Top 31 Valve Technician Interview Questions and Answers [Updated 2025]
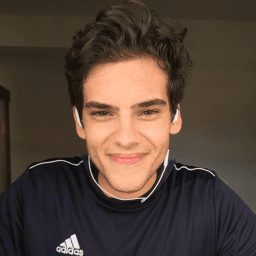
Andre Mendes
•
March 30, 2025
Preparing for a Valve Technician interview can be daunting, but we're here to help you succeed. In this post, you'll find the most common interview questions for the Valve Technician role, complete with example answers and strategic tips on how to respond effectively. Whether you're a seasoned professional or a newcomer to the field, these insights will help you confidently tackle any interview challenge.
Download Valve Technician Interview Questions in PDF
To make your preparation even more convenient, we've compiled all these top Valve Technicianinterview questions and answers into a handy PDF.
Click the button below to download the PDF and have easy access to these essential questions anytime, anywhere:
List of Valve Technician Interview Questions
Behavioral Interview Questions
Can you describe a time you worked as part of a team to troubleshoot a valve issue?
How to Answer
- 1
Start with the specific issue and context you faced.
- 2
Explain your role and the team structure.
- 3
Detail the steps the team took to diagnose the problem.
- 4
Discuss the outcome and what was learned.
- 5
Highlight teamwork and communication throughout the process.
Example Answers
In my previous role, our team faced a leaking valve that was affecting production. I was responsible for gathering data and analyzing the valve performance. We held a team meeting to discuss possible causes, and I suggested reviewing the maintenance logs. After narrowing down the issue, we discovered a faulty seal. We replaced it together, and the leak was resolved, improving our efficiency by 20%. I learned the value of collaborative problem-solving.
Tell me about a challenging valve repair you encountered. How did you handle it?
How to Answer
- 1
Describe the specific valve issue clearly
- 2
Explain the steps you took to diagnose the problem
- 3
Discuss any tools or techniques you employed
- 4
Highlight the final outcome of the repair
- 5
Reflect on what you learned from the experience
Example Answers
I once had a valve that wouldn’t close properly due to corrosion. I diagnosed it by checking the stem and finding pitting. I used a wire brush to clean the affected area and then applied a special sealant. The valve worked perfectly after the repair, and I learned to check for corrosion more regularly.
Don't Just Read Valve Technician Questions - Practice Answering Them!
Reading helps, but actual practice is what gets you hired. Our AI feedback system helps you improve your Valve Technician interview answers in real-time.
Personalized feedback
Unlimited practice
Used by hundreds of successful candidates
Describe a situation where you had to explain a technical issue to someone without a technical background.
How to Answer
- 1
Identify a specific technical issue you dealt with.
- 2
Explain the problem in simple terms without jargon.
- 3
Use analogies or relatable examples to clarify concepts.
- 4
Be patient and encourage questions to ensure understanding.
- 5
Summarize the key points at the end of your explanation.
Example Answers
In my previous job, I had to explain why a network issue was causing downtime. I described the network like a series of roads, where traffic jams could occur. I used a simple map analogy to show where the backups were and confirmed they understood by asking if they had any questions.
Give an example of a time when your attention to detail prevented a major problem.
How to Answer
- 1
Think of a specific situation where your attention to detail was crucial.
- 2
Describe what the potential problem was if you hadn't caught the detail.
- 3
Explain the actions you took to ensure everything was correct.
- 4
Mention the positive outcome resulting from your actions.
- 5
Keep your answer concise and focused on the details.
Example Answers
In my previous job as a quality control technician, I noticed a small deviation in the specifications of a valve component. If I hadn't caught it, it could have led to a product recall. I communicated the issue to my team, and we adjusted our production process, which resulted in saving the company a significant amount in potential losses.
Describe a time when you had to quickly learn a new skill or technology related to valves.
How to Answer
- 1
Identify a specific situation
- 2
Explain the context and urgency
- 3
Describe the new skill or technology
- 4
Highlight your learning process and resources used
- 5
Conclude with the impact of your learning
Example Answers
During a valve repair project, I was assigned to work with a new digital valve positioner. With only a week to understand it, I attended a workshop and used online tutorials to learn its programming. I implemented the new settings effectively, resulting in improved system efficiency.
