Top 30 Production Superintendent Interview Questions and Answers [Updated 2025]
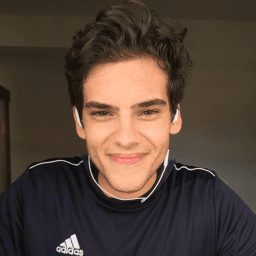
Andre Mendes
•
March 30, 2025
Preparing for a Production Superintendent interview can be daunting, but with the right guidance, you can approach it with confidence. In this blog post, we delve into the most common interview questions for this pivotal role, providing you with insightful example answers and practical tips to help you respond effectively. Whether you're a seasoned professional or a newcomer, these strategies will equip you to impress any hiring panel.
Download Production Superintendent Interview Questions in PDF
To make your preparation even more convenient, we've compiled all these top Production Superintendentinterview questions and answers into a handy PDF.
Click the button below to download the PDF and have easy access to these essential questions anytime, anywhere:
List of Production Superintendent Interview Questions
Behavioral Interview Questions
Can you describe a time when you successfully led a team through a major production challenge?
How to Answer
- 1
Select a specific challenge that had significant impact.
- 2
Explain your role and the actions you took to address the issue.
- 3
Highlight teamwork and collaboration with your team.
- 4
Discuss the outcome and any measurable results.
- 5
Conclude with what you learned from the experience.
Example Answers
In my previous role, we faced a two-week production halt due to equipment failure. I organized daily meetings to assess progress and delegate tasks. By collaborating with engineering and maintenance, we successfully repaired the machinery ahead of schedule, leading to a 15% increase in our output once production resumed. This experience taught me the importance of proactive communication.
Give an example of a conflict you encountered on the production floor. How did you handle it?
How to Answer
- 1
Begin with a brief description of the conflict and the parties involved
- 2
Explain your approach to resolving the issue calmly and constructively
- 3
Highlight the outcome and any lessons learned
- 4
Focus on communication and teamwork in your resolution process
- 5
Emphasize how the situation improved production or morale
Example Answers
In a recent shift, two team members disagreed on the method for maintaining equipment. I brought them together for a discussion, allowing each to voice their perspective. By facilitating a collaborative solutions-focused dialogue, we agreed on a hybrid method that satisfied both parties, improving our maintenance efficiency and team cohesion.
Don't Just Read Production Superintendent Questions - Practice Answering Them!
Reading helps, but actual practice is what gets you hired. Our AI feedback system helps you improve your Production Superintendent interview answers in real-time.
Personalized feedback
Unlimited practice
Used by hundreds of successful candidates
Tell me about a time when you implemented a change that improved production efficiency. What was the outcome?
How to Answer
- 1
Identify a specific change you made in a production process.
- 2
Explain the problem or inefficiency you aimed to address.
- 3
Detail the steps you took to implement this change.
- 4
Share measurable outcomes or improvements resulting from the change.
- 5
Highlight any feedback from team members or stakeholders.
Example Answers
In my previous role, we faced frequent machine downtime due to maintenance delays. I implemented a predictive maintenance schedule, training the team on recognizing potential issues early. As a result, machine downtime decreased by 30%, and our production output improved significantly within three months.
Describe an occasion when you had to work closely with other departments to achieve production goals. What was your approach?
How to Answer
- 1
Identify a specific project and departments involved.
- 2
Highlight clear communication methods you used.
- 3
Explain how you aligned goals with those departments.
- 4
Discuss any challenges faced and how they were overcome.
- 5
Mention the final outcome and benefits of collaboration.
Example Answers
In a recent project to reduce downtime, I collaborated closely with the maintenance and quality control departments. We held regular meetings to align our objectives, which helped identify critical equipment issues early. When we faced a delay due to a parts shortage, I coordinated with suppliers to expedite delivery. Ultimately, we reduced downtime by 20% and improved overall production efficiency.
Can you provide an example of how you prioritized tasks during a high-pressure production deadline?
How to Answer
- 1
Describe the situation clearly and include specific details.
