Top 29 Industrial Hygienist Interview Questions and Answers [Updated 2025]
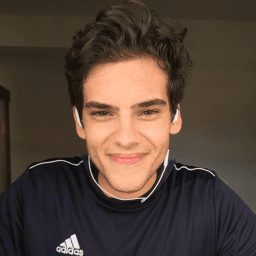
Andre Mendes
•
March 30, 2025
Preparing for an Industrial Hygienist interview can be daunting, but our blog post is here to help. Whether you're a seasoned professional or new to the field, we've compiled the most common questions asked in interviews for this role. With example answers and expert tips on how to respond effectively, you'll be well-equipped to impress potential employers and secure your next opportunity. Dive in to boost your confidence and readiness!
Download Industrial Hygienist Interview Questions in PDF
To make your preparation even more convenient, we've compiled all these top Industrial Hygienistinterview questions and answers into a handy PDF.
Click the button below to download the PDF and have easy access to these essential questions anytime, anywhere:
List of Industrial Hygienist Interview Questions
Behavioral Interview Questions
Can you describe a time when you collaborated with a team to identify and mitigate a workplace hazard?
How to Answer
- 1
Choose a specific hazard you encountered.
- 2
Highlight your role in the team and your contributions.
- 3
Describe the steps taken to identify the hazard.
- 4
Explain the solutions implemented and their effectiveness.
- 5
End with what you learned from the experience.
Example Answers
In my previous role, our team identified a high noise level in the manufacturing area. I organized a walk-through to measure noise levels and involved employees for their input. We implemented engineering controls by installing noise barriers, which resulted in decreased noise complaints. This taught me the importance of involving team members in hazard identification.
Tell me about a challenging project where you had to balance safety and production needs.
How to Answer
- 1
Identify a specific project with clear safety and production elements.
- 2
Explain the safety risks involved and production demands at that time.
- 3
Describe your approach to finding a solution that satisfied both sides.
- 4
Highlight the outcome and any metrics or results achieved.
- 5
Emphasize teamwork or collaboration if applicable.
Example Answers
In a previous role, I worked on a project where we needed to increase output by 20% while addressing noise exposure regulations. I coordinated with production teams to identify quieter machinery options and retrained staff on noise-reduction practices. Ultimately, we achieved a 25% increase in production while reducing noise levels by 15%.
Don't Just Read Industrial Hygienist Questions - Practice Answering Them!
Reading helps, but actual practice is what gets you hired. Our AI feedback system helps you improve your Industrial Hygienist interview answers in real-time.
Personalized feedback
Unlimited practice
Used by hundreds of successful candidates
Give an example of how you communicated risks to employees or management in your previous role.
How to Answer
- 1
Describe the risk clearly and specifically.
- 2
Identify the audience and tailor your communication style.
- 3
Use visual aids or examples to enhance understanding.
- 4
Emphasize the importance of the risk and potential impacts.
- 5
Encourage feedback or questions to ensure clarity.
Example Answers
In my previous role, I created a presentation highlighting the risks of chemical exposure. I tailored it for both management and floor employees, using graphs to illustrate exposure levels. I emphasized potential health impacts and invited questions to ensure everyone understood the risks.
Describe a situation where you had to adapt your strategies quickly in response to new information.
How to Answer
- 1
Think of a specific example from your work experience.
- 2
Clearly outline the new information that changed your approach.
- 3
Explain the original strategy and the immediate adjustment you made.
- 4
Highlight the outcome and what you learned from the experience.
- 5
Keep your explanation concise and focused on your adaptability.
Example Answers
In one project, we discovered high lead levels in the air during a routine assessment. I had to quickly shift from our planned monitoring protocol to implementing immediate engineering controls. This led to a significant reduction in exposure within days, and I learned the importance of remaining flexible under pressure.
Have you ever taken the lead on a safety initiative? What was the outcome?
How to Answer
- 1
Identify a specific safety initiative where you had a lead role.
- 2
Describe the goals of the initiative and your responsibilities.
- 3
Highlight any challenges faced and how you overcame them.
- 4
Quantify the outcomes, such as reduced incidents or improved compliance.
- 5
Emphasize teamwork and collaboration in achieving the results.
Example Answers
I led a safety initiative to improve air quality in our facility. The goal was to reduce exposure levels of VOCs. I organized training for staff and implemented new monitoring systems. As a result, we reduced VOC levels by 30% within six months and achieved compliance with new regulations.
Can you provide an example of a safety program you have improved and how you measured its success?
How to Answer
- 1
Identify a specific safety program you worked on.
- 2
Explain the changes you implemented to improve it.
- 3
Describe the metrics or methods used to measure success.
- 4
Highlight any positive outcomes or feedback received.
- 5
Mention any long-term changes or sustainability of the improvements.
