Top 30 Plant General Manager Interview Questions and Answers [Updated 2025]
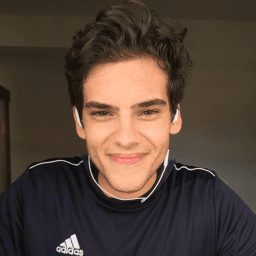
Andre Mendes
•
March 30, 2025
Navigating the competitive landscape of a Plant General Manager interview requires more than just industry knowledge; it demands strategic preparation. In this post, we explore the most common interview questions faced by aspiring Plant General Managers, providing you with insightful example answers and practical tips on how to respond effectively. Equip yourself with the tools to confidently tackle your next interview and make a lasting impression.
Download Plant General Manager Interview Questions in PDF
To make your preparation even more convenient, we've compiled all these top Plant General Managerinterview questions and answers into a handy PDF.
Click the button below to download the PDF and have easy access to these essential questions anytime, anywhere:
List of Plant General Manager Interview Questions
Behavioral Interview Questions
Can you describe a time when you led a major change initiative in a manufacturing plant and what the outcome was?
How to Answer
- 1
Identify a specific initiative with clear goals.
- 2
Explain the steps you took to implement the change.
- 3
Discuss challenges faced and how you overcame them.
- 4
Highlight measurable outcomes from the change.
- 5
Emphasize teamwork and communication throughout the process.
Example Answers
At my previous plant, I led the implementation of a new production scheduling system aimed at reducing downtime. We gathered input from the team to identify bottlenecks, piloted the system in one section, and achieved a 20% increase in overall efficiency within three months.
Tell me about a time you identified a significant risk in your plant operations and how you addressed it.
How to Answer
- 1
Use the STAR method: Situation, Task, Action, Result.
- 2
Focus on a specific risk relevant to plant operations.
- 3
Describe your thought process and decision-making.
- 4
Highlight collaboration with your team or other departments.
- 5
Mention measurable outcomes to demonstrate success.
Example Answers
In 2021, our team noticed a recurring equipment failure that risked production delays. I led a cross-functional meeting to analyze the data and identified a need for regular maintenance scheduling. We implemented a new maintenance protocol that reduced downtime by 30% over six months.
Don't Just Read Plant General Manager Questions - Practice Answering Them!
Reading helps, but actual practice is what gets you hired. Our AI feedback system helps you improve your Plant General Manager interview answers in real-time.
Personalized feedback
Unlimited practice
Used by hundreds of successful candidates
Describe your experience in building and leading a high-performance team in a manufacturing environment.
How to Answer
- 1
Start with the size and type of team you built.
- 2
Include specific strategies you used to develop team skills.
- 3
Mention any metrics or results that demonstrate performance improvement.
- 4
Discuss how you fostered a collaborative culture within the team.
- 5
Share an example of overcoming a challenge as a team.
Example Answers
In my previous role as a Production Manager, I led a team of 15 operators. I implemented training sessions focused on lean manufacturing principles, which boosted our efficiency by 20%. We regularly held team-building exercises that improved communication, leading to a 30% reduction in downtime.
Give an example of how you effectively communicated a difficult decision to your team.
How to Answer
- 1
Choose a specific difficult decision you faced, ensuring it's relevant to plant management.
- 2
Explain the context and reasons behind the decision to give clarity.
- 3
Describe how you communicated the decision to your team, including the method used.
- 4
Highlight the team’s reaction and any follow-up actions you took to support them.
- 5
Conclude with the outcome of the situation and any lessons learned.
Example Answers
In my previous role, I had to decide to implement a reduction in overtime due to budget constraints. I gathered the team for a meeting where I clearly explained the financial situation and the need for the change. I made sure to listen to their concerns and offered solutions, such as adjusting schedules to accommodate their needs. This led to a collaborative effort to improve efficiency and morale remained high despite the changes.
Tell me about a challenging problem you solved in a plant environment and how you approached it.
How to Answer
- 1
Identify a specific problem that affected productivity or safety.
- 2
Outline the steps you took to analyze the issue.
- 3
Describe the solution you implemented and why you chose it.
- 4
Share measurable results that demonstrate the success of your solution.
- 5
Keep the explanation clear and focused on your role in the resolution.
Example Answers
At my previous plant, we faced a significant increase in machine downtime due to equipment failure. I led a root cause analysis team to investigate the patterns of failures. We found that preventive maintenance was not being followed, so I revamped the maintenance schedule and trained the staff on its importance. As a result, we reduced downtime by 30% over the next quarter.
