Top 30 Fixture Maker Interview Questions and Answers [Updated 2025]
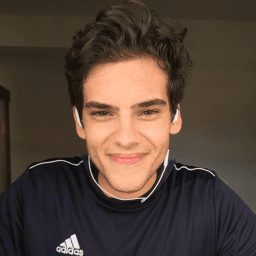
Andre Mendes
•
March 30, 2025
Preparing for a Fixture Maker interview? This blog post is your ultimate guide to acing it! Dive into the most common interview questions tailored for the Fixture Maker role, complete with example answers and expert tips on how to respond effectively. Whether you're a seasoned professional or a newcomer, this resource will equip you with the insights needed to impress your interviewers.
Download Fixture Maker Interview Questions in PDF
To make your preparation even more convenient, we've compiled all these top Fixture Makerinterview questions and answers into a handy PDF.
Click the button below to download the PDF and have easy access to these essential questions anytime, anywhere:
List of Fixture Maker Interview Questions
Behavioral Interview Questions
Can you describe a time when you had to collaborate with engineers or designers to create a fixture?
How to Answer
- 1
Choose a specific project as an example
- 2
Explain your role and contributions clearly
- 3
Highlight how you communicated with team members
- 4
Mention any challenges and how you overcame them
- 5
Discuss the positive outcome of the collaboration
Example Answers
In a recent project, I collaborated with engineers to design a fixture for a new product line. My role involved providing insights on material specifications and assembly processes. We held regular meetings to ensure alignment. We faced a challenge with alignment issues, but we developed a new prototype that addressed this. The final fixture improved production efficiency by 20%.
Tell me about a challenging fixture you worked on. What made it difficult and how did you address those challenges?
How to Answer
- 1
Identify a specific fixture and its purpose.
- 2
Explain the unique challenges faced during the project.
- 3
Describe your problem-solving approach clearly.
- 4
Highlight any collaboration with team members or stakeholders.
- 5
Discuss the outcome and any lessons learned.
Example Answers
I worked on a custom fixture for a new assembly line requiring precise alignments. The challenge was the tight deadlines combined with complex specifications. I organized a series of brainstorming sessions with my team to generate ideas and prototyping solutions. We completed the project on time and improved assembly efficiency by 20%.
Don't Just Read Fixture Maker Questions - Practice Answering Them!
Reading helps, but actual practice is what gets you hired. Our AI feedback system helps you improve your Fixture Maker interview answers in real-time.
Personalized feedback
Unlimited practice
Used by hundreds of successful candidates
Describe an experience where you had to adapt your techniques or methods during a project. What prompted the change?
How to Answer
- 1
Identify a specific project and describe the initial approach you used.
- 2
Explain the situation that required a change in methods or techniques.
- 3
Detail the new approach you implemented and the reasons for this shift.
- 4
Discuss the results or outcomes that followed your adaptation.
- 5
Reflect on what you learned from this experience and how it influences your work.
Example Answers
During a recent project to create a custom fixture for a client, I initially used standard machining techniques. However, midway through, I realized that the material we were using wasn't responding well to these methods, leading to flaws. I switched to a more specialized technique involving heat treatment, which improved the material’s workability. As a result, the final product exceeded client expectations and the project was completed ahead of schedule.
Have you ever had a disagreement with a team member regarding fixture design? How did you resolve it?
How to Answer
- 1
Start by briefly describing the disagreement.
- 2
Explain your perspective on the design issue clearly.
- 3
Discuss how you listened to the other person's viewpoint.
- 4
Highlight the resolution approach you took, such as collaboration or compromise.
- 5
Conclude with the positive outcome for the team or project.
Example Answers
In a recent project, I disagreed with a colleague about using a specific material for a fixture. I felt our choice could affect durability. I listened to their reasons and we discussed alternatives. We decided to prototype both materials to see which performed better. Ultimately, our collaboration led to a solution that satisfied both our concerns, improving the final product's quality.
Can you give an example of how you have mentored a junior technician or new team member in fixtures?
How to Answer
- 1
Identify a specific instance where mentorship took place
- 2
Describe the junior technician's initial skills and challenges
- 3
Explain your approach to mentoring, including techniques used
- 4
Highlight the positive outcome or improvement observed
- 5
Mention any feedback received from the mentee or team
Example Answers
I mentored a junior technician who struggled with CAD software for fixture design. I organized weekly sessions to teach basic functions and shared tips on creating efficient designs. Over time, they gained confidence and created their own successful fixture. They thanked me for making the learning process enjoyable.
