Top 28 Valve Mechanic Interview Questions and Answers [Updated 2025]
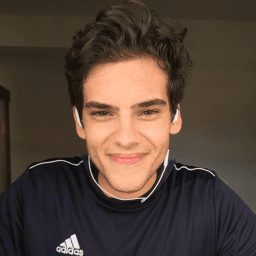
Andre Mendes
•
March 30, 2025
Preparing for a Valve Mechanic interview? Our latest blog post has you covered with the most common questions candidates face. Dive into expertly crafted example answers and essential tips to help you respond confidently and effectively. Whether you're a seasoned professional or new to the field, this guide will equip you with the insights needed to excel in your interview and secure the position.
Download Valve Mechanic Interview Questions in PDF
To make your preparation even more convenient, we've compiled all these top Valve Mechanicinterview questions and answers into a handy PDF.
Click the button below to download the PDF and have easy access to these essential questions anytime, anywhere:
List of Valve Mechanic Interview Questions
Behavioral Interview Questions
Describe a time when you had to work closely with a team to complete a valve installation. What role did you play?
How to Answer
- 1
Pick a specific project that involved teamwork.
- 2
Clearly define your role and contributions.
- 3
Mention any challenges faced and how the team overcame them.
- 4
Highlight the importance of communication and collaboration.
- 5
Conclude with the result of the installation and its impact.
Example Answers
In a recent project, our team was tasked with installing new valves at a facility. I was the lead technician responsible for overseeing the installation process. We encountered a delay due to incorrect valve sizes, but I communicated with the supplier and we quickly resolved the issue. The installation was completed on time and improved the system's efficiency by 20%.
Can you describe a time when you implemented a new technique or tool that improved valve maintenance efficiency?
How to Answer
- 1
Think of a specific situation where you introduced a new method.
- 2
Focus on the tool or technique you used and its benefits.
- 3
Mention quantifiable results, such as time saved or reduced failures.
- 4
Highlight collaboration with team members during implementation.
- 5
Explain how you assessed the impact after the change.
Example Answers
In my previous role, I introduced a digital valve monitoring tool that allowed us to track valve performance in real-time. This reduced our response time to valve issues by 30%, significantly increasing our maintenance efficiency.
Don't Just Read Valve Mechanic Questions - Practice Answering Them!
Reading helps, but actual practice is what gets you hired. Our AI feedback system helps you improve your Valve Mechanic interview answers in real-time.
Personalized feedback
Unlimited practice
Used by hundreds of successful candidates
Tell me about a time when you had to adapt to a major change in processes related to valve maintenance. How did you handle it?
How to Answer
- 1
Choose a specific example where a process changed significantly.
- 2
Describe the change clearly and its impact on your work.
- 3
Focus on how you adapted your skills and approach.
- 4
Highlight any collaboration with colleagues or management.
- 5
Conclude with positive outcomes or lessons learned.
Example Answers
In my previous job, our team switched to a new digital monitoring system for valve performance. I took the initiative to learn the system by attending training sessions and working closely with the IT department. This helped me quickly integrate the new process into our maintenance routines, leading to improved efficiency and faster response times to valve issues.
Have you ever trained someone in valve mechanics? How did you ensure they understood the complexities involved?
How to Answer
- 1
Share a specific example of a training experience.
- 2
Explain the methods used to simplify complex concepts.
- 3
Discuss any tools or resources utilized during training.
- 4
Mention the feedback mechanisms you implemented.
- 5
Highlight how you assessed their understanding throughout the process.
Example Answers
Yes, I trained a junior technician in valve mechanics. I used hands-on demonstrations with actual valves to illustrate concepts like pressure regulation. I also provided visual aids and guides to help simplify the technical details. Regular quizzes helped me assess their progress while they provided feedback on what they found confusing.
Describe a time when you dealt with a dissatisfied client regarding valve work you performed. How did you resolve the situation?
How to Answer
- 1
Acknowledge the client's feelings and concerns clearly.
- 2
Explain the specific valve issue that led to dissatisfaction.
