Top 32 Gauge Checker Interview Questions and Answers [Updated 2025]
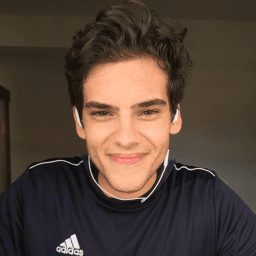
Andre Mendes
•
March 30, 2025
Preparing for a Gauge Checker interview? This post is your ultimate guide to acing it! We've compiled the most common interview questions for the Gauge Checker role, complete with example answers and practical tips to help you respond effectively. Whether you're a seasoned professional or just starting out, these insights will boost your confidence and enhance your interview performance. Dive in and get ready to impress!
Download Gauge Checker Interview Questions in PDF
To make your preparation even more convenient, we've compiled all these top Gauge Checkerinterview questions and answers into a handy PDF.
Click the button below to download the PDF and have easy access to these essential questions anytime, anywhere:
List of Gauge Checker Interview Questions
Behavioral Interview Questions
Can you describe a time when you identified a significant issue with a gauge reading and how you resolved it?
How to Answer
- 1
Select a specific instance with clear details.
- 2
Explain the gauge reading issue clearly, using technical terms if appropriate.
- 3
Describe the steps you took to investigate and resolve the issue.
- 4
Highlight any collaboration with team members or supervisors.
- 5
Mention the outcome and what you learned from the experience.
Example Answers
In my previous job, I noticed that a pressure gauge consistently read 10 PSI higher than the actual value. I double-checked the calibration and found it was off. I recalibrated the gauge and informed my supervisor. This resolved the issue, ensuring accurate readings.
Tell me about a project where your attention to detail directly impacted the outcome.
How to Answer
- 1
Choose a specific project that showcases your attention to detail.
- 2
Describe your role and the importance of detail in that project.
- 3
Explain the specific actions you took to ensure accuracy or thoroughness.
- 4
Highlight the positive outcome or results that resulted from your attention to detail.
- 5
Keep your answer focused and relevant, using concrete examples.
Example Answers
In a previous role as a product inspector, I worked on a quality control project where I meticulously checked each item against specifications. My attention to detail helped identify a batch with a critical defect that could have led to product failure in the field, preventing costly recalls.
Don't Just Read Gauge Checker Questions - Practice Answering Them!
Reading helps, but actual practice is what gets you hired. Our AI feedback system helps you improve your Gauge Checker interview answers in real-time.
Personalized feedback
Unlimited practice
Used by hundreds of successful candidates
Describe a situation where you had to adjust your approach due to unexpected changes in gauge calibration standards.
How to Answer
- 1
Identify a specific instance where calibration standards changed unexpectedly.
- 2
Explain the impact of these changes on your work process or project.
- 3
Discuss the steps you took to adapt to the new standards.
- 4
Highlight any collaboration with team members or stakeholders.
- 5
Reflect on the outcome and what you learned from the experience.
Example Answers
In my previous role, we received a sudden update on gauge calibration standards that affected our production line. I immediately organized a team meeting to discuss the new requirements and developed a new calibration schedule. We worked together to retrain staff on the updated procedures, which ensured compliance. Ultimately, we maintained our production targets without any loss in quality, and I learned the importance of flexibility and teamwork in adapting to changes.
How have you effectively communicated technical information to non-technical team members in the past?
How to Answer
- 1
Use analogies to relate technical concepts to everyday experiences
- 2
Break down complex information into simple, digestible parts
- 3
Encourage questions to ensure understanding
- 4
Use visual aids like diagrams or charts when possible
- 5
Provide practical examples that illustrate the points you are making
Example Answers
In my previous role, I explained a software update to marketing by using a bakery analogy, comparing software bugs to missing ingredients, which helped them understand the need for thorough testing.
Give an example of a time you went above and beyond your normal responsibilities in your gauge checking role.
How to Answer
- 1
Think of a specific situation where you identified a problem outside your regular tasks.
- 2
Describe how you took initiative to resolve the issue effectively.
- 3
Quantify the impact of your actions where possible to illustrate success.
- 4
Emphasize teamwork or collaboration if applicable to showcase your communication skills.
- 5
Conclude with a reflection on what you learned or how it benefited the team.
