Top 29 Fleet Mechanic Interview Questions and Answers [Updated 2025]
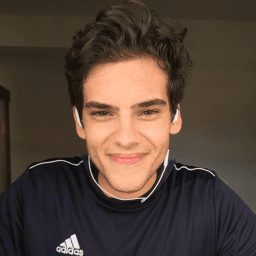
Andre Mendes
•
March 30, 2025
Preparing for a fleet mechanic interview can be daunting, but having the right questions and answers at your fingertips can make all the difference. In this post, we delve into the most common interview questions for the fleet mechanic role, providing you with example answers and practical tips to help you respond effectively. Get ready to boost your confidence and secure that job with our comprehensive guide.
Download Fleet Mechanic Interview Questions in PDF
To make your preparation even more convenient, we've compiled all these top Fleet Mechanicinterview questions and answers into a handy PDF.
Click the button below to download the PDF and have easy access to these essential questions anytime, anywhere: