Top 31 Equipment Specialist Interview Questions and Answers [Updated 2025]
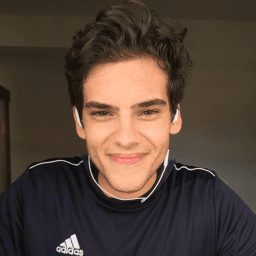
Andre Mendes
•
March 30, 2025
Preparing for an Equipment Specialist interview can be daunting, but we've got you covered! In this blog post, we delve into the most common interview questions for this role, providing you with example answers and expert tips on how to respond effectively. Whether you're a seasoned professional or a newcomer, this guide will help you confidently navigate your next interview and make a lasting impression.
Download Equipment Specialist Interview Questions in PDF
To make your preparation even more convenient, we've compiled all these top Equipment Specialistinterview questions and answers into a handy PDF.
Click the button below to download the PDF and have easy access to these essential questions anytime, anywhere:
List of Equipment Specialist Interview Questions
Behavioral Interview Questions
Can you describe a time when you successfully collaborated with a team to resolve an equipment malfunction?
How to Answer
- 1
Identify a specific malfunction incident you faced.
- 2
Explain your role in the collaboration process.
- 3
Highlight the team members involved and their contributions.
- 4
Describe the steps taken to resolve the issue.
- 5
Share the outcome and what you learned from the experience.
Example Answers
During a production line breakdown, I worked with our maintenance team to diagnose the issue. I coordinated with operators to gather data on the malfunction, and we quickly identified a faulty sensor. Together, we replaced the sensor, tested the equipment, and restored operations within an hour, minimizing downtime.
Tell me about a challenging equipment issue you faced and how you approached solving it.
How to Answer
- 1
Choose a specific equipment issue that had a significant impact.
- 2
Explain the steps you took to diagnose the issue accurately.
- 3
Highlight the solutions you implemented and any collaboration involved.
- 4
Discuss the outcome and what you learned from the experience.
- 5
Keep your answer structured: Situation, Task, Action, Result.
Example Answers
In my previous role, we faced frequent breakdowns of a critical conveyor system. I first gathered data on the failures and consulted with the technicians to identify patterns. After diagnosing it was a lubrication issue, I restructured the maintenance schedule and trained the staff on proper lubricating techniques. This resulted in a 30% decrease in downtime over the next quarter.
Don't Just Read Equipment Specialist Questions - Practice Answering Them!
Reading helps, but actual practice is what gets you hired. Our AI feedback system helps you improve your Equipment Specialist interview answers in real-time.
Personalized feedback
Unlimited practice
Used by hundreds of successful candidates
Describe an instance where you had to lead a team while managing equipment procurement.
How to Answer
- 1
Choose a specific project to highlight your experience.
- 2
Explain your role and responsibilities clearly.
- 3
Focus on the challenges you faced and how you overcame them.
- 4
Mention the outcome and what you learned from the experience.
- 5
Emphasize teamwork and collaboration throughout the process.
Example Answers
In my previous role, I led a team to procure new machinery for a production line. We faced budget constraints, so I organized brainstorming sessions to identify cost-effective options. By collaborating closely with suppliers, we negotiated better prices and secured necessary equipment under budget, enhancing production efficiency by 20%.
Give an example of how you effectively communicated complex technical information to non-technical stakeholders.
How to Answer
- 1
Identify a specific situation where you communicated technical info.
- 2
Use simple language and avoid jargon during your explanation.
- 3
Highlight the tools or methods you used to facilitate understanding.
- 4
Emphasize the outcome or impact of your communication.
- 5
Prepare to describe how you tailored your message to your audience.
Example Answers
In a recent project, I explained a new software system to the sales team. I used visual aids like flowcharts and kept the language simple. As a result, the team felt confident in using the system, which improved their productivity by 20%.
Explain a situation where you had to adapt quickly to changes in equipment specifications or technology.
How to Answer
- 1
Identify a specific instance where equipment specifications changed.
- 2
Describe the initial reaction and how you assessed the new requirements.
- 3
Explain the steps you took to adapt, including any collaborations or learning processes.
- 4
Highlight the positive outcome of your adaptability.
