Top 30 Industrial Manager Interview Questions and Answers [Updated 2025]
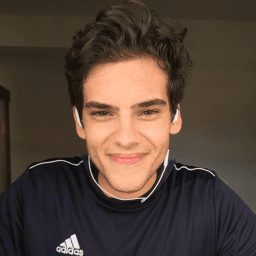
Andre Mendes
•
March 30, 2025
Navigating the competitive landscape of industrial management requires thorough preparation, especially when it comes to interviews. In this post, we explore the most common interview questions faced by aspiring Industrial Managers. You'll find insightful example answers and practical tips on how to answer effectively, equipping you with the confidence needed to excel in your next career step. Dive in to discover how to showcase your skills and experience compellingly.
Download Industrial Manager Interview Questions in PDF
To make your preparation even more convenient, we've compiled all these top Industrial Managerinterview questions and answers into a handy PDF.
Click the button below to download the PDF and have easy access to these essential questions anytime, anywhere:
List of Industrial Manager Interview Questions
Behavioral Interview Questions
Describe a time when you led a team through an important project. What was your approach and what was the outcome?
How to Answer
- 1
Start by briefly explaining the project and its significance.
- 2
Outline your leadership style and decision-making process.
- 3
Highlight teamwork and collaboration among team members.
- 4
Discuss challenges faced and how you overcame them.
- 5
Conclude with the positive outcome and what you learned.
Example Answers
In my previous role, I led a project to streamline our manufacturing process, which was critical for reducing costs. I utilized a collaborative approach, involving team members in brainstorming sessions. We faced a supply chain delay but pivoted by finding alternative suppliers quickly. The project was completed ahead of schedule, reducing costs by 20%.
Can you tell us about a time you had to make a difficult decision with incomplete information? How did you handle it?
How to Answer
- 1
Choose a specific situation that involved uncertainty.
- 2
Explain the context and why it was difficult.
- 3
Discuss the process you used to make the decision.
- 4
Share the outcome and what you learned from it.
- 5
Emphasize your ability to act despite uncertainty.
Example Answers
In my previous role as a production supervisor, I faced a decision on whether to halt production due to a machinery issue. I had limited data on the severity of the problem but assessed the potential risks. I decided to pause operations to ensure safety. Ultimately, we found a minor issue that was quickly resolved. This taught me the value of prioritizing safety and the process of making informed decisions under pressure.
Don't Just Read Industrial Manager Questions - Practice Answering Them!
Reading helps, but actual practice is what gets you hired. Our AI feedback system helps you improve your Industrial Manager interview answers in real-time.
Personalized feedback
Unlimited practice
Used by hundreds of successful candidates
Give an example of a time when you worked with a cross-functional team to achieve a common goal. What was your role and contribution?
How to Answer
- 1
Choose a specific project that involved multiple departments.
- 2
Clearly state your role within the team and main responsibilities.
- 3
Highlight the collaborative efforts and communication strategies used.
- 4
Explain the outcome of the project and how it benefited the organization.
- 5
Reflect on what you learned from the experience and how it improved your skills.
Example Answers
In my previous role as a project coordinator, I worked on a new product launch that involved the marketing, sales, and engineering teams. I organized weekly meetings to ensure alignment between teams, tracked project milestones, and facilitated communication. The launch was successful, achieving a 20% higher sales target than expected. I learned the importance of cross-departmental collaboration for driving results.
Provide an example of how you have implemented an innovative solution to a problem in your previous role.
How to Answer
- 1
Identify a specific problem you faced in your role.
- 2
Describe the innovative solution you proposed and its rationale.
- 3
Explain the implementation process and how you engaged your team.
- 4
Highlight the results and benefits of the solution.
- 5
Keep your answer focused and relevant to the position.
Example Answers
At my previous company, we faced a bottleneck in production due to outdated scheduling methods. I proposed implementing a digital scheduling tool that integrated with our existing software. After evaluating options, I led the training sessions for the team and supervised the rollout. This reduced scheduling conflicts by 30% and increased output by 15%.
Describe a time when you had to communicate complex information to a non-technical audience. How did you ensure understanding?
How to Answer
- 1
Identify a specific complex topic you explained.
- 2
Describe the non-technical audience and their background.
- 3
Explain how you simplified the information using analogies or visuals.
