Top 30 Flaker Interview Questions and Answers [Updated 2025]
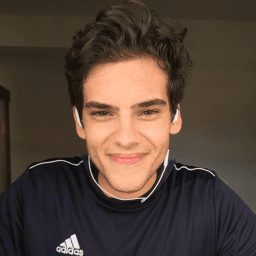
Andre Mendes
•
March 30, 2025
Preparing for a Flaker interview? Look no further! This comprehensive guide offers the most common interview questions for the Flaker role, complete with example answers and insightful tips to help you respond with confidence and finesse. Whether you're a seasoned professional or a newcomer, our updated 2025 collection will equip you with the knowledge and strategies you need to impress your interviewers.
Download Flaker Interview Questions in PDF
To make your preparation even more convenient, we've compiled all these top Flakerinterview questions and answers into a handy PDF.
Click the button below to download the PDF and have easy access to these essential questions anytime, anywhere:
List of Flaker Interview Questions
Behavioral Interview Questions
Can you describe a situation where you had to work closely with a team to meet a critical deadline as a flaker?
How to Answer
- 1
Think of a specific project where teamwork was essential.
- 2
Highlight your role and contributions to the team effort.
- 3
Emphasize communication and collaboration with teammates.
- 4
Mention any challenges faced and how they were overcome.
- 5
End with the outcome and what you learned from the experience.
Example Answers
In my last project, we had a tight deadline to deliver a new packaging design. I coordinated daily check-ins with the team to track progress and ensure everyone was on the same page. We faced some delays due to material shortages, but by communicating openly and reallocating tasks, we managed to meet our deadline successfully. This taught me the importance of flexibility and teamwork.
Tell me about a time when you encountered a significant problem during the flaking process and how you resolved it.
How to Answer
- 1
Identify a specific problem you faced during flaking.
- 2
Explain the context briefly to set the scene.
- 3
Describe the steps you took to resolve the issue.
- 4
Highlight the outcome or what you learned from the experience.
- 5
Keep your answer structured and focused on your actions.
Example Answers
During a flaking project, we faced a significant delay due to a supplier issue that caused a material shortage. I immediately communicated with our team and contacted alternative suppliers. We managed to source the materials in time, and I ensured close communication with all stakeholders. The project was completed on schedule, enhancing my problem-solving skills.
Don't Just Read Flaker Questions - Practice Answering Them!
Reading helps, but actual practice is what gets you hired. Our AI feedback system helps you improve your Flaker interview answers in real-time.
Personalized feedback
Unlimited practice
Used by hundreds of successful candidates
Describe a time when you had to lead a team in the flaking department. What challenges did you face?
How to Answer
- 1
Identify a specific project or task where you led a team.
- 2
Highlight a challenge you encountered, such as time constraints or team dynamics.
- 3
Explain your approach to solving the challenge and how you motivated your team.
- 4
Discuss the outcome and any improvements that were made as a result.
- 5
Keep your answer structured: Situation, Task, Action, Result.
Example Answers
In a recent project, I led a team responsible for increasing our flaking output by 20%. We faced a challenge with equipment maintenance that delayed our progress. I organized a meeting to prioritize the issues, and we worked overtime to keep on track. In the end, not only did we meet our goal, but we also improved equipment efficiency by 15%.
Can you provide an example of a time you had to adapt to a new procedure or change in the workplace?
How to Answer
- 1
Think of a specific change you faced at work.
- 2
Explain the situation briefly to set context.
- 3
Describe how you adapted to the new procedure.
- 4
Highlight the positive outcome of your adaptation.
- 5
Keep it concise and relevant to the Flaker position.
Example Answers
In my previous role, our team implemented a new project management software. I took the initiative to attend training sessions and helped onboard my colleagues. As a result, we improved our project tracking and communication, leading to a 20% increase in efficiency.
Give an example of how you communicated important information to your team regarding the flaking process.
How to Answer
- 1
Identify a specific situation where communication was key.
