Top 29 Greaser Interview Questions and Answers [Updated 2025]
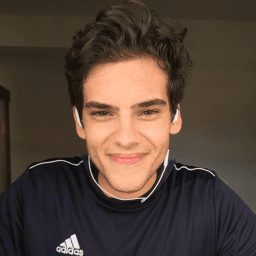
Andre Mendes
•
March 30, 2025
Preparing for a Greaser role interview? Look no further! This blog post is your ultimate guide to the most common interview questions you'll face in this field. We've compiled insightful example answers and expert tips to help you respond effectively and confidently. Whether you're a seasoned professional or new to the industry, these strategies will set you up for success in your next interview.
Download Greaser Interview Questions in PDF
To make your preparation even more convenient, we've compiled all these top Greaserinterview questions and answers into a handy PDF.
Click the button below to download the PDF and have easy access to these essential questions anytime, anywhere:
List of Greaser Interview Questions
Behavioral Interview Questions
Can you describe a time when you worked as part of a team to repair a complex mechanical issue?
How to Answer
- 1
Start with a brief overview of the mechanical issue.
- 2
Explain your specific role within the team.
- 3
Highlight collaboration and communication with team members.
- 4
Mention the steps taken to diagnose and repair the issue.
- 5
Conclude with the successful outcome and what you learned.
Example Answers
In my previous job, our team faced a failing transmission in a fleet vehicle. I took the lead in diagnosing the issue by running tests and gathering data. I communicated findings during team meetings and helped assign tasks based on each member's strengths. We successfully replaced the faulty components and completed the repair ahead of schedule, which improved vehicle reliability. This experience taught me the importance of teamwork and clear communication.
Tell me about a situation where you identified a significant problem during a maintenance check. How did you approach it?
How to Answer
- 1
Start with a specific context or setting
- 2
Clearly describe the problem you found
- 3
Explain your investigation and thought process
- 4
Detail the steps you took to resolve the issue
- 5
Highlight the outcome and any lessons learned
Example Answers
During a routine check, I noticed unusual wear on the belt of a machine. I researched the wear patterns and consulted the equipment manual. I replaced the belt and adjusted the tension. This prevented a potential breakdown and improved machine efficiency.
Don't Just Read Greaser Questions - Practice Answering Them!
Reading helps, but actual practice is what gets you hired. Our AI feedback system helps you improve your Greaser interview answers in real-time.
Personalized feedback
Unlimited practice
Used by hundreds of successful candidates
Describe a time when you had to quickly learn a new technique or tool. How did you manage the situation?
How to Answer
- 1
Identify a specific situation where you had to learn quickly.
- 2
Explain what motivated you to learn the new technique or tool.
- 3
Detail the steps you took to learn effectively under pressure.
- 4
Highlight the outcome and any challenges you overcame.
- 5
Reflect on what you learned from the experience.
Example Answers
At my previous job, I had to learn a new diagnostic tool for a client project. I dedicated a weekend to studying the manual and watching tutorial videos. During the first week, I practiced extensively with guidance from a senior technician. As a result, I completed the project on time and improved the team's efficiency with the new tool.
Give an example of how you communicated a technical issue to a non-technical colleague or customer.
How to Answer
- 1
Use simple language without jargon
- 2
Focus on the customer's perspective and needs
- 3
Explain the impact of the issue clearly
- 4
Offer a solution or next steps
- 5
Be empathetic and reassuring
Example Answers
I had to inform a customer that their software was experiencing downtime. I explained it simply by saying, 'Our system is currently having some issues, and I understand this might impact your work. We are investigating and expect to have it fixed soon. In the meantime, I recommend saving your progress frequently.'
Tell me about a time you had a conflict with a team member. How did you resolve it?
How to Answer
- 1
Choose a specific conflict that shows your problem-solving skills
- 2
Focus on your role in the situation and your actions
- 3
Explain the resolution process clearly and simply
- 4
Highlight what you learned from the experience
- 5
Emphasize teamwork and maintaining relationships
Example Answers
In a project, a team member and I disagreed on the approach. I initiated a one-on-one discussion where we both shared our perspectives. We found common ground and agreed to merge our ideas, which improved the project's outcome. I learned the importance of open communication.
Can you provide an example that demonstrates your dedication to maintaining high work standards?
How to Answer
- 1
Think of a specific situation from your past work experience.
- 2
Focus on a challenge you faced and how you addressed it.
- 3
Highlight the steps you took to ensure quality and standards.
