Top 32 Grease Packer Interview Questions and Answers [Updated 2025]
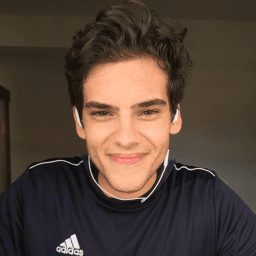
Andre Mendes
•
March 30, 2025
Preparing for a Grease Packer interview can be daunting, but we've got you covered with a comprehensive list of the most common questions you might face. In this post, you'll find insightful example answers and practical tips to help you respond confidently and effectively. Whether you're a seasoned professional or new to the field, this guide is designed to boost your interview readiness and help you land the job.
Download Grease Packer Interview Questions in PDF
To make your preparation even more convenient, we've compiled all these top Grease Packerinterview questions and answers into a handy PDF.
Click the button below to download the PDF and have easy access to these essential questions anytime, anywhere:
List of Grease Packer Interview Questions
Technical Interview Questions
What routine maintenance tasks do you perform on packing machines?
How to Answer
- 1
Identify key maintenance tasks relevant to packing machines.
- 2
Mention frequency of tasks such as daily, weekly, or monthly.
- 3
Highlight any specific checks, like lubrication or belt tension.
- 4
Include the importance of cleaning and inspecting parts.
- 5
Emphasize safety protocols during maintenance procedures.
Example Answers
I perform daily checks on the machine's lubricant levels and ensure that moving parts are well-greased. Weekly, I inspect and tighten any loose belts, and monthly, I clean out any debris to prevent jams.
What types of packing equipment are you familiar with, and how have you used them?
How to Answer
- 1
List specific types of packing equipment you have used.
- 2
Describe your experience with each type briefly.
- 3
Highlight any relevant training or certification.
- 4
Mention how you ensured efficiency and safety when using the equipment.
- 5
Include any examples of troubleshooting issues with the equipment.
Example Answers
I am familiar with vacuum sealers and shrink wrap machines. In my last job, I used a vacuum sealer to package meat products, ensuring they were airtight. I also operated a shrink wrap machine to package boxes for shipment, focusing on speed and accuracy.
Don't Just Read Grease Packer Questions - Practice Answering Them!
Reading helps, but actual practice is what gets you hired. Our AI feedback system helps you improve your Grease Packer interview answers in real-time.
Personalized feedback
Unlimited practice
Used by hundreds of successful candidates
What are the key quality standards you follow when packing grease?
How to Answer
- 1
Ensure cleanliness and hygiene of the packing area and equipment
- 2
Use accurate measuring tools for precise quantities
- 3
Conduct regular quality checks on grease consistency and composition
- 4
Adhere to safety standards to prevent contamination
- 5
Label all products clearly with batch numbers and expiration dates
Example Answers
I make sure the packing area is clean and equipment is sanitized. I always use calibrated measuring devices to ensure I'm packing the correct amount of grease. Regular quality checks are essential for verifying the grease's consistency.
Can you explain the process you follow to ensure the proper filling of containers?
How to Answer
- 1
Begin with a checklist of equipment and materials needed for filling.
- 2
Describe the steps to prepare the container and workspace.
- 3
Mention how you measure the fill volume or weight for accuracy.
- 4
Explain how you inspect each container after filling.
- 5
Emphasize the importance of quality control throughout the process.
Example Answers
I start by gathering all necessary equipment and making sure my workspace is clean. I prepare the containers by inspecting them for damage and ensuring they're compatible with the grease. I then carefully measure the fill volume, using calibrated tools to ensure accuracy, and conduct a final inspection to check for any leaks before sealing.
What types of grease are you familiar with, and does their packing process differ?
How to Answer
- 1
Identify specific types of grease, such as lithium or calcium-based.
- 2
Explain the packing process for each type if there are differences.
- 3
Mention any relevant experience with handling or packing grease.
- 4
Highlight safety considerations during the packing process.
- 5
Keep your answer concise and focused on industry standards.
Example Answers
I am familiar with lithium-based and calcium-based greases. The packing process for lithium grease requires precise temperature control to avoid contamination, while calcium grease is usually packed at room temperature. I have packed both types in my previous job, ensuring quality and safety.
What regulations do you consider important when packing grease products?
How to Answer
- 1
Familiarize yourself with FDA regulations regarding food contact materials.
- 2
Understand OSHA guidelines for safety when handling chemical products.
- 3
Know the relevant environmental regulations for waste disposal related to grease products.
