Top 29 Production Foreman Interview Questions and Answers [Updated 2025]
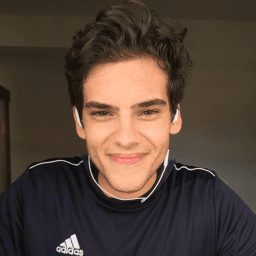
Andre Mendes
•
March 30, 2025
Preparing for a Production Foreman interview can be daunting, but we're here to guide you with the most common questions you'll likely face. In this post, you'll find insightful example answers and expert tips to help you respond with confidence and precision. Whether you're a seasoned professional or new to the role, these strategies will enhance your interview performance and increase your chances of success.
Download Production Foreman Interview Questions in PDF
To make your preparation even more convenient, we've compiled all these top Production Foremaninterview questions and answers into a handy PDF.
Click the button below to download the PDF and have easy access to these essential questions anytime, anywhere:
List of Production Foreman Interview Questions
Technical Interview Questions
What software or technologies have you used as a foreman to improve production efficiency?
How to Answer
- 1
Identify specific software or tools you have used.
- 2
Explain how these technologies improved efficiency.
- 3
Discuss any measurable outcomes achieved.
- 4
Mention any training or implementation experiences.
- 5
Relate your experiences to the job you're applying for.
Example Answers
I have used Lean Manufacturing software to streamline processes, which improved our production efficiency by 15% over six months by reducing waste.
What is your experience with Lean Manufacturing principles and how have you applied them in your previous role?
How to Answer
- 1
Identify specific Lean principles you are familiar with, such as 5S, Kaizen, or Just-in-Time.
- 2
Provide examples of projects where you implemented these principles.
- 3
Describe measurable improvements that resulted from your implementation.
- 4
Focus on teamwork or leadership aspects if applicable.
- 5
Be concise and keep your answers relevant to the role of a Production Foreman.
Example Answers
In my previous role, I implemented 5S strategies on the production floor, which led to a 20% reduction in search time for tools and materials, greatly improving our workflow efficiency.
Good Candidates Answer Questions. Great Ones Win Offers.
Reading sample answers isn't enough. Top candidates practice speaking with confidence and clarity. Get real feedback, improve faster, and walk into your next interview ready to stand out.
Master your interview answers under pressure
Boost your confidence with real-time practice
Speak clearly and impress hiring managers
Get hired faster with focused preparation
Used by hundreds of successful candidates
Can you explain how you conduct routine maintenance checks on production equipment?
How to Answer
- 1
Start by outlining the schedule for checks based on equipment requirements.
- 2
Mention specific tools or methods you use for inspections.
- 3
Discuss how you document the findings during checks.
- 4
Explain your process for addressing any issues found during checks.
- 5
Highlight the importance of safety protocols during maintenance.
Example Answers
I follow a weekly schedule for routine maintenance checks on production equipment. I use a checklist that includes inspecting belts, bearings, and electrical connections. Each time I complete a check, I document my observations and any needed repairs in our maintenance management system.
Can you describe a time when you identified inefficiencies in the production process and how you addressed them?
How to Answer
- 1
Use the STAR method: Situation, Task, Action, Result.
- 2
Focus on a specific example from your experience.
- 3
Clearly describe the inefficiency you identified.
- 4
Explain the steps you took to address it.
- 5
Quantify the results to show impact, if possible.
Example Answers
In my previous role, we had a bottleneck in the assembly line that delayed product delivery. I noticed that two stations were causing delays. I analyzed the workflow and proposed combining tasks at one station. After implementing this change, we reduced assembly time by 20%, improving our delivery schedule significantly.
Describe the process you use for creating production schedules. How do you accommodate unexpected changes?
How to Answer
- 1
Start with how you gather input from the team and departments involved.
- 2
Explain the tools or software you use for scheduling.
- 3
Mention how you prioritize tasks based on urgency and resources.
- 4
Discuss your method for monitoring progress and creating buffer time.
- 5
Describe how you communicate changes to the team effectively.
Example Answers
I create production schedules by first gathering input from the production team and sales to understand demands. I use software like Trello for visualization and prioritizing tasks based on deadlines and available resources. I monitor progress daily and adjust timelines as needed, including buffer time for unexpected delays.
How do you ensure that the production team has all necessary materials without causing overstock issues?
How to Answer
- 1
Implement a just-in-time inventory system to match material supply with production schedules.
