Top 30 Liner Installer Interview Questions and Answers [Updated 2025]
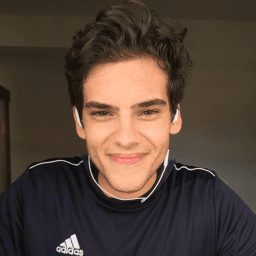
Andre Mendes
•
March 30, 2025
Preparing for a Liner Installer interview? Dive into our comprehensive guide featuring the most common interview questions for this crucial role. You'll find example answers and expert tips on how to respond effectively, ensuring you leave a lasting impression. Whether you're a seasoned professional or a newcomer, this post equips you with the insights needed to confidently tackle any question that comes your way.
Download Liner Installer Interview Questions in PDF
To make your preparation even more convenient, we've compiled all these top Liner Installerinterview questions and answers into a handy PDF.
Click the button below to download the PDF and have easy access to these essential questions anytime, anywhere:
List of Liner Installer Interview Questions
Behavioral Interview Questions
Tell me about a time when you had to work closely with a team to install a liner. How did you ensure effective collaboration?
How to Answer
- 1
Choose a specific project where teamwork was essential.
- 2
Highlight your role and contributions clearly.
- 3
Mention communication strategies used within the team.
- 4
Discuss any challenges faced and how they were resolved together.
- 5
Conclude with the successful outcome of the project.
Example Answers
During a large pool installation project, I worked closely with three other installers. I organized daily meetings to discuss our progress and any issues. To ensure we communicated effectively, we used walkie-talkies to stay in touch throughout the day. One challenge was aligning our schedules, but we adapted by being flexible and offering support to each other. This led to a successful installation ahead of schedule, and the client was extremely satisfied.
Describe a challenging liner installation project you worked on. What made it difficult and how did you overcome the challenges?
How to Answer
- 1
Identify a specific project to discuss
- 2
Explain the unique challenges you faced
- 3
Describe the steps you took to address those challenges
- 4
Highlight any teamwork or collaboration involved
- 5
Conclude with the successful outcome and what you learned
Example Answers
In one project, we faced severe weather conditions that delayed our liner installation timeline. To overcome this, I coordinated with the team to develop a flexible schedule and sourced additional materials in advance. By adapting our approach, we completed the project on time despite the conditions.
Don't Just Read Liner Installer Questions - Practice Answering Them!
Reading helps, but actual practice is what gets you hired. Our AI feedback system helps you improve your Liner Installer interview answers in real-time.
Personalized feedback
Unlimited practice
Used by hundreds of successful candidates
Can you provide an example of a time when you had to ensure the quality of a liner installation? How did you check everything was up to standard?
How to Answer
- 1
Describe a specific project where you installed liners.
- 2
Explain the quality standards you needed to meet.
- 3
Detail the steps you took to inspect the installation.
- 4
Include the tools or methods you used for checking quality.
- 5
Mention the outcome and any feedback from supervisors or clients.
Example Answers
During a recent project installing a pool liner, I followed strict quality standards by checking for proper alignment and securing all seams. I used a level to ensure the liner was perfectly fitted and walked the perimeter to inspect for any wrinkles. After installation, I received positive feedback from the client on the quality of the job.
Give an example of a time you identified a safety hazard while installing liners. What steps did you take to address it?
How to Answer
- 1
Choose a specific incident where you found a safety hazard.
- 2
Describe the hazard clearly and why it was a concern.
- 3
Explain the steps you took to mitigate the hazard, such as communicating with the team.
- 4
Mention any safety protocols or guidelines you followed.
- 5
Conclude with the positive outcome from your actions.
Example Answers
During a recent liner installation, I noticed that the ground was unstable near the installation site. I immediately informed my team leader and we decided to halt work until we could assess the situation. We moved the equipment to a safer location and reinforced the ground before resuming. This not only ensured everyone’s safety but also avoided potential accidents.
Describe a situation where an unexpected problem occurred during a liner installation. How did you adapt to the situation?
How to Answer
- 1
Think of a specific unexpected issue you faced during a past installation.
- 2
Explain how you assessed the problem and its impact on the project.
- 3
Discuss the steps you took to resolve the issue quickly.
- 4
Highlight any tools or techniques you used to adapt during the situation.
- 5
Mention the outcome and what you learned from the experience.
