Top 30 Instrument Mechanic Interview Questions and Answers [Updated 2025]
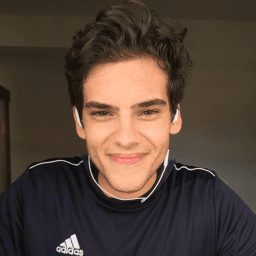
Andre Mendes
•
March 30, 2025
Preparing for an Instrument Mechanic interview can be daunting, but understanding the most common questions can make all the difference. In this blog post, we've compiled the essential interview questions for the Instrument Mechanic role, complete with example answers and valuable tips. Whether you're honing your skills or refreshing your knowledge, this guide is designed to help you respond confidently and effectively, setting you on the path to success.
Download Instrument Mechanic Interview Questions in PDF
To make your preparation even more convenient, we've compiled all these top Instrument Mechanicinterview questions and answers into a handy PDF.
Click the button below to download the PDF and have easy access to these essential questions anytime, anywhere:
List of Instrument Mechanic Interview Questions
Behavioral Interview Questions
Can you describe a time when you diagnosed a complex issue with an instrument? What steps did you take to resolve it?
How to Answer
- 1
Start with a specific instrument and the issue you faced
- 2
Outline the steps you took to diagnose the problem logically
- 3
Explain how you assessed potential causes and ruled them out
- 4
Describe the solution you implemented and why it worked
- 5
Mention any follow-up checks or outcomes to ensure effectiveness
Example Answers
I had a temperature sensor that was reading inconsistently. I first checked the wiring and found a loose connection. After securing it, I tested the sensor against a known standard. The readings stabilized, confirming the fix was successful.
Tell me about a situation where you had to work closely with other technicians or engineers. How did you ensure effective collaboration?
How to Answer
- 1
Choose a specific project or task highlighting teamwork.
- 2
Explain your role and contributions clearly.
- 3
Discuss communication strategies used with the team.
- 4
Mention any challenges faced and how they were resolved.
- 5
Conclude with the positive outcome of the collaboration.
Example Answers
On a recent project to install a new control system, I worked with two engineers and another technician. I organized daily check-ins to track progress and share updates. When we encountered a wiring issue, we brainstormed solutions as a group. This collaboration led us to complete the installation ahead of schedule and without errors.
Don't Just Read Instrument Mechanic Questions - Practice Answering Them!
Reading helps, but actual practice is what gets you hired. Our AI feedback system helps you improve your Instrument Mechanic interview answers in real-time.
Personalized feedback
Unlimited practice
Used by hundreds of successful candidates
Describe an instance where you had to adapt to a sudden change in project requirements or specifications. How did you handle it?
How to Answer
- 1
Think of a specific project that changed unexpectedly.
- 2
Explain the initial requirements and what changed.
- 3
Describe your immediate response and actions taken.
- 4
Highlight the outcome and what you learned.
- 5
Emphasize your flexibility and problem-solving skills.
Example Answers
In a recent project, we were tasked with installing a new control system. Midway, the client requested a different type of sensor. I quickly reviewed the new specifications, adjusted our installation plan, and sourced the necessary components within a week. The project was completed on time and the client was satisfied with the outcome.
Have you ever faced a disagreement with a coworker regarding diagnostic methods? How did you resolve the situation?
How to Answer
- 1
Acknowledge the disagreement without assigning blame
- 2
Explain the diagnostic methods you were using and their rationale
- 3
Listen actively to your coworker's perspective and concerns
- 4
Collaborate to test both methods or compromise when possible
- 5
Summarize the outcome and what you learned from the experience
Example Answers
I once disagreed with a coworker about the proper method for calibrating a pressure gauge. I explained my approach, focusing on its accuracy, while I listened to his concerns about time efficiency. We decided to test both methods side by side, which allowed us to find the best solution together. This experience taught me the value of collaboration in diagnostics.
Can you provide an example of when you took the lead on a project? What was the outcome?
How to Answer
- 1
Choose a specific project where you had a clear leadership role
- 2
Outline your responsibilities and actions taken as a leader
- 3
Highlight the skills or techniques you applied
- 4
Describe the outcome and impact of your leadership
- 5
Reflect on any lessons learned or improvements made
Example Answers
In my previous job, I led a project to upgrade our control systems. I coordinated with a team of technicians, developed a timeline, and ensured compliance with safety standards. The outcome was completing the project two weeks ahead of schedule, which reduced downtime significantly.
