Top 30 Industrial Safety Engineer Interview Questions and Answers [Updated 2025]
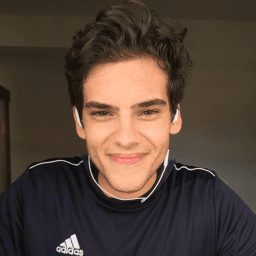
Andre Mendes
•
March 30, 2025
Navigating the competitive landscape of industrial safety engineering interviews can be daunting. In this blog post, we delve into the most common interview questions faced in the 'Industrial Safety Engineer' role. Equipped with example answers and insightful tips, you'll gain the confidence to articulate your expertise effectively and make a lasting impression. Prepare to enhance your interview readiness and secure your next opportunity!
Download Industrial Safety Engineer Interview Questions in PDF
To make your preparation even more convenient, we've compiled all these top Industrial Safety Engineerinterview questions and answers into a handy PDF.
Click the button below to download the PDF and have easy access to these essential questions anytime, anywhere:
List of Industrial Safety Engineer Interview Questions
Behavioral Interview Questions
Describe a situation where you had to communicate a safety concern to upper management. How did you approach it?
How to Answer
- 1
Identify a specific safety issue you encountered.
- 2
Explain how you gathered data or evidence to support your concern.
- 3
Choose an appropriate time to address upper management.
- 4
Present your findings clearly and concisely.
- 5
Propose actionable solutions or recommendations.
Example Answers
In a previous role, I noticed that our machinery lacked proper safety guards. I documented incidents and near misses over a month and created a report. During a management meeting, I brought this up, presented the data clearly, and suggested installing guards to prevent accidents.
Can you describe a time when you successfully worked with a team to implement a new safety protocol in an industrial setting?
How to Answer
- 1
Select a specific project or protocol that you worked on.
- 2
Highlight your role and contributions within the team.
- 3
Explain the challenges faced during implementation and how you resolved them.
- 4
Share the positive outcomes or metrics that resulted from the new protocol.
- 5
Conclude with lessons learned or how it improved safety culture.
Example Answers
In my last job, our team implemented a new lockout/tagout procedure to enhance machine safety. I led the training sessions and collaborated with operators to gather feedback. The main challenge was resistance to change, but by addressing concerns in meetings, we built trust. After implementation, we reduced machine-related incidents by 30%. This experience taught me the importance of communication in safety initiatives.
Don't Just Read Industrial Safety Engineer Questions - Practice Answering Them!
Reading helps, but actual practice is what gets you hired. Our AI feedback system helps you improve your Industrial Safety Engineer interview answers in real-time.
Personalized feedback
Unlimited practice
Used by hundreds of successful candidates
Tell me about a complex safety issue you identified and how you resolved it.
How to Answer
- 1
Choose a specific safety issue relevant to your field
- 2
Explain the context and complexity clearly
- 3
Describe the steps you took to analyze and resolve it
- 4
Emphasize the outcome and any improvements made
- 5
Keep your answer concise and focused
Example Answers
In a manufacturing plant, I identified that equipment maintenance records weren't being tracked properly, leading to increased accidents. I implemented a new maintenance tracking system that ensured regular inspections. After six months, incidents decreased by 40%.
Have you ever led a team in a safety audit? What was the outcome, and how did you manage the process?
How to Answer
- 1
Start with a brief overview of the audit objective
- 2
Explain your role and responsibilities in leading the team
- 3
Describe the process you followed, including planning and execution
- 4
Highlight the key findings and outcomes from the audit
- 5
Reflect on what you learned and how it improved safety measures
Example Answers
In my last role, I led a team for a safety audit aimed at identifying hazards in our manufacturing plant. I organized the audit process, scheduled meetings, and assigned roles. We uncovered several critical safety issues, which led to the implementation of new safety protocols. As a result, we reduced incident reports by 30% over the next quarter.
Give an example of a safety improvement initiative you proposed and implemented. What challenges did you face?
How to Answer
- 1
Select a specific initiative you led or contributed to.
- 2
Outline the problem that necessitated the initiative.
- 3
Explain the steps you took to implement the initiative.
- 4
Discuss challenges such as resistance, budget constraints, or technical difficulties.
- 5
Conclude with the results and impacts of your initiative.
Example Answers
In my previous role, I noticed that our warehouse had high incident rates due to improper lifting techniques. I proposed a comprehensive training program that included hands-on demonstrations. The main challenge was getting management buy-in, as they were concerned about the costs. I created a cost-benefit analysis showing potential savings from fewer injuries. After implementation, we reduced incidents by 40% within six months.
