Top 27 Calibration Technician Interview Questions and Answers [Updated 2025]
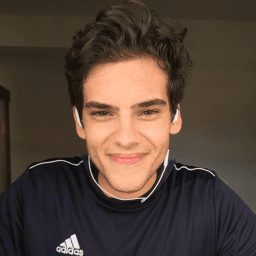
Andre Mendes
•
March 30, 2025
Embarking on a career as a Calibration Technician? Our latest blog post is your go-to guide for mastering the interview process. Dive into the most common interview questions you might face in this role, complete with example answers and expert tips to enhance your responses. Equip yourself with the knowledge and confidence to impress potential employers and secure your position in this precision-driven field.
Download Calibration Technician Interview Questions in PDF
To make your preparation even more convenient, we've compiled all these top Calibration Technicianinterview questions and answers into a handy PDF.
Click the button below to download the PDF and have easy access to these essential questions anytime, anywhere:
List of Calibration Technician Interview Questions
Behavioral Interview Questions
Can you describe a time when you encountered a significant issue during a calibration process? How did you resolve it?
How to Answer
- 1
Start with a brief overview of the calibration process you were involved in.
- 2
Clearly describe the significant issue you faced.
- 3
Explain the steps you took to troubleshoot the problem.
- 4
Highlight the outcome and any lessons learned.
- 5
Keep your answer focused on your role in resolving the issue.
Example Answers
During a routine calibration of pressure gauges, I found inconsistent readings. I carefully reviewed the procedure, identified that the wrong reference standard was used, and quickly replaced it. After recalibrating, the gauges were within specification, and I documented the incident to prevent future occurrences.
Tell me about a time you made a mistake while calibrating equipment. What did you learn from that experience?
How to Answer
- 1
Choose a specific incident to discuss.
- 2
Explain the context and the mistake clearly.
- 3
Describe how you corrected the mistake.
- 4
Highlight the lesson you learned.
- 5
Emphasize how you applied this lesson in future calibrations.
Example Answers
During a routine calibration, I accidentally used an incorrect reference standard, which caused inaccurate readings. I realized the error when double-checking the results. I recalibrated using the correct standard and ensured all data was verified. I learned the importance of thorough checks and have since implemented a checklist to prevent this from happening again.
Don't Just Read Calibration Technician Questions - Practice Answering Them!
Reading helps, but actual practice is what gets you hired. Our AI feedback system helps you improve your Calibration Technician interview answers in real-time.
Personalized feedback
Unlimited practice
Used by hundreds of successful candidates
Describe a situation where you had to collaborate with engineers or other technicians to complete a calibration task. What was your role?
How to Answer
- 1
Choose a specific calibration task for clarity
- 2
Highlight your collaborative role and contributions
- 3
Explain the outcome and any improvements made
- 4
Use action verbs to describe your involvement
- 5
Keep it concise and focused on teamwork
Example Answers
During a project to calibrate precision measurement tools, I worked alongside an engineer and two other technicians. My role was to run diagnostics and gather data on tool performance. By collaborating closely, we identified issues that improved accuracy by 15%.
Have you ever had to explain a technical calibration process to non-technical team members? How did you ensure they understood?
How to Answer
- 1
Use simple language and avoid jargon.
- 2
Provide a step-by-step overview of the process.
- 3
Use analogies or real-world examples to make it relatable.
- 4
Encourage questions to clarify any misunderstandings.
- 5
Use visual aids, like diagrams or charts, if applicable.
Example Answers
Yes, I once had to explain the calibration of measuring tools to our sales team. I used simple terms, described the process in steps, and compared it to adjusting a scale to ensure accuracy. I encouraged them to ask questions to confirm their understanding.
Tell me about a time when you had to prioritize multiple calibration tasks under a tight deadline. How did you manage your time?
How to Answer
- 1
Identify and list all tasks that need to be completed.
- 2
Evaluate the urgency and importance of each task.
- 3
Use a time management tool to allocate specific time slots for each task.
- 4
Communicate with your team about your priorities and deadlines.
- 5
Stay flexible and be ready to adjust your plan as needed.
Example Answers
In my previous role, I had to calibrate several instruments for an upcoming audit. I made a list of all instruments, prioritized them based on their importance for the audit, and used a calendar to block time for each calibration. I also kept my supervisor updated on my progress, which allowed us to address any issues promptly.
Describe a successful calibration project you led. What were the key factors that contributed to its success?
How to Answer
- 1
Start with a clear project overview including the objectives and scope.
- 2
Highlight your specific role and responsibilities in leading the project.
- 3
Identify key challenges faced and how you addressed them.