- 3
Describe the steps you took to rectify the problem and improve the situation.
- 4
Highlight communication efforts with the client throughout the resolution process.
- 5
Conclude with the outcome and any lessons learned from the experience.
Example Answers
I once handled a situation where a client complained about a valve I serviced that was still leaking. I first listened to their concerns to ensure they felt heard. Then, I analyzed my work and realized I had missed a minor adjustment. I promptly scheduled a revisit, made the necessary corrections, and communicated openly with the client throughout the process. Ultimately, the valve worked perfectly, and the client thanked me for my quick response.
Can you provide an example of a challenging valve repair you faced? How did you approach resolving the issue?
How to Answer
- 1
Start with a clear description of the valve and the specific issue.
- 2
Explain the steps you took to diagnose the problem.
- 3
Discuss any challenges you faced during the repair process.
- 4
Highlight the tools and techniques you used.
- 5
Conclude with the outcome and what you learned from the experience.
Example Answers
In a recent project, I dealt with a leaking ball valve in a high-pressure system. I first isolated the valve and inspected for wear and damage. I found that the seals were compromised, so I replaced them using the correct specifications. The challenge was working in a tight space, but I adjusted my tools to fit. The valve functions perfectly now, and I learned the importance of precise measurement.
Tell me about a situation where you had to explain a technical problem with a valve to a non-technical person. How did you ensure they understood?
How to Answer
- 1
Use simple language and avoid jargon
- 2
Relate the technical problem to everyday experiences
- 3
Use analogies to clarify complex concepts
- 4
Check for understanding by asking questions
- 5
Be patient and ready to re-explain if necessary
Example Answers
In a previous role, I had to explain a valve malfunction to a project manager. I compared the valve's function to a faucet at home and used that analogy to explain how a blockage could prevent water flow. I asked if they understood and clarified any points they found confusing.
Give an example of a safety protocol you enforced while working with valves. What steps did you take?
How to Answer
- 1
Choose a specific safety protocol you know well
- 2
Describe the situation that required enforcing the protocol
- 3
Detail the steps you took to ensure safety
- 4
Highlight the outcome of those steps
- 5
Mention any feedback or improvements that resulted from your actions
Example Answers
In my previous job, I enforced a lockout-tagout procedure during valve maintenance. When we had to service a valve, I ensured all team members locked out the energy sources. We communicated our plans in a safety meeting and confirmed everyone was aware before starting work. As a result, there were no accidents during our maintenance period, and management praised our teamwork.
Have you ever led a project involving valve maintenance? What challenges did you overcome in your leadership role?
How to Answer
- 1
Start with a brief overview of the project scope and your role.
- 2
Highlight specific challenges and how you addressed them.
- 3
Emphasize teamwork and communication strategies used.
- 4
Discuss any tools or methods that facilitated the process.
- 5
Conclude with the outcome of the project and what you learned.
Example Answers
In my last role, I led a valve maintenance project for a large water treatment facility. One major challenge was coordinating with multiple teams on tight deadlines. I implemented a shared scheduling tool, which improved communication and helped us to stay on track. We completed the project ahead of schedule, and our maintenance efficiency increased by 15%.
Situational Interview Questions
If you noticed a flaw in a valve that was already installed, what steps would you take to address the issue?
How to Answer
- 1
Identify the nature and extent of the flaw immediately.
- 2
Assess the impact of the flaw on the system's operation.
- 3
Notify your supervisor or relevant team members about the issue.
- 4
Determine if it is safe to continue operation or if the valve should be shut down.
- 5
Plan for a repair or replacement, following standard maintenance procedures.
Example Answers
First, I would assess the flaw to understand its severity and impact on the system. Then, I would inform my supervisor about the issue to ensure we follow protocol. If there's a risk, I would recommend shutting the valve down and preparing for a repair.
Imagine you need a specific part for a valve repair that is out of stock. What alternatives would you consider?
How to Answer
- 1
Consider using a substitute part that meets the same specifications.
- 2
Explore local suppliers or distributors for availability.
- 3
Assess if the part can be repaired instead of replaced.
