Top 30 Lubricator Interview Questions and Answers [Updated 2025]
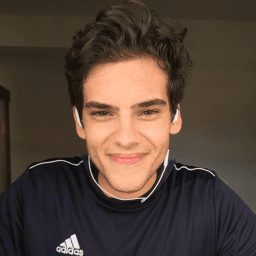
Andre Mendes
•
March 30, 2025
Preparing for a lubricator job interview can be daunting, but we've got you covered with a comprehensive guide featuring the most common interview questions for this role. Dive into our updated 2025 edition to discover insightful example answers and valuable tips on how to effectively articulate your strengths and expertise. Equip yourself with the knowledge and confidence needed to make a lasting impression.
Download Lubricator Interview Questions in PDF
To make your preparation even more convenient, we've compiled all these top Lubricatorinterview questions and answers into a handy PDF.
Click the button below to download the PDF and have easy access to these essential questions anytime, anywhere:
List of Lubricator Interview Questions
Behavioral Interview Questions
Can you describe a time when you had to troubleshoot a lubrication system failure?
How to Answer
- 1
Identify the specific lubrication system and its role.
- 2
Explain the failure symptoms and how you recognized them.
- 3
Detail the steps you took to troubleshoot the issue.
- 4
Include any tools or techniques you used during troubleshooting.
- 5
Mention the outcome and any improvements made afterwards.
Example Answers
In my previous job, we had a hydraulic system that started leaking due to a failure in the lubrication circuit. I noticed the pressure drop during routine checks. To troubleshoot, I examined the lubrication line and found a blockage caused by debris. I cleared the line, replaced the seal, and tested the system to ensure it was functioning correctly. The system's performance improved, and we implemented a new filter to prevent recurrence.
Tell me about a time when you had to work with a team to complete a lubrication task under a tight deadline.
How to Answer
- 1
Choose a specific lubrication task you worked on.
- 2
Describe the team members and their roles.
- 3
Explain the tight deadline and its impact.
- 4
Detail your contribution to the team's success.
- 5
Mention the outcome and what you learned from the experience.
Example Answers
During a scheduled maintenance at the refinery, we had to lubricate multiple pumping stations in just two hours. My team included two technicians and my supervisor. I coordinated the lubrication process and ensured everyone had the right tools ready. We completed the task 15 minutes early, which allowed us to inspect our work, preventing any future issues.
Don't Just Read Lubricator Questions - Practice Answering Them!
Reading helps, but actual practice is what gets you hired. Our AI feedback system helps you improve your Lubricator interview answers in real-time.
Personalized feedback
Unlimited practice
Used by hundreds of successful candidates
Describe an instance where you identified a safety hazard in your lubricating practices. What actions did you take?
How to Answer
- 1
Think of a specific example from your experience.
- 2
Describe the hazard you identified clearly.
- 3
Explain the steps you took to mitigate or eliminate the hazard.
- 4
Mention any tools or procedures you implemented.
- 5
Reflect on the outcome and what you learned.
Example Answers
In my previous job, I noticed that the lubricating equipment had a leak that created a slippery area on the floor. I immediately marked the area as a hazard, reported it to my supervisor, and placed absorbent mats over the leak until it could be repaired. This not only prevented potential slips but also ensured that our workplace remained safe.
Can you give an example of how you've adapted your lubrication techniques to meet changing equipment needs?
How to Answer
- 1
Identify a specific situation where equipment needs changed.
- 2
Explain the original lubrication technique and why it was effective.
- 3
Describe the new equipment needs and how they differed from the old.
- 4
Detail the adjustments you made to your lubrication process.
- 5
Conclude with the results of your adaptations and any improvements observed.
Example Answers
In my previous role, I worked with older hydraulic equipment that required a different viscosity of oil. When we upgraded to newer models, I realized they had tighter tolerances, so I switched to a synthetic lubricant that provided better flow at lower temperatures. This change reduced wear and improved efficiency, and maintenance intervals were extended by 20%.
Can you tell me about a time when you took initiative to improve lubrication practices in your workplace?
How to Answer
- 1
Think of a specific situation where you identified a problem with lubrication practices.