Describe how you handle receiving constructive criticism from supervisors or clients.
How to Answer
- 1
Listen actively and avoid being defensive
- 2
Thank the person giving the feedback for their input
- 3
Reflect on the feedback before responding
- 4
Identify specific areas for improvement based on the feedback
- 5
Demonstrate how you plan to apply the feedback in your work
Example Answers
When I receive constructive criticism, I listen carefully and make sure I understand the points being made. I thank the supervisor for their feedback and take a moment to reflect on it. For instance, when I was told my report lacked clarity, I revised it by using bullet points to present information more effectively. I also asked for any further suggestions they might have for improvement.
What resources do you utilize to keep up with the latest technologies and methods in valve technology?
How to Answer
- 1
Mention specific industry publications for updates.
- 2
Refer to online courses or webinars for skill enhancement.
- 3
Discuss participation in professional organizations or forums.
- 4
Highlight the importance of networking with industry professionals.
- 5
Explain how you use company resources or tools for ongoing learning.
Example Answers
I regularly read industry publications like Valve Magazine and follow key blogs. Additionally, I attend webinars hosted by organizations like ISA to learn about the latest technologies. I also network with professionals at trade shows to exchange knowledge.
Tell me about a successful project you completed related to valve systems and what made it successful.
How to Answer
- 1
Begin with a clear project description, including objectives and context.
- 2
Highlight your specific role and responsibilities in the project.
- 3
Discuss the techniques or tools you used to ensure success.
- 4
Mention the outcomes and how they benefited the team or company.
- 5
Conclude with lessons learned or how this experience shaped your skills.
Example Answers
In a recent project, I worked on upgrading valve controls for a wastewater treatment plant. My role was to lead the team in designing an automated control system. We successfully implemented real-time monitoring, reducing valve failure rates by 30%. This project taught me the importance of effective communication and teamwork.
Don't Just Read Valve Technician Questions - Practice Answering Them!
Reading helps, but actual practice is what gets you hired. Our AI feedback system helps you improve your Valve Technician interview answers in real-time.
Personalized feedback
Unlimited practice
Used by hundreds of successful candidates
Technical Interview Questions
What are the different types of valves you’ve worked with, and what are their specific applications?
How to Answer
- 1
Identify specific types of valves you have hands-on experience with.
- 2
For each valve type, briefly explain its application in your previous roles.
- 3
Mention any relevant projects where you utilized these valves.
- 4
Focus on how your experience with each type has informed your skills as a technician.
- 5
Keep your answers concise and relevant to the position you're applying for.
Example Answers
I have worked primarily with ball valves, gate valves, and check valves. Ball valves are effective for on/off control in piping systems, while gate valves are excellent for flow regulation. In a recent project, I used ball valves to manage fluid flow in a chemical processing plant.
What routine maintenance practices do you recommend for ensuring valve functionality?
How to Answer
- 1
Inspect valves regularly for leaks or abnormalities.
- 2
Lubricate moving parts to prevent sticking or seizing.
- 3
Check and replace seals or gaskets as needed to maintain integrity.
- 4
Test valve operations periodically to ensure accurate performance.
- 5
Document maintenance activities and findings for future reference.
Example Answers
I recommend conducting regular visual inspections to identify leaks and checking for any signs of corrosion. Additionally, lubricating moving components helps maintain smooth operation.
Don't Just Read Valve Technician Questions - Practice Answering Them!
Reading helps, but actual practice is what gets you hired. Our AI feedback system helps you improve your Valve Technician interview answers in real-time.
Personalized feedback
Unlimited practice
Used by hundreds of successful candidates
How do you diagnose a valve that is not functioning correctly?
How to Answer
- 1
Start by visually inspecting the valve for signs of damage or wear.
- 2
Check for leaks around the valve and any associated piping.
- 3
Test the actuator (if applicable) to ensure it’s operating properly.
- 4
Listen for unusual noises during operation that could indicate issues.
- 5
Use diagnostic tools to measure flow rates and pressure drops across the valve.
Example Answers
I begin by performing a visual inspection to look for any obvious damage. Next, I check for leaks around the valve and ensure that the actuator is operating correctly. If everything seems fine, I listen for any unusual noises that could indicate an internal issue.