Describe a situation when you had to meet a tight deadline for a fixture project. How did you manage your time?
How to Answer
- 1
Identify the specific project and deadline clearly
- 2
Explain the steps you took to prioritize tasks
- 3
Mention any tools or methods used to stay organized
- 4
Discuss how you communicated with team members or stakeholders
- 5
Reflect on the outcome and any lessons learned
Example Answers
In my last role, I had a week to create a complex fixture for a new product launch. I started by breaking the project into smaller tasks, prioritizing the design and material sourcing first. I used a project management tool to track progress and set daily goals. I held quick check-ins with my team to ensure alignment. We completed the project on time and received positive feedback from management.
Can you discuss a time when you implemented an innovative solution in your work as a fixture maker?
How to Answer
- 1
Choose a specific project that had a clear problem.
- 2
Highlight the innovative techniques or tools you employed.
- 3
Explain the outcome and benefits of your solution.
- 4
Connect your solution to improved efficiency or quality.
- 5
Keep your answer structured: situation, action, result.
Example Answers
In a previous project, I noticed our manual fixture adjustment process was slow and prone to error. I designed a modular fixture with quick-release clamps that allowed for faster adjustments. This innovation cut our adjustment time by 50%, leading to higher productivity and reduced setup errors.
Describe a scenario where your attention to detail made a significant difference in the fixture you created.
How to Answer
- 1
Think of a specific project where precision was critical.
- 2
Describe the problem you faced and how details influenced your solution.
- 3
Highlight the positive outcome that resulted from your attention to detail.
- 4
Use quantifiable results or feedback to strengthen your example.
- 5
Keep the focus on your personal contribution to the success.
Example Answers
In a recent project, I was tasked with creating a fixture for a complex assembly. I noticed that a minor misalignment could affect the overall product quality, so I double-checked measurements and adjusted the design accordingly. This attention to detail ensured that the fixture fit perfectly, leading to a 20% reduction in assembly errors.
Tell me about a time you identified and implemented a process improvement in fixture making.
How to Answer
- 1
Select a specific example from your experience.
- 2
Clearly outline the problem you faced.
- 3
Describe the process improvement you proposed.
- 4
Explain how you implemented the change and any tools you used.
- 5
Share the outcome and any positive impact on efficiency or quality.
Example Answers
In my previous role, I noticed that our fixture assembly time was delayed due to manual measurements. I suggested using digital calipers for more precise measurements. After implementing this change, we reduced assembly time by 20% and improved fixture accuracy.
Have you ever changed a fixture design based on feedback after testing? What was the outcome?
How to Answer
- 1
Describe the initial design and the feedback received.
- 2
Explain the specific changes you made to the fixture design.
- 3
Discuss how those changes impacted the performance or usability.
- 4
Highlight collaboration with team members during the process.
- 5
Conclude with the final results or lessons learned.
Example Answers
In a recent project, our initial fixture design struggled with part alignment. After testing, the operators highlighted this issue. I redesigned the alignment feature to provide better adjustability. As a result, the production time decreased by 15% and operator satisfaction improved significantly.
Don't Just Read Fixture Maker Questions - Practice Answering Them!
Reading helps, but actual practice is what gets you hired. Our AI feedback system helps you improve your Fixture Maker interview answers in real-time.
Personalized feedback
Unlimited practice
Used by hundreds of successful candidates
Technical Interview Questions
What types of materials have you worked with when creating fixtures? How do you choose the appropriate material for a job?
How to Answer
- 1
List specific materials like wood, metal, plastic, or composites you've used.
- 2
Explain the reasoning behind your material choices based on durability, cost, and application.
- 3
Mention any relevant projects where you successfully selected and implemented materials.
- 4
Discuss how you consider factors like weight, strength, and finish in your decisions.
- 5
Share your process for testing or prototyping materials before final selection.
Example Answers
I have worked with materials such as aluminum for its light weight and strength, along with plywood for its cost-effectiveness. For a recent project creating a fixture for a retail display, I chose metal due to the need for durability and aesthetic appeal.
Which CAD software are you proficient in for creating fixture designs? Can you describe a project where you used it extensively?