Technical Interview Questions
What are the key OSHA regulations that apply to industrial safety, and how do they influence your safety programs?
How to Answer
- 1
Identify key OSHA regulations relevant to your industry, such as General Duty Clause, and specific standards like PPE, Hazard Communication.
- 2
Explain how these regulations shape your safety policies and training programs.
- 3
Discuss your experience implementing these regulations in past roles and their impact on workplace safety.
- 4
Emphasize continuous compliance and regular audits to ensure safety standards are met.
- 5
Highlight the importance of fostering a safety culture that aligns with OSHA standards.
Example Answers
Key OSHA regulations like the General Duty Clause and the standards for Personal Protective Equipment significantly guide my safety programs. For instance, I ensure all employees are trained on PPE usage in line with OSHA requirements, which has reduced incidents by 30% at my previous job.
How do you conduct a risk assessment for a new piece of industrial equipment?
How to Answer
- 1
Identify the equipment and its intended use
- 2
Gather data on potential hazards associated with the equipment
- 3
Assess the likelihood and severity of each hazard
- 4
Determine existing controls and their effectiveness
- 5
Recommend additional safety measures as needed
Example Answers
First, I identify the equipment and understand its intended function. Then, I research potential hazards like mechanical, electrical, and ergonomic risks. I assess each hazard by looking at its likelihood of occurrence and potential impact. Next, I review current safety protocols and suggest improvements based on the findings.
Don't Just Read Industrial Safety Engineer Questions - Practice Answering Them!
Reading helps, but actual practice is what gets you hired. Our AI feedback system helps you improve your Industrial Safety Engineer interview answers in real-time.
Personalized feedback
Unlimited practice
Used by hundreds of successful candidates
Describe the process you follow to identify and evaluate potential hazards in a manufacturing plant.
How to Answer
- 1
Begin with a safety audit of the facility to identify obvious hazards.
- 2
Engage with workers to gather insights on daily safety concerns.
- 3
Utilize risk assessment tools like HAZOP or FMEA to evaluate potential risks.
- 4
Prioritize hazards based on likelihood and severity of impact.
- 5
Document findings and develop mitigation strategies for identified hazards.
Example Answers
I start by conducting a comprehensive safety audit to spot obvious hazards. I also talk to employees to understand practical issues they face. After identifying risks, I use the HAZOP method to analyze potential hazards and prioritize them by severity. Finally, I document everything and create strategies to mitigate the risks.
What are the main components of a safety audit, and how do you ensure its effectiveness?
How to Answer
- 1
Identify key components like planning, data collection, analysis, reporting, and follow-up actions.
- 2
Explain how to involve employees during audits for better compliance and insights.
- 3
Use specific metrics and standards to measure safety performance.
- 4
Emphasize regularity and continuous improvement in the audit process.
- 5
Highlight the importance of management commitment to implementing audit findings.
Example Answers
A safety audit consists of planning, data collection, analysis, reporting, and follow-up. To ensure its effectiveness, I actively involve employees for their input and adherence, use clear metrics to gauge performance, conduct audits regularly, and focus on continuous improvements based on management's commitment.
What steps do you take when conducting an incident investigation?
How to Answer
- 1
Define the scope of the investigation immediately after the incident occurs.
- 2
Gather all relevant facts through interviews and reviews of documents.
- 3
Analyze the data to identify root causes using methods like the 5 Whys or Fishbone Diagram.
- 4
Document findings clearly and outline recommended corrective actions.
- 5
Communicate results to stakeholders and track the implementation of corrective measures.
Example Answers
First, I define the scope of the investigation and ensure all evidence is preserved. Then, I gather relevant facts through interviews and document reviews. I analyze the data for root causes, typically using the 5 Whys technique. Finally, I document my findings along with corrective actions and communicate these to the relevant stakeholders.
What factors do you consider critical when developing an emergency response plan for an industrial facility?
How to Answer
- 1
Identify the specific hazards present in the facility
- 2
Ensure clear roles and responsibilities for emergency personnel
- 3
Incorporate training and drills for all employees
- 4
Establish communication protocols for emergencies
- 5
Develop evacuation routes and safe zones
Example Answers
I consider the specific hazards, like chemicals and machinery risks, to identify what emergencies could occur. Clear roles for responders and regular employee training are also essential.
How do you determine the appropriate personal protective equipment (PPE) for different tasks in an industrial setting?
