Top 29 Production Plant Manager Interview Questions and Answers [Updated 2025]
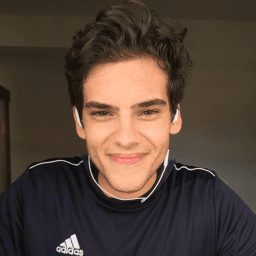
Andre Mendes
•
March 30, 2025
Preparing for a Production Plant Manager interview can be daunting, but having the right questions and answers at your fingertips can make all the difference. In this post, we've compiled the most common interview questions for this pivotal role, complete with example answers and helpful tips to respond effectively. Get ready to impress your interviewers with confidence and clarity as you navigate your path to success.
Download Production Plant Manager Interview Questions in PDF
To make your preparation even more convenient, we've compiled all these top Production Plant Managerinterview questions and answers into a handy PDF.
Click the button below to download the PDF and have easy access to these essential questions anytime, anywhere:
List of Production Plant Manager Interview Questions
Technical Interview Questions
What methods do you use to optimize production processes and increase efficiency?
How to Answer
- 1
Identify key performance indicators to measure efficiency.
- 2
Implement lean manufacturing techniques to eliminate waste.
- 3
Use data analysis to identify bottlenecks in production.
- 4
Engage staff in continuous improvement initiatives.
- 5
Regularly review and update production workflows.
Example Answers
I focus on key performance indicators like cycle time and defect rates. By analyzing these metrics, I apply lean techniques to reduce waste, ensuring we streamline processes effectively.
What inventory management strategies do you employ to ensure adequate stock levels without overstocking?
How to Answer
- 1
Analyze historical sales data to forecast inventory needs accurately
- 2
Implement Just-In-Time (JIT) inventory to reduce holding costs
- 3
Utilize inventory management software for real-time tracking
- 4
Establish strong relationships with suppliers for flexible reordering
- 5
Regularly review stock levels and adjust reorder points based on demand
Example Answers
I analyze historical sales data to create accurate forecasts, allowing me to maintain optimal stock levels. Additionally, I utilize Just-In-Time inventory practices to minimize holding costs and rely on inventory management software to keep track of stock in real-time.
Don't Just Read Production Plant Manager Questions - Practice Answering Them!
Reading helps, but actual practice is what gets you hired. Our AI feedback system helps you improve your Production Plant Manager interview answers in real-time.
Personalized feedback
Unlimited practice
Used by hundreds of successful candidates
What is your approach to planning and managing equipment maintenance to prevent downtime?
How to Answer
- 1
Implement a preventive maintenance schedule based on manufacturer recommendations.
- 2
Train staff on proper equipment usage to minimize wear and tear.
- 3
Utilize data analytics to predict maintenance needs through equipment performance tracking.
- 4
Establish clear communication with your team about the maintenance plan and schedules.
- 5
Review and adjust the maintenance approach regularly based on performance outcomes.
Example Answers
I focus on preventive maintenance by creating a detailed schedule that follows the manufacturer's guidelines. I also leverage performance data to adjust the timing of maintenance activities based on actual usage and condition.
How do you ensure that your production schedule aligns with supply chain requirements and constraints?
How to Answer
- 1
Establish strong communication with supply chain teams to understand their needs.
- 2
Use data analytics to track inventory levels and production capacity.
- 3
Implement flexible scheduling to quickly adapt to supply chain changes.
- 4
Regularly review and update the production schedule based on demand forecasts.
- 5
Leverage technology for real-time monitoring of supply chain and production metrics.
Example Answers
I hold regular meetings with the supply chain team to align our production goals with their inventory strategies. By using data analytics, I can monitor inventory levels and adjust the production schedule proactively.
Explain your experience with lean manufacturing principles. How have you implemented these in a production environment?
How to Answer
- 1
Define lean manufacturing and its core principles like waste reduction and continuous improvement.
- 2
Share specific examples of lean tools you used, such as 5S, Kaizen, or Value Stream Mapping.
- 3
Discuss measurable results you've achieved, such as increased efficiency or reduced cycle times.
- 4
Emphasize teamwork and employee involvement in the lean process.
- 5
Explain how you overcame challenges during implementation.
