working with chemicals.
- 4
Explain how you ensure quality by following manufacturing specifications.
- 5
Talk about the maintenance of equipment to meet industry standards.
Example Answers
I follow ASTM D3868 standards for the vulcanization process, ensuring precise temperature and pressure control for optimal results.
Describe how you determine the appropriate curing time for different rubber materials.
How to Answer
- 1
Identify the specific rubber type and its curing characteristics.
- 2
Refer to the manufacturer's curing guidelines for the material.
- 3
Consider the thickness and dimensions of the rubber part being cured.
- 4
Adjust curing time based on previous experience with similar materials.
- 5
Monitor the curing process and make adjustments if necessary.
Example Answers
I first identify the rubber type and check the manufacturer's curing specifications. Then, I assess the thickness of the rubber part, as thicker items generally need longer curing times. I monitor the process closely and adjust based on my past experiences with similar materials.
Don't Just Read Vulcanizer Questions - Practice Answering Them!
Reading helps, but actual practice is what gets you hired. Our AI feedback system helps you improve your Vulcanizer interview answers in real-time.
Personalized feedback
Unlimited practice
Used by hundreds of successful candidates
Situational Interview Questions
If you discover that a batch of vulcanized products has defects, what steps would you take to address the issue?
How to Answer
- 1
Identify the source of defects through inspection and testing
- 2
Isolate the defective products to prevent further distribution
- 3
Communicate the issue with your team and management promptly
- 4
Investigate the production process to determine what went wrong
- 5
Implement corrective actions and review quality control measures
Example Answers
First, I would inspect the batch to identify the defects and their causes. Then, I would isolate all defective products to prevent them from being shipped. After informing my supervisor, I would analyze the production process to find any underlying issues and work on corrective measures to ensure it doesn’t happen again.
How would you handle a situation where production quality does not meet company standards?
How to Answer
- 1
Identify the specific quality issues and gather data.
- 2
Communicate immediately with relevant team members.
- 3
Assess the root cause of the quality problem.
- 4
Implement corrective actions and monitor results.
- 5
Document the process and share lessons learned.
Example Answers
I would first gather data on the quality issues to understand what specifically is not meeting standards. Then, I would communicate with my team to discuss the problems. After assessing, if I find that the machines were not calibrated correctly, I would fix that, monitor production closely, and document our findings to prevent future issues.
Don't Just Read Vulcanizer Questions - Practice Answering Them!
Reading helps, but actual practice is what gets you hired. Our AI feedback system helps you improve your Vulcanizer interview answers in real-time.
Personalized feedback
Unlimited practice
Used by hundreds of successful candidates
Imagine you are facing a tight deadline with increasing production demands. How would you prioritize your tasks?
How to Answer
- 1
Assess the urgency and impact of each task
- 2
Communicate with your team about priorities
- 3
Break tasks into manageable parts
- 4
Focus on high-demand areas first
- 5
Stay flexible and adjust as needed
Example Answers
I would start by listing all tasks and their deadlines. Then, I would identify which tasks have the biggest impact on production and prioritize those. Team communication is key, so I would confirm priorities with my coworkers to ensure we are aligned.
If a team member is not following safety protocols, how would you address this issue?
How to Answer
- 1
Stay calm and approach the situation respectfully.
- 2
Address the team member privately to avoid embarrassment.
- 3
Explain the importance of safety protocols for everyone's well-being.
- 4
Ask if they need help understanding the protocols or following them.
- 5
Follow up to ensure the issue is resolved and encourage a culture of safety.
Example Answers
I would first calmly speak to the team member privately, explaining the importance of following safety protocols for their safety and the team's. I would ask if they need help understanding any specific protocols.
What would you do if a critical material needed for vulcanization is suddenly out of stock?
How to Answer
- 1
Assess the impact of the material shortage on production timelines
- 2
Identify alternative materials that can be used for vulcanization
- 3
Communicate the issue with the team and management quickly
- 4
Source the critical material from alternative suppliers if possible
- 5
Implement a contingency plan to minimize downtime
Example Answers
I would first evaluate how the shortage affects our production schedule. Then, I would look for any substitute materials that could be used in the process. It's also essential to inform my team and management of the situation to decide on the best course of action.
