Top 30 Instrument Control Technician Interview Questions and Answers [Updated 2025]
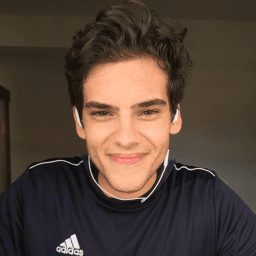
Andre Mendes
•
March 30, 2025
Preparing for an Instrument Control Technician interview can be daunting, but we've got you covered with a comprehensive guide to the most common questions you'll encounter. This post provides insightful example answers and practical tips to help you respond effectively, boosting your confidence and readiness. Dive in to enhance your interview skills and secure that coveted role with ease and assurance.
Download Instrument Control Technician Interview Questions in PDF
To make your preparation even more convenient, we've compiled all these top Instrument Control Technicianinterview questions and answers into a handy PDF.
Click the button below to download the PDF and have easy access to these essential questions anytime, anywhere:
List of Instrument Control Technician Interview Questions
Behavioral Interview Questions
Can you describe a time when you had to troubleshoot a complex instrument control system issue? What was the problem and how did you resolve it?
How to Answer
- 1
Start with a clear description of the issue you faced.
- 2
Explain the steps you took to diagnose the problem systematically.
- 3
Highlight any tools or techniques you used during troubleshooting.
- 4
Discuss the resolution process and how you verified the fix.
- 5
Mention any lessons learned or how it improved system performance.
Example Answers
In my previous role at ABC Manufacturing, we had a major issue where the temperature control loop was fluctuating wildly. I first gathered data logs to analyze the system behavior. I then checked the calibration of the temperature sensors and found one was off. I recalibrated it and validated the stability of the loop over the next few hours, which resolved the fluctuations and improved process stability.
Tell us about a time when you worked as part of a team to complete a project involving instrument controls. What was your role and what did you learn from the experience?
How to Answer
- 1
Start with a brief context about the project and your team.
- 2
Clearly define your specific role and responsibilities.
- 3
Highlight any challenges faced and how the team overcame them.
- 4
Discuss what you learned about teamwork and instrument controls.
- 5
Keep it concise and focus on your contribution to the team's success.
Example Answers
In my previous position, we worked on upgrading the instrument control system for a production facility. I served as the lead technician, responsible for wiring and calibration. We faced delays due to inconsistent sensor performance, but we improved communication and reallocated resources. This taught me the importance of flexibility in teamwork and the critical nature of accurate instrumentation.
Don't Just Read Instrument Control Technician Questions - Practice Answering Them!
Reading helps, but actual practice is what gets you hired. Our AI feedback system helps you improve your Instrument Control Technician interview answers in real-time.
Personalized feedback
Unlimited practice
Used by hundreds of successful candidates
Describe a situation where you had to explain a technical issue to a non-technical colleague. How did you ensure they understood the problem and the solution?
How to Answer
- 1
Identify the technical issue clearly and simply.
- 2
Use analogies or relatable examples to make concepts understandable.
- 3
Break the solution into easy-to-follow steps.
- 4
Ask questions to gauge their understanding.
- 5
Encourage them to ask for clarification if needed.
Example Answers
In a previous role, I had to explain a calibration issue with our instruments to a marketing colleague. I explained it by comparing it to how a car needs tuning to run smoothly. I then outlined the calibration steps in a checklist format and checked if they followed along, allowing them to ask questions as needed.
Give an example of when you had to learn a new tool or technology quickly to solve an instrument control related problem.
How to Answer
- 1
Identify a specific tool or technology relevant to instrument control.
- 2
Describe the problem that required quick learning of this tool.
- 3
Explain how you approached learning the tool under time pressure.
- 4
Mention the outcome and how it improved the situation.
- 5
Emphasize your adaptability and ability to learn quickly.
Example Answers
In my previous role, we faced a sudden failure in our PLC system. I had to learn how to use a new HMI software quickly to diagnose the issue. I watched tutorial videos and consulted the manual within a few hours. By doing so, I was able to troubleshoot the problem effectively and restore operations within a day, minimizing downtime.
Was there a project where you had to take the lead in troubleshooting or upgrading an instrument control system? How did you handle it and what was the outcome?
How to Answer
- 1
Select a specific project that highlights your leadership in troubleshooting or upgrading.
- 2
Describe the problem clearly and what steps you took to manage the situation.
- 3
Mention any tools or methodologies used during troubleshooting.
- 4
Highlight the outcome and what you learned from the experience.
- 5
Emphasize teamwork and how you communicated with others during the project.
