Top 32 Industrial Control Technician Interview Questions and Answers [Updated 2025]
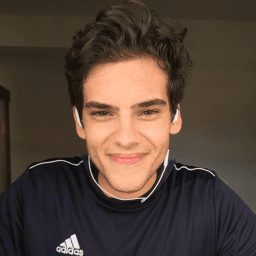
Andre Mendes
•
March 30, 2025
Navigating the interview process for an Industrial Control Technician role can be daunting, but preparation is key to success. In this blog post, we've compiled the most common interview questions you’ll encounter, along with example answers and insightful tips to help you respond effectively. Whether you're a seasoned professional or just starting out, this guide will equip you with the tools to impress and secure your next position.
Download Industrial Control Technician Interview Questions in PDF
To make your preparation even more convenient, we've compiled all these top Industrial Control Technicianinterview questions and answers into a handy PDF.
Click the button below to download the PDF and have easy access to these essential questions anytime, anywhere:
List of Industrial Control Technician Interview Questions
Behavioral Interview Questions
Give an example of a time you took the initiative to improve a process or system.
How to Answer
- 1
Choose a specific example from your experience.
- 2
Explain the problem or inefficiency you identified.
- 3
Describe the action you took to address the issue.
- 4
Highlight the positive outcome or impact of your initiative.
- 5
Keep it concise and relevant to the role of an Industrial Control Technician.
Example Answers
In my previous position, I noticed that the downtime during maintenance was excessive. I proposed a new scheduling system that grouped similar tasks, which reduced downtime by 20%. This improvement helped increase overall productivity.
Can you describe a time when you worked as part of a team to solve a complex technical problem?
How to Answer
- 1
Choose a specific project or situation that highlights teamwork.
- 2
Focus on your role and contributions to the team.
- 3
Explain the problem clearly and the steps taken to solve it.
- 4
Highlight any challenges faced and how the team overcame them.
- 5
Conclude with the positive outcome and what you learned.
Example Answers
In my last job, our team faced unexpected downtime in our HVAC control systems. I took the lead in gathering information, coordinating with electricians and software engineers. We mapped out the entire system and identified a faulty sensor as the root cause. We implemented a fix within hours, restoring operations quickly. I learned the importance of clear communication during crisis situations.
Don't Just Read Industrial Control Technician Questions - Practice Answering Them!
Reading helps, but actual practice is what gets you hired. Our AI feedback system helps you improve your Industrial Control Technician interview answers in real-time.
Personalized feedback
Unlimited practice
Used by hundreds of successful candidates
Tell me about a conflict you had with a colleague and how you resolved it.
How to Answer
- 1
Focus on a specific conflict and set the context clearly
- 2
Describe your role and feelings during the conflict
- 3
Explain the actions you took to resolve the conflict
- 4
Emphasize collaboration and communication in your resolution
- 5
Conclude with the positive outcome and what you learned
Example Answers
I had a disagreement with a colleague about the best methodology for solving a control system issue. I felt that my approach was more effective. I calmly discussed our different perspectives and proposed we test both methods. After running both simulations, my method proved to be more efficient, and we agreed to integrate the best aspects of both approaches. This not only resolved our conflict but also strengthened our working relationship.
Describe an instance where you encountered a major issue during an installation. How did you handle it?
How to Answer
- 1
Start with a clear description of the installation project.
- 2
Identify the specific issue that arose during the installation.
- 3
Explain the steps you took to diagnose and resolve the issue.
- 4
Highlight any collaboration with team members or stakeholders.
- 5
Conclude with the outcome and what you learned from the experience.
Example Answers
During an installation of a new control system at a manufacturing plant, we encountered a significant communication error between the PLC and the HMI. I quickly assessed the wiring and configuration settings, and worked with a colleague to review the programming. We discovered a misconfigured IP address, which we corrected, and the installation was completed successfully. This experience taught me the importance of thorough pre-installation testing.
Have you ever identified a safety risk in a control system? What actions did you take?
How to Answer
- 1
Recall a specific incident where you identified a risk.
- 2
Explain how you assessed the severity of the risk.
- 3
Describe the steps you took to mitigate or eliminate the risk.
- 4
Mention any collaboration with team members or safety protocols followed.
- 5
Highlight the outcome and any improvements made to the control system.
Example Answers
In a previous role, I noticed that the pressure sensors on our control system were malfunctioning, which could lead to over-pressurization. I immediately conducted a risk assessment and reported the issue to my supervisor. We isolated the affected system and replaced the sensors, which prevented a potential safety incident.
