Top 30 Manufacturing Director Interview Questions and Answers [Updated 2025]
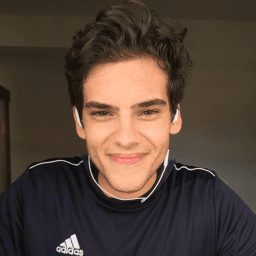
Andre Mendes
•
March 30, 2025
Navigating the competitive landscape of manufacturing leadership requires thorough preparation, especially when vying for a Manufacturing Director role. This blog post presents the most common interview questions tailored for aspiring directors in the manufacturing sector. Discover insightful example answers and valuable tips to craft your responses effectively, ensuring you leave a lasting impression and stand out as the ideal candidate. Dive in to elevate your interview readiness!
Download Manufacturing Director Interview Questions in PDF
To make your preparation even more convenient, we've compiled all these top Manufacturing Directorinterview questions and answers into a handy PDF.
Click the button below to download the PDF and have easy access to these essential questions anytime, anywhere:
List of Manufacturing Director Interview Questions
Behavioral Interview Questions
Can you describe a time when you had to lead a major change initiative in a manufacturing setting? What approach did you take and what were the results?
How to Answer
- 1
Choose a specific project or initiative you led.
- 2
Explain the need for change and your vision.
- 3
Describe the steps you took to implement the change.
- 4
Highlight how you engaged and motivated your team.
- 5
Share the tangible results of the initiative.
Example Answers
In my previous role, I led an initiative to implement Lean manufacturing practices. We faced long lead times, and after assessing the processes, I proposed a series of workshops. I engaged the team by encouraging their input and support. As a result, we reduced lead times by 30% and increased overall efficiency.
Describe a successful continuous improvement project you led. What was your strategy, and what were the outcomes?
How to Answer
- 1
Choose a specific project that had clear results
- 2
Explain your role and how you led the project
- 3
Discuss the strategies or methodologies used, like Lean or Six Sigma
- 4
Quantify the outcomes with metrics or data where possible
- 5
Reflect on any challenges faced and how you overcame them
Example Answers
I led a Lean initiative that reduced waste in our assembly line. My strategy involved mapping the processes, engaging the team in identifying inefficiencies, and implementing 5S practices. As a result, we improved production efficiency by 25% and reduced lead time by 30%.
Don't Just Read Manufacturing Director Questions - Practice Answering Them!
Reading helps, but actual practice is what gets you hired. Our AI feedback system helps you improve your Manufacturing Director interview answers in real-time.
Personalized feedback
Unlimited practice
Used by hundreds of successful candidates
How have you managed manufacturing budgets in past roles? Can you provide an example of how you successfully reduced costs?
How to Answer
- 1
Start with a clear overview of your budgeting responsibilities.
- 2
Include specific metrics or percentages to quantify cost reductions.
- 3
Mention tools or processes you implemented to track and manage budgets.
- 4
Provide a real example that demonstrates strategic cost-saving measures.
- 5
Highlight the impact of your cost reductions on overall production efficiency.
Example Answers
In my previous role as Manufacturing Manager, I oversaw a $5 million annual budget. By implementing a new inventory management software, we reduced waste by 15%, lowering our costs by $750,000 over two years. This also improved our production efficiency by 20%.
Describe a time when you improved the safety practices in your previous manufacturing environment. What steps did you take?
How to Answer
- 1
Choose a specific incident where safety was a concern.
- 2
Explain the analysis you conducted to identify safety issues.
- 3
Describe the specific measures you implemented to improve safety.
- 4
Share the results or feedback following your improvements.
- 5
Emphasize collaboration with the team during this process.
Example Answers
In my last role, I noticed that near-miss incidents were frequent in our assembly line. I conducted a safety audit and identified a lack of proper training. I organized workshops, updated our training materials, and instituted regular safety drills. As a result, we saw a 30% decrease in incidents over six months.
Tell me about a challenging problem that you faced in a manufacturing environment and how you resolved it.
How to Answer
- 1
Identify a specific problem that had a significant impact on production.
- 2
Explain the analysis process you used to understand the root cause.
- 3
Describe the steps you took to resolve the issue, including team involvement.
- 4
Highlight the outcome and any metrics that demonstrate success.
