Top 28 Shop Supervisor Interview Questions and Answers [Updated 2025]
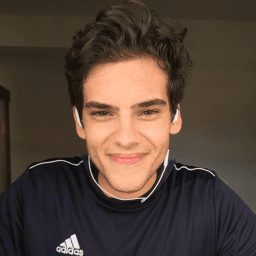
Andre Mendes
•
March 30, 2025
Navigating the interview process for a Shop Supervisor role can be daunting, but preparation is key to success. In this post, we delve into the most common interview questions candidates face, providing insightful example answers and practical tips to help you respond with confidence and clarity. Whether you're a seasoned professional or new to the field, these strategies will equip you to make a lasting impression.
Download Shop Supervisor Interview Questions in PDF
To make your preparation even more convenient, we've compiled all these top Shop Supervisorinterview questions and answers into a handy PDF.
Click the button below to download the PDF and have easy access to these essential questions anytime, anywhere:
List of Shop Supervisor Interview Questions
Behavioral Interview Questions
Can you describe a time when you had to lead a team through a challenging project?
How to Answer
- 1
Choose a specific project that had clear challenges.
- 2
Highlight your leadership role and actions taken.
- 3
Explain how you motivated the team and resolved issues.
- 4
Share the outcome and what was learned from the experience.
- 5
Keep it concise, focusing on impact rather than details.
Example Answers
In my previous role, we faced a tight deadline on a store relaunch. I organized daily check-ins, assigned tasks based on team strengths, and kept morale high with team-building activities. We completed the project on time and exceeded sales targets by 20%.
Tell me about a situation where you had to resolve a conflict between team members. How did you handle it?
How to Answer
- 1
Identify the specific conflict and the involved parties.
- 2
Explain your approach to understanding both sides of the issue.
- 3
Describe the steps you took to facilitate a resolution.
- 4
Highlight the outcome and any improvements in teamwork following the resolution.
- 5
Reflect on what you learned from the experience.
Example Answers
In a previous role, two team members disagreed about the best way to approach a project. I arranged a meeting where both could express their viewpoints. By encouraging open communication, we found a compromise that incorporated elements from both perspectives. As a result, the project was completed on time and the team’s collaboration improved significantly.
Don't Just Read Shop Supervisor Questions - Practice Answering Them!
Reading helps, but actual practice is what gets you hired. Our AI feedback system helps you improve your Shop Supervisor interview answers in real-time.
Personalized feedback
Unlimited practice
Used by hundreds of successful candidates
Describe an instance where you worked collaboratively with your team to meet a production goal.
How to Answer
- 1
Choose a specific project or goal to discuss.
- 2
Highlight your role and contributions clearly.
- 3
Emphasize teamwork and collaboration aspects.
- 4
Mention the outcome and what you learned.
- 5
Keep it concise and focused on your experience.
Example Answers
In my previous role, we had a target to increase output by 20% in a month. I coordinated daily check-ins with my team to monitor progress and address challenges. By encouraging open communication, we identified workflow bottlenecks and adjusted our processes. As a result, we exceeded the goal, achieving a 25% increase in production.
Can you provide an example of how you effectively communicated a safety procedure to your team?
How to Answer
- 1
Choose a specific safety procedure relevant to the shop environment.
- 2
Describe the context and why the procedure was important.
- 3
Explain the communication method used (e.g., meeting, training session).
- 4
Mention how you ensured understanding (e.g., Q&A, demonstrations).
- 5
Highlight the outcome, showing improvement or compliance.
Example Answers
In my previous role, we implemented a new hazard communication procedure. I organized a team meeting where I explained the significance of properly labeling chemicals. I used visual aids and real examples to illustrate the process, followed by a Q&A session to clarify doubts. As a result, our compliance with labeling increased by 30% within a month.
Tell me about a time you had to prioritize multiple tasks in a fast-paced environment. How did you manage?
How to Answer
- 1
Identify the specific situation and tasks you faced.
- 2
Explain how you determined priorities and made decisions.
- 3
Describe the tools or methods you used to stay organized.
- 4
Share the outcome and any lessons learned.
- 5
Keep it concise and focus on your role in the scenario.
Example Answers
In my previous role, I managed a busy retail floor where I had to handle customer inquiries, restock shelves, and oversee cashier duties simultaneously. I prioritized customer interactions first since they directly impact sales, then delegated shelf stocking to available staff. I used a simple checklist to monitor restocking and cashier performance. This approach increased customer satisfaction and improved sales during peak hours.
Describe a time when you coached a team member to improve their skills. What approach did you take?
