Top 28 Controls Technician Interview Questions and Answers [Updated 2025]
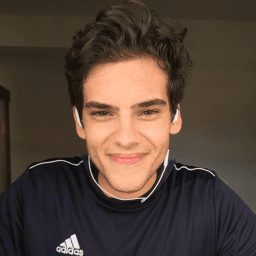
Andre Mendes
•
March 30, 2025
Preparing for a Controls Technician interview can be daunting, but with the right guidance, you can confidently tackle any question that comes your way. In this blog post, we delve into the most common interview questions for the Controls Technician role, providing you with insightful example answers and practical tips on how to respond effectively. Get ready to enhance your interview skills and impress potential employers!
Download Controls Technician Interview Questions in PDF
To make your preparation even more convenient, we've compiled all these top Controls Technicianinterview questions and answers into a handy PDF.
Click the button below to download the PDF and have easy access to these essential questions anytime, anywhere:
List of Controls Technician Interview Questions
Behavioral Interview Questions
Can you describe a time when you had to troubleshoot a complex control system issue? What was your approach and the outcome?
How to Answer
- 1
Start with a specific example from your experience
- 2
Outline the steps you took to identify the issue
- 3
Mention any tools or methods you used for troubleshooting
- 4
Discuss the final outcome and what you learned
- 5
Highlight how your actions impacted the project or system
Example Answers
In my last role, a production line went down due to a control system failure. I immediately analyzed the PLC logs to check for error codes. Using a multimeter, I verified the inputs and outputs. I found a faulty sensor and replaced it. The production was back on track within two hours, saving the team from significant downtime.
Tell me about a situation where you had to collaborate with multiple teams to complete a project. How did you ensure effective communication?
How to Answer
- 1
Select a specific project that involved collaboration across teams
- 2
Highlight your role and the teams you worked with
- 3
Discuss communication methods used, like regular meetings or updates
- 4
Mention any challenges faced and how you overcame them
- 5
Explain the positive outcome and lessons learned
Example Answers
In a recent automation project, I worked with the software and maintenance teams. I set up weekly update meetings to track progress and used a shared document to record issues. When we faced a delay in software development, I facilitated additional discussions to address concerns, leading to timely resolution. The project was completed on schedule, enhancing our production efficiency.
Don't Just Read Controls Technician Questions - Practice Answering Them!
Reading helps, but actual practice is what gets you hired. Our AI feedback system helps you improve your Controls Technician interview answers in real-time.
Personalized feedback
Unlimited practice
Used by hundreds of successful candidates
Describe an instance when you had to quickly learn and adapt to a new technology or control system. How did you manage?
How to Answer
- 1
Identify a specific technology or system you learned.
- 2
Briefly describe the context of the situation.
- 3
Explain steps taken to learn the new technology.
- 4
Highlight any resources or tools used during your learning process.
- 5
Share the outcome or impact of your adaptation on the project.
Example Answers
At my previous job, we needed to implement a new PLC system on short notice. I quickly reviewed technical manuals and online tutorials. I also reached out to a colleague experienced with the system for insights. Within a week, I successfully programmed and tested the PLC, which improved production efficiency by 20%.
Discuss a time when you had multiple control system projects to complete under tight deadlines. How did you prioritize your tasks?
How to Answer
- 1
Identify the projects you had and their deadlines.
- 2
Explain how you assessed the urgency and importance of each task.
- 3
Discuss any tools or methods you used for tracking progress.
- 4
Mention how you communicated with stakeholders about priorities.
- 5
Describe any adjustments you made to stay on schedule.
Example Answers
In my previous role, I had three control system projects due within the same week. I listed the deadlines and evaluated their impacts on production. I decided to tackle the most critical project first, using a project management tool to track my progress and communicate with my team about any shifts in priorities. This method ensured that I met all deadlines without compromising quality.
Have you ever had to lead a team through a technical challenge? What strategies did you use to guide your team?