- 4
Check if you can borrow the part from another department or facility.
- 5
Review inventory for similar parts that could be modified to suit your needs.
Example Answers
I would first look for a substitute part with the same specifications. If I can't find one, I'd reach out to local suppliers to see if they have the part in stock.
Don't Just Read Valve Mechanic Questions - Practice Answering Them!
Reading helps, but actual practice is what gets you hired. Our AI feedback system helps you improve your Valve Mechanic interview answers in real-time.
Personalized feedback
Unlimited practice
Used by hundreds of successful candidates
You have just completed a valve installation and your supervisor asks for a detailed report. What information would you include?
How to Answer
- 1
Include specifications of the valve installed, such as type and size.
- 2
Document the installation process, highlighting any challenges encountered.
- 3
Record any tests conducted post-installation and their results.
- 4
Mention tools and materials used for the installation.
- 5
Note any maintenance recommendations or observations.
Example Answers
I would include the valve type, size, and specifications, detail the installation steps with any issues faced, and record the testing results showing the valve's functionality.
Suppose you are assigned to a team with varying levels of experience in valve mechanics. How would you ensure effective collaboration?
How to Answer
- 1
Encourage open communication for team members to share ideas.
- 2
Pair experienced members with less experienced ones for mentorship.
- 3
Set clear goals and roles for each team member to understand their contributions.
- 4
Use regular check-ins to assess progress and address any challenges together.
- 5
Foster a supportive environment where questions are welcomed and learning is prioritized.
Example Answers
I would facilitate open discussions to allow everyone to share their insights and raise concerns. By pairing senior mechanics with juniors, we can promote knowledge sharing and hands-on learning.
If you are unsure about the state of a valve and its safety, how would you approach the decision to use or replace it?
How to Answer
- 1
Inspect the valve for visible signs of wear or damage.
- 2
Consult maintenance logs and records for the valve's history.
- 3
Perform functional tests to assess if the valve operates correctly.
- 4
Evaluate the potential risks of using a faulty valve versus replacing it.
- 5
Involve a supervisor or experienced colleague for a second opinion.
Example Answers
First, I would visually inspect the valve for any signs of leaks or corrosion. Then, I would check its maintenance logs to see if there have been previous issues. After that, I would conduct functional tests to see if it opens and closes properly. If anything seems off, I would consult a supervisor before making a final decision.
You receive a last-minute job request for emergency valve repairs. How would you organize your time and resources?
How to Answer
- 1
Quickly assess the urgency and scope of the repair needed
- 2
Gather necessary tools and materials before heading to the job site
- 3
Communicate effectively with the team and the client about estimated time frames
- 4
Prioritize tasks based on safety and criticality of the repairs
- 5
Document the process for future reference and to improve efficiency
Example Answers
First, I would assess how urgent the valve repairs are and what specific tools are needed. Then, I would gather those tools and materials immediately, ensuring that I have everything before heading to the site. I would keep the client informed about when I expect to arrive and what the initial steps will be.
If you encountered a leaking valve in a critical system, what immediate actions would you take?
How to Answer
- 1
Assess the situation and determine the severity of the leak.
- 2
Shut down the system if necessary to prevent further damage.
- 3
Report the issue to a supervisor or relevant personnel immediately.
- 4
Implement temporary measures to contain the leak if safe to do so.
- 5
Prepare for repairs by gathering necessary tools and materials.
Example Answers
First, I would quickly assess the leak's severity. If it poses an immediate risk, I would shut down the system to prevent catastrophic failure. Next, I would inform my supervisor to ensure proper protocols are followed and prepare to contain the leak.
What would you do if a team member disagreed with your approach to a valve repair? How would you handle the situation?
How to Answer
- 1
Listen to their concerns without interrupting.
- 2
Ask clarifying questions to understand their perspective.
- 3
Present your reasoning and evidence for your approach.
- 4
Suggest a collaborative approach to find the best solution.
- 5
Remain open to compromise or a different viewpoint.
