Top 30 Factory Manager Interview Questions and Answers [Updated 2025]
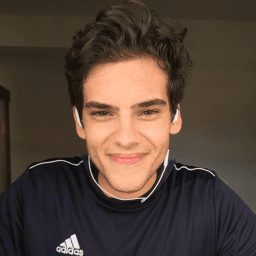
Andre Mendes
•
March 30, 2025
Navigating the path to becoming a successful Factory Manager begins with acing the interview. In this post, we delve into the most common interview questions for this pivotal role, providing you with insightful example answers and practical tips to respond effectively. Whether you're a seasoned professional or a newcomer, gain the confidence and knowledge to impress your potential employers and secure your dream position.
Download Factory Manager Interview Questions in PDF
To make your preparation even more convenient, we've compiled all these top Factory Managerinterview questions and answers into a handy PDF.
Click the button below to download the PDF and have easy access to these essential questions anytime, anywhere:
List of Factory Manager Interview Questions
Behavioral Interview Questions
Can you describe a time when you led a team to achieve operational efficiency improvements in a factory setting?
How to Answer
- 1
Choose a specific project with measurable outcomes
- 2
Describe your leadership role and the team's actions
- 3
Highlight the tools or methods used for improvement
- 4
Discuss the results and impact on the factory's operations
- 5
Conclude with lessons learned or how it influenced future practices
Example Answers
In my previous role, I led a project to reduce waste in our assembly line. By implementing lean principles and engaging the team in brainstorming sessions, we identified key areas for improvement. We introduced a new inventory tracking system that decreased excess stock by 30%, resulting in a 15% increase in output. This experience taught me the value of team collaboration in achieving efficiency.
Tell me about a situation where you had to resolve a conflict between team members on the factory floor. What was the outcome?
How to Answer
- 1
Use the STAR method: Situation, Task, Action, Result.
- 2
Describe the conflict clearly and concisely.
- 3
Explain your role in facilitating the resolution.
- 4
Highlight the positive outcome or lessons learned.
- 5
Keep it professional and focus on teamwork.
Example Answers
During a production shift, two operators had a disagreement over the proper way to handle a malfunctioning machine, which was causing delays. I stepped in and facilitated a discussion where each could share their perspective. I encouraged them to find common ground on a solution and, in the end, they agreed on a modified approach that combined their ideas. This not only resolved the conflict but improved our workflow.
Don't Just Read Factory Manager Questions - Practice Answering Them!
Reading helps, but actual practice is what gets you hired. Our AI feedback system helps you improve your Factory Manager interview answers in real-time.
Personalized feedback
Unlimited practice
Used by hundreds of successful candidates
Describe a challenging problem you faced in a factory setting and how you resolved it.
How to Answer
- 1
Identify a specific challenging problem you encountered.
- 2
Explain the context and impact of the problem on production.
- 3
Detail the steps you took to analyze and address the issue.
- 4
Highlight collaboration with your team or other departments if applicable.
- 5
Conclude with the outcome and any lessons learned from the experience.
Example Answers
In my previous role, we faced a significant delay in supply deliveries that impacted our production schedule. I first analyzed the supply chain process and identified that one vendor was consistently late. I communicated with the vendor to understand the issue and collaborated with my procurement team to find alternative suppliers. Ultimately, we reduced delays by 30% and improved our production timelines.
Give an example of how you managed to reduce operational costs while maintaining quality in production.
How to Answer
- 1
Identify a specific project or initiative you led.
- 2
Explain the methods used to assess and reduce costs.
- 3
Highlight how quality was monitored and maintained during the process.
- 4
Provide measurable outcomes to demonstrate success.
- 5
Conclude with how this experience impacted the team or company positively.
Example Answers
In my previous role, I led a project that introduced a lean manufacturing initiative. We identified excess inventory and reduced waste by 15%. We implemented new training for staff on efficiency while maintaining product standards. As a result, we saved 20% on operational costs and improved product quality metrics by 10%.
Can you discuss a time when your communication skills helped simplify a complex process for your team?
How to Answer
- 1
Identify a specific complex process you faced.
- 2
Explain how you broke down the process into simpler steps.
- 3
Describe the communication methods you used with your team.
- 4
Give a clear outcome that resulted from your actions.
- 5
Highlight any feedback from the team about the clarity you provided.