- 2
Describe the method used to convey the information (email, meeting, etc.).
- 3
Explain how you ensured the team understood the information clearly.
- 4
Include any feedback you received from the team about the communication.
- 5
Mention the outcome or impact of the communication.
Example Answers
In a team meeting, I presented a detailed slide deck on the flaking process updates. I used visuals to clarify the changes and encouraged questions to ensure understanding. The team appreciated the clarity and we implemented changes effectively.
Describe a time when you received constructive criticism about your flaking work. How did you respond?
How to Answer
- 1
Choose a specific instance where you received constructive criticism.
- 2
Explain the context of the situation and the feedback you received.
- 3
Describe how you felt about the feedback initially.
- 4
Outline the steps you took to address the criticism.
- 5
Share the positive outcome or lesson learned from the experience.
Example Answers
In a group project, I was told that my contributions were not meeting expectations. I felt defensive at first, but I took time to reflect. I met with the team leader, asked for specific examples, and focused on improving my organization. As a result, my next submissions were on time and well-received.
Tell me about a time when you took the initiative to solve a problem in the flaking line.
How to Answer
- 1
Identify a specific problem you encountered.
- 2
Explain the steps you took to address it.
- 3
Highlight the positive outcome from your actions.
- 4
Focus on your role and the initiative you showed.
- 5
Keep it concise and relevant to flaking line experience.
Example Answers
At my last job, we noticed a consistent issue with flakes sticking together. I suggested a modification to the drying process that involved adjusting the temperature settings. After implementing my changes, we reduced stickiness by 30%, improving overall production efficiency.
Have you ever suggested an improvement to the flaking process? What was your suggestion and the outcome?
How to Answer
- 1
Think of a specific suggestion you made in the past.
- 2
Describe the reason behind your suggestion and what issue it addressed.
- 3
Explain how you implemented or proposed this change.
- 4
Share the outcome including any quantifiable results.
- 5
Use the STAR method: Situation, Task, Action, Result.
Example Answers
In my previous job, I noticed that the flaking process was often slow due to manual checks. I suggested implementing a digital checklist system. I worked with the IT team to create it, and the outcome was a 20% reduction in processing time.
Don't Just Read Flaker Questions - Practice Answering Them!
Reading helps, but actual practice is what gets you hired. Our AI feedback system helps you improve your Flaker interview answers in real-time.
Personalized feedback
Unlimited practice
Used by hundreds of successful candidates
Technical Interview Questions
What types of flaking equipment are you proficient in operating?
How to Answer
- 1
List specific types of flaking equipment you have experience with
- 2
Mention any relevant certifications or training
- 3
Include examples of tasks you performed with the equipment
- 4
Emphasize safety practices and maintenance knowledge
- 5
Tailor your response to the job requirements
Example Answers
I am proficient in operating diamond flakers and slab flakers. I have a certification in using these tools and have used them to produce high-quality flake sizes for various projects while ensuring safety protocols are followed.
Can you explain the flaking process and the techniques you use to ensure efficiency?
How to Answer
- 1
Define the flaking process clearly, such as its steps and purpose.
- 2
Mention specific techniques you use, such as tools or methods that enhance efficiency.
- 3
Include any metrics or outcomes that demonstrate the effectiveness of your techniques.
- 4
Highlight teamwork or collaboration aspects if applicable.
- 5
Share a brief personal experience that illustrates your approach.
Example Answers
The flaking process involves removing or shaping materials through techniques like chipping or hammering. I ensure efficiency by using high-quality tools, calibrating them for precise control, and maintaining a consistent workflow to minimize downtime.
Don't Just Read Flaker Questions - Practice Answering Them!
Reading helps, but actual practice is what gets you hired. Our AI feedback system helps you improve your Flaker interview answers in real-time.
Personalized feedback
Unlimited practice
Used by hundreds of successful candidates
What safety protocols do you follow when operating flaking machinery?
