Top 31 Line Supervisor Interview Questions and Answers [Updated 2025]
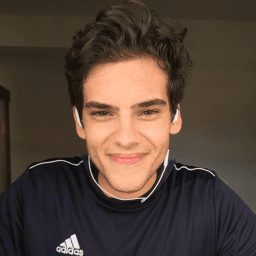
Andre Mendes
•
March 30, 2025
Navigating the competitive landscape of job interviews can be challenging, especially for aspiring line supervisors. This blog post equips you with the most common interview questions for the line supervisor role, offering insightful example answers and practical tips to help you respond effectively. Prepare to enhance your interview skills and confidently tackle the questions that matter most in securing your next supervisory position.
Download Line Supervisor Interview Questions in PDF
To make your preparation even more convenient, we've compiled all these top Line Supervisorinterview questions and answers into a handy PDF.
Click the button below to download the PDF and have easy access to these essential questions anytime, anywhere:
List of Line Supervisor Interview Questions
Behavioral Interview Questions
Can you describe a time when you had to lead a team through a challenging project? What steps did you take to ensure success?
How to Answer
- 1
Choose a specific project with clear challenges
- 2
Highlight your role and leadership style
- 3
Explain the strategies you used to motivate the team
- 4
Mention how you overcame obstacles and adapted plans
- 5
Conclude with the successful outcome and lessons learned
Example Answers
During a product launch, our team faced tight deadlines and resource shortages. I organized daily stand-up meetings to keep everyone aligned and motivated. We prioritized tasks and delegated efficiently, which allowed us to meet our launch date successfully and improve team morale.
Give an example of how you dealt with a conflict between team members. What was the outcome?
How to Answer
- 1
Describe the conflict briefly and who was involved
- 2
Explain your role in addressing the conflict
- 3
Outline the steps you took to facilitate resolution
- 4
Share the outcome and what was learned
- 5
Emphasize collaboration and maintaining a positive team environment
Example Answers
In a previous role, two team members had a disagreement over project responsibilities. I facilitated a meeting, allowing each to voice their concerns. By encouraging open communication, they found common ground. The project was completed successfully, and both felt more valued as team members.
Don't Just Read Line Supervisor Questions - Practice Answering Them!
Reading helps, but actual practice is what gets you hired. Our AI feedback system helps you improve your Line Supervisor interview answers in real-time.
Personalized feedback
Unlimited practice
Used by hundreds of successful candidates
Tell me about a time when you had to solve a production issue under tight deadlines. What was your approach?
How to Answer
- 1
Briefly describe the situation and the urgency.
- 2
Explain the specific steps you took to address the issue.
- 3
Highlight any teamwork or communication involved.
- 4
Share the outcome and what you learned.
- 5
Keep it concise and focused on your role.
Example Answers
In my previous role, we faced a machinery breakdown just before a shipment deadline. I quickly assessed the situation, rallied a team to identify a workaround, and communicated with upper management about our progress. We successfully rerouted resources and completed the order on time, which taught me the importance of quick decision-making and teamwork under pressure.
Describe a situation where you had to motivate a team that was underperforming. What techniques did you use?
How to Answer
- 1
Identify the specific reasons for the team's underperformance
- 2
Communicate a clear and achievable goal to the team
- 3
Recognize individual strengths and contributions
- 4
Implement a regular feedback loop for progress tracking
- 5
Encourage team collaboration and celebrate small wins
Example Answers
In my previous role, our team was struggling to meet project deadlines. I first held a meeting to discuss the obstacles we faced, which allowed us to set a clear, achievable deadline. By highlighting each member's strengths, I assigned tasks that played to their skills. We improved with weekly check-ins, celebrating our milestones together, which boosted morale and accountability.
Tell me about a time when you had to communicate important information to your team. How did you ensure everyone understood?
How to Answer
- 1
Choose a specific instance where clear communication was crucial.
- 2
Describe the method of communication you used, like a meeting or a written memo.
- 3
Explain how you checked for understanding, such as asking for feedback or questions.
- 4
Highlight any follow-up actions you took to reinforce the message.
- 5
Mention the positive outcome as a result of your effective communication.