Example Answers
In my previous role, we had a complicated inventory management system. I created a visual flowchart that outlined each step of the process clearly. I presented this during a team meeting, which helped everyone understand their responsibilities better and reduced errors by 30%.
Describe how you have developed and motivated your factory team to ensure high performance.
How to Answer
- 1
Highlight specific training programs or skill development initiatives you implemented.
- 2
Discuss how you set clear performance goals and aligned them with team objectives.
- 3
Share examples of recognition or reward systems you established to motivate staff.
- 4
Explain how you encouraged open communication to foster a collaborative work environment.
- 5
Mention any team-building activities that improved morale and teamwork.
Example Answers
I implemented a training program where team members could develop their skills in specific machinery. This was complemented by monthly performance goals that aligned with our production targets. I also established a recognition program that rewarded employees for their contributions, which boosted morale significantly.
Describe a situation where you identified a significant risk in factory operations and how you mitigated it.
How to Answer
- 1
Start with a brief description of the risk you identified.
- 2
Explain how you assessed the potential impact of the risk.
- 3
Detail the specific steps you took to mitigate the risk.
- 4
Include any measures you implemented to prevent future occurrences.
- 5
Conclude with the positive outcome or lessons learned.
Example Answers
In my previous role, I noticed that equipment failure was a recurring issue due to lack of maintenance. I assessed that this could lead to significant production delays. I implemented a scheduled maintenance program which reduced machine downtime by 30%. As a result, we improved overall productivity and reduced repair costs.
Can you give an example of a difficult decision you had to make in a factory environment and the factors you considered?
How to Answer
- 1
Start with a specific situation that required a tough decision.
- 2
Clearly outline the factors you considered, such as safety, cost, and production efficiency.
- 3
Explain your decision-making process and any consultations with your team.
- 4
Discuss the outcome of your decision and any lessons learned.
- 5
Keep your response structured to highlight your critical thinking skills.
Example Answers
In my previous role, I had to decide whether to halt production due to a mechanical failure. I considered the potential delays, the safety of my team, and the financial impact on our clients. I consulted with my maintenance team, weighed the risks, and decided to stop production until the issue was fixed. This decision ultimately safeguarded our team and maintained our quality standards.
Tell me about a time you worked with a cross-functional team to improve factory operations.
How to Answer
- 1
Choose a specific project that involved different departments.
- 2
Describe your role and contributions clearly.
- 3
Highlight the challenge you aimed to solve.
- 4
Explain the outcome and benefits to operations.
- 5
Mention any skills or tools utilized during the project.
Example Answers
In my last role, I led a project to reduce downtime by collaborating with the maintenance and production teams. We identified key bottlenecks and implemented a new preventive maintenance schedule. As a result, we reduced downtime by 15% within three months, significantly improving overall productivity.
Technical Interview Questions
What methods do you typically use to analyze and optimize production processes in a factory?
How to Answer
- 1
Identify key performance indicators (KPIs) that reflect production efficiency.
- 2
Utilize data analysis tools like Six Sigma or Lean methodologies for process improvement.
- 3
Conduct regular audits and observations on the production floor to identify bottlenecks.
- 4
Engage employees for feedback on process challenges and suggestions for improvement.
- 5
Implement continuous improvement practices, such as Plan-Do-Check-Act cycles.
Example Answers
I typically analyze production processes by establishing KPIs like cycle time and yield rates. Using Lean methodologies, I identify waste and streamline workflows. I also involve my team in brainstorming sessions to find practical solutions for process optimization.
Explain your understanding of lean manufacturing principles and how you have applied them in your work.
How to Answer
- 1
Define lean manufacturing and its key principles such as waste reduction and continuous improvement.
- 2
Provide specific examples from your experience where you implemented lean principles.
- 3
Highlight the results of your lean initiatives, such as cost savings or efficiency gains.
- 4
Emphasize teamwork and how you engaged staff in lean practices.
- 5
Be clear and concise; avoid jargon that may confuse the interviewer.
Example Answers
Lean manufacturing focuses on eliminating waste and maximizing efficiency. In my previous role, we implemented 5S to organize our workspace, resulting in a 20% increase in productivity.
Don't Just Read Factory Manager Questions - Practice Answering Them!
Reading helps, but actual practice is what gets you hired. Our AI feedback system helps you improve your Factory Manager interview answers in real-time.
Personalized feedback
Unlimited practice
Used by hundreds of successful candidates
What are the key safety regulations you need to ensure compliance with, and how do you implement them?