Example Answers
In my previous role, I implemented 5S to organize our workspace, which led to a 20% increase in productivity. I trained my team on the importance of maintaining organized work areas, resulting in fewer errors and faster turnaround times.
How do you utilize data analytics to drive production decisions and improvements?
How to Answer
- 1
Identify key metrics that affect production performance.
- 2
Discuss tools or software you use for data analysis.
- 3
Emphasize how data leads to actionable insights.
- 4
Give a specific example of a decision made using data.
- 5
Mention the outcome of the data-driven decision.
Example Answers
In my previous role, I tracked key metrics like cycle time and yield using a dashboard. We utilized a software tool that visualized our production data, which helped us identify bottlenecks. By analyzing the data, we realized that changing a machine setting could reduce cycle time by 20%, leading to a significant increase in overall production.
Discuss your experience with integrating automation into production processes. What challenges did you face?
How to Answer
- 1
Be specific about your role in automation projects
- 2
Mention the types of automation technologies used
- 3
Discuss measurable outcomes or improvements
- 4
Highlight any resistance faced and how you overcame it
- 5
Explain what you learned from the challenges encountered
Example Answers
In my previous position, I led a project to integrate robotic arms into our assembly line, which reduced labor costs by 20%. One significant challenge was pushback from the workforce, worried about job loss. I facilitated workshops to explain the benefits and reassured them about job transformation rather than elimination.
How do you ensure that production processes comply with relevant industry regulations and standards?
How to Answer
- 1
Stay updated on industry regulations and standards through training and seminars
- 2
Implement regular audits to assess compliance in production processes
- 3
Develop clear SOPs for production that align with regulations
- 4
Train staff on compliance requirements and the importance of adherence
- 5
Utilize compliance software to track and document processes
Example Answers
I ensure compliance by regularly attending industry seminars and workshops. I also conduct monthly audits of our production processes to identify any non-compliance issues. Additionally, I have developed SOPs that are regularly updated to meet current regulations.
How do you manage the production budget? What tools or strategies do you use to track and control expenses?
How to Answer
- 1
Establish a clear budget plan based on historical data and production goals
- 2
Use budgeting software or spreadsheets for tracking expenses
- 3
Implement regular reviews of budget vs. actual spending
- 4
Identify and monitor key performance indicators (KPIs) related to production costs
- 5
Encourage team feedback to find cost-saving opportunities
Example Answers
I manage the production budget by creating a detailed budget plan that relies on historical data to set realistic production goals. I use Excel for tracking expenses and review them weekly against our actual spending to ensure we stay on track.
Describe your approach to managing large-scale production projects. What methodologies do you use?
How to Answer
- 1
Start by outlining your project management methodology, such as Lean or Six Sigma.
- 2
Explain how you set clear goals and KPIs for the project.
- 3
Discuss the importance of team communication and collaboration.
- 4
Mention how you monitor progress and adapt plans as needed.
- 5
Provide an example of a successful project where you implemented these methods.
Example Answers
I typically use Lean Manufacturing principles to manage large-scale production projects. I set clear KPIs at the outset, ensuring everyone knows the targets. Regular team check-ins help facilitate communication, and I track progress weekly, adapting the plan when necessary. For example, in a recent project, we increased efficiency by 20% by implementing these methods.
Don't Just Read Production Plant Manager Questions - Practice Answering Them!
Reading helps, but actual practice is what gets you hired. Our AI feedback system helps you improve your Production Plant Manager interview answers in real-time.
Personalized feedback
Unlimited practice
Used by hundreds of successful candidates
Behavioral Interview Questions
Describe a time when you had to lead a team under pressure to meet a tight deadline. How did you ensure success?
How to Answer
- 1
Choose a specific project with a clear deadline and outcome.
- 2
Explain the pressure factors and challenges faced.
- 3
Detail your leadership actions taken to rally the team.
- 4
Highlight communication strategies used to keep everyone informed.
- 5
Conclude with the successful result and any lessons learned.
Example Answers
In my last role, we faced a sudden increase in orders, and I had to lead my team to meet a deadline of one week. I organized daily stand-up meetings to assess progress and address issues. By redistributing tasks and ensuring open communication, we not only met the deadline but also improved our efficiency by 15%.
Can you give an example of a complex production issue you resolved? What steps did you take?