How to Answer
- 1
Identify hazards associated with each task
- 2
Consult safety data sheets for materials involved
- 3
Assess the risk levels for potential exposures
- 4
Involve workers in discussions about PPE effectiveness
- 5
Regularly review and update PPE guidelines based on new regulations or incidents
Example Answers
I begin by identifying the specific hazards present for the task at hand, such as chemical exposure or machinery risks. Then I reference safety data sheets to ensure I select the correct PPE that meets the necessary protection levels. I also involve the team to discuss the PPE's comfort and effectiveness during their work.
Describe the key elements of an effective industrial safety training program.
How to Answer
- 1
Identify clear training objectives that align with safety regulations and company policies
- 2
Incorporate hands-on training and simulations to enhance practical understanding
- 3
Regularly assess trainee knowledge through quizzes or practical evaluations
- 4
Provide ongoing training and updates to address new safety protocols or equipment
- 5
Gather feedback from participants to continuously improve the training program
Example Answers
An effective industrial safety training program includes clear training objectives based on current regulations, practical hands-on training, regular assessments, ongoing updates for new protocols, and participant feedback for continuous improvement.
How do you use data analysis to improve workplace safety measures?
How to Answer
- 1
Identify the types of data relevant to safety, such as incident reports and near misses
- 2
Explain how you analyze trends over time to spot safety issues
- 3
Discuss using data to prioritize safety initiatives based on risk assessment
- 4
Mention the importance of involving staff in data collection to improve accuracy
- 5
Share how data informs training programs and policy updates
Example Answers
I analyze historical incident data to identify the most common types of accidents. By tracking these trends, I can focus on high-risk areas and implement targeted safety measures, which have proven to reduce incidents by 20%.
Explain how ergonomics can be applied to improve safety in industrial workplaces.
How to Answer
- 1
Start by defining ergonomics and its relevance in the workplace.
- 2
Mention specific ergonomic assessments or tools that can be used.
- 3
Provide examples of ergonomic improvements like tool design or workstation setup.
- 4
Discuss the benefits of ergonomics, such as reducing injuries and increasing productivity.
- 5
Conclude by highlighting the importance of continuous ergonomic training for employees.
Example Answers
Ergonomics focuses on designing work environments that fit the worker. Using tools like workstation assessments, we can identify hazards like repetitive strain injuries. For instance, providing adjustable chairs and proper tool grips improves posture and reduces fatigue, leading to fewer injuries and higher productivity.
Don't Just Read Industrial Safety Engineer Questions - Practice Answering Them!
Reading helps, but actual practice is what gets you hired. Our AI feedback system helps you improve your Industrial Safety Engineer interview answers in real-time.
Personalized feedback
Unlimited practice
Used by hundreds of successful candidates
Situational Interview Questions
Imagine a minor safety incident occurred at the plant. How would you handle the situation from start to finish?
How to Answer
- 1
Immediately ensure the safety of all personnel involved.
- 2
Assess the situation and document the details of the incident.
- 3
Notify relevant management and safety teams about the incident.
- 4
Investigate the cause of the incident and identify any risks.
- 5
Implement corrective actions and improve safety protocols to prevent reoccurrence.
Example Answers
First, I would ensure that everyone is safe and that there are no injuries. Then, I would document what happened and notify my supervisor. After that, I would investigate the root cause and collaborate with the safety team to improve our protocols.
A worker is refusing to follow a safety protocol due to perceived inefficiencies. How would you address this?
How to Answer
- 1
Listen to the worker's concerns without interrupting.
- 2
Acknowledge their feelings but emphasize the importance of safety.
- 3
Provide evidence or examples of why the protocol is necessary.
- 4
Suggest a discussion to explore possible improvements to the protocol.
- 5
Follow up with a plan to address both safety and efficiency.
Example Answers
I would first listen to the worker's concerns about the safety protocol. Once I understand their point of view, I would explain why the protocol is crucial for their safety and the safety of others. Then, I would invite them to a discussion where we can consider ways to improve the protocol without compromising safety.
Don't Just Read Industrial Safety Engineer Questions - Practice Answering Them!
Reading helps, but actual practice is what gets you hired. Our AI feedback system helps you improve your Industrial Safety Engineer interview answers in real-time.
Personalized feedback
Unlimited practice
Used by hundreds of successful candidates
If there was a chemical spill in the facility, what would be your immediate steps to handle it?