Example Answers
In my previous role, I noticed that our gauge calibration process was causing delays. I took the initiative to analyze the workflow and proposed a new scheduling system that reduced downtime. This not only improved efficiency by 20% but also allowed the team to handle more projects consecutively.
Can you discuss a time when you received constructive feedback on your work as a gauge checker? How did you react?
How to Answer
- 1
Think of a specific example from your experience.
- 2
Describe the feedback you received clearly and honestly.
- 3
Explain how you felt and reacted to the feedback.
- 4
Discuss the steps you took to improve based on the feedback.
- 5
Share the outcome and how it benefited your work.
Example Answers
In my previous job, I received feedback about my calibration process being slightly off. Initially, I felt disappointed, but I took it as an opportunity to learn. I reviewed the calibration guidelines thoroughly and sought advice from a senior checker. As a result, my accuracy improved, and I became more diligent in following procedures.
What motivates you to perform your best as a gauge checker?
How to Answer
- 1
Emphasize attention to detail as a key motivator.
- 2
Mention the importance of accuracy in ensuring quality.
- 3
Highlight personal pride in contributing to overall safety.
- 4
Discuss a passion for continuous improvement and learning.
- 5
Share a specific example that aligns with your motivation.
Example Answers
I am motivated by my attention to detail and the responsibility that comes with ensuring that all gauges provide accurate measurements, as this directly affects safety and quality in production.
Can you provide an example of how your gauge checking work positively impacted your previous employer's operations?
How to Answer
- 1
Choose a specific project or task where you performed gauge checking.
- 2
Explain the issue you identified and how it affected operations.
- 3
Describe the solution you implemented or recommended.
- 4
Quantify the results if possible, like time saved or error reduction.
- 5
Highlight any feedback from supervisors or team members.
Example Answers
In my previous role, I identified inaccuracies in calibration of our assembly line gauges. This was causing delays in production. I recalibrated the gauges and improved the accuracy by 30%, which reduced production errors and increased output by 15%. My supervisor noted the significant positive impact on our efficiency.
Don't Just Read Gauge Checker Questions - Practice Answering Them!
Reading helps, but actual practice is what gets you hired. Our AI feedback system helps you improve your Gauge Checker interview answers in real-time.
Personalized feedback
Unlimited practice
Used by hundreds of successful candidates
How do you handle stress or pressure when monitoring gauge output in a busy work environment?
How to Answer
- 1
Stay organized and prioritize tasks to focus on essential metrics.
- 2
Use deep breathing techniques to maintain calmness during high-pressure moments.
- 3
Take regular short breaks to clear your mind and reset focus.
- 4
Communicate effectively with the team to ensure support and clarity on tasks.
- 5
Practice time management to manage workload and avoid feeling overwhelmed.
Example Answers
I handle stress by prioritizing gauge metrics based on urgency, using deep breathing to stay calm, and communicating clearly with my team for support.
Technical Interview Questions
What types of gauges are you familiar with, and how do you determine which to use in a given situation?
How to Answer
- 1
List specific types of gauges you have worked with such as calipers, micrometers, or dial indicators.
- 2
Explain the characteristics of each gauge type and their typical applications.
- 3
Mention how precision required and the type of measurement influence gauge selection.
- 4
Provide an example of a situation and the gauge chosen for that task.
- 5
Emphasize any experience with calibration or maintenance of gauges.
Example Answers
I am familiar with calipers, micrometers, and dial indicators. I choose calipers for measuring larger dimensions and micrometers for precise thickness measurements. For instance, if I need to check a part's diameter, I would use a micrometer because it offers greater accuracy.
Can you explain the process of calibrating a gauge and why it's important?
How to Answer
- 1
Start by defining gauge calibration clearly
- 2
Describe the step-by-step process of calibration
- 3
Emphasize the importance of accuracy in measurements
- 4
Mention specific standards or methods used
- 5
Conclude with the implications of improper calibration
Example Answers
Calibrating a gauge involves comparing its readings against a known standard. First, you set up the gauge, then measure the standard, and finally adjust the gauge if necessary. This process is crucial for ensuring accuracy in measurements to maintain quality control.
Don't Just Read Gauge Checker Questions - Practice Answering Them!