Can you give an example of a time when you had to learn a new technology quickly to complete a task?
How to Answer
- 1
Identify a relevant technology you learned quickly.
- 2
Explain the context and why it was necessary to learn it.
- 3
Describe the steps you took to learn it efficiently.
- 4
Mention the outcome and how it benefited the project.
- 5
Be specific about the skills or knowledge you gained.
Example Answers
In my previous role, I had to learn a new SCADA system in just a week. The system was crucial for an upcoming project. I focused on online tutorials and hands-on training. By the end of the week, I was able to run the system independently, which helped keep our project on schedule with no downtime.
Describe a situation where you had to lead a project or a team. How did you motivate your team?
How to Answer
- 1
Choose a specific project where you had a leadership role.
- 2
Explain your role in setting team goals and expectations.
- 3
Discuss how you communicated with your team and listened to their ideas.
- 4
Highlight how you recognized team efforts and achievements.
- 5
Mention any challenges faced and how you encouraged problem-solving.
Example Answers
In my previous role, I led a project to upgrade our control systems. I set clear goals for the team and held regular meetings to track progress. I encouraged team input and celebrated our milestones, which helped maintain high morale.
Discuss a time when your attention to detail made a significant difference in the outcome of a project.
How to Answer
- 1
Choose a specific project or task where detail was crucial.
- 2
Explain the context and your role in the project clearly.
- 3
Describe the specific details you focused on and how they were critical.
- 4
Share the outcome and how your attention to detail positively impacted it.
- 5
Use metrics or specific results to emphasize the significance.
Example Answers
During a recent maintenance project on a control system, I noticed that the wiring diagram had a missing connection. I took the time to double-check and clarify it with the engineering team, which prevented a potential malfunction that could have halted operations.
How do you prioritize tasks when working on multiple projects simultaneously?
How to Answer
- 1
List all tasks and deadlines to get a complete overview
- 2
Evaluate the urgency and importance of each task using a priority matrix
- 3
Communicate with team members to understand their needs and timelines
- 4
Focus on high-impact tasks that align with project goals first
- 5
Adjust priorities regularly based on project updates and feedback
Example Answers
I start by listing all tasks and their deadlines to see what I need to accomplish. Then, I use a priority matrix to evaluate which tasks are most urgent and important. I constantly communicate with my team to adjust priorities based on their needs.
Don't Just Read Industrial Control Technician Questions - Practice Answering Them!
Reading helps, but actual practice is what gets you hired. Our AI feedback system helps you improve your Industrial Control Technician interview answers in real-time.
Personalized feedback
Unlimited practice
Used by hundreds of successful candidates
Can you tell me about a time you had to perform under pressure? How did you handle it?
How to Answer
- 1
Choose a clear and relevant example from your experience.
- 2
Describe the situation and the pressure you faced succinctly.
- 3
Explain the specific actions you took to handle the pressure.
- 4
Highlight the results of your actions, showing a positive outcome.
- 5
Keep your answer focused and don't overload with unnecessary details.
Example Answers
During a major system failure at my last job, I had to quickly diagnose the issue. I gathered the team to assess the situation and we discovered a critical software bug. I coordinated the team's efforts to implement a temporary fix while another member worked on a long-term solution. We managed to restore operations in under two hours, minimizing downtime.
Technical Interview Questions
What PLC programming languages are you familiar with, and how have you used them in past projects?
How to Answer
- 1
List specific PLC languages like Ladder Logic, Function Block Diagram, or Structured Text.
- 2
Briefly describe a project where you applied these languages.
- 3
Highlight any specific outcomes or improvements from your programming.
- 4
Mention any troubleshooting or optimization tasks you performed.
- 5
Be ready to discuss tools or software you've used in conjunction with the languages.
Example Answers
I'm familiar with Ladder Logic and Structured Text. In a recent project, I programmed a PLC to automate a bottling line using Ladder Logic. This improved efficiency by 20% and reduced downtime during operations.
How would you diagnose a malfunction in a control system? What steps would you take?
How to Answer
- 1
Begin by checking the control system's display for error codes or alerts
- 2
Verify power supply and connections to ensure everything is functional
- 3
Inspect sensors and actuators for physical damage or disconnections
- 4
Use diagnostic tools like multimeters or oscilloscopes to test components
- 5
Review system logs for anomalies or patterns that indicate failures
Example Answers
First, I would check the control system's display for any error codes that could give clues about the malfunction. Then, I would ensure that the power supply is stable and all connections are secure. Next, I would inspect the sensors and actuators for any visible signs of failure and use diagnostic tools to test their operation. If necessary, I would also review system logs for additional insights.