Example Answers
In a recent project, our facility was experiencing frequent shutdowns due to faulty flow meters. I led a team to troubleshoot the issue by firstly mapping out the entire control network. We used diagnostic tools to identify the malfunctioning instruments. After replacing the defective parts and recalibrating the system, we achieved a 30% increase in efficiency, and there were no further shutdowns for six months. This experience taught me the importance of thorough investigation and clear communication.
Technical Interview Questions
What programming languages or tools are you proficient in for configuring PLCs and how do you typically use them for control systems?
How to Answer
- 1
List specific PLC programming languages like Ladder Logic, Structured Text, or Function Block Diagrams.
- 2
Mention any tools or software you have experience with, such as Siemens TIA Portal or Rockwell PLC Studio.
- 3
Explain how you use these languages and tools in real projects, giving brief examples.
- 4
Highlight your problem-solving skills and how programming has helped optimize control systems.
- 5
Keep your answer focused on practical applications rather than theoretical knowledge.
Example Answers
I am proficient in Ladder Logic and Structured Text for PLC programming. I use Siemens TIA Portal for developing control programs, which allows me to effectively set up automation systems for manufacturing. For example, I recently implemented a control system that improved the efficiency of our assembly line by 15%.
Can you explain the process you follow for calibrating instruments? What tools do you use and how do you ensure accuracy?
How to Answer
- 1
Start by outlining the step-by-step process you typically follow for calibration.
- 2
Mention specific tools you use for calibration.
- 3
Highlight any industry standards or guidelines you adhere to.
- 4
Discuss how you verify accuracy after calibration is complete.
- 5
Share any documentation or record-keeping practices you follow.
Example Answers
I start the calibration process by first checking the manufacturer's specifications for the instrument. I use a multimeter and calibration weights as tools. After adjusting the instrument, I verify its accuracy by comparing the readings with known standards. I document all results in a calibration log for future reference.
Don't Just Read Instrument Control Technician Questions - Practice Answering Them!
Reading helps, but actual practice is what gets you hired. Our AI feedback system helps you improve your Instrument Control Technician interview answers in real-time.
Personalized feedback
Unlimited practice
Used by hundreds of successful candidates
How do you approach PID tuning for a control loop? Can you describe the steps you take and any challenges you may encounter?
How to Answer
- 1
Start by clearly defining the control loop objectives and specifications.
- 2
Use a systematic approach like the Ziegler-Nichols method for initial tuning parameters.
- 3
Perform step tests to assess system response and adjust PID parameters.
- 4
Iterate on gains and observe system behavior to minimize overshoot and settling time.
- 5
Document the process and challenges faced for future reference and continuous improvement.
Example Answers
I begin by defining the control loop goals, such as desired response time and stability. Then, I apply the Ziegler-Nichols method to get initial PID values. I adjust the parameters by testing the response and iterating until I achieve the desired overshoot and settling time. Challenges often include unexpected system behavior which requires me to revisit my initial assumptions and tuning approach.
What experience do you have with safety integrated systems and how do you ensure compliance with safety standards in your work?
How to Answer
- 1
Highlight specific safety integrated systems you've worked with
- 2
Discuss the importance of safety standards in your role
- 3
Provide examples of processes you follow for compliance
- 4
Mention any certifications or training related to safety
- 5
Emphasize collaboration with safety teams or departments
Example Answers
In my previous role, I worked extensively with safety integrated systems like SIL (Safety Integrity Level) assessments. I ensured compliance by conducting regular checks and audits, and always staying updated on industry safety standards through continuing education.
What are the key considerations you take into account when designing an HMI for a control system?
How to Answer
- 1
Ensure user-friendliness with intuitive layout and navigation
- 2
Prioritize critical information for immediate visibility
- 3
Incorporate feedback mechanisms for user actions
- 4
Design for accessibility to accommodate all users
- 5
Test design with real users to gather feedback and improve
Example Answers
When designing an HMI, I focus on user-friendliness by creating an intuitive layout that minimizes clicks. I prioritize displaying critical alerts prominently and ensure that users receive immediate feedback from their actions. It's also essential to accommodate accessibility features for diverse users.
Describe your experience with SCADA systems. What have been the key challenges in setting up or maintaining SCADA systems?
How to Answer
- 1
Briefly explain your hands-on experience with SCADA systems.
- 2
Discuss specific projects where you implemented or maintained SCADA.
- 3
Highlight challenges you faced and how you addressed them.
- 4
Mention any relevant tools or software you are familiar with.
- 5
Conclude with the outcomes of your efforts in enhancing SCADA systems.