- 4
Mention any recognition or feedback you received as a result.
- 5
Keep your response clear and to the point.
Example Answers
In my previous job at a local garage, I noticed that customer complaints about service quality were increasing. I implemented a checklist for vehicle inspections, ensuring every detail was checked before delivery. This reduced complaints by 40% and increased customer satisfaction scores.
Can you discuss a mistake you made in your work and what you learned from it?
How to Answer
- 1
Choose a real mistake that had a clear impact.
- 2
Briefly explain the situation and your role in it.
- 3
Discuss the specific action you took that led to the mistake.
- 4
Highlight the lesson learned and how you applied it afterward.
- 5
Show growth by relating it to your current work ethic or approach.
Example Answers
In my last job, I miscalculated a budget forecast which led to overspending. I learned the importance of double-checking my data and asking for a second opinion. Now, I always review budgets with a colleague before finalizing.
What interests you most about the work you do as a greaser?
How to Answer
- 1
Highlight your passion for mechanical work and problem solving.
- 2
Mention the enjoyment of working in a hands-on environment.
- 3
Discuss the teamwork aspect and camaraderie among colleagues.
- 4
Express interest in learning new skills and techniques.
- 5
Share how you appreciate maintaining and improving vehicle performance.
Example Answers
I love the hands-on nature of being a greaser. There's something satisfying about diagnosing problems and getting engines to run smoothly.
Technical Interview Questions
What are the most common types of mechanical repairs you have performed in previous positions?
How to Answer
- 1
Focus on relevant repairs that align with the greaser role
- 2
Use specific examples to illustrate your experience
- 3
Mention any tools or equipment you utilized
- 4
Highlight your problem-solving skills during repairs
- 5
Conclude with a brief note on your ability to learn new techniques
Example Answers
In my previous role, I regularly performed brake repairs, including replacing pads and rotors. I used hydraulic tools and ensured safety standards were met. I also diagnosed engine issues with diagnostic software.
What diagnostic tools are you proficient in using, and how do you apply them in your work?
How to Answer
- 1
Identify specific tools you know well.
- 2
Explain how each tool helps diagnose issues.
- 3
Mention any relevant experiences using these tools.
- 4
Focus on outcomes or improvements made through their use.
- 5
Be prepared to discuss learning new tools if required.
Example Answers
I am proficient in using diagnostic software like AutoMate and ScanTool. I apply these tools to diagnose vehicle performance issues by analyzing real-time data and error codes, which helps me identify root causes and improve repair times.
Don't Just Read Greaser Questions - Practice Answering Them!
Reading helps, but actual practice is what gets you hired. Our AI feedback system helps you improve your Greaser interview answers in real-time.
Personalized feedback
Unlimited practice
Used by hundreds of successful candidates
What standard maintenance procedures do you follow to ensure machinery operates efficiently?
How to Answer
- 1
Start with daily checks for oil levels and coolant.
- 2
Follow a weekly inspection routine for belts and filters.
- 3
Establish a monthly cleaning schedule to remove debris.
- 4
Document any irregularities during these checks for follow-up.
- 5
Stay updated on manufacturer recommendations for specific machinery.
Example Answers
I perform daily oil and coolant checks and inspect for leaks. Weekly, I check the belts and replace filters as needed. Monthly, I ensure the machinery is clean and review any noted irregularities.
Can you explain the safety regulations you adhere to while performing repairs?
How to Answer
- 1
Start with personal protective equipment such as gloves and goggles
- 2
Mention compliance with local and federal safety standards
- 3
Discuss proper tool usage and regular maintenance checks
- 4
Highlight the importance of a clean and organized workspace
- 5
Include emergency procedures and first aid readiness
Example Answers
I always wear gloves and goggles to protect myself while working. I make sure to follow OSHA regulations and ensure all tools are well-maintained before use to avoid accidents.
What types of lubrication techniques do you find most effective for machinery upkeep?
How to Answer
- 1
Mention specific types of lubricants like grease or oil suitable for different machinery.
- 2
Discuss the importance of regular lubrication schedules to prevent wear and tear.
- 3
Highlight techniques such as full immersion, drip lubrication, or manual application based on machinery types.
- 4
Include personal experience with a lubrication technique that significantly improved machine performance.
- 5
Emphasize safety practices when handling lubricants.
Example Answers
I find using a high-quality synthetic grease most effective for heavy-duty machinery. Regular lubrication every 500 operating hours has helped me prevent breakdowns.
How do you document repairs and maintenance procedures that you've implemented?