How to Answer
- 1
Describe the specific technical challenge clearly and briefly.
- 2
Explain your role in leading the team and the methods you used.
- 3
Mention how you encouraged collaboration and communication.
- 4
Highlight any tools or techniques you implemented to solve the issue.
- 5
Conclude with the outcome and any lessons learned.
Example Answers
In my previous role, our team faced a major issue with automation failures. I organized daily stand-up meetings to ensure everyone was aligned. I utilized a root cause analysis tool which helped us pinpoint the problem quickly. The team’s collaboration led to a successful implementation of a new control strategy, resolving the issue within a week.
Can you provide an example of how you have used feedback from your peers or supervisors to improve your work as a Controls Technician?
How to Answer
- 1
Choose a specific project or task.
- 2
Mention the type of feedback received.
- 3
Explain how you implemented the feedback.
- 4
Highlight the positive outcome of the change.
- 5
Keep the example relevant to Controls Technician duties.
Example Answers
In a recent project, I received feedback from my supervisor that the control panel design could be more user-friendly. I took that feedback to heart and redesigned the layout, simplifying access to critical components. This change reduced troubleshooting time by 30% during maintenance.
Tell me about a time when you implemented a new technology or method in your work as a Controls Technician. What was the impact?
How to Answer
- 1
Choose a specific technology or method you implemented
- 2
Explain the reason for implementing it and the problem it addressed
- 3
Describe your role in the implementation process
- 4
Highlight the outcome and how it benefited the team or company
- 5
Use metrics or specific examples to quantify the impact if possible
Example Answers
In my last job, I implemented a new PLC programming method that reduced troubleshooting time by 30%. I identified that the existing method was inefficient, so I researched and proposed a shift to a modular approach. I led training sessions for the team, and we saw a significant decrease in downtime on our assembly line.
Describe a time when you had to explain a complex technical concept to a non-technical audience. How did you ensure understanding?
How to Answer
- 1
Identify the technical concept and its relevance.
- 2
Break down the concept into simple terms and relatable examples.
- 3
Use visuals or analogies to clarify points.
- 4
Encourage questions throughout the explanation.
- 5
Summarize key points to reinforce understanding.
Example Answers
In my previous role, I needed to explain PLC programming to a team of operators. I used everyday language, compared the PLC functions to a traffic light system, and provided a visual diagram. I encouraged them to ask questions, which helped me address their specific concerns. In the end, they felt confident in understanding the basics.
Technical Interview Questions
What experience do you have with PLC programming languages such as Ladder Logic or Structured Text? Can you provide an example of a project where you used them?
How to Answer
- 1
Identify specific PLC programming languages you have used.
- 2
Choose a relevant project that showcases your skills.
- 3
Explain your role and the outcomes of the project.
- 4
Mention any specific challenges you faced and how you overcame them.
- 5
Keep your response focused and clear.
Example Answers
I have experience with Ladder Logic, which I used in a project to automate a packaging line. My role was to design the control program, and I successfully reduced cycle time by 15%. I faced an issue with timing errors, but I resolved it by adjusting the timing parameters in the logic.
Explain the difference between open-loop and closed-loop control systems. Can you give an example of each?
How to Answer
- 1
Define both types of control systems clearly.
- 2
Highlight key characteristics that differentiate them.
- 3
Use specific and relatable examples for clarity.
- 4
Keep the explanation concise and straightforward.
- 5
Consider using a real-world scenario or application.
Example Answers
An open-loop control system operates without feedback, meaning it does not adjust based on the output. For example, a toaster is open-loop; it heats for a set time regardless of toast color. A closed-loop system uses feedback to correct its actions. A thermostat is a closed-loop system; it adjusts heating based on the current room temperature.
Don't Just Read Controls Technician Questions - Practice Answering Them!
Reading helps, but actual practice is what gets you hired. Our AI feedback system helps you improve your Controls Technician interview answers in real-time.