How to Answer
- 1
Always wear appropriate personal protective equipment, including gloves and goggles.
- 2
Inspect the flaking machine for any wear or damage before each use.
- 3
Ensure all safety guards are in place and operational before starting the machine.
- 4
Follow lockout/tagout procedures when performing maintenance or repairs.
- 5
Maintain a clean work area to prevent slips, trips, or falls.
Example Answers
I always wear gloves and goggles while operating the flaker, and I check the machine for any signs of damage before use.
How do you perform routine maintenance on flaking equipment to ensure optimal performance?
How to Answer
- 1
Inspect equipment regularly for wear and tear.
- 2
Follow the manufacturer's maintenance schedule closely.
- 3
Lubricate moving parts as required to prevent friction.
- 4
Clean the equipment to remove debris and buildup.
- 5
Test the equipment after maintenance to ensure proper functionality.
Example Answers
I perform routine inspections of the flaking equipment every month, checking for any signs of wear, and following the manufacturer's maintenance schedule for lubrication and cleaning.
What are common issues that arise during flaking, and how do you troubleshoot them?
How to Answer
- 1
Identify specific issues such as uneven flakes, contamination, and equipment malfunctions
- 2
Explain common causes for these issues, like improper technique or errors in material preparation
- 3
Outline straightforward troubleshooting steps for each issue
- 4
Emphasize the importance of regular maintenance of tools and equipment
- 5
Share a brief personal experience related to troubleshooting a flaking issue
Example Answers
Common issues include uneven flakes due to inconsistent pressure during the flaking process. I troubleshoot this by ensuring uniform application and checking the pressure calibration of my equipment. Regular maintenance helps prevent this issue.
What types of materials have you experience flaking, and how do their properties affect the process?
How to Answer
- 1
Identify specific materials you have experience with, such as metals or coatings.
- 2
Discuss the properties of these materials that influence flaking characteristics.
- 3
Use examples to illustrate how you adapted your techniques based on material properties.
- 4
Highlight any challenges you faced with various materials and how you overcame them.
- 5
Emphasize safety and quality control measures relevant to the flaking process.
Example Answers
I have worked with aluminum and zinc coatings. Aluminum is lightweight and prone to surface oxidation, which can affect adhesion and flaking. I adjusted my flaking process to include pre-treatment to improve quality.
How do you assess the final output of the flaking process for quality assurance?
How to Answer
- 1
Identify key quality indicators relevant to flaking.
- 2
Use visual inspections to check for uniform thickness and color.
- 3
Conduct strength tests to evaluate structural integrity.
- 4
Implement a sampling method for thorough inspection of output batches.
- 5
Document findings and maintain records for continuous improvement.
Example Answers
I assess the final output of the flaking process by first checking for uniformity in thickness and color, which indicates consistency. Next, I perform strength tests on samples to ensure they meet our quality standards. Lastly, I keep detailed records of each batch to track performance over time.
What software or computer systems have you used to track flaking operations or quality metrics?
How to Answer
- 1
Identify specific software or tools you've used for flaking operations.
- 2
Highlight any metrics you provided through these systems.
- 3
Mention how the software improved accuracy or efficiency.
- 4
Discuss your familiarity with data analysis features in the software.
- 5
Share any relevant certifications or training related to the software.
Example Answers
In my previous role, I used SAP ERP to track flaking operations. It allowed me to monitor key quality metrics such as flake size and consistency, which improved production accuracy by 20%.
What industry standards are applicable to the flaking process, and how do you ensure compliance?
How to Answer
- 1
Identify relevant industry standards like ISO 9001, ASTM, or any specific regulations for your field.
- 2
Explain the steps you take to stay updated on these standards.
- 3
Discuss your methods for training staff on compliance requirements.
- 4
Mention how you implement quality control measures in the flaking process.
- 5
Provide examples of audits or assessments you conduct to ensure adherence.