Example Answers
At my previous job, I improved the chemical handling safety program by introducing better labeling and training procedures. We measured success through a reduction in chemical spills and incidents, which dropped by 30% over six months.
Describe a conflict you faced regarding workplace safety. How did you resolve it?
How to Answer
- 1
Identify the specific safety issue and stakeholders involved
- 2
Explain the differing perspectives clearly and objectively
- 3
Describe the steps you took to address the conflict
- 4
Highlight the resolution and its impact on workplace safety
- 5
Reflect on any lessons learned from the experience
Example Answers
In a previous role, our team disagreed on the need for additional PPE for a new project. I organized a meeting with safety officers and team leads to discuss data on potential hazards. We reviewed the risks together and agreed on implementing enhanced safety measures. This improved compliance and reduced incidents on site.
What was your most successful training session on occupational health and safety, and what made it successful?
How to Answer
- 1
Choose a specific training session that had a measurable impact.
- 2
Highlight the audience and their needs to show relevance.
- 3
Include engaging methods you used, like interactive activities.
- 4
Discuss feedback received and changes made based on it.
- 5
Mention any follow-up actions or changes in behavior post-training.
Example Answers
In a training session for construction workers, I used hands-on demonstrations with safety equipment. The participants were more engaged and able to ask questions. Post-training, I received a 90% satisfaction rate, and I noticed a decrease in safety incidents on-site.
Technical Interview Questions
What federal regulations and standards do you think are most critical for an Industrial Hygienist?
How to Answer
- 1
Identify key regulations such as OSHA standards and NIOSH recommendations.
- 2
Discuss specific regulations relevant to your industry or job role.
- 3
Mention the importance of compliance for worker safety and health.
- 4
Explain how regulations impact assessment and control measures.
- 5
Be prepared to give examples of how you’ve implemented these standards.
Example Answers
I believe OSHA standards, particularly those addressing hazardous chemicals under the Hazard Communication Standard, are critical. They ensure workplaces are safe by requiring proper labeling and safety data sheets.
Explain how you would conduct a risk assessment in a manufacturing facility.
How to Answer
- 1
Identify potential hazards through a walkthrough of the facility.
- 2
Engage employees to gather insights on safety concerns.
- 3
Evaluate the likelihood and severity of identified risks.
- 4
Document findings and prioritize risks based on exposure level.
- 5
Recommend mitigation strategies and follow up on their implementation.
Example Answers
I would start by conducting a thorough walkthrough of the manufacturing facility to spot potential hazards. Engaging with employees is crucial, as they can provide valuable insights. I would assess each risk by determining how likely it is to occur and the potential severity. Finally, I'd document the risks and propose strategies to mitigate them and ensure their implementation is monitored.
Don't Just Read Industrial Hygienist Questions - Practice Answering Them!
Reading helps, but actual practice is what gets you hired. Our AI feedback system helps you improve your Industrial Hygienist interview answers in real-time.
Personalized feedback
Unlimited practice
Used by hundreds of successful candidates
What methods do you use to monitor exposure levels to hazardous substances?
How to Answer
- 1
Discuss specific monitoring techniques like air sampling and personal monitoring devices
- 2
Mention any relevant tools or equipment you are experienced with
- 3
Include the importance of using both qualitative and quantitative methods
- 4
Highlight any regulatory standards you follow during monitoring
- 5
Explain how you analyze and interpret the data collected
Example Answers
I regularly utilize personal monitoring devices and air sampling pumps to measure exposure levels. I've worked with real-time dust monitors to ensure compliance with OSHA standards, and I analyze the data to identify trends and necessary interventions.
What engineering controls have you recommended in the past, and what was the rationale behind your recommendations?
How to Answer
- 1
Identify specific engineering controls you've implemented.
- 2
Explain the hazards they were designed to mitigate.
- 3
Describe the expected outcomes of your recommendations.
- 4
Mention any measurements or data used to support your decisions.
- 5
Highlight collaboration with other teams to implement solutions.
Example Answers
I recommended the installation of a local exhaust ventilation system to control airborne contaminants in a manufacturing plant. This was to reduce worker exposure to harmful fumes, as previous monitoring showed levels exceeded permissible limits.
How do you analyze data from air monitoring equipment, and what tools do you use?
How to Answer
- 1
Describe the specific equipment you use for air monitoring.
- 2
Explain your systematic approach to data collection and analysis.
- 3
Mention software tools or statistical methods you employ.
- 4
Discuss how you interpret the results to assess compliance with standards.
- 5
Highlight how you communicate findings to stakeholders.
Example Answers
I use real-time air monitors like PID sensors to collect data on VOC levels. I analyze the data using software like Excel for initial calculations and then employ statistical tools like R for detailed analysis. I ensure the results align with OSHA standards and present my findings in clear reports for management.
What is the significance of understanding chemical properties in industrial hygiene?