Personalized feedback
Unlimited practice
Used by hundreds of successful candidates
What types of sensors are you familiar with, and how do they integrate into control systems?
How to Answer
- 1
Identify common types of sensors like temperature, pressure, and flow sensors.
- 2
Explain how each sensor type collects data and sends it to a control system.
- 3
Mention the role of sensors in feedback loops for system control.
- 4
Discuss integration methods, such as analog vs. digital signals.
- 5
Provide examples of where you've used these sensors in previous projects.
Example Answers
I am familiar with temperature sensors like thermocouples and RTDs. They collect temperature data and send it as an analog signal to the control system, which uses this information for feedback loops in heating processes.
How do you approach diagnosing a failure in an automated control system? What tools and techniques do you use?
How to Answer
- 1
Begin with gathering data from system logs to identify error messages.
- 2
Use visual inspection to check for obvious physical issues like damaged wiring or components.
- 3
Employ diagnostic tools like multimeters and oscilloscopes to measure electrical signals.
- 4
Simulate the system in a safe environment to replicate the issue if possible.
- 5
Document findings and systematically test each component to isolate the fault.
Example Answers
I start by checking the system logs for error messages that indicate where the failure may have occurred. Then, I conduct a visual inspection for any visible damage. Using tools like a multimeter, I measure the signals to pinpoint the issue before testing individual components.
What is your experience with Human-Machine Interface (HMI) development, and how do you ensure it meets user requirements?
How to Answer
- 1
Highlight specific HMI software tools you've used.
- 2
Discuss a project where you gathered user feedback.
- 3
Mention how you verify usability and functionality.
- 4
Explain your process for iterative design.
- 5
Include any relevant training or certifications.
Example Answers
I have developed HMIs using Wonderware and Siemens software. In a recent project, I conducted user interviews to gather requirements, ensuring the final design included intuitive navigation features. I also ran usability tests to verify that the interface met user expectations before final deployment.
What networking protocols are commonly used in control systems, and why are they important?
How to Answer
- 1
Identify key protocols like Modbus, EtherNet/IP, and Profibus.
- 2
Explain their roles in communication between devices.
- 3
Mention their impact on performance and reliability.
- 4
Discuss the importance of compatibility and industry standards.
- 5
Keep answers concise and focused on practical applications.
Example Answers
Common protocols in control systems include Modbus for its simplicity and EtherNet/IP for high-speed communication. These protocols are vital for ensuring reliable data exchange between devices and maintaining system efficiency.
Describe your experience with integrating various control systems. What challenges did you face?
How to Answer
- 1
Start with a brief overview of your relevant experience in control systems integration.
- 2
Mention specific types of control systems you have integrated, like PLCs or SCADA.
- 3
Highlight a key challenge, explain how you addressed it, and what you learned.
- 4
Use metrics or outcomes to show the success of your integration efforts.
- 5
Demonstrate adaptability and problem-solving skills in your examples.
Example Answers
In my previous position, I integrated PLCs and SCADA systems in a manufacturing plant. A challenge I faced was syncing data between legacy and modern systems, which I addressed by developing a custom middleware solution. This improved data accuracy by 30%, and I learned the importance of thorough testing.
How do you utilize data analysis in your role to improve control system performance?
How to Answer
- 1
Identify key performance indicators for control systems
- 2
Use software tools to collect and analyze real-time data
- 3
Perform trend analysis to identify patterns over time
- 4
Implement data-driven adjustments to optimize performance
- 5
Collaborate with team members to validate analysis results
Example Answers
I track key performance indicators like response time and error rates using software tools. By analyzing real-time data, I identify any performance dips and adjust control parameters accordingly.
Explain the importance of documentation in control systems and your approach to maintaining it.
How to Answer
- 1
Highlight that documentation ensures system reliability and consistency.
- 2
Mention how it aids in troubleshooting and maintenance.
- 3
Emphasize collaboration, as it helps teams understand system design and changes.