How to Answer
- 1
Identify key safety regulations relevant to the factory, such as OSHA standards or ISO 45001.
- 2
Describe how you conduct regular training sessions for all employees.
- 3
Explain the implementation of safety audits and inspections to ensure compliance.
- 4
Discuss the importance of proper PPE and ensuring it's available and used correctly.
- 5
Mention how you foster a safety culture by encouraging reporting of unsafe conditions.
Example Answers
In my experience, key regulations include OSHA standards and ISO 45001. I ensure compliance by conducting regular training sessions for all employees to keep them informed and safe. Additionally, I implement safety audits to check adherence to these standards and ensure that we have proper PPE available for everyone.
How do you establish and maintain quality control standards in a factory environment?
How to Answer
- 1
Define clear quality standards for each product line
- 2
Implement regular training for employees on quality processes
- 3
Use data analytics to monitor quality metrics in real-time
- 4
Conduct frequent audits and inspections to ensure compliance
- 5
Incorporate feedback loops to continuously improve quality controls
Example Answers
I establish quality control standards by first defining specific criteria for each product line based on client expectations and industry benchmarks. I ensure that all team members are trained on these standards and incorporate regular audits to ensure adherence.
What experience do you have in managing supply chain logistics in a manufacturing setting?
How to Answer
- 1
Highlight specific roles with logistics responsibilities
- 2
Provide examples of key logistics processes managed
- 3
Discuss any supply chain software or tools used
- 4
Mention any improvements made to logistics operations
- 5
Emphasize collaboration with suppliers and distribution networks
Example Answers
In my previous role as a Production Supervisor, I managed logistics for our manufacturing line, coordinating daily shipments and inventory levels using SAP. This helped reduce lead times by 20%.
How do you ensure that production schedules and deadlines are consistently met?
How to Answer
- 1
Analyze past production data to identify patterns and potential bottlenecks
- 2
Set realistic and achievable deadlines based on resource availability
- 3
Implement regular monitoring of progress against the schedule
- 4
Communicate openly with team members and stakeholders about any issues
- 5
Use technology or software to assist in tracking and optimizing production schedules
Example Answers
I analyze past production data to pinpoint any recurring delays, allowing me to proactively address them. I also set deadlines that are realistic based on the resources we have.
Describe your approach to ensuring regular maintenance and upkeep of factory equipment.
How to Answer
- 1
Implement a preventive maintenance schedule covering all equipment.
- 2
Train staff on equipment usage and maintenance protocols.
- 3
Utilize a maintenance management software to track repairs and service.
- 4
Perform regular audits of equipment to identify and address issues early.
- 5
Encourage a culture of responsibility among team members for equipment care.
Example Answers
I implement a preventive maintenance schedule that ensures all equipment is regularly serviced and checked to prevent breakdowns. My team is trained to perform daily checks, and we use maintenance software to log and track any issues that arise.
What experience do you have with ERP systems, and how have you used them in managing factory operations?
How to Answer
- 1
Be specific about the ERP systems you have used
- 2
Highlight your role and responsibilities with the ERP
- 3
Discuss how you improved efficiency or solved problems using the system
- 4
Mention collaboration with other departments through the ERP
- 5
Share any measurable outcomes or successes achieved
Example Answers
In my previous role, I worked extensively with SAP ERP for managing inventory and production scheduling. I streamlined the order fulfillment process by using real-time data, which reduced our lead time by 20%.
How do you ensure efficient inventory management to avoid shortages or overstocking?
How to Answer
- 1
Utilize an automated inventory management system for real-time tracking
- 2
Conduct regular audits to reconcile physical stock with inventory records
- 3
Analyze historical sales data to forecast demand accurately
- 4
Implement a just-in-time inventory model to reduce excess stock
- 5
Maintain strong relationships with suppliers for reliable restocking
Example Answers
I use an automated system that tracks inventory levels in real time. This helps me see when stock is running low and allows for quick reordering. I also analyze historical sales data to forecast demand and avoid both shortages and overstocking.
What strategies have you implemented to ensure sustainable practices in a factory?
How to Answer
- 1
Highlight specific sustainability initiatives you've led
- 2
Mention metrics that demonstrate success
- 3
Include team involvement and training aspects
- 4
Discuss partnerships with suppliers for sustainable materials
- 5
Emphasize continuous improvement and feedback mechanisms
Example Answers
In my previous role, I implemented a waste reduction program that cut our scrap rate by 30% over two years. We achieved this by training staff on better material handling and recycling most of our byproducts.