Describe a time when you proposed a new method or process that improved efficiency in instrumentation work.
How to Answer
- 1
Think of a specific situation where you identified an inefficiency.
- 2
Explain the method you proposed and why you chose it.
- 3
Share the impact your proposal had on the team's efficiency.
- 4
Use metrics or data to show the improvement, if possible.
- 5
Be concise and focus on your role in the process.
Example Answers
At my last job, I noticed that our calibration process for instruments took too long. I proposed a new software to automate parts of the process, which cut the time by 30%. This allowed us to calibrate more instruments in a day and improved overall productivity.
Tell me about a challenging project you managed. How did you ensure it was completed on time and within budget?
How to Answer
- 1
Identify a specific project that had clear challenges.
- 2
Explain the steps you took to manage the project effectively.
- 3
Highlight how you tracked progress and adjusted plans as needed.
- 4
Discuss how you communicated with your team and stakeholders.
- 5
Mention the outcome and any lessons learned.
Example Answers
In my previous role, I led a project replacing outdated control systems in a refinery. The challenge was a tight deadline and limited budget. I created a detailed project timeline with milestones, monitored spending closely, and held weekly check-ins with the team to address issues quickly. We finished two weeks early and 5% under budget, improving efficiency significantly.
What has been your greatest learning experience in your role as an instrument mechanic?
How to Answer
- 1
Identify a specific incident that challenged you.
- 2
Explain what knowledge you gained from that experience.
- 3
Share how you applied that learning in future situations.
- 4
Focus on both technical and soft skills development.
- 5
Keep it concise and relevant to the job you're applying for.
Example Answers
My greatest learning experience was when I had to troubleshoot a malfunctioning control system under tight deadlines. I learned the importance of systematic problem-solving and communication with my team to ensure we solved the issue quickly. This experience taught me to remain calm under pressure and prioritize tasks effectively.
Technical Interview Questions
What are the key steps involved in calibrating an instrument? Can you explain a calibration technique you commonly use?
How to Answer
- 1
Identify the instrument and its specifications
- 2
Gather necessary tools and reference standards
- 3
Perform a series of test measurements
- 4
Adjust the instrument as needed based on measurements
- 5
Document the calibration results and any adjustments made
Example Answers
To calibrate an instrument, I first identify the instrument and its specifications. Then, I gather the required tools and reference standards. I take test measurements and compare them to the standards. If adjustments are needed, I make them and document everything for future reference.
What process do you follow when troubleshooting a malfunctioning instrument? Can you give an example?
How to Answer
- 1
Start with a clear understanding of the instrument's specifications and expected performance.
- 2
Check for obvious issues like power supply or loose connections.
- 3
Use diagnostic tools to measure performance parameters.
- 4
Document any findings and steps taken during the troubleshooting process.
- 5
Communicate clearly with team members about issues and resolutions.
Example Answers
When troubleshooting an instrument, I first ensure I understand its specifications. For example, with a malfunctioning pressure sensor, I checked the power supply and found a loose connection, which resolved the issue.
Don't Just Read Instrument Mechanic Questions - Practice Answering Them!
Reading helps, but actual practice is what gets you hired. Our AI feedback system helps you improve your Instrument Mechanic interview answers in real-time.
Personalized feedback
Unlimited practice
Used by hundreds of successful candidates
What hand tools and diagnostic equipment are you familiar with as an instrument mechanic? How do you determine which tools to use for specific tasks?
How to Answer
- 1
List specific hand tools like wrenches, screwdrivers, and pliers that you use regularly.
- 2
Mention diagnostic equipment such as multimeters, oscilloscopes, and calibrators you are experienced with.
- 3
Explain your process for choosing tools based on the task requirements and equipment type.
- 4
Provide examples of past scenarios where specific tools were crucial for task completion.
- 5
Highlight any relevant certifications or training that enhance your tool usage proficiency.
Example Answers
I am familiar with hand tools like adjustable wrenches, needle-nose pliers, and various screwdrivers. For diagnostic equipment, I frequently use multimeters and process calibrators. I determine which tools to use by first assessing the task requirements; for example, using a multimeter for electrical troubleshooting or specific calibration tools for precision work.