- 4
Discuss collaboration with team members and stakeholders.
- 5
Conclude with measurable results or positive outcomes from the project.
Example Answers
I led a calibration project for a production facility where we needed to align several measurement instruments. My role involved planning the timeline and coordinating with the engineering team. We faced a shortage of calibration standards, but I sourced alternatives that met requirements. Collaboration was key, as I communicated regularly with the team. As a result, we completed the project two weeks ahead of schedule, improving production accuracy by 15%.
Reflect on a calibration job that did not go as planned. How did you handle the situation and what adjustments did you make?
How to Answer
- 1
Identify a specific calibration issue you faced.
- 2
Explain the impact it had on the outcome.
- 3
Describe the immediate actions you took to address the problem.
- 4
Include any adjustments made to your process or equipment.
- 5
Highlight the lesson learned and how it improved your future calibrations.
Example Answers
During a calibration for a pressure gauge, I discovered it was giving inconsistent readings. I investigated and found that the calibration source was faulty. I replaced the equipment and recalibrated, resulting in accurate readings. This taught me to double-check my tools before starting a job.
Technical Interview Questions
What types of measurement instruments have you worked with, and how do you ensure their accuracy and reliability?
How to Answer
- 1
List specific instruments you have experience with.
- 2
Mention any calibration standards you follow.
- 3
Describe procedures for regular maintenance and checks.
- 4
Emphasize the importance of documentation and traceability.
- 5
Include experience with troubleshooting or resolving inaccuracies.
Example Answers
I have worked with digital multimeters, oscilloscopes, and pressure gauges. I ensure accuracy by following ISO 17025 standards and performing calibrations annually, along with regular functionality tests.
Can you explain the importance of calibration standards, such as ISO 17025, and how they apply to your work?
How to Answer
- 1
Define calibration standards and their role in ensuring accuracy.
- 2
Mention ISO 17025 specifically and its relevance to laboratory operations.
- 3
Explain how adherence to these standards ensures quality and credibility.
- 4
Discuss the impact of calibration on safety and compliance in industries.
- 5
Provide a personal example of how you have applied these standards in your work.
Example Answers
Calibration standards ensure that measurements are accurate and reliable, which is crucial in our work as technicians. ISO 17025 specifically sets requirements for laboratory competence and is essential for maintaining quality. By adhering to these standards, I can ensure that instruments perform correctly, which directly affects safety and compliance in our operations.
Don't Just Read Calibration Technician Questions - Practice Answering Them!
Reading helps, but actual practice is what gets you hired. Our AI feedback system helps you improve your Calibration Technician interview answers in real-time.
Personalized feedback
Unlimited practice
Used by hundreds of successful candidates
How do you analyze calibration data to determine if equipment is operating within specifications?
How to Answer
- 1
Review calibration standards and specifications for the equipment.
- 2
Collect and record calibration data accurately during the testing process.
- 3
Use statistical methods such as mean, standard deviation, and tolerance limits.
- 4
Compare measured values against acceptable limits to assess compliance.
- 5
Document findings and identify any trends or anomalies in data.
Example Answers
I start by checking the equipment specifications and collecting the calibration data accurately. Then, I calculate the mean and standard deviation of the measurements and compare these values against the specified tolerance limits. If the data falls within limits, I’ll document it, but if not, I’ll investigate potential causes.
What calibration software or tools are you familiar with, and how have you used them in your previous work?
How to Answer
- 1
Identify specific calibration software you have worked with.
- 2
Explain how you utilized the software in your calibration processes.
- 3
Mention any relevant certifications or training you have completed.
- 4
Highlight any successes or improvements achieved using these tools.
- 5
Be prepared to discuss your troubleshooting experiences with the software.
Example Answers
I have extensive experience with Fluke Calibration software, which I used to maintain and calibrate electronic instruments. During my last position, I improved our calibration turnaround time by 20% by implementing this tool effectively.
Describe a time when you had to troubleshoot a malfunctioning piece of equipment. What steps did you take?
How to Answer
- 1
Start with the context of the equipment and the problem encountered.
- 2
Explain the diagnostic steps taken to identify the issue clearly.
- 3
Detail the specific actions you took to resolve the problem.
- 4
Mention any tools or techniques used during the troubleshooting.
- 5
Conclude with the outcome and what you learned from the experience.
Example Answers
At my previous job, the calibration unit was giving inconsistent readings. I inspected the connections and found a loose wire. After reattaching it, I ran several tests to verify accuracy, and the readings became stable again. This taught me the importance of checking connections first.
What technical manuals or guidelines do you refer to for ensuring compliance during calibration procedures?