Don't Just Read Factory Manager Questions - Practice Answering Them!
Reading helps, but actual practice is what gets you hired. Our AI feedback system helps you improve your Factory Manager interview answers in real-time.
Personalized feedback
Unlimited practice
Used by hundreds of successful candidates
Situational Interview Questions
Imagine a scenario where you have an unexpected machine breakdown during peak production. What steps would you take to address the situation?
How to Answer
- 1
Immediately assess the impact of the breakdown on production schedules.
- 2
Communicate with your team and relevant stakeholders about the issue.
- 3
Initiate the troubleshooting process to identify the cause of the breakdown.
- 4
Explore backup plans such as reallocating resources or adjusting workloads.
- 5
Report any required repairs to maintenance and establish a timeline for resolution.
Example Answers
First, I would assess how the breakdown affects our current output, then inform my team to avoid confusion. I would start troubleshooting to diagnose the issue while coordinating with maintenance. If needed, I'd adjust shifts or redistribute tasks to ensure other areas remain productive during repairs.
If you were faced with limited resources but a high production demand, how would you prioritize tasks?
How to Answer
- 1
Assess the production goals and deadlines clearly
- 2
Identify the most critical tasks that impact production output
- 3
Evaluate resource availability and allocate them strategically
- 4
Communicate priorities to the team to ensure alignment
- 5
Monitor progress and adjust priorities as needed to meet demands
Example Answers
I would first clarify the production goals and deadlines, then identify which tasks are critical for meeting those goals. I would allocate resources based on the impact of tasks on output and communicate these priorities to the team to keep everyone aligned.
Don't Just Read Factory Manager Questions - Practice Answering Them!
Reading helps, but actual practice is what gets you hired. Our AI feedback system helps you improve your Factory Manager interview answers in real-time.
Personalized feedback
Unlimited practice
Used by hundreds of successful candidates
You need to implement a new technology on the factory floor. How would you manage this change?
How to Answer
- 1
Assess the current workflow and identify areas for improvement with the new technology.
- 2
Engage and train employees early to gain their support and ensure smooth adoption.
- 3
Establish clear communication about the benefits of the new technology and how it impacts their work.
- 4
Implement the technology in phases to monitor progress and make adjustments as needed.
- 5
Collect feedback from the team during the rollout to address any issues promptly.
Example Answers
First, I would assess the current processes to see how the new technology could enhance production efficiency. Then, I would involve the employees by providing them with training sessions to highlight the benefits, addressing any concerns they might have. I would introduce the technology in phases, allowing for adjustments based on feedback.
If you discover that your current production capacity cannot meet forecasted demand, what actions would you take?
How to Answer
- 1
Analyze current production processes for inefficiencies
- 2
Consider scaling operations with overtime or additional shifts
- 3
Explore options for outsourcing or temporary staffing
- 4
Invest in equipment upgrades or maintenance if budget allows
- 5
Communicate with sales and planning teams to adjust forecasts
Example Answers
I would start by analyzing our existing production processes to identify any inefficiencies. Then, I would look at the possibility of adding overtime shifts to boost output in the short term.
If you were informed of a potential non-compliance issue, how would you address it?
How to Answer
- 1
Acknowledge the importance of compliance and safety.
- 2
Gather all relevant information about the potential issue.
- 3
Communicate with the team involved to understand the situation.
- 4
Develop a corrective action plan based on findings.
- 5
Monitor the implementation and follow up to ensure compliance.
Example Answers
I would start by confirming the details of the non-compliance issue and gather all relevant information from the team. Then, I would hold a meeting to discuss the issue and develop a corrective action plan that addresses the root cause. Finally, I would ensure that we implement the plan and monitor its effectiveness.
You see an opportunity to innovate a product line in the factory. How would you lead this initiative?
How to Answer
- 1
Identify the specific opportunity and its potential impact on the product line.
- 2
Engage with the team to gather insights and ideas for innovation.
- 3
Develop a clear plan that includes goals, resources, and timeline.
- 4
Communicate the vision and benefits of innovation to stakeholders.
- 5
Monitor progress and be open to feedback and adjustments.