How to Answer
- 1
Use a standardized format for all documentation to ensure consistency.
- 2
Include key details such as date, equipment type, issue found, and steps taken.
- 3
Utilize digital tools or software for easy access and organization.
- 4
Implement a review process to check for accuracy and completeness.
- 5
Maintain regular updates to the documentation after each repair or maintenance task.
Example Answers
I document all repairs using a standardized template that includes the date, equipment type, issue, and steps taken. This consistency helps in understanding past repairs.
What experience do you have working with electrical systems in machinery?
How to Answer
- 1
Highlight specific types of machinery you've worked on.
- 2
Mention relevant training or certifications you've obtained.
- 3
Describe a specific project or repair you've completed involving electrical systems.
- 4
Emphasize problem-solving skills in diagnosing electrical issues.
- 5
Include safety procedures you follow when working with electrical components.
Example Answers
I have experience working on industrial conveyors, where I diagnosed and repaired electrical faults. I completed a certification in industrial electrical systems, which helped me understand the wiring and components involved.
Can you describe your experience with hydraulic systems and any specific projects involving them?
How to Answer
- 1
Identify key projects that involved hydraulic systems.
- 2
Highlight specific roles you played in those projects.
- 3
Mention any tools or technologies you used.
- 4
Discuss successful outcomes or learnings from each project.
- 5
Keep your response focused and relevant to the position.
Example Answers
In my previous role, I worked on a project where I helped design a hydraulic lift system for warehouse use. I was responsible for selecting hydraulic components and ensuring they met safety standards. This project improved our load handling efficiency by 30%.
What types of engine systems have you worked on, and what specific repairs did you handle?
How to Answer
- 1
Identify key engine systems you've worked with like gasoline, diesel, or hybrid.
- 2
Mention specific repairs such as overhauls, valve adjustments, or fuel injector replacements.
- 3
Describe any relevant tools or technologies you used during repairs.
- 4
Highlight your problem-solving skills in diagnosing issues.
- 5
Be prepared to discuss any challenges faced and how you overcame them.
Example Answers
I have worked on gasoline and diesel engines. I recently handled a complete overhaul of a diesel engine, which involved replacing the cylinder head and re-tuning the fuel system for better efficiency.
Situational Interview Questions
If you were working on a machine and it suddenly broke down, what steps would you take to address the issue?
How to Answer
- 1
Stay calm and assess the situation quickly
- 2
Identify the cause of the breakdown if possible
- 3
Follow safety protocols and shut down the machine
- 4
Communicate the issue to your supervisor or team
- 5
Document the problem and steps taken to address it
Example Answers
First, I would stay calm and quickly assess what happened. I'd turn off the machine following safety protocols and try to identify any visible issues. Then, I would inform my supervisor about the breakdown and document what I've observed.
How would you prioritize multiple repair requests when time is limited?
How to Answer
- 1
Assess the safety implications of each repair request first
- 2
Determine the impact on operations for each issue
- 3
Estimate the time required for each repair
- 4
Communicate with the team about priorities and progress
- 5
Stay organized and document all requests for future reference
Example Answers
First, I would evaluate which repairs pose a safety risk and address those immediately. Then, I would look at the requests that affect operations the most, prioritizing them based on urgency. I would keep the team informed about what I'm working on to ensure smooth communication.
Don't Just Read Greaser Questions - Practice Answering Them!
Reading helps, but actual practice is what gets you hired. Our AI feedback system helps you improve your Greaser interview answers in real-time.
Personalized feedback
Unlimited practice
Used by hundreds of successful candidates
If you were asked to train a new greaser, what key skills or knowledge would you emphasize?
How to Answer
- 1
Highlight technical skills in auto maintenance and repair
- 2
Emphasize the importance of teamwork and communication
- 3
Stress safety practices in the shop environment
- 4
Encourage attention to detail in diagnosing issues
- 5
Teach time management for efficient service delivery
Example Answers
I would emphasize technical skills like car diagnostics and repair, as well as the importance of working well with the team. Safety practices are crucial too, so I'd make sure they know how to stay safe in the shop.
How would you handle a situation where you were missing critical tools or parts to complete a repair?
How to Answer
- 1
Stay calm and assess the situation quickly
- 2
Identify exactly what tools or parts are missing
- 3
Look for alternative tools that could substitute
- 4
Communicate with your team or supervisor for additional resources
- 5
If necessary, prioritize tasks and create a plan for completing the repair later
Example Answers
If I find I'm missing critical tools, I first check what I do have that could work as a substitute. I’ll then communicate with my supervisor to see if those parts can be sourced quickly. If not, I'll prioritize what's already finished and plan to come back to it once I have the necessary tools.