Reading helps, but actual practice is what gets you hired. Our AI feedback system helps you improve your Gauge Checker interview answers in real-time.
Personalized feedback
Unlimited practice
Used by hundreds of successful candidates
What methods do you use to ensure measurement accuracy in gauge checks?
How to Answer
- 1
Calibrate gauges regularly according to the manufacturer's specifications
- 2
Use standard reference measurements to verify accuracy
- 3
Perform checks in controlled environments to minimize external factors
- 4
Document all measurements and discrepancies for review
- 5
Train regularly to stay updated on best practices and technology
Example Answers
I ensure measurement accuracy by calibrating gauges according to the manufacturer's specifications regularly. I also cross-check measurements with standard references to verify their accuracy.
What industry standards do you follow when performing gauge checks?
How to Answer
- 1
Research relevant standards like ISO, ANSI, and ASME specific to your industry.
- 2
Highlight any specific protocols you follow in your current role.
- 3
Mention how you ensure compliance with calibration frequencies and procedures.
- 4
Discuss the importance of traceability and documentation in gauge checking.
- 5
Emphasize continuous learning and staying updated with industry best practices.
Example Answers
I follow ISO 9001 standards, ensuring all gauges are calibrated according to schedule. I document each calibration and maintain traceability to confirm compliance.
Describe your experience with using digital gauges versus manual gauges. What are the pros and cons of each?
How to Answer
- 1
Define your experience with both types of gauges clearly
- 2
List key advantages of digital gauges, like accuracy and ease of use
- 3
Mention benefits of manual gauges, such as reliability and simplicity
- 4
Discuss any personal experiences that illustrate your points
- 5
Be prepared to explain your preference and why it matters for the role
Example Answers
I have used both digital and manual gauges in my previous job. Digital gauges are more accurate and easier to read, which speeds up measurements. However, I find manual gauges are very reliable in tough environments because they don't rely on batteries. Overall, I prefer digital for most tasks, but I carry a manual as a backup.
How do you interpret data from gauge readings to make informed decisions?
How to Answer
- 1
Focus on understanding the measurements and what they indicate about the process or product.
- 2
Use statistical analysis to identify trends or anomalies in the data.
- 3
Prioritize accuracy and calibration of gauges to ensure reliable data.
- 4
Compare readings against specifications to determine compliance.
- 5
Communicate findings and recommendations clearly to team members.
Example Answers
I analyze the gauge readings by first ensuring all measuring tools are calibrated correctly. Then, I look for patterns in the data over time, and if I notice any deviations from expected results, I investigate further by checking other related parameters. This helps me make informed decisions about process adjustments or quality control.
What tools do you consider essential for effectively performing gauge checks?
How to Answer
- 1
Start with the primary tools like calipers and micrometers.
- 2
Mention software tools if applicable, for data recording.
- 3
Discuss the importance of maintaining tools for accuracy.
- 4
Consider safety tools, such as gloves and goggles, if relevant.
- 5
End with a brief mention of training or skill in using the tools.
Example Answers
I believe essential tools for gauge checks include calipers and micrometers for precise measurements. Additionally, I find software tools like Excel helpful for recording data efficiently. Regular maintenance of these tools is key to ensuring their accuracy.
What steps do you take when you need to report a gauge issue to your supervisor?
How to Answer
- 1
Identify the specific gauge and issue clearly
- 2
Document the issue with details such as time and conditions
- 3
Notify your supervisor immediately and verbally report the issue
- 4
Provide any supporting data or evidence related to the gauge
- 5
Follow up to ensure the issue is addressed and resolved
Example Answers
I first identify the gauge and describe the specific problem I'm experiencing. Then, I document all relevant details including when it happened. I notify my supervisor immediately and give a brief verbal report. I also provide any supporting data I have. Finally, I make sure to follow up later to confirm the issue has been resolved.
Describe your approach to troubleshooting gauges that consistently fail calibration.
How to Answer
- 1
Start by reviewing the calibration records to identify patterns in failures.
- 2
Check for environmental factors that may affect the gauge's performance.
- 3
Inspect the physical condition of the gauges for signs of wear or damage.
- 4
Cross-reference with standard operating procedures to ensure proper usage.