- 4
Share the methods you used to check for understanding.
- 5
Conclude with the outcome of the communication.
Example Answers
During a project meeting, I needed to explain a new production process to the marketing team. I used a simple analogy comparing the process to baking a cake, breaking down the steps involved while illustrating with visuals. I asked them questions to ensure they followed along and encouraged them to share their thoughts. They grasped the concept and were able to promote the project effectively.
Tell us about a time you identified a potential risk in a project and how you managed it.
How to Answer
- 1
Choose a specific project where you identified a clear risk.
- 2
Describe the risk and its potential impact on the project.
- 3
Explain the steps you took to address the risk.
- 4
Discuss the outcome and what you learned.
- 5
Keep the story focused and ensure it highlights your problem-solving skills.
Example Answers
In a recent project to launch a new product, I identified that the supply chain could be disrupted due to vendor reliability issues. I organized a meeting to assess alternative suppliers, which led us to diversify our vendor options. As a result, we minimized delays and delivered on time.
Have you ever resolved a conflict within your team? How did you approach resolving it?
How to Answer
- 1
Identify the conflict clearly and the parties involved
- 2
Listen actively to each person's perspective
- 3
Encourage open communication to find common ground
- 4
Propose solutions collaboratively and find a compromise
- 5
Follow up to ensure resolution and team cohesion
Example Answers
In a previous project, two team members disagreed on the approach to take. I facilitated a meeting where each could express their views while I actively listened. We eventually identified a combined method that incorporated both ideas, which improved our project's efficiency.
Describe a situation where you set a challenging goal for your team and the steps you took to achieve it.
How to Answer
- 1
Identify a specific goal you set that was challenging but achievable.
- 2
Discuss how you communicated the goal to your team clearly.
- 3
Explain the steps taken to break down the goal into manageable tasks.
- 4
Share how you motivated the team and tracked progress.
- 5
Conclude with the outcome and what you learned from the experience.
Example Answers
In my previous role, I set a goal to reduce production waste by 20% within six months. I communicated this objective during a team meeting, emphasizing its importance for our budget. We then brainstormed ideas and broke the goal into weekly targets, assigning tasks to different team members. I held weekly check-ins to monitor progress and motivate the team. Ultimately, we achieved a 25% reduction in waste, improving our sustainability and profitability.
Technical Interview Questions
Explain how you would approach analyzing and improving a manufacturing process to increase efficiency.
How to Answer
- 1
Identify key performance indicators to measure efficiency
- 2
Conduct a value stream mapping to visualize the process
- 3
Engage the team to gather insights and suggestions
- 4
Implement small-scale tests of proposed changes
- 5
Review data and adjust based on feedback and results
Example Answers
To improve efficiency, I would first identify key performance indicators like cycle time and waste rates. Then, I would create a value stream map to visualize and analyze the current process, identifying bottlenecks. Engaging with the team would be crucial to gather their insights and suggestions. I would implement small-scale tests of changes, review the outcomes, and adjust based on performance data.
What quality control methods do you commonly use in industrial management, and why?
How to Answer
- 1
Identify specific quality control methods you have experience with
- 2
Explain why each method is effective in your context
- 3
Mention how these methods contribute to operational efficiency
- 4
Provide examples or outcomes from using these methods
- 5
Consider including any relevant metrics or improvements achieved
Example Answers
In my role, I commonly use Statistical Process Control (SPC) to monitor process variation. SPC helps in identifying trends that can lead to defects before they happen, improving product quality and reducing waste.
Don't Just Read Industrial Manager Questions - Practice Answering Them!
Reading helps, but actual practice is what gets you hired. Our AI feedback system helps you improve your Industrial Manager interview answers in real-time.
Personalized feedback
Unlimited practice
Used by hundreds of successful candidates
Describe the key components of an effective supply chain management system in an industrial context.
How to Answer
- 1
Identify and define key components such as procurement, production, distribution, and logistics.
- 2
Emphasize the importance of communication and information flow in the supply chain.
- 3
Discuss the role of technology and data analytics in enhancing supply chain efficiency.
- 4
Mention the significance of supplier relationships and partnerships.
- 5
Highlight the need for continuous improvement and flexibility in the supply chain.
