Top 32 Gage Maker Interview Questions and Answers [Updated 2025]
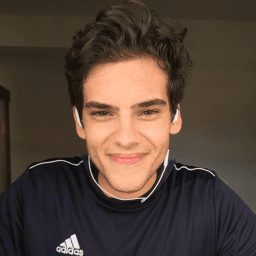
Andre Mendes
•
March 30, 2025
Preparing for a Gage Maker interview can be daunting, but this comprehensive guide is here to help you succeed. Dive into the most common interview questions tailored for the Gage Maker role, complete with insightful example answers and practical tips for crafting your responses effectively. Whether you're a seasoned professional or just starting out, this post will equip you with the knowledge and confidence to ace your interview.
Download Gage Maker Interview Questions in PDF
To make your preparation even more convenient, we've compiled all these top Gage Makerinterview questions and answers into a handy PDF.
Click the button below to download the PDF and have easy access to these essential questions anytime, anywhere:
List of Gage Maker Interview Questions
Behavioral Interview Questions
Can you describe a time when you had to troubleshoot a problem with a gauge you had manufactured?
How to Answer
- 1
Talk about a specific problem you encountered with a gauge.
- 2
Explain the steps you took to identify the issue.
- 3
Describe how you implemented a solution and what the outcome was.
- 4
Emphasize teamwork if others were involved in troubleshooting.
- 5
Highlight what you learned from the experience and how it improved future work.
Example Answers
In my previous job, we had a precision gauge that was consistently reading higher than expected. I checked the calibration against a known standard and found it was out of spec. I recalibrated the gauge, corrected the settings, and conducted a series of tests to confirm accuracy. This not only fixed the issue but also improved our overall quality checks by incorporating more frequent calibration checks.
Tell me about an experience where your attention to detail made a significant difference in your work.
How to Answer
- 1
Choose a specific situation that highlights your attention to detail.
- 2
Explain the context and your role in the task.
- 3
Describe the actions you took that demonstrated your attention to detail.
- 4
Discuss the positive outcome that resulted from your attention to detail.
- 5
Keep your answer focused and relevant to the skills needed for the Gage Maker position.
Example Answers
In my previous role as a quality inspector, I was responsible for reviewing machining parts. Once, I noticed a slight deviation in the measurements of a batch of gauges. I double-checked my findings against the specifications, and my attention to detail prevented us from sending out defective products, which would have led to costly returns.
Don't Just Read Gage Maker Questions - Practice Answering Them!
Reading helps, but actual practice is what gets you hired. Our AI feedback system helps you improve your Gage Maker interview answers in real-time.
Personalized feedback
Unlimited practice
Used by hundreds of successful candidates
Describe a situation where you worked closely with a team to complete a project related to gage manufacturing.
How to Answer
- 1
Focus on a specific project and your role within the team
- 2
Highlight collaboration and communication with team members
- 3
Mention any challenges faced and how the team overcame them
- 4
Emphasize the outcome and what you learned from the experience
- 5
Relate the experience to the skills needed for gage manufacturing
Example Answers
In my last position, I worked on a project to develop a new set of precision gauges. I collaborated with engineers and technicians, dividing tasks based on our strengths. We faced a calibration issue, but through daily meetings, we identified the problem and tested solutions together. Ultimately, we met our deadline and improved the calibration accuracy by 20%. This taught me the importance of team communication and problem-solving.
Can you give an example of a difficult decision you had to make regarding materials or processes in gage making?
How to Answer
- 1
Think of a specific situation where you faced a tough choice.
- 2
Focus on the factors you considered in making your decision.
- 3
Describe the outcome and what you learned from the experience.
- 4
Use metrics, if possible, to showcase the impact of your decision.
- 5
Make sure to highlight your problem-solving and analytical skills.
Example Answers
In a project, I had to choose between two types of steel for a gage. One was more cost-effective but had lower durability, while the other offered better longevity. After evaluating the long-term impact on maintenance costs, I decided on the durable option. This choice reduced failures and ultimately saved the company time and money in repairs.
Have you ever faced a conflict while working on a project? How did you handle it?
How to Answer
- 1
Identify a specific conflict scenario you experienced.
- 2
Describe the main issue and parties involved briefly.
- 3
Explain your approach to resolving the conflict and the actions you took.
- 4
Highlight the positive outcome or what you learned from the experience.
- 5
Keep it professional and focus on problem-solving.
