Top 28 Instrumentation Technician Interview Questions and Answers [Updated 2025]
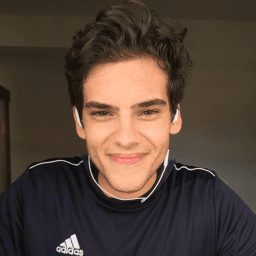
Andre Mendes
•
March 30, 2025
Navigating an interview for an Instrumentation Technician role can be daunting, but preparation is key to success. In this blog post, you'll discover the most common interview questions for this specialized position, complete with example answers and insightful tips to craft your responses effectively. Equip yourself with the knowledge and confidence needed to impress your interviewers and secure that coveted role.
Download Instrumentation Technician Interview Questions in PDF
To make your preparation even more convenient, we've compiled all these top Instrumentation Technicianinterview questions and answers into a handy PDF.
Click the button below to download the PDF and have easy access to these essential questions anytime, anywhere:
List of Instrumentation Technician Interview Questions
Behavioral Interview Questions
Can you describe a time when you had to troubleshoot a complex instrumentation issue? What steps did you take to resolve it?
How to Answer
- 1
Identify a specific instrumentation issue you faced.
- 2
Explain the steps you took to diagnose the problem.
- 3
Describe how you involved tools or technologies in your troubleshooting.
- 4
Share the outcome and what you learned from the experience.
- 5
Emphasize teamwork if applicable, mentioning collaboration with others.
Example Answers
In my previous job, I encountered a failure in a pressure transmitter that caused erroneous readings. I started by checking the calibration and found it was off. I used a multimeter to verify wiring integrity and discovered a loose connection. I fixed the wiring, recalibrated the transmitter, and confirmed correct operation, which restored accurate readings and improved process efficiency.
Tell me about a situation where you had to collaborate with engineers to improve a system. What was your role, and what was the outcome?
How to Answer
- 1
Identify a specific project where collaboration took place.
- 2
Clearly define your role and responsibilities in the project.
- 3
Discuss the impact of the collaboration on system performance.
- 4
Include any challenges faced and how they were overcome.
- 5
Mention measurable outcomes or improvements achieved.
Example Answers
In a recent project, I worked with engineers to upgrade our control system for a pumping station. My role was to analyze existing instrumentation and provide insights on necessary improvements. We identified a bottleneck in signal transmission, which I helped resolve by recommending new sensors that improved response time by 30%. The outcome was a more efficient system that reduced downtime significantly.
Don't Just Read Instrumentation Technician Questions - Practice Answering Them!
Reading helps, but actual practice is what gets you hired. Our AI feedback system helps you improve your Instrumentation Technician interview answers in real-time.
Personalized feedback
Unlimited practice
Used by hundreds of successful candidates
Describe a time your initial approach to an instrumentation task failed. How did you adapt and what did you learn?
How to Answer
- 1
Choose a specific situation where your approach didn't work.
- 2
Explain clearly what the failure was and why it happened.
- 3
Describe the immediate steps you took to adapt to the situation.
- 4
Highlight what you learned from the experience and how it improved your skills.
- 5
Connect your learning to how it benefits your future work in instrumentation.
Example Answers
In a calibration project, my initial method for measuring pressure inconsistencies yielded inaccurate results. I realized I had overlooked a critical sensor specification. I quickly switched to a different calibration technique, double-checked against manufacturer guidelines, and achieved accurate readings. This taught me the importance of thoroughly reviewing equipment specifications before starting a task.
What is an example of a safety protocol you had to implement during an instrumentation project? How did you ensure compliance?
How to Answer
- 1
Choose a specific project where safety was crucial.
- 2
Describe the safety protocol you implemented clearly.
- 3
Explain your methods for ensuring team compliance.
- 4
Highlight any training or communication strategies used.
- 5
Mention the outcomes or improvements resulting from the protocol.