Describe a time when you successfully implemented cost-reduction measures in your plant operations.
How to Answer
- 1
Use the STAR method: Situation, Task, Action, Result.
- 2
Highlight specific cost-reduction measures and their impact.
- 3
Quantify savings or improvements where possible.
- 4
Explain the role of team collaboration in your success.
- 5
Mention any challenges faced and how you overcame them.
Example Answers
In Q2 of last year, our plant faced rising input costs (Situation). I was tasked with reducing expenditures (Task). I initiated a review of our vendor contracts and negotiated better rates, while also implementing a lean inventory system to minimize waste (Action). As a result, we achieved a 15% reduction in operational costs over six months, directly contributing to our bottom line (Result).
Can you provide an example of a difficult decision you made and how you arrived at your conclusion?
How to Answer
- 1
Choose a situation relevant to plant management.
- 2
Describe the context and the stakes involved.
- 3
Explain the decision-making process and considerations.
- 4
Highlight the outcome and what you learned.
- 5
Keep it concise and focused on your leadership role.
Example Answers
In my previous role, we faced a critical delay in our production line due to equipment failure. I had to decide whether to invest in a quick fix or a complete overhaul. I gathered input from my engineering team and weighed the immediate costs against long-term productivity. I chose the overhaul, which led to improved efficiency and reduced future downtime. This experience taught me the importance of strategic investment over short-term solutions.
Tell me about a time when you introduced an innovative solution that improved plant operations.
How to Answer
- 1
Focus on a specific example from your experience.
- 2
Describe the challenge the plant faced before your solution.
- 3
Explain the innovative solution you introduced clearly.
- 4
Highlight the results and improvements achieved.
- 5
Use metrics or data to quantify the impact where possible.
Example Answers
At my previous plant, we faced excessive downtime due to equipment failures. I introduced a predictive maintenance program using IoT sensors to monitor equipment health. This reduced our downtime by 30% and saved us $200,000 annually in operational costs.
Describe how you have managed underperforming employees in your team.
How to Answer
- 1
Identify specific underperformance issues with clear examples.
- 2
Discuss the importance of open communication and feedback.
- 3
Explain how you set clear expectations and goals.
- 4
Share any tools or strategies you used for performance improvement.
- 5
Mention follow-up actions and how success was measured.
Example Answers
In my previous role, I noticed one team member consistently missed deadlines. I scheduled a one-on-one to discuss their challenges and we established clearer expectations. I provided resources and checked in weekly, resulting in improved performance over three months.
Give an example of how you participated in strategic planning for a plant's growth.
How to Answer
- 1
Identify a specific strategic planning initiative you led or participated in.
- 2
Mention the goals of the strategic plan and how they aimed at growth.
- 3
Explain the steps you took to implement the plan, including collaboration with teams.
- 4
Highlight measurable outcomes or results that demonstrate success.
- 5
Reflect on any adjustments made during the implementation to stay aligned with goals.
Example Answers
In my previous role as an operations manager, I spearheaded a strategic planning initiative to increase our plant's production capacity by 20% over two years. We set specific goals and collaborated with engineering and maintenance teams to streamline processes. By implementing lean manufacturing techniques, we reduced waste and improved efficiency, resulting in a 25% increase in output with a 15% cost reduction.
Don't Just Read Plant General Manager Questions - Practice Answering Them!
Reading helps, but actual practice is what gets you hired. Our AI feedback system helps you improve your Plant General Manager interview answers in real-time.
Personalized feedback
Unlimited practice
Used by hundreds of successful candidates
Technical Interview Questions
What are the key metrics you use to evaluate plant performance, and how do you use them to drive improvement?
How to Answer
- 1
Identify specific metrics like OEE, safety incidents, and production efficiency.
- 2
Explain how you track these metrics regularly using dashboards.
- 3
Discuss how you analyze trends to pinpoint areas needing improvement.
- 4
Mention using metrics for team accountability and goal-setting.
- 5
Highlight examples of improvements made based on specific metrics.
Example Answers
I focus on key metrics like Overall Equipment Effectiveness (OEE), production yield, and safety incident rates. I track these through daily dashboards and team meetings, which helps us spot trends. For instance, when OEE dropped below 85%, I worked with the maintenance team to identify bottlenecks, leading to a 20% increase in equipment uptime.
Can you explain the principles of lean manufacturing and how you have implemented them in a plant setting?
How to Answer
- 1
Start with defining lean manufacturing clearly and concisely.
- 2
Mention key principles like value stream mapping, waste reduction, and continuous improvement.