- 2
Identify the most critical tasks that needed immediate attention.
- 3
Explain the criteria used for prioritization.
- 4
Highlight communication with the team during this process.
- 5
Conclude with the positive outcome achieved because of your prioritization.
Example Answers
During an unexpected surge in demand, I assessed all production tasks. I prioritized the tasks based on delivery deadlines and resource availability. I communicated these priorities to my team, and we focused on key orders first. This helped us meet deadlines and maintain customer satisfaction.
Can you discuss a time when you had to give constructive feedback to a team member? What was your approach?
How to Answer
- 1
Choose a specific instance that highlights your feedback skills.
- 2
Describe the context and the relationship with the team member.
- 3
Explain the feedback you gave and the rationale behind it.
- 4
Detail the method of delivery, focusing on positivity and support.
- 5
Conclude with the outcome and any improvements observed.
Example Answers
In my previous role, I noticed a team member struggling with time management. I scheduled a private meeting to discuss my observations and asked if they needed support. I provided practical tips and offered to help them prioritize tasks. They improved their efficiency over the next month and thanked me for the guidance.
Describe a time when you had to adapt to significant changes in production processes. How did you manage that?
How to Answer
- 1
Choose a specific change in production processes you faced.
- 2
Explain the context and why the change was significant.
- 3
Describe the steps you took to adapt, including team involvement.
- 4
Highlight the outcomes of the adaptation.
- 5
Reflect on what you learned from the experience.
Example Answers
In my previous role, we switched to a new inventory management system. I organized training sessions for the team to ensure everyone was comfortable with the software. This increased efficiency by 15% within three months. I learned the importance of proactive communication during such transitions.
Tell me about a time when effective communication helped resolve a production issue.
How to Answer
- 1
Identify a specific production issue you faced.
- 2
Explain the communication methods you used to address the issue.
- 3
Highlight who you communicated with and why their input was important.
- 4
Describe the positive outcome resulting from your communication.
- 5
Keep your answer focused on your role and contributions.
Example Answers
In my previous role, we faced a significant delay due to a machine breakdown. I quickly scheduled a meeting with the maintenance team and production staff to discuss the issue. By clearly sharing the impact on our production schedule, we collaboratively identified the most critical repairs and got the machine back online within hours, minimizing downtime.
Don't Just Read Production Superintendent Questions - Practice Answering Them!
Reading helps, but actual practice is what gets you hired. Our AI feedback system helps you improve your Production Superintendent interview answers in real-time.
Personalized feedback
Unlimited practice
Used by hundreds of successful candidates
Technical Interview Questions
What methods do you use for creating and managing production schedules?
How to Answer
- 1
Start with defining project goals and timelines clearly
- 2
Incorporate input from team members about resource availability
- 3
Utilize scheduling software to visualize timelines and bottlenecks
- 4
Review and adjust schedules regularly based on performance and changes
- 5
Communicate updates to all stakeholders to ensure alignment
Example Answers
I begin by clearly defining production goals and timelines, then collaborate with my team to assess resource availability. I use scheduling software to create visual timelines and identify any potential bottlenecks. Regular reviews allow me to adjust the schedule as needed, and I always keep open communication with all stakeholders to keep everyone informed.
How do you ensure that all production equipment is maintained and serviced on schedule?
How to Answer
- 1
Develop a detailed maintenance schedule for all equipment based on manufacturer recommendations.
- 2
Utilize maintenance management software to track service dates and maintenance history.
- 3
Assign specific team members responsible for monitoring equipment condition and performing routine checks.
- 4
Implement regular training sessions to ensure all staff understand maintenance procedures and importance.
- 5
Establish a communication system for reporting issues immediately to prevent downtime.
Example Answers
I create a maintenance schedule using manufacturer guidelines and integrate it into a tracking software to monitor service dates. Each technician is assigned specific equipment to oversee, allowing for greater accountability.
Don't Just Read Production Superintendent Questions - Practice Answering Them!