Example Answers
During a project to install pressure sensors, I implemented a lockout/tagout (LOTO) protocol to ensure all power sources were safely disconnected. I conducted training sessions to ensure everyone understood the procedure and followed up with daily check-ins to confirm compliance, resulting in zero accidents during installation.
Provide an example of how you've communicated a complex idea regarding instrumentation to a non-technical audience.
How to Answer
- 1
Identify the complex idea you need to explain.
- 2
Use analogies or everyday examples to simplify concepts.
- 3
Break the information into smaller, digestible parts.
- 4
Encourage questions to clarify understanding.
- 5
Summarize the main points at the end.
Example Answers
In a previous role, I explained how a pressure transmitter works by comparing it to a water gauge in a home. I broke down its functions into measuring pressure and sending signals, allowing the audience to relate to a familiar concept.
Can you give an example of a time when you proposed a process improvement for instrumentation operations? What was the result?
How to Answer
- 1
Identify a specific situation where you noticed inefficiencies.
- 2
Describe the process improvement you proposed and the rationale behind it.
- 3
Explain how you implemented the change and engaged stakeholders.
- 4
Share measurable results or benefits that followed after the improvement.
- 5
Use clear and straightforward language to convey your experience.
Example Answers
At my previous job, I noticed that our calibration process for pressure sensors took too long and led to downtime. I proposed a streamlined procedure that included a standardized checklist. After training the team, we reduced calibration time by 30%, which significantly decreased operational delays.
Describe a time when you had to lead a team through a challenging instrumentation project. What was your approach?
How to Answer
- 1
Select a specific project that highlights your leadership skills.
- 2
Explain the challenges faced and the impact on the team.
- 3
Describe your leadership approach and decision-making process.
- 4
Mention the outcome of the project and any lessons learned.
- 5
Use clear metrics or results to quantify success.
Example Answers
In a previous role, I led a team tasked with upgrading old instrumentation in a manufacturing plant. The challenge was tight timelines and outdated technology. I organized daily check-ins to track progress and address issues quickly. By fostering open communication, we finished the project two weeks early, improving efficiency by 20%.
Technical Interview Questions
What types of instrumentation systems are you most familiar with, and what are their key components?
How to Answer
- 1
Identify specific types of instrumentation systems you have worked with.
- 2
Mention key components of each system and their functions.
- 3
Use relevant examples from your experience to illustrate your familiarity.
- 4
Be concise and focus on systems that are most applicable to the job.
- 5
Prepare to discuss how you troubleshoot or maintain these systems.
Example Answers
I am most familiar with process control systems, particularly PID controllers, flow meters, and temperature sensors. For example, in my last job, I regularly calibrated flow meters to ensure accurate measurements in chemical processes.
Can you explain the process of calibrating an instrument? What tools do you typically use?
How to Answer
- 1
Start with defining calibration and its importance in ensuring accuracy.
- 2
Outline the step-by-step process clearly and concisely.
- 3
Mention specific tools required for calibration based on the instrument type.
- 4
Highlight the importance of documentation and compliance with standards.
- 5
Conclude with how often calibration should be performed.
Example Answers
Calibration is adjusting an instrument to ensure its accuracy. First, I check the instrument's specifications, then I use a reference standard to compare readings. Tools like a multimeter or calibration weights are often used. Finally, I document the calibration results and schedule the next calibration based on equipment usage.
Don't Just Read Instrumentation Technician Questions - Practice Answering Them!
Reading helps, but actual practice is what gets you hired. Our AI feedback system helps you improve your Instrumentation Technician interview answers in real-time.
Personalized feedback
Unlimited practice
Used by hundreds of successful candidates
What methods do you use to test the accuracy and functionality of instrumentation devices?
How to Answer
- 1
Describe specific testing methods you have used in past roles
- 2
Mention tools or technologies that assist in your testing processes
- 3
Include examples of calibration and maintenance procedures
- 4
Discuss how you document and analyze testing results
- 5
Explain how you troubleshoot and resolve identified issues
Example Answers
I use calibrated reference standards and multimeters for ensuring measurement accuracy. I perform regular calibration checks and maintain detailed logs of each test to track performance over time.