- 3
Provide a specific example from your experience implementing lean in a plant.
- 4
Discuss measurable outcomes that resulted from your lean initiatives.
- 5
Highlight teamwork and employee involvement in your implementation.
Example Answers
Lean manufacturing focuses on maximizing customer value while minimizing waste. In my last role, we implemented value stream mapping to identify inefficiencies. By organizing a cross-functional team, we reduced production lead time by 20% over six months.
Don't Just Read Plant General Manager Questions - Practice Answering Them!
Reading helps, but actual practice is what gets you hired. Our AI feedback system helps you improve your Plant General Manager interview answers in real-time.
Personalized feedback
Unlimited practice
Used by hundreds of successful candidates
What strategies do you use to ensure a stable and efficient supply chain in plant operations?
How to Answer
- 1
Conduct regular assessments of supply chain vulnerabilities
- 2
Establish strong relationships with key suppliers
- 3
Implement just-in-time inventory practices
- 4
Utilize technology for real-time tracking and forecasting
- 5
Develop contingency plans for supply disruptions
Example Answers
I prioritize regular assessments of the supply chain to identify any vulnerabilities. By maintaining strong relationships with key suppliers, I ensure that we can address any issues proactively.
How do you develop and manage the budget for a manufacturing plant?
How to Answer
- 1
Analyze historical financial data to identify trends and areas for improvement
- 2
Engage department heads to understand their needs and align with overall plant goals
- 3
Create a detailed budget that includes both fixed and variable costs
- 4
Implement a monitoring system to track budget adherence and make adjustments as needed
- 5
Communicate regularly with stakeholders about financial performance and budget updates
Example Answers
I begin by reviewing past financial data to spot spending patterns and inefficiencies. Then, I collaborate with department heads to gather their budgetary needs, ensuring alignment with our overall plant goals. I draft a comprehensive budget and set up regular reviews to track our spending against it, making adjustments as necessary to stay on course and informing stakeholders on our financial status regularly.
What safety standards and practices do you consider essential for a manufacturing plant?
How to Answer
- 1
Identify key safety standards relevant to your industry, such as OSHA regulations.
- 2
Discuss the importance of regular safety training for employees.
- 3
Emphasize the role of personal protective equipment (PPE) in a safe working environment.
- 4
Mention the significance of safety audits and inspections.
- 5
Highlight the need for a safety culture that encourages reporting hazards.
Example Answers
I believe essential safety standards include adherence to OSHA regulations and regular employee training on safety protocols. PPE usage is critical, and I ensure that safety audits are conducted routinely to identify and mitigate risks. Creating a safety-first culture is also key.
What role do you believe technology plays in modern plant operations, and how have you integrated it in the past?
How to Answer
- 1
Focus on specific technologies relevant to the plant industry
- 2
Mention how technology improves efficiency and safety
- 3
Provide a concrete example from past experience
- 4
Discuss any measurable outcomes from technology integration
- 5
Highlight your vision for future technology in plant operations
Example Answers
In modern plant operations, technology is crucial for optimizing processes. In my last role, we implemented a real-time monitoring system that reduced downtime by 15%. I believe that continued advancements in automation will further enhance productivity.
What techniques do you employ for process optimization to enhance plant efficiency?
How to Answer
- 1
Identify data-driven methods to analyze current processes.
- 2
Discuss continuous improvement frameworks like Lean or Six Sigma.
- 3
Emphasize the importance of employee training and engagement in optimization.
- 4
Highlight the use of technology for automation and monitoring.
- 5
Provide examples of specific projects where you achieved measurable results.
Example Answers
I utilize Six Sigma methodologies to analyze process data, which helps identify bottlenecks. One example was reducing cycle time by 15% through value stream mapping and employee workshops.
How do you approach capacity planning to meet production demands?
How to Answer
- 1
Analyze historical production data to identify trends and peaks.
- 2
Engage with sales and marketing to forecast future demand accurately.
- 3
Assess current equipment and workforce capacity to identify gaps.
- 4
Develop flexible production schedules to adjust to changes in demand.
- 5
Implement a continuous improvement process for capacity utilization.
Example Answers
To meet production demands, I start by reviewing past production data to identify seasonal trends. Then, I work closely with the sales team to forecast upcoming demands and adjust capacity accordingly. I also ensure our production line is flexible enough to scale up or down based on these forecasts.
What is your approach to maintenance planning to minimize downtime in plant operations?
How to Answer
- 1
Implement a predictive maintenance strategy using data analytics to foresee equipment failures.