How to Answer
- 1
Assess the situation and identify the type of chemical involved
- 2
Ensure personal safety and secure the area to prevent further exposure
- 3
Activate emergency response protocols and alert designated personnel
- 4
Contain the spill if safe to do so, using appropriate materials
- 5
Follow up with proper reporting and documentation procedures
Example Answers
First, I would assess the situation to identify the chemical and determine the risks involved. Then, I would ensure that all personnel are safe and evacuate the area if necessary. Next, I would activate our emergency response plan and inform the safety team. If it's safe, I would use spill containment materials to limit the spread of the chemical. Finally, I would document the incident as per our procedures.
During an external safety audit, a major compliance issue is discovered. How would you manage the situation?
How to Answer
- 1
Acknowledge the issue immediately and express commitment to resolve it.
- 2
Gather a team to investigate the root cause of the compliance issue.
- 3
Develop an action plan with clear steps to address the issue.
- 4
Communicate transparently with stakeholders about the findings and actions taken.
- 5
Establish a follow-up process to ensure compliance and prevent future issues.
Example Answers
I would first acknowledge the compliance issue and ensure the external auditors that we take it seriously. Next, I'd form a team to identify the root cause and outline an action plan. Communication with all stakeholders would be paramount, and I would schedule follow-up audits to confirm compliance.
You have a limited budget to upgrade safety equipment. How would you prioritize the spending?
How to Answer
- 1
Assess the current safety equipment and identify the most critical gaps.
- 2
Prioritize upgrades that mitigate the highest risks to employees.
- 3
Consider compliance with safety regulations and prioritize those areas first.
- 4
Engage with employees to gather input on their safety concerns and needs.
- 5
Evaluate potential ROI of the equipment in terms of injury prevention and cost savings.
Example Answers
I would start by conducting a thorough assessment of our current safety equipment to identify critical gaps. Then, I'd prioritize upgrades that address the highest risks, especially those that are in violation of safety regulations. Additionally, I'd get feedback from employees on their safety concerns to ensure their needs are met.
You identify a safety risk in a well-established process. What steps would you take to mitigate the risk without disrupting production?
How to Answer
- 1
Assess the level of the risk and its potential impacts on safety.
- 2
Engage with relevant stakeholders to discuss the identified risk.
- 3
Develop a plan to implement changes during off-peak hours.
- 4
Provide training to employees about any new procedures or equipment.
- 5
Monitor the effectiveness of the implemented changes closely.
Example Answers
First, I would evaluate the severity of the safety risk and determine how it affects employees. Then, I would hold a meeting with production managers and safety officers to discuss the issue and gather input. After that, I’d propose mitigations that could be implemented during scheduled maintenance hours to minimize disruption.
A new regulation requires changes in safety procedures. How would you implement these changes effectively?
How to Answer
- 1
Review the new regulation thoroughly to understand all requirements
- 2
Engage with stakeholders to gather input and support for changes
- 3
Develop a clear plan that outlines steps, timelines, and responsibilities
- 4
Provide training to all affected employees to ensure compliance
- 5
Monitor the implementation and adjust strategies as necessary
Example Answers
I would start by carefully reviewing the new regulation to ensure all aspects are understood. I would then meet with relevant stakeholders to discuss the changes and gain their support. After that, I would create a step-by-step implementation plan with specific timelines and responsibilities. Training sessions would be organized for the employees to familiarize them with the new procedures. Finally, I would monitor the implementation closely and make adjustments if needed.
You notice safety training effectiveness is declining. What actions would you take to address this issue?
How to Answer
- 1
Conduct a survey to gather feedback from employees on current training methods
- 2
Analyze incident reports to identify specific areas where training is lacking
- 3
Update training materials to include real-life scenarios and hands-on experiences
- 4
Implement regular retraining sessions and refreshers based on employee feedback
- 5
Monitor training outcomes through follow-up assessments and performance metrics
Example Answers
First, I would survey employees to understand their perceptions of the training. Then, I would analyze incident reports to see where gaps in knowledge exist. Finally, I would revise the training program to include practical exercises and schedule regular refresher sessions.
If you receive data suggesting an increase in near-misses, what proactive measures would you implement?
How to Answer
- 1
Analyze the near-miss data to identify trends and common factors
- 2
Conduct team meetings to discuss safety concerns and promote open communication
- 3
Implement safety training sessions focusing on identified issues
- 4
Enhance reporting and feedback systems for near-miss incidents
- 5
Regularly review and update safety protocols based on findings
Example Answers
I would start by analyzing the data to determine if there are specific patterns, then organize safety meetings to encourage discussion. Based on that, I'd ensure targeted training is provided to address identified risks.
How would you foster a culture of safety in a reluctant work environment?
How to Answer
- 1
Start by conducting a safety assessment to identify specific issues.