Example Answers
In a team project, I faced a conflict when two team members disagreed on the project direction. I facilitated a meeting where each could express their views. We collaboratively listed pros and cons, which helped us reach a consensus. The project moved forward smoothly and we delivered successfully.
Describe an innovative solution you implemented in your previous gage-making role.
How to Answer
- 1
Think of a specific project where you introduced a new idea or method.
- 2
Focus on the problem you faced and the innovative solution you created.
- 3
Highlight the impact of your solution on efficiency, accuracy, or cost.
- 4
Use metrics or results to quantify the success of your innovation.
- 5
Be ready to discuss the steps you took to implement the solution.
Example Answers
In my previous gage-making role, I noticed that our measurement process was slow and prone to error. I developed a jig that allowed us to hold parts securely while measuring, which sped up our workflow by 30% and improved accuracy. This innovation reduced our production time significantly.
How have you kept your skills current in the evolving field of gage making?
How to Answer
- 1
Mention specific training courses or certifications you've completed.
- 2
Discuss staying up-to-date with industry trends through journals and webinars.
- 3
Highlight collaboration with peers in gage making or related fields.
- 4
Talk about hands-on experience with new technologies or tools.
- 5
Share any participation in professional organizations or events.
Example Answers
I recently completed a certification in advanced metrology, which helped me understand the latest techniques in gage making. I also subscribe to several industry journals to stay informed about new innovations.
Have you worked with other departments such as engineering or sales? How was that experience?
How to Answer
- 1
Identify specific departments you have collaborated with.
- 2
Describe the context of the collaboration and your role.
- 3
Highlight any challenges faced and how you overcame them.
- 4
Mention any positive outcomes or successes from the collaboration.
- 5
Convey the importance of teamwork and cross-department communication.
Example Answers
In my previous role, I worked closely with the engineering team to streamline the gage design process. We faced some initial miscommunication, but by setting up regular check-ins, we improved our workflow and reduced design time by 15%.
Describe a time when you had to adapt to a change in project requirements or specifications.
How to Answer
- 1
Identify a specific project where requirements changed.
- 2
Explain the change and why it happened.
- 3
Describe your immediate reaction and steps taken.
- 4
Show how you communicated with your team and stakeholders.
- 5
Highlight the outcome and what you learned from the experience.
Example Answers
In my last project, we were initially tasked with developing a simple gage tool. Midway through, the client requested additional features for precision measurement. I quickly arranged a team meeting to discuss the new requirements and delegated tasks. We successfully integrated the changes and delivered the updated tool on time, which impressed the client and strengthened our relationship.
Don't Just Read Gage Maker Questions - Practice Answering Them!
Reading helps, but actual practice is what gets you hired. Our AI feedback system helps you improve your Gage Maker interview answers in real-time.
Personalized feedback
Unlimited practice
Used by hundreds of successful candidates
Tell me about a time when you went above and beyond for a client during a gage project.
How to Answer
- 1
Describe the specific client need or challenge.
- 2
Explain the extra steps you took to meet their needs.
- 3
Highlight the positive outcome for the client.
- 4
Include any feedback you received from the client.
- 5
Keep the story concise and focused on your actions.
Example Answers
During a gage project for a key client, they faced a critical deadline. I worked late to ensure we delivered the gages ahead of schedule, even coordinating additional resources. The client appreciated our commitment and praised us for our reliability.
Technical Interview Questions
What specific measuring techniques do you employ when creating a precision gage?
How to Answer
- 1
Identify key measurement tools you use such as micrometers or calipers.
- 2
Explain how you ensure accuracy in measurements, like calibration processes.
- 3
Discuss specific techniques like shadow graph or optical methods.
- 4
Mention how you handle tolerances and precision requirements.
- 5
Share any experience with digital measurement systems or software.
Example Answers
I primarily use micrometers and calipers for initial measurements. I ensure accuracy by calibrating these tools regularly and using them in controlled environments. For highly precise applications, I employ optical measuring techniques.
Which tools and equipment are most critical in the gage-making process?
How to Answer
- 1
Identify key gage-making tools specific to your experience
- 2
Mention both manual and CNC equipment if applicable
- 3
Highlight any industry standards or certifications relevant to gages
- 4
Discuss maintenance or calibration practices briefly
- 5
End with how these tools impact quality and precision
Example Answers
The most critical tools in gage making include precision measuring instruments like micrometers and calipers, CNC milling machines for fabrication, and inspection tools like comparators. Regular calibration ensures accuracy, which is vital for quality assurance.