- 5
Keep your response structured, using the STAR method (Situation, Task, Action, Result).
Example Answers
In my previous role, we faced a major issue with product defects during a critical production run. After analyzing the defect rates, I discovered it was due to a faulty machine. I coordinated with the maintenance team to repair the machine and implemented a new quality control process. As a result, defect rates dropped by 50%, significantly improving our yield.
Give an example of how you dealt with a conflict between team members in a production line.
How to Answer
- 1
Identify the conflict clearly and its impact on production.
- 2
Listen to both parties to understand their perspectives.
- 3
Facilitate a discussion to find common ground.
- 4
Propose a solution and ensure both agree to it.
- 5
Follow up to ensure the solution is working.
Example Answers
In a previous role, I noticed two team members disagreeing on how to set up a machine. Their conflict was causing delays. I met with each of them separately to hear their viewpoints and then brought them together to discuss. We decided to test both methods for a week and the best one would be adopted. This resolved the conflict and improved our efficiency.
Can you provide an example of how you implemented a successful training program for manufacturing staff?
How to Answer
- 1
Identify a specific training need in your team
- 2
Describe the steps you took to develop the program
- 3
Mention how you involved staff in the training process
- 4
Highlight measurable outcomes or improvements from the program
- 5
Discuss how you gathered feedback for continuous improvement
Example Answers
In my previous role, we noticed a high error rate in assembly. I developed a hands-on training program where experienced staff mentored new hires. We saw a 30% reduction in errors within three months due to this structured approach.
Tell me about a time when you introduced an innovative solution that improved manufacturing processes or outcomes.
How to Answer
- 1
Choose a specific project where you implemented an innovative solution.
- 2
Use the STAR method: describe the Situation, Task, Action, and Result.
- 3
Focus on the innovative aspect and why it was necessary.
- 4
Quantify the results if possible to show impact.
- 5
Reflect on what you learned from the experience.
Example Answers
In my previous role, we faced inefficiencies with our assembly line. I introduced a real-time data tracking system that allowed us to monitor production metrics on the fly. This innovation led to a 20% increase in throughput and reduced downtime by 15%. I learned the importance of adapting technology to improve processes.
Technical Interview Questions
Can you explain the key principles of lean manufacturing and how you have implemented them?
How to Answer
- 1
Identify the core principles of lean manufacturing like value, waste reduction, continuous improvement, and empowering employees.
- 2
Prepare examples from your experience where you successfully applied these principles in manufacturing settings.
- 3
Focus on specific results or improvements you achieved through lean initiatives.
- 4
Be ready to discuss challenges you faced and how you overcame them during implementation.
- 5
Convey your understanding of both the theory and practice of lean manufacturing processes.
Example Answers
In my previous role, I led a team to implement value stream mapping to identify waste. We reduced lead time by 20% by eliminating unnecessary steps in our assembly process.
What is Six Sigma, and how have you applied its methodologies in your previous roles?
How to Answer
- 1
Define Six Sigma clearly in your own words
- 2
Mention specific methodologies like DMAIC or DMADV
- 3
Provide a concrete example of a project where you used Six Sigma
- 4
Explain the impact that applying Six Sigma had on your project or the organization
- 5
Tie your experience with Six Sigma to the requirements of the Manufacturing Director role
Example Answers
Six Sigma is a data-driven approach to eliminate defects and improve processes. In my last role, I used the DMAIC methodology to reduce production defects by 30% in six months. I led a cross-functional team to identify root causes and implement changes, which significantly improved our product quality and customer satisfaction.
Don't Just Read Manufacturing Director Questions - Practice Answering Them!
Reading helps, but actual practice is what gets you hired. Our AI feedback system helps you improve your Manufacturing Director interview answers in real-time.
Personalized feedback
Unlimited practice
Used by hundreds of successful candidates
How do you ensure that the supply chain is efficient and aligns with production needs?
How to Answer
- 1
Analyze production forecasts and adjust supply chain strategies accordingly
- 2
Establish strong communication channels with suppliers for real-time updates
- 3
Invest in technology for inventory management and demand forecasting
- 4
Regularly review and optimize logistics and transportation processes
- 5
Implement a feedback loop between production and supply chain teams
Example Answers
I analyze production forecasts to align supply chain strategies, maintaining open communication with suppliers for timely updates.