- 4
Discuss the need for regular updates to reflect any modifications.
- 5
Include examples of tools or methods used for effective documentation.
Example Answers
Documentation is crucial because it guarantees the reliability of control systems. It helps troubleshoot issues quickly and allows others to understand modifications. I maintain it by regularly updating the system logs and using software like AutoCAD for diagrams.
What types of control algorithms are you familiar with, and can you describe a situation where you implemented one?
How to Answer
- 1
Identify key control algorithms you know like PID, Fuzzy Logic, and Predictive Control.
- 2
Select a specific project to discuss that highlights your experience.
- 3
Explain the problem you faced and why you chose a particular algorithm.
- 4
Describe the implementation process clearly, focusing on steps taken.
- 5
Mention the outcome and any improvements seen after implementation.
Example Answers
I am familiar with PID and Fuzzy Logic control algorithms. In a recent project, we needed to stabilize a temperature system. I implemented a PID controller to adjust heating elements. After tuning the parameters, the system responded quickly and maintained temperature within a 1-degree range, significantly improving product quality.
Don't Just Read Controls Technician Questions - Practice Answering Them!
Reading helps, but actual practice is what gets you hired. Our AI feedback system helps you improve your Controls Technician interview answers in real-time.
Personalized feedback
Unlimited practice
Used by hundreds of successful candidates
Situational Interview Questions
If you discovered that a component in a control system was incorrectly specified, how would you handle the situation with your client and your team?
How to Answer
- 1
Acknowledge the mistake promptly with both client and team.
- 2
Assess the impact of the incorrect specification on the project.
- 3
Propose a solution or alternative for the issue identified.
- 4
Communicate transparently and maintain trust with all stakeholders.
- 5
Document the issue and solution for future reference and learning.
Example Answers
I would immediately inform both my team and the client about the incorrect specification, explaining the potential impact. Then, I’d suggest a suitable alternative component that meets the requirements and organize a meeting to discuss the changes.
Suppose you are working on a control system, and during the implementation phase, you realize that the original plan is insufficient. What steps would you take to address this?
How to Answer
- 1
Assess the specific limitations of the original plan
- 2
Gather input from team members and stakeholders
- 3
Develop alternative solutions or adjustments to the plan
- 4
Implement changes incrementally and test each adjustment
- 5
Document the process and communicate changes clearly to all stakeholders
Example Answers
I would first identify the areas where the plan is lacking. Then, I'd consult with my team to gather diverse perspectives. After that, I'd propose new strategies, implement them step-by-step, and ensure everyone is updated on the changes.
Don't Just Read Controls Technician Questions - Practice Answering Them!
Reading helps, but actual practice is what gets you hired. Our AI feedback system helps you improve your Controls Technician interview answers in real-time.
Personalized feedback
Unlimited practice
Used by hundreds of successful candidates
Imagine you are assigned to support two different projects with conflicting deadlines. How would you manage your workload?
How to Answer
- 1
Assess the priorities of each project based on deadlines and importance
- 2
Communicate with stakeholders to set clear expectations and deadlines
- 3
Break down tasks into smaller, manageable chunks for each project
- 4
Use a project management tool to visualize your workload and deadlines
- 5
Allocate specific blocks of time in your calendar dedicated to each project
Example Answers
I would first review the priorities and deadlines of both projects. Then, I'd communicate with my team to clarify expectations. I'd break down my tasks into manageable pieces and schedule specific times to work on each project, ensuring I stay on track.
If you encounter a safety issue while working on a control system, what would your immediate response be?
How to Answer
- 1
Assess the situation quickly to determine the level of risk
- 2
Immediately stop any work that could exacerbate the issue
- 3
Inform all team members and relevant management about the situation
- 4
Follow established safety protocols or procedures for such incidents
- 5
Document the issue for future reference and preventive measures
Example Answers
I would first assess the situation to gauge the risk level. Safety comes first, so I would stop any ongoing work and alert my team and supervisors. Then, I would follow the safety protocols in place, ensuring everyone is safe.
