Top 29 Fitter Interview Questions and Answers [Updated 2025]
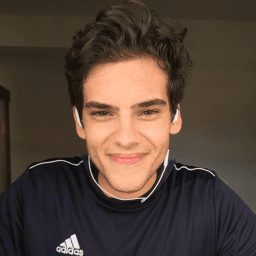
Andre Mendes
•
March 30, 2025
Preparing for a Fitter interview can be daunting, but we've got you covered. In this post, you'll find the most common interview questions for the Fitter role, complete with example answers and practical tips to help you respond confidently and effectively. Whether you're a seasoned professional or new to the field, our guide will help you impress your interviewers and secure that job.
Download Fitter Interview Questions in PDF
To make your preparation even more convenient, we've compiled all these top Fitterinterview questions and answers into a handy PDF.
Click the button below to download the PDF and have easy access to these essential questions anytime, anywhere: