Top 31 Process Control Technician Interview Questions and Answers [Updated 2025]
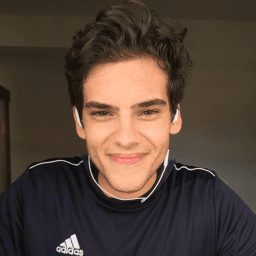
Andre Mendes
•
March 30, 2025
Are you preparing for a Process Control Technician interview and want to stand out from the crowd? This blog post is your go-to resource, featuring a collection of the most common interview questions for this role. Dive into example answers and insightful tips on how to respond effectively, ensuring you're ready to impress and secure that job. Let's get you interview-ready!
Download Process Control Technician Interview Questions in PDF
To make your preparation even more convenient, we've compiled all these top Process Control Technicianinterview questions and answers into a handy PDF.
Click the button below to download the PDF and have easy access to these essential questions anytime, anywhere:
List of Process Control Technician Interview Questions
Behavioral Interview Questions
Can you describe a time when you identified and resolved a critical process issue?
How to Answer
- 1
Use the STAR method: Situation, Task, Action, Result
- 2
Be specific about the issue you identified
- 3
Highlight the steps you took to resolve the problem
- 4
Quantify the impact of your actions if possible
- 5
Conclude with what you learned from the experience
Example Answers
In my previous role, I noticed a significant drop in the efficiency of our distillation process (Situation). My task was to identify the root cause of this inefficiency (Task). I conducted a series of tests and discovered a malfunctioning valve caused the issue (Action). After replacing the valve, efficiency improved by 20% (Result). This taught me the importance of regular equipment checks.
Tell me about a situation where you collaborated with engineers to improve a process.
How to Answer
- 1
Choose a specific project where collaboration occurred.
- 2
Describe your role and contributions clearly.
- 3
Focus on the outcome and any measurable results.
- 4
Highlight the importance of teamwork in the improvement.
- 5
Mention any tools or methods used to facilitate communication.
Example Answers
In my previous role, I worked with engineers on a project to reduce downtime in the assembly line. I suggested implementing a new control system that I had researched. By collaborating closely, we were able to decrease downtime by 25%, which significantly improved productivity.
Don't Just Read Process Control Technician Questions - Practice Answering Them!
Reading helps, but actual practice is what gets you hired. Our AI feedback system helps you improve your Process Control Technician interview answers in real-time.
Personalized feedback
Unlimited practice
Used by hundreds of successful candidates
Describe a time when you had to adapt to a change in process control technology.
How to Answer
- 1
Select a specific example where you faced a technology change.
- 2
Explain the context and urgency of the change.
- 3
Detail the steps you took to adapt to the new technology.
- 4
Highlight any training or resources you used.
- 5
Share the positive outcomes or improvements achieved.
Example Answers
In my previous role, our facility upgraded to a new DCS system. I quickly attended training sessions and collaborated with the IT team to learn the system. By creating a user guide for my colleagues, I helped ease the transition, resulting in a smoother implementation and improved operational efficiency.
Give an example of how you communicated a technical issue to non-technical team members.
How to Answer
- 1
Identify the technical issue clearly and simply.
- 2
Use analogies or relatable concepts to explain complex ideas.
- 3
Encourage questions to ensure understanding.
- 4
Summarize the impact of the issue in practical terms.
- 5
Offer a straightforward solution or next steps.
Example Answers
In a recent project, we had a sensor malfunction that caused inaccurate data readings. I explained to my team that it was like reading a faulty thermometer. I encouraged them to ask questions and summarized that this could lead to incorrect decisions. We decided on a plan to replace the sensor and test its accuracy.
Have you ever taken the lead on a project to enhance process efficiency? What was the outcome?
How to Answer
- 1
Choose a specific project where you led, detailing your role.
- 2
Highlight the problem you identified and your solution.
- 3
Discuss the tools or methods you used to implement changes.
- 4
Include measurable outcomes or improvements as a result.
- 5
Reflect on what you learned and how it impacted your team.