How to Answer
- 1
Choose a specific example that highlights your coaching ability
- 2
Focus on the skills the team member needed to improve
- 3
Explain your coaching methods, like one-on-one training or feedback sessions
- 4
Include the outcome and how it benefited the team or the individual
- 5
Reflect on what you learned as a coach from the experience
Example Answers
I noticed one of my team members struggled with inventory management. I set up weekly one-on-one sessions to review the inventory system together. I provided practical examples and allowed them to practice tracking inventory. Over a month, their accuracy improved by 30%, leading to fewer stockouts.
Can you think of a difficult decision you made as a supervisor? What was the outcome?
How to Answer
- 1
Choose a specific situation that shows your leadership.
- 2
Explain the factors that made the decision difficult.
- 3
Describe your thought process and how you reached your conclusion.
- 4
Highlight the outcome and what you learned from it.
- 5
Keep it focused on your actions and impact as a supervisor.
Example Answers
I once had to decide whether to terminate a long-term employee who was underperforming. It was difficult because we had a close relationship. I analyzed performance metrics, consulted with HR, and ultimately decided to let him go. The outcome was the team improved significantly, and I learned the importance of making tough decisions for the greater good.
Describe a time when you had to advocate for change in the shop. What was your vision, and how did you communicate it?
How to Answer
- 1
Identify a specific change you advocated for that had a measurable impact.
- 2
Explain your vision clearly and why it was necessary for the shop.
- 3
Discuss how you gathered support from your team and management.
- 4
Mention the methods you used to communicate your vision, such as meetings or presentations.
- 5
Include the outcome and any lessons learned from the experience.
Example Answers
In my previous role, I noticed our cleaning process was inefficient, leading to delays. I advocated for a new cleaning schedule that prioritized high-traffic areas. I presented my idea during a team meeting, outlining the benefits and soliciting feedback. Ultimately, we adopted the new schedule, which improved our workflow and reduced downtime by 20%.
Don't Just Read Shop Supervisor Questions - Practice Answering Them!
Reading helps, but actual practice is what gets you hired. Our AI feedback system helps you improve your Shop Supervisor interview answers in real-time.
Personalized feedback
Unlimited practice
Used by hundreds of successful candidates
Technical Interview Questions
What software or tools do you use for scheduling shifts and managing workforce in the shop?
How to Answer
- 1
Mention specific tools you are familiar with, like Excel or dedicated software.
- 2
Highlight how you use these tools to streamline scheduling and reduce conflicts.
- 3
Discuss any experience with mobile apps for employee access to schedules.
- 4
Emphasize any integration with payroll or HR systems for efficiency.
- 5
Share examples of how your approach improved team communication or productivity.
Example Answers
I often use Excel for scheduling shifts due to its flexibility and ease of use. I create templates to manage staff availability and to prevent conflicts, ensuring everyone is aware of their shifts well in advance.
What safety standards and regulations do you think are most critical in a shop environment?
How to Answer
- 1
Identify key safety regulations like OSHA standards.
- 2
Discuss the importance of PPE in protecting workers.
- 3
Mention the significance of proper machine operation training.
- 4
Highlight the need for regular safety audits and inspections.
- 5
Emphasize the importance of emergency procedures and drills.
Example Answers
I believe OSHA standards are critical as they set the baseline for safety practices. Proper use of PPE is also essential to protect workers from injuries. Regular training on machine operation prevents accidents and ensures everyone knows how to use equipment safely.
Don't Just Read Shop Supervisor Questions - Practice Answering Them!
Reading helps, but actual practice is what gets you hired. Our AI feedback system helps you improve your Shop Supervisor interview answers in real-time.
Personalized feedback
Unlimited practice
Used by hundreds of successful candidates
How do you track and manage inventory in your shop? What systems do you prefer to use?
How to Answer
- 1
Describe the inventory tracking methods you use.
- 2
Mention specific software or systems you are familiar with.
- 3
Emphasize your experience with regular inventory audits.
- 4
Discuss how you handle stock levels and reorder points.
- 5
Include a brief example of a successful inventory management outcome.
Example Answers
I use a combination of manual counts and an inventory management software like TradeGecko. Regular audits help me maintain accuracy, and I track stock levels to ensure timely reordering.
Can you explain your approach to ensuring product quality in a manufacturing environment?
How to Answer
- 1
Emphasize the importance of a quality management system.
- 2
Discuss regular training and development for team members.
- 3
Highlight the role of inspections at various stages of production.
- 4
Mention the use of metrics to track and analyze quality data.