Don't Just Read Gage Maker Questions - Practice Answering Them!
Reading helps, but actual practice is what gets you hired. Our AI feedback system helps you improve your Gage Maker interview answers in real-time.
Personalized feedback
Unlimited practice
Used by hundreds of successful candidates
How do you determine the best materials to use for different types of gages?
How to Answer
- 1
Consider the environment where the gage will be used, such as temperature and exposure to chemicals.
- 2
Evaluate the required precision and durability of the gage to inform material choice.
- 3
Research common materials used in similar applications to understand industry standards.
- 4
Balance cost with performance needs to select an economically viable material.
- 5
Consult with engineers or technicians to get insights on material performance in specific applications.
Example Answers
I assess the gage's working environment first, factoring in elements like temperature and potential exposure to chemicals. For example, stainless steel may be ideal for corrosive environments.
What steps do you take to ensure that gages are accurately calibrated?
How to Answer
- 1
Review the manufacturer specifications for the gage
- 2
Use traceable standards for calibration
- 3
Conduct regular calibration checks based on a schedule
- 4
Document all calibration results and any adjustments made
- 5
Train staff on proper calibration techniques and procedures
Example Answers
I ensure accurate calibration by first reviewing the manufacturer specifications for each gage. Then, I use traceable calibration standards to verify precision. Regular checks are scheduled to maintain accuracy, and I document all results for compliance.
Can you explain the importance of industry standards in gage making?
How to Answer
- 1
Define industry standards in the context of gage making.
- 2
Highlight how they ensure product quality and consistency.
- 3
Discuss how standards facilitate communication between different parties.
- 4
Mention compliance with safety regulations as a key factor.
- 5
Provide examples of standards relevant to gage making.
Example Answers
Industry standards in gage making refer to the established guidelines that ensure precision and compatibility. They are vital because they maintain the quality and consistency of measurement tools, enabling manufacturers to produce reliable parts. For example, ISO 9001 is a standard that helps organizations ensure they meet customer and regulatory requirements.
What CAD software are you proficient in and how have you used it in gage design?
How to Answer
- 1
Identify specific CAD software you know like SolidWorks or AutoCAD
- 2
Mention any gage design projects where you applied the software
- 3
Highlight relevant features of the software used for gage design
- 4
Discuss your role in the design process and any team collaboration
- 5
Conclude with any positive outcomes from your designs
Example Answers
I am proficient in SolidWorks, which I used extensively for designing precision gages. In a recent project, I designed a custom gage for measuring features on mechanical parts. I utilized the assembly tools to ensure proper fit and alignment which reduced the manufacturing time by 20%.
What types of precision tools do you frequently use in your gage-making processes?
How to Answer
- 1
Identify specific tools you use regularly.
- 2
Include both measuring and inspection tools.
- 3
Mention tools that reflect your experience and expertise.
- 4
Explain how these tools contribute to accuracy.
- 5
Be prepared to describe a situation where a tool was crucial.
Example Answers
In my gage-making process, I frequently use calipers, micrometers, and height gauges to ensure precision measurements. These tools help achieve tight tolerances, which is critical in my work.
How do you account for measurement error in your designs?
How to Answer
- 1
Identify types of measurement errors that can occur: systematic and random errors.
- 2
Discuss the importance of tolerances and how they affect design.
- 3
Utilize statistical methods to analyze the data and predict error.
- 4
Incorporate redundancy in measurements to ensure accuracy.
- 5
Regularly calibrate instruments to minimize measurement variability.
Example Answers
I account for measurement error by identifying both systematic and random errors and incorporating tolerances into my designs. For instance, I ensure that the specifications allow room for error by using statistical analysis to predict the possible range of errors.
What methods do you use to achieve the desired surface finish on gages?
How to Answer
- 1
Understand the specifications for surface finish required for the gage
- 2
Discuss various machining techniques such as grinding, polishing, and honing
- 3
Mention the role of materials in achieving the desired finish
- 4
Explain the importance of measuring surface finish with appropriate tools and methods
- 5
Highlight the significance of deburring and cleaning processes after machining
Example Answers
I achieve the desired surface finish by using precision grinding followed by polishing to meet the specific Ra values required for the gage.
How do you determine the necessary tolerances for specific gage applications?