- 2
Schedule regular maintenance during off-peak hours to reduce impact on production.
- 3
Train staff on quick response procedures to minimize downtime during unexpected failures.
- 4
Utilize a computerized maintenance management system for efficient tracking and scheduling.
- 5
Engage with operators to gather insights on equipment performance and early signs of wear.
Example Answers
I prioritize predictive maintenance by utilizing data analytics to anticipate and prevent failures. This helps us schedule timely interventions without disrupting operations.
How have you implemented automation to improve productivity in past plant operations?
How to Answer
- 1
Identify specific automation tools or systems you have implemented.
- 2
Quantify improvements in productivity or efficiency after implementation.
- 3
Discuss how you trained staff to adapt to new automated processes.
- 4
Mention any challenges faced during implementation and how you overcame them.
- 5
Highlight ongoing monitoring and adjustments made post-implementation.
Example Answers
At my previous plant, I introduced a robotic assembly line that increased our production rate by 30%. I ensured the staff received training on the new system, which minimized transition issues. We monitored the process closely and adjusted workflows to optimize efficiency further.
Don't Just Read Plant General Manager Questions - Practice Answering Them!
Reading helps, but actual practice is what gets you hired. Our AI feedback system helps you improve your Plant General Manager interview answers in real-time.
Personalized feedback
Unlimited practice
Used by hundreds of successful candidates
Situational Interview Questions
If there is a conflict between two department heads in the plant affecting production, how would you handle it?
How to Answer
- 1
Remain neutral and listen to both sides to understand the root cause of the conflict.
- 2
Facilitate a meeting between the department heads to discuss the issue openly.
- 3
Encourage collaboration by focusing on common goals and the impact on production.
- 4
Establish clear action items and follow up regularly until the issue is resolved.
- 5
Promote a culture of communication to prevent future conflicts.
Example Answers
I would first meet individually with each department head to understand their perspectives. Then, I would bring them together for a discussion, emphasizing our shared goal of ensuring smooth production. Together, we would identify actionable steps to resolve the conflict and I would check in afterward to ensure everything stayed on track.
How would you manage an unexpected shutdown of the plant due to a critical equipment failure?
How to Answer
- 1
Quickly assess the situation and gather a team of key personnel.
- 2
Identify the root cause of the equipment failure and prioritize safety.
- 3
Communicate clearly with all employees about the situation and next steps.
- 4
Develop a recovery plan that addresses repairs and minimizes downtime.
- 5
Keep stakeholders informed about progress and expected timeline for resolution.
Example Answers
In the event of a critical equipment failure, I would first assemble a team of engineers and safety officers to assess the situation and ensure everyone's safety. Next, we would identify the root cause of the failure and prioritize urgent repairs. I would communicate openly with all staff, explaining the situation and how it affects our operations. Then, I would create a recovery plan to expedite repairs while minimizing production losses. Throughout the process, I would keep all relevant parties updated on our progress and any changes to our timeline.
Don't Just Read Plant General Manager Questions - Practice Answering Them!
Reading helps, but actual practice is what gets you hired. Our AI feedback system helps you improve your Plant General Manager interview answers in real-time.
Personalized feedback
Unlimited practice
Used by hundreds of successful candidates
A recent audit has revealed consistent quality issues in production. What steps would you take to address this?
How to Answer
- 1
Investigate the root cause of quality issues by analyzing production data and feedback.
- 2
Engage with frontline employees to gather insights and suggestions for improvements.
- 3
Implement targeted training programs to address skill gaps and reinforce quality standards.
- 4
Develop a corrective action plan with clear timelines and responsibilities.
- 5
Establish a regular review process to monitor progress and adjust strategies as needed.
Example Answers
I would first conduct a thorough analysis of production data to identify patterns in the quality issues. Then, I’d meet with the production team to hear their insights, as they often know what’s working and what’s not. Based on this, I would implement targeted training to enhance skills. I would also create a corrective action plan and schedule regular check-ins to ensure we are progressing.
How would you approach introducing a new product line in your plant?
How to Answer
- 1
Conduct a thorough market analysis to understand demand and competition
- 2
Involve cross-functional teams early in the planning process for diverse insights
- 3
Develop a detailed project timeline and allocate resources effectively
- 4
Implement a pilot program to test production processes and gather feedback
- 5
Ensure training and support for staff to adapt to new production requirements
Example Answers
I would start with market analysis to determine target customers and trends. Then, I would gather a cross-functional team to brainstorm and outline the product specifications. A pilot run would help identify any issues before full-scale production, and I'd ensure that all staff are trained on the new processes.