Example Answers
In my experience, standards like ISO 9001 are crucial for the flaking process. I regularly review updates to these standards and ensure my team receives training on them. We implement quality controls such as regular checks during production and perform internal audits to maintain compliance.
How do you measure your personal performance as a flaker?
How to Answer
- 1
Identify specific goals related to flaking that you want to achieve
- 2
Track the number of successful flake deliveries over a set period
- 3
Assess the quality of flakes based on feedback from peers or supervisors
- 4
Evaluate your adaptability in managing unexpected challenges
- 5
Reflect regularly on your progress and areas for improvement
Example Answers
I measure my performance by setting clear goals for each week, such as aiming to complete at least 20 successful flakes. I also seek feedback on my work to continually improve and adapt my approach based on that input.
Don't Just Read Flaker Questions - Practice Answering Them!
Reading helps, but actual practice is what gets you hired. Our AI feedback system helps you improve your Flaker interview answers in real-time.
Personalized feedback
Unlimited practice
Used by hundreds of successful candidates
Situational Interview Questions
If you notice a sudden drop in production quality while flaking, what steps would you take to investigate the issue?
How to Answer
- 1
Check for recent changes in equipment settings or maintenance.
- 2
Review production logs for any inconsistencies or anomalies.
- 3
Inspect the raw materials for quality or contamination.
- 4
Consult with team members to gather their observations.
- 5
Conduct a test run to identify if the issue persists.
Example Answers
First, I would check if there have been any recent changes to the equipment settings or maintenance that could affect quality. Then, I would review the production logs to identify any patterns in the drop. Next, I would inspect the raw materials to ensure they haven't changed and are up to standard. Finally, I'd discuss with my team to see if anyone has noticed something unusual.
Imagine you have conflicting priorities between quality and speed during the flaking process. How would you handle this situation?
How to Answer
- 1
Assess the impact of quality versus speed on the project outcomes
- 2
Communicate with your team and stakeholders about priorities
- 3
Identify which aspects of quality can be compromised without major issues
- 4
Consider implementing a phased approach to balance both priorities
- 5
Document the decision-making process to maintain transparency
Example Answers
I would first evaluate how critical the quality is to the project's success and discuss with my team to reach a consensus. If speed is essential, I might focus on areas where we can reduce effort without impacting the end result significantly.
Don't Just Read Flaker Questions - Practice Answering Them!
Reading helps, but actual practice is what gets you hired. Our AI feedback system helps you improve your Flaker interview answers in real-time.
Personalized feedback
Unlimited practice
Used by hundreds of successful candidates
What would you do if a team member was consistently underperforming in their flaking duties?
How to Answer
- 1
Identify the specific areas where the team member is underperforming.
- 2
Initiate a private conversation to discuss performance issues directly.
- 3
Offer support and resources to help them improve.
- 4
Set clear expectations and goals for future performance.
- 5
Monitor progress and provide feedback regularly.
Example Answers
I would first identify the specific tasks they struggle with. Then, I'd have a private chat to discuss my observations and see if they face any challenges. I would offer my help and provide resources to support them. After that, I’d set clear goals and check in regularly to see how they're improving.
How would you assess whether a new flaking technique should be adopted in your workplace?
How to Answer
- 1
Review existing data on current techniques and their performance metrics.
- 2
Conduct a pilot test of the new technique on a small scale.
- 3
Gather feedback from team members involved in the pilot.
- 4
Evaluate cost implications versus expected benefits of the new technique.
- 5
Consider alignment with long-term production goals and quality standards.
Example Answers
First, I would analyze our current flaking techniques and their success rates. Next, I'd implement a small-scale pilot of the new technique to see how it performs. After gathering feedback from my team on the pilot, I'd assess the costs and benefits compared to our current methods before making a decision.
If you were tasked with training new employees in the flaking department, what key points would you emphasize?
How to Answer
- 1
Highlight safety protocols as the top priority.
- 2
Demonstrate the correct use of flaking equipment through hands-on training.
- 3
Explain the importance of precision and quality control in the flaking process.