What quality control processes have you implemented to ensure product standards are met?
How to Answer
- 1
Identify specific quality control methods you have implemented.
- 2
Discuss measurable outcomes or improvements from the processes.
- 3
Explain how these processes integrate with manufacturing operations.
- 4
Highlight teamwork and training aspects involved in quality control.
- 5
Mention any industry standards or certifications related to quality.
Example Answers
In my previous role, I implemented a Total Quality Management system which included regular audits and real-time monitoring of production metrics. This improved product consistency by 20%.
Have you worked with ERP systems in manufacturing? Which systems are you familiar with, and how have you used them to improve operations?
How to Answer
- 1
Identify specific ERP systems you have used in the past.
- 2
Explain how you utilized these systems to streamline processes.
- 3
Provide examples of measurable outcomes from your use of ERP.
- 4
Mention any collaboration with other departments using the ERP.
- 5
Highlight skills in evaluating and implementing ERP solutions.
Example Answers
In my previous role, I worked extensively with SAP ERP. I used it to integrate inventory management with production scheduling, which reduced downtime by 15%. Furthermore, I led training sessions for staff, ensuring everyone was equipped to utilize the system effectively.
What is your experience with manufacturing automation, and how have you used technology to improve production processes?
How to Answer
- 1
Identify specific automation technologies you have worked with
- 2
Explain a successful project where you implemented automation
- 3
Describe measurable improvements in efficiency or cost savings
- 4
Mention collaboration with IT or engineering teams
- 5
Showcase your ability to train staff on new technologies
Example Answers
In my previous role, I led the automation of our assembly line using robotic arms, which reduced labor costs by 25% and increased production speed by 30%.
How do you approach production scheduling to maximize efficiency?
How to Answer
- 1
Analyze historical data to identify peak production times.
- 2
Implement a just-in-time inventory system to reduce waste.
- 3
Utilize scheduling software for optimal resource allocation.
- 4
Communicate efficiently with all departments to align schedules.
- 5
Continuously monitor and adjust schedules based on real-time data.
Example Answers
I analyze historical production data to identify patterns and peak times, allowing me to better allocate resources. I also use scheduling software that helps balance workloads across shifts.
Can you discuss a method you've used to optimize manufacturing processes?
How to Answer
- 1
Identify a specific process you improved.
- 2
Quantify the improvements with metrics like time saved or cost reduced.
- 3
Explain the steps you took to implement the changes.
- 4
Highlight any tools or techniques used, like Lean or Six Sigma.
- 5
Mention the impact on the team and production outcomes.
Example Answers
In my previous role, I optimized our assembly line by implementing a Lean approach. We reduced cycle time by 20%, increasing throughput by 15%. I led the team in value stream mapping to identify waste and streamlined processes, which significantly improved production efficiency.
How do you manage and plan for manufacturing capacity to meet demand without overextending resources?
How to Answer
- 1
Analyze historical demand data to forecast future needs
- 2
Develop flexible manufacturing strategies to adjust capacity
- 3
Implement lean manufacturing principles to increase efficiency
- 4
Regularly communicate with sales and inventory teams
- 5
Conduct periodic capacity reviews to identify shortfalls
Example Answers
I start by analyzing historical data to identify trends and forecast demand. I then develop flexible strategies, such as scheduling overtime only when necessary. By implementing lean principles, I ensure we maximize efficiency without overextending resources.
What steps do you take to ensure manufacturing compliance with industry standards and regulations?
How to Answer
- 1
Stay updated on relevant regulations and industry standards.
- 2
Implement a robust training program for all employees on compliance topics.
- 3
Conduct regular audits and assessments of manufacturing processes.
- 4
Establish clear communication channels for reporting compliance issues.
- 5
Use metrics to measure compliance and improve continuously.
Example Answers
I regularly review the latest industry regulations and ensure my team is trained on compliance. We conduct quarterly audits to identify any gaps and communicate openly about compliance challenges.
Don't Just Read Manufacturing Director Questions - Practice Answering Them!
Reading helps, but actual practice is what gets you hired. Our AI feedback system helps you improve your Manufacturing Director interview answers in real-time.