What tools and equipment do you typically use for valve repair and maintenance?
How to Answer
- 1
List specific tools relevant to valve repair like wrenches, pliers, or special valve tools.
- 2
Mention safety equipment such as gloves and goggles to highlight awareness of safety.
- 3
Discuss any diagnostic tools you use to assess valve performance.
- 4
Include examples of any equipment used for testing, such as pressure gauges.
- 5
Keep your answer focused on both mechanical and diagnostic aspects.
Example Answers
I typically use a variety of wrenches, pliers, and valve lapping tools for mechanical repairs. I also ensure to use safety goggles and gloves while working.
What kinds of materials are often used in valve manufacturing, and how do they affect performance?
How to Answer
- 1
Identify common materials like stainless steel, bronze, and plastic.
- 2
Explain the properties of each material, such as corrosion resistance and strength.
- 3
Discuss how the material choice impacts the valve's application, like pressure handling.
- 4
Mention any industry standards related to material use in valve manufacturing.
- 5
Be prepared to give examples of specific valves and their material applications.
Example Answers
Common materials used in valve manufacturing include stainless steel for its durability and corrosion resistance, bronze for excellent strength and wear resistance, and plastic, which is lightweight and suitable for lower pressure applications. The choice of material directly influences the valve's performance and longevity.
What industry standards do you follow in valve maintenance and installation?
How to Answer
- 1
Identify and mention relevant standards like API, ASME, or ISO.
- 2
Discuss specific procedures you follow for regular maintenance checks.
- 3
Emphasize the importance of safety protocols and compliance with local regulations.
- 4
Mention any relevant certifications you hold that relate to valve work.
- 5
Highlight your experience with industry-standard tools and technologies.
Example Answers
I follow API 598 for valve inspection and testing, ensuring all installed valves are operational and leak-free as per the guidelines.
How do you conduct performance tests on valves after repairs?
How to Answer
- 1
Identify the specific type of valve and its operational requirements.
- 2
Establish baseline performance metrics before testing.
- 3
Utilize appropriate testing equipment like pressure gauges and flow meters.
- 4
Conduct tests in a controlled environment to ensure accuracy.
- 5
Document the results and compare them to specifications.
Example Answers
I start by checking the valve type and its specifications to prepare relevant tests. I use pressure gauges to monitor the pressure drop across the valve while checking for leaks. Finally, I document the results to ensure the valve meets the performance requirements.
What steps do you follow when troubleshooting pneumatic valves?
How to Answer
- 1
Begin by visually inspecting the valve for any obvious signs of damage or leaks
- 2
Check the supply pressure and ensure it matches the specifications for the valve
- 3
Test the valve's operation by manually actuating it and observing the response
- 4
Examine the pneumatic lines for blockages or restrictions
- 5
If issues persist, consult the manufacturer's manual for specific troubleshooting steps related to the model
Example Answers
I start by visually inspecting the valve to look for any signs of leaks or damage. Then, I check the supply pressure to ensure it is at the correct level. I also manually actuate the valve to see if it responds as expected.
What are the key steps you follow for the proper installation of a valve?
How to Answer
- 1
Read the manufacturer's installation manual for specific instructions.
- 2
Check the valve and piping system for compatibility and cleanliness.
- 3
Ensure the valve is oriented correctly according to flow direction.
- 4
Install gaskets and seals properly to prevent leaks.
- 5
Torque the bolts to the specified tightness to secure the valve.
Example Answers
First, I always consult the manufacturer's installation manual to ensure compliance with specific guidelines. Then, I inspect both the valve and the piping for cleanliness and compatibility. It's crucial to install the valve in the correct orientation based on the flow direction. I also make sure to use proper gaskets and seals to avoid any leaks. Finally, I torque the bolts to the manufacturer's specifications for a secure fit.
What is the role of control valves in a system, and how do they differ from other types of valves?
How to Answer
- 1
Define control valves and their primary function in regulating flow and pressure.
- 2
Explain how control valves adjust flow based on control signals.
- 3
Compare control valves with isolation and check valves in their purpose and function.
- 4
Discuss the performance implications of using control valves in a process system.