- 2
Engage employees by soliciting their input on safety improvements.
- 3
Implement regular training sessions that emphasize the importance of safety.
- 4
Provide recognition and rewards for safe behavior to motivate others.
- 5
Lead by example and consistently demonstrate safe practices in your own work.
Example Answers
I would begin by assessing the current safety situation to pinpoint challenges. Then, I would involve employees in safety discussions and training programs to get their buy-in. Recognizing their contributions to safety practices would help shift the culture over time.
Don't Just Read Industrial Safety Engineer Questions - Practice Answering Them!
Reading helps, but actual practice is what gets you hired. Our AI feedback system helps you improve your Industrial Safety Engineer interview answers in real-time.
Personalized feedback
Unlimited practice
Used by hundreds of successful candidates
You need to collaborate with engineering on a safety-related project. How would you ensure productive cooperation?
How to Answer
- 1
Establish clear communication channels from the start.
- 2
Involve engineering in the safety planning process early.
- 3
Set common goals that align safety and engineering objectives.
- 4
Hold regular check-in meetings to discuss progress and challenges.
- 5
Be open to feedback and encourage mutual respect between teams.
Example Answers
I would start by setting up regular meetings with the engineering team to discuss the project scope and safety requirements. Establishing clear communication channels would help us address issues promptly and collaboratively.
A new safety technology is available. How would you evaluate its potential benefits and implementation in the workplace?
How to Answer
- 1
Identify the specific safety issues the technology addresses
- 2
Assess the cost-effectiveness and return on investment
- 3
Conduct a risk assessment and regulatory compliance check
- 4
Engage with employees and gather feedback on usability
- 5
Plan a pilot program to test the technology before full implementation
Example Answers
I would first look at the safety issues it solves, like reducing accidents in high-risk areas. Then, I'd calculate the cost and potential savings from fewer injuries. Next, I'd ensure it meets safety regulations and ask employees for their thoughts on it. Finally, I would run a small pilot to see how it performs in practice.
How would you establish a continuous improvement program for safety standards?
How to Answer
- 1
Identify existing safety standards and regulations to benchmark against.
- 2
Engage employees at all levels to gather insights and suggestions.
- 3
Implement regular training sessions to keep safety knowledge current.
- 4
Establish metrics to measure safety performance and compliance.
- 5
Review and update safety procedures based on feedback and performance data.
Example Answers
To establish a continuous improvement program for safety standards, I would start by benchmarking our current practices against industry standards. Then, I would involve employees by creating safety committees to solicit their input. Regular training sessions would be scheduled to ensure everyone is up to date on safety protocols, and I would track our safety performance through clear metrics. Finally, I would continually review our processes using this data to make informed updates.
Workers have provided feedback on safety concerns. How would you incorporate their feedback into your safety strategy?
How to Answer
- 1
Acknowledge the feedback promptly to show workers their input is valued.
- 2
Analyze feedback for common themes or recurring issues to prioritize actions.
- 3
Engage workers in discussions to clarify concerns and potential solutions.
- 4
Implement changes based on feedback and communicate these improvements back to workers.
- 5
Establish a follow-up system to assess the effectiveness of implemented changes.
Example Answers
I would start by acknowledging the feedback to show employees their voices matter. Then, I would look for patterns in the concerns raised and discuss them with workers to gain clarity. After prioritizing key issues, I would implement necessary safety changes and inform the team of the updates. Finally, I would seek their input on the effectiveness of these changes to ensure they address the concerns.
You need to develop a new safety policy. What process would you follow to ensure it is comprehensive and effective?
How to Answer
- 1
Identify the specific hazards and risks in the workplace.
- 2
Engage stakeholders to get input and understand concerns.
- 3
Review existing policies and regulations for compliance.
- 4
Draft the policy with clear, actionable responsibilities.
- 5
Implement training and communication plans for awareness.
Example Answers
First, I would identify all potential hazards and risks associated with operations. Then, I would engage with employees and management to gather insights and concerns. After that, I would review existing policies and relevant regulations to ensure compliance. I would draft the safety policy with clear responsibilities outlined for every role. Finally, I would communicate the new policy and provide necessary training to ensure everyone understands and follows it.
Industrial Safety Engineer Position Details
Recommended Job Boards
These job boards are ranked by relevance for this position.
Related Positions
Ace Your Next Interview!
Practice with AI feedback & get hired faster
Personalized feedback
Used by hundreds of successful candidates
Ace Your Next Interview!
Practice with AI feedback & get hired faster
Personalized feedback
Used by hundreds of successful candidates