What safety protocols do you follow when working with hazardous materials or electrical instruments?
How to Answer
- 1
Always wear appropriate personal protective equipment (PPE) including gloves, goggles, and hard hats.
- 2
Ensure proper labeling and storage of hazardous materials to avoid accidental exposure.
- 3
Follow lockout/tagout procedures when servicing electrical instruments to prevent accidental energization.
- 4
Keep a first-aid kit handy and know the location of safety equipment like eyewash stations.
- 5
Stay informed about Material Safety Data Sheets (MSDS) for all hazardous materials you work with.
Example Answers
I always wear the necessary PPE for the task, such as gloves and goggles, to protect myself from hazardous materials. I also make sure all materials are properly labeled and stored to prevent any mix-ups.
How do you ensure accurate readings from measurement instruments? What factors can affect these readings?
How to Answer
- 1
Calibrate instruments regularly to maintain accuracy
- 2
Inspect and clean sensors and components before use
- 3
Understand the instrument's specifications and operating range
- 4
Account for environmental factors like temperature and humidity
- 5
Perform multiple readings and average them for reliability
Example Answers
I ensure accurate readings by calibrating instruments regularly and cleaning the sensors before each use. I also keep in mind the instrument's specifications and check for any environmental impacts like temperature changes.
What software tools or systems do you use for monitoring and maintaining instrument performance? Can you provide an example of how you've used one?
How to Answer
- 1
Identify specific software tools you have experience with.
- 2
Mention the purpose of the tools in monitoring instrument performance.
- 3
Provide a concrete example from your experience.
- 4
Highlight the outcome or value added by using the tool.
- 5
Keep your answer structured and to the point.
Example Answers
I use DeltaV as a monitoring tool for instrument performance. In my last job, I used it to track a pressure transmitter's readings. I noticed a dip in performance, and I was able to calibrate it, which improved accuracy by 15%.
What industry standards do you follow when working with instrumentation in your field?
How to Answer
- 1
Identify key industry standards relevant to instrumentation like ISA, IEC, or ISO.
- 2
Mention how you apply these standards in daily tasks or projects.
- 3
Emphasize the importance of safety and accuracy in compliance.
- 4
Provide specific examples of instruments used and standards followed.
- 5
Stay current by participating in training or professional development programs.
Example Answers
I follow the ISA standards for automation and control systems, ensuring accuracy and safety in my work. In my last project, I applied IEC 61508 for functional safety in instrumentation.
Can you explain the function of various components in a control loop system? Which components do you work with most frequently?
How to Answer
- 1
Identify the main components: sensor, controller, actuator, and process.
- 2
Briefly explain the role of each component in the control loop.
- 3
Mention specific components you routinely work with.
- 4
Highlight your experience with troubleshooting in these systems.
- 5
Use clear and technical language while keeping it understandable.
Example Answers
A control loop system consists of a sensor that measures a process variable, a controller that compares this to a desired setpoint, and an actuator that adjusts the process based on the controller's output. I frequently work with temperature sensors and PID controllers in my current role.
What routine maintenance tasks do you typically perform on instruments, and why are they important?
How to Answer
- 1
Identify key routine maintenance tasks such as calibration, cleaning, and lubrication.
- 2
Explain the importance of each task in ensuring accuracy and reliability.
- 3
Mention safety checks and their role in preventing malfunctions.
- 4
Discuss frequency of tasks to demonstrate proactive maintenance.
- 5
Relate tasks to industry standards or best practices for credibility.
Example Answers
I typically perform calibration, cleaning, and lubrication on instruments. Calibration ensures accuracy, which is vital for reliable data. Regular cleaning prevents buildup that can affect performance, while lubrication helps maintain moving parts, reducing wear and tear.
What diagnostic techniques are most effective for identifying faults in process instrumentation?
How to Answer
- 1
Start with systematic checks to verify input signals and output responses.
- 2
Utilize calibration techniques to ensure the instrument is working within specifications.
- 3
Apply troubleshooting tools like multimeters and oscilloscopes for real-time analysis.
- 4
Review diagnostic error codes if the instrument has built-in diagnostic capabilities.
- 5
Conduct a root cause analysis to identify underlying issues after initial diagnostics.