Reading helps, but actual practice is what gets you hired. Our AI feedback system helps you improve your Production Superintendent interview answers in real-time.
Personalized feedback
Unlimited practice
Used by hundreds of successful candidates
What quality control measures do you implement to maintain product standards?
How to Answer
- 1
Establish clear quality benchmarks for each product.
- 2
Implement regular inspections at various production stages.
- 3
Use statistical process control to analyze production data.
- 4
Train staff on quality standards and procedures.
- 5
Encourage feedback loops for continuous improvement.
Example Answers
I establish clear quality benchmarks for each product and implement inspections at critical production stages to ensure compliance.
What are some key safety standards and regulations you ensure are followed on the production floor?
How to Answer
- 1
Identify specific industry regulations relevant to your sector, such as OSHA.
- 2
Discuss training programs you implement for staff on safety protocols.
- 3
Mention regular safety audits and how you handle findings.
- 4
Highlight the importance of personal protective equipment (PPE) and compliance.
- 5
Connect safety standards to operational efficiency and employee well-being.
Example Answers
I ensure compliance with OSHA regulations by conducting quarterly safety audits and offering monthly training sessions for staff on our safety protocols.
Can you explain your experience with lean manufacturing principles in a production setting?
How to Answer
- 1
Identify specific lean tools you've implemented, like 5S or Kanban.
- 2
Give examples of measurable improvements from your lean initiatives.
- 3
Discuss cross-functional collaboration in lean projects.
- 4
Mention any training or certifications in lean methodologies.
- 5
Highlight your approach to sustaining lean practices over time.
Example Answers
In my previous role, I implemented 5S and saw a 20% reduction in waste, which improved our turnaround times significantly. I trained the team on these principles, ensuring we maintained the improvements long term.
What methods do you use to analyze production data for decision-making?
How to Answer
- 1
Identify key performance indicators relevant to production goals.
- 2
Utilize statistical tools or software for data analysis.
- 3
Visualize data trends using graphs or dashboards for better insights.
- 4
Incorporate feedback from the team to validate findings.
- 5
Regularly review and adjust methods based on outcomes and new data.
Example Answers
I focus on key performance indicators like efficiency and downtime to guide my analysis. I typically use software like Excel or Tableau to visualize data trends, which helps in making informed decisions.
What steps do you take to ensure compliance with industry regulations in production?
How to Answer
- 1
Stay updated on industry regulations and changes through regular training.
- 2
Conduct regular audits and inspections of production processes.
- 3
Establish clear compliance protocols and train the team on them.
- 4
Implement documentation practices to track compliance activities.
- 5
Engage with regulatory bodies and industry groups for best practices.
Example Answers
I stay updated on regulations by participating in industry training sessions and workshops. I also conduct regular audits of our production processes to ensure we are compliant and adhere to established protocols.
How do you approach process planning and development in your production environment?
How to Answer
- 1
Identify key production goals and metrics to align process planning.
- 2
Involve team members in brainstorming to gather diverse insights.
- 3
Utilize data analysis to evaluate current workflows and identify bottlenecks.
- 4
Prioritize continuous improvement through regular feedback loops.
- 5
Implement pilot projects to test new processes before full-scale rollout.
Example Answers
I start by defining production goals with my team, ensuring we all understand what success looks like. Then, we analyze our existing processes using data to identify challenges and inefficiencies. I encourage team collaboration for fresh ideas, and we regularly revisit our processes to incorporate feedback and drive improvements.
What performance metrics do you track to measure production effectiveness?
How to Answer
- 1
Identify key production metrics such as output rate, downtime, and efficiency.
- 2
Explain how you utilize those metrics to drive process improvements.
- 3
Include examples of how monitoring these metrics has benefited previous teams.
- 4
Emphasize collaboration with other departments to align on production goals.
- 5
Highlight any tools or software you use to track these metrics.
Example Answers
I track output rate, equipment downtime, and overall equipment effectiveness (OEE). By analyzing these metrics, I can identify bottlenecks and implement timely adjustments, which led to a 15% increase in productivity in my last role.