Example Answers
I have over three years of experience with SCADA systems, particularly using Wonderware and Siemens software. I worked on a project integrating SCADA with a water treatment plant. One challenge was ensuring real-time data accuracy; I resolved this by implementing regular calibration of sensors, leading to a 15% efficiency increase in monitoring.
Can you list some types of instruments you have worked with and how you typically interface them with control systems?
How to Answer
- 1
Identify the key types of instruments relevant to the position
- 2
Include specific examples such as pressure sensors, flow meters or temperature controllers
- 3
Explain the interfacing method, such as using 4-20 mA signals or digital communication protocols
- 4
Mention any specific control systems you have experience with
- 5
Be concise and focus on relevant technical experience.
Example Answers
I have worked with pressure transducers and flow meters, typically interfacing them with our control systems using 4-20 mA analog signals. This method allows for accurate readings that the PLC can interpret easily.
What networking protocols are commonly used in instrument control systems and what is your experience with them?
How to Answer
- 1
Identify key protocols like Modbus, Profibus, and Ethernet/IP.
- 2
Discuss specific projects or systems where you have applied these protocols.
- 3
Mention any troubleshooting experience you have with these protocols.
- 4
Highlight your understanding of protocol differences and their applications.
- 5
Be ready to explain how these protocols fit into control system architecture.
Example Answers
I have worked extensively with Modbus and Profibus in our process control systems. For example, I used Modbus RTU to communicate with PLCs in a water treatment facility, which improved our data acquisition times.
How would you approach diagnosing a network communication failure between a PLC and a SCADA system?
How to Answer
- 1
Start by checking physical connections and cables for damage.
- 2
Verify that the PLC and SCADA system have the correct IP configuration.
- 3
Use network diagnostic tools to test connectivity, like ping or traceroute.
- 4
Check for any error messages on the PLC or SCADA system.
- 5
Review the network switches and routers for traffic issues or device failures.
Example Answers
First, I would inspect the physical connections between the PLC and the SCADA system to ensure everything is securely connected and undamaged. Then, I would verify the IP settings on both devices to ensure they are on the same subnet and properly configured. Running a ping test would help confirm if the devices can communicate over the network. If everything seems fine, I'd investigate any error logs from the PLC or SCADA for additional insights.
What is your process for documenting changes or troubleshooting steps for future reference in control systems?
How to Answer
- 1
Create a standardized template for documentation to maintain consistency.
- 2
Use clear and concise language to describe changes and troubleshooting steps.
- 3
Incorporate diagrams or flowcharts when applicable to visualize processes.
- 4
Regularly review and update documentation to reflect current practices.
- 5
Ensure all team members have access to documentation and are trained on its use.
Example Answers
I use a standardized template for documenting changes which includes date, description, and impact. I also add diagrams for complex troubleshooting. This makes it easier for others to understand and helps maintain consistency.
Don't Just Read Instrument Control Technician Questions - Practice Answering Them!
Reading helps, but actual practice is what gets you hired. Our AI feedback system helps you improve your Instrument Control Technician interview answers in real-time.
Personalized feedback
Unlimited practice
Used by hundreds of successful candidates
Situational Interview Questions
Imagine you arrive at a facility and find that a vital instrument control system has failed, causing production to halt. What steps would you take to assess and rectify the situation?
How to Answer
- 1
Quickly identify the failed system and check for any error messages or alarms.
- 2
Communicate with relevant personnel to gather information about the failure.
- 3
Perform an immediate visual inspection of the hardware and wiring.
- 4
Use diagnostic tools to analyze the system and pinpoint the issue.
- 5
Implement a temporary workaround if needed and then plan for a permanent fix.
Example Answers
First, I would identify the failed system and check for error messages. Then, I would consult with the operators to understand the context of the failure. After that, I would inspect the hardware visually for any obvious issues before using diagnostic tools to isolate the problem. If possible, I would implement a temporary workaround to restore production while planning the permanent fix.
A client requests advice on setting up a preventive maintenance schedule for their control systems. How would you go about advising them?
How to Answer
- 1
Assess the current condition and age of the control systems
- 2
Identify critical components that require regular maintenance
- 3
Determine optimal maintenance frequency based on manufacturer guidelines and operational demands
- 4
Consider integrating automation tools for scheduling and tracking maintenance
- 5
Develop a checklist and document results from each maintenance session
Example Answers
I would start by reviewing the existing control systems to understand their condition and age. Then, I'd identify which components are critical and their maintenance requirements. Based on that, I'd suggest a schedule that aligns with manufacturer recommendations and the client's operational needs.
Don't Just Read Instrument Control Technician Questions - Practice Answering Them!
Reading helps, but actual practice is what gets you hired. Our AI feedback system helps you improve your Instrument Control Technician interview answers in real-time.