Example Answers
I find that starting with systematic checks on both input and output signals helps identify discrepancies quickly. I also use multimeters to ensure voltage and current levels are correct.
Don't Just Read Instrument Mechanic Questions - Practice Answering Them!
Reading helps, but actual practice is what gets you hired. Our AI feedback system helps you improve your Instrument Mechanic interview answers in real-time.
Personalized feedback
Unlimited practice
Used by hundreds of successful candidates
What measures do you take to ensure compliance with industry regulations while working on instruments?
How to Answer
- 1
Stay updated on relevant regulations and standards in your field
- 2
Utilize checklists to verify compliance during installation and maintenance
- 3
Document all processes and modifications for audit trails
- 4
Attend training sessions or workshops on regulatory changes
- 5
Communicate with team members to ensure collective compliance
Example Answers
I regularly review the latest industry regulations and keep a checklist to ensure compliance during every project. This helps me catch any potential issues early.
Situational Interview Questions
If you are asked to perform a calibration on an instrument that is critical to operations, but you are also responsible for routine maintenance tasks, how would you prioritize your work?
How to Answer
- 1
Assess the urgency of the calibration task based on operational needs
- 2
Coordinate with your team to communicate priorities and ensure coverage
- 3
Schedule downtime for routine maintenance to avoid disruption during critical operations
- 4
Document your prioritization rationale for transparency
- 5
Seek assistance or delegate routine tasks if necessary
Example Answers
I would first evaluate the calibration's impact on operations. If it's critical, I would communicate with my team, prioritize the calibration, and schedule routine maintenance around it.
Imagine you discover a malfunction in a vital instrument while operations are ongoing. What steps would you take to communicate this to your team and resolve the issue?
How to Answer
- 1
Immediately assess the severity of the malfunction.
- 2
Notify the team leader or supervisor as soon as possible.
- 3
Communicate the issue clearly, including the potential impact on operations.
- 4
Suggest a temporary workaround if possible, while starting repairs.
- 5
Document the malfunction and any actions taken for future reference.
Example Answers
I would evaluate the malfunction to understand its severity, then promptly inform my supervisor. I would explain the issue and its potential effects on operations, suggest a temporary workaround, and begin repairs while keeping the team updated.
Don't Just Read Instrument Mechanic Questions - Practice Answering Them!
Reading helps, but actual practice is what gets you hired. Our AI feedback system helps you improve your Instrument Mechanic interview answers in real-time.
Personalized feedback
Unlimited practice
Used by hundreds of successful candidates
If your team disagrees on the best approach to repair an instrument, how would you facilitate a discussion to reach a consensus?
How to Answer
- 1
Encourage all team members to share their perspectives without interruption
- 2
Summarize the key points from each viewpoint to clarify understanding
- 3
Identify common goals or concerns among the team to focus the discussion
- 4
Suggest a pros and cons analysis for each proposed solution
- 5
Aim for a collaborative solution that combines the best ideas from each approach
Example Answers
I would start by encouraging everyone to voice their opinions so that all perspectives are heard. Then, I would summarize the main points to ensure understanding. By focusing on our common goal of effective repair, I would suggest we analyze the pros and cons of each approach to reach a consensus.
What would you do if an instrument you recently serviced fails unexpectedly a day later? How would you approach troubleshooting?
How to Answer
- 1
Stay calm and avoid jumping to conclusions about the cause.
- 2
Review the service performed to identify any potential oversights.
- 3
Gather operational data and perform a preliminary assessment.
- 4
Consult with colleagues or documentation for troubleshooting protocols.
- 5
Implement a step-by-step troubleshooting process to isolate the issue.
Example Answers
I would first calm myself and review the service record to ensure I didn't miss anything. Then, I would check the operational environment and gather any relevant data. After that, I would follow a troubleshooting guide to systematically identify the problem.
How would you manage your tasks if you were faced with a tight deadline for multiple instrument repairs? What strategies would you employ?
How to Answer
- 1
List all repairs and prioritize by urgency and impact.
- 2
Break down tasks into smaller, manageable steps.
- 3
Communicate with your team about deadlines and status updates.
- 4
Use time management tools to allocate specific time slots for each task.
- 5
Stay flexible and be ready to adjust priorities as needed.
