Top 29 Cushion Filler Interview Questions and Answers [Updated 2025]
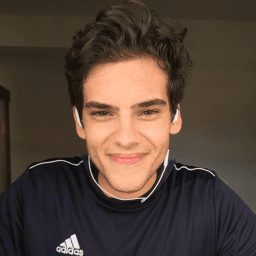
Andre Mendes
•
March 30, 2025
Preparing for a job interview can be daunting, especially for specialized roles like Cushion Filler. In this blog post, we delve into the most common interview questions for this unique position, providing example answers and insightful tips on how to respond effectively. Whether you're a seasoned professional or new to the industry, this guide will help you confidently navigate your next interview.
Download Cushion Filler Interview Questions in PDF
To make your preparation even more convenient, we've compiled all these top Cushion Fillerinterview questions and answers into a handy PDF.
Click the button below to download the PDF and have easy access to these essential questions anytime, anywhere:
List of Cushion Filler Interview Questions
Technical Interview Questions
What are the different types of materials commonly used for cushion filling, and how do they affect the cushion's properties?
How to Answer
- 1
Identify the most common cushion filling materials like foam, fiberfill, and down.
- 2
Explain the properties of each material, such as firmness, durability, and comfort.
- 3
Discuss how these properties influence the intended use of the cushion.
- 4
Mention any environmental aspects or care requirements for the materials.
- 5
Be concise and clear in your explanations to show your knowledge.
Example Answers
There are several common cushion filling materials. Foam offers good support and firmness, making it great for seating. Fiberfill is softer and provides more plushness, suitable for decorative cushions. Down filling is soft and luxurious but requires more care and is not as supportive.
Can you describe the process of evenly distributing filling in a large cushion?
How to Answer
- 1
Start with the cushion cover laid flat to prevent uneven filling.
- 2
Use a funnel or tool to help guide the filling into the corners.
- 3
Add filling in small amounts and evenly distribute it with your hands.
- 4
Check for lumps or uneven areas while filling and adjust as necessary.
- 5
After filling, shake or gently pat the cushion to settle the filling.
Example Answers
To evenly distribute the filling, I first lay out the cushion cover flat to avoid any bumps. I use a funnel to fill the corners, then I add small amounts and massage the filling with my hands to spread it evenly. I frequently check for uneven areas and adjust the filling as needed, followed by gently shaking the cushion to settle everything.
Don't Just Read Cushion Filler Questions - Practice Answering Them!
Reading helps, but actual practice is what gets you hired. Our AI feedback system helps you improve your Cushion Filler interview answers in real-time.
Personalized feedback
Unlimited practice
Used by hundreds of successful candidates
What tools or machinery do you typically use when filling cushions?
How to Answer
- 1
Identify specific tools you have experience with
- 2
Mention any relevant machinery like sewing machines or stuffing machines
- 3
Discuss the types of filling materials used, such as foam or polyester
- 4
Highlight any safety practices or training related to using these tools
- 5
Be ready to explain how you maintain these tools for optimal performance
Example Answers
I typically use a sewing machine for closing up the cushions after filling them. I also work with stuffing machines for larger productions, and I prefer foam and polyester filling for comfort and durability.
How do you ensure that a cushion is filled consistently and to the right firmness?
How to Answer
- 1
Use a measuring device to quantify the amount of filling for each cushion
- 2
Test the firmness of the cushion by pressing on it and comparing it with others
- 3
Adjust the filling based on feedback from touch tests
- 4
Keep a record of the filling amounts used for consistency
- 5
Train to recognize the ideal firmness through experience and practice
Example Answers
I use a measuring device that allows me to fill each cushion with a specific amount of filling, ensuring they are all uniform. After filling, I press on each cushion to check if the firmness matches our standards before finalizing the product.
How do you adjust filling techniques for cushions with different density requirements?
How to Answer
- 1
Identify the specific density required for the cushion type.
- 2
Use lighter fills for softer cushions and denser materials for firmer support.
- 3
Consider the purpose of the cushion, such as decorative or functional.