Don't Just Read Industrial Control Technician Questions - Practice Answering Them!
Reading helps, but actual practice is what gets you hired. Our AI feedback system helps you improve your Industrial Control Technician interview answers in real-time.
Personalized feedback
Unlimited practice
Used by hundreds of successful candidates
Explain your experience with different types of sensors and instrumentation used in industrial control systems.
How to Answer
- 1
Identify key types of sensors you have worked with.
- 2
Describe specific applications or projects where you used these sensors.
- 3
Mention any relevant calibration or troubleshooting experience.
- 4
Emphasize your understanding of how these sensors integrate into control systems.
- 5
Conclude with how your experience can benefit the role you are applying for.
Example Answers
I have worked extensively with RTDs and thermocouples for temperature measurement in HVAC systems. In my previous job, I calibrated these sensors to ensure accurate readings for process control. This experience taught me about their integration with PLCs for monitoring critical temperatures.
Can you discuss your experience in designing user interfaces for human-machine interaction?
How to Answer
- 1
Highlight specific projects where you designed user interfaces.
- 2
Explain your design process and the tools you used.
- 3
Mention any user feedback you incorporated into your design.
- 4
Discuss how you ensured the interface was user-friendly.
- 5
Share examples of how your design improved efficiency or safety.
Example Answers
In my last role, I designed the user interface for a monitoring system used in a manufacturing plant. I used Sketch for the design and conducted user testing to gather feedback. Based on this feedback, I simplified navigation, which improved user engagement by 30%.
What is your understanding of industrial networking protocols, and how have you implemented them?
How to Answer
- 1
Identify key industrial networking protocols like Ethernet/IP, Modbus, and PROFINET.
- 2
Explain specific scenarios where you have used these protocols in your work.
- 3
Discuss the benefits and challenges you've experienced with these networking protocols.
- 4
Mention any relevant certifications or training in industrial networking.
- 5
Be prepared to talk about troubleshooting network issues related to these protocols.
Example Answers
I understand that industrial networking protocols such as Ethernet/IP and Modbus are crucial for communication between devices in automation. In my last role, I implemented Modbus TCP for connecting PLCs to SCADA systems, which improved data acquisition speed. While configuring the network, I faced challenges with device compatibility, but I resolved this by updating firmware, ensuring smooth communication.
What experience do you have with integrating different control systems and ensuring compatibility?
How to Answer
- 1
Identify specific types of control systems you have worked with.
- 2
Mention tools or software you used for integration.
- 3
Discuss a challenging integration project and how you overcame obstacles.
- 4
Highlight your understanding of communication protocols like Modbus or Ethernet/IP.
- 5
Emphasize the importance of testing and validation after integration.
Example Answers
In my previous role, I integrated PLCs with DCS using Ethernet/IP and Modbus. I utilized software like RSLogix for configuration. One challenging project involved troubleshooting communication issues, which I resolved by ensuring proper addressing and protocols were followed.
What steps do you take to ensure that all instruments in a control system are properly calibrated?
How to Answer
- 1
Review manufacturer guidelines for calibration procedures
- 2
Use standard calibration equipment that is regularly verified
- 3
Document calibration schedules and results for each instrument
- 4
Perform initial calibration checks before start-up and regularly thereafter
- 5
Adjust and fine-tune instruments based on calibration findings
Example Answers
I start by reviewing the manufacturer’s guidelines to understand the calibration process specific to each instrument. Then, I utilize calibrated standard equipment to ensure accuracy. I maintain a detailed record of calibration schedules and results, performing checks regularly.
What are some key safety standards you follow in industrial control projects?
How to Answer
- 1
Identify and understand OSHA regulations applicable in your field
- 2
Discuss the importance of risk assessments before starting any project
- 3
Mention the use of lockout/tagout procedures to ensure safety during maintenance
- 4
Emphasize the significance of following manufacturer guidelines for equipment
- 5
Highlight the need for regular training and safety audits to uphold standards
Example Answers
I always start by ensuring compliance with OSHA regulations specific to industrial control, and I conduct thorough risk assessments to identify potential hazards before beginning any project.
Can you explain how you utilize data analysis in troubleshooting control systems?
How to Answer
- 1
Identify key data metrics relevant to the control system such as temperature, pressure, or flow rates.
- 2
Use tools like spreadsheets or specialized software to organize and visualize data trends over time.
- 3
Analyze historical data to identify patterns or anomalies that may indicate underlying issues.