How to Answer
- 1
Identify key chemical properties relevant to safety, such as toxicity and volatility.
- 2
Discuss how these properties influence exposure limits and control measures.
- 3
Explain the role of Material Safety Data Sheets (MSDS) in understanding chemical risks.
- 4
Highlight how understanding chemical behavior aids in incident prevention.
- 5
Mention the importance of proper labeling and storage based on chemical properties.
Example Answers
Understanding chemical properties like toxicity and volatility is crucial because it helps us establish exposure limits and implement appropriate control measures. By knowing how a substance behaves under certain conditions, we can better protect workers and prevent potential incidents.
What process do you follow for identifying potential chemical hazards in a new workplace?
How to Answer
- 1
Conduct a thorough walkthrough of the facility to observe processes and materials used
- 2
Review Safety Data Sheets (SDS) for all chemicals present in the workplace
- 3
Engage with employees to understand their tasks and any concerns they may have about chemical exposure
- 4
Utilize assessment tools like hazard checklists and chemical inventories for systematic evaluation
- 5
Document findings and prioritize hazards based on potential risk to health and safety
Example Answers
First, I conduct a walkthrough of the facility to understand the processes and materials involved. Then, I review the Safety Data Sheets for all chemicals in use, talking to employees about their experiences and concerns. This helps me document potential hazards and assess them systematically using a hazard checklist.
What factors do you consider when selecting personal protective equipment for employees?
How to Answer
- 1
Identify the specific hazards present in the work environment.
- 2
Evaluate the level of exposure risk associated with each hazard.
- 3
Consider the comfort and fit of the equipment for long-term use.
- 4
Ensure compliance with relevant safety regulations and standards.
- 5
Involve employees in the selection process for feedback on usability.
Example Answers
I assess the hazards in the environment and evaluate the risks of exposure. Then, I choose PPE that meets safety standards while also ensuring it is comfortable for employees to wear during their tasks.
What techniques do you use to assess noise exposure in the workplace?
How to Answer
- 1
Discuss using sound level meters for initial measurements
- 2
Mention dosimetry for personal noise exposure over time
- 3
Include techniques like area noise mapping for identifying hotspots
- 4
Talk about comparing results to OSHA and NIOSH standards
- 5
Emphasize the importance of employee interviews for qualitative data
Example Answers
I utilize sound level meters to get baseline noise measurements in different areas. For personal exposure, I often deploy dosimeters that employees wear throughout their shifts to get accurate data.
Can you explain the difference between permissible exposure limits (PELs) and threshold limit values (TLVs)?
How to Answer
- 1
Define PELs as legally enforceable limits set by OSHA.
- 2
Define TLVs as guidelines developed by ACGIH, not legally binding.
- 3
Explain that PELs are often based on an 8-hour workday.
- 4
Mention that TLVs can use different time-weighted averages, including shorter durations.
- 5
Highlight that PELs are for specific substances, while TLVs may include more comprehensive health effects.
Example Answers
PELs are legally enforceable limits established by OSHA to protect workers, while TLVs are recommended guidelines from ACGIH that are not legally binding. PELs usually apply over an 8-hour workday, whereas TLVs might include various time frames.
Don't Just Read Industrial Hygienist Questions - Practice Answering Them!
Reading helps, but actual practice is what gets you hired. Our AI feedback system helps you improve your Industrial Hygienist interview answers in real-time.
Personalized feedback
Unlimited practice
Used by hundreds of successful candidates
What industrial processes do you find most challenging in terms of regulatory compliance?
How to Answer
- 1
Identify specific processes you have experience with
- 2
Link challenges to specific regulations they involve
- 3
Discuss the impact of these challenges on health and safety
- 4
Suggest potential solutions or improvements you've considered
- 5
Show awareness of evolving regulations in the industry
Example Answers
I find chemical manufacturing processes challenging due to strict OSHA and EPA regulations. These processes require constant monitoring to ensure compliance with exposure limits. For example, managing VOCs involves ongoing checks that can be resource-intensive, but implementing better ventilation systems could alleviate some issues.
Situational Interview Questions
If you discovered hazardous material in a workplace, how would you prioritize your actions?
How to Answer
- 1
Identify the type and extent of the hazardous material quickly
- 2
Ensure the safety of all personnel by evacuating the area if needed
- 3
Notify appropriate authorities and stakeholders immediately
- 4
Implement containment measures to prevent further exposure
- 5
Document the incident and your actions for follow-up and compliance
Example Answers
First, I would quickly assess the type and quantity of the hazardous material. Then, I would ensure everyone in the vicinity is evacuated for safety. I would notify emergency services and management to handle the situation. I would set up barriers to contain the material and finally document every step taken for future review.
What steps would you take if an employee was exposed to a hazardous substance?
How to Answer
- 1
Immediately assess the situation and ensure the employee is safe.