How to Answer
- 1
Identify specific manuals like ISO 17025 or NIST guidelines.
- 2
Mention equipment manufacturer documentation for calibration recommendations.
- 3
Discuss internal company protocols or SOPs for calibration consistency.
- 4
Emphasize the importance of traceability in your calibration process.
- 5
Highlight any industry-specific standards relevant to the role.
Example Answers
I regularly refer to ISO 17025 for general calibration guidelines, along with the manufacturer’s manuals for specific equipment to ensure compliance and accuracy.
How do you integrate preventative maintenance practices into your calibration work?
How to Answer
- 1
Establish a routine schedule for preventative maintenance based on equipment usage.
- 2
Document calibration procedures and results for easy reference and analysis.
- 3
Train staff on the importance of preventative maintenance to ensure compliance.
- 4
Use software tools for tracking maintenance schedules and alerts.
- 5
Review and update maintenance practices regularly to adapt to new equipment or standards.
Example Answers
I set up a calendar for regular maintenance check-ups based on the calibration equipment's usage frequency, ensuring that calibration tools are serviced before critical operations.
Situational Interview Questions
If you discover that a calibrated device is producing inconsistent results, what immediate steps would you take to address the issue?
How to Answer
- 1
Verify the calibration status of the device
- 2
Check for any environmental factors affecting measurements
- 3
Inspect the device for visible damage or wear
- 4
Review the measurement procedure for accuracy
- 5
Document findings and escalate if necessary
Example Answers
First, I would confirm the calibration status to ensure it's up to date. Then, I would examine the surrounding environment for temperature or interference issues. Lastly, I'd check the device for any physical damage before documenting everything.
Imagine you are working with a team that disagrees on calibration methods. How would you handle the conflict and reach a consensus?
How to Answer
- 1
Listen to all team members' perspectives without interruption
- 2
Identify common goals and objectives related to calibration
- 3
Encourage open discussion while respecting differing opinions
- 4
Propose a trial of the different methods to gather data
- 5
Aim for a collaborative solution that incorporates the best aspects of each method
Example Answers
I would start by listening to everyone's viewpoints to understand the reasons behind their preferences. Then, I'd focus on our common goal of accurate calibration and suggest a trial period for each method to see which performs best based on data.
Don't Just Read Calibration Technician Questions - Practice Answering Them!
Reading helps, but actual practice is what gets you hired. Our AI feedback system helps you improve your Calibration Technician interview answers in real-time.
Personalized feedback
Unlimited practice
Used by hundreds of successful candidates
What would you do if you noticed a safety violation while performing calibration tasks on heavy equipment?
How to Answer
- 1
Immediately stop calibration tasks to ensure safety.
- 2
Identify the specific safety violation clearly.
- 3
Document the violation with details and evidence.
- 4
Report the violation to your supervisor or safety officer.
- 5
Propose corrective actions or improvements if applicable.
Example Answers
If I noticed a safety violation, I would stop my work right away to prevent any accidents. I would then document the specific violation and report it to my supervisor to ensure it gets addressed promptly.
If you had to choose between following standard procedures and innovating a new method to enhance efficiency, how would you approach the decision?
How to Answer
- 1
Assess the current procedure's effectiveness and limitations
- 2
Consider the potential benefits of the new method
- 3
Evaluate any risks associated with deviating from standard procedures
- 4
Consult with colleagues or supervisors for their inputs
- 5
Make a decision based on data and collaboration rather than emotion
Example Answers
I would first evaluate how well the current procedures are performing and identify any bottlenecks. If the standard method is not meeting our efficiency targets, I would then outline the advantages of the new approach and discuss it with my team to gather their insights before making a recommendation.
How would you respond if a colleague suggested skipping certain calibration checks to save time?
How to Answer
- 1
Emphasize the importance of accuracy in calibration.
- 2
Address the potential risks of skipping checks.
- 3
Encourage a discussion on optimizing processes without compromising quality.
- 4
Highlight industry regulations that mandate thorough checks.
- 5
Suggest evaluating time-saving options that maintain safety and quality.
Example Answers
I would explain that skipping calibration checks can lead to inaccuracies, affecting product quality and safety. It's crucial we adhere to all checks to meet industry standards.
If a client expressed dissatisfaction with the calibration results, how would you handle their concerns?
How to Answer
- 1
Listen actively to the client's specific concerns
- 2
Apologize for any inconvenience caused
- 3
Clarify the calibration process and results without being defensive
- 4
Offer to reevaluate or retest if appropriate
- 5
Follow up after resolution to ensure satisfaction
Example Answers
I would listen carefully to the client's concerns and apologize for any inconvenience. Then, I would explain the calibration process and ensure transparency about the results. If needed, I would offer to retest the equipment to regain their trust.