- 2
Explain the steps you took to gather information and assess the situation.
- 3
Describe the solution you implemented and how you communicated it to the team.
- 4
Highlight the positive outcomes resulting from your initiative.
- 5
Mention any metrics or feedback that demonstrate the impact of your actions.
Example Answers
In my last job at the manufacturing plant, I noticed that we had frequent machinery breakdowns due to inadequate lubrication. I initiated an inspection of all lubrication points and found that many were using the wrong grease. I proposed a switch to a synthetic lubricant that was more effective and led training sessions on proper application. As a result, we reduced breakdowns by 30% in six months.
Describe a situation where you learned a new lubrication technique. What motivated you to learn it?
How to Answer
- 1
Think of a specific instance when you acquired a new lubrication skill.
- 2
Explain the context that required you to learn this technique.
- 3
Describe your motivation, such as improving efficiency or solving a problem.
- 4
Highlight the outcome or benefits gained from learning the technique.
- 5
Keep it clear and direct, focusing on your learning process.
Example Answers
In my previous job, we had a recurring issue with a machine overheating. I learned a new technique involving precise grease application and temperature checks to resolve it. My motivation was to increase machine longevity and reduce downtime. This resulted in a 20% decrease in maintenance costs.
Have you ever trained someone in lubrication techniques? What approach did you take?
How to Answer
- 1
Start by describing the individual you trained and their background.
- 2
Explain the specific lubrication techniques you taught.
- 3
Detail the steps you took to ensure effective understanding.
- 4
Mention how you assessed their learning and provided feedback.
- 5
Conclude with the outcome of the training and any improvements noticed.
Example Answers
I trained a new technician by first assessing their previous knowledge. I then introduced them to the specific lubrication techniques we use, demonstrating each step while explaining the importance of proper lubrication. I provided hands-on practice and checked understanding through quizzes and practical tests. The technician became proficient quickly and improved machinery performance significantly.
Can you provide an example where your attention to detail made a difference in lubrication maintenance?
How to Answer
- 1
Think of a specific situation where attention to detail was crucial.
- 2
Use the STAR method: Situation, Task, Action, Result.
- 3
Highlight any problems that arose from a lack of attention to detail.
- 4
Mention the specific lubrication methods or tools you used.
- 5
Conclude with the positive outcome resulting from your careful work.
Example Answers
In my previous role as a lubricator, I noticed an unusual wear pattern on a machinery part during routine inspections. I checked the lubrication levels and found they were below the recommended amount. I adjusted the lubrication schedule and applied the right type of lubricant. As a result, the machinery ran smoothly for six months without issues, preventing a potential breakdown.
Technical Interview Questions
What are the differences between synthetic and mineral lubricants, and in what situations would you prefer one over the other?
How to Answer
- 1
Define synthetic and mineral lubricants clearly.
- 2
Mention performance differences like temperature stability and viscosity index.
- 3
Discuss the benefits of each type, such as cost and application.
- 4
Provide specific scenarios where one would be preferred, like extreme temperatures.
- 5
Conclude with personal insights on usage based on experience or industry practices.
Example Answers
Synthetic lubricants are man-made and offer superior stability and performance, especially in extreme temperatures, whereas mineral lubricants are derived from crude oil and are often less expensive but may not perform as well under stress. I would choose synthetic lubricants for high-performance engines or machinery facing high heat, while mineral lubricants are suitable for general use in lower-demand applications.
What types of lubrication systems are you familiar with and how do you approach their maintenance?
How to Answer
- 1
Identify different lubrication systems such as oil mist, grease, and centralized systems.
- 2
Explain your routine maintenance practices including checking oil levels, replacing filters, and monitoring system performance.
- 3
Mention any specific tools or technologies you use for maintenance checks.
- 4
Share examples of troubleshooting issues you have faced with lubrication systems.
- 5
Highlight the importance of documentation and following manufacturer guidelines for each system.
Example Answers
I am familiar with centralized lubrication systems and grease systems. For maintenance, I regularly check lubricant levels, replace worn hoses, and ensure that filters are clean to prevent blockages.