How would you handle a disagreement with a colleague regarding the best vulcanization method to use?
How to Answer
- 1
Listen carefully to your colleague's reasoning
- 2
Discuss the benefits and drawbacks of each method
- 3
Refer to any relevant data or past experiences
- 4
Seek common ground or a compromise solution
- 5
Stay respectful and professional throughout the discussion
Example Answers
I would start by listening to my colleague's points on their preferred method. Then, I would share my perspective on my choice, focusing on data that supports it. Together, we could examine the pros and cons of both methods and find a solution that incorporates the best aspects of each.
If a vulcanizing press fails during operation, what immediate actions would you take?
How to Answer
- 1
Stop the press immediately to prevent further damage.
- 2
Ensure the area is safe and clear of personnel.
- 3
Perform a quick visual inspection for obvious issues.
- 4
Notify your supervisor and maintenance team.
- 5
Document the failure and any observations for future reference.
Example Answers
I would first stop the vulcanizing press to avoid any further risk or damage. Then, I would clear the area to ensure safety before checking for any visible issues. After that, I would inform my supervisor and maintenance so they can help resolve the problem. Finally, I would document what happened to help prevent similar issues in the future.
How would you manage multiple vulcanization projects with overlapping deadlines?
How to Answer
- 1
Prioritize projects based on deadlines and importance.
- 2
Create a detailed schedule to allocate time for each project.
- 3
Communicate with team members to delegate tasks effectively.
- 4
Monitor progress regularly to make adjustments as needed.
- 5
Ensure quality standards are maintained despite tight timelines.
Example Answers
I would start by prioritizing the projects according to their deadlines and importance. Then, I would create a detailed schedule that allocates specific time slots for each project, ensuring that I stick to it. Communication with my team is vital, so I would delegate tasks based on each member's strengths. I would also monitor the progress of each project closely to make any necessary adjustments on the fly.
Imagine you are tasked with reducing production costs in the vulcanization process. What strategies would you consider?
How to Answer
- 1
Evaluate the current materials and consider using more cost-effective alternatives.
- 2
Assess the machinery for efficiency and potential upgrades or maintenance needs.
- 3
Implement process improvements to reduce cycle time and energy consumption.
- 4
Train staff on best practices to minimize waste and enhance productivity.
- 5
Negotiate with suppliers for bulk purchasing discounts or better terms.
Example Answers
I would start by reviewing the raw materials used in the vulcanization process and identify if there are lower-cost alternatives without sacrificing quality.
How would you respond if a customer complained about the quality of a vulcanized product?
How to Answer
- 1
Listen actively to the customer's complaint without interruption.
- 2
Acknowledge the issue and empathize with the customer.
- 3
Ask clarifying questions to understand the specifics of the complaint.
- 4
Offer a solution or explain the next steps to resolve the issue.
- 5
Follow up to ensure the customer is satisfied with the outcome.
Example Answers
I would start by listening to the customer and letting them express their concerns. Then, I'd acknowledge their frustration and ask questions to get more details about the issue. After that, I would offer a solution, such as a replacement or repair, and follow up afterward to ensure they are satisfied.
Don't Just Read Vulcanizer Questions - Practice Answering Them!
Reading helps, but actual practice is what gets you hired. Our AI feedback system helps you improve your Vulcanizer interview answers in real-time.
Personalized feedback
Unlimited practice
Used by hundreds of successful candidates
Vulcanizer Position Details
Recommended Job Boards
CareerBuilder
www.careerbuilder.com/jobs/vulcanizerZipRecruiter
www.ziprecruiter.com/Jobs/VulcanizerThese job boards are ranked by relevance for this position.
Related Positions
- Tire Vulcanizer
- Tire Builder
- Tire Mounter
- Rubber Liner
- Tire Groover
- Tire Recapper
- Plastics Fabricator
- Kneader
- Fiberglass Laminator
- Candle Maker
Similar positions you might be interested in.
Ace Your Next Interview!
Practice with AI feedback & get hired faster
Personalized feedback
Used by hundreds of successful candidates
Ace Your Next Interview!
Practice with AI feedback & get hired faster
Personalized feedback
Used by hundreds of successful candidates