- 4
Emphasize the importance of quality control standards, such as ISO 9001.
- 5
Be prepared to discuss how you stay updated on regulatory changes.
Example Answers
When packing grease products, I consider FDA regulations essential to ensure safety for food contact. I also follow OSHA guidelines to maintain a safe working environment, and I ensure compliance with waste disposal regulations to protect the environment.
What packaging materials do you consider best for grease and why?
How to Answer
- 1
Identify common materials used for grease packaging like metal containers and plastic tubs.
- 2
Explain the advantages of each material, such as resistance to leakage and durability.
- 3
Mention any relevant industry standards or regulations that these materials meet.
- 4
Consider the environmental impact of packaging and any recyclable options available.
- 5
Show awareness of cost-effectiveness and practicality in choosing packaging materials.
Example Answers
For grease packaging, I believe metal containers are best due to their resistance to leakage and ability to keep the grease stable over time. They also meet safety standards for hazardous materials.
What personal protective equipment do you think is essential when working as a grease packer?
How to Answer
- 1
Mention gloves to protect hands from grease and potential chemicals.
- 2
Include safety goggles to shield eyes from splashes.
- 3
Highlight steel-toed boots for foot protection in case of heavy items.
- 4
Discuss the importance of a lab coat or coveralls to keep clean and safe.
- 5
State that masks can be necessary if there are fumes or dust present.
Example Answers
As a grease packer, I believe essential personal protective equipment includes gloves to protect my hands from grease and chemicals. Safety goggles are also important to prevent splashes into the eyes. Additionally, steel-toed boots help protect my feet from any heavy equipment or materials.
What is the importance of accurate labeling in grease packing?
How to Answer
- 1
Emphasize safety in handling and usage of greases.
- 2
Discuss legal compliance and regulatory standards.
- 3
Highlight the need for clear product identification to prevent errors.
- 4
Mention the impact on customer trust and brand reputation.
- 5
Note the role of labeling in inventory management and tracking.
Example Answers
Accurate labeling is crucial for safety because it ensures workers know how to handle each grease properly. It also helps in complying with legal standards, reducing liability.
Describe the safety protocols you follow when handling grease and packing materials.
How to Answer
- 1
Always wear appropriate personal protective equipment like gloves and goggles
- 2
Follow proper storage procedures to prevent contamination
- 3
Keep work areas clean and organized to avoid spills
- 4
Use proper lifting techniques to handle heavy grease containers
- 5
Report any leaks or spills immediately to a supervisor.
Example Answers
I always wear gloves and goggles when handling grease to protect my skin and eyes. I make sure that all materials are stored properly and that spills are cleaned up promptly to maintain a safe workspace.
Don't Just Read Grease Packer Questions - Practice Answering Them!
Reading helps, but actual practice is what gets you hired. Our AI feedback system helps you improve your Grease Packer interview answers in real-time.
Personalized feedback
Unlimited practice
Used by hundreds of successful candidates
Behavioral Interview Questions
Can you describe a time when you had to work closely with a team to meet production goals?
How to Answer
- 1
Choose a specific project where teamwork was critical.
- 2
Highlight your role and contributions to the team.
- 3
Discuss the challenges faced and how the team overcame them.
- 4
Mention the outcome and how it met the production goals.
- 5
Emphasize communication and collaboration as key factors.
Example Answers
In my last job, our team was tasked with increasing production efficiency during a busy season. I took the initiative to coordinate daily check-ins to address any bottlenecks. Despite some initial delays, our open communication allowed us to share insights and resolve issues quickly. In the end, we surpassed our production goal by 15%.
Tell me about a situation where you identified a safety hazard in your workplace. What steps did you take?
How to Answer
- 1
Identify a real safety hazard you encountered.
- 2
Explain how you noticed the hazard and assessed the risk.
- 3
Describe the steps you took to report or correct the issue.
- 4
Mention any follow-up actions to ensure safety measures were effective.
- 5
Keep the focus on your proactive approach and teamwork.
Example Answers
In my previous job, I noticed that some boxes were stacked too high in the warehouse, creating a tipping hazard. I reported it to my supervisor immediately and suggested we implement a maximum stacking height rule. After discussing with the team, we rearranged the area safely and used tape to mark the height limit.
Don't Just Read Grease Packer Questions - Practice Answering Them!
Reading helps, but actual practice is what gets you hired. Our AI feedback system helps you improve your Grease Packer interview answers in real-time.