How to Answer
- 1
Identify a specific problem related to production efficiency or quality.
- 2
Describe the analysis you conducted to understand the root cause.
- 3
Explain the solution you implemented step-by-step.
- 4
Highlight the results achieved from your solution.
- 5
Mention any lessons learned or how it improved processes long-term.
Example Answers
In my previous role, we experienced a bottleneck in our assembly line that delayed shipments. I analyzed the workflow and discovered that outdated machinery was the main issue. I proposed upgrading the equipment and worked with the team to schedule installations during off-hours. As a result, we increased our output by 30% and met shipping deadlines consistently.
Don't Just Read Production Plant Manager Questions - Practice Answering Them!
Reading helps, but actual practice is what gets you hired. Our AI feedback system helps you improve your Production Plant Manager interview answers in real-time.
Personalized feedback
Unlimited practice
Used by hundreds of successful candidates
Tell me about a time when you had to mediate a conflict between team members on the production floor. How did you handle it?
How to Answer
- 1
Start with a clear description of the conflict situation.
- 2
Explain the impact of the conflict on productivity or morale.
- 3
Describe the steps you took to mediate between the team members.
- 4
Highlight the resolution and how it improved the team's dynamics.
- 5
Mention any follow-up actions to prevent future conflicts.
Example Answers
In my previous role, there was a disagreement between two operators over machine settings that affected production. I held a meeting with both to hear their perspectives and facilitate a discussion. By focusing on facts and data, we identified a common ground and adjusted the settings collaboratively. This not only resolved the issue but also built a better rapport between the operators, leading to smoother operations.
Describe an experience where you improved safety standards in a production environment. What was the outcome?
How to Answer
- 1
Use the STAR method: Situation, Task, Action, Result.
- 2
Focus on a specific example with measurable outcomes.
- 3
Highlight collaborative efforts with the team to enhance safety.
- 4
Mention any training or new protocols implemented.
- 5
Discuss the impact on overall production and team morale.
Example Answers
In my previous role, we had a high rate of minor accidents. I led a team to conduct a safety audit, identifying areas for improvement. We introduced new safety protocols and training sessions. Over six months, we reduced incidents by 40%, promoting a safer work environment and boosting team morale.
Have you initiated any process improvements or innovations in a previous role? What was the impact?
How to Answer
- 1
Identify a specific process improvement you led.
- 2
Explain the problem you aimed to solve with the improvement.
- 3
Describe your approach and steps taken.
- 4
Quantify the impact or results of the improvement if possible.
- 5
Be prepared to discuss any challenges you faced during implementation.
Example Answers
In my previous role, I implemented a new inventory management system that reduced stock discrepancies by 30%. I identified frequent errors in order fulfillment as the main issue, and after researching solutions, I led a team to adopt a software that streamlined our tracking process. This not only improved accuracy but also saved us approximately 15 hours of work time per week.
Give me an example of how you effectively communicated a change in procedure to your team. What was the key to success?
How to Answer
- 1
Use a specific example from your experience.
- 2
Outline the change that was made and its importance.
- 3
Describe how you communicated the change to your team.
- 4
Mention the tools or methods you used to facilitate communication.
- 5
Highlight the positive outcome of your communication.
Example Answers
In my previous role, we switched to a new safety protocol that required immediate implementation. I held a team meeting to explain the changes, focusing on the benefits for our safety. I used visual aids and a step-by-step guide to explain the new procedures. As a result, compliance improved significantly and we had zero safety incidents in the following month.
Describe a time when you had to adapt quickly to a change in production demands. How did you manage it?
How to Answer
- 1
Identify a specific situation where demand changed unexpectedly.
- 2
Explain the steps you took to assess the change in demands.
- 3
Highlight your communication with the team about the changes.
- 4
Detail any adjustments made to schedules or processes.
- 5
Conclude with the outcome and what you learned.
Example Answers
In my previous role, we received a major order with a two-week turnaround. I quickly assessed our current production schedule, communicated with my team to gauge their capacity, and prioritized tasks. I reallocated resources to focus on the new order and coordinated shifts. We successfully met the deadline and learned to be more flexible in our planning.
How have you mentored or developed team members in your previous managerial roles?
How to Answer
- 1
Share specific examples of mentorship experiences.