- 2
Regularly analyze usage patterns to predict material needs accurately.
- 3
Establish strong communication with suppliers for timely deliveries.
- 4
Use inventory management software to track stock levels in real-time.
- 5
Conduct periodic audits of inventory to adjust forecasts and reduce excess.
Example Answers
I ensure our team has necessary materials by utilizing a just-in-time inventory system. This helps us align material orders closely with production schedules, reducing the risk of overstock.
Explain the safety protocols you follow for maintaining a safe production environment.
How to Answer
- 1
Start with a brief overview of safety training and certifications.
- 2
Mention specific safety protocols you enforce, like PPE usage.
- 3
Discuss regular safety audits and inspections you conduct.
- 4
Include how you promote a culture of safety among workers.
- 5
Share an example of a safety incident and how it was managed.
Example Answers
I always ensure that my team has completed the necessary safety training and holds relevant certifications. We strictly enforce the use of personal protective equipment like helmets and gloves. I conduct weekly safety audits and encourage team members to report any hazards. By fostering an open dialogue about safety, we maintain a culture of vigilance. For instance, last year we had a near-miss incident that we learned from and implemented additional safety measures to prevent it from recurring.
What quality control methods do you implement to ensure product consistency?
How to Answer
- 1
Discuss specific quality control tools you've used such as Statistical Process Control or Six Sigma.
- 2
Mention regular training for staff on quality standards and procedures.
- 3
Describe how you conduct routine inspections and audits of the production process.
- 4
Explain how you gather and analyze data on product defects for continuous improvement.
- 5
Share examples of feedback mechanisms from production staff to improve quality.
Example Answers
In my previous role, I implemented Statistical Process Control to monitor process variables and ensure products met specifications. We also conducted weekly training sessions to keep all staff informed of quality standards.
What tools or systems do you use for tracking and reporting production metrics?
How to Answer
- 1
Identify specific tools you have used such as ERP systems or production software.
- 2
Mention any metrics that are particularly important to track, like throughput or downtime.
- 3
Describe how you ensure data accuracy and consistency in reporting.
- 4
Explain any experience with data visualization tools to present metrics clearly.
- 5
Highlight your ability to adapt to new systems or enhance existing ones.
Example Answers
I have extensive experience using ERP systems like SAP for tracking production metrics. Specifically, I focus on metrics such as cycle time and scrap rates, ensuring data integrity through regular audits.
How have you helped reduce production costs in your previous positions?
How to Answer
- 1
Identify specific cost reduction initiatives you led or contributed to.
- 2
Use quantifiable results to demonstrate the impact of your actions.
- 3
Mention collaboration with other teams or departments to achieve savings.
- 4
Discuss any process improvements you implemented.
- 5
Highlight your understanding of the production metrics relevant to cost.
Example Answers
In my last position, I led a team to streamline the assembly line process, which reduced material waste by 15%, saving the company $10,000 annually.
Good Candidates Answer Questions. Great Ones Win Offers.
Reading sample answers isn't enough. Top candidates practice speaking with confidence and clarity. Get real feedback, improve faster, and walk into your next interview ready to stand out.
Master your interview answers under pressure
Boost your confidence with real-time practice
Speak clearly and impress hiring managers
Get hired faster with focused preparation
Used by hundreds of successful candidates
Behavioral Interview Questions
Tell us about a time when you had to lead a team through a difficult project. How did you ensure the project was successful?
How to Answer
- 1
Choose a specific project that had clear challenges.
- 2
Outline your role and leadership techniques you used.
- 3
Explain how you communicated with the team and stakeholders.
- 4
Describe how you kept the team motivated and focused.
- 5
Summarize the outcome and what you learned from the experience.
Example Answers
In my previous role, we faced a major equipment upgrade that had tight deadlines. I organized daily briefings to track progress and address issues. By fostering open communication, I ensured everyone felt heard, which kept morale high. We completed the upgrade ahead of schedule and under budget.
Describe a situation where there was a conflict between team members in the production line. How did you handle it?
How to Answer
- 1
Focus on a specific conflict scenario
- 2
Explain your role in mediating the conflict
- 3
Highlight communication techniques you used
- 4
Discuss the outcome after resolution
- 5
Emphasize teamwork and maintaining productivity
Example Answers
In a previous role, two team members disagreed over the best method to operate a machine. I facilitated a meeting where each could express their views. I guided the discussion towards finding common ground. We agreed on a trial of both methods, which improved cooperation and ultimately increased our output by 15%.