If you were given an outdated calibration tool that was not performing well, how would you go about ensuring accurate calibration results?
How to Answer
- 1
Assess the current performance of the tool and identify specific issues.
- 2
Research if there are updates or modifications available for the tool.
- 3
Implement routine maintenance or calibration procedures as per manufacturer guidelines.
- 4
Consider using supplementary tools or references for cross-verification.
- 5
Document all findings and adjustments for future reference.
Example Answers
I would first test the tool to identify specific performance issues, then check if updates or modifications are available to improve accuracy.
You are tasked with training a new technician on calibration protocols. What key points would you focus on in your training?
How to Answer
- 1
Start with the importance of calibration and its impact on product quality
- 2
Explain the specific tools and equipment used in the calibration process
- 3
Demonstrate the step-by-step calibration procedures for common instruments
- 4
Emphasize documentation and record-keeping for compliance
- 5
Include troubleshooting tips for common calibration issues
Example Answers
I would begin by explaining the significance of calibration in ensuring accuracy and reliability in measurements. Then, I'd introduce the key tools like calipers and gauges, followed by a demonstration of their calibration procedures. I'd highlight the necessity of proper documentation and provide strategies for troubleshooting typical calibration problems.
How would you address a situation where your calibration results did not meet internal quality assurance standards?
How to Answer
- 1
Analyze the results to identify specific discrepancies or trends.
- 2
Communicate the issue promptly with relevant team members.
- 3
Investigate potential causes and consider environmental or equipment factors.
- 4
Implement corrective actions and re-calibrate if necessary.
- 5
Document findings and adjustments to enhance future calibration processes.
Example Answers
If calibration results don't meet standards, I first review the data to pinpoint discrepancies. Then, I inform my supervisor and collaborate with the team to investigate potential causes, such as equipment malfunction. After identifying the issue, I apply corrective measures and re-calibrate to ensure compliance.
If you identified a new calibration technique that could improve efficiency, how would you propose it to your supervisor?
How to Answer
- 1
Research the new technique thoroughly to understand its benefits and drawbacks.
- 2
Prepare a clear presentation or document that outlines the efficiency improvements.
- 3
Include data or examples from your research to support your proposal.
- 4
Suggest a trial period to test the new technique and gather results.
- 5
Be open to feedback and ready to discuss concerns your supervisor may have.
Example Answers
I would first research the new calibration technique in detail. Then, I'd prepare a concise presentation that highlights the potential efficiency gains, supported by data from similar implementations. I would propose a trial period for testing.
Don't Just Read Calibration Technician Questions - Practice Answering Them!
Reading helps, but actual practice is what gets you hired. Our AI feedback system helps you improve your Calibration Technician interview answers in real-time.
Personalized feedback
Unlimited practice
Used by hundreds of successful candidates
You have multiple calibration requests with tight deadlines. How would you prioritize your work to meet the demands?
How to Answer
- 1
Evaluate the deadlines of each calibration request
- 2
Identify which equipment is critical for production or safety
- 3
Consider the complexity and time required for each task
- 4
Communicate with team members and stakeholders about priorities
- 5
Stay flexible to adjust as urgent issues arise
Example Answers
I would first list all the calibration requests by deadline and urgency. Then, I'd prioritize tasks involving critical equipment used in production. I would communicate with my team to ensure resources are aligned and be ready to adjust if an unexpected situation comes up.
If you were part of a team responsible for improving calibration processes, what steps would you take to identify areas for improvement?
How to Answer
- 1
Review current calibration procedures for efficiency and thoroughness
- 2
Gather feedback from team members on pain points and challenges
- 3
Analyze calibration data for trends indicating potential issues
- 4
Research industry best practices to identify gaps in current processes
- 5
Conduct regular team meetings to discuss findings and brainstorm solutions
Example Answers
I would start by reviewing the current calibration procedures to spot inefficiencies. Gathering feedback from the team would help me understand their challenges. I would analyze calibration data for any trends that suggest improvement areas and benchmark against industry standards to see where we might be lacking.
Calibration Technician Position Details
Salary Information
Average Salary
$67,360
Source: BLS.gov
Recommended Job Boards
ZipRecruiter
www.ziprecruiter.com/Jobs/Calibration-TechnicianThese job boards are ranked by relevance for this position.
Related Positions
Ace Your Next Interview!
Practice with AI feedback & get hired faster
Personalized feedback
Used by hundreds of successful candidates
Ace Your Next Interview!
Practice with AI feedback & get hired faster
Personalized feedback
Used by hundreds of successful candidates