- 5
Highlight the importance of proper selection and sizing for control valves.
Example Answers
Control valves are crucial in controlling the flow and pressure within a system. They adjust flow rates according to signals from a control system. Unlike isolation valves, which simply shut off flow, control valves actively manage it to maintain desired conditions.
Don't Just Read Valve Technician Questions - Practice Answering Them!
Reading helps, but actual practice is what gets you hired. Our AI feedback system helps you improve your Valve Technician interview answers in real-time.
Personalized feedback
Unlimited practice
Used by hundreds of successful candidates
How important is documentation in valve maintenance, and what do you include in a maintenance log?
How to Answer
- 1
Emphasize the role of documentation in ensuring compliance and safety.
- 2
Include details on tracking maintenance frequency and results.
- 3
Mention the importance of recording any issues and resolutions.
- 4
Discuss how documentation aids in training and knowledge transfer.
- 5
Highlight the use of logs to analyze patterns for future maintenance.
Example Answers
Documentation is critical in valve maintenance as it ensures compliance and enhances safety. In a maintenance log, I include the date of service, the type of maintenance performed, any issues found, and resolutions. This helps track maintenance frequency, which is vital for reliability.
Situational Interview Questions
If you discovered a major leak in a valve during routine checks, what steps would you take immediately?
How to Answer
- 1
Assess the severity of the leak to determine the risk level.
- 2
Immediately alert your supervisor and relevant personnel.
- 3
Isolate the valve to stop the flow if safe to do so.
- 4
Document the incident and the actions taken.
- 5
Follow up with repairs and conduct safety checks.
Example Answers
First, I would evaluate how serious the leak is and whether it poses an immediate danger. Then, I would notify my supervisor and any necessary team members to ensure everyone is aware. If it is safe, I would isolate the valve to stop the leak. I would document everything that happened for future reference and to help with repairs.
Imagine you are behind schedule on a valve installation project. How would you handle it?
How to Answer
- 1
Assess the reasons for the delay clearly
- 2
Identify critical tasks that will get the project back on track
- 3
Communicate with your team to gather input and support
- 4
Reallocate resources efficiently to prioritize important tasks
- 5
Provide regular updates to stakeholders to maintain transparency
Example Answers
I would first analyze the causes of the delay and identify which tasks are critical. Next, I would rally the team for ideas to speed up the process while reallocating resources to priority areas. Keeping stakeholders informed is essential, so I would provide regular updates on our recovery plan.
Don't Just Read Valve Technician Questions - Practice Answering Them!
Reading helps, but actual practice is what gets you hired. Our AI feedback system helps you improve your Valve Technician interview answers in real-time.
Personalized feedback
Unlimited practice
Used by hundreds of successful candidates
If you and a coworker disagree on the best repair method for a valve, how would you resolve the conflict?
How to Answer
- 1
Listen actively to your coworker's perspective
- 2
Present your reasoning and evidence for your method
- 3
Suggest collaborating on a trial of both methods if possible
- 4
Focus on the end goal of the repair, not personal opinions
- 5
Seek input from a supervisor or more experienced colleague if needed
Example Answers
I would start by listening to my coworker's reasoning and understanding their perspective. Then, I would share my own approach and the rationale behind it. If we still disagree, I'd propose trying out both methods on a test valve to see which yields better results.
You have multiple valves requiring urgent repairs. How do you prioritize your tasks?
How to Answer
- 1
Assess the severity of each valve issue and its impact on operations.
- 2
Identify which valves affect safety or environment first.
- 3
Check the availability of repair tools and parts for each task.
- 4
Communicate with team members to understand any urgency from other areas.
- 5
Create a quick action plan based on your findings.
Example Answers
I would first evaluate each valve's problem, prioritizing those that could lead to safety hazards or environmental issues. Next, I would check what tools and parts I have on hand and coordinate with my team on the most urgent cases.
You are in a position where you must operate a valve under hazardous conditions. What safety precautions would you take?