Explain the steps you take to troubleshoot a malfunctioning control loop in a process control system.
How to Answer
- 1
Start by gathering data from the control system logs and monitoring tools
- 2
Verify the sensor and actuator performance to ensure they are functioning correctly
- 3
Check the control loop parameters, including setpoints and tuning values
- 4
Analyze the control loop response to identify any patterns in the malfunction
- 5
Implement corrective actions based on your findings and test the loop for stability
Example Answers
First, I would review the system logs and monitoring tools to pinpoint when the issue began. Then, I would check the sensors and actuators to make sure they are operational. After that, I would examine the control loop parameters to see if anything has changed. I’d analyze the response of the loop to understand the problem better, and finally, I would apply the corrective actions and test the system.
What is your experience with signal processing in instrumentation? Can you provide an example?
How to Answer
- 1
Describe your hands-on experience with signal processing tools or software.
- 2
Explain a specific project where you utilized signal processing techniques.
- 3
Highlight the outcomes or improvements achieved through your efforts.
- 4
Mention any relevant certifications or training related to signal processing.
- 5
Keep your answer structured: context, action, and result.
Example Answers
In my previous role, I worked with an oscilliscope and MATLAB for signal filtering in a temperature monitoring project. We were able to reduce noise by 30%, leading to more accurate readings.
What software tools are you comfortable using for managing and analyzing instrumentation data?
How to Answer
- 1
Identify specific software tools you have experience with.
- 2
Mention how you have used these tools in past projects.
- 3
Highlight any certifications or formal training related to these tools.
- 4
Discuss the type of data you have managed or analyzed with these tools.
- 5
Be ready to explain any challenges you faced and how you overcame them.
Example Answers
I am comfortable using software such as LabVIEW and MATLAB for managing and analyzing instrumentation data. In my last role, I utilized LabVIEW to automate data collection from sensors, which improved our efficiency by 30%. I also have experience with Excel for data analysis and reporting.
What regulations and standards regarding instrumentation have you worked with, and how do they influence your work?
How to Answer
- 1
Identify specific regulations like ISA standards, OSHA, or IEC.
- 2
Mention your experience with compliance processes in your work.
- 3
Discuss how these regulations impact safety and quality in your projects.
- 4
Highlight any training or certification you have related to these standards.
- 5
Use real examples to demonstrate your understanding and application of these regulations.
Example Answers
I have worked with ISA standards and OSHA regulations throughout my career. These standards influence my work by ensuring safety protocols are met and equipment is calibrated correctly. For instance, in my last project, we followed ISA guidelines to improve our measurement accuracy, which helped us avoid costly downtime.
Which diagnostic tools do you frequently use for troubleshooting instrumentation and why?
How to Answer
- 1
Identify key tools you use regularly.
- 2
Explain the specific purpose of each tool.
- 3
Share a brief example of how you used each tool to solve a problem.
- 4
Mention any software tools or handheld devices that aid in diagnostics.
- 5
Emphasize the impact of these tools on improving efficiency.
Example Answers
I frequently use a multimeter, which is essential for measuring voltage, current, and resistance. For instance, I once used it to identify a faulty sensor by checking the resistance and confirming it was outside the normal range.
How do you handle data analysis for instrumentation performance evaluation?
How to Answer
- 1
Collect relevant performance data from instruments regularly.
- 2
Utilize statistical tools to analyze trends and identify anomalies.
- 3
Compare current data against baseline performance metrics.
- 4
Document findings and insights for team reviews.
- 5
Implement corrective actions based on analysis outcomes.
Example Answers
I regularly collect performance data from our instrumentation, apply statistical tools to identify any trends or anomalies, and compare this data with established baseline metrics to ensure optimal performance.