Example Answers
During a liner installation, we discovered that the ground conditions were much different than expected due to recent rain, which caused excess water pooling. I quickly assessed the impact on our schedule and decided to pump out the water and use sandbags to divert further water. This allowed us to continue the installation within the planned timeframe, and I learned the importance of assessing weather conditions before starting a project.
Can you provide an example of when you took leadership during a liner installation project? What was the outcome?
How to Answer
- 1
Think of a specific project where you led a team.
- 2
Describe your role and how you organized the work.
- 3
Mention any challenges faced and how you overcame them.
- 4
Share the outcome and what was achieved.
- 5
Reflect on what you learned about leadership from this experience.
Example Answers
During a recent liner installation in a large residential complex, I took the lead by coordinating between the crew and the project manager. We faced unexpected rain, which could have delayed the project. I organized the team to cover the work area with tarps and adjusted our schedule to complete the task ahead of the weather. As a result, we finished on time and the client was very satisfied.
Describe a time when your attention to detail prevented a potential issue during liner installation.
How to Answer
- 1
Select a specific incident related to liner installation.
- 2
Explain what details you noticed that others might have missed.
- 3
Describe the action you took to address the issue.
- 4
Share the positive outcome or result from your action.
- 5
Use clear and simple language to keep the answer focused.
Example Answers
During a recent liner installation, I noticed that the seams were not aligning correctly. I double-checked the measurements against the installation plan and found a discrepancy. By recalculating and adjusting the liner placement, I ensured everything fitted perfectly, which prevented water leakage later on.
Can you describe a time when you implemented a new technique or tool in liner installation that improved efficiency or quality?
How to Answer
- 1
Think of a specific tool or technique you introduced.
- 2
Focus on the problem it solved in the installation process.
- 3
Quantify the improvements if possible, like time saved or quality increased.
- 4
Explain how you got the team on board with the new method.
- 5
Highlight any positive feedback from clients or management.
Example Answers
I introduced a new laser alignment tool that reduced alignment errors by 30%. This was crucial in preventing leaks post-installation. The team quickly adapted to the new technology after I provided training sessions, and we received positive feedback from our client about the improved quality.
Tell me about a successful interaction you had with a client during or after a liner installation project.
How to Answer
- 1
Choose a specific instance that highlights your communication skills.
- 2
Emphasize how you understood the client's needs and addressed any concerns.
- 3
Describe the positive outcome for the client and the project.
- 4
Use a clear structure: situation, action, result.
- 5
Keep the tone professional and focused on client satisfaction.
Example Answers
During a recent liner installation, a client was worried about the timeline. I took the time to explain each step and provided regular updates. This eased their concerns and led to a successful installation that they were very pleased with.
Don't Just Read Liner Installer Questions - Practice Answering Them!
Reading helps, but actual practice is what gets you hired. Our AI feedback system helps you improve your Liner Installer interview answers in real-time.
Personalized feedback
Unlimited practice
Used by hundreds of successful candidates
Technical Interview Questions
What methods do you use to ensure that liners are installed without wrinkles or air bubbles?
How to Answer
- 1
Start by preparing the surface thoroughly before installation.
- 2
Use a methodical approach to lay out the liner, ensuring it is properly aligned.
- 3
Work from the center outward to help minimize air pockets and wrinkles.
- 4
Utilize tools such as a squeegee to push out air and smooth the surface evenly.
- 5
Regularly check for bubbles and wrinkles during the installation process to address them immediately.
Example Answers
I ensure the surfaces are clean and prepped, then I lay the liner out from the center, using a squeegee to push out air as I go.
What are the different types of materials used in liner installations and what are their respective advantages?
How to Answer
- 1
Identify main types of liner materials like polyethylene, PVC, and EPDM.
- 2
Briefly explain advantages like durability, cost-effectiveness, and installation ease.
- 3
Mention specific applications for each material type.
- 4
Use clear, non-technical language for better understanding.
- 5
Prepare to give practical examples of where you’ve used these materials.
Example Answers
There are several types of materials used in liner installations, such as polyethylene, PVC, and EPDM. Polyethylene is known for its durability and resistance to chemicals, making it great for industrial applications. PVC is often more affordable and easy to install, suitable for residential projects. EPDM rubber is highly flexible, which is beneficial for applications that require a weather-resistant solution.
Don't Just Read Liner Installer Questions - Practice Answering Them!