Good Candidates Answer Questions. Great Ones Win Offers.
Reading sample answers isn't enough. Top candidates practice speaking with confidence and clarity. Get real feedback, improve faster, and walk into your next interview ready to stand out.
Master your interview answers under pressure
Boost your confidence with real-time practice
Speak clearly and impress hiring managers
Get hired faster with focused preparation
Used by hundreds of successful candidates
Can you give an example of a significant problem you solved as a foreman? What was the outcome?
How to Answer
- 1
Identify a specific problem related to production or team dynamics.
- 2
Describe the steps you took to analyze and address the issue.
- 3
Highlight the collaboration with team members and any techniques used.
- 4
Mention the positive outcome and how it improved operations.
- 5
Reflect briefly on any lessons learned from this experience.
Example Answers
In one instance, we faced a consistent delay in our production line due to equipment failures. I organized a team meeting to gather input and discovered that scheduled maintenance was being overlooked. I implemented a maintenance checklist and arranged for timely service, resulting in a 30% reduction in downtime over the next three months.
Describe how you have communicated complex instructions to your team to ensure they are understood.
How to Answer
- 1
Break down complex instructions into smaller, manageable parts.
- 2
Use visual aids like charts or diagrams to illustrate key points.
- 3
Encourage team members to ask questions for clarification.
- 4
Summarize the instructions at the end to reinforce understanding.
- 5
Check comprehension by asking team members to repeat the instructions back.
Example Answers
In my previous role, I often communicated complex production schedules. I would break them down into weekly tasks, use a Gantt chart for visual reference, and hold a Q&A session afterward to clarify any doubts.
Describe a time when you identified a safety issue on the production floor and how you addressed it.
How to Answer
- 1
Start with a clear summary of the safety issue you found.
- 2
Explain how you assessed the situation and gathered facts.
- 3
Describe the steps you took to resolve the issue and prevent recurrence.
- 4
Highlight the importance of communication with your team and management.
- 5
Mention any positive outcomes from your actions, such as improved safety compliance.
Example Answers
In my previous role, I noticed that the floor was cluttered with tools and materials, creating a trip hazard. I immediately documented the issue and reported it to my supervisor. I then organized a team clean-up session and set up a daily checklist for maintenance. This not only improved safety but also boosted team morale as everyone participated.
Tell me about a time you faced strict deadlines. How did you manage your team to meet those deadlines?
How to Answer
- 1
Describe a specific project with a tight deadline.
- 2
Focus on communication and how you motivated your team.
- 3
Mention any strategies you used to prioritize tasks.
- 4
Explain how you tracked progress and adjusted the plan if necessary.
- 5
Highlight the outcome and how it impacted the team or project.
Example Answers
In my previous role, we had a production line overhaul due in three weeks. I held daily morning meetings to align the team on priorities, delegated clear tasks based on skills, and used a shared tracking tool for real-time progress updates. By fostering teamwork and maintaining open communication, we completed the project on time and improved efficiency by 15%.
Give an example of a time when you helped improve the quality standards in your production area.
How to Answer
- 1
Think of a specific project or situation where you made a significant impact.
- 2
Describe what problems you identified in quality standards.
- 3
Explain the solution you implemented and how it affected production.
- 4
Include metrics or results to demonstrate the improvement.
- 5
Show your role and leadership in making the change happen.
Example Answers
In my previous role, we faced high defect rates in our assembly line. I noticed we lacked a standardized inspection process. I developed a checklist for quality checks and trained the team. As a result, we reduced defects by 30% over three months.
Describe your approach to training new employees on your production team.
How to Answer
- 1
Assess the new hire's background and skills before training begins
- 2
Use a structured onboarding plan with clear milestones
- 3
Incorporate hands-on training alongside theoretical lessons
- 4
Encourage questions and provide immediate feedback during training
- 5
Pair new employees with experienced team members for mentorship
Example Answers
I start by understanding the new hire's previous experience, then I use a structured plan that includes both classroom learning and hands-on practice to ensure they grasp essential concepts. Regular check-ins help me gauge their understanding and adjust the pace as necessary.
How have you handled a situation where a team member's performance was not meeting expectations?