- 5
Mention any skills or knowledge gained that apply to future scenarios.
Example Answers
In my previous job, our team was informed of a software update for our machining equipment that altered the programming interface. I immediately studied the updated user manual and arranged a quick team meeting to discuss the changes. We collaboratively practiced the new programming methods, which allowed us to complete a project ahead of schedule and improve our overall efficiency.
Have you ever implemented a new technology or process that improved equipment performance? Please describe.
How to Answer
- 1
Identify the technology or process you implemented.
- 2
Explain the problem it addressed or the performance issue.
- 3
Describe the implementation steps you took.
- 4
Quantify the results or improvements achieved.
- 5
Reflect on any lessons learned from the experience.
Example Answers
In my previous role, I implemented a predictive maintenance software that analyzed equipment data. This addressed frequent breakdowns, leading to a 30% reduction in downtime within six months. I trained the team on the software, ensuring smooth adoption and continuous monitoring for further improvements.
Can you discuss a time you used performance metrics to improve equipment efficiency?
How to Answer
- 1
Identify a specific instance where you analyzed performance metrics.
- 2
Explain the metrics you used and why they were relevant.
- 3
Discuss the steps you took to improve equipment efficiency based on the data.
- 4
Highlight the results achieved after implementing your changes.
- 5
Emphasize any teamwork or collaboration involved in the process.
Example Answers
In my last role, I noticed that our conveyor system was frequently experiencing downtime. I analyzed the performance metrics, focusing on average downtime per week and reasons for stoppages. By implementing a scheduled maintenance plan based on these findings, we reduced downtime by 30% over three months.
Describe how you handle feedback from team members regarding equipment issues.
How to Answer
- 1
Listen actively to understand the feedback clearly
- 2
Acknowledge the team's input and express appreciation
- 3
Assess the validity of the feedback by reviewing the issue
- 4
Collaborate with the team to find a solution
- 5
Follow up to ensure the issue has been resolved and gather further feedback
Example Answers
I start by listening carefully to my team's feedback to fully understand the equipment issue. I thank them for bringing it to my attention and then review the problem to assess its validity. Together, we brainstorm potential solutions, and I ensure to follow up afterward to confirm that the issue was resolved.
Don't Just Read Equipment Specialist Questions - Practice Answering Them!
Reading helps, but actual practice is what gets you hired. Our AI feedback system helps you improve your Equipment Specialist interview answers in real-time.
Personalized feedback
Unlimited practice
Used by hundreds of successful candidates
Can you describe any professional development activities you have pursued to enhance your equipment expertise?
How to Answer
- 1
Identify specific courses or certifications related to equipment management or operation.
- 2
Mention any hands-on training experiences or workshops attended.
- 3
Highlight participation in industry conferences or networking events.
- 4
Discuss any relevant reading materials, such as manuals or industry publications.
- 5
Explain how these activities have directly improved your skills or knowledge.
Example Answers
I completed a certification course in equipment management that covered best practices in maintenance and operation. Additionally, I attended a workshop on advanced diagnostic techniques, which helped me troubleshoot issues more effectively.
Technical Interview Questions
What types of equipment are you most experienced with, and how do you stay updated on industry trends?
How to Answer
- 1
Identify specific equipment relevant to the position.
- 2
Mention any certifications or training you have.
- 3
Explain how you engage with industry publications or online communities.
- 4
Include any experience with new technology or innovations.
- 5
Discuss networking with professionals in the field.
Example Answers
I have extensive experience with heavy machinery such as excavators and forklifts, and I've completed certification programs for both. I regularly read industry magazines like Equipment World and participate in online forums to keep up with trends.
Can you explain the standard procedures for maintaining critical equipment?
How to Answer
- 1
Identify equipment types and their specific maintenance requirements
- 2
Schedule regular inspections to check for wear and tear
- 3
Follow the manufacturer's maintenance guidelines and best practices
- 4
Keep detailed records of maintenance tasks and any issues encountered
- 5
Train staff on proper use and maintenance protocols
Example Answers
For critical equipment, I prioritize understanding the maintenance manual. I schedule routine inspections monthly to catch any issues early, ensuring compliance with manufacturer guidelines while tracking all maintenance in a log.