- 4
Correlate data from different sensors to pinpoint the source of a problem more accurately.
- 5
Communicate findings clearly and suggest corrective actions based on your data analysis.
Example Answers
In troubleshooting control systems, I focus on key metrics like temperature and pressure. I use software tools to visualize these data trends, which helps me identify any anomalies. For instance, I once noticed a pressure drop coinciding with specific valve cycles, allowing me to replace a faulty valve quickly.
What importance do you place on documentation in industrial control systems, and how do you approach it?
How to Answer
- 1
Emphasize that documentation is crucial for safety and compliance.
- 2
Discuss how it aids in troubleshooting and maintenance.
- 3
Mention the role of documentation in training new team members.
- 4
Explain your process for creating and updating documentation.
- 5
Highlight the need for clear, detailed, and easily accessible documents.
Example Answers
I consider documentation essential in industrial control systems because it ensures safety, compliance, and effective troubleshooting. I maintain comprehensive documentation for all systems and update it regularly to reflect changes and upgrades. This helps not just in maintenance but also in training new employees who need to understand the systems quickly.
Don't Just Read Industrial Control Technician Questions - Practice Answering Them!
Reading helps, but actual practice is what gets you hired. Our AI feedback system helps you improve your Industrial Control Technician interview answers in real-time.
Personalized feedback
Unlimited practice
Used by hundreds of successful candidates
What fundamental concepts of control theory do you apply in your daily work as a technician?
How to Answer
- 1
Identify key control theory principles you use regularly
- 2
Relate your experience with feedback loops and PID controllers
- 3
Discuss how you implement system stability and performance
- 4
Mention troubleshooting techniques based on control theory
- 5
Provide examples of how theory translates into practical solutions
Example Answers
In my daily work, I frequently apply feedback control concepts, particularly PID controllers, to ensure system stability in our processes. For instance, I adjust the proportional, integral, and derivative parameters to achieve optimal performance in temperature control systems.
Situational Interview Questions
If a critical control system were to fail during operation, what immediate actions would you take?
How to Answer
- 1
Assess the situation to understand the impact of the failure.
- 2
Initiate safety protocols to protect personnel and equipment.
- 3
Attempt to reset or recover the system if safe to do so.
- 4
Communicate the issue to the relevant team members and management.
- 5
Document the incident and actions taken for further analysis.
Example Answers
In the event of a critical control system failure, I would first assess the situation to understand the risks. Next, I would activate our safety protocols to ensure everyone is safe. If possible, I would attempt to reset the system and then promptly inform my team and management about the situation.
Imagine you are close to a project deadline but see that a system isn't performing correctly. What do you do?
How to Answer
- 1
Assess the severity of the issue quickly
- 2
Prioritize communication with the team
- 3
Identify immediate steps to troubleshoot
- 4
Consider seeking help if necessary
- 5
Document the issue for future reference
Example Answers
I would first assess how critical the issue is and if it impacts the deadline. Then, I'd inform my team about the situation so we can brainstorm solutions together. I'd troubleshoot the system, starting with common issues, and if needed, reach out to a colleague for additional support.
Don't Just Read Industrial Control Technician Questions - Practice Answering Them!
Reading helps, but actual practice is what gets you hired. Our AI feedback system helps you improve your Industrial Control Technician interview answers in real-time.
Personalized feedback
Unlimited practice
Used by hundreds of successful candidates
How would you handle a situation where sudden changes are required in a control system design after implementation has begun?
How to Answer
- 1
Assess the necessity and impact of the changes immediately
- 2
Communicate with the team to gather insights and feedback
- 3
Prioritize changes based on urgency and feasibility
- 4
Develop a revised plan that includes timeline and resources required
- 5
Ensure all stakeholders are informed and aligned with the new plan
Example Answers
I would first assess the necessity of the changes to understand why they are needed. Then, I would communicate with my team to gather insights and evaluate the impact of these changes. After prioritizing the changes based on urgency, I would create a revised implementation plan and ensure all stakeholders are aligned before proceeding.
If you were given a limited budget for controls upgrades, how would you prioritize the upgrades?
How to Answer
- 1
Identify critical systems that have the highest risk of failure.
- 2
Consider upgrades that will provide the greatest efficiency improvements.
- 3
Evaluate which upgrades have the best return on investment.
- 4
Take into account any regulatory compliance needs.
- 5
Consult with team members to understand their pain points.
Example Answers
I would prioritize upgrades for critical systems that are outdated and prone to failure, ensuring we maintain plant safety first. After that, I'd look at efficiency improvements that could reduce energy costs.