- 2
Highlight any training programs you implemented.
- 3
Discuss one-on-one coaching sessions you conducted.
- 4
Mention how you identified team members' strengths and weaknesses.
- 5
Explain the positive outcomes of your mentorship efforts.
Example Answers
In my last role, I mentored a junior engineer by providing weekly one-on-one coaching sessions. I helped him improve his project management skills, which ultimately led to his promotion within a year.
Can you provide an example of how you managed to cut costs in a production setting without sacrificing quality?
How to Answer
- 1
Identify specific cost-cutting measures you implemented
- 2
Emphasize the importance of quality assurance during the process
- 3
Use data to support your results, such as percentages or actual dollar savings
- 4
Describe collaboration with teams or departments to achieve goals
- 5
Conclude with the long-term benefits of the changes made
Example Answers
In my previous role, I led an initiative to reduce material waste by implementing a new inventory management system. This reduced our material costs by 15% while ensuring that we maintained strict quality controls. We also conducted regular audits to keep quality on track.
Tell us about a time you identified a quality issue in the production process. What actions did you take to address it?
How to Answer
- 1
Describe the specific quality issue you encountered.
- 2
Mention how you discovered the issue and its impact on production.
- 3
Explain the steps you took to investigate and diagnose the root cause.
- 4
Detail the corrective actions you implemented to resolve the issue.
- 5
Conclude with the positive outcome or improvements that resulted.
Example Answers
In my previous role, we noticed that the defect rate of one of our product lines had risen sharply. I reviewed production logs and discovered that the rise in defects coincided with a change in a supplier's material. I initiated a quality audit of the materials, discussed findings with the supplier, and switched back to the original material. As a result, defect rates returned to normal within two weeks.
Don't Just Read Production Plant Manager Questions - Practice Answering Them!
Reading helps, but actual practice is what gets you hired. Our AI feedback system helps you improve your Production Plant Manager interview answers in real-time.
Personalized feedback
Unlimited practice
Used by hundreds of successful candidates
Situational Interview Questions
You find that your production line is frequently overloaded. How would you handle resource allocation to balance the workload?
How to Answer
- 1
Analyze production data to identify peak times and bottlenecks
- 2
Evaluate workforce capacity and consider cross-training staff
- 3
Assess equipment availability and optimize machine usage
- 4
Implement a shift scheduling system to increase production hours
- 5
Communicate with team members to gather input on workload management
Example Answers
I would start by analyzing production data to pinpoint when bottlenecks occur. Then, I'd evaluate our current workforce and explore cross-training options to ensure flexibility. Additionally, I would look at equipment utilization to maximize efficiency.
If a key supplier failed to deliver materials on time, delaying production, how would you address the issue?
How to Answer
- 1
Assess the impact of the delay on production schedules
- 2
Communicate immediately with the supplier to understand the cause
- 3
Explore alternative suppliers or materials to mitigate delays
- 4
Develop a recovery plan to minimize production downtimes
- 5
Implement measures to prevent future supply chain issues
Example Answers
First, I would evaluate how the delay affects our production timeline. Then, I'd contact the supplier to understand the issue and work on a timeline for resolution. If necessary, I'd reach out to alternative suppliers to source the materials quickly and ensure production continues with minimal downtime.
Don't Just Read Production Plant Manager Questions - Practice Answering Them!
Reading helps, but actual practice is what gets you hired. Our AI feedback system helps you improve your Production Plant Manager interview answers in real-time.
Personalized feedback
Unlimited practice
Used by hundreds of successful candidates
A sudden increase in production demand has resulted in a staff shortage. How would you manage this situation?
How to Answer
- 1
Assess current staffing levels and identify gaps.
- 2
Implement overtime for existing employees to meet demand.
- 3
Consider hiring temporary staff or subcontracting work.
- 4
Improve workflow efficiency to maximize output with available workforce.
- 5
Communicate transparently with your team about the situation and solutions.
Example Answers
I would first evaluate our current staffing levels to see where we can optimize. Implementing overtime for our existing staff would be my immediate approach, combined with seeking temporary workers to fill any gaps.
A safety incident has occurred on the production floor. What immediate actions would you take, and how would you prevent future incidents?