Example Answers
I led a project to reduce downtime in our production line by analyzing workflow bottlenecks. I implemented a new scheduling system that improved our efficiency by 20%. Our team was able to produce more within the same timeframe, saving costs and boosting morale.
Describe a conflict you had with a colleague regarding a process issue and how you resolved it.
How to Answer
- 1
Identify the specific process issue and your colleague's viewpoint.
- 2
Explain your feelings and thought process during the conflict.
- 3
Discuss how you approached the resolution, focus on communication.
- 4
Highlight the outcome and what you learned from the experience.
- 5
Emphasize teamwork and collaboration in resolving the issue.
Example Answers
I had a disagreement with a colleague about the best way to control a chemical reaction's temperature. I felt that using a PID controller was essential, while they preferred manual adjustments. We sat down, discussed each perspective, and reviewed data from previous operations. In the end, we decided to run a trial using both methods and analyzed the results together. This led to improved efficiency and stronger collaboration in our team.
Can you provide an example of how you have contributed to innovative process control solutions?
How to Answer
- 1
Identify a specific project where innovation was essential
- 2
Describe your role and the innovative approach you took
- 3
Highlight the measurable outcomes or improvements resulting from your solution
- 4
Use technical terms relevant to the industry to demonstrate expertise
- 5
Ensure your example showcases teamwork and collaboration if applicable
Example Answers
In my previous role, I worked on a project to automate temperature control in our processing unit. I developed a feedback loop system using advanced PID tuning, which reduced temperature fluctuations by 20%, resulting in improved product quality.
Describe a successful project in which you played a key role as a process control technician.
How to Answer
- 1
Choose a project that highlights your skills in process control.
- 2
Focus on your specific contributions and the impact they had.
- 3
Use metrics to demonstrate success, like efficiency improvement or cost reduction.
- 4
Mention any collaboration with team members or departments.
- 5
Conclude with what you learned and how it applies to future projects.
Example Answers
In a project to optimize a distillation column, I analyzed process data and adjusted the control parameters, leading to a 15% increase in yield and a 10% reduction in energy costs. I collaborated with the engineering team to implement these changes.
Technical Interview Questions
What programming languages and software tools are you proficient in for process control?
How to Answer
- 1
List specific programming languages you have experience with, such as PLC programming (Ladder Logic, Python).
- 2
Mention relevant software tools like SCADA systems, HMI software, or simulation tools.
- 3
Highlight any relevant certifications or training in these areas.
- 4
Provide examples of projects where you used these languages and tools.
- 5
Tailor your answer to match the job description and emphasize relevant skills.
Example Answers
I am proficient in Ladder Logic and Python for PLC programming, and I have experience with SCADA systems like Wonderware. In my last position, I automated a production line that improved efficiency by 20%.
Can you explain the difference between open-loop and closed-loop control systems?
How to Answer
- 1
Define open-loop control clearly with a simple example.
- 2
Define closed-loop control clearly with a simple example.
- 3
Highlight the key difference focusing on feedback presence.
- 4
Mention common applications for each type briefly.
- 5
Keep the explanation concise to ensure clarity.
Example Answers
An open-loop control system operates without feedback. For instance, a toaster operates on a timer, regardless of whether the bread is toasted or not. In contrast, a closed-loop control system uses feedback to adjust its output, like a thermostat that regulates temperature by adjusting heating or cooling based on the current room temperature.
Don't Just Read Process Control Technician Questions - Practice Answering Them!
Reading helps, but actual practice is what gets you hired. Our AI feedback system helps you improve your Process Control Technician interview answers in real-time.
Personalized feedback
Unlimited practice
Used by hundreds of successful candidates
What steps do you follow to troubleshoot a malfunctioning control system?
How to Answer
- 1
Identify the symptoms and document them clearly.
- 2
Check all inputs to the control system for accuracy.
- 3
Examine the system settings and configurations.
- 4
Test the output signals for any irregularities.
- 5
Consult documentation and collaborate with team members for insights.