Don't Just Read Equipment Specialist Questions - Practice Answering Them!
Reading helps, but actual practice is what gets you hired. Our AI feedback system helps you improve your Equipment Specialist interview answers in real-time.
Personalized feedback
Unlimited practice
Used by hundreds of successful candidates
What safety protocols do you follow when operating and maintaining equipment?
How to Answer
- 1
Always perform a pre-operation inspection for any visible issues.
- 2
Ensure all protective gear is worn according to equipment requirements.
- 3
Follow manufacturer guidelines for operation and maintenance.
- 4
Document any incidents or near misses to improve safety protocols.
- 5
Engage in regular training or refreshers on safety procedures.
Example Answers
I conduct a pre-operation inspection to check for any potential hazards and wear the necessary protective gear. I strictly follow the manufacturer's guidelines to ensure safe operation.
Describe your process for diagnosing equipment failures.
How to Answer
- 1
Start by gathering data on the equipment's performance history.
- 2
Inspect the equipment visually for obvious signs of failure or wear.
- 3
Utilize diagnostic tools and software to identify error codes or issues.
- 4
Consult technical manuals and schematics to understand normal operation.
- 5
Test components systematically to isolate the problem.
Example Answers
I begin by reviewing the equipment's maintenance logs and any error codes. Then I perform a visual inspection for any obvious issues. If needed, I use diagnostic software to pinpoint the failure before testing individual components to confirm the diagnosis.
What regulations and compliance standards do you consider when selecting equipment?
How to Answer
- 1
Identify and mention industry-specific regulations such as OSHA or EPA.
- 2
Discuss adherence to local, state, and federal safety standards.
- 3
Highlight the importance of equipment certifications like CE, ISO, or UL.
- 4
Explain the significance of reviewing user manuals and compliance documentation.
- 5
Consider environmental and sustainability regulations that may apply.
Example Answers
When selecting equipment, I focus on industry safety standards like OSHA, ensuring compliance with federal regulations. I also check for relevant certifications such as ISO 9001 and review the equipment's manual for compliance documentation.
What equipment testing procedures do you find most effective for ensuring equipment reliability?
How to Answer
- 1
Focus on the specific testing methods you have used.
- 2
Mention how you analyze the data collected from tests.
- 3
Discuss the importance of routine maintenance checks.
- 4
Include examples of adjustments made based on testing outcomes.
- 5
Highlight collaboration with other teams during the testing process.
Example Answers
I believe in using performance testing and stress testing as key methods. Analyzing test data helps identify trends early. Routine maintenance checks are vital to prevent unexpected failures.
What experience do you have with software used for monitoring and managing equipment?
How to Answer
- 1
Identify specific software you have used, such as CMMS or ERP systems.
- 2
Mention the types of equipment you monitored using these tools.
- 3
Explain how you utilized the software to improve efficiency or reduce downtime.
- 4
Share any relevant metrics or achievements resulting from your work with the software.
- 5
Be prepared to discuss troubleshooting or issues you resolved using the software.
Example Answers
I have experience using CMMS software like UpKeep to monitor HVAC systems. I regularly scheduled maintenance, which reduced downtime by 20%.
What specific troubleshooting techniques do you employ when addressing equipment malfunctions?
How to Answer
- 1
Identify the symptoms of the malfunction clearly
- 2
Refer to the equipment manual for troubleshooting steps
- 3
Isolate the problem by checking one component at a time
- 4
Use diagnostic tools like multimeters or software for deeper analysis
- 5
Document findings and steps taken for future reference
Example Answers
I start by identifying the symptoms of the issue, then consult the equipment manual for specific troubleshooting steps. I isolate the problem by checking one component at a time and use diagnostic tools to analyze the situation accurately.
What key factors do you consider when installing new equipment?
How to Answer
- 1
Assess the location and space requirements for the new equipment
- 2
Evaluate compatibility with existing systems and processes
- 3
Consider safety regulations and compliance standards
- 4
Plan for training and support for staff operating the equipment
- 5
Anticipate maintenance needs and availability of parts
Example Answers
I focus on ensuring the installation site has adequate space and utilities. I also check how the new equipment integrates with our current systems and confirm compliance with all safety regulations.