You notice that a particular control process is inefficient. What strategies would you propose to improve it?
How to Answer
- 1
Analyze data to identify bottlenecks or issues
- 2
Engage with team members to gather insights
- 3
Research best practices in similar processes
- 4
Propose automation or optimization tools and techniques
- 5
Implement a pilot program to test the changes
Example Answers
I would start by reviewing performance data to identify the specific areas where the process is lagging. Then, I would discuss with my team to understand their perspectives and any challenges they face. Based on collective insights and research, I might suggest introducing automation tools to streamline repetitive tasks and propose a pilot program to monitor the improvements.
You are leading a project that has fallen behind schedule. What actions would you take to get it back on track?
How to Answer
- 1
Assess the current project status and identify specific delays.
- 2
Prioritize tasks based on urgency and impact on the project timeline.
- 3
Communicate openly with the team and stakeholders about challenges.
- 4
Reassign resources or adjust timelines if necessary.
- 5
Implement a daily check-in to monitor progress and address issues quickly.
Example Answers
I would evaluate the project status to pinpoint delays, then prioritize critical tasks to regain momentum. Clear communication with my team and stakeholders would ensure everyone is aligned.
If a client requests changes to a control system after it has been finalized, how would you handle their requests?
How to Answer
- 1
Acknowledge the client's request and show understanding of their needs
- 2
Assess the impact of the changes on the existing system and schedule
- 3
Communicate clearly about any potential costs and timeline adjustments
- 4
Involve relevant team members to provide input and ensure feasibility
- 5
Document all changes and agreements to maintain clarity
Example Answers
I would first acknowledge the client's request, showing that I understand their concerns. Then, I would assess how the changes affect the current system and discuss any implications on costs and timeline. I would collaborate with the team to ensure we meet the client's needs effectively before documenting the adjustments in our project records.
If you were asked to implement a change that you believe could potentially compromise system integrity, how would you respond?
How to Answer
- 1
Acknowledge the importance of system integrity.
- 2
Explain your need for thorough assessment before proceeding.
- 3
Discuss potential risks and impacts of the change.
- 4
Suggest collaboration with team members or stakeholders.
- 5
Offer to propose alternative solutions that maintain integrity.
Example Answers
I would first assess the change's potential risks to system integrity. I would then discuss my concerns with the team and gather input to ensure we consider all perspectives. If necessary, I would propose an alternative solution that achieves the goal without compromising integrity.
If you were given the task of upgrading an outdated control system, what steps would you take to ensure a smooth transition?
How to Answer
- 1
Assess the current system's capabilities and limitations before planning the upgrade
- 2
Engage stakeholders to gather requirements and expectations for the new system
- 3
Develop a detailed project plan that includes timelines and resource allocation
- 4
Implement the new system in phases to minimize disruption and allow for testing
- 5
Provide training and support to staff after implementation to ensure user adoption
Example Answers
First, I would evaluate the existing system to understand its strengths and weaknesses. Then, I would consult with key stakeholders to determine their needs. Once I have that information, I would create a project plan outlining the upgrade timeline and necessary resources. I believe in a phased approach, so I would implement the new system step-by-step to ensure everything works correctly before full deployment. Finally, I would offer training sessions to staff to help them transition smoothly to the new system.
Controls Technician Position Details
Salary Information
Recommended Job Boards
CareerBuilder
www.careerbuilder.com/jobs/controls-technicianZipRecruiter
www.ziprecruiter.com/Jobs/Controls-TechnicianThese job boards are ranked by relevance for this position.
Related Positions
Ace Your Next Interview!
Practice with AI feedback & get hired faster
Personalized feedback
Used by hundreds of successful candidates
Ace Your Next Interview!
Practice with AI feedback & get hired faster
Personalized feedback
Used by hundreds of successful candidates