Example Answers
I start by noting the symptoms of the malfunction, which helps me focus on the issue. Next, I verify all inputs to ensure they are correct. Then, I review the system settings and conduct output tests to identify where the failure occurs.
What types of sensors and instruments have you worked with in process control?
How to Answer
- 1
Identify specific types of sensors and instruments you have experience with
- 2
Mention their applications in process control settings
- 3
Highlight any relevant technical skills in calibration or maintenance
- 4
Include experiences with troubleshooting and problem-solving related to these devices
- 5
Relate your answers to the requirements of the Process Control Technician role
Example Answers
I have worked with temperature sensors such as thermocouples and RTDs in various applications, including monitoring reactor temperatures. I also have experience with pressure transducers for ensuring safe operating conditions in pipelines.
Are you familiar with any industry regulations that impact process control systems?
How to Answer
- 1
Research key regulations like OSHA, EPA, and ISO standards.
- 2
Mention how these regulations affect safety and efficiency in process control.
- 3
Discuss any specific experiences you have related to compliance.
- 4
Highlight your understanding of documentation and reporting requirements.
- 5
Be prepared to explain how you stay current with regulations.
Example Answers
Yes, I am familiar with OSHA regulations which ensure workplace safety and impact how we design and implement process control systems to prevent hazards.
How do you use data analytics in monitoring and optimizing process performance?
How to Answer
- 1
Identify key performance indicators relevant to the processes you oversee
- 2
Utilize software tools to collect and analyze process data effectively
- 3
Regularly review historical data to detect patterns or anomalies
- 4
Develop predictive models to anticipate performance issues before they arise
- 5
Collaborate with team members to interpret data findings and implement improvements
Example Answers
I focus on key performance indicators such as flow rates and temperature, using software like MATLAB to analyze real-time data. This helps identify any deviations from expected performance.
What experience do you have with process control software like SCADA or DCS?
How to Answer
- 1
Identify specific software you have used and the context.
- 2
Explain your role and responsibilities with the software.
- 3
Share a successful project or achievement related to process control.
- 4
Mention any training or certifications you have in SCADA or DCS.
- 5
Highlight how your experience improved efficiency or resolved an issue.
Example Answers
I have worked extensively with SCADA systems in my previous position at XYZ Manufacturing. I was responsible for monitoring real-time data and managing alarms, which improved our response time to issues by 30%.
What safety protocols do you follow when working with process control systems?
How to Answer
- 1
Always wear personal protective equipment appropriate for the environment.
- 2
Conduct a risk assessment before starting any task in the process control area.
- 3
Follow lockout/tagout procedures to ensure equipment is properly shut down during maintenance.
- 4
Be familiar with emergency shutdown procedures and safety data sheets for chemicals.
- 5
Maintain clear communication with team members about safety practices and potential hazards.
Example Answers
I always wear the necessary PPE like gloves and safety goggles. Before starting work, I conduct a thorough risk assessment to identify any potential hazards. I also adhere strictly to lockout/tagout protocols when maintaining equipment.
How do you ensure successful integration between different process control systems?
How to Answer
- 1
Identify communication protocols used by each system and ensure compatibility.
- 2
Regularly test data transfer between systems to troubleshoot issues.
- 3
Implement centralized monitoring to oversee system interactions.
- 4
Document integration processes and changes for reference.
- 5
Engage in continuous training to stay updated on new technologies.
Example Answers
I ensure successful integration by first analyzing the communication protocols of each system to verify compatibility. Regular testing of data transfers helps identify issues early, and I employ centralized monitoring to keep an eye on interactions. Documentation of processes is crucial, so everyone is informed.
How do you approach the analysis of a complex control system?
How to Answer
- 1
Identify key components and their functions in the system
- 2
Review system documentation and control logic diagrams
- 3
Use simulations or software tools to visualize control loops
- 4
Analyze historical data to identify trends and anomalies
- 5
Collaborate with team members to gather insights and verify findings
Example Answers
I start by identifying the main components in the control system and understanding their roles. Then, I review the system documentation and control logic to get a clear picture. After that, I use simulation tools to visualize the control loops and look for any inefficiencies.