How do you collaborate with engineers to ensure that equipment meets operational requirements?
How to Answer
- 1
Establish clear communication channels from the start.
- 2
Involve engineers early in the equipment selection process.
- 3
Organize regular meetings to review equipment performance and requirements.
- 4
Use data and feedback to inform design choices.
- 5
Promote a team-oriented mindset to encourage idea sharing.
Example Answers
I set up regular meetings with engineers to discuss equipment specs and operational needs. This ensures everyone is aligned and can address potential issues early.
Don't Just Read Equipment Specialist Questions - Practice Answering Them!
Reading helps, but actual practice is what gets you hired. Our AI feedback system helps you improve your Equipment Specialist interview answers in real-time.
Personalized feedback
Unlimited practice
Used by hundreds of successful candidates
Situational Interview Questions
If you were presented with a new type of equipment that has not been tested in your environment, how would you proceed?
How to Answer
- 1
Research the equipment specifications and capabilities.
- 2
Consult with manufacturers for user manuals and support.
- 3
Draft a plan for initial testing with clear objectives and metrics.
- 4
Involve relevant team members for diverse insights and expertise.
- 5
Document findings throughout the testing process.
Example Answers
I would start by researching the equipment specifications and consulting the manufacturer for any available documentation. Then, I'd draft a testing plan with specific benchmarks and involve the relevant team members for broader insights.
Imagine you have a limited budget for equipment upgrades. How would you prioritize your selections?
How to Answer
- 1
Assess current equipment performance and identify critical needs
- 2
Consider the impact of upgrades on overall productivity
- 3
Evaluate the return on investment for each potential upgrade
- 4
Prioritize upgrades that can enhance safety and compliance
- 5
Involve team members to understand usage and suggest improvements
Example Answers
I would start by reviewing the existing equipment and identifying which items are underperforming or failing to meet safety standards. Then, I would prioritize upgrades that promise the highest increase in productivity and that comply with safety regulations.
Don't Just Read Equipment Specialist Questions - Practice Answering Them!
Reading helps, but actual practice is what gets you hired. Our AI feedback system helps you improve your Equipment Specialist interview answers in real-time.
Personalized feedback
Unlimited practice
Used by hundreds of successful candidates
How would you train team members on the operation and maintenance of newly acquired equipment?
How to Answer
- 1
Assess the training needs of the team based on current skill levels
- 2
Develop a hands-on training program that includes demonstrations
- 3
Create easy-to-understand manuals or quick reference guides
- 4
Use feedback sessions to address questions and improve training
- 5
Schedule follow-up sessions to reinforce learning and assess progress
Example Answers
I would start by assessing my team's current knowledge and skills. Then, I'd organize hands-on training sessions to demonstrate the operation of the new equipment, supplemented by clear manuals to help them reference key points. I’d gather feedback after each session to ensure understanding.
What steps would you take if a piece of critical equipment failed during production?
How to Answer
- 1
Immediately assess the situation and gather information about the failure
- 2
Notify the relevant team members and management to initiate a response
- 3
Implement emergency protocols to minimize production loss
- 4
Coordinate with maintenance to diagnose and repair the equipment
- 5
Document the incident and analyze it to prevent future failures
Example Answers
First, I would quickly assess the failure and gather details about the equipment involved. Then, I would notify the team leader and relevant departments to address the situation promptly. We would execute our emergency protocols to reduce downtime, and I'd coordinate with maintenance for a swift repair. Finally, I would document the incident for future analysis.
You need to choose a new vendor for equipment supply. What criteria would you use to make this decision?
How to Answer
- 1
Evaluate vendor reputation and reliability in the industry
- 2
Consider cost-effectiveness and pricing transparency
- 3
Assess quality and durability of equipment offered
- 4
Check for customer support and after-sales service
- 5
Look into delivery timelines and supply chain stability
Example Answers
I would first assess the vendor's reputation by researching their history in the industry, then I would compare pricing to ensure it aligns with our budget while offering good value. Quality of equipment is crucial, so I would ask for samples or customer reviews. Customer support is essential, as timely assistance can prevent operational delays. Lastly, I would verify their delivery capabilities to avoid disruptions in our supply chain.