Reading helps, but actual practice is what gets you hired. Our AI feedback system helps you improve your Liner Installer interview answers in real-time.
Personalized feedback
Unlimited practice
Used by hundreds of successful candidates
What tools and equipment are essential for liner installation, and how are they used?
How to Answer
- 1
Identify the key tools like liner materials, adhesive, installation tools, and safety gear.
- 2
Explain the purpose of each tool and how they contribute to successful installation.
- 3
Mention any specific techniques or methods used with these tools.
- 4
Keep your answer organized and logical, starting with the most critical tools.
- 5
Be prepared to discuss safety protocols associated with the tools.
Example Answers
Essential tools for liner installation include the liner material itself, high-quality adhesive, scissors for trimming, and a smooth roller for applying pressure. The liner is laid out first, adhesive is applied to the surface, then the liner is carefully positioned before using the roller to ensure it sticks smoothly.
Can you outline the typical process for installing a liner from start to finish?
How to Answer
- 1
Begin with site preparation including site inspection and cleaning
- 2
Next, layout the liner and make necessary cuts or adjustments
- 3
Secure the liner in place with appropriate anchoring or bonding methods
- 4
After securing, focus on sealing seams and ensuring water tightness
- 5
Finally, perform a quality check before completing the installation
Example Answers
The first step is to prepare the site by clearing debris and inspecting for obstacles. Then, I layout the liner, cutting it to fit properly. After positioning, I secure the liner using anchors or adhesive. It's important to seal all seams to prevent leaks, and finally, I check everything to ensure it's installed correctly.
What steps do you take to ensure compatibility of the liner material with the project requirements?
How to Answer
- 1
Review project specifications thoroughly to understand material requirements
- 2
Consult with manufacturers for material properties and suitability
- 3
Consider environmental factors that may affect material performance
- 4
Evaluate installation conditions and compatibility with existing systems
- 5
Test material samples when possible to verify compatibility
Example Answers
I start by reviewing the project specifications to identify specific liner requirements. Then, I consult with the liner manufacturers to understand the properties of the materials available. I also assess any environmental factors, like temperature and exposure to chemicals, that could affect material performance.
How do you calculate the dimensions and placement of a liner to ensure optimal fit and performance?
How to Answer
- 1
Measure the exact dimensions of the area for the liner installation
- 2
Consider the material properties of the liner for flexibility and fitting
- 3
Account for any necessary overlaps or seams in the liner design
- 4
Use precise techniques such as computer-aided design for accuracy
- 5
Conduct a test fitting to verify dimensions before final installation
Example Answers
To calculate the dimensions, I start by accurately measuring the installation area to ensure the liner fits perfectly. I also check the liner's material for flexibility to avoid any unexpected issues during installation. I account for overlaps, ensuring they don't compromise performance, and then use CAD software for precise dimensions. Finally, I perform a test fitting to confirm everything is correct before proceeding with the installation.
What common issues might arise during liner installation, and how would you address them?
How to Answer
- 1
Identify typical installation issues such as misalignment or tears.
- 2
Discuss preventive measures like proper training and checking materials.
- 3
Explain how to troubleshoot during installation, including adjustments and repairs.
- 4
Mention the importance of communication with the team during challenges.
- 5
Highlight the significance of post-installation inspections to ensure quality.
Example Answers
Common issues during liner installation include misalignment and tearing. To prevent these, I always ensure that the team is properly trained and that we check all materials before starting. If misalignment occurs, I would stop the installation to make adjustments right away to avoid larger problems.
What are the key techniques for ensuring strong adhesion of liners to surfaces?
How to Answer
- 1
Clean the surface thoroughly to remove dirt, grease, or contaminants.
- 2
Ensure the surface is dry and at an appropriate temperature for adhesion.
- 3
Select the right adhesive or bonding agent for the liner material and surface type.
- 4
Apply the adhesive evenly and without gaps.
- 5
Allow adequate curing time as per manufacturer's specifications.
Example Answers
I ensure strong adhesion by starting with a clean and dry surface, then selecting the right adhesive tailored for the liner material. I apply it evenly and follow up by letting it cure properly.
What techniques are used to ensure that installed liners are watertight?