Don't Just Read Process Control Technician Questions - Practice Answering Them!
Reading helps, but actual practice is what gets you hired. Our AI feedback system helps you improve your Process Control Technician interview answers in real-time.
Personalized feedback
Unlimited practice
Used by hundreds of successful candidates
Situational Interview Questions
If you noticed a sudden deviation in process parameters, what immediate actions would you take?
How to Answer
- 1
Quickly assess the deviation to determine its significance and potential impact
- 2
Verify the accuracy of measurement tools and data readings
- 3
Identify the potential causes of the deviation, considering both equipment and process factors
- 4
Notify relevant team members or supervisors about the deviation for further support
- 5
Take immediate corrective actions if safety is at risk or if the deviation affects product quality
Example Answers
First, I would assess the deviation to understand its impact. Then, I would check all measuring instruments to ensure they are functioning correctly. After that, I'd investigate possible causes and communicate with my supervisor about the issue. If it affects safety or quality, I would implement immediate corrective actions.
Imagine you are tasked with improving a slow and inefficient process. What steps would you take?
How to Answer
- 1
Identify the specific problem areas in the process through data analysis.
- 2
Engage with team members for their insights and suggestions.
- 3
Utilize process mapping to visualize the current workflow.
- 4
Implement small-scale changes and monitor results before full-scale rollout.
- 5
Document findings and adjustments for future reference and improvement.
Example Answers
I would first analyze performance data to pinpoint where delays occur. Next, I would talk to team members for their insights on bottlenecks. After that, using process mapping, I would visualize the workflow and identify specific inefficiencies. I would then test minor changes in a controlled setting and track the outcomes before applying them widely.
Don't Just Read Process Control Technician Questions - Practice Answering Them!
Reading helps, but actual practice is what gets you hired. Our AI feedback system helps you improve your Process Control Technician interview answers in real-time.
Personalized feedback
Unlimited practice
Used by hundreds of successful candidates
How would you handle a situation where a cross-functional team disagrees on process control strategies?
How to Answer
- 1
Listen to all perspectives to understand the root of the disagreement
- 2
Facilitate a collaborative discussion to clarify goals and priorities
- 3
Analyze data and facts to support the decision-making process
- 4
Propose a trial or pilot to test competing strategies without full commitment
- 5
Aim for consensus but be ready to escalate if necessary for project timelines
Example Answers
In a past project, I ensured everyone voiced their concerns, then guided the team to find common goals. We focused on data analysis to reach a consensus, and when disagreements continued, I suggested a pilot project to evaluate the best approach.
If you discovered a long-term pattern of poor performance in a process, how would you report it?
How to Answer
- 1
Gather data to illustrate the pattern clearly
- 2
Identify the root cause using relevant analysis tools
- 3
Draft a concise report with findings and suggested improvements
- 4
Present to stakeholders in a clear format
- 5
Follow up to ensure action is taken on the report
Example Answers
I would first collect and analyze relevant data to show the extent of the poor performance. Then, I would use tools like process mapping to identify the root causes. After preparing a clear report, I'd present it to the team and suggest actionable improvements and follow up to ensure we implement the changes.
If a new process control technology is implemented, how would you approach training the team?
How to Answer
- 1
Assess the current skill levels of the team before training begins
- 2
Create a structured training plan that includes hands-on sessions
- 3
Use visual aids and documentation to support learning
- 4
Encourage team collaboration through group exercises
- 5
Gather feedback post-training to identify areas for improvement
Example Answers
I would start by evaluating the team's existing skills to understand their training needs. Then, I'd develop a hands-on training program that includes practical exercises with the new technology. Visual aids would be provided to enhance understanding, and I would facilitate group activities to promote teamwork. After the training, I'd collect feedback to see what worked well and what needs to be adjusted.
You are assigned to a project with a tight deadline. How would you prioritize your tasks?