Personalized feedback
Unlimited practice
Used by hundreds of successful candidates
Can you give an example of how you handled constructive criticism regarding your packing work?
How to Answer
- 1
Think of a specific instance where you received feedback
- 2
Describe the feedback you received clearly and honestly
- 3
Explain how you felt about the feedback initially
- 4
Detail the actions you took to address the criticism
- 5
Mention any positive outcomes from implementing the feedback
Example Answers
Once, my supervisor pointed out that my packing efficiency could improve. At first, I felt a bit defensive, but I took it as an opportunity to learn. I asked for specific tips and implemented those changes. As a result, my packing speed increased by 20% in the following month.
Describe a time when you faced a challenge in your packing duties. How did you resolve it?
How to Answer
- 1
Identify a specific packing challenge you experienced.
- 2
Explain the impact of the challenge on your work or team.
- 3
Describe the steps you took to address the issue.
- 4
Highlight the outcome and what you learned from the situation.
- 5
Keep your answer concise and focused on your role in resolving the issue.
Example Answers
In my previous role, I faced a situation where we ran out of packing materials during a peak time. I informed my supervisor and quickly sourced alternative materials from nearby storage. This minimized downtime and we completed the packing ahead of schedule. I learned to always check stock levels before starting the task.
How do you prioritize your tasks when faced with tight deadlines during packing shifts?
How to Answer
- 1
Identify the most urgent tasks that directly affect shipping schedules.
- 2
Break down tasks into smaller steps to assess time needed for each.
- 3
Use a checklist to ensure you are completing priorities in order.
- 4
Communicate with team members to understand and redistribute workload if necessary.
- 5
Stay flexible and ready to adjust priorities as new time-sensitive requests come in.
Example Answers
When faced with tight deadlines, I first identify which items need to be packed for the earliest shipments. I break down my packing tasks and create a checklist. This helps me stay focused and ensures nothing is overlooked. I also check in with my teammates to see if they need assistance or if we can help each other out to meet the deadlines. I remain adaptable in case new priorities arise.
Have you ever caught a mistake in a pack before it went out? What did you do?
How to Answer
- 1
Think of a specific instance when you caught a mistake.
- 2
Explain what the mistake was and how you discovered it.
- 3
Describe your immediate action to correct the mistake.
- 4
Emphasize the importance of quality control in your answer.
- 5
Mention any steps you took to prevent future mistakes.
Example Answers
Yes, I once noticed a label was missing on a pack. I was inspecting the items before sealing and saw it wasn't there. I immediately informed my supervisor and we replaced the label before it went out. This ensured the product had all the correct information for the customer.
Give an example of how you adapted to a significant change in packing procedures or technology.
How to Answer
- 1
Identify a specific change you faced in packing procedures.
- 2
Explain how you learned about the new procedures or technology.
- 3
Describe the steps you took to adapt quickly and effectively.
- 4
Highlight any positive outcomes from your adaptation.
- 5
Keep your answer focused on your role and contributions.
Example Answers
In my previous job, we switched to a new automated packing line. I spent time learning the new system through online tutorials and hands-on training. I then helped train my colleagues, which improved our team's efficiency and reduced packing errors by 15%.
Describe a time when you took on a leadership role in your packing team. What was the outcome?
How to Answer
- 1
Think of a specific situation where you led your team.
- 2
Focus on the actions you took to guide your team.
- 3
Highlight collaboration and communication strengths.
- 4
Emphasize the results that improved team efficiency.
- 5
Use metrics or outcomes to quantify your success.
Example Answers
In my previous role, our team faced a critical deadline. I organized a meeting to delegate tasks based on each member's strengths, and we completed the packing ahead of schedule, improving our output by 20%.
Have you ever trained a new employee on packing procedures? How did you approach this?
How to Answer
- 1
Start by explaining your training method clearly.
- 2
Mention any specific techniques you used to convey information.
- 3
Include how you ensured the trainee understood the procedures.
- 4
Highlight any positive outcomes from your training.
- 5
Be confident and show the value of your experience.
Example Answers
Yes, I trained a new employee on packing procedures by first giving them a detailed overview of the process. I used step-by-step demonstrations and then had them practice under my supervision, providing feedback along the way. This ensured they felt comfortable and understood the importance of efficiency in packing.
Tell me about a time when you had to maintain accurate records of your packing work. How did you ensure accuracy?
How to Answer
- 1
Choose a specific example from your experience.
- 2
Explain the method you used to keep records.