How to Answer
- 1
Assess the environment for hazards such as pressure, temperature, and flammable materials
- 2
Wear appropriate personal protective equipment like gloves, goggles, and hard hats
- 3
Communicate with your team to ensure everyone is aware of the operation
- 4
Use lockout/tagout procedures to ensure the valve is safe to operate
- 5
Follow proper operational protocols and manufacturer guidelines
Example Answers
I would first assess the surroundings for any potential hazards. Then, I would wear my PPE including gloves and goggles. Before operating the valve, I would communicate with my team and ensure everyone is aware of the procedure, and finally, I would follow the lockout/tagout protocols to ensure safety.
If you were tasked with improving the efficiency of valve operations, what approach would you take?
How to Answer
- 1
Analyze current valve performance data to identify inefficiencies
- 2
Implement a preventive maintenance schedule to reduce failures
- 3
Train staff on valve operation best practices and troubleshooting
- 4
Explore technology upgrades for automation and monitoring
- 5
Collaborate with engineering to enhance valve design or selection
Example Answers
I would start by analyzing the current performance data to pinpoint specific inefficiencies in valve operations. Based on that analysis, I would implement a preventive maintenance schedule to ensure the valves operate smoothly and minimize downtime.
A client is dissatisfied with a valve you repaired. How would you handle this situation?
How to Answer
- 1
Acknowledge the client's concerns without being defensive
- 2
Ask for specific details about the dissatisfaction
- 3
Offer to inspect or test the valve on-site if possible
- 4
Communicate your plan to address the issue clearly
- 5
Follow up after the repair to ensure satisfaction
Example Answers
I would first listen carefully to the client's concerns and acknowledge their frustration. Then, I would ask them to explain the specific issues they are facing with the valve. I would offer to come out and inspect the valve, and discuss how I plan to resolve the problem. After fixing the issue, I would follow up to ensure they are satisfied with the repair.
Picture this: you made an error during a valve installation. How would you rectify the situation?
How to Answer
- 1
Acknowledge the error quickly and honestly.
- 2
Assess the situation to understand the impact of the mistake.
- 3
Inform your supervisor or team about the error immediately.
- 4
Develop a corrective plan to fix the installation mistake.
- 5
Document the error and the steps taken to resolve it.
Example Answers
I would first acknowledge my mistake to my team and assess how it affects the installation. Then, I would communicate with my supervisor, and together we would develop a corrective plan ensuring the valve is installed correctly adhering to safety standards.
How would you decide whether to repair or replace a malfunctioning valve?
How to Answer
- 1
Assess the extent of the damage to the valve
- 2
Consider the cost of repair versus replacement
- 3
Evaluate the valve's age and remaining useful life
- 4
Check for availability of replacement parts
- 5
Analyze the impact on system performance and reliability
Example Answers
If the damage is minimal and repair costs are low, I would choose to repair the valve. However, if replacement parts are hard to find and the valve is old, I would opt for a replacement to ensure long-term reliability.
If you were assigned to train a new technician on valve operations, what key points would you emphasize?
How to Answer
- 1
Start with the fundamental types of valves and their functions.
- 2
Explain key operational principles such as pressure regulation and flow control.
- 3
Highlight safety procedures and the importance of personal protective equipment.
- 4
Discuss the significance of routine maintenance and troubleshooting common issues.
- 5
Encourage hands-on practice to build familiarity with equipment.
Example Answers
I would emphasize the different types of valves like ball, gate, and globe valves and their specific uses. Understanding how each operates is crucial. Then, I would explain the principles of flow control, including how to adjust settings for optimal performance. Safety is paramount, so I’d stress using PPE and operation procedures. I’d also cover routine maintenance tasks and troubleshooting techniques. Lastly, I’d encourage new technicians to engage in practical exercises to reinforce their learning.
Don't Just Read Valve Technician Questions - Practice Answering Them!
Reading helps, but actual practice is what gets you hired. Our AI feedback system helps you improve your Valve Technician interview answers in real-time.
Personalized feedback
Unlimited practice
Used by hundreds of successful candidates
Valve Technician Position Details
Salary Information
Recommended Job Boards
These job boards are ranked by relevance for this position.
Related Positions
Ace Your Next Interview!
Practice with AI feedback & get hired faster
Personalized feedback
Used by hundreds of successful candidates
Ace Your Next Interview!
Practice with AI feedback & get hired faster
Personalized feedback
Used by hundreds of successful candidates