Can you discuss your experience in designing instrumentation systems? What are the key factors to consider?
How to Answer
- 1
Start by outlining the specific projects where you designed systems.
- 2
Highlight your familiarity with various instrumentation tools and technologies.
- 3
Discuss collaboration with other engineers or stakeholders for successful design.
- 4
Mention critical factors like accuracy, reliability, and safety in designs.
- 5
Conclude by emphasizing results or improvements achieved through your designs.
Example Answers
In my previous role, I led a project redesigning a pressure monitoring system. I used PLCs and collaborated closely with the mechanical team to ensure all safety standards were met. Key factors I considered included the system's accuracy, reliability under extreme conditions, and user accessibility, which ultimately increased system efficiency by 20%.
Don't Just Read Instrumentation Technician Questions - Practice Answering Them!
Reading helps, but actual practice is what gets you hired. Our AI feedback system helps you improve your Instrumentation Technician interview answers in real-time.
Personalized feedback
Unlimited practice
Used by hundreds of successful candidates
What emergency procedures are you familiar with when dealing with instrumentation failures in a plant environment?
How to Answer
- 1
Identify specific procedures you know related to instrumentation failures
- 2
Mention safety protocols to follow during an emergency
- 3
Include steps for reporting and documenting incidents
- 4
Explain how to isolate or shut down affected systems
- 5
Emphasize the importance of teamwork and communication
Example Answers
In the event of an instrumentation failure, I follow the established emergency procedures that include isolating the affected system and notifying my supervisor immediately. I ensure everyone's safety by following lockout/tagout protocols and document the failure for future analysis.
Situational Interview Questions
If a critical instrument fails during a production run, what steps would you take to address the issue while minimizing downtime?
How to Answer
- 1
Quickly assess the situation to determine the impact of the failure.
- 2
Refer to the instrument's troubleshooting guide to diagnose the issue.
- 3
Implement emergency procedures if available, such as switching to a backup instrument.
- 4
Communicate effectively with the production team about the status and expected downtime.
- 5
Document the issue and follow up with a detailed report after resolution.
Example Answers
I would first assess the failure to understand its impact on production. Then, I would check the troubleshooting guide for the specific instrument. If it’s a critical failure, I would switch to a backup instrument to keep the production running. I would keep the production team informed throughout the process. Lastly, I would document the incident for future reference.
Imagine you are tasked with performing a maintenance check on a newly installed system. What factors would you prioritize in your assessment?
How to Answer
- 1
Check system documentation for specifications and operational standards
- 2
Inspect safety features and ensure they are functional
- 3
Evaluate calibration of instruments against standards
- 4
Monitor performance metrics for any discrepancies
- 5
Identify and address any potential hazards or risks
Example Answers
I would start by reviewing the system documentation to ensure I understand the specifications. Then, I would verify that all safety features are operational. Calibration checks are next, followed by performance monitoring to detect any irregularities.
Don't Just Read Instrumentation Technician Questions - Practice Answering Them!
Reading helps, but actual practice is what gets you hired. Our AI feedback system helps you improve your Instrumentation Technician interview answers in real-time.
Personalized feedback
Unlimited practice
Used by hundreds of successful candidates
If you were to upgrade an outdated instrumentation system, what considerations would you take into account?
How to Answer
- 1
Assess current system performance and identify shortcomings.
- 2
Understand the specific needs of the application and users.
- 3
Evaluate compatibility with existing equipment and technology.
- 4
Consider budget constraints and return on investment.
- 5
Plan for training and support for staff on the new system.
Example Answers
I would first assess the current system's performance to identify key areas that need improvement. Then, I’d ensure that the new instrumentation meets the specific needs of the application, considering what the users find most critical.
How would you approach training a new technician on the specific instrumentation technology your team uses?
How to Answer
- 1
Start with an overview of the technology and its applications.
- 2
Create a structured training plan with hands-on sessions.