How do you ensure your supply chain is reliable and can meet production demands?
How to Answer
- 1
Establish strong relationships with key suppliers to ensure priority and reliability.
- 2
Implement inventory management systems to track stock levels and forecast needs.
- 3
Regularly review and assess supplier performance and capacity.
- 4
Diversify suppliers to mitigate risks and avoid reliance on a single source.
- 5
Use data analytics to anticipate demand fluctuations and adjust orders accordingly.
Example Answers
I ensure a reliable supply chain by building strong relationships with my key suppliers. This allows me to prioritize orders during peak times. Additionally, I utilize an inventory management system to continually assess stock levels and forecast our production needs accurately.
Don't Just Read Production Superintendent Questions - Practice Answering Them!
Reading helps, but actual practice is what gets you hired. Our AI feedback system helps you improve your Production Superintendent interview answers in real-time.
Personalized feedback
Unlimited practice
Used by hundreds of successful candidates
Situational Interview Questions
If you notice a sudden drop in production output, what steps would you take to identify and resolve the issue?
How to Answer
- 1
Collect and analyze production data to pinpoint the timing of the drop.
- 2
Inspect machinery and equipment for any signs of malfunction or maintenance needs.
- 3
Engage with team members to gather insights on workflow changes or issues.
- 4
Evaluate inventory levels and supply chain factors that could affect production.
- 5
Implement corrective actions based on findings and monitor for improvements.
Example Answers
Firstly, I would analyze production data to identify when the drop occurred and correlate it with any operational changes. Then, I would inspect equipment to rule out mechanical issues. Finally, I would talk to my team to gather their perspectives and apply any necessary adjustments.
Imagine you have limited resources and multiple urgent production requests. How would you decide on the priorities?
How to Answer
- 1
Assess the urgency of each request by considering deadlines and impact.
- 2
Consult with stakeholders to understand the importance of each request.
- 3
Evaluate resource availability and constraints to determine feasibility.
- 4
Rank the requests based on business goals and potential returns.
- 5
Communicate your prioritization rationale clearly to the team.
Example Answers
I would first categorize each request by urgency and deadline, then talk to team leads to gauge the importance. After assessing resources, I would rank them to align with our overall business objectives.
Don't Just Read Production Superintendent Questions - Practice Answering Them!
Reading helps, but actual practice is what gets you hired. Our AI feedback system helps you improve your Production Superintendent interview answers in real-time.
Personalized feedback
Unlimited practice
Used by hundreds of successful candidates
If a new piece of equipment is introduced, how would you approach training your staff on its operation?
How to Answer
- 1
Assess the training needs based on staff experience and the equipment's complexity
- 2
Organize hands-on training sessions with a knowledgeable operator as a mentor
- 3
Develop easy-to-follow training materials, including manuals and videos
- 4
Schedule regular follow-up sessions to address questions and reinforce learning
- 5
Encourage a culture of open communication where staff can share feedback and concerns
Example Answers
I would start by evaluating the team's familiarity with similar equipment. Then, I'd arrange hands-on sessions led by an experienced operator, complemented by clear training materials. Regular check-ins would help ensure everyone feels confident.
How would you handle a situation where a machine breaks down during peak production hours?
How to Answer
- 1
Stay calm and assess the situation quickly
- 2
Communicate the issue to the team and relevant stakeholders immediately
- 3
Prioritize safety and prevent further disruptions
- 4
Initiate a troubleshooting process while considering backup options
- 5
Document the incident and analyze root causes for future prevention
Example Answers
I would first assess the situation to understand the machine's status, then inform my team and management about the breakdown. While ensuring everyone’s safety, I would troubleshoot the problem and explore backup production methods until the machine is fixed.
If you were given a production budget cut, how would you adjust operations to stay within budget?
How to Answer
- 1
Identify areas of inefficiency and seek to optimize them.
- 2
Consider reallocating resources to high-impact areas.
- 3
Engage team members in cost-saving initiatives for their insights.