Example Answers
I would start by listing all the instruments needing repair and ranking them based on urgency. Then, I would break down each repair into smaller tasks and assign time slots to complete them. I would keep my team informed about progress and adjust priorities if unexpected issues arise.
If you were asked to mentor a new instrument mechanic, what key lessons or skills would you focus on teaching them?
How to Answer
- 1
Emphasize the importance of safety protocols in all tasks.
- 2
Teach them how to read and interpret technical drawings and schematics.
- 3
Focus on hands-on training with calibration tools and techniques.
- 4
Encourage problem-solving skills and troubleshooting methodologies.
- 5
Instill the value of continuous learning and staying updated with technology.
Example Answers
I would start by emphasizing safety protocols, as they are crucial in this line of work. Next, I'd teach them how to read technical drawings since proper interpretation is vital for accurate installations. I would then provide hands-on training with calibration tools, guiding them step-by-step through techniques. Problem-solving skills are essential, so I would create scenarios for troubleshooting to enhance their skills. Lastly, I’d encourage them to keep learning about new technologies and updates in our field.
If you needed a specific part to fix an instrument but it wasn't available, how would you approach the situation?
How to Answer
- 1
Identify alternative solutions, such as substitutions or temporary fixes.
- 2
Consult with colleagues or supervisors for additional options.
- 3
Check if the part can be ordered or sourced from a different supplier.
- 4
Document the issue and your response for future reference.
- 5
Prioritize safety and the operational integrity of the instrument.
Example Answers
If the part I need isn't available, I'd first look for any suitable alternatives that could temporarily resolve the issue. I would also talk to my colleagues to see if they have encountered similar problems and how they handled them.
How would you handle a situation where you need to train a colleague on a new instrument or technology that you are familiar with?
How to Answer
- 1
Assess the colleague's current knowledge level to tailor your approach
- 2
Break down the training into manageable steps or modules
- 3
Use hands-on demonstrations to illustrate key concepts
- 4
Encourage questions throughout the training for better understanding
- 5
Provide resources or documentation for further learning after the session
Example Answers
I would start by asking what they already know about the instrument to customize the training. Then, I would demonstrate its use step-by-step, allowing them to practice after each section. I’d encourage them to ask questions at any time to ensure they are following along.
If you discover a significant issue with equipment during a routine check, how would you communicate this information to management?
How to Answer
- 1
Assess the severity of the issue before reporting.
- 2
Provide clear and factual details, including observed symptoms and potential impacts.
- 3
Suggest immediate actions or a timeline for follow-up.
- 4
Use formal communication channels, like emails or reports.
- 5
Follow up to ensure the issue is addressed.
Example Answers
I would first evaluate the issue's severity. Then, I would compose a detailed report outlining the findings, potential risks, and recommend immediate actions. I’d send this to management through our established communication channels.
How would you approach a challenge where instrument specifications need adjustment during a project in progress?
How to Answer
- 1
Quickly assess the impact of the proposed changes on the project timeline and budget
- 2
Communicate with stakeholders to understand the reasons for the adjustments
- 3
Collaborate with the engineering team to determine feasible alternatives
- 4
Document all changes and their implications for future reference
- 5
Implement changes systematically to avoid disruption of ongoing work
Example Answers
I would first evaluate the impact of the adjustments on our schedule and costs. Then, I would reach out to stakeholders for clarity on the reasons for the change. After understanding these needs, I would work with the engineering team to explore viable options and document everything for transparency.
Don't Just Read Instrument Mechanic Questions - Practice Answering Them!
Reading helps, but actual practice is what gets you hired. Our AI feedback system helps you improve your Instrument Mechanic interview answers in real-time.
Personalized feedback
Unlimited practice
Used by hundreds of successful candidates
Instrument Mechanic Position Details
Recommended Job Boards
CareerBuilder
www.careerbuilder.com/jobs/instrument-mechanicZipRecruiter
www.ziprecruiter.com/Jobs/Instrument-MechanicThese job boards are ranked by relevance for this position.
Related Positions
Ace Your Next Interview!
Practice with AI feedback & get hired faster
Personalized feedback
Used by hundreds of successful candidates
Ace Your Next Interview!
Practice with AI feedback & get hired faster
Personalized feedback
Used by hundreds of successful candidates