- 4
Blend different materials to achieve the desired density and comfort.
- 5
Test the fill after making adjustments to ensure it meets standards.
Example Answers
For softer cushions, I use materials like polyester fiberfill, which provides a plush feel. For firmer cushions, I would switch to high-resilience foam to achieve the necessary support.
How do you measure the amount of filling required for different cushion sizes?
How to Answer
- 1
Identify the dimensions of the cushion (length, width, height)
- 2
Consider the desired firmness and plushness of the cushion
- 3
Use a filling density chart relevant to the material being used
- 4
Calculate the volume of the cushion and multiply by the filling density
- 5
Adjust based on user preferences or previous filling experiences
Example Answers
For a standard sofa cushion measuring 24x24x6 inches, I would first calculate the volume, which is 24x24x6 equals 3456 cubic inches. Then, I would refer to my filling density guide to find out how much filling material I need per cubic inch based on the required firmness.
What steps do you take to handle and store filling materials properly?
How to Answer
- 1
Always follow safety protocols when handling materials.
- 2
Store materials in a dry, clean area to prevent contamination.
- 3
Keep filling materials away from direct sunlight to maintain quality.
- 4
Label all containers clearly with contents and date of storage.
- 5
Use appropriate PPE (personal protective equipment) when handling substances.
Example Answers
I ensure to follow all safety protocols by wearing PPE and handling materials carefully. I store them in a clean, dry place away from sunlight and label everything properly to avoid confusion.
What are some safety precautions you follow when filling cushions?
How to Answer
- 1
Always wear appropriate safety gear, such as gloves and a mask, to protect yourself from dust and allergens.
- 2
Ensure the workspace is free from clutter and hazards to prevent accidents while handling materials.
- 3
Follow manufacturer guidelines for materials to avoid using harmful substances or incorrect filling.
- 4
Keep tools and equipment well-maintained to prevent malfunctions during the filling process.
- 5
Stay hydrated and take regular breaks to avoid fatigue that could lead to careless mistakes.
Example Answers
I always wear gloves and a face mask while filling cushions to protect myself from allergens. I also make sure my workspace is clean and organized.
How do you interpret and follow customer specifications for custom cushion orders?
How to Answer
- 1
Listen carefully to the customer's needs and preferences.
- 2
Ask clarifying questions if any specification is unclear.
- 3
Refer to the company's guidelines for measurements and materials.
- 4
Confirm the order details with the customer before proceeding.
- 5
Document everything to ensure accuracy throughout the process.
Example Answers
I begin by attentively listening to the customer's specifications, taking notes on their preferences. If anything is unclear, I ask questions to ensure I understand fully. Once I have all the information, I double-check everything against our standards before confirming the order with them.
What are some common issues you encounter when filling cushions, and how do you troubleshoot them?
How to Answer
- 1
Identify specific issues like uneven filling or compressed materials.
- 2
Discuss preventive measures to avoid these issues during filling.
- 3
Explain how to assess and point out the problem quickly.
- 4
Describe techniques to correct the problem, such as redistributing fill.
- 5
Emphasize the importance of quality control in the filling process.
Example Answers
One common issue is uneven filling. I ensure even distribution by fluffing the filling before using it and regularly checking for lumps. If I spot an issue, I redistribute the filling manually to create a balanced surface.
Don't Just Read Cushion Filler Questions - Practice Answering Them!
Reading helps, but actual practice is what gets you hired. Our AI feedback system helps you improve your Cushion Filler interview answers in real-time.
Personalized feedback
Unlimited practice
Used by hundreds of successful candidates
How does the type of cushion cover affect your filling technique?
How to Answer
- 1
Identify different types of cushion covers such as fabric, leather, or waterproof materials.
- 2
Explain how each cover type affects the filling density and method.
- 3
Discuss considerations like weight, durability, and comfort based on the cover material.
- 4
Mention adjustments needed in your filling technique to prevent bulging or unevenness.
- 5
Provide examples of specific filling materials that work best with different cover types.