- 4
Negotiate better terms with suppliers for materials and services.
- 5
Analyze production schedules to reduce overtime and downtime.
Example Answers
I would first assess our current operations to pinpoint inefficiencies, such as excessive material waste. By optimizing these areas, we could reduce costs without impacting production.
How would you address a situation where you have surplus inventory affecting production efficiency?
How to Answer
- 1
Assess the root cause of the surplus inventory
- 2
Engage with production and sales teams for insights
- 3
Implement a clear inventory management strategy
- 4
Consider promotions or discounts to reduce excess stock
- 5
Evaluate and adjust future production planning
Example Answers
I would start by analyzing the data to determine why we have surplus inventory. Then, I would consult with the production and sales teams to understand demand forecasting issues. Finally, I would implement a targeted promotional campaign to clear excess stock while adjusting our future inventory levels.
If a team member is frequently underperforming, how would you address the situation?
How to Answer
- 1
Schedule a private meeting to discuss performance concerns.
- 2
Use specific examples of underperformance to highlight issues.
- 3
Listen to the team member's perspective to understand root causes.
- 4
Set clear expectations and develop a performance improvement plan together.
- 5
Follow up regularly to monitor progress and provide ongoing support.
Example Answers
I would first meet privately with the team member to discuss their performance, using specific examples. I would listen to their side and identify any challenges they face. Together, we would set clear expectations and a plan for improvement, ensuring I check in regularly to support them.
How would you respond if a key client places an urgent order that disrupts existing production plans?
How to Answer
- 1
Assess current production capacity and resources immediately
- 2
Communicate with the team about the urgent order and gather input
- 3
Prioritize tasks to accommodate the urgent order without jeopardizing quality
- 4
Engage with the client to confirm requirements and delivery timelines
- 5
Implement a flexible plan that allows for adjustments as production progresses
Example Answers
I would first evaluate our current production schedule to identify any capacity we can leverage. Then, I would gather the team to discuss the necessary adjustments and prioritize tasks. I would also reach out to the client to confirm their needs and establish a realistic timeline for delivery.
If two different projects require the same resource at the same time, how would you decide which project gets priority?
How to Answer
- 1
Identify the overall business goals tied to each project.
- 2
Assess the potential impact of each project on stakeholders.
- 3
Evaluate deadlines and urgency of the projects.
- 4
Consider resource availability and project timelines.
- 5
Engage with team members for additional insights and collaboration.
Example Answers
I would first review the business objectives of each project and prioritize the one that aligns more closely with our strategic goals. Then, I would consider the urgency and potential impact on stakeholders before making a decision.
If team morale is low due to repeated production failures, what steps would you take to address this?
How to Answer
- 1
Acknowledge the issue openly with the team.
- 2
Conduct a root cause analysis to identify failure reasons.
- 3
Involve the team in brainstorming solutions.
- 4
Set achievable short-term goals to rebuild confidence.
- 5
Recognize and celebrate small wins to boost morale.
Example Answers
First, I would have an open discussion with the team about our challenges to ensure everyone feels heard. Then, I would lead a root cause analysis to identify why we are facing these failures. By involving the team in generating solutions, we can foster a sense of ownership. Lastly, I would set small, achievable goals and celebrate our wins to gradually rebuild morale.
Don't Just Read Production Superintendent Questions - Practice Answering Them!
Reading helps, but actual practice is what gets you hired. Our AI feedback system helps you improve your Production Superintendent interview answers in real-time.
Personalized feedback
Unlimited practice
Used by hundreds of successful candidates
Production Superintendent Position Details
Salary Information
Average Salary
$88,703
Source: Zippia
Recommended Job Boards
These job boards are ranked by relevance for this position.
Related Positions
Ace Your Next Interview!
Practice with AI feedback & get hired faster
Personalized feedback
Used by hundreds of successful candidates
Ace Your Next Interview!
Practice with AI feedback & get hired faster
Personalized feedback
Used by hundreds of successful candidates