Example Answers
In my previous role, I had to announce a change in our safety protocols. I held a team meeting to explain the changes in detail, encouraging questions throughout. After the meeting, I sent out a summary email and asked team members to confirm their understanding. This led to improved compliance and safety on the floor.
Describe a time when you received constructively critical feedback. How did you respond?
How to Answer
- 1
Choose a specific example that highlights your ability to accept feedback.
- 2
Explain the feedback clearly and why it was important.
- 3
Describe your emotional response and how you managed it.
- 4
Detail the actions you took in response to the feedback.
- 5
Conclude with the positive outcome and what you learned.
Example Answers
In a recent project, my manager pointed out that my reports lacked clarity. I felt initially defensive but took a step back to reflect. I revised my report format based on her suggestions and sought additional input from colleagues. As a result, my following reports improved significantly, leading to better team communication.
Can you give an example of how you introduced a new idea or innovation to improve line operations?
How to Answer
- 1
Identify a specific problem in line operations you faced.
- 2
Describe the innovative idea you proposed to address it.
- 3
Explain how you implemented this idea and the steps you took.
- 4
Share the results or improvements that occurred after implementation.
- 5
Highlight any team involvement or feedback you received.
Example Answers
In my previous role, we faced delays in production due to manual tracking of inventory. I proposed implementing a digital inventory management system. I led the team in training and integrating this new tool. As a result, we reduced inventory discrepancies by 30% and improved overall efficiency.
Describe a difficult decision you had to make as a Line Supervisor. What was your thought process?
How to Answer
- 1
Focus on a specific situation that highlights your decision-making skills.
- 2
Explain the challenges you faced and why it was a tough decision.
- 3
Detail your thought process step by step to show clarity.
- 4
Include the outcome and what you learned from the experience.
- 5
Mention how this decision impacted your team or production positively.
Example Answers
I once had to decide whether to reassign a team member who was struggling. I analyzed their performance, spoke with them about their challenges, considered team dynamics, and concluded that a different role would suit them better. The outcome was positive; they thrived in their new position and improved overall team morale.
Give an example of when you needed to collaborate with other departments to achieve a goal. How did you ensure effective communication?
How to Answer
- 1
Identify a specific project that required inter-departmental collaboration
- 2
Highlight the departments involved and their roles
- 3
Explain the communication methods used to facilitate collaboration
- 4
Describe any challenges faced and how they were overcome
- 5
Conclude with the successful outcome and lessons learned
Example Answers
In my last role, we launched a new product that required collaboration with the marketing and logistics departments. I set up weekly meetings and used a shared project management tool to track progress. When we faced delays in shipping, we adjusted timelines and communicated openly, ensuring everyone was aligned. Ultimately, the product launched successfully on time and under budget.
Don't Just Read Line Supervisor Questions - Practice Answering Them!
Reading helps, but actual practice is what gets you hired. Our AI feedback system helps you improve your Line Supervisor interview answers in real-time.
Personalized feedback
Unlimited practice
Used by hundreds of successful candidates
Technical Interview Questions
What quality control measures do you typically implement on a production line?
How to Answer
- 1
Discuss specific checks at critical points during production
- 2
Mention the use of standardized testing methods for product quality
- 3
Emphasize the importance of training staff on quality standards
- 4
Include data tracking and analysis for continuous improvement
- 5
Highlight the role of feedback loops for addressing issues promptly
Example Answers
I implement quality checks at key stages, like pre-production inspections and final assembly audits, to catch issues early.
How do you ensure compliance with safety standards in your line operations?
How to Answer
- 1
Regularly conduct safety training sessions for all team members
- 2
Implement daily safety checks and audits on the production line
- 3
Encourage open communication about safety concerns among staff
- 4
Establish clear protocols and signage for safety procedures
- 5
Review and update safety policies to align with current regulations regularly
Example Answers
I conduct weekly safety training for my team to ensure everyone is aware of protocols, and I implement daily checks to monitor compliance. Open communication about safety concerns is encouraged, fostering a proactive culture.
Don't Just Read Line Supervisor Questions - Practice Answering Them!
Reading helps, but actual practice is what gets you hired. Our AI feedback system helps you improve your Line Supervisor interview answers in real-time.