How to Answer
- 1
Identify the specific CAD software you are skilled in.
- 2
Mention the features of the software you leveraged for your project.
- 3
Choose a relevant project that showcases your design capabilities.
- 4
Explain your role in the project and the challenges you faced.
- 5
Highlight the outcomes or benefits of your design solutions.
Example Answers
I am proficient in SolidWorks. In a recent project, I designed a custom fixture for assembling electronic components. I utilized SolidWorks' parametric modeling features to create adjustable sections, which solved alignment issues. My design reduced assembly time by 20%.
Don't Just Read Fixture Maker Questions - Practice Answering Them!
Reading helps, but actual practice is what gets you hired. Our AI feedback system helps you improve your Fixture Maker interview answers in real-time.
Personalized feedback
Unlimited practice
Used by hundreds of successful candidates
What manufacturing processes do you find most important when making fixtures? Why?
How to Answer
- 1
Identify key manufacturing processes relevant to fixtures such as machining, welding, or additive manufacturing.
- 2
Explain the importance of precision and tolerances in fixture making.
- 3
Discuss how material selection impacts the effectiveness and durability of fixtures.
- 4
Mention how processes affect production efficiency and cost.
- 5
Highlight the role of assembly techniques in ensuring functionality.
Example Answers
I believe machining is crucial for achieving precise dimensions, which is essential for fit and function. Welding is also important for durability, especially in high-stress applications.
How do you ensure precision when creating fixtures? What tools or techniques do you use?
How to Answer
- 1
Use precise measuring tools like calipers and micrometers for accuracy.
- 2
Implement CAD software for detailed design and simulation.
- 3
Conduct thorough checks and adjustments throughout the fixture creation process.
- 4
Utilize jigs and templates to maintain consistency in repetitive tasks.
- 5
Develop a quality control plan including inspection and testing of the fixtures.
Example Answers
I ensure precision by using calipers and micrometers during measurements. I also leverage CAD software to design the fixtures, allowing for virtual simulations before physical creation. Regular adjustments and checks help maintain accuracy throughout the process.
What safety standards do you follow when designing and creating fixtures?
How to Answer
- 1
Mention specific safety standards relevant to the industry, such as ANSI or OSHA.
- 2
Explain how you incorporate risk assessments into your design process.
- 3
Discuss the importance of using appropriate materials and finishes.
- 4
Highlight your approach to testing and quality control measures.
- 5
Emphasize the role of ongoing training and updates on safety compliance.
Example Answers
I follow ANSI and OSHA standards when designing fixtures. I conduct risk assessments for each project to identify potential hazards and ensure appropriate materials are used. I also implement quality control measures that include testing the fixtures prior to final approval.
Can you explain your approach to troubleshooting issues with fixtures that do not work as intended?
How to Answer
- 1
Identify specific symptoms of the issue clearly
- 2
Check for common issues like alignment or wear and tear
- 3
Review design specifications and operational requirements
- 4
Use a systematic approach to isolate the problem
- 5
Document findings and potential solutions for future reference
Example Answers
First, I would identify the symptoms of the malfunction, ensuring I understand exactly what isn't working. Next, I would check for common issues such as alignment problems or signs of wear. If the fixture still doesn't work, I would review the design specifications to confirm it meets operational needs. I would isolate the problem systematically, and once resolved, I would document the issue and the solution for future reference.
What is your approach to documenting fixture designs and modifications? Why is it important?
How to Answer
- 1
Use clear diagrams and sketches to show designs.
- 2
Maintain a digital log for all modifications with dates.
- 3
Include material specifications and dimensions in documentation.
- 4
Review and update documents regularly to ensure accuracy.
- 5
Explain the importance of documentation for future reference and compliance.
Example Answers
I document fixture designs using detailed sketches and maintain a digital log for modifications. This allows easy tracking of changes and ensures that all specifications are up to date, which is crucial for quality control.
What assembly techniques do you prefer when putting together complex fixtures?
How to Answer
- 1
Focus on precision and attention to detail.
- 2
Utilize modular designs for easier assembly.
- 3
Incorporate jigs and fixtures to ensure consistency.
- 4
Use appropriate fasteners and adhesives for durability.
- 5
Consider assembly order to optimize efficiency.