How would you evaluate and implement a new technology in an existing control system?
How to Answer
- 1
Assess the current control system for compatibility with new technology
- 2
Conduct a cost-benefit analysis for implementation
- 3
Pilot the new technology in a controlled environment before full rollout
- 4
Gather feedback from operators and technicians during pilot
- 5
Create a comprehensive training plan for staff on the new technology
Example Answers
I would first evaluate the existing control system's architecture to ensure compatibility with the new technology. Then, I'd perform a cost-benefit analysis to see if the implementation makes sense financially. After piloting it on a small scale, I would gather feedback from the operators to make necessary adjustments before full deployment.
How would you approach training a new technician in the use of a control system?
How to Answer
- 1
Start with an overview of the control system, including key components.
- 2
Demonstrate basic operations through hands-on practice with the system.
- 3
Use real-world scenarios to explain troubleshooting techniques.
- 4
Encourage questions and provide frequent feedback during training.
- 5
Assess understanding through short quizzes or practical tests.
Example Answers
I would begin by giving the new technician a clear overview of the control system, explaining its components and functionalities. Then, I would let them operate the system in a controlled environment, guiding them through basic tasks. Throughout this process, I would encourage them to ask questions and provide feedback, ensuring they're comfortable. Finally, I would assess their understanding through a practical test to ensure they can apply what they've learned.
If a critical component from a vendor is delayed, what steps would you take to manage the situation?
How to Answer
- 1
Assess the impact of the delay on operations and timelines
- 2
Communicate with the vendor for an update and estimated delivery
- 3
Determine alternatives or workarounds to minimize downtime
- 4
Inform stakeholders about the situation and implications
- 5
Document the issue and actions taken for future reference
Example Answers
I would first assess how the delay affects our operations and which projects are impacted. Next, I would contact the vendor to get an update on the situation and see if they can expedite the delivery. In the meantime, I would look for temporary solutions or components that could substitute until we receive the required part and keep the relevant stakeholders informed.
If you had to collaborate with a software engineer to solve a control issue, how would you facilitate the communication?
How to Answer
- 1
Schedule regular meetings to discuss progress and issues
- 2
Use clear, technical language and avoid jargon if possible
- 3
Document all discussions and decisions for future reference
- 4
Encourage an open environment for asking questions and sharing ideas
- 5
Utilize visual aids like flowcharts or diagrams to illustrate problems
Example Answers
I would set up regular check-in meetings where we can discuss the control issue in detail. I would make sure to document our discussions and keep track of any actions needed. Using diagrams would help us visualize the issue and facilitate better understanding.
How would you approach testing and validating a new control system before it goes live?
How to Answer
- 1
Begin with reviewing the system specifications and requirements.
- 2
Develop a detailed test plan covering all functionalities.
- 3
Conduct unit tests on individual components before integration.
- 4
Perform integration testing to ensure all components work together correctly.
- 5
Simulate real-world scenarios to validate system performance under load.
Example Answers
I would start by reviewing the specifications to understand the system's requirements. Then, I would create a detailed test plan that includes unit tests for each component. After that, I'd conduct integration tests to check how components interact, followed by simulating real-world scenarios to ensure the system performs well before going live.
If you noticed a serious flaw in a system design that could lead to safety issues but it's already been approved, what would you do?
How to Answer
- 1
Acknowledge the importance of safety and compliance.
- 2
Clearly document the flaw and potential risks involved.
- 3
Gather supporting information or data to substantiate your claim.
- 4
Communicate the issue to the relevant stakeholders promptly.
- 5
Suggest possible solutions or alternatives to mitigate the risk.
Example Answers
I would first document the flaw in detail, including the potential risks it poses. Then, I would communicate this to my supervisor immediately, emphasizing the safety implications. I would also suggest a meeting with the design team to discuss possible redesigns or safety measures.
Don't Just Read Industrial Control Technician Questions - Practice Answering Them!
Reading helps, but actual practice is what gets you hired. Our AI feedback system helps you improve your Industrial Control Technician interview answers in real-time.
Personalized feedback
Unlimited practice
Used by hundreds of successful candidates
Industrial Control Technician Position Details
Recommended Job Boards
These job boards are ranked by relevance for this position.
Related Positions
Ace Your Next Interview!
Practice with AI feedback & get hired faster
Personalized feedback
Used by hundreds of successful candidates
Ace Your Next Interview!
Practice with AI feedback & get hired faster
Personalized feedback
Used by hundreds of successful candidates