How to Answer
- 1
Understand the application requirements and quality standards
- 2
Consult engineering drawings and specifications for dimensions
- 3
Consider manufacturing capabilities and variations
- 4
Evaluate the function of the gage and critical characteristics
- 5
Communicate with stakeholders for input on tolerances
Example Answers
I first assess the specific requirements of the application, taking into account quality standards and engineering drawings. I then factor in the manufacturing processes involved, ensuring that the tolerances are achievable and appropriate for the intended use of the gage.
Don't Just Read Gage Maker Questions - Practice Answering Them!
Reading helps, but actual practice is what gets you hired. Our AI feedback system helps you improve your Gage Maker interview answers in real-time.
Personalized feedback
Unlimited practice
Used by hundreds of successful candidates
What finishing processes do you consider essential for gage production?
How to Answer
- 1
Identify key finishing processes like grinding, honing, and lapping.
- 2
Explain the importance of precision in each process for gage accuracy.
- 3
Mention surface finish and tolerances relevant to gage performance.
- 4
Relate finishing processes to the materials used in gage construction.
- 5
Include examples of how poor finishing can affect gage functionality.
Example Answers
I believe grinding and lapping are essential for achieving the necessary tolerances in gage production. Good surface finishes achieved through these processes ensure that gages are precise and reliable for measurement.
Situational Interview Questions
Imagine you discover that a batch of gages does not meet quality standards. What actions would you take?
How to Answer
- 1
Confirm the issue by re-inspecting the gages for accuracy.
- 2
Document the findings clearly with supporting evidence.
- 3
Notify relevant stakeholders immediately about the quality issue.
- 4
Implement corrective actions, such as quarantining the affected batch.
- 5
Conduct a root cause analysis to prevent future occurrences.
Example Answers
First, I would double-check the gages to make sure the quality issue is accurate. Then, I'd document everything, including measurements and any discrepancies. Next, I would inform my supervisor and the quality control team. I would suggest quarantining the batch and begin investigating the root cause to avoid similar issues later.
You have multiple projects with tight deadlines. How would you prioritize and manage your time?
How to Answer
- 1
List all projects and their deadlines to visualize your workload
- 2
Assess the impact of each project on overall goals
- 3
Use a prioritization technique like the Eisenhower Box or ABCD method
- 4
Break projects into smaller tasks and create a timeline for each
- 5
Regularly review progress and adjust priorities as needed
Example Answers
I would start by listing all projects along with their deadlines. Then, I would prioritize them based on their impact and urgency. I might use the ABCD prioritization method to categorize tasks and ensure I focus on what's most critical. Each project would be broken into smaller tasks with specific timelines, and I would review my progress daily to adjust as needed.
Don't Just Read Gage Maker Questions - Practice Answering Them!
Reading helps, but actual practice is what gets you hired. Our AI feedback system helps you improve your Gage Maker interview answers in real-time.
Personalized feedback
Unlimited practice
Used by hundreds of successful candidates
A customer is unhappy with a gage you produced. How would you address their concerns?
How to Answer
- 1
Listen actively to the customer's concerns without interrupting.
- 2
Acknowledge the issue and express empathy for their frustration.
- 3
Ask clarifying questions to fully understand the problem.
- 4
Offer a solution or a way to resolve the issue, such as a replacement or adjustment.
- 5
Follow up with the customer to ensure the solution met their expectations.
Example Answers
I would first listen to the customer to understand their specific concerns. I would acknowledge their frustration and let them know I’m here to help. Then, I would ask questions to clarify the problem and suggest a replacement if necessary. Finally, I’d follow up to ensure they are satisfied with the solution.
If you were tasked with improving the gage-making process, what initial steps would you consider?
How to Answer
- 1
Conduct a thorough analysis of the current gage-making process to identify bottlenecks and inefficiencies.
- 2
Engage with team members to gather input on pain points and suggestions for improvement.
- 3
Research and propose new technologies or tools that could enhance accuracy and efficiency.
- 4
Create a streamlined workflow diagram to visualize the process and identify areas for optimization.
- 5
Test the proposed changes on a small scale before full implementation to assess impact.
Example Answers
I would start with a detailed analysis of the current process to identify any bottlenecks. Next, I'd gather feedback from my colleagues about their experiences and challenges. Based on that, I might research automation tools to improve our accuracy and efficiency.
If you find that you've made an error in a design, what is your approach to rectify it?