Don't Just Read Lubricator Questions - Practice Answering Them!
Reading helps, but actual practice is what gets you hired. Our AI feedback system helps you improve your Lubricator interview answers in real-time.
Personalized feedback
Unlimited practice
Used by hundreds of successful candidates
How do you determine the appropriate amount of lubricant to use for different types of machinery?
How to Answer
- 1
Refer to the manufacturer's specifications for lubrication.
- 2
Consider the operating conditions like temperature and load.
- 3
Evaluate the type of machinery and its lubrication system.
- 4
Use lubrication charts or guides if available.
- 5
Monitor machinery performance and adjust lubrication as needed.
Example Answers
I determine the lubricant amount by checking the manufacturer's specifications for each machine, which detail the optimal quantity depending on its type and operating conditions.
Can you explain how to properly use a grease gun and the common mistakes to avoid when using it?
How to Answer
- 1
Check that the grease gun is filled and the nozzle is clean before use.
- 2
Ensure you position the grease gun securely against the fitting to prevent leaks.
- 3
Use short, controlled bursts of grease to avoid over-lubrication.
- 4
Always wipe off any excess grease from the fitting after use for a clean workplace.
- 5
Avoid using a grease gun that has not been maintained or inspected for damages.
Example Answers
To use a grease gun correctly, I first check that it's filled with the appropriate grease and that the nozzle is clean. Next, I position it firmly against the fitting and apply short bursts of grease to avoid over-lubricating. After I'm done, I always clean up any excess grease to keep the area tidy.
What methods do you use to test the effectiveness of a lubricant in a given application?
How to Answer
- 1
Identify specific tests for lubricant viscosity and temperature performance.
- 2
Discuss field tests in real operational conditions.
- 3
Mention lab tests such as wear testing or friction measurements.
- 4
Include evaluation of lubricant's life cycle and degradation over time.
- 5
Highlight the importance of manufacturer specifications and standards.
Example Answers
I use a combination of viscosity testing and thermal stability checks, along with field tests to assess performance under real-world conditions.
What factors do you consider when selecting lubricants for extreme temperature environments?
How to Answer
- 1
Understand the temperature range the lubricant will be exposed to
- 2
Consider the viscosity and thermal stability of the lubricant
- 3
Evaluate the lubricant's resistance to oxidation and degradation
- 4
Assess compatibility with materials and seals in the application
- 5
Review manufacturer specifications and performance data for extreme temperatures
Example Answers
I consider the temperature range first, ensuring the lubricant maintains proper viscosity within that range. I also look at oxidative stability to prevent breakdown.
Are you familiar with any regulations regarding lubricants in industrial applications? Can you provide an example?
How to Answer
- 1
Research key regulations such as OSHA and EPA standards related to lubricants.
- 2
Mention specific lubricant types and their compliance requirements.
- 3
Provide an example of a regulation and how it applies to safety or environmental impact.
- 4
Connect the regulations to your personal experience or industry knowledge.
- 5
Be concise but detailed enough to show familiarity with industry standards.
Example Answers
Yes, I'm familiar with OSHA regulations regarding the safe handling of industrial lubricants. For example, OSHA requires that lubricant containers be properly labeled with hazard warnings to minimize risks in the workplace.
How do you diagnose the root cause of excessive wear in a lubricated component?
How to Answer
- 1
Inspect the lubricated component for visible signs of wear.
- 2
Review lubrication history and ensure proper lubrication was applied.
- 3
Check alignment and fit of the components involved.
- 4
Monitor operating conditions like temperature and load.
- 5
Use diagnostic tools like vibration analysis or oil analysis.
Example Answers
I first visually inspect the component for wear patterns and compare them to expected wear models. Then, I look into the lubrication history to confirm that the correct lubricant was used at recommended intervals.
What safety measures do you adhere to while working with lubricating agents?
How to Answer
- 1
Always wear appropriate personal protective equipment like gloves and goggles
- 2
Keep Material Safety Data Sheets (MSDS) accessible for all lubricants
- 3
Use lubricants in well-ventilated areas to avoid inhalation hazards
- 4
Regularly inspect equipment for leaks and spills to maintain a clean workspace
- 5
Follow proper storage guidelines to prevent reactions and accidents
Example Answers
I always wear gloves and goggles to protect myself from skin and eye contact while handling lubricants. I also ensure that the work area is well-ventilated to prevent inhaling fumes.