How to Answer
- 1
Discuss material selection for waterproof liners
- 2
Mention proper seam sealing techniques
- 3
Explain the importance of correct installation procedures
- 4
Highlight the use of testing methods post-installation
- 5
Reference maintenance practices to ensure long-term watertight integrity
Example Answers
To ensure that installed liners are watertight, I focus on using high-quality materials specifically designed for waterproofing. I ensure that seams are properly sealed with compatible adhesives or welding techniques to prevent leaks. Following precise installation procedures is key, as is performing water testing after installation to verify there are no leaks.
How do you account for thermal expansion and contraction in liner installations?
How to Answer
- 1
Understand the materials being used and their thermal expansion properties
- 2
Include allowances for expansion in the installation design
- 3
Use appropriate anchoring techniques to accommodate movement
- 4
Monitor environmental conditions during installation and throughout the liner's lifespan
- 5
Conduct regular inspections to identify any issues related to expansion or contraction
Example Answers
I account for thermal expansion by ensuring that the materials selected have known expansion coefficients, allowing for proper spacing and overlaps during installation to accommodate those changes.
Don't Just Read Liner Installer Questions - Practice Answering Them!
Reading helps, but actual practice is what gets you hired. Our AI feedback system helps you improve your Liner Installer interview answers in real-time.
Personalized feedback
Unlimited practice
Used by hundreds of successful candidates
Situational Interview Questions
You are running behind schedule on a liner installation project. How do you manage the situation to ensure deadlines are met?
How to Answer
- 1
Assess the current status of the project and identify delays.
- 2
Prioritize tasks that are critical to meeting the deadline.
- 3
Communicate with the team to delegate responsibilities effectively.
- 4
Consider working overtime or adjusting shifts to gain more time.
- 5
Maintain regular updates to ensure everyone is aligned and aware of changes.
Example Answers
First, I would assess what caused the delay and identify the tasks that are critical. I'd then prioritize those tasks and ensure that the team knows what needs to happen to catch up. I might even arrange for overtime if necessary to help meet our deadline.
During an outdoor liner installation, unexpected rain begins. How do you handle the situation to ensure the quality of the installation?
How to Answer
- 1
Assess the weather conditions quickly and determine the severity of the rain.
- 2
Protect the installation area by using tarps or plastic sheeting to shield the liner from water.
- 3
Pause any ongoing work if the rain threatens the quality or safety of the installation.
- 4
Communicate with your team about the situation and your plan to address it.
- 5
Resume work only when it is safe and conditions are suitable for installation.
Example Answers
If rain starts during the installation, I would first evaluate how heavy it is. If it's light, I would use tarps to cover the liner. If it's heavy, I'd stop working and wait for it to clear before continuing.
Don't Just Read Liner Installer Questions - Practice Answering Them!
Reading helps, but actual practice is what gets you hired. Our AI feedback system helps you improve your Liner Installer interview answers in real-time.
Personalized feedback
Unlimited practice
Used by hundreds of successful candidates
If a critical piece of equipment fails during an installation, what steps would you take to resolve the issue and continue the project?
How to Answer
- 1
Assess the failure to understand the problem
- 2
Quickly inform the team and relevant supervisors
- 3
Identify if there's a backup option or a substitute tool available
- 4
Implement a temporary solution to maintain progress
- 5
Document the issue and follow up for long-term resolution
Example Answers
If a critical piece of equipment fails, I would first assess the situation to understand what exactly went wrong. After that, I would notify my team and supervisors immediately so we can all stay informed. If we have a backup tool or equipment, I would use that to continue the work, while I document the failure for future reference.
A client is unsatisfied with the initial liner installation result. How would you address their concerns and ensure they are satisfied with the final outcome?
How to Answer
- 1
Listen actively to the client's concerns without interrupting.
- 2
Apologize for the inconvenience and express understanding of their dissatisfaction.
- 3
Assess the situation to identify the specific issues with the installation.
- 4
Provide clear options for resolution, such as repairs or a complete redo.
- 5
Follow up with the client after the resolution to ensure satisfaction.
Example Answers
I would start by listening carefully to what the client has to say about their concerns. I would apologize for any inconvenience and assure them that I understand their dissatisfaction. Then, I would evaluate the installation to pinpoint the issues and discuss possible solutions, like fixing the liner or doing a complete reinstallation if necessary. Finally, I would check in with the client afterward to confirm that they are happy with the work.
You notice two team members having a disagreement about an installation approach. How do you handle the situation to maintain a productive work environment?