Example Answers
For softer fabric covers, I use a lighter filling technique to keep the cushion plush and comfortable, while with leather covers, I prefer a denser filling to maintain firmness and prevent sagging.
How do you keep track of the filling material inventory to ensure continuous production?
How to Answer
- 1
Utilize inventory management software to track stock levels.
- 2
Conduct weekly physical counts of filling materials to confirm accuracy.
- 3
Set reorder points for each material to trigger restocking.
- 4
Communicate regularly with suppliers to ensure timely deliveries.
- 5
Log usage rates to forecast future material needs.
Example Answers
I use inventory management software that updates stock levels in real time. This allows me to monitor materials and set reorder points so we never run out.
Behavioral Interview Questions
Describe a time when your attention to detail prevented a potential problem.
How to Answer
- 1
Choose a specific example from your past experiences.
- 2
Highlight the details you noticed that others might have missed.
- 3
Explain the consequences of the potential problem you prevented.
- 4
Discuss the positive outcome that resulted from your attention to detail.
- 5
Keep it concise and focused on your role in the situation.
Example Answers
In my previous job, I was responsible for checking the inventory levels before a major shipment. I noticed that one item was miscounted, which would have led to a shortfall. I corrected it before the shipment went out, ensuring we met our client's needs on time and avoided a costly delay.
Can you tell me about a time you worked as part of a team to complete a large batch of cushion fillings?
How to Answer
- 1
Choose a specific project involving cushion fillings.
- 2
Describe your role and how you contributed to the team.
- 3
Highlight any challenges the team faced and how you overcame them together.
- 4
Mention communication methods used within the team.
- 5
Emphasize the successful outcome and what you learned.
Example Answers
In my previous job, we had to fill 500 cushions for a big order. I coordinated with my teammates to divide the work efficiently. We communicated through daily check-ins to ensure everyone was on track. When we faced a shortage of filling material, we brainstormed and quickly sourced more. We completed the order on time, and the client was very happy.
Don't Just Read Cushion Filler Questions - Practice Answering Them!
Reading helps, but actual practice is what gets you hired. Our AI feedback system helps you improve your Cushion Filler interview answers in real-time.
Personalized feedback
Unlimited practice
Used by hundreds of successful candidates
Give an example of a difficult challenge you faced when filling cushions and how you overcame it.
How to Answer
- 1
Identify a specific challenge related to cushion filling.
- 2
Explain the steps you took to address the challenge.
- 3
Emphasize the skills you used during the process.
- 4
Share the outcome and what you learned from the experience.
- 5
Keep it concise and focused on your role in overcoming the challenge.
Example Answers
In my previous position, I struggled with inconsistency in the cushion filling which affected the final product's quality. I developed a step-by-step process for measuring and filling the cushions evenly, monitored my techniques, and adjusted the filling materials for optimal results. As a result, the quality improved significantly, and we received positive feedback from customers.
Describe how you adapt to changes in production requirements or specifications.
How to Answer
- 1
Stay calm and open-minded when changes occur.
- 2
Assess the impact of the changes on your work and the team.
- 3
Communicate proactively with your supervisor or team.
- 4
Be ready to adjust your workflow and priorities as needed.
- 5
Seek feedback to improve future responses to changes.
Example Answers
When production requirements changed last month, I took time to understand the new specifications and how they affected my tasks. I communicated with team members to align our efforts and adjusted my schedule to prioritize urgent changes.
Tell me about a time you improved the efficiency of your cushion filling process.
How to Answer
- 1
Identify a specific problem you encountered in the cushion filling process.
- 2
Explain the steps you took to analyze and improve the process.
- 3
Highlight any tools or techniques you used to implement changes.
- 4
Discuss the measurable outcomes or efficiency gains from your improvements.
- 5
Reflect on what you learned from the experience.
Example Answers
In my previous role, we faced delays due to manual filling. I analyzed the time taken for each step, then introduced automated filling equipment, which cut our filling time by 30%. The improvements boosted our output and reduced labor costs significantly.
How do you prioritize your tasks when you have multiple orders with similar deadlines?