- 4
Encourage teamwork and communication among employees.
- 5
Provide a clear overview of procedures and troubleshooting tips.
Example Answers
I would emphasize safety protocols first, ensuring that everyone understands the importance of wearing protective gear. Then, I would demonstrate how to properly use the flaking equipment, allowing new employees to practice under supervision.
What would you do if there was a disagreement within your team about the best flaking practices?
How to Answer
- 1
Listen to all team members and understand their viewpoints
- 2
Encourage open discussion to foster collaboration
- 3
Identify common goals related to flaking outcomes
- 4
Propose a trial period for different practices to see which works best
- 5
Document the findings and make a collective decision based on observed results
Example Answers
I would first listen to each team member's perspective on flaking practices. Then, I would facilitate a meeting where everyone can share their thoughts openly. To resolve the disagreement, I might suggest we try different methods for a short period and evaluate the outcomes together to decide which approach is best.
How would you respond if a flaking machine malfunctioned and you had a tight deadline to meet?
How to Answer
- 1
Assess the situation quickly to understand the nature of the malfunction
- 2
Communicate promptly with your supervisor or team about the issue
- 3
Determine if there are quick fixes or workarounds available
- 4
Prioritize tasks to ensure critical deadlines are still met
- 5
Be prepared to report the incident and suggest improvements after resolving the issue
Example Answers
I would first assess the malfunction to identify the issue. Then, I would inform my supervisor about the situation and discuss potential quick fixes or if we needed alternate solutions. Meanwhile, I would reorganize my workload to focus on the most critical tasks so that we could still meet our deadline.
If you were required to document the flaking process for compliance purposes, what key areas would you cover?
How to Answer
- 1
Identify each step in the flaking process clearly.
- 2
Include safety protocols and compliance regulations that apply.
- 3
Document equipment used and maintenance schedules.
- 4
Note any quality control measures taken throughout the process.
- 5
Provide a summary of roles and responsibilities for staff involved.
Example Answers
I would begin by detailing the steps of the flaking process, including the inputs and outputs. I would then include relevant safety regulations, list the equipment and its maintenance records, outline quality control checks, and clarify the roles of each team member in the process.
If you witnessed a colleague cutting corners in the flaking process, how would you address the situation?
How to Answer
- 1
Stay calm and assess the situation clearly before taking action
- 2
Consider discussing your observations directly with the colleague first
- 3
Emphasize the importance of quality and safety in flaking
- 4
If necessary, escalate the issue to a supervisor or manager
- 5
Document your observations to provide context if needed
Example Answers
I would first approach my colleague and share my concerns about their process, highlighting how it could affect quality. If they are unresponsive, I would then report my observations to a supervisor.
If you are running low on raw materials crucial for flaking, what steps would you take?
How to Answer
- 1
Assess the current inventory and identify exact shortages.
- 2
Communicate with suppliers to determine lead times for replenishment.
- 3
Explore alternative suppliers or substitute materials if possible.
- 4
Evaluate production scheduling to manage the impact of shortages.
- 5
Implement a preventive measure for future shortages, like maintaining a minimum stock level.
Example Answers
First, I would check the inventory to find out which materials are low. Then, I would reach out to our suppliers to confirm when we can expect new deliveries. If the lead time is too long, I would look for backup suppliers or substitute materials. I would also adjust production schedules to minimize disruptions. Finally, I would recommend implementing a policy to maintain higher safety stocks in the future.
Don't Just Read Flaker Questions - Practice Answering Them!
Reading helps, but actual practice is what gets you hired. Our AI feedback system helps you improve your Flaker interview answers in real-time.
Personalized feedback
Unlimited practice
Used by hundreds of successful candidates
Ace Your Next Interview!
Practice with AI feedback & get hired faster
Personalized feedback
Used by hundreds of successful candidates
Ace Your Next Interview!
Practice with AI feedback & get hired faster
Personalized feedback
Used by hundreds of successful candidates