If a teammate is consistently making mistakes during repairs, how would you address this?
How to Answer
- 1
Approach the teammate privately to avoid embarrassment.
- 2
Use specific examples of the mistakes to illustrate the issue.
- 3
Encourage an open dialogue to understand their perspective.
- 4
Offer help or resources to improve their skills.
- 5
Follow up to ensure the improvements are being implemented.
Example Answers
I would first speak to my teammate privately about the mistakes, providing specific examples. I'd ask if they are facing any challenges and offer my assistance or resources to help them improve.
If you noticed a quality issue in a repair you completed, what would your response be?
How to Answer
- 1
Acknowledge the issue quickly and take responsibility
- 2
Assess the impact of the quality issue and gather details
- 3
Communicate the problem to your supervisor or team immediately
- 4
Plan for correction, including steps to fix the issue
- 5
Reflect on the incident to prevent future occurrences
Example Answers
I would first admit the mistake and gather all relevant details about the repair. Then, I would inform my supervisor about the issue and discuss the best way to correct it. After addressing the problem, I would take some time to think about how I can avoid similar issues in the future.
How would you handle negative feedback from a client regarding a repair you conducted?
How to Answer
- 1
Listen carefully to the client's concerns without interrupting
- 2
Acknowledge the client's feelings and validate their experience
- 3
Apologize for any inconvenience caused, regardless of fault
- 4
Offer a solution or corrective action to resolve the issue
- 5
Follow up to ensure satisfaction after addressing the feedback
Example Answers
I would first listen to the client's feedback fully and thank them for bringing it to my attention. Then, I would apologize for their inconvenience and propose a solution, such as offering a free follow-up repair.
Describe how you would handle an unexpected challenge during a repair process.
How to Answer
- 1
Stay calm and assess the situation quickly.
- 2
Identify the challenge and gather necessary information.
- 3
Discuss the problem with your team or supervisor for insights.
- 4
Adjust your repair plan based on the new information.
- 5
Document the issue and solution for future reference.
Example Answers
If I encounter an unexpected challenge like a faulty part, I would first assess the situation to understand the issue. Then, I would consult with my team to see if anyone has faced a similar problem. Based on their input, I would adjust my repair strategy and keep a record of the challenge and how I resolved it.
Imagine you have a tight deadline for a repair. How would you ensure that the work meets quality standards?
How to Answer
- 1
Prioritize tasks based on urgency and complexity
- 2
Break down the repair into manageable steps
- 3
Verify that you have all necessary tools and parts before starting
- 4
Perform quality checks at each stage of the repair
- 5
Communicate with teammates if collaboration is needed
Example Answers
I would first identify the most critical parts of the repair and tackle those first. After breaking it down into steps, I'd ensure I have all the tools ready, then check my work at each stage to maintain quality.
Don't Just Read Greaser Questions - Practice Answering Them!
Reading helps, but actual practice is what gets you hired. Our AI feedback system helps you improve your Greaser interview answers in real-time.
Personalized feedback
Unlimited practice
Used by hundreds of successful candidates
If an important machine is down and you have a deadline, what steps would you take to ensure timely resolution?
How to Answer
- 1
Assess the issue quickly to understand the severity and impact.
- 2
Notify your supervisor and relevant team members about the situation.
- 3
Determine if there are immediate fixes or alternatives available.
- 4
Prioritize tasks to manage the deadline effectively.
- 5
Document the problem and solutions for future reference.
Example Answers
I would first assess the machine to identify the problem, then inform my supervisor and the team. If there’s an easy fix, I’d tackle that first; otherwise, I’d look for a backup plan to meet our deadline.
Greaser Position Details
Recommended Job Boards
ZipRecruiter
www.ziprecruiter.com/Jobs/GreaserThese job boards are ranked by relevance for this position.
Related Positions
- Shop Mechanic
- Machine Mechanic
- Machinery Mechanic
- Grease Worker
- Car Greaser
- Grease Man
- Pan Greaser
- Lubricator
- Lubrication Technician
- Machine Oiler
Similar positions you might be interested in.
Ace Your Next Interview!
Practice with AI feedback & get hired faster
Personalized feedback
Used by hundreds of successful candidates
Ace Your Next Interview!
Practice with AI feedback & get hired faster
Personalized feedback
Used by hundreds of successful candidates