How to Answer
- 1
Acknowledge the error quickly and take responsibility
- 2
Analyze the error to understand its impact on the project
- 3
Propose potential solutions or corrective actions
- 4
Communicate transparently with the team about the issue
- 5
Learn from the mistake to prevent it in the future
Example Answers
I would first acknowledge the error and take responsibility. Then, I would analyze how it affects the design and propose a solution. After communicating this with my team, I would implement the fix and document lessons learned for future reference.
You are given a limited budget for materials. How would you manage resources effectively?
How to Answer
- 1
Prioritize the most essential materials needed for the project
- 2
Research cost-effective alternatives or suppliers for materials
- 3
Use a tracking tool or spreadsheet to monitor spending
- 4
Negotiate with vendors for better pricing or bulk discounts
- 5
Review and reassess material needs regularly throughout the project
Example Answers
I would start by identifying the critical materials necessary for the project and ensuring we acquire those first. Then, I would look for affordable suppliers or consider substitute materials that still meet our quality standards.
If tasked with leading a gage project, how would you motivate your team to achieve the best results?
How to Answer
- 1
Set clear goals and expectations for the project.
- 2
Encourage open communication and feedback among team members.
- 3
Recognize and celebrate small achievements to boost morale.
- 4
Provide opportunities for team members to develop their skills.
- 5
Lead by example and maintain a positive attitude.
Example Answers
I would start by establishing clear project goals and ensure everyone understands their role. Encouraging open communication is vital, so we would have regular check-ins to discuss progress and challenges. I would celebrate the completion of milestones to keep the team motivated and suggest training sessions to help develop relevant skills.
Describe how you would handle a technical challenge while creating a custom gage.
How to Answer
- 1
Identify the specific technical challenge clearly.
- 2
Explain the analysis process you would use to understand the issue.
- 3
Outline the tools or methods you would apply to solve the problem.
- 4
Discuss collaboration with team members for insights and solutions.
- 5
Share how you would test the solution to ensure it meets specifications.
Example Answers
If I faced a challenge with the accuracy of a gage design, I'd first pinpoint whether it was a measurement or material issue. I would analyze existing data and consult with colleagues who have experience in that material type. I'd then apply simulation software to test different designs before finalizing one that meets the specifications, and I would validate it through initial prototype testing.
If a gage failed during testing, what steps would you take to investigate the failure?
How to Answer
- 1
Review the testing procedure and ensure it was followed correctly.
- 2
Inspect the gage for any visible damage or wear.
- 3
Check the calibration of the gage against known standards.
- 4
Consult the maintenance records for prior issues or repairs.
- 5
Document your findings and outline any necessary corrective actions.
Example Answers
I would start by reviewing the testing procedure to confirm it was conducted properly. Then, I would inspect the gage for visible damage before checking its calibration against standards. Any anomalies would be documented, and I would review previous maintenance records for insights.
What safety protocols do you believe are critical in the gage making environment?
How to Answer
- 1
Emphasize the importance of personal protective equipment (PPE).
- 2
Discuss the need for regular maintenance and calibration of gages.
- 3
Highlight the significance of proper training for all staff on safety procedures.
- 4
Mention the importance of a clean and organized workspace to prevent accidents.
- 5
Talk about the need for clear labeling and signage in hazardous areas.
Example Answers
I believe that personal protective equipment like safety glasses and gloves are essential in ensuring everyone's safety while working with gages. Regular maintenance also prevents tool malfunction.
Don't Just Read Gage Maker Questions - Practice Answering Them!
Reading helps, but actual practice is what gets you hired. Our AI feedback system helps you improve your Gage Maker interview answers in real-time.
Personalized feedback
Unlimited practice
Used by hundreds of successful candidates
Gage Maker Position Details
Recommended Job Boards
ZipRecruiter
www.ziprecruiter.com/Jobs/GageThese job boards are ranked by relevance for this position.
Related Positions
- Jig Maker
- Die Maker
- Cam Maker
- Gauge Checker
- Tool Maker
- Guitar Maker
- Dial Maker
- Instrument Maker
- Golf Club Maker
- Mat Maker
Similar positions you might be interested in.
Ace Your Next Interview!
Practice with AI feedback & get hired faster
Personalized feedback
Used by hundreds of successful candidates
Ace Your Next Interview!
Practice with AI feedback & get hired faster
Personalized feedback
Used by hundreds of successful candidates