Example Answers
I would first listen to my team member's concerns. Then I'd ask questions to understand their viewpoint. After that, I'd explain my reasoning and the evidence backing my approach. If we still disagreed, I'd suggest we work together to explore both options and find a solution that works for the team.
You are behind schedule on a valve installation due to unforeseen issues. How would you prioritize your tasks to catch up?
How to Answer
- 1
Assess the critical tasks impacting project completion.
- 2
Identify any dependencies among tasks and address those first.
- 3
Communicate with your team about the priorities and any changes.
- 4
Allocate resources to the highest priority tasks for maximum impact.
- 5
Review progress frequently and adjust your plan as needed.
Example Answers
I would first evaluate which tasks are critical to the valve installation and which ones can be postponed. I'll focus on completing the tasks that directly affect the installation timeline, and communicate with my team to align our efforts. This way, we can maximize our productivity.
Technical Interview Questions
What routine maintenance practices do you follow to keep valves in optimal working condition?
How to Answer
- 1
Inspect valves regularly for leaks or signs of wear.
- 2
Lubricate moving parts according to manufacturer specifications.
- 3
Test valve operation frequently for proper opening and closing.
- 4
Clean valve bodies and sealing surfaces to prevent buildup.
- 5
Document all maintenance performed for future reference.
Example Answers
I regularly inspect valves for leaks and overall condition, lubricate moving parts per the manual, and ensure they operate smoothly through frequent testing.
What materials do you find are most effective for manufacturing or repairing valves, and why?
How to Answer
- 1
Identify common valve materials like stainless steel, brass, and PVC.
- 2
Explain the properties that make these materials suitable, such as corrosion resistance or strength.
- 3
Mention specific applications where each material excels.
- 4
Consider factors like compatibility with fluids being controlled.
- 5
Discuss maintenance and repair aspects related to material choice.
Example Answers
For manufacturing valves, I find stainless steel highly effective due to its corrosion resistance and strength, making it ideal for high-pressure applications. Brass is excellent for lower-pressure systems where durability and machinability are important, especially in water applications. PVC is great for chemical applications due to its resistance to corrosive substances.
Don't Just Read Valve Mechanic Questions - Practice Answering Them!
Reading helps, but actual practice is what gets you hired. Our AI feedback system helps you improve your Valve Mechanic interview answers in real-time.
Personalized feedback
Unlimited practice
Used by hundreds of successful candidates
What is the most common issue you encounter with valves, and how do you troubleshoot it?
How to Answer
- 1
Identify a specific common valve issue, such as leakage or sticking.
- 2
Explain the symptoms that indicate the issue.
- 3
Describe a systematic approach to troubleshooting the problem.
- 4
Mention any tools or techniques used in troubleshooting.
- 5
Conclude with how to prevent the issue from recurring.
Example Answers
One common issue I encounter is valve leakage. Symptoms include visible fluid leaks around the valve body. I troubleshoot by first checking the seals and gaskets for damage, then tightening screws or bolts as necessary. I use a torque wrench for proper tightening. To prevent leakage, I recommend regular maintenance checks and replacing worn seals.
How do you ensure that a new valve integrates seamlessly with existing systems?
How to Answer
- 1
Conduct thorough compatibility assessments with existing systems
- 2
Engage in detailed collaboration with engineering and design teams
- 3
Perform simulations or modeling to predict integration outcomes
- 4
Implement a phased testing approach to monitor integration
- 5
Document all integration processes for future reference
Example Answers
I ensure seamless integration by first assessing the compatibility of the new valve with existing systems, followed by collaborating closely with the engineering team to address any concerns. I also run simulations to forecast performance and execute phased testing for smooth deployment.
What are the different types of valves you have experience working with, and what are their specific applications?
How to Answer
- 1
List the types of valves you have worked with, such as gate, globe, check, ball, or butterfly.
- 2
Briefly describe a specific application for each type of valve mentioned.
- 3
Highlight any relevant projects or experiences that involved these valves.
- 4
Use clear and concise language to convey your expertise.
- 5
Conclude with your willingness to learn about other types of valves if needed.