You have limited resources but need to increase production. How would you prioritize and manage this?
How to Answer
- 1
Assess current production capabilities and identify bottlenecks.
- 2
Evaluate resource allocation and consider cross-training employees.
- 3
Implement lean manufacturing principles to reduce waste.
- 4
Prioritize high-impact areas that directly enhance output.
- 5
Communicate with the team to foster collaboration and creativity.
Example Answers
First, I would analyze our current production process to find bottlenecks. Then, I would prioritize reallocation of resources towards those critical areas, and involve the team in brainstorming efficiencies through lean practices.
How would you handle a situation where there is pressure from stakeholders to meet unrealistic production targets?
How to Answer
- 1
Assess the feasibility of the targets with your team
- 2
Communicate openly with stakeholders about constraints
- 3
Propose adjusted targets based on resources and capacity
- 4
Suggest a phased approach to meet production goals
- 5
Gather data to support your position and recommendations
Example Answers
I would first analyze the production targets with my team to understand our current capabilities and constraints. Then, I would arrange a meeting with stakeholders to communicate the realities and propose a more achievable target, emphasizing a phased approach to attain our goals.
How would you ensure that your plant meets all environmental regulations and standards?
How to Answer
- 1
Regularly review and stay updated on local, state, and federal environmental regulations.
- 2
Implement an environmental management system (EMS) that monitors compliance.
- 3
Conduct regular training sessions for all employees on environmental policies and best practices.
- 4
Establish a routine auditing process to identify and rectify any compliance gaps.
- 5
Engage with environmental consultants for expert guidance and to conduct assessments.
Example Answers
To ensure compliance, I would first establish an environmental management system to monitor regulations closely. Regular audits and staff training would reinforce our standards and keep everyone informed.
A union is threatening to strike over working conditions. How do you handle this situation?
How to Answer
- 1
Listen actively to union representatives to understand their concerns
- 2
Analyze the specific complaints and assess the validity of issues raised
- 3
Communicate transparently with both the union and management about possible solutions
- 4
Engage in negotiation to find a compromise that addresses grievances
- 5
Document all discussions and agreements to ensure clarity and commitment
Example Answers
I would first meet with the union leaders to listen to their concerns actively. Understanding the specific complaints allows me to assess their validity. Following that, I would communicate possible solutions to both the union and management, engaging in negotiations to find a compromise that works for everyone.
If raw material costs unexpectedly rise, how would you adapt your budget and production plans?
How to Answer
- 1
Assess the impact of raw material costs on overall budget
- 2
Identify alternative materials or suppliers to reduce costs
- 3
Prioritize production schedules based on profitability
- 4
Engage with stakeholders to communicate changes and gather input
- 5
Monitor market trends for potential future adjustments
Example Answers
I would first evaluate how the rise in raw material costs affects our total production budget. Then, I would look for alternative suppliers or substitute materials that could help manage costs. Meanwhile, I would adjust our production priorities to focus on the most profitable products and communicate with the team about these changes.
A major client is dissatisfied with delivery times. What actions would you take to resolve the issue?
How to Answer
- 1
Acknowledge the client's concerns first to show empathy.
- 2
Investigate the root cause of the delayed deliveries.
- 3
Communicate clearly with the client about the steps you're taking to resolve the issue.
- 4
Propose actionable solutions or alternatives to improve delivery times.
- 5
Follow up with the client after implementing changes to ensure satisfaction.
Example Answers
I would start by acknowledging the client's concerns and apologize for the inconvenience caused. Then, I would investigate the supply chain and production processes to find the root cause of the delays. After identifying the issue, I would communicate with the client about the steps we are taking to improve delivery times and offer them options for expedited shipping as a temporary solution.
Don't Just Read Plant General Manager Questions - Practice Answering Them!
Reading helps, but actual practice is what gets you hired. Our AI feedback system helps you improve your Plant General Manager interview answers in real-time.
Personalized feedback
Unlimited practice
Used by hundreds of successful candidates
Plant General Manager Position Details
Salary Information
Recommended Job Boards
CareerBuilder
www.careerbuilder.com/jobs/plant-general-managerZipRecruiter
www.ziprecruiter.com/Jobs/Plant-General-ManagerThese job boards are ranked by relevance for this position.
Related Positions
Ace Your Next Interview!
Practice with AI feedback & get hired faster
Personalized feedback
Used by hundreds of successful candidates
Ace Your Next Interview!
Practice with AI feedback & get hired faster
Personalized feedback
Used by hundreds of successful candidates