- 5
Test the gauges with known standards to isolate the issue.
Example Answers
I begin by analyzing previous calibration records to spot any recurring issues, which helps me determine if the problem is environmental or mechanical. Next, I examine the gauges for any physical damage and verify they are used according to standard procedures.
What regulatory requirements must be considered when performing gauge checks in your industry?
How to Answer
- 1
Identify key industry standards relevant to gauge accuracy.
- 2
Discuss calibration requirements and frequency based on regulations.
- 3
Mention documentation practices and record-keeping mandates.
- 4
Highlight any specific safety regulations governing gauge use.
- 5
Consider environmental factors that may affect gauge performance.
Example Answers
In our industry, we adhere to ISO 9001 standards, which dictate that all gauges must be calibrated annually. Additionally, we maintain thorough documentation of all calibration records as required by regulatory compliance.
Don't Just Read Gauge Checker Questions - Practice Answering Them!
Reading helps, but actual practice is what gets you hired. Our AI feedback system helps you improve your Gauge Checker interview answers in real-time.
Personalized feedback
Unlimited practice
Used by hundreds of successful candidates
Situational Interview Questions
Imagine you discover that a gauge has been giving inaccurate readings. What steps would you take to investigate and resolve the issue?
How to Answer
- 1
Check the gauge calibration to ensure it is set correctly.
- 2
Inspect the gauge for any physical damage or wear.
- 3
Verify the environmental conditions affecting the gauge's performance.
- 4
Cross-reference readings with a backup gauge or standard for reliability.
- 5
Document findings and implement a corrective action plan.
Example Answers
First, I would check the gauge calibration to make sure it's accurate. Then, I'd look for any signs of physical damage. After that, I'd verify the conditions around the gauge. If needed, I'd compare its readings to another gauge. Finally, I'd document the issue and follow up with corrective actions.
If a colleague disagreed with your method of gauge checking, how would you handle the situation?
How to Answer
- 1
Acknowledge their perspective respectfully
- 2
Ask questions to understand their concerns better
- 3
Explain your method clearly and why you chose it
- 4
Discuss possible compromises or alternatives
- 5
Focus on the goal of accuracy and quality outcomes
Example Answers
I would listen to my colleague's concerns, ask for their reasoning, and explain my gauge checking method. If we still disagreed, I would suggest we try both methods on a trial basis to see which one yields better results.
Don't Just Read Gauge Checker Questions - Practice Answering Them!
Reading helps, but actual practice is what gets you hired. Our AI feedback system helps you improve your Gauge Checker interview answers in real-time.
Personalized feedback
Unlimited practice
Used by hundreds of successful candidates
How would you prioritize your tasks if you were under tight deadlines and discovered multiple gauges were out of calibration?
How to Answer
- 1
Assess the severity and impact of each gauge's calibration issue
- 2
Identify any gauges that are critical to immediate operations
- 3
Communicate with the team to understand workload and support needs
- 4
Create a prioritized list based on urgency and importance
- 5
Address the gauges one by one or in batches if possible to maximize efficiency
Example Answers
I would first identify which gauges are crucial for safety and production. I would tackle the most critical ones first and coordinate with my team to ensure we meet deadlines effectively. After addressing the urgent calibrations, I would schedule the rest based on their impact on operations.
What would you do if you encountered a gauge malfunction during a critical production run?
How to Answer
- 1
Immediately stop the production process to prevent defective products.
- 2
Notify the supervisor or shift manager about the malfunction.
- 3
Isolate the affected equipment to ensure safety.
- 4
Attempt to troubleshoot the gauge issue following standard operating procedures.
- 5
Document the malfunction and the steps taken for future reference.
Example Answers
I would stop the production line immediately to prevent any quality issues. Then, I'd inform my supervisor about the malfunction. After that, I would isolate the gauge and attempt to troubleshoot based on the guidelines provided in our SOP.
How would you approach training a new team member on gauge checking procedures?
How to Answer
- 1
Start with an overview of gauge checking and its importance in quality control.
- 2
Demonstrate the gauge checking process in a hands-on session.
- 3
Encourage the new team member to perform the checks under supervision.
- 4
Provide clear documentation and resources for reference.
- 5
Schedule follow-up sessions to address questions and reinforce learning.