Example Answers
An effective supply chain management system includes procurement for sourcing materials, production for manufacturing goods, and logistics for distribution. Communication across all levels is crucial, supported by technology like ERP systems for real-time data analysis.
What is lean manufacturing, and how can it be applied in an industrial setting?
How to Answer
- 1
Define lean manufacturing clearly and concisely.
- 2
Mention the principles of eliminating waste and maximizing value.
- 3
Give examples of lean tools like 5S, Kaizen, or Value Stream Mapping.
- 4
Explain how these principles can streamline production processes.
- 5
Highlight measurable benefits such as cost reduction and improved efficiency.
Example Answers
Lean manufacturing is a method focused on minimizing waste while maximizing productivity. In an industrial setting, we can apply it by using tools like 5S to organize the workplace effectively and implementing Kaizen for continuous improvement.
How do you handle budgeting for industrial projects, and what are some key considerations?
How to Answer
- 1
Identify and list all project costs clearly
- 2
Prioritize critical expenses and allocate funds accordingly
- 3
Implement a monitoring system to track budget vs. actual expenses
- 4
Adjust budgets as necessary while keeping stakeholders informed
- 5
Review past projects for lessons learned to improve future budgeting
Example Answers
In managing budgets for industrial projects, I start by identifying all potential costs, including materials, labor, and overhead. I prioritize these expenses to ensure critical areas are funded first. Regular monitoring of the budget against actual expenditures helps me stay on track, and I adjust as needed while keeping my team updated.
How do you use data analysis to inform your decisions in industrial management?
How to Answer
- 1
Identify key performance indicators relevant to your operations
- 2
Utilize statistical tools to analyze production data and trends
- 3
Make data-driven decisions to improve efficiency and reduce costs
- 4
Regularly review data to adjust strategies in real time
- 5
Communicate findings clearly to your team for collaborative decision-making
Example Answers
I regularly analyze key performance indicators such as production yield and downtime. By using statistical tools, I can identify trends and make informed decisions to enhance operational efficiency and cut costs.
Discuss your experience with implementing automation in an industrial setting. What are the benefits and challenges?
How to Answer
- 1
Begin with a specific example of an automation project you led or participated in
- 2
Outline the technology used and the processes that were automated
- 3
Explain the benefits such as improved efficiency or cost savings with metrics if possible
- 4
Discuss challenges encountered like workforce adjustment or technical issues
- 5
Conclude with lessons learned and how they guide future automation efforts
Example Answers
In my previous role at XYZ Manufacturing, I implemented an automated assembly line using robotic arms. This reduced production time by 30% and lowered labor costs by 20%. The main challenge was training the existing workforce to operate alongside robots, which we overcame with comprehensive training sessions.
What project management methodologies are you familiar with, and how do you apply them in industrial projects?
How to Answer
- 1
Identify key project management methodologies relevant to industrial settings like Agile, Lean, and Six Sigma.
- 2
Explain how you implement these methodologies in specific projects with examples.
- 3
Highlight outcomes or improvements achieved through these methodologies.
- 4
Discuss the team dynamics and collaboration aspects involved.
- 5
Be prepared to address how you adapt methodologies to fit different project needs.
Example Answers
I am familiar with Lean and Six Sigma methodologies. For instance, in a recent manufacturing project, I applied Lean principles to streamline our production line. This led to a 20% reduction in waste and a 15% increase in efficiency.
How do you determine the best allocation of resources in an industrial environment?
How to Answer
- 1
Assess the current resource availability and needs of each department
- 2
Use data analysis to identify which areas require more support
- 3
Prioritize projects based on impact and alignment with strategic goals
- 4
Engage with team leaders to gather insights on resource usage
- 5
Continuously monitor performance and adjust allocations as necessary
Example Answers
To determine the best allocation of resources, I first assess the current needs of each department and analyze data to identify resource gaps. I prioritize allocation based on the projects with the highest impact on our strategic goals. This approach ensures that our resources are used effectively.
How do you evaluate and integrate new technologies into existing industrial processes?
How to Answer
- 1
Start by identifying the specific needs of your processes.
- 2
Research and analyze potential technologies that can address these needs.
- 3
Assess the compatibility of new technologies with existing systems.
- 4
Pilot the chosen technology in a controlled environment before full integration.
- 5
Gather feedback from operators and monitor performance metrics post-integration.