Personalized feedback
Unlimited practice
Used by hundreds of successful candidates
You're tasked with integrating a new instrument control system but there is disagreement between engineering and operations on its configuration. How do you handle this conflict?
How to Answer
- 1
Identify the key concerns of both engineering and operations teams.
- 2
Facilitate a meeting to discuss the differences and seek common ground.
- 3
Encourage collaboration by highlighting the goals of the integration.
- 4
Gather data to support decisions and address any misunderstandings.
- 5
Be open to compromise and develop a configuration that satisfies both sides.
Example Answers
I would first meet with both teams to understand their concerns. By facilitating an open discussion, we can find common ground and address misunderstandings. I would aim to highlight how the integration serves our shared goals, and I’d back our approaches with data to aid in decision-making.
If you are given a project to improve the efficiency of an existing control system, how would you go about identifying potential improvements?
How to Answer
- 1
Analyze existing system performance data to identify bottlenecks.
- 2
Engage with operators and engineers to gather insights on recurring issues.
- 3
Review control system architecture and documentation for optimization opportunities.
- 4
Benchmark against industry standards and best practices for control systems.
- 5
Develop a list of potential upgrades, considering both hardware and software.
Example Answers
I would start by analyzing performance data from the system logs to identify any inefficiencies or bottlenecks. Next, I would interview operators to understand their challenges, as they often have valuable insights. After that, I would review the control system's architecture to see if there are outdated components that could be improved or optimized. I would also compare our system to industry standards to identify areas for enhancements.
Describe how you would respond to a fire alarm that has been triggered by a faulty sensor in the control system.
How to Answer
- 1
Stay calm and assess the situation quickly.
- 2
Confirm the fire alarm status with the control panel.
- 3
Follow emergency evacuation procedures if necessary.
- 4
Communicate with your supervisor and emergency responders.
- 5
Investigate the sensor issue and document everything for future reference.
Example Answers
First, I would ensure everyone's safety by confirming the evacuation procedures are being followed. Then I would check the control panel to verify if the alarm is due to a faulty sensor. If so, I would inform my supervisor about the malfunction and together we could decide on the next steps, such as resetting the system or replacing the sensor.
You need to train junior technicians on new equipment. How would you structure this training to be most effective?
How to Answer
- 1
Start with an overview of the equipment and its importance to the operation.
- 2
Break down the training into hands-on sessions and theoretical lessons.
- 3
Encourage questions and provide clear answers during the training.
- 4
Use visual aids and demonstrations to enhance understanding.
- 5
Assess learning through practical tests or scenarios at the end.
Example Answers
I would begin the training with an overview of the equipment and its role in our processes. Then, I would split the training into practical demonstrations and theoretical lessons, allowing time for hands-on practice. I would encourage the junior technicians to ask questions throughout and utilize visual aids to clarify complex concepts. Finally, I would conduct a practical assessment to ensure they've understood the training material.
If a customer is unhappy with the performance of a newly installed system, how would you approach resolving their concerns?
How to Answer
- 1
Listen carefully to the customer's concerns without interrupting.
- 2
Ask open-ended questions to fully understand the issue.
- 3
Reassure the customer that their satisfaction is your priority.
- 4
Provide a clear plan for addressing the problem, including timelines.
- 5
Follow up to ensure the solution meets the customer's expectations.
Example Answers
I would first listen to the customer's concerns attentively and avoid interrupting them. After understanding the issue, I would ask clarifying questions to get specific details. Then, I would reassure them that their satisfaction is important to me and outline the steps I would take to resolve the issue, including a follow-up check-in.
In a project with limited resources, how would you prioritize tasks to ensure critical milestones are met?
How to Answer
- 1
Identify the critical milestones and their deadlines
- 2
Assess the tasks required to meet those milestones
- 3
Determine resource availability for each task
- 4
Rank tasks based on impact and urgency
- 5
Communicate priorities clearly to the team
Example Answers
I start by identifying the critical milestones and their deadlines. Then I list the tasks needed to meet those milestones and assess the available resources. I rank these tasks by their impact on the project, focusing on those that are most urgent to complete first. Finally, I ensure the team is aware of these priorities so we can work together effectively.
A new regulation requires changes in the control system's configuration. How would you ensure compliance while minimizing downtime?
How to Answer
- 1
Review the new regulation and identify specific changes needed.
- 2
Create a detailed plan for implementing the changes with timelines.
- 3
Schedule changes during off-peak hours to reduce impact.
- 4
Communicate with all stakeholders to prepare for the updates.
- 5
Test the updated system thoroughly before going live.