- 2
Provide first aid or emergency care based on the nature of the exposure.
- 3
Report the incident to the appropriate supervisors and safety personnel.
- 4
Document the exposure details and the actions taken.
- 5
Follow up with medical evaluation for the affected employee.
Example Answers
First, I would ensure the employee is moved to a safe area away from the hazard. Then, I would provide necessary first aid and ensure they receive medical evaluation. Next, I would report the exposure to supervisors and document everything that happened.
Don't Just Read Industrial Hygienist Questions - Practice Answering Them!
Reading helps, but actual practice is what gets you hired. Our AI feedback system helps you improve your Industrial Hygienist interview answers in real-time.
Personalized feedback
Unlimited practice
Used by hundreds of successful candidates
How would you train employees on safe handling of chemicals in the workplace?
How to Answer
- 1
Assess the specific chemicals used in the workplace and their hazards
- 2
Develop a tailored training program that includes the proper handling, storage, and disposal procedures
- 3
Incorporate hands-on demonstrations to show safe practices
- 4
Schedule regular refresher courses to ensure ongoing compliance and awareness
- 5
Utilize visual aids like Safety Data Sheets (SDS) and posters to reinforce key guidelines
Example Answers
I would start by identifying the chemicals in use and conducting a risk assessment. Then, I would create a training program covering the safe handling, storage, and disposal of these substances. Hands-on demonstrations would help employees practice these safety procedures effectively.
How would you handle being pressured by management to bypass certain safety protocols?
How to Answer
- 1
Stay calm and professional during the conversation
- 2
Emphasize the importance of safety protocols for employee health
- 3
Offer alternative solutions that meet both safety and management goals
- 4
Document the conversation for future reference if needed
- 5
Be prepared to escalate the issue if safety is at risk
Example Answers
I would calmly explain to management that safety protocols are in place to protect employees and ensure compliance with regulations. I would suggest alternative methods to achieve management's goals without compromising safety.
How would you work with other departments to improve workplace safety?
How to Answer
- 1
Establish regular communication channels with each department
- 2
Conduct joint safety training sessions to create a unified approach
- 3
Encourage departments to share their specific safety concerns and suggestions
- 4
Implement cross-departmental safety committees for collaborative oversight
- 5
Use data from all departments to tailor safety improvements
Example Answers
I would set up regular meetings with department heads to discuss safety issues and progress. By facilitating joint training sessions, we would ensure everyone understands the importance of safety across our operations.
How would you approach communicating potential risks from a new operation to the workforce?
How to Answer
- 1
Identify the specific risks associated with the new operation before communicating.
- 2
Use clear and simple language to ensure understanding across all levels of the workforce.
- 3
Incorporate visual aids or examples to make the information more relatable.
- 4
Encourage open dialogue and provide a platform for workers to ask questions.
- 5
Offer ongoing training sessions to reinforce safety practices related to the new operation.
Example Answers
I would start by identifying the specific risks of the operation and prepare an easy-to-understand presentation. Using visuals, I'd explain the risks and ensure everyone has a chance to ask questions, fostering an open dialogue about safety.
How would you manage a project where the deadline conflicts with necessary safety assessments?
How to Answer
- 1
Prioritize safety assessments by evaluating their importance to project success.
- 2
Communicate with stakeholders about safety risks related to the timeline.
- 3
Explore options for accelerating assessments without compromising integrity.
- 4
Document any compromises or risks for transparency and future reference.
- 5
Develop a contingency plan that addresses potential safety issues arising from deadline pressure.
Example Answers
I would assess the critical safety assessments needed and communicate to stakeholders about the importance of these evaluations. If possible, I’d work to expedite the safety assessments while ensuring compliance. I would keep documentation of any trade-offs made.
How would you engage and gain support from stakeholders who are resistant to safety changes?
How to Answer
- 1
Listen to stakeholders' concerns and validate their feelings about the changes
- 2
Present data and case studies showing the benefits of the changes
- 3
Involve stakeholders in the planning process to foster ownership
- 4
Provide clear, practical examples of how changes improve their work environment
- 5
Offer training sessions to ease the transition and address questions directly
Example Answers
I would start by listening to their concerns, ensuring they feel heard. Then, I'd share relevant data showing how similar changes led to positive outcomes in other organizations. Involving them in the planning process could help them take ownership of the changes.
Industrial Hygienist Position Details
Salary Information
Recommended Job Boards
BCSP Career Center
jobs.bcsp.org/q-industrial-hygienist-jobs.htmlThese job boards are ranked by relevance for this position.
Related Positions
Ace Your Next Interview!
Practice with AI feedback & get hired faster
Personalized feedback
Used by hundreds of successful candidates
Ace Your Next Interview!
Practice with AI feedback & get hired faster
Personalized feedback
Used by hundreds of successful candidates