- 5
Include a commitment to continuous improvement in processes.
Example Answers
I ensure product quality by implementing a robust quality management system that includes regular inspections throughout the production process. Training team members on quality standards is crucial, and I use metrics to monitor our performance and identify areas for improvement.
What types of maintenance procedures do you consider essential for shop equipment?
How to Answer
- 1
Identify key equipment types in your shop
- 2
Discuss routine inspections and their frequency
- 3
Mention specific cleaning methods for equipment longevity
- 4
Include safety checks and compliance with regulations
- 5
Highlight the importance of keeping maintenance records
Example Answers
I consider regular inspections essential, typically every week, to check for wear and tear on equipment like saws and drills. This includes cleaning parts and ensuring all safety features are functional.
What types of machinery are you most familiar with, and how have you ensured their efficient operation?
How to Answer
- 1
List specific types of machinery you have experience with.
- 2
Mention any certifications or training related to the machinery.
- 3
Explain your methods for monitoring machine performance.
- 4
Provide examples of preventive maintenance practices you implemented.
- 5
Highlight any improvements you made to enhance efficiency.
Example Answers
I have extensive experience with CNC machines and forklift operations. I ensure efficiency by conducting regular inspections and scheduling preventive maintenance, which reduced downtime by 20%.
What strategies do you use to identify and implement process improvements in the shop?
How to Answer
- 1
Observe daily operations and note inefficiencies or delays
- 2
Gather feedback from staff on challenges they face
- 3
Analyze performance metrics to identify trends and areas for improvement
- 4
Benchmark against industry standards for best practices
- 5
Pilot changes with a small team before wider implementation
Example Answers
I regularly observe our workflow and notice where tasks slow down. For example, I identified a bottleneck at the packing station and implemented a new layout, which reduced packing time by 20%.
What training methods have you found most effective for onboarding new staff?
How to Answer
- 1
Use hands-on training to give new hires practical experience.
- 2
Implement a mentorship program pairing new staff with experienced employees.
- 3
Provide clear, easy-to-follow onboarding materials and checklists.
- 4
Encourage group training sessions to build team dynamics.
- 5
Solicit feedback from new hires to continuously improve the training process.
Example Answers
I find hands-on training to be very effective, as it allows new staff to learn by doing. Pairing them with a mentor helps them feel supported and integrated into the team.
How do you determine pricing strategies for products manufactured in your shop?
How to Answer
- 1
Analyze production costs including materials and labor to set a baseline price.
- 2
Research competitor pricing to understand market positioning.
- 3
Consider perceived value and customer willingness to pay for quality.
- 4
Adjust pricing based on demand and seasonality to maximize profit.
- 5
Implement promotional strategies to introduce new products or clear inventory.
Example Answers
I start by calculating all production costs, including materials and labor, to ensure my base pricing covers expenses. Then, I research competitor pricing to ensure we remain competitive but also emphasize our product's quality to justify any premium pricing.
Situational Interview Questions
If you encounter a significant machinery failure during peak hours, what steps would you take to minimize downtime?
How to Answer
- 1
Immediately assess the situation to understand the extent of the failure.
- 2
Notify the maintenance team as soon as possible for rapid response.
- 3
Communicate with staff to redirect workflow and minimize disruption.
- 4
Implement temporary solutions, like adjusting schedules or reallocating resources.
- 5
Document the incident and analyze it afterward to prevent future occurrences.
Example Answers
First, I would quickly assess the machinery to determine the specific issue. Then, I would call the maintenance team for immediate assistance. While waiting, I would inform my staff to shift operations to other available machines to keep productivity up.
How would you motivate your team during a particularly slow production period?
How to Answer
- 1
Communicate transparently about current challenges and expectations
- 2
Encourage team brainstorming for process improvements or new ideas
- 3
Recognize and reward small achievements to boost morale
- 4
Offer training opportunities to enhance skills during downtime
- 5
Schedule team-building activities to maintain a positive atmosphere
Example Answers
During a slow production period, I would hold a team meeting to discuss our current challenges and encourage everyone to share ideas for improvement. Recognizing small wins would help keep morale high.
Don't Just Read Shop Supervisor Questions - Practice Answering Them!
Reading helps, but actual practice is what gets you hired. Our AI feedback system helps you improve your Shop Supervisor interview answers in real-time.
Personalized feedback
Unlimited practice
Used by hundreds of successful candidates
What would you do if a new employee is struggling to adapt to the shop's processes?