How to Answer
- 1
Stay calm and listen to both team members' points of view
- 2
Acknowledge their concerns and validate their feelings
- 3
Encourage them to share their ideas with the team
- 4
Suggest finding a compromise or a better solution together
- 5
Follow up after the discussion to ensure harmony is restored
Example Answers
I would first listen to both sides to understand their concerns. Then, I would encourage them to share their ideas openly and guide them towards finding a solution that incorporates both perspectives.
During a project, you realize you are short of liner material. What actions do you take to resolve the issue without delaying the project?
How to Answer
- 1
Assess the quantity needed and the project requirements immediately
- 2
Check existing stock for any available liner material that could be used
- 3
Contact suppliers to find out about expedited shipping options for additional material
- 4
Consider alternative materials that could be used temporarily if necessary
- 5
Communicate with the project team about the issue and the steps being taken
Example Answers
I would first assess how much liner material is truly needed and check our inventory for any spare material. Then, I would contact our suppliers to inquire about expedited shipping for the required materials and keep my team informed throughout the process to ensure no time is wasted.
You discover midway through an installation that the liner material isn't meeting the quality standards required. How do you handle this issue?
How to Answer
- 1
Stay calm and assess the situation clearly
- 2
Communicate the issue to your team leaders immediately
- 3
Determine if the installation can continue or needs to be paused
- 4
Document the quality issue and the steps taken
- 5
Ensure the correct materials are sourced before proceeding
Example Answers
I would first take a moment to evaluate the extent of the quality issue. Then, I would inform my supervisor and the team about the problem. If necessary, I would pause the installation to prevent further issues and document everything for accountability.
The scope of your installation project changes after you have already begun. How do you adjust your plans and resources accordingly?
How to Answer
- 1
Assess the new requirements thoroughly
- 2
Reprioritize tasks based on the new scope
- 3
Communicate with your team about the changes
- 4
Adjust timelines and resources based on current capabilities
- 5
Maintain flexibility to adapt to further changes
Example Answers
When the scope changes, I first assess the new requirements to understand the impact on the project. Then, I reprioritize tasks and communicate with the team to ensure everyone is aligned. I adjust timelines and allocate resources where needed to meet the new objectives.
A miscommunication has led to an incorrect liner being delivered. How do you address the situation with the supplier and your team?
How to Answer
- 1
Stay calm and assess the situation clearly.
- 2
Communicate the issue to your team first to align on the facts.
- 3
Contact the supplier promptly to clarify the mistake.
- 4
Propose a solution or ask how they can resolve the issue swiftly.
- 5
Keep your team informed about any updates from the supplier.
Example Answers
First, I would gather my team to clearly explain the miscommunication regarding the liner delivery. Then, I would reach out to the supplier to confirm the error and discuss how we can quickly get the correct liner. I would also keep my team updated on any progress.
You are tasked with installing a liner in a high-risk area. How do you conduct a risk assessment and what precautions do you take?
How to Answer
- 1
Identify potential hazards in the area such as unstable ground or nearby structures.
- 2
Assess environmental conditions like weather that could impact safety.
- 3
Develop a clear safety plan detailing all safety gear and procedures.
- 4
Ensure all team members are briefed on risks and emergency procedures.
- 5
Use appropriate monitoring tools to continuously assess risks during installation.
Example Answers
First, I would identify potential hazards like unstable ground or obstacles in the area. Then, I would assess weather conditions and ensure all team members are wearing the necessary safety gear. Finally, I would create a monitoring plan to review risks throughout the installation process.
Don't Just Read Liner Installer Questions - Practice Answering Them!
Reading helps, but actual practice is what gets you hired. Our AI feedback system helps you improve your Liner Installer interview answers in real-time.
Personalized feedback
Unlimited practice
Used by hundreds of successful candidates
Liner Installer Position Details
Recommended Job Boards
These job boards are ranked by relevance for this position.
Related Positions
- Liner
- Bottom Liner
- Door Liner
- Window Installer
- Hardware Installer
- Action Installer
- Stove Fitter
- Door Fitter
- Trim Installer
- Cushion Filler
Similar positions you might be interested in.
Ace Your Next Interview!
Practice with AI feedback & get hired faster
Personalized feedback
Used by hundreds of successful candidates
Ace Your Next Interview!
Practice with AI feedback & get hired faster
Personalized feedback
Used by hundreds of successful candidates