How to Answer
- 1
Identify the specific performance issue clearly
- 2
Communicate with the team member privately
- 3
Discuss the barriers they might be facing
- 4
Provide support and resources for improvement
- 5
Set clear expectations and follow up regularly
Example Answers
In a recent project, one team member was consistently missing deadlines. I scheduled a one-on-one to discuss their challenges. I learned they were struggling with time management, so I guided them on prioritizing tasks and offered to help them set up a better schedule. After that, their performance improved significantly.
Situational Interview Questions
Imagine a scenario where a critical piece of equipment fails in the middle of a large order. How would you handle the situation?
How to Answer
- 1
Assess the situation quickly to understand the impact of the failure.
- 2
Communicate promptly with the team and relevant stakeholders.
- 3
Identify alternative solutions or equipment to minimize downtime.
- 4
Implement a plan to address the failure and resume production.
- 5
Document the incident for future reference and process improvement.
Example Answers
I would start by assessing how the failure affects the current order. Then, I would inform my team and management. Next, I would look for backup equipment or reallocate resources to keep production moving. After implementing the solution, I'd document the incident to improve our response for the future.
If a key team member suddenly leaves the company, how would you address their absence in the schedule?
How to Answer
- 1
Assess the immediate impact on production schedules and workflows
- 2
Communicate with the team to understand their current workload and capabilities
- 3
Reallocate tasks among remaining team members based on skills and availability
- 4
Consider temporary solutions, such as overtime or hiring contractors, if necessary
- 5
Document the changes and keep management informed of progress and issues
Example Answers
I would first assess how critical their role is to our current production schedule. Then, I'd speak with the rest of the team to see who can take on their tasks, ensuring we don’t overload anyone. If needed, I’d explore hiring a temporary worker or arranging overtime to maintain our output.
Good Candidates Answer Questions. Great Ones Win Offers.
Reading sample answers isn't enough. Top candidates practice speaking with confidence and clarity. Get real feedback, improve faster, and walk into your next interview ready to stand out.
Master your interview answers under pressure
Boost your confidence with real-time practice
Speak clearly and impress hiring managers
Get hired faster with focused preparation
Used by hundreds of successful candidates
You have two high-priority projects with tight deadlines. How do you prioritize your team's efforts?
How to Answer
- 1
Assess the impact of each project on overall operations.
- 2
Identify critical deadlines and deliverables for both projects.
- 3
Communicate with stakeholders to clarify priorities.
- 4
Allocate resources based on project requirements and team strengths.
- 5
Monitor progress and be flexible to adjust priorities as needed.
Example Answers
I would first assess which project has the greater impact on our operational goals. Then, I'd identify the key deadlines for each project and communicate with stakeholders to ensure alignment. Based on this, I would allocate my team’s strengths to the most urgent tasks and keep monitoring progress, making adjustments if necessary.
Suppose a team member approaches you with a potential safety concern that you've not heard of before. How would you proceed?
How to Answer
- 1
Listen carefully to the team member's concern without interrupting
- 2
Ask clarifying questions to fully understand the issue
- 3
Assure the team member that safety is a priority and their concern is valid
- 4
Investigate the concern promptly by gathering more information
- 5
Develop a plan to address the concern if necessary, and communicate findings back to the team
Example Answers
I would listen to my team member attentively and ask questions to understand the safety issue. I would ensure they feel heard and valued. Then, I would look into the concern by gathering more information and consult relevant safety protocols. If the concern is serious, I would escalate it to ensure we're acting swiftly to maintain a safe environment.
If two team members are in disagreement about how to conduct a certain task, how do you resolve the dispute?
How to Answer
- 1
Listen to both team members to understand their perspectives
- 2
Encourage open communication and respect between the parties
- 3
Identify common goals that both team members share
- 4
Propose a compromise or solution that incorporates elements from both sides
- 5
If necessary, involve a third party or escalate the issue to management for further resolution
Example Answers
I would first listen carefully to both team members to understand their viewpoints. Then, I would facilitate a discussion between them to promote respect and communication. I would try to find common goals that they both agree on and suggest a solution that satisfies both perspectives.
Imagine the production budget is suddenly cut by 10%. What steps would you take to adjust?