Personalized feedback
Unlimited practice
Used by hundreds of successful candidates
Situational Interview Questions
Imagine there is a significant recall due to a defect in the product. How would you handle the situation to minimize impact?
How to Answer
- 1
Immediately communicate with stakeholders and inform them of the recall.
- 2
Assess the scope of the defect and gather relevant data quickly.
- 3
Develop a clear recall strategy, including logistics for retrieving the products.
- 4
Implement corrective actions to prevent future defects and enhance quality control.
- 5
Monitor the situation actively and provide updates to customers and the team.
Example Answers
I would first inform all stakeholders about the recall to ensure transparency. Then, I’d evaluate the scope of the product defect and collect necessary details for effective recovery. Next, I would create a thorough recall plan, including how to retrieve the affected products efficiently. It’s crucial to implement corrective measures to prevent similar issues later. I would keep communication ongoing with customers throughout the process.
If you have limited resources and a high-demand product, how would you prioritize production elements?
How to Answer
- 1
Assess the demand to understand which product variants need to be produced first.
- 2
Evaluate existing inventory levels to determine what can be fulfilled immediately.
- 3
Identify critical resource constraints that impact production capacity.
- 4
Implement a production schedule that focuses on high-priority items while maintaining quality.
- 5
Communicate transparently with stakeholders about production limitations and timelines.
Example Answers
I would start by analyzing the current demand data to identify which product variants are most popular. Next, I would check our inventory levels to see how quickly we can fulfill requests for those products. I would prioritize production based on this analysis, ensuring we use our limited resources efficiently.
Don't Just Read Manufacturing Director Questions - Practice Answering Them!
Reading helps, but actual practice is what gets you hired. Our AI feedback system helps you improve your Manufacturing Director interview answers in real-time.
Personalized feedback
Unlimited practice
Used by hundreds of successful candidates
A portion of your team is demotivated due to overtime demands for a project. How would you address their concerns?
How to Answer
- 1
Acknowledge the team's concerns and listen actively to their feedback.
- 2
Communicate the reasons for the overtime and project importance clearly.
- 3
Discuss potential solutions, such as flexible hours or additional time off.
- 4
Consider recognizing and rewarding extra effort to boost morale.
- 5
Follow up with the team regularly to reassess their feelings and workloads.
Example Answers
I would first hold a team meeting to listen to their concerns about overtime demands. Then, I would explain the project's importance and see if we can implement flexible hours or compensatory time off. Recognizing their extra efforts with small rewards can also help re-engage them.
You need to negotiate a contract with a key vendor under tight budget constraints. What approach would you take?
How to Answer
- 1
Prepare by understanding the vendor's needs and constraints.
- 2
Identify areas where you can compromise without impacting quality.
- 3
Communicate your budget constraints clearly and respectfully.
- 4
Explore alternative solutions or services the vendor could offer.
- 5
Build a relationship and trust with the vendor for future negotiations.
Example Answers
I would begin by researching the vendor thoroughly to understand their pressures and how they align with my goals. Then, I would clearly outline our budget constraints while emphasizing our long-term partnership, seeking creative solutions that benefit both parties.
A new technology could potentially triple production but requires substantial investment. How would you evaluate whether to implement it?
How to Answer
- 1
Conduct a cost-benefit analysis to assess potential ROI
- 2
Consider the risk factors and technology reliability
- 3
Gather input from production and financial teams
- 4
Evaluate market demand and capacity needs
- 5
Develop a pilot program to test the technology before full implementation
Example Answers
I would start with a cost-benefit analysis to see if the ROI justifies the investment. Then, I would assess the risks involved and consult with my production and finance teams to get their input. It’s also important to analyze market demand before making a decision.
How would you set and communicate production goals during a company-wide initiative to increase output by 20%?
How to Answer
- 1
Define clear and measurable goals tied to the 20% increase.
- 2
Communicate goals to all levels, ensuring everyone understands their role.
- 3
Use visual aids like dashboards to track progress and visibility.
- 4
Encourage feedback loops to address concerns and adjust strategies.
- 5
Celebrate small wins to maintain motivation and focus on the end goal.
Example Answers
I would start by breaking down the 20% increase into specific targets for each department, ensuring they align with our overall strategy. Then, I would hold a company-wide meeting to explain these goals, using presentations and visuals to ensure clarity. Regular updates through dashboards would help everyone track progress and feel involved.