How would you manage a project involving the installation of new equipment while minimizing disruption to operations?
How to Answer
- 1
Conduct a thorough assessment of current operations and identify critical times for installation.
- 2
Engage with team members and gather input on potential impacts to their work.
- 3
Develop a detailed project plan with clear timelines to avoid peak operation hours.
- 4
Communicate regularly with all stakeholders about the installation process and schedule.
- 5
Establish a contingency plan to address unforeseen issues that may arise during installation.
Example Answers
I would first analyze our operational schedule to identify low-traffic times for installation, engaging with staff to understand their workflow. Then, I would create a detailed timeline that respects these periods and communicate it regularly to all involved.
If after analysis, you notice that multiple pieces of equipment are frequently failing, what steps would you take to determine the cause?
How to Answer
- 1
Collect failure data and identify common patterns across the equipment.
- 2
Inspect the equipment for any physical signs of wear or damage.
- 3
Review maintenance records to check for any missed service intervals.
- 4
Engage operators for insights on usage and operational conditions.
- 5
Consider environmental factors that may affect equipment performance.
Example Answers
I would first gather and analyze failure data to spot trends among the equipment. Then, I’d inspect the affected units for wear, review maintenance logs for missed services, and consult with operators to understand their usage patterns.
How would you assess whether to repair or replace aging equipment that is still in use?
How to Answer
- 1
Evaluate the current performance and reliability of the equipment.
- 2
Calculate the total cost of ownership comparing repair costs versus replacement costs.
- 3
Assess the technology and efficiency of new equipment.
- 4
Consider the impact on production and downtime during repair or replacement.
- 5
Obtain input from relevant stakeholders on preferences and experiences.
Example Answers
I would start by analyzing the performance of the aging equipment and identify any recurring issues. Then, I'd calculate repair costs versus the cost of a new unit while considering long-term efficiency gains. Finally, I'd consult with the team to factor in any downtime concerns before making a decision.
If new regulations affect your equipment usage, how would you approach ensuring compliance?
How to Answer
- 1
Stay informed about the new regulations and their implications for equipment usage
- 2
Conduct a thorough assessment of current equipment and procedures to identify gaps
- 3
Develop an action plan to modify operations or equipment as needed for compliance
- 4
Implement training sessions for staff on the new regulations and compliance measures
- 5
Regularly review and update practices to ensure ongoing compliance with any future changes
Example Answers
I would start by researching the new regulations to understand how they impact our current equipment. Next, I would assess our existing operations to find any compliance gaps and create an action plan to address them. Training our team on these updates would be crucial to ensure everyone is informed and compliant.
How would you leverage data from past equipment performance to inform future purchasing decisions?
How to Answer
- 1
Analyze historical performance data for equipment reliability and efficiency
- 2
Identify trends in maintenance costs and downtime for existing equipment
- 3
Use performance metrics to compare similar equipment options
- 4
Gather stakeholder feedback on previous equipment to understand user experience
- 5
Ensure alignment of equipment specifications with future operational needs
Example Answers
I would analyze the historical performance data to identify which equipment had the highest reliability and lowest maintenance costs. This would help in choosing options that are cost-effective and efficient.
Don't Just Read Equipment Specialist Questions - Practice Answering Them!
Reading helps, but actual practice is what gets you hired. Our AI feedback system helps you improve your Equipment Specialist interview answers in real-time.
Personalized feedback
Unlimited practice
Used by hundreds of successful candidates
Equipment Specialist Position Details
Salary Information
Recommended Job Boards
CareerBuilder
www.careerbuilder.com/jobs/equipment-specialistZipRecruiter
www.ziprecruiter.com/Jobs/Equipment-SpecialistThese job boards are ranked by relevance for this position.
Related Positions
Ace Your Next Interview!
Practice with AI feedback & get hired faster
Personalized feedback
Used by hundreds of successful candidates
Ace Your Next Interview!
Practice with AI feedback & get hired faster
Personalized feedback
Used by hundreds of successful candidates