Example Answers
First, I would analyze the current product line to identify areas for improvement, then I would hold a brainstorming session with my team to gather their ideas. Based on our discussions, I would create a step-by-step plan with clear goals and resources needed, ensuring everyone understands the benefits of the innovation.
How would you handle a situation where multiple employees call in sick on a critical production day?
How to Answer
- 1
Assess the immediate needs of production to understand critical tasks
- 2
Communicate with the team to gauge capability and redistribute workload
- 3
Consider temporary adjustments such as overtime or shift swaps
- 4
Explore options for hiring temporary staff if necessary
- 5
Implement a plan to improve employee attendance and morale moving forward
Example Answers
I would first review the production schedule and identify the critical tasks that need coverage. Then, I'd quickly communicate with the remaining team to see who can help cover the gaps, possibly by shifting roles or working overtime. If necessary, I would consider bringing in temporary workers to maintain productivity.
How would you handle a situation where you receive a last-minute large order that requires immediate fulfillment?
How to Answer
- 1
Assess current production capacity and resources immediately.
- 2
Communicate with the team to gather input and allocate tasks effectively.
- 3
Prioritize this order while maintaining quality standards.
- 4
Consider temporary adjustments like overtime or extra shifts if needed.
- 5
Keep the customer informed about progress and expected timelines.
Example Answers
I would first evaluate our current production capacity to see if we can accommodate the large order. I'd communicate with my team to redistribute tasks and prioritize the order while ensuring quality is not compromised. If necessary, I would arrange for overtime work to meet the deadline and keep the customer updated throughout the process.
A new process needs to be introduced, and the staff is unfamiliar with it. How do you ensure they are properly trained?
How to Answer
- 1
Assess the current skill level of the staff before training.
- 2
Create a detailed training plan with clear objectives.
- 3
Incorporate hands-on training and real-life scenarios.
- 4
Provide ongoing support and resources after the initial training.
- 5
Gather feedback to improve future training sessions.
Example Answers
First, I would assess the current skills of my team to identify knowledge gaps. Then, I would develop a training plan tailored to their needs, including hands-on workshops. I will offer resources like manuals and video tutorials, and after the training, I will be available for questions to ensure they feel confident in using the new process.
If a key supplier was unable to deliver materials on time, what steps would you take to address the shortfall?
How to Answer
- 1
Assess the severity of the impact on production timelines
- 2
Reach out to the supplier for updates and potential solutions
- 3
Explore alternative suppliers or backup options
- 4
Communicate with internal stakeholders about delays and solutions
- 5
Implement a contingency plan to minimize disruption
Example Answers
First, I would evaluate how much the delay affects our production schedule. Then, I would contact the supplier to understand the cause and discuss potential solutions. Meanwhile, I would look for alternative suppliers that could fulfill our needs quickly. After gathering this information, I would update my team and management about the situation and our plan of action.
Don't Just Read Factory Manager Questions - Practice Answering Them!
Reading helps, but actual practice is what gets you hired. Our AI feedback system helps you improve your Factory Manager interview answers in real-time.
Personalized feedback
Unlimited practice
Used by hundreds of successful candidates
You receive feedback that your factory’s performance metrics are declining. How would you investigate and respond to this issue?
How to Answer
- 1
Review current performance metrics and identify specific areas of decline
- 2
Conduct a root cause analysis involving key team members
- 3
Engage with operators on the floor for firsthand insights
- 4
Implement corrective actions based on findings and monitor their effectiveness
- 5
Communicate findings and strategies to all stakeholders to ensure transparency
Example Answers
I would first analyze the performance metrics to pinpoint the exact areas where we are declining. Then, I would gather a cross-functional team to conduct a root cause analysis, including operators who provide valuable insights. Based on the data, I would implement necessary changes and closely monitor the results before sharing updates with all stakeholders.
Factory Manager Position Details
Salary Information
Average Salary
$95,831
Source: Indeed
Recommended Job Boards
ManufacturingJobs.com
www.manufacturingjobs.com/jobs/factory-managerCareerBuilder
www.careerbuilder.com/jobs-factory-managerZipRecruiter
www.ziprecruiter.com/Jobs/Factory-ManagerThese job boards are ranked by relevance for this position.
Related Positions
Ace Your Next Interview!
Practice with AI feedback & get hired faster
Personalized feedback
Used by hundreds of successful candidates
Ace Your Next Interview!
Practice with AI feedback & get hired faster
Personalized feedback
Used by hundreds of successful candidates