How to Answer
- 1
Assess the specific areas where the employee is struggling
- 2
Provide one-on-one training sessions focused on those areas
- 3
Encourage open communication and ask for feedback from the new employee
- 4
Pair the new employee with a more experienced team member for support
- 5
Set clear goals and timelines for improvement
Example Answers
I would first identify where the new employee is having trouble and provide targeted training to help them understand our processes better.
How would you handle a situation where an established policy is hindering production efficiency?
How to Answer
- 1
Identify specific inefficiencies caused by the policy
- 2
Gather input from team members about the impact on their work
- 3
Research potential alternatives or adjustments to the policy
- 4
Present findings and suggestions to management with data
- 5
Be prepared to collaborate with others to implement changes
Example Answers
I would first analyze how the policy is affecting our production metrics. Then, I would solicit feedback from my team to understand their challenges. After gathering data, I'd propose a revised approach to management, highlighting potential efficiency gains.
If you had to allocate limited resources between two competing projects, how would you decide?
How to Answer
- 1
Identify the goals and objectives of both projects
- 2
Assess the potential impact and ROI of each project
- 3
Consider team workload and expertise for each project
- 4
Engage stakeholders to gather input and prioritize needs
- 5
Make a decision based on data and align with overall business strategy
Example Answers
I would first look at the goals of both projects to see which aligns better with our current business objectives. Then I would evaluate the expected ROI and impact of each project, considering team capacity and stakeholder input before making a final decision.
If you noticed unsafe practices being followed by your team, how would you address it?
How to Answer
- 1
Identify the specific unsafe practices clearly
- 2
Engage the team in a conversation about safety
- 3
Provide immediate corrective actions if needed
- 4
Document the issues and the steps taken
- 5
Follow up to ensure ongoing compliance and improvement
Example Answers
I would first observe and identify the unsafe practices clearly. Then, I'd bring the team together to discuss these issues, emphasizing the importance of safety. If there were immediate risks, I would take necessary actions to correct them right away. Finally, I'd document the incidents and follow up to ensure the team understood the changes.
How would you handle a situation where customer feedback suggests a need for a change in product quality?
How to Answer
- 1
Acknowledge the feedback and its importance to customer satisfaction
- 2
Gather specific data from customer feedback for insights
- 3
Communicate with relevant teams to discuss potential improvements
- 4
Implement a plan to test changes and monitor results
- 5
Follow up with customers to inform them of changes and gather further feedback
Example Answers
I would start by acknowledging the customer feedback and its role in improving our products. Then, I would collect specific data from the feedback to identify key issues. After that, I would collaborate with our quality control team to explore practical changes. We would test these changes and closely monitor customer reactions. Lastly, I'd reach out to those who provided feedback to inform them of our improvements and gather their thoughts.
How would you approach delivering constructive feedback to an underperforming team member?
How to Answer
- 1
Prepare specific examples of the performance issues.
- 2
Create a safe, private environment for the conversation.
- 3
Focus on behaviors and outcomes, not the person.
- 4
Encourage dialogue by asking for their perspective.
- 5
End with a clear action plan for improvement.
Example Answers
I would first gather specific instances where the team member's performance didn't meet expectations. Then, I would find a quiet space to discuss this privately, ensuring they feel safe. I would explain the impact of their actions rather than making it personal. I'd ask for their thoughts on the situation to foster open communication, and together we would outline clear steps for improvement.
If a key supplier fails to deliver materials on time, how would you manage production requirements?
How to Answer
- 1
Assess the impact on production schedules immediately.
- 2
Communicate promptly with the supplier to understand reasons for the delay.
- 3
Explore alternative suppliers or materials to mitigate delays.
- 4
Prioritize tasks based on available resources and customer impact.
- 5
Keep the team informed about changes and adjustments to the plan.
Example Answers
First, I would evaluate how the delay affects our production timeline and determine critical tasks. Then, I would contact the supplier to get updates and explore any potential alternatives. If necessary, I’d look for other suppliers who could provide the materials quickly while ensuring the team is updated on our revised plan.
Shop Supervisor Position Details
Recommended Job Boards
CareerBuilder
www.careerbuilder.com/jobs/keyword/shop-supervisorZipRecruiter
www.ziprecruiter.com/Jobs/Shop-SupervisorThese job boards are ranked by relevance for this position.
Related Positions
Ace Your Next Interview!
Practice with AI feedback & get hired faster
Personalized feedback
Used by hundreds of successful candidates
Ace Your Next Interview!
Practice with AI feedback & get hired faster
Personalized feedback
Used by hundreds of successful candidates