Personalized feedback
Unlimited practice
Used by hundreds of successful candidates
What methodologies have you used to identify areas for process improvement on the line?
How to Answer
- 1
Discuss specific methodologies like Lean, Six Sigma, or Kaizen
- 2
Mention any data collection tools used, such as Pareto charts or value stream mapping
- 3
Provide an example of a successful implementation and its impact
- 4
Highlight your collaboration with team members for insights
- 5
Emphasize continuous improvement and adaptability in your approach
Example Answers
I have utilized the Lean methodology to streamline processes, focusing on waste reduction. By implementing value stream mapping, my team identified bottlenecks, leading to a 15% increase in efficiency.
How do you assess whether machinery requires maintenance and how do you report it?
How to Answer
- 1
Regularly perform visual inspections for signs of wear and tear.
- 2
Utilize scheduled maintenance checklists to track machinery performance.
- 3
Monitor operational metrics like noise levels and temperature for anomalies.
- 4
Document any issues with detailed descriptions and timestamps.
- 5
Report to management using a standardized form or maintenance software.
Example Answers
I assess machinery by conducting weekly inspections for physical damage and checking performance metrics. If I find any issues, I document them immediately and report to my supervisor using our maintenance software.
What key performance indicators do you track to measure production efficiency?
How to Answer
- 1
Identify specific KPIs relevant to the industry and role.
- 2
Discuss how each KPI relates to production goals.
- 3
Emphasize the importance of real-time monitoring.
- 4
Mention how you use KPIs to identify areas for improvement.
- 5
Highlight your experience analyzing KPIs to drive decision-making.
Example Answers
I track overall equipment effectiveness (OEE), cycle time, and scrap rate. These KPIs help me evaluate machine performance and product quality, ensuring we meet our production targets.
What specific technical skills do you possess that relate to managing a production line?
How to Answer
- 1
Identify specific technical skills relevant to production management
- 2
Use examples from previous experiences to demonstrate these skills
- 3
Highlight skills in areas like machinery operation, process optimization, and quality control
- 4
Mention any relevant certifications or training you have
- 5
Be prepared to discuss how these skills contribute to efficiency and productivity
Example Answers
I have strong skills in using production management software, which allows me to effectively schedule and monitor line activities. In my previous role, I implemented a new system that improved our output by 15%.
How do you leverage data analysis in your decision-making process on the line?
How to Answer
- 1
Identify key performance indicators relevant to production.
- 2
Use historical data to spot trends and forecast future issues.
- 3
Implement real-time data monitoring for immediate insights.
- 4
Engage team members in analyzing data to promote collaboration.
- 5
Make data-driven adjustments that enhance efficiency and productivity.
Example Answers
I regularly track KPIs such as production rate and defect rates. By analyzing these metrics, I can identify trends and implement changes that improve our efficiency, such as adjusting workflows during peak times.
What experience do you have with logistics and workflow management in a manufacturing environment?
How to Answer
- 1
Highlight specific roles involving logistics and workflow.
- 2
Mention any tools or software used for managing processes.
- 3
Discuss measurable improvements achieved in previous positions.
- 4
Include examples of team collaboration for enhancing workflow.
- 5
Emphasize any problem-solving experiences related to logistics.
Example Answers
In my previous role as an operations coordinator, I managed logistics for a team of 15, optimizing our workflow using SAP software which improved our delivery times by 20%.
How do you handle inventory discrepancies that you notice during your shift?
How to Answer
- 1
Immediately investigate the discrepancy to determine the cause.
- 2
Check previous records to see if this is a recurring issue.
- 3
Communicate with team members involved to gather insights.
- 4
Document the findings and any actions taken for future reference.
- 5
Implement corrective measures to prevent similar discrepancies.
Example Answers
I first investigate the discrepancy by cross-referencing with past inventory logs. Then, I talk to team members to understand if there were any irregularities during their shifts. Lastly, I document everything and work on solutions, like adjusting our sorting process to prevent future issues.
How do you approach troubleshooting when something goes wrong with the production equipment?
How to Answer
- 1
Identify the issue by reviewing error logs or machine alerts.
- 2
Gather input from operators to understand the context of the problem.