How to Answer
- 1
Assess the situation quickly to ensure no further hazards are present
- 2
Provide immediate medical assistance to anyone injured
- 3
Investigate the incident to gather facts and identify causes
- 4
Communicate transparently with the team about what happened
- 5
Implement safety training sessions to address identified weaknesses
Example Answers
First, I would assess the scene for additional dangers and ensure the area is safe. Then, I would call for medical assistance for anyone affected. After addressing immediate needs, I would investigate the incident by speaking to witnesses and reviewing safety protocols. Finally, I would conduct a training on the relevant safety procedures to prevent future occurrences.
A major customer has complained about the quality of a recent order. How would you respond to resolve the issue?
How to Answer
- 1
Acknowledge the customer's complaint promptly and sincerely.
- 2
Gather specific details about the quality issue from the customer.
- 3
Investigate the root cause of the quality problem internally.
- 4
Develop a corrective action plan based on findings.
- 5
Communicate the resolution plan and follow up with the customer.
Example Answers
I would first acknowledge the customer's concern and thank them for bringing it to my attention. Then, I would ask for specific details about the quality issue they experienced. After gathering information, I would investigate within our team to find the root cause and implement a corrective action plan. Finally, I would communicate our findings and how we plan to resolve the issue, ensuring the customer feels valued and informed.
An unexpected equipment breakdown has halted production. What steps would you take to minimize downtime and resume operations?
How to Answer
- 1
Quickly assess the situation to identify the cause of the breakdown.
- 2
Communicate with the team and inform relevant stakeholders about the issue.
- 3
Initiate immediate repairs or adjustments while exploring alternative production methods.
- 4
Keep detailed documentation of the incident and resolutions for future reference.
- 5
Review and analyze the breakdown afterward to implement preventive measures.
Example Answers
First, I would assess the equipment to determine the cause of the breakdown. Then, I would communicate with my team to keep everyone informed. If possible, I would start repairs right away and look for temporary solutions to keep production moving.
You notice that some team members are frequently making mistakes due to lack of training. How would you address this?
How to Answer
- 1
Assess the specific areas where mistakes are occurring
- 2
Gather feedback from team members about their training needs
- 3
Develop a targeted training program based on identified gaps
- 4
Implement regular training sessions and hands-on workshops
- 5
Monitor progress and adjust training as necessary
Example Answers
I would first identify the specific tasks where mistakes are happening and discuss with the team to understand their training needs. Then, I would create a focused training program that addresses these gaps and ensure regular sessions to foster skill development.
During an emergency situation, such as a natural disaster, how would you ensure the safety of your employees and continuity of operations?
How to Answer
- 1
Develop and communicate an emergency response plan before any situation occurs
- 2
Train employees regularly on emergency procedures and safety protocols
- 3
Establish clear communication channels for updates during an emergency
- 4
Identify critical operations and ensure they have backup plans
- 5
Engage with local emergency services for support and resource sharing
Example Answers
In the event of an emergency, I would first implement our pre-established emergency response plan, ensuring all employees are aware of evacuation protocols. Regular training sessions help everyone stay prepared and know their roles. Communication channels like a text notification system would keep everyone updated on the situation.
Management suggests implementing a new technology in production that you've never used before. How would you evaluate and proceed with this proposal?
How to Answer
- 1
Research the new technology and its applications in similar industries.
- 2
Engage with vendors for demonstrations and practical insights.
- 3
Consult with your team for their input and expertise.
- 4
Evaluate potential impact on productivity and costs.
- 5
Develop a pilot plan to test the technology before full implementation.
Example Answers
I would start by researching the technology to understand its benefits and applications. Then, I would reach out to the vendor for a demo and gather feedback from my team. After evaluating the potential costs and productivity impacts, I would propose running a pilot project to see how it performs in our production environment.
Production Plant Manager Position Details
Recommended Job Boards
Michael Page
www.michaelpage.com/jobs/plant-managerCareerBuilder
www.careerbuilder.com/jobs/production-plant-managerThese job boards are ranked by relevance for this position.
Related Positions
Ace Your Next Interview!
Practice with AI feedback & get hired faster
Personalized feedback
Used by hundreds of successful candidates
Ace Your Next Interview!
Practice with AI feedback & get hired faster
Personalized feedback
Used by hundreds of successful candidates