Example Answers
I first assess the current process and identify inefficiencies, then I research technologies that fit our needs. I ensure the new technology integrates well with our existing systems and pilot it in one area to gather data before full rollout.
Don't Just Read Industrial Manager Questions - Practice Answering Them!
Reading helps, but actual practice is what gets you hired. Our AI feedback system helps you improve your Industrial Manager interview answers in real-time.
Personalized feedback
Unlimited practice
Used by hundreds of successful candidates
What strategies do you use for managing waste and ensuring sustainability in manufacturing?
How to Answer
- 1
Assess current waste levels and identify areas for reduction.
- 2
Implement recycling programs for materials like plastic and metal.
- 3
Engage employees in sustainability initiatives to foster a culture of responsibility.
- 4
Utilize technology for monitoring waste and optimizing processes.
- 5
Develop partnerships with suppliers who prioritize sustainable practices.
Example Answers
I start by conducting a waste audit to see where we can cut down on excess. For example, at my last job, we introduced a recycling program that reduced our plastic waste by 30%.
How do you ensure compliance with industry regulations and standards in industrial operations?
How to Answer
- 1
Stay updated on relevant regulations and standards through continuous education.
- 2
Implement a compliance management system to monitor and enforce standards.
- 3
Conduct regular audits and inspections to identify and rectify non-compliance.
- 4
Train staff on compliance requirements and best practices.
- 5
Establish a reporting system for compliance issues and corrective actions.
Example Answers
I ensure compliance by continuously updating my knowledge on regulations and standards, and I have implemented a compliance management system to monitor our processes. We also conduct regular audits to catch any potential issues early.
Discuss your experience with Enterprise Resource Planning (ERP) systems in an industrial context.
How to Answer
- 1
Mention specific ERP systems you have used, like SAP or Oracle.
- 2
Describe your role in implementing or managing these systems.
- 3
Provide examples of how ERP improved efficiency or decision-making in your past jobs.
- 4
Highlight any training or support you provided to team members regarding ERP.
- 5
Discuss any challenges faced with ERP implementation and how you overcame them.
Example Answers
In my previous position, I worked with SAP for inventory management and production planning. I was responsible for managing the implementation process and trained staff on how to use the system. This led to a 20% reduction in inventory costs due to better stock management.
Situational Interview Questions
Imagine you are managing a project that is falling behind schedule. How would you address this situation with your team?
How to Answer
- 1
Assess the reasons for the delay by gathering input from team members.
- 2
Communicate transparently with the team about the current status and challenges.
- 3
Prioritize tasks and adjust project timelines collaboratively with the team.
- 4
Implement regular check-ins to monitor progress and make adjustments as needed.
- 5
Encourage team feedback and solutions to promote ownership and morale.
Example Answers
I would start by having an open discussion with the team to identify the root causes of the delay. From there, we would prioritize our tasks and revise the timeline together, ensuring everyone is on board. I believe regular check-ins would help keep us on track.
A safety issue has been reported on the factory floor. What steps would you take to resolve the issue and prevent future incidents?
How to Answer
- 1
Assess the safety issue immediately and gather facts from all relevant parties
- 2
Isolate the area and ensure that safety protocols are followed to protect personnel
- 3
Implement immediate corrective actions to resolve the issue on site
- 4
Conduct a thorough investigation to understand root causes and contributing factors
- 5
Develop a safety training plan or update existing protocols to prevent recurrence
Example Answers
First, I would assess the situation by speaking to employees and examining the area. Then, I would isolate the affected zone to ensure everyone's safety. After that, I would implement corrective actions and investigate the root cause. Finally, I would work on enhancing our safety training to prevent similar issues in the future.
Don't Just Read Industrial Manager Questions - Practice Answering Them!
Reading helps, but actual practice is what gets you hired. Our AI feedback system helps you improve your Industrial Manager interview answers in real-time.
Personalized feedback
Unlimited practice
Used by hundreds of successful candidates
A major client is unhappy with the delivery times. How would you handle the situation to improve client satisfaction?
How to Answer
- 1
Acknowledge the client's concerns promptly and empathetically.
- 2
Investigate the cause of the delays by reviewing internal processes.
- 3
Communicate openly with the client about the findings and proposed solutions.
- 4
Implement a corrective action plan and set realistic timelines.