- 3
Conduct a quick visual inspection of the equipment for obvious issues.
- 4
Check if preventive maintenance was performed according to schedule.
- 5
Implement temporary fixes if needed, and prioritize long-term solutions.
Example Answers
I start by checking the error logs to see if there are any alerts. Then, I speak with the operators to get their perspective on what happened. After that, I visually inspect the equipment for any obvious issues before looking into maintenance records.
Don't Just Read Line Supervisor Questions - Practice Answering Them!
Reading helps, but actual practice is what gets you hired. Our AI feedback system helps you improve your Line Supervisor interview answers in real-time.
Personalized feedback
Unlimited practice
Used by hundreds of successful candidates
Situational Interview Questions
If a significant machine breakdown occurs during your shift, how would you prioritize addressing the issue while managing staff and production?
How to Answer
- 1
Assess the situation quickly to understand the impact on production
- 2
Notify the maintenance team immediately for prompt resolution
- 3
Communicate with your team about the issue and reassign tasks
- 4
Implement contingency plans to minimize downtime
- 5
Keep upper management updated on the situation and progress
Example Answers
I would first assess the severity of the breakdown and its impact. Then, I'd notify the maintenance team to start repairs while communicating with my staff to reassign roles for maximum efficiency. We'd use any downtime to perform preventive maintenance on other machines.
If you notice two team members are not collaborating effectively, what steps would you take to improve their relationship?
How to Answer
- 1
Observe interactions to identify specific issues causing the lack of collaboration
- 2
Schedule a private meeting with each team member to understand their perspectives
- 3
Facilitate a joint meeting to encourage open dialogue between them
- 4
Set clear collaboration goals and follow up on their progress
- 5
Provide ongoing support and resources to help them improve their working relationship
Example Answers
First, I would observe the team dynamics to pinpoint the issues. Then, I would meet privately with each person to hear their side before bringing them together for an open discussion. Finally, I’d set collaboration goals and check in regularly to ensure they stay on track.
Don't Just Read Line Supervisor Questions - Practice Answering Them!
Reading helps, but actual practice is what gets you hired. Our AI feedback system helps you improve your Line Supervisor interview answers in real-time.
Personalized feedback
Unlimited practice
Used by hundreds of successful candidates
How would you handle a situation where demand unexpectedly spikes, and resources are limited?
How to Answer
- 1
Quickly assess the current inventory and resource availability
- 2
Prioritize tasks based on urgency and customer impact
- 3
Communicate with the team about the situation and needs
- 4
Seek temporary solutions like reallocating resources or adjusting schedules
- 5
Monitor progress and be ready to adapt as new information comes in
Example Answers
I would start by evaluating our available resources and identifying the most critical tasks. Then, I would communicate with the team to reallocate efforts towards high-priority orders and see if we can extend shifts or shift schedules to handle the surge.
How would you approach training new team members to ensure they quickly become effective in their roles?
How to Answer
- 1
Assess the new team member's background and learning style
- 2
Create a structured training plan with clear objectives
- 3
Incorporate hands-on training with real tasks early on
- 4
Provide regular feedback and encouragement
- 5
Pair new members with experienced team members for mentorship
Example Answers
I would start by understanding each new team member's background and preferred learning style to tailor the training. Then, I'd develop a structured training plan that outlines key objectives. Hands-on tasks would be integrated from day one to facilitate learning, along with regular feedback sessions to track progress.
If a team member consistently underperforms, how would you address this issue with them?
How to Answer
- 1
Observe and gather specific examples of underperformance
- 2
Schedule a private one-on-one meeting to discuss concerns
- 3
Use a constructive tone and focus on the behavior, not the person
- 4
Listen actively to understand any underlying issues
- 5
Collaborate on a plan for improvement with clear goals and timelines
Example Answers
I would first observe and document specific instances of the underperformance. Then, I would arrange a private meeting to discuss these observations, ensuring a constructive tone. I’d listen to their perspective and collaboratively develop an improvement plan with set goals.
How would you handle a situation where a team member disrupts the workflow by not adhering to the processes?