How to Answer
- 1
Identify which orders are the most urgent or time-sensitive first.
- 2
Consider the complexity and time required for each task.
- 3
Communicate with stakeholders to clarify priorities if necessary.
- 4
Use a task management tool to visualize deadlines and workloads.
- 5
Remain flexible and adjust priorities as new information arises.
Example Answers
I first look at the urgency of each order to determine which needs to be filled first. Then I assess the complexity of each order and tackle the simpler tasks first, balancing the workload. If needed, I will check in with my supervisor to confirm priorities.
Describe a situation where you took initiative to solve a problem on the job.
How to Answer
- 1
Think of a specific problem you encountered at work.
- 2
Explain the action you took without being prompted.
- 3
Detail the positive outcome from your action.
- 4
Use the STAR method: Situation, Task, Action, Result.
- 5
Keep it relevant to the skills needed for the Cushion Filler position.
Example Answers
In my previous role, we ran out of cushioning materials unexpectedly. I took the initiative to contact our suppliers directly to expedite a new order, ensuring we could continue production without delays. As a result, we minimized downtime by 24 hours.
Have you ever suggested a change in the filling process that improved the final product? What was it?
How to Answer
- 1
Think of a specific instance where you noticed a problem in the filling process.
- 2
Describe the observation that led to your suggestion.
- 3
Explain the change you proposed clearly and simply.
- 4
Discuss the positive outcome resulting from your suggestion.
- 5
Be ready to highlight your role in implementing the change.
Example Answers
In my previous role, I noticed that the filling machine often produced inconsistencies in the volume of filling. I suggested implementing a regular calibration schedule, which I helped set up. As a result, we achieved a 15% reduction in volume deviations and improved overall product quality.
Describe a time you had a conflict with a coworker in the production process and how it was resolved.
How to Answer
- 1
Identify a specific conflict scenario you faced.
- 2
Explain the differing viewpoints clearly and neutrally.
- 3
Describe the steps you took to address the conflict directly.
- 4
Highlight the outcome and what you learned from the experience.
- 5
Emphasize teamwork and maintaining a positive work environment.
Example Answers
In our production team, I had a disagreement with a coworker about the best method to stack cushions for efficiency. We both believed strongly in our approaches. I proposed a short meeting where we could each present our techniques. After discussing, we decided to combine our methods, which resulted in a more effective stacking process. This experience taught me the value of collaboration.
Situational Interview Questions
A customer requests a rush order for a large number of cushions. How would you handle this situation?
How to Answer
- 1
Acknowledge the urgency and importance of the customer's request.
- 2
Ask specific questions about the requirements and timeline.
- 3
Check current production capacity and resources immediately.
- 4
Communicate clearly if the rush order can be fulfilled and by when.
- 5
Offer alternatives if the timeline cannot be met.
Example Answers
First, I would thank the customer for their order and ask for details on the quantity and desired delivery date. Then, I would check our current production capabilities to see if we can meet that timeline and inform the customer if we can fulfill the order and when they can expect delivery.
You notice that the materials you received are defective. What steps would you take to address this issue?
How to Answer
- 1
Inspect the materials thoroughly to confirm defects
- 2
Document the defects clearly with photos and notes
- 3
Contact the supplier immediately to report the issue
- 4
Request a replacement or refund as necessary
- 5
Inform your supervisor about the situation and next steps
Example Answers
First, I would inspect the materials to confirm they are indeed defective and document my findings with photos. Then, I'd contact the supplier to explain the situation and request replacements. Lastly, I would keep my supervisor updated on the progress.
Don't Just Read Cushion Filler Questions - Practice Answering Them!
Reading helps, but actual practice is what gets you hired. Our AI feedback system helps you improve your Cushion Filler interview answers in real-time.
Personalized feedback
Unlimited practice
Used by hundreds of successful candidates
You find that some cushions are not meeting the quality standards. How would you handle this?
How to Answer
- 1
Identify the specific issues with the cushions.
- 2
Communicate the findings with the production team.