Suppose you're asked to reduce operational costs by 10% without sacrificing quality. What strategies would you consider?
How to Answer
- 1
Analyze current operational expenses to identify the highest costs.
- 2
Implement lean manufacturing techniques to eliminate waste.
- 3
Negotiate better terms with suppliers to reduce material costs.
- 4
Invest in technology that increases efficiency and lowers labor costs.
- 5
Train staff on best practices to enhance productivity and reduce errors.
Example Answers
I would start by analyzing our current expenses to identify where we can cut costs. I would then implement lean manufacturing techniques to streamline processes and eliminate waste. Additionally, I would negotiate with suppliers for better pricing on materials.
How would you ensure compliance with new industry regulations that require changes in manufacturing processes?
How to Answer
- 1
Identify key regulations and their implications for current processes
- 2
Engage cross-functional teams to discuss necessary changes
- 3
Develop a clear implementation plan with timelines and responsibilities
- 4
Provide training and resources to staff to adapt to new regulations
- 5
Establish a monitoring system to ensure ongoing compliance
Example Answers
To ensure compliance with new regulations, I would first assess the specific changes needed by reviewing the regulations closely. Then, I'd coordinate a meeting with the production and quality assurance teams to ensure everyone understands the implications. After that, I'd create a step-by-step implementation plan, assign roles, and set deadlines to keep us on track.
There's a delay in product launch due to cross-functional issues. How would you facilitate better collaboration?
How to Answer
- 1
Identify key stakeholders in affected teams and initiate a meeting.
- 2
Encourage open communication to surface specific collaboration challenges.
- 3
Use structured problem-solving techniques to address issues collectively.
- 4
Establish clear roles and responsibilities for all teams involved.
- 5
Set up regular follow-up check-ins to monitor progress and maintain accountability.
Example Answers
I would start by organizing a meeting with all key stakeholders to discuss the issues. By facilitating an open conversation, we can identify the root causes of the delays and collaboratively develop a plan to address them. Clearly defining roles and responsibilities will ensure everyone knows their contribution.
Describe how you would handle an unplanned and urgent shutdown of your production facility.
How to Answer
- 1
Assess the immediate cause of the shutdown and gather facts.
- 2
Communicate promptly with all stakeholders including employees and management.
- 3
Implement emergency protocols to ensure safety and compliance.
- 4
Develop a plan for quick resolution and restarting production.
- 5
Review the incident to prevent future occurrences and improve processes.
Example Answers
First, I would quickly assess the cause of the shutdown by gathering facts from the team. Then, I would communicate with all stakeholders to ensure everyone is aware of the situation. I would activate our emergency protocols to ensure safety, and then work on a plan to resolve the issue quickly. After everything is back to normal, I would review the incident to improve our processes and prevent future shutdowns.
Don't Just Read Manufacturing Director Questions - Practice Answering Them!
Reading helps, but actual practice is what gets you hired. Our AI feedback system helps you improve your Manufacturing Director interview answers in real-time.
Personalized feedback
Unlimited practice
Used by hundreds of successful candidates
How would you use data analytics to identify and solve production bottlenecks?
How to Answer
- 1
Identify key performance indicators relevant to production efficiency.
- 2
Utilize data visualization tools to highlight trends and patterns.
- 3
Segment data by shifts, machines, or products to pinpoint specific issues.
- 4
Implement predictive analytics to anticipate and mitigate potential bottlenecks.
- 5
Regularly review and adjust strategies based on real-time data feedback.
Example Answers
I would first define key performance metrics, like cycle time and throughput. Then I would use dashboards to visualize these metrics and identify outliers. By segmenting the data by machine, I could find which ones consistently underperform and address maintenance issues there.
Manufacturing Director Position Details
Salary Information
Recommended Job Boards
CareerBuilder
www.careerbuilder.com/jobs/director-of-manufacturingThese job boards are ranked by relevance for this position.
Related Positions
Ace Your Next Interview!
Practice with AI feedback & get hired faster
Personalized feedback
Used by hundreds of successful candidates
Ace Your Next Interview!
Practice with AI feedback & get hired faster
Personalized feedback
Used by hundreds of successful candidates