How to Answer
- 1
Address the issue promptly and privately with the team member
- 2
Listen to their perspective to understand their reasoning
- 3
Reiterate the importance of the processes and how they support the team
- 4
Offer additional support or training if needed
- 5
Monitor the situation after the discussion to ensure improvement
Example Answers
I would talk to the team member privately to understand why they are not following the processes. It's important to hear their side. Then, I would explain how sticking to these processes helps the team succeed and offer any support they might need.
If you are faced with too many simultaneous tasks on the line, how do you prioritize them?
How to Answer
- 1
Assess urgency and impact of each task quickly
- 2
Communicate with team members to understand their needs
- 3
Identify tasks that can be delegated based on skill sets
- 4
Focus on critical tasks that align with production goals
- 5
Stay flexible and ready to adjust priorities if new issues arise
Example Answers
I first evaluate which tasks are most urgent and impact overall production. Then, I communicate with my team to see if someone can assist with tasks that can be delegated. Finally, I keep an eye on any changes that may require me to shift priorities quickly.
What would you do if you had to maintain production levels during an unexpected shortage of materials?
How to Answer
- 1
Assess the current inventory and identify critical materials.
- 2
Communicate with suppliers for potential quick sourcing options.
- 3
Explore alternative materials or processes that could temporarily substitute.
- 4
Engage with the team to brainstorm efficiency improvements or workarounds.
- 5
Prioritize production tasks to focus on critical output first.
Example Answers
I would first evaluate our inventory to identify which materials are in critical supply. Next, I would reach out to our suppliers to see if we can source materials quickly. Simultaneously, I'd discuss with my team possible alternatives or adjustments to our processes that could help maintain production.
How would you improve team morale during a particularly demanding production schedule?
How to Answer
- 1
Acknowledge the challenges the team is facing openly
- 2
Implement regular check-ins to gauge team sentiment
- 3
Integrate short breaks and team-building activities to relieve stress
- 4
Recognize individual and team accomplishments publicly
- 5
Encourage open communication and feedback to enhance collaboration
Example Answers
I would start by openly acknowledging the demanding schedule and the stress it brings. Regular check-ins would help me understand the team's feelings, and I would schedule short breaks and team-building activities to maintain energy and morale.
If you had to implement a new shift schedule due to increased demand, how would you communicate this to your team?
How to Answer
- 1
Prepare a clear and concise message outlining the reasons for the shift changes
- 2
Schedule a team meeting to discuss the new schedule face-to-face
- 3
Encourage open dialogue and feedback from team members during the meeting
- 4
Provide a written outline of the new schedule after the meeting for reference
- 5
Be available for one-on-one discussions for team members who may have concerns
Example Answers
I would first prepare a clear message explaining the reasons for the new schedule, then I would hold a team meeting to discuss it. I believe in transparency, so I would encourage everyone to share their thoughts and concerns, and I would provide written details afterward.
Don't Just Read Line Supervisor Questions - Practice Answering Them!
Reading helps, but actual practice is what gets you hired. Our AI feedback system helps you improve your Line Supervisor interview answers in real-time.
Personalized feedback
Unlimited practice
Used by hundreds of successful candidates
What steps would you take to integrate sustainable practices into your production line operations?
How to Answer
- 1
Assess current processes to identify waste and inefficiencies
- 2
Implement energy-efficient machinery and equipment
- 3
Promote recycling and materials recovery within the line
- 4
Train team members on sustainable practices and their importance
- 5
Set measurable sustainability goals and track progress regularly
Example Answers
First, I would conduct a thorough assessment of our current operations to pinpoint areas of waste. Then, I would invest in energy-efficient machinery and initiate a recycling program for materials used in production. Additionally, I would organize training sessions for all team members to ensure everyone understands the significance of sustainability in our processes.
Line Supervisor Position Details
Salary Information
Recommended Job Boards
CareerBuilder
www.careerbuilder.com/jobs?keywords=Line+SupervisorZipRecruiter
www.ziprecruiter.com/Jobs/Line-SupervisorThese job boards are ranked by relevance for this position.
Related Positions
Ace Your Next Interview!
Practice with AI feedback & get hired faster
Personalized feedback
Used by hundreds of successful candidates
Ace Your Next Interview!
Practice with AI feedback & get hired faster
Personalized feedback
Used by hundreds of successful candidates