Example Answers
I would begin by explaining the significance of gauge checking in maintaining quality standards. Then, I would demonstrate the process step-by-step. After that, I would allow the new team member to try it out with my guidance to ensure they understand it properly.
If you had the opportunity to suggest an improvement in gauge checking processes, what would it be?
How to Answer
- 1
Identify a specific area of the current process that could be more efficient
- 2
Consider incorporating new technology or tools that could aid in accuracy
- 3
Think about ways to simplify documentation or reporting processes
- 4
Propose training or skill development for gauge checkers to enhance performance
- 5
Assess how safety and compliance can be improved through your suggestion
Example Answers
I would suggest implementing a digital tracking system for gauge checks. It could reduce errors in documentation and streamline the process by allowing real-time updates.
You have several pieces of equipment that need gauge checking. How would you prioritize them?
How to Answer
- 1
Identify critical equipment that impacts safety or operations
- 2
Evaluate the last calibration dates and frequency of use
- 3
Consider the consequences of using uncalibrated gauges
- 4
Group equipment by similar types for efficient checking
- 5
Communicate with team members for any specific priorities
Example Answers
I would first prioritize equipment that is crucial for safety, then look at the last calibration dates to ensure we check those that haven’t been done recently.
How would you handle a situation where you find a persistent error in gauge readings that affects quality assurance?
How to Answer
- 1
Identify the source of the error immediately
- 2
Communicate the issue to the quality assurance team and management
- 3
Document the findings and the steps taken to investigate
- 4
Implement corrective actions and monitor results closely
- 5
Follow up with training or updates to prevent future occurrences
Example Answers
I would first investigate the gauge readings to determine the source of the error. Then, I would inform the quality assurance team and management of the issue. After documenting my findings, I would implement corrective actions and monitor the readings to ensure accuracy. Finally, I’d suggest additional training for staff to prevent similar issues.
How would you approach the integration of new technology into existing gauge checking processes?
How to Answer
- 1
Evaluate the current processes and identify areas for improvement.
- 2
Research and select technology that complements existing systems.
- 3
Develop a clear implementation plan with timelines and training.
- 4
Pilot the new technology in a controlled environment before full rollout.
- 5
Gather feedback from users to refine the integration.
Example Answers
I would first assess our current gauge checking processes to find bottlenecks. Then, I'd research technologies that enhance accuracy and efficiency, choose the right one, and create a detailed plan for implementation, including training sessions for the team.
How would you decide whether to recommend a gauge for repair or replacement?
How to Answer
- 1
Assess the gauge's age and condition first
- 2
Check the cost of repairs versus replacement value
- 3
Consider the frequency of previous repair issues
- 4
Evaluate the impact of gauge failure on operations
- 5
Consult manufacturer guidelines for repair limits
Example Answers
I would first look at how old the gauge is and its current condition. If it's past its recommended lifespan or frequently fails, I would consider recommending a replacement instead of repairs.
Don't Just Read Gauge Checker Questions - Practice Answering Them!
Reading helps, but actual practice is what gets you hired. Our AI feedback system helps you improve your Gauge Checker interview answers in real-time.
Personalized feedback
Unlimited practice
Used by hundreds of successful candidates
If you were missing a crucial tool for gauge checking, what alternative solutions would you consider?
How to Answer
- 1
Identify the specific tool that is missing
- 2
Consider using other available tools for a similar purpose
- 3
Think of creative workarounds or methods
- 4
Consult with team members for advice or alternative solutions
- 5
Document the incident to avoid future issues
Example Answers
If a caliper is missing, I would use a micrometer if available, or I could find a ruler for rough measurements while ensuring these are noted as estimates.
Gauge Checker Position Details
Related Positions
- Scale Tester
- Gage Maker
- Gas Tester
- Gas Inspector
- Bill Checker
- Metal Tester
- Air Tester
- Design Checker
- Gasoline Tester
- Battery Inspector
Similar positions you might be interested in.
Ace Your Next Interview!
Practice with AI feedback & get hired faster
Personalized feedback
Used by hundreds of successful candidates
Ace Your Next Interview!
Practice with AI feedback & get hired faster
Personalized feedback
Used by hundreds of successful candidates