Example Answers
I would start by reviewing the new regulation to understand the requirements. Then, I would develop a detailed implementation plan and schedule downtime during off-peak hours. After making the changes, I would run tests to ensure everything complies before final deployment.
You are part of a multi-department team upgrading a plant's control system. How do you ensure smooth collaboration and communication across teams?
How to Answer
- 1
Establish clear communication channels early on
- 2
Schedule regular meetings to track progress and address issues
- 3
Encourage open dialogue and feedback among team members
- 4
Define roles and responsibilities to avoid confusion
- 5
Utilize collaboration tools to keep everyone updated
Example Answers
I would set up a shared communication platform to ensure everyone is on the same page and schedule weekly check-in meetings to discuss progress and any issues that arise.
Don't Just Read Instrument Control Technician Questions - Practice Answering Them!
Reading helps, but actual practice is what gets you hired. Our AI feedback system helps you improve your Instrument Control Technician interview answers in real-time.
Personalized feedback
Unlimited practice
Used by hundreds of successful candidates
Management asks you to reduce costs in the maintenance of control systems. What steps would you take to achieve this without compromising safety or efficiency?
How to Answer
- 1
Analyze current maintenance practices for inefficiencies.
- 2
Implement predictive maintenance technologies to prevent costly downtimes.
- 3
Train staff thoroughly to reduce errors and improve productivity.
- 4
Standardize spare parts inventory to decrease costs and simplify management.
- 5
Review vendor contracts for better pricing and negotiate terms.
Example Answers
I would start by reviewing our current maintenance schedules to identify any inefficiencies, then transition to predictive maintenance to avoid unexpected failures. Additionally, I’d ensure staff training is up-to-date to minimize mistakes.
How would you manage the implementation of a significant software upgrade on a live control system with minimal disruption?
How to Answer
- 1
Conduct a thorough risk assessment to identify potential issues.
- 2
Develop a step-by-step upgrade plan with timelines and milestones.
- 3
Schedule the upgrade during low-usage hours to minimize impact.
- 4
Implement rollback procedures in case the upgrade fails.
- 5
Train staff on new features before going live with the upgrade.
Example Answers
I would first perform a risk assessment to understand the impact of the upgrade. Then, I'd create a detailed plan that schedules the upgrade for a time with minimal activity, ensuring plenty of time for testing. Rollback procedures would also be in place if things don't go as expected.
You have multiple conflicting priorities on control system projects. How do you decide which tasks to focus on first?
How to Answer
- 1
Assess tasks based on their deadlines and urgency
- 2
Identify which tasks have the most significant impact on the project goals
- 3
Communicate with stakeholders to understand their priorities
- 4
Utilize a prioritization matrix to evaluate tasks
- 5
Stay flexible and ready to adjust priorities as new information arises
Example Answers
I prioritize tasks by first evaluating their deadlines. Critical tasks with impending due dates take precedence. Then, I review the impact of each task on overall project goals and adjust based on stakeholder feedback.
You are given a set of control system performance data showing irregularities. How would you analyze this data to identify the root cause?
How to Answer
- 1
Examine the data for patterns and trends over time
- 2
Use statistical analysis to identify outliers
- 3
Correlate performance issues with changes in system parameters
- 4
Consider environmental factors that might affect performance
- 5
Review historical data for similar occurrences
Example Answers
First, I would plot the data to visualize any trends or patterns. Then, I would perform statistical analysis to identify any outliers that could indicate specific issues. After that, I would correlate these irregularities with any operational changes to pinpoint the root cause.
If you have to work with a vendor to replace obsolete instruments in a control system, how would you ensure a seamless process from procurement to installation?
How to Answer
- 1
Define the specific requirements for the new instruments early.
- 2
Communicate clearly with the vendor about timeline and expectations.
- 3
Coordinate closely with installation teams for scheduling.
- 4
Conduct a thorough testing plan before going live.
- 5
Document every step for future reference and compliance.
Example Answers
I would start by defining the instrument specifications and requirements, ensuring they meet system needs. Then, I'd communicate a clear timeline and expectations to the vendor for procurement. Coordination with our installation team would be crucial to align on scheduling. Before taking the new instruments live, I would set up a testing phase to verify functionality, and document everything for compliance purposes.
Instrument Control Technician Position Details
Recommended Job Boards
These job boards are ranked by relevance for this position.
Related Positions
Ace Your Next Interview!
Practice with AI feedback & get hired faster
Personalized feedback
Used by hundreds of successful candidates
Ace Your Next Interview!
Practice with AI feedback & get hired faster
Personalized feedback
Used by hundreds of successful candidates