- 3
Highlight tools or systems utilized for accuracy.
- 4
Discuss how you verified the records afterwards.
- 5
Mention the impact of your accuracy on the team or operations.
Example Answers
In my last job, I was responsible for packing products and recording the quantities. I used a digital inventory system to log each item packed. I double-checked the counts during and after packing, which helped avoid any discrepancies. My attention to detail ensured that we maintained a consistent supply for shipments.
Don't Just Read Grease Packer Questions - Practice Answering Them!
Reading helps, but actual practice is what gets you hired. Our AI feedback system helps you improve your Grease Packer interview answers in real-time.
Personalized feedback
Unlimited practice
Used by hundreds of successful candidates
Can you recall a specific time when your attention to detail made a difference in the packing process?
How to Answer
- 1
Think of a situation where a small error could have led to a bigger problem.
- 2
Describe the steps you took to ensure everything was correct.
- 3
Highlight the positive outcome as a result of your attention to detail.
- 4
Use specific metrics or examples to illustrate your impact.
- 5
Keep the story focused on your actions and the results.
Example Answers
At my previous job, I noticed that some packages were not sealed properly. I double-checked each one, which prevented a potential shipment delay. As a result, we maintained our delivery schedule and customer satisfaction remained high.
Describe an instance when you took the initiative to improve a packing process.
How to Answer
- 1
Think of a specific situation where you identified a problem.
- 2
Explain the action you took to address the issue.
- 3
Highlight the positive outcome or result of your initiative.
- 4
Use quantifiable metrics if possible, like time saved or increased efficiency.
- 5
Keep it concise and focused on your role.
Example Answers
In my last job, I noticed that the packing line was frequently slowing down due to inefficient arrangement of packing materials. I reorganized the layout to reduce movement and trained my team on the new setup. This cut packing time by 20%.
Situational Interview Questions
Imagine you have a limited supply of packing materials for the day. How would you manage your output?
How to Answer
- 1
Prioritize the most important items to pack first.
- 2
Estimate the packing material needed for each task.
- 3
Communicate with the team about the material constraints.
- 4
Look for ways to optimize packing techniques to use less material.
- 5
Monitor usage throughout the day and adjust plans as needed.
Example Answers
I would first prioritize the most critical items to pack, ensuring they get done first. Then, I would estimate how much packing material each item requires and communicate with my team about our limited supply. If we notice we're running low, I would adjust our packing techniques to minimize material use.
What would you do if a packing machine malfunctioned in the middle of a production run?
How to Answer
- 1
Immediately stop the machine to avoid further issues.
- 2
Notify the supervisor or maintenance team about the malfunction.
- 3
Inspect the machine for any visible issues while waiting for help.
- 4
Document the malfunction for future reference and analysis.
- 5
Follow company protocols for machine malfunctions and safety.
Example Answers
I would quickly stop the packing machine to prevent damage. Then, I would notify my supervisor and the maintenance team about the issue. While waiting for assistance, I would check for any visible problems, and I would make sure to document the incident for our records.
Don't Just Read Grease Packer Questions - Practice Answering Them!
Reading helps, but actual practice is what gets you hired. Our AI feedback system helps you improve your Grease Packer interview answers in real-time.
Personalized feedback
Unlimited practice
Used by hundreds of successful candidates
If there was a disagreement with a co-worker about packing procedures, how would you handle it?
How to Answer
- 1
Listen to the co-worker's perspective first before responding
- 2
Express your views calmly and clearly, focusing on the issue, not the person
- 3
Propose a solution or compromise that considers both views
- 4
Involve a supervisor if necessary to mediate the discussion
- 5
Follow up after the discussion to ensure the agreement is being implemented
Example Answers
I would first listen to my co-worker's concerns about the packing procedures to understand their point of view. Then, I would calmly share my perspective and suggest a compromise that incorporates both our ideas. If we can't agree, I would involve a supervisor to help us resolve it.
How would you handle a sudden increase in orders that requires you to pack more grease quickly?
How to Answer
- 1
Assess current packing capacity and resources immediately
- 2
Prioritize order fulfillment based on delivery timelines
- 3
Organize team members to optimize packing processes
- 4
Streamline workflow by reducing any bottlenecks
- 5
Communicate with management about resource needs if necessary
Example Answers
I would quickly evaluate our current packing capacity and organize the team to prioritize the most urgent orders, ensuring we use all available resources efficiently.
What steps would you take if a batch of grease packaging did not meet quality standards?