- 3
Encourage questions and provide immediate feedback during practice.
- 4
Pair the new technician with an experienced mentor.
- 5
Use real-life scenarios to demonstrate problem-solving techniques.
Example Answers
I would first give the new technician a brief overview of our instrumentation technology, explaining its importance in our processes. Then, I'd design a structured training plan that includes hands-on sessions where they can interact with the equipment. I would encourage them to ask questions and provide feedback as they practice. Additionally, pairing them with a mentor would help them learn from real-life experiences. Lastly, I would incorporate real scenarios to enhance their understanding of problem-solving in our context.
A technician proposes a new method for data collection. How would you evaluate and potentially implement this new method?
How to Answer
- 1
Assess the feasibility and reliability of the proposed method by analyzing the data it collects.
- 2
Discuss the method with the proposing technician to understand its potential advantages and drawbacks.
- 3
Pilot test the method in a controlled environment before wider implementation.
- 4
Review relevant standards and regulations to ensure compliance.
- 5
Gather feedback from the team to identify any potential issues or improvements.
Example Answers
First, I would evaluate the proposed method’s reliability by analyzing sample data it generates. Then, I’d discuss its strengths and weaknesses with the technician. If promising, I’d run a pilot test before full implementation, ensuring it meets all standards.
If you are given an urgent request for troubleshooting an instrumentation issue while you are already engaged in a scheduled task, how would you handle it?
How to Answer
- 1
Assess the urgency of the request quickly
- 2
Communicate clearly with the requesting party
- 3
Evaluate the impact of the scheduled task
- 4
Determine if you can delegate or reschedule tasks
- 5
Prioritize the urgent request if necessary
Example Answers
I would quickly assess how critical the instrumentation issue is and communicate with the team to understand the impact. If it’s urgent, I would evaluate my current task to see if it can wait or be delegated.
How would you approach a situation where you're running low on essential spare parts for instrumentation repairs?
How to Answer
- 1
Assess the inventory to identify critical spares needed immediately
- 2
Communicate with the team to gauge urgency and potential workarounds
- 3
Contact suppliers for expedited orders or alternatives
- 4
Develop a short-term plan for repairs using available resources
- 5
Implement a system for better inventory management in the future
Example Answers
I would first check our inventory to see which parts we are low on. Then, I would discuss with my team to determine which repairs are critical and look for temporary solutions. Meanwhile, I would contact our suppliers to expedite any orders needed.
If you notice a drop in team morale after a critical failure in instrumentation, what steps would you take to address this?
How to Answer
- 1
Acknowledge the team's feelings and validate their concerns
- 2
Organize a team meeting to discuss the failure openly
- 3
Encourage collaboration on solutions to boost engagement
- 4
Recognize individual contributions and celebrate small wins
- 5
Provide support and resources for skill improvement
Example Answers
I would start by acknowledging the team's feelings about the failure, then hold a meeting where we can discuss the issues openly. Collaborating on solutions can help the team feel involved and valued.
If you discovered that there was a significant error in data from instrumentation that could affect safety, what would you do?
How to Answer
- 1
Immediately report the error to your supervisor or safety officer
- 2
Assess the data to understand the impact on safety
- 3
Document the error and your response steps clearly
- 4
Collaborate with the team to validate and rectify the issue
- 5
Follow up to ensure corrective actions are implemented
Example Answers
I would first report the error to my supervisor to ensure safety is prioritized. Next, I would analyze the data to determine how it affects operations. I would document everything and work with the team to correct the error and prevent future occurrences.
Instrumentation Technician Position Details
Recommended Job Boards
These job boards are ranked by relevance for this position.
Related Positions
Ace Your Next Interview!
Practice with AI feedback & get hired faster
Personalized feedback
Used by hundreds of successful candidates
Ace Your Next Interview!
Practice with AI feedback & get hired faster
Personalized feedback
Used by hundreds of successful candidates