Example Answers
I have experience with gate valves, which are used for on-off control in water supply systems. I worked on a project where we installed them in a municipal water treatment facility. I also have experience with ball valves, used in gas systems for fast shut-off, and check valves that prevent backflow in piping networks.
How do you diagnose a faulty valve? Please explain the steps you would take.
How to Answer
- 1
Begin with visual inspection for leaks or damage
- 2
Check valve operation by manually actuating it if possible
- 3
Use pressure gauges to assess the pressure upstream and downstream
- 4
Listen for unusual sounds during operation that might indicate a problem
- 5
Consult the system's documentation for specific diagnostic steps
Example Answers
I start with a visual inspection, looking for any obvious leaks or physical damage. If it seems fine, I manually operate the valve to ensure it opens and closes properly. Then, I check the pressure readings on either side of the valve to identify any discrepancies, and listen for any unusual sounds during operation.
What industry codes and standards do you follow when installing or repairing valves?
How to Answer
- 1
Research relevant industry standards such as ASME, API, and ISO.
- 2
Mention specific codes like ASME B16.34 or API 600 that relate to valve design and installation.
- 3
Explain how you ensure compliance with safety regulations and guidelines.
- 4
Discuss your experience with inspections and testing standards related to valves.
- 5
Highlight any certifications or training that relate to valve standards.
Example Answers
I follow ASME standards, particularly ASME B16.34 for valve design and API 600 for gate valves. I ensure that all repairs align with these codes to maintain safety and reliability.
What tools do you typically use when working on valves, and what are their specific purposes?
How to Answer
- 1
Identify the specific types of valves you work with.
- 2
List the primary tools you use with a brief explanation of each.
- 3
Highlight any unique or advanced tools you may have experience with.
- 4
Connect your tool usage to successful valve maintenance or repair examples.
- 5
Keep your answer focused and relevant to the Valve Mechanic role.
Example Answers
I regularly use a valve wrench for opening and closing valves, a torque wrench for ensuring proper tightness, and a pressure gauge to check for leaks. For testing valve functionality, I use a flow meter which helps me ensure everything operates within specifications.
What methods do you use to test and ensure the functionality of a valve after repair or installation?
How to Answer
- 1
Perform a visual inspection for any obvious defects or misalignments.
- 2
Conduct a pressure test to verify that there are no leaks in the valve.
- 3
Check the valve's operational movement manually to ensure it opens and closes smoothly.
- 4
Utilize testing equipment like a flow meter to assess the performance under operational conditions.
- 5
Document all tests and results to provide a thorough record of the functionality.
Example Answers
I start with a visual inspection to identify any misalignments. Then, I perform a pressure test to check for leaks, and ensure the valve operates smoothly by opening and closing it manually. Lastly, I document the results for future reference.
What software or diagnostic tools do you use for valve monitoring and analysis?
How to Answer
- 1
Identify specific software tools you have experience with.
- 2
Mention how these tools help in monitoring or diagnosing valve issues.
- 3
Highlight any relevant certifications or training with these tools.
- 4
Explain how you stay updated with new technologies in valve analysis.
- 5
Provide examples of successful outcomes using these tools.
Example Answers
I primarily use software like Fluke Connect for real-time monitoring and ValveLink for performance analysis. These tools help me diagnose valve performance issues quickly and accurately.
Don't Just Read Valve Mechanic Questions - Practice Answering Them!
Reading helps, but actual practice is what gets you hired. Our AI feedback system helps you improve your Valve Mechanic interview answers in real-time.
Personalized feedback
Unlimited practice
Used by hundreds of successful candidates
Valve Mechanic Position Details
Recommended Job Boards
CareerBuilder
www.careerbuilder.com/jobs-valve-technicianZipRecruiter
www.ziprecruiter.com/Jobs/Valve-TechnicianThese job boards are ranked by relevance for this position.
Related Positions
Ace Your Next Interview!
Practice with AI feedback & get hired faster
Personalized feedback
Used by hundreds of successful candidates
Ace Your Next Interview!
Practice with AI feedback & get hired faster
Personalized feedback
Used by hundreds of successful candidates