How to Answer
- 1
Identify the specific quality issues with the packaging.
- 2
Isolate the affected batch to prevent further distribution.
- 3
Document the quality issues and investigate the cause.
- 4
Implement corrective actions to address the identified problems.
- 5
Communicate with relevant team members and maintain transparency.
Example Answers
I would first identify what went wrong with the packaging. Then, I would isolate the batch to prevent it from being shipped. Next, I would document the issues and investigate their cause. After that, I would implement corrective measures, and finally, I would update my team on the situation to ensure everyone is aware.
If you received a complaint about packed grease, how would you respond?
How to Answer
- 1
Acknowledge the complaint promptly to show responsiveness.
- 2
Gather details about the specific issue from the complainant.
- 3
Investigate the cause of the problem in your packing process.
- 4
Provide clear communication about steps taken to resolve the issue.
- 5
Follow up with the complainant to ensure satisfaction after resolution.
Example Answers
I would first acknowledge the complaint and thank the person for bringing it to my attention. I'd ask for specifics about the issue, such as when it occurred and what the complaint was. Then, I would check the packing process for any potential errors and resolve it. Finally, I'd inform the complainant about the actions taken and follow up to ensure they are satisfied.
How would you approach suggesting a new packing method that could improve efficiency?
How to Answer
- 1
Identify current packing challenges and inefficiencies.
- 2
Research alternative packing methods used in the industry.
- 3
Gather data on potential benefits of the new method.
- 4
Prepare a presentation or proposal outlining your suggestion.
- 5
Be open to feedback and willing to collaborate with the team.
Example Answers
I would start by analyzing our current packing process to pinpoint specific inefficiencies. Then, I'd research proven packing methods in similar industries. After that, I'd compile data showing how my suggested method could save time and reduce costs, and I'd present this to my manager for review.
If your entire team had to pack under a new schedule that you found challenging, what would you do?
How to Answer
- 1
Assess the new schedule and identify specific challenges
- 2
Communicate with the team about the new expectations
- 3
Encourage collaboration to find solutions together
- 4
Utilize team strengths to allocate tasks effectively
- 5
Stay positive and lead by example to motivate the team
Example Answers
I would first review the new schedule to understand the time pressures. Then I would hold a team meeting to discuss everyone's thoughts and how we can work together to meet the objectives. By dividing up tasks based on each person's strengths, we can manage the workload better and stay on track.
How would you implement feedback received from a supervisor about your packing process?
How to Answer
- 1
Acknowledge the feedback and thank your supervisor.
- 2
Identify specific areas of improvement based on their suggestions.
- 3
Create a step-by-step plan to incorporate the feedback into your packing process.
- 4
Set a timeline to review the changes and assess their effectiveness.
- 5
Communicate with your supervisor about the adjustments you made.
Example Answers
I would first thank my supervisor for their feedback and take note of the specific points they mentioned. Then, I would create a plan to adjust my packing technique based on those points, such as changing how I stack items to save space. After implementing these changes, I would check back in with my supervisor after a week to discuss if the adjustments improved the efficiency.
If you noticed a grease spill in your work area, what immediate actions would you take?
How to Answer
- 1
Stay calm and assess the size of the spill.
- 2
Immediately inform your supervisor about the spill.
- 3
Use a spill kit to contain the area around the spill.
- 4
Wear appropriate PPE before starting cleanup.
- 5
Clean up the spill using absorbent materials as per safety protocols.
Example Answers
I would first assess the spill and then quickly inform my supervisor. I would grab the spill kit, contain the area, put on my gloves and goggles, and use absorbent pads to clean it up safely.
Don't Just Read Grease Packer Questions - Practice Answering Them!
Reading helps, but actual practice is what gets you hired. Our AI feedback system helps you improve your Grease Packer interview answers in real-time.
Personalized feedback
Unlimited practice
Used by hundreds of successful candidates
Grease Packer Position Details
Recommended Job Boards
These job boards are ranked by relevance for this position.
Related Positions
- Grease Worker
- Grease Man
- Lubricator
- Pump Oiler
- Car Greaser
- Machine Oiler
- Oiler
- Pot Liner
- Crane Oiler
- Belt Lacer
Similar positions you might be interested in.
Ace Your Next Interview!
Practice with AI feedback & get hired faster
Personalized feedback
Used by hundreds of successful candidates
Ace Your Next Interview!
Practice with AI feedback & get hired faster
Personalized feedback
Used by hundreds of successful candidates