How to Answer
- 1
Assess current expenditures and identify non-essential areas for cuts
- 2
Engage the team to gather input on efficiency improvements
- 3
Prioritize critical operations and allocate resources accordingly
- 4
Explore alternative suppliers or materials for cost savings
- 5
Implement a monitoring system to track spending effectively
Example Answers
I would begin by reviewing the budget line items to pinpoint areas where we can reduce spending without compromising quality. Engaging with my team can also reveal opportunities for efficiency that we may have overlooked previously.
How would you handle a situation where you've been tasked with increasing productivity without increasing costs?
How to Answer
- 1
Identify current bottlenecks in the production process
- 2
Implement lean manufacturing techniques to eliminate waste
- 3
Encourage team collaboration and communication for better efficiency
- 4
Invest in employee training to enhance skills without raising costs
- 5
Utilize technology to automate repetitive tasks and streamline workflows
Example Answers
I would start by analyzing our current production workflow to identify any bottlenecks. By applying lean principles, we can eliminate wasteful practices and improve overall efficiency. Additionally, I would encourage my team to suggest improvements and provide training to enhance their skills, all while exploring automation options to speed up repetitive tasks without incurring extra costs.
A new complex machine is introduced to the production line. How would you ensure your team is properly trained to operate it?
How to Answer
- 1
Assess the current skill level of the team to tailor the training.
- 2
Organize training sessions with hands-on practice on the new machine.
- 3
Utilize manufacturer resources or expert trainers to provide initial training.
- 4
Create instructional materials or reference guides for ongoing support.
- 5
Schedule follow-up assessments to ensure competence and address any questions.
Example Answers
I would start by assessing my team's current skills to understand their training needs. Then, I would organize hands-on training sessions with the new machine, possibly inviting a manufacturer representative to help. I would develop reference materials for them to use later and schedule assessments to ensure everyone is confident in operating the machine.
If you notice that our production process has a lot of downtime, how would you approach analyzing and fixing the issue?
How to Answer
- 1
Identify key metrics to measure downtime such as operational uptime and cycle time.
- 2
Conduct a root cause analysis to determine the specific reasons for the downtime.
- 3
Engage with the production team to gather insights and suggestions on the downtime causes.
- 4
Implement solutions that target the root causes and monitor their effectiveness.
- 5
Communicate the changes and results with the team to ensure continuous improvement.
Example Answers
I would start by gathering data on the downtime incidents to analyze trends and patterns. Then, I would conduct a root cause analysis to identify whether equipment failure, process inefficiencies, or workforce issues are contributing to the downtime. After pinpointing the causes, I would work with the team to develop and implement targeted solutions, such as preventive maintenance schedules or process optimization techniques, and monitor the results closely.
A major customer complains about the quality of a recent batch. What steps would you take to address and resolve the issue?
How to Answer
- 1
Acknowledge the customer's concern immediately and take it seriously
- 2
Gather specific details about the complaint from the customer
- 3
Investigate the production batch for potential quality issues
- 4
Communicate findings to the customer and outline corrective actions
- 5
Follow up after the resolution to ensure customer satisfaction
Example Answers
I would first acknowledge the customer's complaint and assure them that we take quality issues seriously. Then, I would ask for specific details regarding the quality problems they experienced. I would inspect the affected batch for any defects and assess whether changes in our process could have contributed. After identifying the issue, I would communicate my findings and proposed corrective actions to the customer. Finally, I would follow up to ensure the customer is satisfied with our resolution.
Good Candidates Answer Questions. Great Ones Win Offers.
Reading sample answers isn't enough. Top candidates practice speaking with confidence and clarity. Get real feedback, improve faster, and walk into your next interview ready to stand out.
Master your interview answers under pressure
Boost your confidence with real-time practice
Speak clearly and impress hiring managers
Get hired faster with focused preparation
Used by hundreds of successful candidates
Production Foreman Position Details
Salary Information
Recommended Job Boards
CareerBuilder
www.careerbuilder.com/jobs/production-foremanZipRecruiter
www.ziprecruiter.com/Jobs/Production-ForemanThese job boards are ranked by relevance for this position.
Related Positions
Good Candidates Answer Questions. Great Ones Win Offers.
Master your interview answers under pressure
Boost your confidence with real-time practice
Speak clearly and impress hiring managers
Get hired faster with focused preparation
Used by hundreds of successful candidates
Good Candidates Answer Questions. Great Ones Win Offers.
Master your interview answers under pressure
Boost your confidence with real-time practice
Speak clearly and impress hiring managers
Get hired faster with focused preparation
Used by hundreds of successful candidates