- 3
Suggest corrective actions to prevent future issues.
- 4
Document the quality control process.
- 5
Follow up to ensure the standards are met consistently.
Example Answers
I would first examine the cushions to determine the specific quality issues, like uneven filling. Then, I would share my findings with the production team and suggest adjustments in the filling process. I would also document the issues and our corrective actions to track progress.
If a team member was repeatedly filling cushions incorrectly, how would you approach the situation?
How to Answer
- 1
Address the issue privately and calmly with the team member
- 2
Observe their filling process to identify specific mistakes
- 3
Provide constructive feedback and offer assistance
- 4
Suggest additional training or resources if needed
- 5
Follow up to ensure improvement and maintain open communication
Example Answers
I would first talk to the team member privately to understand their process and why mistakes are occurring. Then, I would observe them filling cushions to pinpoint issues and offer constructive feedback. If necessary, I would suggest further training and ensure I follow up to see their progress.
There is a shortage of a specific type of filling material. How would you manage your resources to continue production?
How to Answer
- 1
Assess current inventory levels of filling materials.
- 2
Identify alternative filling materials that can be used.
- 3
Communicate with suppliers to find out timelines for restocking.
- 4
Evaluate production priorities and adjust as necessary.
- 5
Implement a temporary production plan using available resources.
Example Answers
I would first check our inventory to see how much filling material we have left, then I'd research alternative fillers that could maintain product quality. I'd also reach out to suppliers for updates on material availability and adjust our production schedule to prioritize high-demand items.
A customer complains that their cushions are too firm. How would you resolve their issue?
How to Answer
- 1
Listen to the customer's concerns without interrupting.
- 2
Acknowledge their feelings and validate their experience.
- 3
Ask specific questions to understand their preference for firmness.
- 4
Suggest possible solutions, like an exchange or a softer option.
- 5
Follow up with the customer to ensure their satisfaction.
Example Answers
I would first listen carefully to the customer's concerns and acknowledge that I understand firm cushions might not be comfortable for everyone. Then, I would ask if they have a specific level of softness in mind and suggest we can exchange it for a softer option that might suit them better.
How would you handle a situation where your workload suddenly doubles due to unexpected orders?
How to Answer
- 1
Prioritize tasks based on urgency and importance
- 2
Communicate with your supervisor about the workload increase
- 3
Seek assistance from coworkers if possible
- 4
Use time management techniques to optimize your workflow
- 5
Stay calm and focused to maintain productivity
Example Answers
I would first talk to my supervisor to inform them of the sudden increase in workload and seek their advice on prioritizing tasks. I would identify the most urgent orders and tackle those first, while asking my team for support if needed.
You're asked to develop a new filling technique to enhance cushion comfort. How would you approach this task?
How to Answer
- 1
Research current filling materials and techniques
- 2
Identify key comfort factors like support and pressure distribution
- 3
Brainstorm new materials or combinations for enhanced comfort
- 4
Prototype the filling technique and test it with users
- 5
Gather feedback and refine the approach based on user preferences
Example Answers
I would start by researching existing filling materials like memory foam and gel to understand their comfort properties. Then, I'd identify key factors such as support and pressure relief. After that, I could experiment with a blend of these materials to create a hybrid filling technique, prototype it, and conduct user testing to gather feedback.
Cushion Filler Position Details
Recommended Job Boards
SimplyHired
www.simplyhired.com/search?q=cushion+fillZipRecruiter
www.ziprecruiter.com/Jobs/Cushion-FillerThese job boards are ranked by relevance for this position.
Related Positions
- Cushion Maker
- Mattress Filler
- Mold Filler
- Door Liner
- Bottom Liner
- Coverer
- Bed Maker
- Plastic Fabricator
- Chair Maker
- Body Fitter
Similar positions you might be interested in.
Ace Your Next Interview!
Practice with AI feedback & get hired faster
Personalized feedback
Used by hundreds of successful candidates
Ace Your Next Interview!
Practice with AI feedback & get hired faster
Personalized feedback
Used by hundreds of successful candidates