Don't Just Read Lubricator Questions - Practice Answering Them!
Reading helps, but actual practice is what gets you hired. Our AI feedback system helps you improve your Lubricator interview answers in real-time.
Personalized feedback
Unlimited practice
Used by hundreds of successful candidates
What industry standards do you follow for lubricating machinery and equipment?
How to Answer
- 1
Mention specific standards such as ISO, ASTM, or NLGI.
- 2
Talk about understanding manufacturer guidelines for equipment.
- 3
Include safety practices for handling lubricants.
- 4
Discuss the importance of proper lubrication intervals.
- 5
Highlight keeping up-to-date with industry best practices.
Example Answers
I follow ISO 12925 for industrial lubricants and ensure I adhere to manufacturer recommendations for lubrication intervals and types of lubricants used. Safety is also a priority, so I handle all materials according to MSDS guidelines.
How do you incorporate preventive maintenance in your lubrication routines?
How to Answer
- 1
Review equipment manuals to determine lubrication intervals
- 2
Monitor equipment performance trends to identify lubrication needs
- 3
Keep accurate records of lubrication activities and equipment condition
- 4
Implement a schedule for regular lubrication checks and maintenance
- 5
Educate team members on the importance of proper lubrication practices
Example Answers
I ensure to follow the manufacturer's guidelines for lubrication intervals and regularly check equipment performance to adjust lubrication based on observed trends.
Situational Interview Questions
If you discovered that a machine was operating at a higher temperature than normal due to inadequate lubrication, what steps would you take to address this?
How to Answer
- 1
Immediately shut down the machine to prevent damage
- 2
Inspect lubrication levels and replenish with the proper lubricant
- 3
Check for any blockages in lubrication lines or filters
- 4
Evaluate the lubrication schedule and adjust if necessary
- 5
Document the issue and report it to the supervisor for further action
Example Answers
I would first shut down the machine to prevent any potential damage. Then, I would check the lubrication levels and refill them as needed. After that, I would inspect the lubrication lines for blockages and ensure everything is functioning properly. Finally, I would inform my supervisor about the situation.
You have multiple machines requiring lubrication at the same time. How would you prioritize your workload?
How to Answer
- 1
Identify which machines are most critical to operations.
- 2
Check for any machines that have lubrication schedules or timelines.
- 3
Consider the severity of the lubrication needs for each machine.
- 4
Communicate with your team to align on priorities.
- 5
Use a systematic approach to tackle one machine at a time efficiently.
Example Answers
I would first identify the machines crucial to current production. Then, I’d look at their lubrication schedules to see if any are overdue. If one machine is at risk of damage, I would prioritize that one, while communicating with my team about the status and progress.
Don't Just Read Lubricator Questions - Practice Answering Them!
Reading helps, but actual practice is what gets you hired. Our AI feedback system helps you improve your Lubricator interview answers in real-time.
Personalized feedback
Unlimited practice
Used by hundreds of successful candidates
If you and a colleague disagree on the best type of lubricant to use for a specific application, how would you resolve the situation?
How to Answer
- 1
Listen to your colleague's reasoning and validate their perspective.
- 2
Present your own evidence or experience supporting your choice of lubricant.
- 3
Suggest discussing the specific requirements of the application to clarify needs.
- 4
Consider discussing the pros and cons of each option together.
- 5
Propose a small test or trial to evaluate both lubricants in practice.
Example Answers
I would first listen to my colleague's perspective and ensure I understand their reasoning. Then, I would share my own experience with the lubricant I recommend. Together, we could discuss the specific application needs and pros and cons, and if needed, suggest a trial to see which option performs better.
Imagine you have a tight deadline and notice that an important lubrication component is not functioning correctly. What would you do?
How to Answer
- 1
Quickly assess the extent of the issue with the lubrication component.
- 2
Prioritize immediate actions to either fix or temporarily bypass the problem.