- 5
Follow up regularly with the client to ensure their satisfaction with the improvements.
Example Answers
I would first reach out to the client to acknowledge their concerns and assure them that I'm taking their feedback seriously. Then, I would analyze our delivery processes to identify any bottlenecks. After that, I would update the client about what I found and present a concrete plan to improve delivery times.
If you notice a consistent decline in productivity on your team, what steps would you take to identify and address the underlying issues?
How to Answer
- 1
Review productivity metrics and gather data to understand the decline.
- 2
Conduct one-on-one meetings with team members to listen to their concerns.
- 3
Analyze workflows and processes to identify any bottlenecks or inefficiencies.
- 4
Encourage open communication in team meetings to discuss challenges and potential solutions.
- 5
Implement targeted training or support based on the identified issues.
Example Answers
First, I'd analyze productivity data to see exactly when the decline started. Then I'd meet with each team member to understand their perspectives and challenges. Lastly, I'd review our processes for any inefficiencies and adjust as needed.
You are close to a project deadline, but there are still unresolved issues. How would you prioritize tasks and manage stress levels?
How to Answer
- 1
Identify critical issues that could impact the deadline.
- 2
Break down tasks into manageable chunks and assign responsibilities.
- 3
Focus on high-impact tasks that align with project goals.
- 4
Set short-term goals to track progress and maintain motivation.
- 5
Implement stress-management techniques such as time-outs or quick exercises.
Example Answers
I would first identify the critical issues affecting the project deadline and assess their impact on the overall goals. Then, I would break down the remaining tasks, prioritize them based on urgency and importance, and delegate responsibilities to the team. By setting short-term goals and checkpoints, I can keep the team motivated and focused. Additionally, I would encourage brief team breaks to help manage stress levels.
An unexpected machine breakdown halts production. How would you handle the situation to minimize downtime and impact?
How to Answer
- 1
Assess the situation immediately to understand the extent of the breakdown
- 2
Notify your maintenance team and ensure they are on their way to troubleshoot
- 3
Communicate with the production team to inform them of the delay and expected timeline
- 4
Explore alternative solutions, such as reallocating resources or using backup machines
- 5
Document the incident and review preventative measures for the future
Example Answers
First, I would assess the situation and determine the cause of the breakdown. Then I would promptly notify the maintenance team to begin repairs. Meanwhile, I would communicate with the production workers to keep them updated about the situation and timelines for resolution. If possible, I would consider reallocating tasks to other areas to maintain some level of productivity until the machine is operational again.
If the process improvement initiative is not delivering results as expected, what steps would you take to address this?
How to Answer
- 1
Analyze the current process data to identify bottlenecks and issues.
- 2
Engage with the team to gather insights on challenges faced.
- 3
Review the original objectives and criteria for success to ensure alignment.
- 4
Adjust the strategy or specific tactics based on findings from analysis.
- 5
Monitor the changes closely to track improvements and make further adjustments.
Example Answers
I would start by analyzing the data we have to pinpoint where the process is failing. Then, I would discuss the issues with my team to gather their insights and input. After reviewing our initial objectives, I'd make necessary adjustments to our approach and keep a close watch on the results to ensure we're heading in the right direction.
Your company is undergoing a major change in operations. How would you manage the transition and support your team?
How to Answer
- 1
Communicate transparently about the changes and the reasons behind them.
- 2
Involve your team in the planning and implementation process.
- 3
Provide necessary training and resources to ease the transition.
- 4
Establish regular check-ins to address concerns and gather feedback.
- 5
Promote a positive and adaptable culture to support change.
Example Answers
I would start by holding a meeting to explain the reasons for the change clearly and how it impacts everyone. I’d involve my team in creating a transition plan and offer training sessions to help them adjust. Regular check-ins would help me address any concerns and adapt our approach as necessary.
Industrial Manager Position Details
Recommended Job Boards
CareerBuilder
www.careerbuilder.com/jobs/industrial-managerZipRecruiter
www.ziprecruiter.com/Jobs/Industrial-ManagerThese job boards are ranked by relevance for this position.
Related Positions
Ace Your Next Interview!
Practice with AI feedback & get hired faster
Personalized feedback
Used by hundreds of successful candidates
Ace Your Next Interview!
Practice with AI feedback & get hired faster
Personalized feedback
Used by hundreds of successful candidates