How to Answer
- 1
Identify critical tasks that impact project completion.
- 2
Break down tasks into smaller, manageable steps.
- 3
Assess the time required for each task and prioritize based on urgency.
- 4
Communicate with team members to align on priorities.
- 5
Set short milestones to track progress and stay motivated.
Example Answers
I would start by identifying the critical tasks that must be completed first to meet the project deadline. Then, I'd break those tasks into smaller steps to make them more manageable. I'll prioritize based on urgency and communicate with my team to ensure we're all aligned.
How would you react if you received negative feedback on your process control strategy from management?
How to Answer
- 1
Stay calm and listen actively to the feedback without being defensive
- 2
Ask for specific examples to understand the concerns better
- 3
Reflect on the feedback and identify areas for improvement
- 4
Communicate your willingness to adapt and make necessary changes
- 5
Follow up after implementing changes to show progress and accountability
Example Answers
I would listen carefully to the feedback and ask for specific examples that illustrate the concerns. This would help me understand the issues better and improve my process control strategy.
What would you do if you were given limited resources to address a critical process issue?
How to Answer
- 1
Assess the criticality of the issue and prioritize actions.
- 2
Identify alternative solutions that require fewer resources.
- 3
Collaborate with team members for their insights and support.
- 4
Implement a phased approach to address the most impactful areas first.
- 5
Document the process and outcomes for future reference.
Example Answers
I would first evaluate the issue's impact and prioritize the most critical actions. Then, I would seek alternative solutions that require fewer resources, potentially using existing tools effectively.
How would you handle resistance among coworkers when introducing a new process control method?
How to Answer
- 1
Identify the reasons for resistance through open discussions.
- 2
Provide clear benefits of the new process to the team.
- 3
Involve coworkers in the implementation to promote buy-in.
- 4
Offer training sessions to build confidence with the new method.
- 5
Follow up and gather feedback to address any ongoing concerns.
Example Answers
I would start by opening a dialogue with my coworkers to understand their concerns. Once I know the reasons for their resistance, I would explain the benefits of the new method and how it can improve our workflow. By involving them in the implementation process and providing necessary training, I can help them feel more comfortable with the change.
What would you do if a process control failure leads to product quality issues?
How to Answer
- 1
Assess the extent of the quality issues immediately
- 2
Identify the root cause of the process control failure
- 3
Implement containment measures to prevent further defects
- 4
Coordinate with team members to develop a corrective action plan
- 5
Document the incident and the steps taken for future reference
Example Answers
First, I would assess the extent of the product quality issues by reviewing the affected batches. Then, I would identify the root cause of the process control failure and implement containment measures to stop any further defects while notifying my team. Finally, I would work with them to create a corrective action plan and document everything for future reference.
Don't Just Read Process Control Technician Questions - Practice Answering Them!
Reading helps, but actual practice is what gets you hired. Our AI feedback system helps you improve your Process Control Technician interview answers in real-time.
Personalized feedback
Unlimited practice
Used by hundreds of successful candidates
How would you approach engaging stakeholders when implementing process control changes?
How to Answer
- 1
Identify key stakeholders and their roles in the process.
- 2
Schedule initial meetings to discuss the proposed changes and gather feedback.
- 3
Use clear and simple language to explain the benefits of the changes.
- 4
Establish a regular communication plan to keep stakeholders informed throughout the process.
- 5
Incorporate stakeholder feedback into the implementation plan to foster collaboration.
Example Answers
I would first identify all stakeholders, including operators and management, and then hold a meeting to present the changes. I would explain the benefits in layman's terms and actively seek their input to make sure everyone's voice is heard.
Process Control Technician Position Details
Salary Information
Recommended Job Boards
These job boards are ranked by relevance for this position.
Related Positions
Ace Your Next Interview!
Practice with AI feedback & get hired faster
Personalized feedback
Used by hundreds of successful candidates
Ace Your Next Interview!
Practice with AI feedback & get hired faster
Personalized feedback
Used by hundreds of successful candidates