Example Answers
I prefer using modular designs, as they allow for simpler assembly and adjustments. Incorporating jigs helps maintain precision, and I always pay attention to the assembly order for efficiency.
How do you evaluate the performance and usability of the fixtures you design?
How to Answer
- 1
Conduct regular testing with end-users to gather feedback on fixture usability
- 2
Analyze production efficiency metrics to see if fixtures improve workflow
- 3
Implement changes based on data collected from testing and user input
- 4
Consider material durability and ease of maintenance in evaluations
- 5
Use standardized criteria for assessing stability, accuracy, and ergonomic design
Example Answers
I evaluate the performance of my fixtures by conducting user testing sessions where we gather real-time feedback. I also track production metrics to ensure that the fixtures enhance overall efficiency.
What measurement techniques do you use to ensure the accuracy of your fixtures?
How to Answer
- 1
Discuss specific tools like calipers and micrometers for precise measurements.
- 2
Explain the use of gauge blocks for setting reference points.
- 3
Mention the importance of checking for squareness and flatness with a surface plate.
- 4
Talk about the role of 3D modeling and simulation in fixture design validation.
- 5
Highlight periodic calibration of measuring equipment to maintain accuracy.
Example Answers
I use calipers and micrometers for precise measurements, ensuring all components are within tolerance. Additionally, I rely on gauge blocks to set reference points, and I always check for squareness on a surface plate.
Don't Just Read Fixture Maker Questions - Practice Answering Them!
Reading helps, but actual practice is what gets you hired. Our AI feedback system helps you improve your Fixture Maker interview answers in real-time.
Personalized feedback
Unlimited practice
Used by hundreds of successful candidates
What quality control methods do you implement in your fixture making process?
How to Answer
- 1
Describe the inspection process for materials before use
- 2
Explain in-process checks during fixture assembly
- 3
Discuss final inspection methods and tools used
- 4
Emphasize the importance of feedback loops for continuous improvement
- 5
Mention any relevant quality standards or certifications followed
Example Answers
I implement a rigorous inspection of raw materials, checking for defects before they enter the production phase. During assembly, I carry out dimensional checks to ensure all components fit together as designed. Finally, I use calipers and gauges for a thorough final inspection and adhere to ISO 9001 standards to maintain high-quality output.
Situational Interview Questions
If you receive a last-minute request to alter a fixture design, how would you handle it?
How to Answer
- 1
Stay calm and assess the request's impact on the project timeline.
- 2
Communicate with your team to gather input on feasibility.
- 3
Prioritize the changes based on importance and urgency.
- 4
Document the changes clearly to avoid confusion later.
- 5
Be prepared to explain any potential trade-offs or risks involved.
Example Answers
I would first assess how the request impacts the timeline and resources. Then, I would discuss with the team to see if the change is feasible within our constraints. If it is, I would prioritize the change and document it fully to prevent any misunderstandings.
Imagine you have limited resources for a fixture project. How would you prioritize tasks and materials?
How to Answer
- 1
Identify the core objectives of the fixture project.
- 2
Evaluate the most critical tasks that have the highest impact.
- 3
Assess available materials and prioritize based on quality and necessity.
- 4
Consider alternatives and substitutions for high-cost materials.
- 5
Communicate clearly with the team about priorities and decisions.
Example Answers
I would start by defining the core objectives, then list tasks based on their impact. I'd assess the materials at hand, prioritizing those essential for functionality. Any high-cost items would be scrutinized for alternatives, ensuring the team is aligned on the priorities.
Don't Just Read Fixture Maker Questions - Practice Answering Them!
Reading helps, but actual practice is what gets you hired. Our AI feedback system helps you improve your Fixture Maker interview answers in real-time.
Personalized feedback
Unlimited practice
Used by hundreds of successful candidates
You are in a team meeting where everyone disagrees about a fixture design approach. How would you facilitate the discussion?
How to Answer
- 1
Acknowledge each person's input to show you value their perspective
- 2
Encourage open dialogue by asking clarifying questions
- 3
Identify common goals shared by the team to foster collaboration
- 4
Summarize key points of agreement and disagreement periodically
- 5
Propose a structured approach for evaluating each idea
Example Answers
I would start by acknowledging everyone's opinions and then ask clarifying questions to understand their perspectives better. Then, I would highlight our common goals to bring focus and suggest a structured process to evaluate each design option based on those goals.