- 3
Communicate with your team about the issue and your plan.
- 4
Document the problem and actions taken for future reference.
- 5
Focus on maintaining safety while addressing the lubrication issue.
Example Answers
First, I would assess the lubrication component to see if it can be repaired quickly. If it can't, I would find a suitable temporary solution to keep the equipment running while informing my supervisor and team about the situation.
If you are tasked with creating lubrication protocols for new machinery, what factors would you consider?
How to Answer
- 1
Identify the type of machinery and its operational conditions.
- 2
Consider the manufacturer's specifications for lubrication.
- 3
Assess the environmental conditions where the machinery will operate.
- 4
Determine the best lubrication materials based on compatibility and performance.
- 5
Establish a maintenance schedule based on usage patterns and wear rates.
Example Answers
I would start by understanding the machinery and its operating environment to tailor the lubrication accordingly. Then, I'd refer to the manufacturer's guidelines for the correct lubricants and intervals.
How would you respond if a lubrication system malfunctioned and resulted in a machine breakdown during production?
How to Answer
- 1
Assess the situation quickly to understand the extent of the malfunction
- 2
Communicate immediately with your team to halt production and ensure safety
- 3
Isolate the affected machinery to prevent further damage
- 4
Diagnose the lubrication issue and identify root causes
- 5
Implement corrective actions and document the incident for future reference
Example Answers
I would first assess the malfunction to determine how serious it is. After that, I would communicate with my team to stop production, ensuring everyone is safe. Then, I would isolate the machine to avoid more issues while diagnosing what went wrong with the lubrication system.
You receive feedback from a supervisor about your lubrication methods not meeting standards. How would you approach this feedback?
How to Answer
- 1
Acknowledge the feedback without being defensive
- 2
Ask for specific examples of the issues observed
- 3
Discuss how you plan to improve your techniques
- 4
Show willingness to learn and adapt your methods
- 5
Follow up after implementing changes to demonstrate progress
Example Answers
I appreciate the feedback and would like to understand exactly what methods did not meet the standards. I will review my techniques, seek additional training if necessary, and ensure I apply any changes moving forward.
If you were part of a team where some members are resistant to your lubrication strategies, how would you handle it?
How to Answer
- 1
Understand their concerns and ask for feedback
- 2
Clearly explain the benefits of your lubrication strategies
- 3
Demonstrate effectiveness with data or examples
- 4
Find common ground and collaborate on solutions
- 5
Stay patient and open to ongoing dialogue
Example Answers
I would first meet with my team members to understand their reservations regarding my lubrication strategies. Listening to their concerns can help me tailor my approach and provide solutions that address their doubts. I would then present clear data showing the success of my methods in previous scenarios, aiming to show how these strategies can positively impact our results. Collaboration is key, so I would suggest we adapt parts of the strategy together to create a compromise that works for everyone.
If you had the chance to introduce a new lubrication technology to your workplace, how would you present your case?
How to Answer
- 1
Research the lubrication technology and its benefits thoroughly
- 2
Prepare data on cost savings and efficiency improvements
- 3
Identify potential challenges and solutions to address them
- 4
Engage key stakeholders early in the process for their input
- 5
Use a clear and structured presentation format to communicate your ideas
Example Answers
I would start by researching the new lubrication technology extensively, highlighting its key benefits such as reduced friction and increased equipment lifespan. Then, I would gather data on how it can lead to cost savings through lower maintenance downtime. I would also address potential challenges by proposing a phased implementation plan and seek feedback from my team to ensure buy-in.
Lubricator Position Details
Recommended Job Boards
These job boards are ranked by relevance for this position.
Related Positions
- Machine Oiler
- Grease Worker
- Car Greaser
- Pump Oiler
- Grease Packer
- Grease Man
- Crane Oiler
- Oiler
- Belt Lacer
- Maintenance Man
Similar positions you might be interested in.
Ace Your Next Interview!
Practice with AI feedback & get hired faster
Personalized feedback
Used by hundreds of successful candidates
Ace Your Next Interview!
Practice with AI feedback & get hired faster
Personalized feedback
Used by hundreds of successful candidates