If your fixture project is behind schedule, what steps would you take to bring it back on track?
How to Answer
- 1
Assess current progress and identify specific delays
- 2
Communicate clearly with the team and stakeholders about issues
- 3
Prioritize tasks and focus on critical path activities
- 4
Reallocate resources where possible to speed up key areas
- 5
Set new milestones to track the revised progress
Example Answers
I would analyze the reasons for the delay, discuss them with the team, and focus on the critical tasks that need to be accelerated. Additionally, I would seek to reprioritize and see if we can allocate more resources to critical areas.
How would you respond if a client was unhappy with a fixture you designed? What steps would you take to rectify the situation?
How to Answer
- 1
Listen actively to the client's concerns without interrupting.
- 2
Acknowledge their feelings and validate their feedback.
- 3
Ask clarifying questions to understand specific issues.
- 4
Propose solutions to address the concerns and involve the client in the decision.
- 5
Follow up after the changes to ensure satisfaction.
Example Answers
I would listen carefully to the client's concerns and ensure they feel heard. Then, I'd ask specific questions to clarify the issues they have with the fixture. After that, I would suggest potential adjustments we could make together and follow up to ensure they are satisfied with the changes.
If a senior designer provides critical feedback on your fixture design, how would you react?
How to Answer
- 1
Listen actively to the feedback without interrupting.
- 2
Ask clarifying questions to fully understand the concerns.
- 3
Acknowledge the feedback and express appreciation for their insights.
- 4
Reflect on the feedback and consider how it can improve your design.
- 5
Follow up with a revised design or solutions based on the feedback.
Example Answers
I would listen carefully to the feedback and take notes. I would then ask questions to ensure I understand their perspective. I value their experience and would appreciate their insights, reflecting on how I can incorporate their suggestions into my design.
You’re tasked with reducing the cost of a fixture project without sacrificing quality. How would you approach this?
How to Answer
- 1
Evaluate current material costs and explore alternative suppliers
- 2
Review design specifications for potential simplifications
- 3
Investigate manufacturing processes for efficiency improvements
- 4
Analyze labor costs and consider cross-training team members
- 5
Engage in open communication with stakeholders for collaborative cost-saving ideas
Example Answers
I would start by assessing the current materials used and research alternative suppliers that can provide similar quality at a lower cost. Additionally, I would simplify the design where possible without compromising functionality.
How would you integrate new technologies into your fixture manufacturing process?
How to Answer
- 1
Research the latest technologies relevant to fixture manufacturing.
- 2
Identify areas in your current process that could benefit from automation or improved accuracy.
- 3
Propose how you would test and implement new tools or software on a small scale first.
- 4
Consider the training needs of the team for new technology adoption.
- 5
Highlight the potential cost savings and efficiency improvements.
Example Answers
I would start by researching CAD software advancements that could improve our design process. Then, I would identify tasks that are repetitive and could be automated, like CNC milling setups. After testing a new tool on a small project, I would evaluate the outcomes and train the team accordingly.
If a client has specific requirements that are outside of standard protocols, how would you handle the project?
How to Answer
- 1
Listen carefully to the client's specific needs and document them.
- 2
Evaluate the feasibility of their requirements against your capabilities.
- 3
Communicate openly with the client about any potential challenges.
- 4
Propose solutions that align their needs with practical options.
- 5
Ensure you have a clear agreement on adjustments to the standard protocols.
Example Answers
I would start by actively listening to the client's specific requirements and documenting everything. After evaluating what’s feasible, I would discuss any potential challenges with them. Then, I would propose alternative solutions that align with their goals and get their agreement on any modifications to our standard procedures.
Fixture Maker Position Details
Recommended Job Boards
ZipRecruiter
www.ziprecruiter.com/Jobs/Fixture-MakerThese job boards are ranked by relevance for this position.
Related Positions
- Instrument Maker
- Machine Fitter
- Tool Machinist
- Model Maker
- Fabricator
- Foundation Maker
- Fly Maker
- Mat Maker
- Piece Maker
- Factory Manager
Similar positions you might be interested in.
Ace Your Next Interview!
Practice with AI feedback & get hired faster
Personalized feedback
Used by hundreds of successful candidates
Ace Your Next Interview!
Practice with AI feedback & get hired faster
Personalized feedback
Used by hundreds of successful candidates